This introduction paper is based on the paper "Synthesis and Characterization of SiC p Reinforced Magnesium Alloy Based Metal Matrix Composite Through Vacuum Assisted Stir Casting Process" published by "International Journal of Applied Engineering Research".
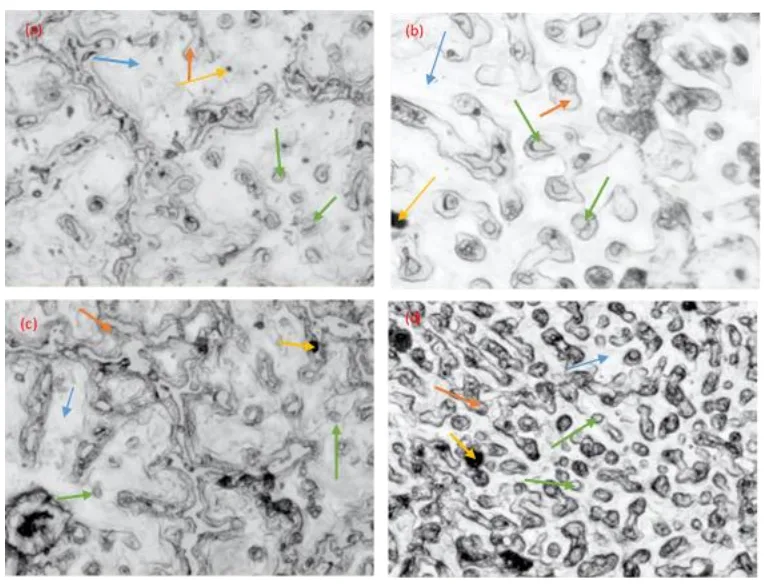
1. Overview:
- Title: Synthesis and Characterization of SiC p Reinforced Magnesium Alloy Based Metal Matrix Composite Through Vacuum Assisted Stir Casting Process
- Author: Anil Kumar, Santosh Kumar and N. K. Mukhopadhyay
- Year of publication: 2017
- Journal/academic society of publication: International Journal of Applied Engineering Research (Volume 12, Number 24 (2017) pp. 16087-16093)
- Keywords: Magnesium alloy, composite, particle reinforcement
2. Abstract:
Development of light weight material is one of the challenging task for all the engineers and scientist. The magnesium as a light weight material has limited application in pure form due to high corrosion and average mechanical properties. The alloying element has tendency to improve corrosion as well as mechanical properties of the magnesium alloy. The particle reinforced metal matrix composites of magnesium alloy is one of the solution to improve utility of the magnesium. This paper present the characterization of SiC particulate reinforced metal matrix composites, where commercial magnesium alloy (AZ91) is used as a matrix material. The microstructural examination using optical microscope and scanning electron microscope (SEM) has been performed for the composite prepared using stir casting method in inert atmosphere. The mechanical properties like tensile and hardness were examined. The yield strength, ultimate strength and tensile facto-graph are also evaluated in this study.
3. Introduction:
The production of metal matrix composites (MMCs) has seen significant enhancement due to their attractive properties compared to monolithic materials. There is an increasing demand for lightweight materials across various engineering fields, including automobile, aerospace, sports, electronics, and medical applications. Magnesium stands out as a promising lightweight structural metal, being even lighter than aluminum, with a density of 1.74 g/cm³. However, pure magnesium suffers from high corrosion rates and poor mechanical properties, which limits its direct application. Magnesium alloys are therefore used to improve these characteristics.
Magnesium alloy based MMCs offer the dual benefits of light weight and enhanced mechanical properties. The addition of particulate reinforcements, such as ceramic particles like SiC, Al2O3, TiC, and MgO, can significantly improve the stiffness and strength of magnesium alloys, both at room and elevated temperatures. Various fabrication techniques are available for producing MMCs, including stir casting, gas infiltration, powder metallurgy, squeeze casting, spray deposition, injection moulding, and in-situ techniques. Among these, stir casting is considered one of the most economical processes for the production of magnesium alloy based MMCs. This study focuses on the synthesis and characterization of SiCp reinforced AZ91 magnesium alloy composites produced by vacuum assisted stir casting.
