This introductory paper is the research content of the paper "Thermal challenges of Wide Band Gap power electronics component in electrical vehicle" published by ResearchGate.

1. Overview:
- Title: Thermal challenges of Wide Band Gap power electronics component in electrical vehicle
- Author: J. Hélie, J.-P. Fradin, F. Piscaglia
- Publication Year: 2022
- Published Journal/Society: Conference Paper
- Keywords: wide band gap, GaN, SiC, packaging, power electronic, cooling, heat transfer, EV, PHEV
2. Abstract
The cooling of power electronics is a fundamental for the best compromise between efficiency, compactness and cost. For the next generation of High Voltage boxes we focus here on liquid forced convection cooling. Firstly, some examples of cold plates schematics, and cold plate design constraints, are illustrated. Some potential innovation for the design of these configurations is obtained by simulations via topology optimization (TO); TO offers, thanks to the weak turbulence level, an alternative to the traditional engineer design. Secondly, the new generation of transistors adopting Wide Band Gap (SiC and GaN) material offers improved features. Also, a recent packaging strategy defined as "Top cooled" is composed of a thermal exposed pad in front of the heatsink, and not anymore onto the PCB. The packaging size is the key relevant parameter for the cooling design. The size of the exposed pad will influence both the thermal resistance of the thermal path between the die and the heatsink, and the spreading capability of the material. Finally, this influence can be analytically proved, quantified, and experimentally verified. The packaging size will also finally influence the surface of exchange with the cooling fluid, reinforcing this effect.
3. Research Background:
Background of the research topic:
The cooling of power electronic boards [1] in automotive applications, particularly High Voltage power electronic boards, is critical.
Status of previous research:
Wide Band Gap (WBG) materials like SiC and GaN offer improved features compared to traditional silicon-based devices. The Keyes merit factor [3] provides a comparison of different materials from a thermal perspective [4], showing that SiC-4H and SiC-6H perform significantly better than Silicon (Figure 3). GaN also shows potential for efficiency improvement [2]. Previous research has explored embedded die concepts [5,6] and integrated modules.
Need for research:
There is a need to optimize the cooling of power electronics for efficiency, compactness, and cost, especially with the advent of WBG materials and new packaging strategies like "Top cooled" components.
4. Research purpose and research question:
Research purpose:
To investigate the thermal challenges and design considerations for cooling WBG power electronic components in electric vehicles, focusing on liquid forced convection cooling.
Core research:
- Exploring cold plate designs and constraints.
- Investigating the impact of packaging size on thermal resistance.
- Quantifying and verifying the influence of packaging size analytically and experimentally.
- Utilizing topology optimization for innovative cooling designs.
5. Research methodology
The research employs a combination of analytical modeling, numerical simulations, and experimental validation.
- Analytical Modeling: Thermal resistance networks are used to model the heat transfer path from the junction to the cooling fluid (Equation 1). 1D models and spreading resistance calculations are employed (Equation 2).
- Numerical Simulations: Topology optimization (TO) is used for cold plate design. Multidimensional simulations, including Computational Fluid Dynamics (CFD) and heat transfer analysis, are performed. "digital twin" approach.
- Experimental Validation: Measurements are conducted on different WBG technologies and components to validate the models and simulations (Figure 7, Figure 10).
6. Key research results:
Key research results and presented data analysis:
- A trade-off exists between heat transfer coefficient and pressure drop in cold plate design (Figure 2).
- The stability of RDson versus temperature is significantly higher for SiC compared to Silicon (Figure 4).
- Top-cooled and bottom-cooled SMD component implementations have different thermal bottlenecks (Figure 5).
- The thermal resistance of the intermediate material (IM) layer is crucial (Figure 7).
- Packaging surface area significantly impacts thermal resistance (Figure 7).
- Spreading resistance needs to be considered, especially for smaller packaging sizes.
- Simulation results show good agreement with experimental data for air-cooled conditions (Figure 10).
- Topology optimization can generate innovative cold plate designs (Figure 11, Figure 13).
