This article introduces the paper ['Solute micro-segregation profile and associated precipitation in cast Al-Mg-Si alloy'] presented at the ['Philosophical Magazine']
1. Overview:
- Title: Solute micro-segregation profile and associated precipitation in cast Al-Mg-Si alloy
- Author: Artenis Bendo, Jonathan Fellowes, Matthew Smith, Masoud Moshtaghi, Zelong Jin, Kenji Matsuda, Zhongyun Fan & Xiaorong Zhou
- Publication Year: 2024
- Publishing Journal/Academic Society: Philosophical Magazine
- Keywords: aluminium alloy; casting; segregation; intermetallic phases; precipitation; transmission electron microscopy

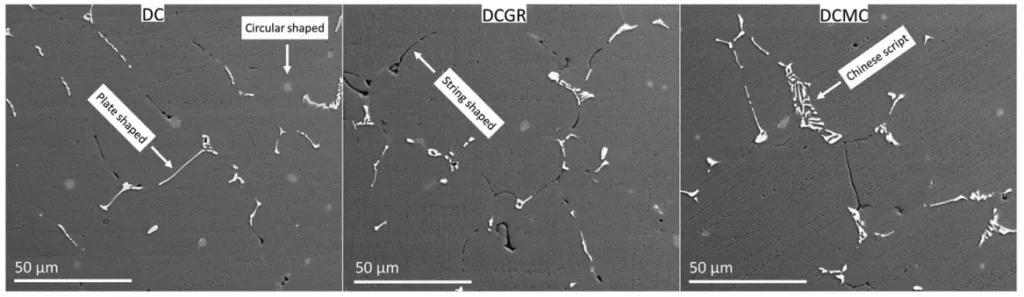
2. Research Background:
Background of the Research Topic:
Solute segregation is an inherent phenomenon during the solidification process of aluminium alloys. This is primarily attributed to non-equilibrium conditions arising from rapid cooling rates, a characteristic of many casting processes [1]. The advancing solid/liquid interface during solidification leads to a continuous build-up of solute in the melt [2]. The partition coefficient of each element dictates its preferential enrichment in either the solid or liquid phase during this process.
Status of Existing Research:
Prior investigations into macro-segregation within cast Al-Mg-Si alloys have indicated a depletion of Mg and Si at the billet's center and enrichment near the surface [5], a phenomenon termed negative centreline segregation. Furthermore, research has suggested the presence of metastable β' and stable β phases, alongside Fe-rich intermetallics, within micro-segregated regions of Al-Mg-Si alloys [6–8,10,11]. However, a gap in the existing literature pertains to the detailed concentration gradients and atomic-scale structures within these micro-segregation bands.
Necessity of the Research:
Al-Mg-Si alloys are increasingly critical in the manufacturing of vehicle components [12], with AA6082 aluminium alloy demonstrating exceptional mechanical performance when subjected to conventional down-stream thermomechanical treatments [13]. Industry trends are shifting towards utilizing parts directly in their as-cast condition to reduce manufacturing costs associated with down-stream thermomechanical processes. The precipitation of strengthening phases in wrought Al-Mg-Si alloys is critically dependent on Mg and Si solute elements, the concentrations of which are significantly influenced by micro-segregation profiles. Therefore, a comprehensive understanding of the structure of these segregation bands is paramount.
3. Research Purpose and Research Questions:
Research Purpose:
This research aims to elucidate the nature of micro-segregation in as-cast AA6082 aluminium alloy by differentiating between major and minor micro-segregation. The primary focus is to characterize the microstructure of minor micro-segregation bands, specifically investigating their distribution patterns, concentration gradients, and nano-structures. Furthermore, the study seeks to clarify the relationship between minor and major micro-segregation bands.
Key Research:
- Detailed characterization of the microstructure within minor micro-segregation bands.
- Analysis of distribution patterns and concentration gradients of solute elements within these bands.
- Investigation of the nano-structures present in minor micro-segregation bands.
- Elucidation of the relationship between minor micro-segregation bands and major micro-segregation features.