4. Summary of the study:
Background of the research topic:
The engineering demand for lightweight materials is continuously growing, driven by benefits such as improved energy efficiency and performance. Magnesium, as the lightest structural metal, offers substantial weight reduction potential. However, its inherent limitations like poor corrosion resistance and mechanical properties in pure form necessitate alloying and the development of composites. Magnesium-based Metal Matrix Composites (MMCs) reinforced with ceramic particulates like Silicon Carbide (SiC) provide a pathway to enhance mechanical properties such as stiffness and strength while maintaining low density.
Status of previous research:
Extensive research has been conducted on magnesium MMCs, exploring various reinforcement materials (e.g., SiC, Al2O3) and fabrication methods. Common manufacturing techniques include stir casting, powder metallurgy, squeeze casting, and spray forming. Stir casting is widely recognized for its cost-effectiveness and scalability in producing particulate reinforced MMCs. Previous studies have highlighted the influence of reinforcement type, size, volume fraction, and processing parameters on the microstructure and mechanical behavior of magnesium composites.
Purpose of the study:
The primary purpose of this study was to synthesize SiC particulate (SiCp) reinforced AZ91 magnesium alloy metal matrix composites using a vacuum assisted stir casting process. The research aimed to systematically investigate and characterize the effect of varying weight percentages of SiC particles (3%, 6%, 9%, and 12%) on the microstructure and mechanical properties (specifically tensile strength, yield strength, and hardness) of the AZ91 alloy. Additionally, the study sought to evaluate the fracture behavior of the developed composites.
Core study:
The core of this study involved the fabrication of AZ91 magnesium alloy matrix composites reinforced with different weight percentages (3, 6, 9, and 12 wt%) of SiC particles, having an average particle size of 20 microns. The fabrication was carried out using a vacuum assisted stir casting method. Subsequent characterization included:
- Microstructural analysis of the unreinforced AZ91 alloy and the SiCp reinforced composites using optical microscopy (OM) and scanning electron microscopy (SEM) coupled with Energy Dispersive X-ray Spectroscopy (EDS).
- Mechanical property evaluation through:
- Tensile testing at room temperature to determine yield strength and ultimate tensile strength.
- Vickers micro-hardness and macro-hardness tests to assess the hardness and the homogeneity of reinforcement distribution.
- Analysis of tensile fracture surfaces using SEM to understand the fracture mechanisms in the composites.
5. Research Methodology
Research Design:
This study utilized an experimental research design to synthesize and characterize SiCp reinforced AZ91 magnesium alloy MMCs. The independent variable was the weight percentage of SiC particle reinforcement (0%, 3%, 6%, 9%, and 12%), and the dependent variables were the microstructural features and mechanical properties of the composites.
Data Collection and Analysis Methods:
- Materials: Commercial magnesium alloy AZ91D served as the matrix material. The elemental composition of the as-received AZ91D alloy is detailed in Table 1 of the original paper. Silicon carbide (SiC) particles with an average particle size of 20 microns were used as the reinforcement.
- Composite Fabrication: Metal matrix composites were fabricated by melting the AZ91 alloy in a metallic crucible within an electric resistance furnace at 700°C. Four different weight percentages of SiC particles (3, 6, 9, and 12 percent) were added to the matrix material using a vacuum assisted stir casting technique. The melt was held at 700°C for 20 minutes and then stirred mechanically for 15 minutes. The molten composite material was subsequently poured into a die through a bottom pouring facility in an inert atmosphere to minimize porosity.
- Microstructural Characterization: Samples for microstructural observation were sectioned from the die-cast composites, followed by mechanical grinding and polishing. The mirror-polished samples were etched for 5 seconds using an etchant prepared by mixing ethyl glycol, distilled water, and nitric acid in the ratio of 75:24:1. The microstructure was examined using a Leica optical microscope (OM) and a scanning electron microscope (SEM) equipped with EDS for surface topography and elemental composition analysis.
- Mechanical Testing:
- Tensile Testing: Tensile tests were performed on SiCp reinforced MMCs and the unreinforced AZ91 alloy to evaluate their mechanical properties. Tensile samples with a gauge length of 20 mm and a gauge diameter of 8 mm were prepared according to the ASTM E8/E8M standard. Tests were conducted at room temperature on an Instron-4208 universal testing machine at an initial strain rate of 0.005 s⁻¹.
