This introductory paper is the research content of the paper "Thermal Factor of Aluminium High pressure Die Casting Container (Mould) to achieve Six Sigma Quality of Castings" published by IJERT.
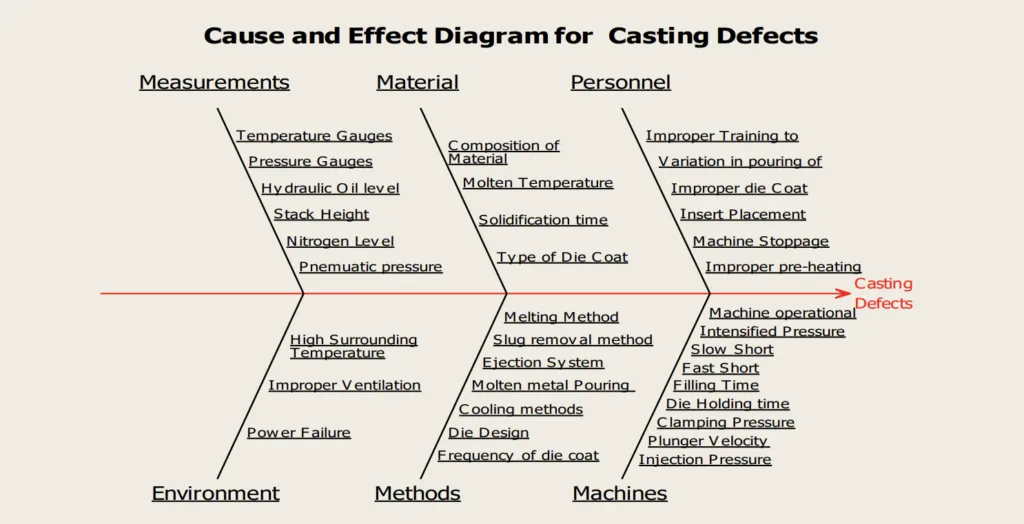
1. Overview:
- Title: Thermal Factor of Aluminium High pressure Die Casting Container (Mould) to achieve Six Sigma Quality of Castings
- Author: Suraj Marathe, Dr. Carmo Quadros
- Publication Year: 2020
- Published Journal/Society: International Journal of Engineering Research & Technology (IJERT)
- Keywords: High Pressure Die-casting (HPDC); Preheating temperature; Six Sigma quality of a casting; ProCast
2. Abstract
This paper deals with the analysis of the temperature factors of aluminium high pressure die casting Container (mould). It also describes the development of expression for preheating temperature factor of mould to maintain the molten aluminium temperature, which gives the six sigma quality product depending on the degree of preheating of mould. The monitored temperature factors are very much important in the die-casting process, which is positively reflected in production efficiency and the quality of the casting. In die casting, the melted metal is pressed under high temperature into a mould cavity of significantly lower temperature. The mould is then exposed to a thermal strain of individual surface layers of the mould material. The speed of cooling of the castings in the metal mould increases, causing an increase of thermal gradients in the casting. Intensive heat exchange between the castings And the metal mould harms fluidity, which increases the danger of incomplete replenishment and the occurrence of cold joints. Analysis and optimization were performed with the help of ProCast Simulation software which uses Finite Element Analysis Technology.
3. Research Background:
Background of the research topic:
Die casting is a high-volume manufacturing process for metal parts, particularly aluminum alloys. Aluminum alloys offer lightweight and high dimensional stability for complex shapes. However, casting defects are common, making the process inherently uncertain.
Status of previous research:
- The global market demands high-quality castings, driving the need for efficient techniques like Six Sigma [1].
- Casting quality is influenced by thermal and technological factors, including temperatures of the alloy, filling chamber, and mould [3, 6].
- Numerous factors affect pressure die castings, such as pressing velocity, pressure, and filling time [7].
- Prior work includes optimization of die casting [13, 14], gating system redesign [5], DOE and Taguchi methods [1, 11], flow simulation [15, 16], and thermal factor analysis [17].
- A stable finite difference scheme has been used for 3D thermal analysis in die casting [8].
- Semi-solid die casting has been studied for improving mechanical properties [9].