Research Hypotheses:
While not explicitly stated as formal hypotheses, the research operates on the premise that micro-segregation in as-cast AA6082 can be effectively categorized into major and minor types, each with distinct characteristics and formation mechanisms. A central tenet is that a detailed understanding of minor micro-segregation bands is crucial for controlling and optimizing the precipitation of strengthening phases, thereby influencing the final material properties.
4. Research Methodology
Research Design:
The study employed an experimental research design, utilizing as-cast AA6082 aluminium alloy samples produced via three distinct casting processes: conventional direct chill casting (DC), direct chill casting with grain refiners (DCGR), and direct chill casting with melt conditioning (DCMC). This comparative approach allowed for the investigation of micro-segregation patterns under varying solidification conditions.
Data Collection Method:
A multi-faceted approach to data collection was adopted, employing a suite of advanced analytical techniques:
- Scanning Electron Microscopy (SEM): Backscattered electron imaging (BSE) and energy dispersive X-ray spectroscopy (EDS) were conducted using FEI Quanta 250 FEG, FEI Quanta 650 FEG, and Tescan Mirai3LC FEG SEMs.
- Electron Probe Micro-Analysis (EPMA): Quantitative elemental mapping was performed using a JEOL JXA-8530F equipped with FEG, SXES, and EDS detectors.
- Transmission Electron Microscopy (TEM) and Scanning Transmission Electron Microscopy (STEM): Detailed microstructural and atomic-scale characterization was achieved using FEI Tecnai TF30 FEG TEM, FEI Talos F200 X-Field Emission Gun (X-FEG) STEM, and FEI Titan G2 80-200 aberration-corrected STEM.
- Spark Emission Spectroscopy (SES): Overall chemical compositions were determined using a Thermo Scientific ARL iSpark optical spark emission spectrometer.
Analysis Method:
The collected data was subjected to rigorous analysis, encompassing:
- Microscopy Image Analysis: Qualitative and quantitative analysis of SEM, TEM, and STEM images to characterize micro-segregation morphology and precipitate distribution.
- Elemental Mapping and Line Scans: EPMA and EDS data were used to generate elemental maps and concentration profiles, quantifying solute segregation within micro-segregation bands.
- Electron Diffraction: Selected area electron diffraction (SAED) patterns obtained in TEM were used for phase identification.
- Atomic-Scale Resolution Imaging: HAADF-STEM imaging and Fast Fourier Transformations (FFT) were employed to analyze the atomic structure of precipitates.
- Thermodynamic Calculations: Scheil solidification calculations were performed to predict phase formation sequences during solidification.
Research Subjects and Scope:
The research focused on as-cast AA6082 aluminium alloy samples. Samples were prepared from billets produced by DC, DCGR, and DCMC casting methods. The scope of the study was limited to the investigation of micro-segregation phenomena at the micro- and nano-scale within these as-cast materials, specifically focusing on the characterization of micro-segregation bands and associated precipitates.
5. Main Research Results:
Key Research Results:
The investigation revealed that micro-segregation in as-cast AA6082 aluminium alloy forms an interconnected network along grain boundaries and inter-dendritic channels. Micro-segregation was categorized into two distinct types:
- Major Micro-segregation: Predominantly located at grain boundaries and characterized by the presence of iron-bearing intermetallic phases.
- Minor Micro-segregation: Observed along both grain boundaries and inter-dendritic channels, primarily composed of Mg and Si alloying elements.
Atomic-scale imaging revealed that minor segregation bands are sites for precipitate formation. These precipitates nucleate via two mechanisms:
- Heterogeneous Nucleation: Occurring on dislocation networks. These precipitates are composed of a mixture of phases formed throughout the precipitation sequence.
- Homogeneous Nucleation: Occurring within the aluminium matrix. These precipitates are discrete phases that appear at the early stages of the precipitation sequence.
Data Interpretation:
Major vs. Minor Segregation: SEM analysis (Figure 1) revealed coarse features associated with major segregation, including plate, Chinese script, string, and circular shapes. Elemental mapping (Figure 2) indicated that these major segregation features are enriched in Si, Fe, and Mn. In contrast, minor segregation bands, as revealed by EPMA (Figure 3), are finer, approximately 5-15 µm in width, and enriched in Mg and Si.
