This introductory paper is the research content of the paper "Study of Process Parameters in High Pressure Die Casting" published by International Journal of Science and Research (IJSR).
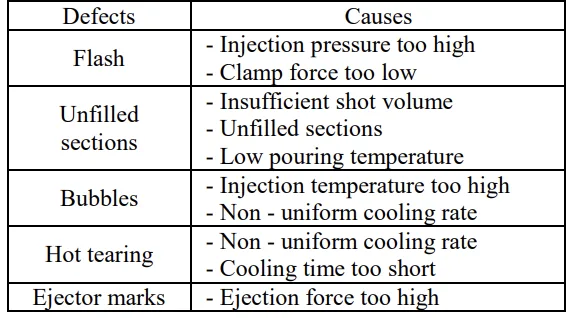
1. Overview:
- Title: Study of Process Parameters in High Pressure Die Casting
- Authors: Amitkumar Advekar, Y. Arunkumar, M. S. Srinath
- Publication Year: 2022
- Published Journal/Society: International Journal of Science and Research (IJSR)
- Keywords: High pressure die casting (HPDC), HPDC products, Process parameters, Improved quality, Quality castings, Productivity, Casting Defects.
2. Abstract
A study has been carried out for the die casting process parameters in order to achieve the improved quality of high pressure die casting (HPDC) products, which is the challenge for the small and large scale manufacturers of HPDC products. Aluminum Silicon alloys are the most extensively used, Aluminium alloys are widely used in high - pressure die casting (HPDC) of automotive components. Several process parameters need to be controlled during HPDC in order to obtain sound and reliable castings.. The objective was to reduce the defects in the components to obtain the good quality castings and increase productivity. The porosity is the most common defect frequently encountered in aluminium high pressure die castings, which increases the rejection rate and scrap rate and reduces the productivity. Porosity formation is closely related to die casting process. In this paper the effect of process parameters on porosity formation in HPDC have been presented.
3. Research Background:
Background of the research topic:
High Pressure Die Casting (HPDC) is a metal casting process characterized by forcing molten metal under high pressure into a mold cavity. It is used extensively for manufacturing non-ferrous metal parts, especially with zinc, copper, aluminum, and magnesium alloys [1]. The process is known for its ability to produce castings with very good surface finish and dimensional consistency [1].
Status of previous research:
The document cites several previous works related to HPDC, including studies on process parameter optimization using Taguchi methods [2, 6, 7], minimization of casting defects [3], numerical optimization of casting [4], and general reviews of casting defects and remedies [5].
Need for research:
The need for this research stems from the challenge of achieving improved quality in HPDC products, particularly in reducing defects like porosity, which is a common problem in aluminum high-pressure die castings. This defect impacts productivity and increases rejection and scrap rates.
4. Research purpose and research question:
Research purpose:
The purpose of this research is to study the process parameters in HPDC to improve the quality of castings and reduce defects, specifically porosity.
Core research:
The core research focuses on presenting the effects of process parameters on porosity formation in HPDC.
5. Research methodology
The research methodology is implied to be a review and presentation of existing literature. The paper reviews and discusses various aspects of:
- HPDC process.
- Advantages and Disadvantages.
- Common defects.
- Critical process parameters.
- Casting materials.
- Mold materials.
6. Key research results:
Key research results and presented data analysis:
The key results presented are a compilation of information from various sources, including:
- Description of the HPDC process: The paper describes the three phases of the cold chamber HPDC process (Fig 1.1) [11].
- Advantages of HPDC: Including excellent dimensional accuracy, smooth surfaces, and high production rates [1].
- Common defects and their causes: A table (Table 2.1) lists common defects like flash, unfilled sections, bubbles, hot tearing, and ejector marks, along with their potential causes [3].
- Classification of defects: Defects are categorized as surface and sub-surface defects.
- Critical process parameters: These include flash, cast material, mold material, pouring temperature, flow temperature, solidification time, and shrinkage/porosity [2, 3].
- Casting materials: Discussion of aluminum, zinc, magnesium, and copper-base alloys [10, 7].
- Mold materials: Description of using hardened tool steel dies [1].
- Influence of process parameters: Detailed discussion on the effects of parameters like pouring temperature and solidification time on casting quality.