- Rejection levels in casting are typically 11-13%, motivating efforts to reach Six Sigma limits [1].
Need for research:
Despite existing research, many factors and problems in die casting remain unexplained. This study specifically addresses the impact of thermal factors on casting quality. The need is to reduce rejection and to achive six sigma quality.
4. Research purpose and research question:
Research purpose:
To investigate the effects of thermal factors in a die casting process on the quality of cast product and optimize the process using ProCast Simulation.
Core research:
- Identify critical parameters (thermal and pressure) contributing to casting rejection.
- Develop an expression for the preheating temperature factor of the mould.
- Analyze and optimize the preheating temperature using ProCast software.
5. Research methodology
- Research Design: Experimental and simulation-based.
- Data Collection:
- Critical parameters (molten metal, mould, and filling chamber temperatures; intensified and clamping pressures) were monitored.
- ProCast Simulation software, using Finite Element Analysis, was employed.
- Experimental setup: 100T HPDC machine, diesel-fired holding furnace, close-loop cooling system.
- Products: Die-casted rotors (100S, M50, B48) with varying dimensions.
- Analysis Method:
- A thermal balance equation (Equation 7) was developed to determine the required mould preheating temperature.
- ProCast simulation was used to validate the equation and analyze mould temperature evolution.
- Cause and effect diagram (Fig. 1) was used to identify process parameters.
6. Key research results:
Key research results and presented data analysis:
- A heat balance equation (Equation 7) was derived to calculate the required preheating temperature. This equation considers factors like:
- Weight and surface area of the casting.
- Specific heat of molten and solid aluminum.
- Temperatures of molten and solidus aluminum.
- Latent heat of solidus aluminum.
- Heat transfer coefficient.
- Casting temperature upon removal from the mould.
- The equation was validated using ProCast simulation.
- Preheating temperatures for 100S and M50 rotors were determined (63.68°C and 76.33°C, respectively) to achieve six sigma quality.
- Simulation showed mould temperature reaching a peak of 475°C, affecting filling time (Fig. 3 and Fig. 4).
- Mould temperature can be controlled by regulating the cooling system flow (Fig. 5 and Fig. 6).
- Filling time is less in case of preheating temperature.
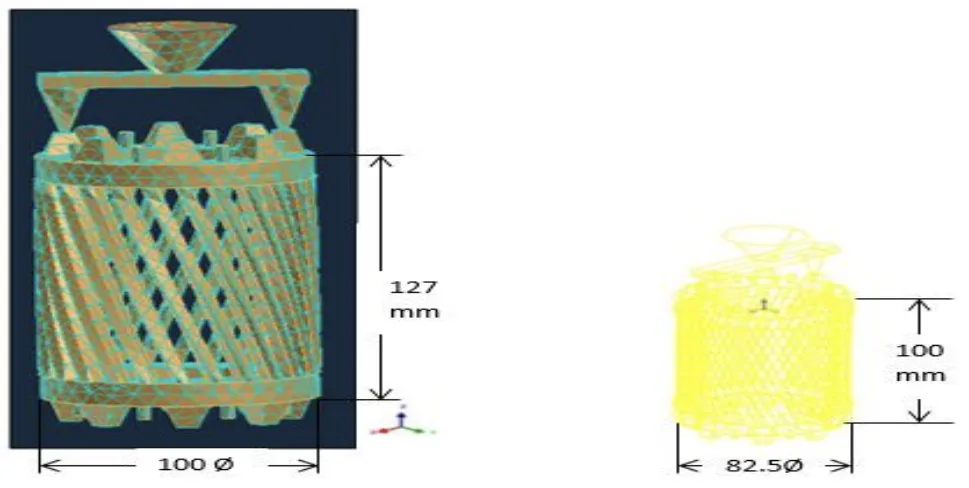
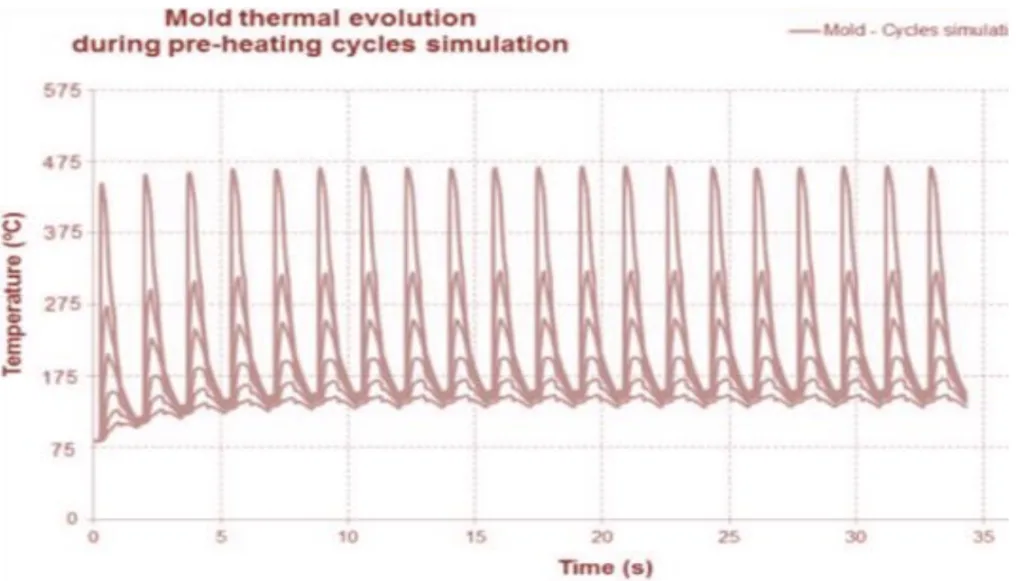
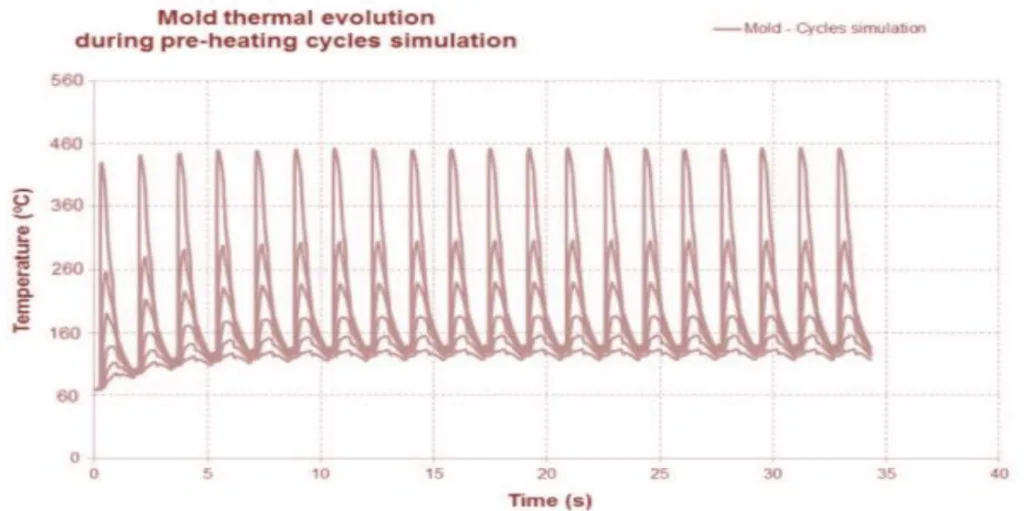
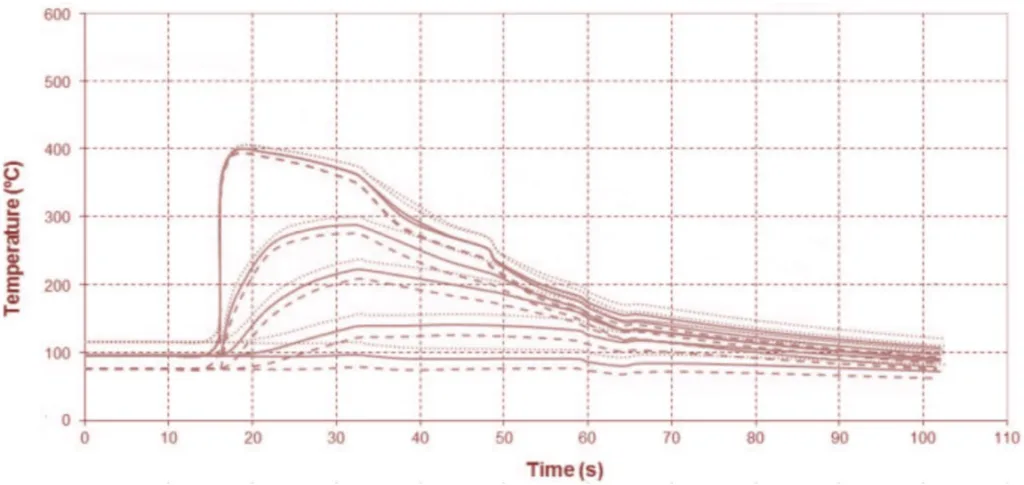