- Hardness Testing: Vickers micro-hardness tests were performed across the section of polished composites using a load of 1.0 kgf with a dwell time of 10 seconds. Macro-hardness tests were also conducted on the composites using a load of 3 kgf with a dwell time of 10 seconds. A LECO'S LV Series Macro-Vickers Hardness machine was used for these tests.
- Fracture Surface Analysis: The tensile fracture surfaces of the AZ91/SiC particulate composites were analyzed by SEM to study the morphology of the fractured surfaces.
Research Topics and Scope:
The research focused on the synthesis of AZ91/SiCp MMCs with varying SiC content (0 wt% to 12 wt%). The scope included the characterization of the resulting microstructures, specifically focusing on grain refinement and SiC particle distribution. The study investigated key mechanical properties such as yield strength, ultimate tensile strength, and Vickers hardness (both micro and macro). A significant part of the scope was to analyze the relationship between the SiC content, the observed microstructure, and the resultant mechanical properties, as well as to examine the tensile fracture behavior of these composites.
6. Key Results:
Key Results:
- Microstructure:
- Optical microscopy revealed that the addition of SiC particles led to a decrease in the grain size of the magnesium alloy matrix, indicating grain refinement (Figure 1).
- FE SEM micrographs showed that the distribution of SiC particles in the magnesium alloy was almost uniform (Figure 2).
- Sound castings were observed, with no significant gas inclusions or porosity in the cast microstructure of the magnesium alloy composites.
- Yield Strength:
- The yield strength of the AZ91 alloy was 119.94 MPa. Upon addition of SiC reinforcement, the yield strength of the composites initially decreased (e.g., 57 MPa for 3% SiC). However, the yield strength of the composites increased with increasing SiC percentage from 3% to 9%. The highest yield strength among the AZ91/SiC composites was 105.44 MPa, observed for the 9% SiC reinforced composite. The 12% SiC composite showed a yield strength of 79 MPa (Figure 3).
- Ultimate Tensile Strength (UTS):
- The UTS of the unreinforced AZ91 alloy was found to be 187.67 MPa.
- The UTS of the SiC particulate reinforced composites generally increased with an increasing percentage of SiC reinforcement. The highest UTS value of 193.96 MPa was recorded for the composite containing 12% SiC (Figure 4).
- Vickers Hardness:
- The average micro-Vickers hardness of the composites increased with an increasing volume fraction of SiC particle reinforcement. The highest average micro-Vickers hardness was 107 HV for the 12% SiC/AZ91 composite (Figure 6).
- The macro-Vickers hardness (measured at 3 kgf load) also increased with increasing SiC particle content (Figure 7).
- Macro-Vickers hardness values were generally higher than micro-Vickers hardness values for the same composite, attributed to more reinforced particles resisting indentation at higher loads.
- Fracture Behavior:
- SEM analysis of the tensile fracture surfaces (Figure 8.a - 8.d) indicated that the fracture behavior of the magnesium matrix in AZ91/SiC composites was a combination of brittle and ductile features.
- As the percentage of SiC increased, the dimple size in the fractured surface decreased. The morphology also revealed an increase in small size dimples, cracks, shrinkage porosity, and cleavage fracture with increasing volume fraction of reinforcement, suggesting that the composite materials became more brittle and less ductile.