Precipitation in Minor Segregation Bands: EPMA maps (Figure 3) and TEM/STEM analysis (Figures 4-8) demonstrated that minor segregation bands act as preferential sites for precipitation. Heterogeneous nucleation on dislocation lines leads to the formation of coarser precipitates with a mixture of phases (Figure 6 & 7). Homogeneous nucleation within the Al matrix results in finer, discrete precipitates, primarily precursors to β" and Type-B/U2 phases (Figure 8).
Segregation Network: The interconnected nature of minor segregation bands was highlighted by EPMA maps (Figure 9), showing that these bands form a network following grain boundaries and inter-dendritic channels, connecting high-concentration domains of Si and Mg.
Figure Name List:
- Figure 1. The back-scattered electron SEM images of the microstructure of AA6082 Al alloy in the as-cast DC, DCGR and DCMC conditions. The precipitation of the plate, Chinese script, string and circular shaped features has taken place.
- Figure 2. The back-scattered electron images of three casting conditions and the corresponding elemental maps. The labellings show the main element composition of the indicated phases.
- Figure 3. The qualitative electron probe micro-analysis (EPMA) maps of Si and Mg segregation in three different casting conditions. The EPMA maps are purposefully enhanced to reveal the minor segregation bands. The line scans are indicated with white dashed lines. The concentration (at.%) vs distance (µm) plots correspond to the respective line scans in the EPMA maps.
- Figure 4. The observed morphology in the micro-segregation bands in the DCGR cast. The TEM image of a hexagonal-shaped alpha-phase iron-rich particle, corresponding electron diffraction, elemental maps and noise filtered atomic-scale HAADF-STEM image along the (111) zone axis of the cubic alpha iron-rich phase.
- Figure 5. (A0) The HAADF-STEM image of the microstructure along the [001] aluminium zone axis, next to a coarse dendritic feature in the DCGR cast. (A1) The enlarged area marked with dashed white lines in the AO image. (A2) The area marked with white dashed lines in the A1 image and the corresponding elemental maps.
- Figure 6. The TEM and STEM imaging along the [001] aluminium zone axis, next to a coarse intermetallic in the minor-segregation bands in the DCGR cast. (A0) TEM image of the microstructure next to a coarse intermetallic. (A1) The enlarged TEM image of the area marked with dashed black lines in the A0 image. (A2) The HAADF-STEM image of the area marked with dashed black lines in the upper part of the A1 image. (1 & 2) The precipitates 1 and 2 imaged in their entirety using HAADF-STEM mode. The unfiltered atomic-scale images of the cross-sections of the precipitates 1 and 2 marked with white dashed lines. The overlaying of the Si-rich atomic columns in green and Cu-rich atomic columns in blue, and the corresponding FFTs. In the FFTs, the white circles indicate the Al matrix, and the white dashed circles indicate the Si network reflections.
- Figure 7. (a, b) The unfiltered atomic-scale HAADF-STEM images along the [001] aluminium zone axis, revealing the precipitate cross-sections of the heterogeneously nucleated precipitates. (I, II, III, IV) The enlarged parts from the different precipitate cross-section areas and the respective metastable phases. The atomic coordinates of the atomic columns parallel with the incident beam (z-coordinates) are neglected.
- Figure 8. The TEM and STEM image of the microstructure in the minor-segregation bands in the DCGR cast. (AO) The TEM image of the same area as in the Figure 6 (A1). (A1) The enlarged HAADF-STEM image of the area marked with dashed black lines in the A0 image. The homogenous precipitation has taken place. (a, b) The unfiltered atomic-scale HAADF-STEM image of the precipitates homogeneously nucleated inside the Al matrix and their corresponding FFTs.
- Figure 9. The EPMA maps of segregation pattern in the DCGR cast. (a) The Si segregation map and its schematic. (b) The Mg segregation map and its schematic. (c) The Mn segregation map and its schematic. The Mn segregation map is equivalent to the Fe segregation map. Check Appendix. (d) Illustration of the microstructure of the minor-segregation band. (e) Two aluminium dendrites prior to the bump into an aluminium dendritic boundary.