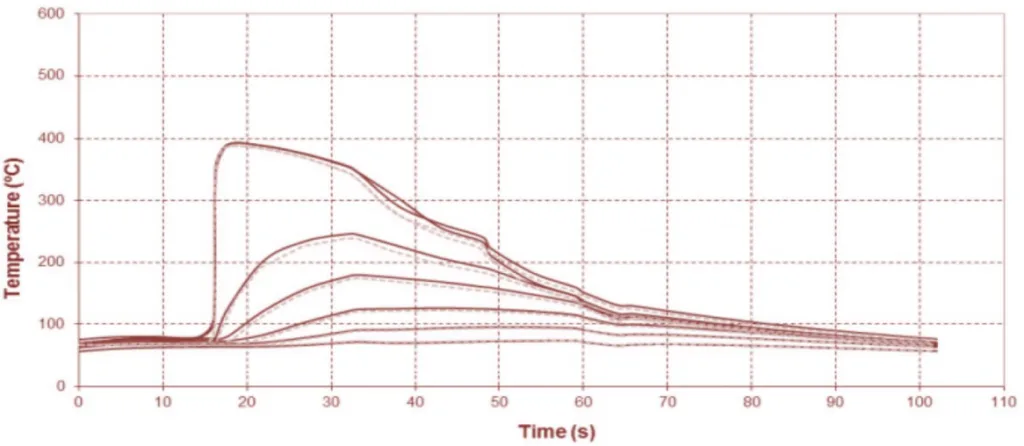
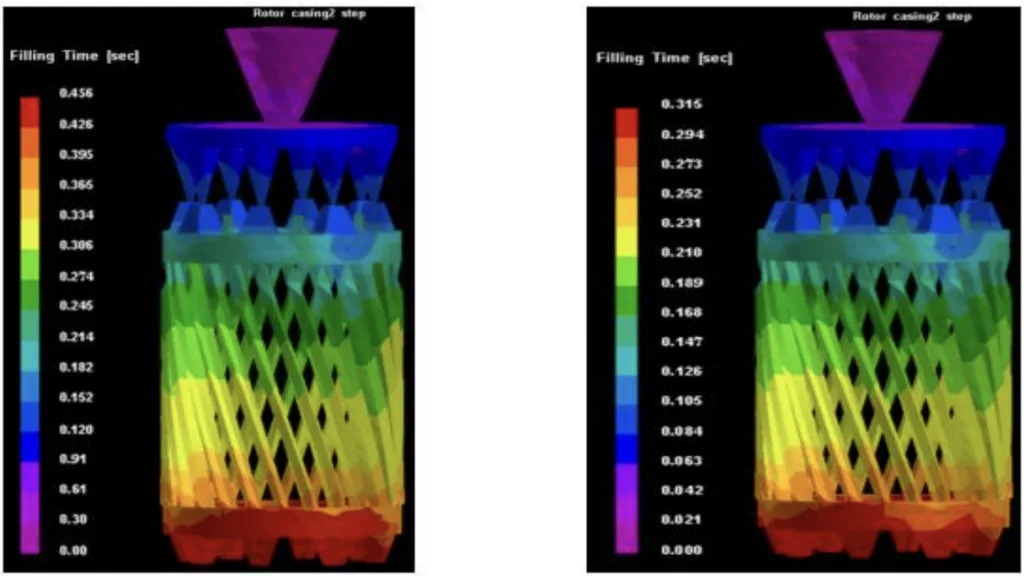
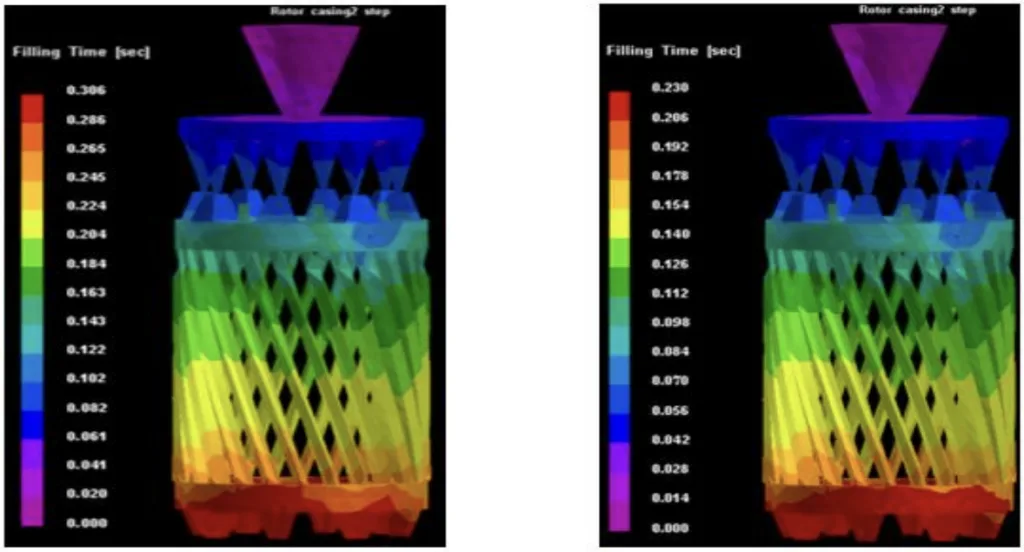
List of figure names:
- Fig 1: Cause and Effect Diagram for Casting Defects
- Fig.2: Mesh Model of the 100S and M50 Frame Rotors.
- Fig.3: Mould Thermal evolution during pre-heating of M50 Rotor cycles simulation
- Fig 4: Mould thermal evolution during pre-heating of 100S Rotor cycle simulation
- Fig 5: Mould temperature for M50 rotor
- Fig 6: Mould Temperature for 100S Rotor
- Fig 7: Simulated results for 100S rotor for filling time
- Fig 8: Simulated results for M50 rotor for filling time
7. Conclusion:
Summary of key findings:
- The thermal balance equation accurately predicts the required preheating temperature for different casting sizes.
- Filling time is reduced with preheating.
- The preheating temperature, calculated by the thermal equation, should be maintained by controlling the cooling system's flow.
- Using the heat balance equation, waste shots due to improper preheating can be eliminated.
{Summary of research results. Academic significance of the research, practical implications of the research}
The thermal balance equation is beneficial to improve the thermal parameters, predicting the defects related to the filling process, as to achieve the six sigma products.
8. References:
- [1] A.K.Sahoo, M.K. Tiwari, A.R.Mileham "Six Sigma based approach to optimize the radial forging operation Variables" journal of materials processing technology 202, pp.125-136, 2008
- [2] Jay M. Patel, Yagnang R. Pandya, Devang Sharma, Ravi C. Patel," Various Type of Defects on Pressure Die Casting for Aluminium Alloys" International Journal for Scientific Research & Development Vol. 5, Issue 01, pp 2321-0613, 2017
- [3] Santosh S. Dabhole, Chaitanya A. Kurundwad, Sujit R. Prajapati "Design, and development of die casting Die for rejection reduction" International Journal of Mechanical Engineering and Technology, Volume 8, Issue 5, May 2017, pp. 1061-1070
- [4] Case Studies of Innovative Die-casting Machines, Alessandro Benini - Italpresse, Brescia, Italy
- [5] Darina Matiskova, Stefan Gaspar and Ladislac Mura "Thermal Factors of Die Casting and Their Impact on The Service Life of Moulds and the Quality of Castings" Journal of Acta Polytechnica Hungarica, Vol.10, No. 3, 2013
- [6] Sk.Nagoor Vali, S.Sureshkumar, M.A.Athiya, K.Manigandan, and H.Fayazdeen "A review on die-casting Process parameters", International Journal of Scientific Research and Review, Vol. 7, Issue 3, 2018
- [7] Stefan Gaspar, "Technological Factors of Pressure Die Casting" Annals of faculty Engineering Hunedora, International Journal of Engineering Tome IX (the year 2011).