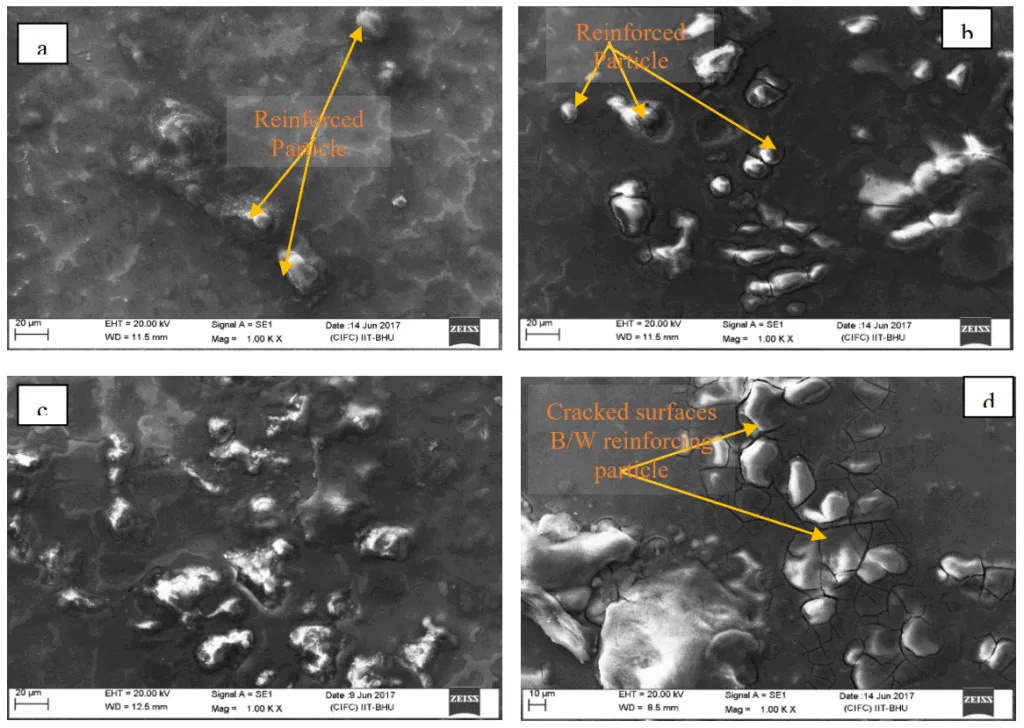
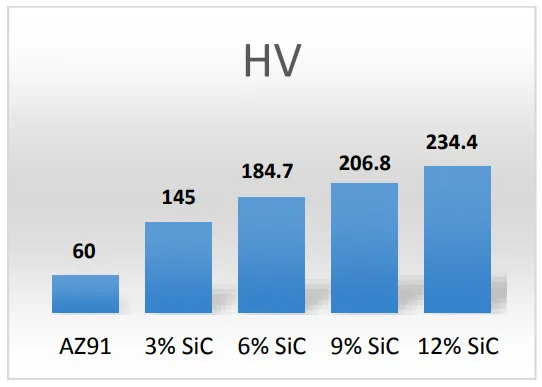
Figure Name List:
- Figure 1. Optical Micrograph (a)3% SiC in AZ91(b)6% SiC in AZ91(c)9% SiC in AZ91(d)12% SiC in AZ91
- Figure 2. Scanning Electron Micrograph (a)3% SiC in AZ91(b)6% SiC in AZ91(c)9% SiC in AZ91(d)12% SiC in AZ91
- Figure 3. Yield Strength of Magnesium Alloy
- Figure 4. Ultimate Tensile strength with different percentage of SiC
- Figure 5. Vickers Hardness Value at different position of the composite (a) 3% SiC in AZ91 (b) 6% SiC in AZ91 (c) 9% SiC in AZ91 (d) 12% SiC in AZ91
- Figure 6. Comparison of average micro -Vickers hardness of composites with AZ91
- Figure 7. Comparison of average macro -Vickers hardness of composites with AZ91
- Figure 8. Tensile facture of the composite (a) 3% SiC in AZ91 (b) 6% SiC in AZ91 (c) 9% SiC in AZ91 (d) 12% in AZ91
(Note: Table 1. Elemental Composition of alloy AZ91 is presented in the original paper and provides the chemical composition of the matrix material.)
7. Conclusion:
The following conclusions are extracted from the experimental analysis and characterization of AZ91/SiC metal matrix composites.
- On addition of hard reinforcement the yield strength of the materials (AZ91) decreases but yield strength increases as the percentage of SiC particulate increases. The highest value of yield strength is 105.44 M Pa for AZ91/SiC composites.
- The ultimate tensile strength is also increases with increase in percentage of reinforcement. The highest value of ultimate tensile strength is 193.96 M Pa for 12% SiC reinforced composite.