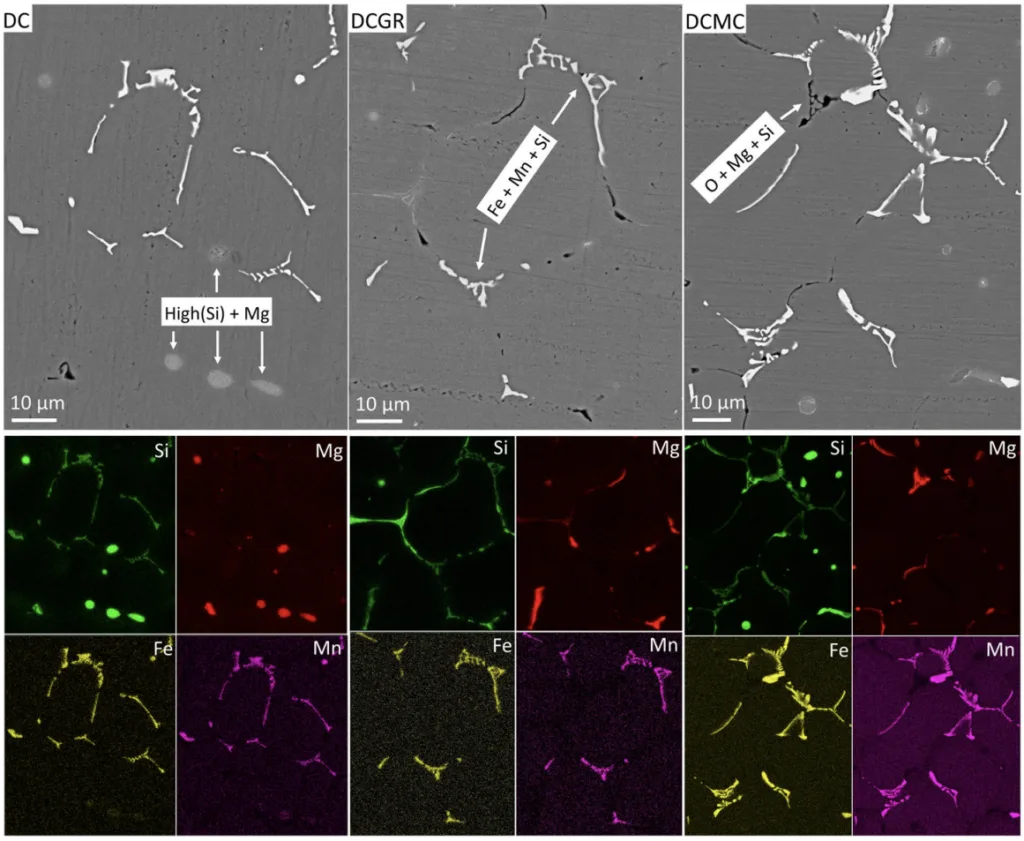
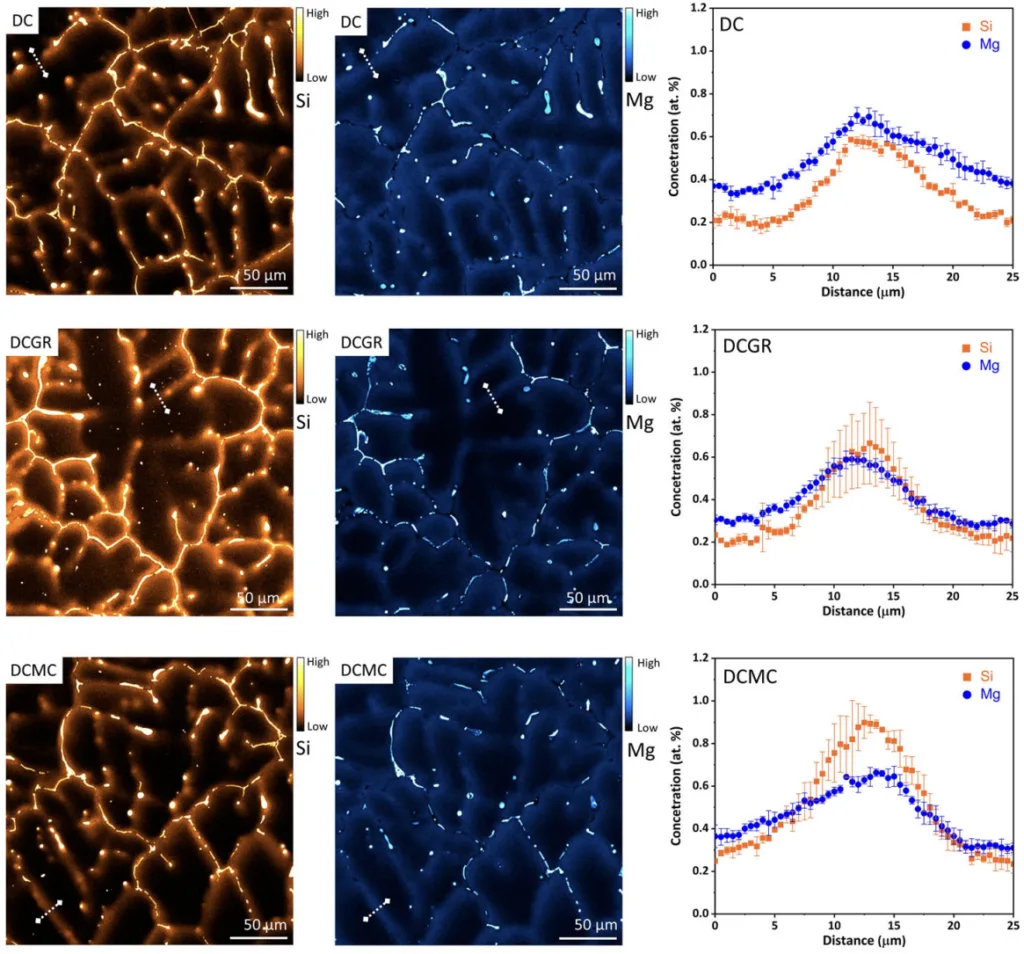
6. Conclusion:
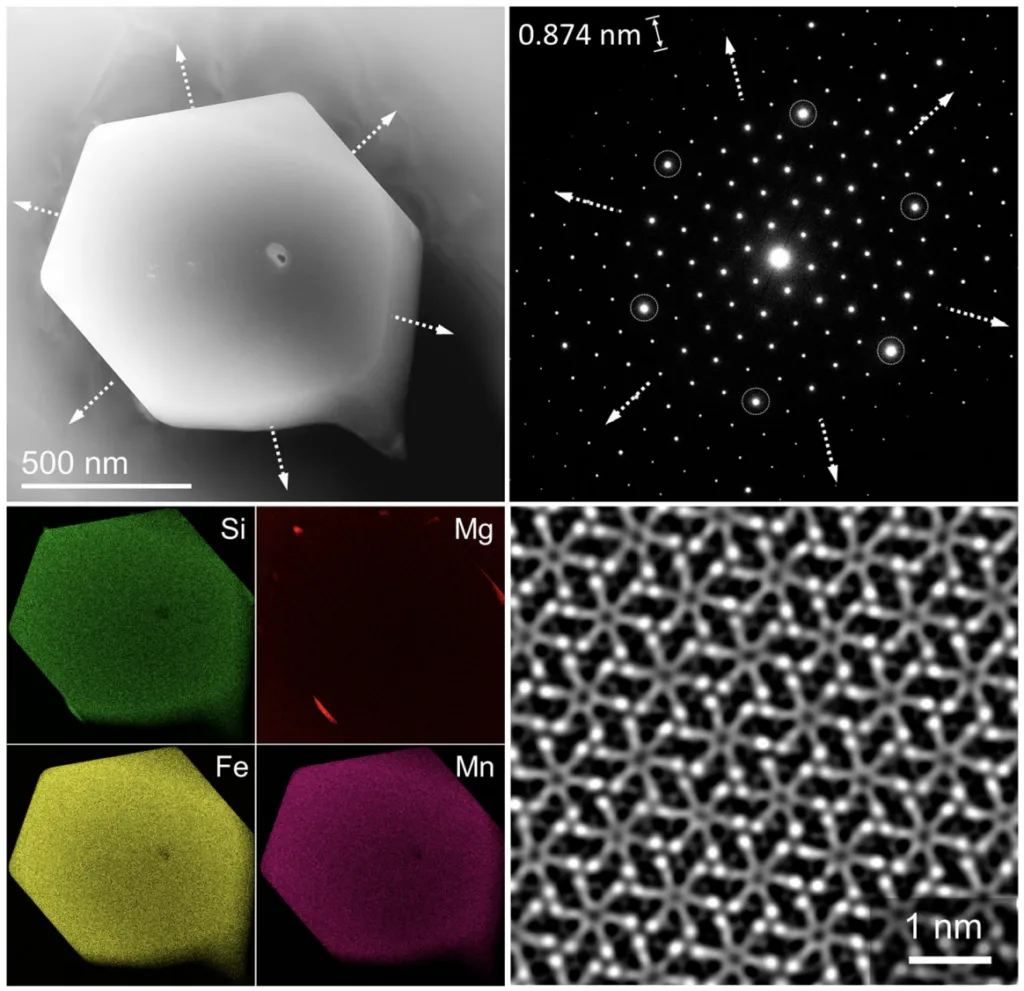
![Figure 5. (A0) The HAADF-STEM image of the microstructure along the [001] aluminium zone axis, next to a coarse dendritic feature in the DCGR cast. (A1) The enlarged area marked with dashed white lines in the AO image. (A2) The area