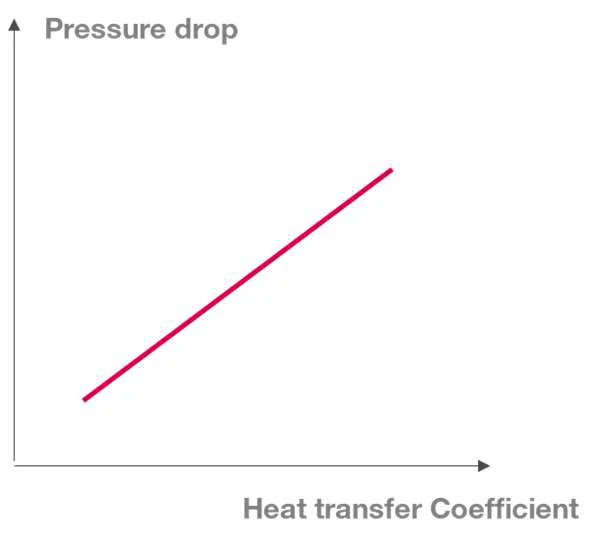
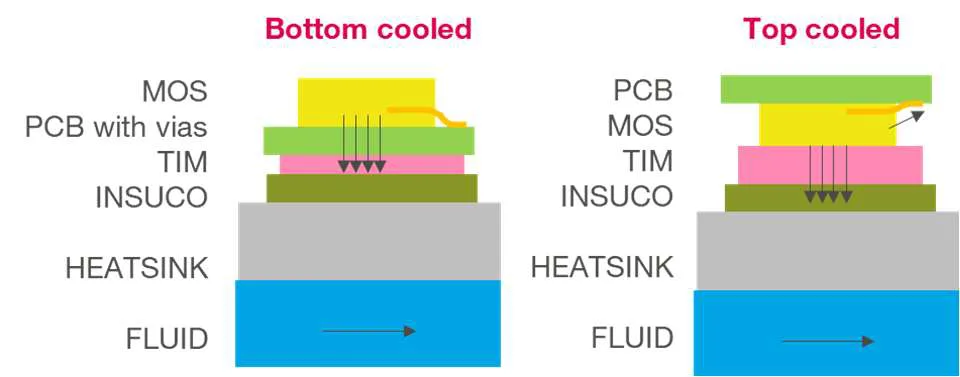
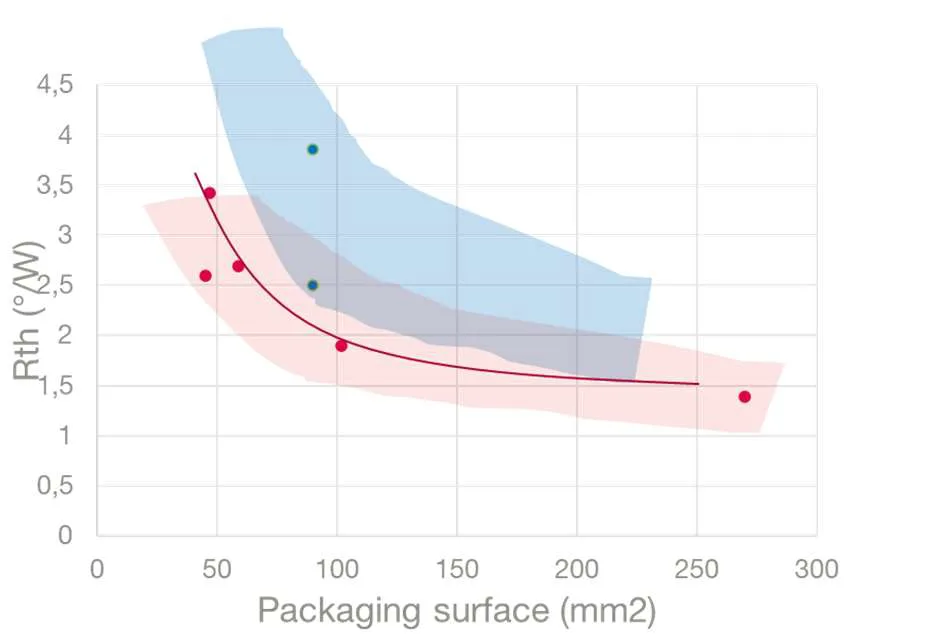
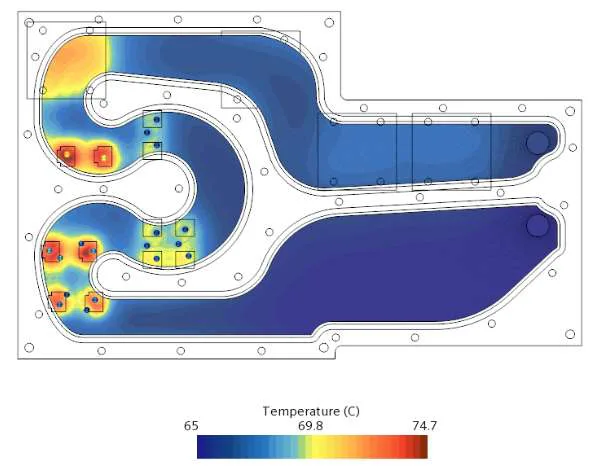
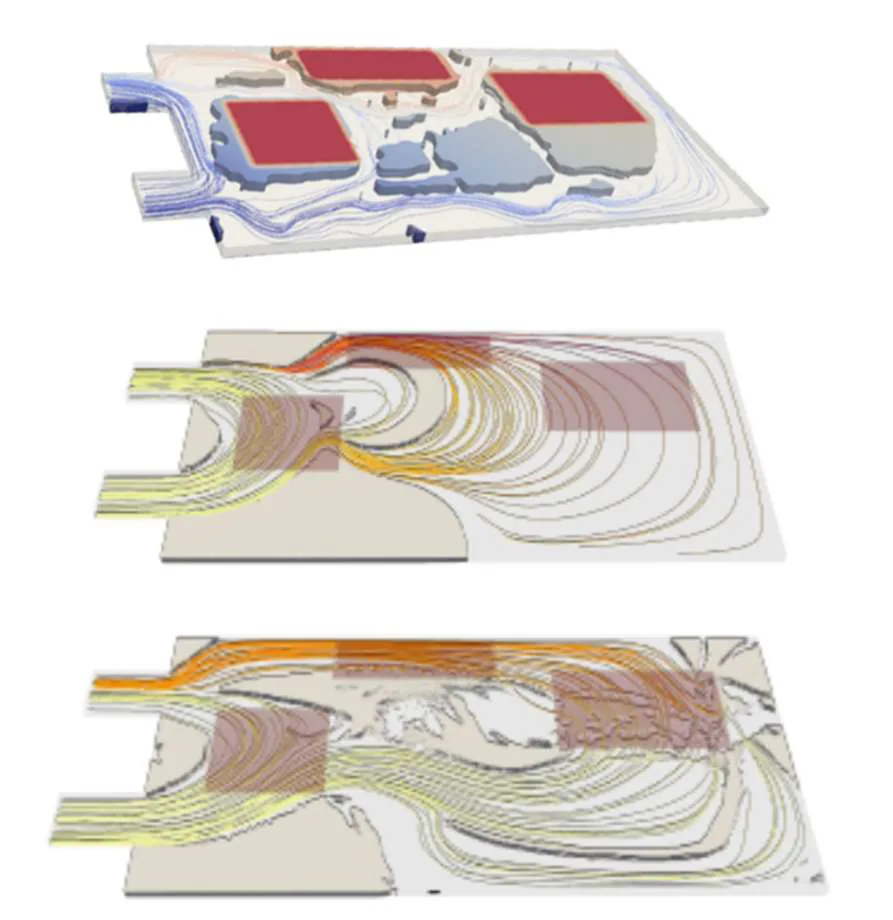
List of figure names:
- Figure 1: Typical powerelectronic stage
- Figure 2: Win/Loss trade-off
- Figure 3: Comparison of materials using Keyes Merit factor (normalised by Silicon)
- Figure 4: Comparison of materials: stability of RDson versus Temperature
- Figure 5: Bottom and Top cooled SMD mechatronic implementation
- Figure 6: Comparison of a large component and a 60mm2 Mosfet on top of a typical Pin-array cold plate. Bottom appears the pin array that is immerged in the main fluid flow.
- Figure 7: Thermal resistance for different MOSFET. Points: measurements. Line: 1D model. Semi-transparent area: range. Grey refers to bottom-cooled, pink refers to top-cooled
- Figure 8: Coupled Conduction-convection in the solid (as cold plate base). Top: Non dimensional thermal resistance. Bottom: Non dimensional temperature cone width
- Figure 9: Top: air-cooled example. Bottom: liquid-cooled example.