- The micro Vickers hardness value is not uniform throughout the surface of the composite, but the average micro hardness value increases with increase in percentage of SiC particulate in AZ91 metal matrix. The highest value of micro Vickers hardness is 107 HV for 12% SiC/AZ91 composite.
- The macro Vickers hardness value is higher than micro Vickers hardness because at higher load (i.e.3 kgf) the indentation area was more and in this case more number of the reinforced particle resist indentation.
- The facto-graphy of the tensile sample reveals that the composite materials is more brittle and less ductile because the dimple was very small in size and more number of cracks and cleavage fracture.
8. References:
- [1] J. F. King, “Magnesium: commodity or exotic?,” Mater. Sci. Technol., vol. 23, no. 1, pp. 1–14, 2007.
- [2] W. D. Callister "Materials Science and Engineering: An introduction". New York: Wiley, 2003
- [3] S. Jayalakshmi, S. V. Kailas, and S. Seshan, "Tensile behaviour of squeeze cast AM100 magnesium alloy and its Al2O3 fibre reinforced composites," Compos. Part A Appl. Sci. Manuf., vol. 33, no. 8, pp. 1135-1140, 2002.
- [4] M. Avedesian and H. Baker, “ASM Specialty Handbook:Magnesium and Magnesium Alloys,” ASM International, Materials Park, OH. p. 314, 1999.
- [5] S. F. Hassan and M. Gupta, “Development of high strength magnesium based composites using elemental nickel particulates as reinforcement,” J. Mater. Sci., vol. 37, no. 12, pp. 2467–2474, 2002.
- [6] B. L. Mordike and T. Ebert, "Magnesium Properties - applications - potential," Mater. Sci. Eng. A, vol. 302, no. 1, pp. 37-45, 2001.
- [7] K. Ponappa, S. Aravindan, and P. V. Rao, “Influence of Y2 O 3 particles on mechanical properties of magnesium and magnesium alloy (AZ91D),” J. Compos. Mater., vol. 47, no. 10, pp. 1231-1239, 2013.
- [8] K. Ponappa, S. Aravindan, and P. V. Rao, "Grinding of magnesium /Y 2 O 3 metal matrix composites," Proc. Inst. Mech. Eng. Part B J. Eng. Manuf., vol. 226, no. 10, pp. 1675-1683, 2012.
- [9] L. Lu, K. K. Thong, and M. Gupta, "Mg-based composite reinforced by Mg2Si," Compos. Sci. Technol., vol. 63, no. 5, pp. 627-632, 2003.
- [10] X. Zhang, Q. Zhang, and H. Hu, “Tensile behaviour and microstructure of magnesium AM60-based hybrid composite containing Al2O3 fibres and particles,” Mater. Sci. Eng. A, vol. 607, pp. 269–276, 2014.
- [11] D. Lu, Y. Jiang, and R. Zhou, "Wear performance of nano-Al2O3 particles and CNTs reinforced magnesium matrix composites by friction stir processing,” Wear, vol. 305, no. 1-2, pp. 286-290, 2013.
- [12] M. Paramsothy, X. H. Tan, J. Chan, R. Kwok, and M. Gupta, "Al2O3 nanoparticle addition to concentrated magnesium alloy AZ81: Enhanced ductility,” J. Alloys Compd., vol. 545, pp. 12–18, 2012.
- [13] H. Ferkel and B. L. Mordike, “Magnesium strengthened by SiC nanoparticles," Mater. Sci. Eng. A, vol. 298, no. 1–2, pp. 193–199, 2001.
- [14] M. Gui, J. Han, and P. Li, "Fabrication and Characterization of Cast Magnesium Matrix Composites by Vacuum Stir Casting Process,” J. Mater. Eng. Perform., vol. 12, no. 2, pp. 128–134, 2003.
- [15] H.P. Degischer, P.A. Schulz, W. Lacom, "Properties of continuous fibre reinforced Al and Mg-matrix composites produced by gas pressure infiltration”. Key Eng Mater;127-131:99-110,1996
- [16] K. S. Tun and M. Gupta, “Improving mechanical properties of magnesium using nano-yttria reinforcement and microwave assisted powder metallurgy method,” Compos. Sci. Technol., vol. 67, no. 13, pp. 2657–2664, 2007.