- Shrinkage and porosity defect: The paper describes the reason and improvement of shrinkage porosity. (Fig 3.2)
![Figure 1.1: Different phases of die casting with a cold
chamber machine: (a) Moulding die is closed, (b) The short
plunger forces the melt into the mould, (c) Moulding die is
opened [11].](https://castman.co.kr/wp-content/uploads/image-1630-png.webp)
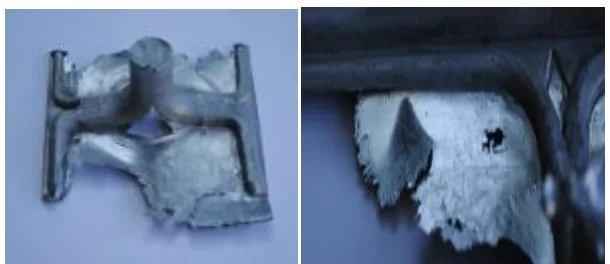
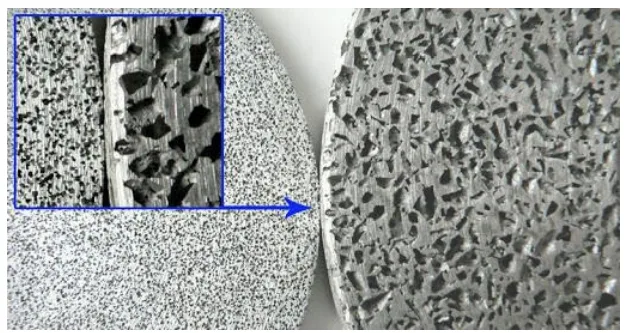
List of figure names:
- Figure 1.1: Different phases of die casting with a cold chamber machine.
- Figure 3.1: Flash.
- Figure 3.2: Shrinkage and porosity defect.
7. Conclusion:
Summary of key findings:
The paper provides a detailed overview of process parameters in HPDC, including their advantages, disadvantages, and common defects like shrinkage and porosity. It emphasizes that casting defects are a serious concern in the manufacturing industry. The paper concludes that a thorough understanding and control of process parameters are crucial for minimizing defects and achieving high-quality HPDC products. The study highlights the need for validation through experimental methods. It also notes that higher temperatures can lead to rough casting surfaces and defects like blow holes.
8. References:
- [1] Franco Bonollo, Nicola Gramegna And Giulio Timelli1, High - Pressure Die - Casting: Contradictions and Challenges, JOM: the journal of the Minerals, Metals & Materials Society (TMS) JOM, Vol.67, No.5, May 2015, ISSN 1047 - 4838.
- [2] Mahesh N Adke Shrikant V Karanjkar, Optimization of die casting process parameters to identify optimized level for cycle time using Taguchi method, International Journal of Engineering Research and General Science Volume 3, Issue 2, March - April, 2015, ISSN 2091 - 2730.
- [3] Beeresh chatrad1, Nithin Kammar2, Prasanna P Kulkarni3, Srinivas patil4, A Study on Minimization of Critical Defects in Casting Process Considering Various Parameters, International Journal of Innovative Research in Science, Engineering and Technology Vol.5, Issue 5, May 2016.
- [4] Umesh S. Patill, Dr. K. H. Inamdar2, Numerical Optimization of Casting for Defects Analysis and Minimization, A Review. IJARSE, Volume No.06, Issue No.10, October 2017.
- [5] Vaibhav Inglel Madhukar Sorte2, Defects, Root Causes in Casting Process and Their Remedies: Review, Vaibhav Ingle. Int. Journal of Engineering Research and Application ISSN: 2248 - 9622, Vol.7, Issue 3, (Part - 3) March 2017, pp.47 - 54.
- [6] Senthiil, P. V., M. Chinnapandian and Aakash Sirusshti, Optimization of Process Parameters In Cold Chamber Die Casting Process Using Taguchi Method, International Journal of Innovative Science, Engineering & Technology, Vol.1 Issue 6, August 2014.
- [7] Md Ainul Haquel, Prof Babuli Kumar Jena2,, Prof Dilip Kumar Mohanta3, Optimization of process parameters in cold chamber Pressure die casting using DOE, International Research Journal of Engineering and Technology (IRJET) e ISSN: 2395-0056, Volume: 04 Issue: 04 | Apr - 2017.
- [8] Utkarsh S. Khadel, Vishwajit Nimbalkar2, Application of 3D Cad Modeling and Casting Simulation to Eliminate Casting Defects, IJRAT, ISSN; 2321 9637, Special Conference NCMMM - 2016, 19 March 2016.
- [9] Dr. B. Ravi, Computer - aided Casting Design and Simulation, STTP, V. N. I. T. Nagpur, July 21, 2009.
- [10] Lus, H. M., 2011. Effect of casting parameters on the microstructure and mechanical properties of squeeze cast A380 aluminum die cast alloy", Yildiz Technical University, Department of Metallurgical and Materials Engineering, Istanbul, 34210 Turkey November 2011.
- [11] URL: http: //www.chemtrend. com/material/alloys_metals/aluminum, accessed on 1/9/2014.
9. Copyright:
- This material is a paper by "Amitkumar Advekar, Y. Arunkumar, M. S. Srinath": Based on "Study of Process Parameters in High Pressure Die Casting".
- Source of paper: [DOI: 10.21275/SR22609200329]
This material was created to introduce the above paper, and unauthorized use for commercial purposes is prohibited. Copyright © 2025 CASTMAN. All rights reserved.