- Figure 10: Air-cooled example; comparison simulation/experiment
- Figure 11: liquid-cooled example; simulation prediction of skin temperature
- Figure 12: Categories of optimization approaches
- Figure 13: Proof of concept: Simulations results with 3 components. Alpha threshold is superimposed with streamlines. Top: 2D simulations extruded. Centre: 3D simulations, objective function set for pressure drop. Bottom: objective function set for component temperature.
7. Conclusion:
Summary of key findings:
WBG components are crucial for increasing power density in electric vehicle power electronics. The design of the thermal path, particularly the spreading of heat from the small thermal spot, is critical. Both traditional and innovative simulation methods, including topology optimization, can aid in cold plate design.
Summary of research results.
The research highlights the importance of packaging size and interface materials in the thermal management of WBG power electronics. It demonstrates the effectiveness of topology optimization in generating novel cooling solutions.
Academic significance of the research, practical implications of the research
The research provides valuable insights into the thermal design challenges and opportunities presented by WBG technology in electric vehicle applications. The findings can guide the development of more efficient and compact power electronics systems.
8. References:
- [1] F. Boissière, M Glötz, M Hackelsperger, K. Boukhris: "High Voltage Box for Electrified Vehicles", MTZ, 2022
- [2] G. Rösel, M. Hackelsperger, R. Knorr, J. Popov, Chr. Preis, A. Reich: "Achieving benchmark in power density and sustainability for power net, power supply and onboard chargers by a new generation of DC/DC converters and OBCs with Gallium nitride semiconductors", 2022
- [3] R. W. Keyes: "Figure of merit for semiconductors for high-speed switches", Proceedings of the IEEE, Feb. 1972
- [4] H. Okumura: "Present Status and Future Prospect of Widegap Semiconductor High-Power Devices", Japanese Journal of Applied Physics Vol. 45, No. 10A, 2006, pp. 7565-7586
- [5] M. Aussel: "CHPA : Feasibility of 'PCB with embebbed bare dies' for Electric Vehicle On Board Chargers", National Reliability Technology Workshop, Toulouse, 2021
- [6] A. Marie, J.-P. Fradin, L. Allirand, M. Aussel, P.-Y. Hamelin "Assessment of embedded GaN HEMT junction temperature measurement accuracy" THERMAL2023 : 16th European Advanced Technology Workshop on Micropackaging and thermal, March 2023
- [7] D. Schweitzer and L. Chen, "Heat spreading revisited – effective heat spreading angle," 2015 31st Thermal Measurement, Modeling & Management Symposium (SEMI-THERM), 2015
- [8] F. Ghioldi, J. Hélie, F. Piscaglia: "A Fast Computational Method for the Optimal Thermal Design of Anisotropic Multilayer Structures with Discrete Heat Sources for Electrified Propulsion Systems", International Journal of Heat and Mass Transfer, 2021
- [9] T. Q. Feng, J. L. X: "An analytical solution of thermal resistance of cubic heat spreaders for electronic cooling", Applied Thermal Engineering 24 (2-3) 2004
- [10] Pironneau O.: "On optimum design in fluid mechanics". Journal of Fluid Mechanics 1974; 64(1): 97-110
- [11] E.M. Dede: "Multiphysics Topology Optimization of Heat Transfer and Fluid Flow Systems", Proceedings of the COMSOL Conference 2009 Boston
- [12] Dwight R, Brezillon J: "Effect of Various Approximations of the Discrete Adjoint on Gradient-Based Optimization", Aerospace Sciences Meetings. American Institute of Aeronautics and Astronautics. 2006
- [13] E. Gallorini, J. Helie, F. Piscaglia: "A Thermal Adjoint-Based Solver with Adaptive Mesh Refinement For Topology Optimization", Int J. Num. Methods Fluids, 2022, submitted
9. Copyright:
- This material is a paper by "J. Hélie, J.-P. Fradin, F. Piscaglia": Based on "Thermal challenges of Wide Band Gap power electronics component in electrical vehicle".
- Source of paper: [The URL is not provided in the document.]
This material was created to introduce the above paper, and unauthorized use for commercial purposes is prohibited. Copyright © 2025 CASTMAN. All rights reserved.