- [17] Y. B. LIU, S. C. LIM, L. LU, and M. O. LAI, “Recent development in the fabrication of metal matrix-particulate composites using powder metallurgy techniques,” J. Materals Sci., vol. 29, pp. 1999–2007, 1994.
- [18] H. Hu, "Squeeze casting of magnesium alloys and their composites". J Mater Sci; 33:1579-89, 1998.
- [19] H. Z. Ye and X. Y. Liu, "Review of recent studies in magnesium matrix composites," J. Mater. Sci., vol. 39, pp. 6153-6171, 2004.
- [20] N. H. Loh, S. B. Tor, and K. A. Khor, “Production of metal matrix composite part by powder injection molding," J. Mater. Process. Technol., vol. 108, no. 3, pp. 398-407, 2001.
- [21] H. Y. Wang, Q. C. Jiang, X. L. Li, and J. G. Wang, “In situ synthesis of TiC/Mg composites in molten magnesium," Scr. Mater., vol. 48, no. 9, pp. 1349-1354, 2003.
- [22] L. H. Dai, Z. Ling, and Y. L. Bai, “Size-dependent inelastic behavior of particle-reinforced metal-matrix composites," Compos. Sci. Technol., vol. 61, no. 8, pp. 1057-1063, 2001.
- [23] T. W. Clyne and P. J. Withers, “An Introduction to Metal Matrix Composites" Cambridge: Cambridge University Press, 1993
- [24] C. S. Goh, J. Wei, L. C. Lee, and M. Gupta, "Development of novel carbon nanotube reinforced magnesium nanocomposites using the powder metallurgy technique,” Nanotechnology, vol. 17, no. 1, pp. 7-12, 2006.
- [25] M. Kouzeli and A. Mortensen, “Size dependent strengthening in particle reinforced aluminium," Acta Mater., vol. 50, no. 1, pp. 39–51, 2002.
- [26] Z. Zhang and D. L. Chen, “Consideration of Orowan strengthening effect in particulate-reinforced metal matrix nanocomposites: A model for predicting their yield strength,” Scr. Mater., vol. 54, no. 7, pp. 1321–1326, 2006.
- [27] R. J. Arsenault and N. Shi, "Dislocation generation due to differences between the coefficients of thermal expansion," Mater. Sci. Eng., vol. 81, no. C, pp. 175-187, 1986.
- [28] V. C. Nardone and K. M. Prewo, "On the strength of discontinuous silicon carbide reinforced aluminum composites," Scr. Metall., vol. 20, no. 1, pp. 43-48, 1986.
- [29] N. Ramakrishnan, "An analytical study on strengthening of particulate reinforced metal matrix composites," Acta Mater., vol. 44, no. 1, pp. 69–77, 1996.
- [30] X. L. Zhong, W. L. E. Wong, and M. Gupta, "Enhancing strength and ductility of magnesium by integrating it with aluminum nanoparticles," Acta Mater., vol. 55, no. 18, pp. 6338-6344, 2007.
- [31] A. Luo, “Processing, microstructure, and mechanical behavior of cast magnesium metal matrix composites," Metall. Mater. Trans. A Phys. Metall. Mater. Sci., vol. 26A, no. 9, pp. 2445–2455, 1995.
- [32] X. J. Wang, K. B. Nie, X. J. Sa, X. S. Hu, K. Wu, and M. Y. Zheng, "Microstructure and mechanical properties of SiCp/MgZnCa composites fabricated by stir casting," Mater. Sci. Eng. A, vol. 534, pp. 60-67, 2012.
9. Copyright:
- This material is a paper by "Anil Kumar, Santosh Kumar and N. K. Mukhopadhyay". Based on "Synthesis and Characterization of SiC p Reinforced Magnesium Alloy Based Metal Matrix Composite Through Vacuum Assisted Stir Casting Process".
- Source of the paper: https://www.researchgate.net/publication/325660679
This material is summarized based on the above paper, and unauthorized use for commercial purposes is prohibited.
Copyright © 2025 CASTMAN. All rights reserved.