- [8] Xiong Shoumei, F. Lau, W.B. Lee "An efficient thermal analysis system for the die-casting process"Journal of Materials Processing Technology 128 (2002) 19-24
- [9] P.K. Seo, D.U. Kim and C.G. Kang "Effects of die shape and injection conditions proposed with Numerical integration design on liquid segregation and mechanical properties in semi-solid die casting Process" Journal of Materials Processing Technology, Vol.176, pp.45-54, 2006.
- [10] C. Mohantyl, B. K. Jena, "Optimization of Aluminium Die Casting Process Using Artificial Neural Network International Journal of Emerging Technology and Advanced Engineering (ISSN 2250-2459, Volume 4, Issue 7, July 2014)
- [11] Satish Kumar, Arun Kumar Gupta, Pankaj Chandna," Optimization of Process Parameters of Pressure Die Casting using Taguchi Methodology" World Academy of Science, Engineering and Technology Vol: 6, 2012.
- [12] Henry Hu, Fang Chen, Xiang Chen, Yeou-li Chu, Patrick Cheng, "Effect of cooling water flow rates on Local temperatures and heat transfer of casting dies, Journal of Materials Processing Technology 148(2004) 57-67
- [13] L.X. Kong, F.H. She, W.M. Gao, S. Nahavandi, P.D. Hodgson, "Integrated optimization system for high Pressure die casting processes" Journal of materials processing technology 2 01 (2 008) 629-634
- [14] Senthiil P, V. M.Chinnapandian and Sirushti, "Optimization of Process Parameters in Cold Chamber Die Casting Process Using Taguchi Method "IJISET International Journal of Innovative Science, Engineering & Technology, Vol. 1 Issue 6, August 2014.
- [15] V. E. Bazhenov, A.V. Koltygin, and A. V. Fadeev "The Use of the ProCast Software to Simulate the Process of Investment Casting of Alloy Based on Titanium Aluminide TNM_B1 into Ceramic Molds" Russian Journal of Nonferrous Metals, Vol. 55, No. 1, pp. 15-19, 2014.
- [16] Hong Yan, Wenwei Zhuang, Yong Hu, Qiansheng Zhang, Hong Jin," Numerical simulation of AZ91D Alloy automobile plug-in pressure die casting process" Journal of Materials Processing Technology 187-188 (2007) 349-353
- [17] S.M. Xiong, F. Lau, W.B. Lee, L.R. Jia, "Numerical methods to improve the computational efficiency of Thermal analysis for the die casting process" Journal of Materials Processing Technology 139 (2003) 457-461
- [18] Matthew S. Dargusch, G. Dour, N. Schauer, C.M. Dinnis, G. Savage, "The influence of pressure during Solidification of high-pressure die-cast aluminium telecommunications components' Journal of MaterialsProcessing Technology.2006
- [19] B.Kosec, G.Kosec, M. Sokovia," Temperature Field and Failure analysis of die casting die, 'International Scientific Journal, Vol.28, Issue3, 2007
9. Copyright:
- This material is a paper by "Suraj Marathe, Dr. Carmo Quadros": Based on "Thermal Factor of Aluminium High pressure Die Casting Container (Mould) to achieve Six Sigma Quality of Castings".
- Source of paper: http://www.ijert.org
This material was created to introduce the above paper, and unauthorized use for commercial purposes is prohibited. Copyright © 2025 CASTMAN. All rights reserved.