marked with white dashed lines in the A1 image and the corresponding elemental maps.](https://castman.co.kr/wp-content/uploads/image-563-1024x719.webp)
![Figure 7. (a, b) The unfiltered atomic-scale HAADF-STEM images along the [001] aluminium zone axis, revealing the precipitate cross-sections of the heterogeneously nucleated precipitates. (I, II, III, IV) The enlarged parts from the different precipitate cross-section areas and the respective metastable phases. The atomic coordinates of the atomic columns parallel with the incident beam (z-coordinates) are neglected.](https://castman.co.kr/wp-content/uploads/image-564-1024x991.webp)
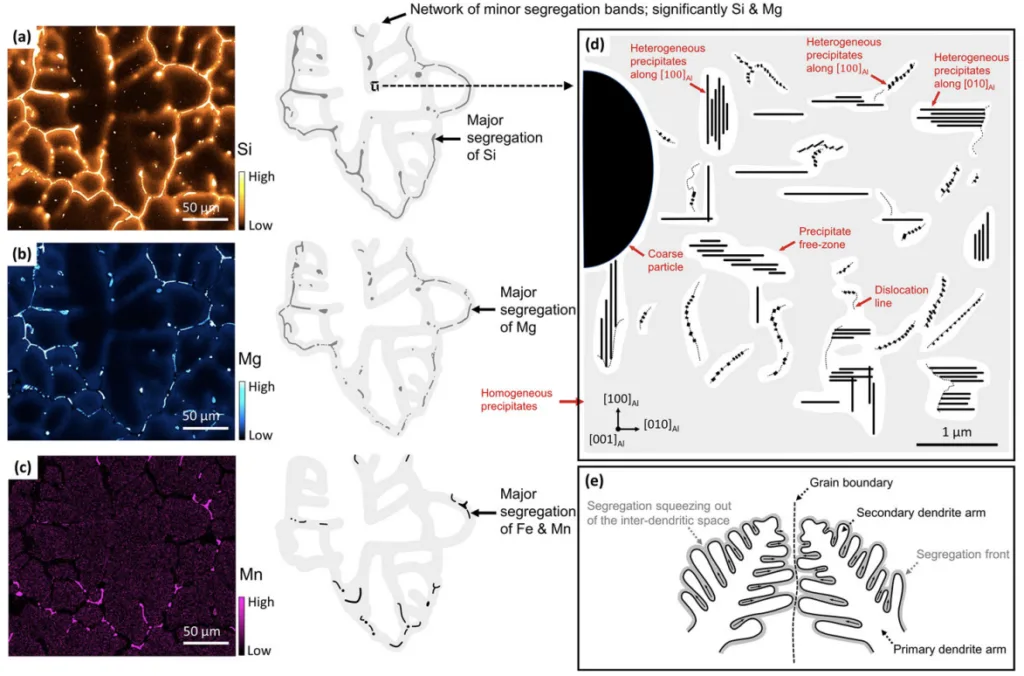
Summary of Main Results:
This research provides a comprehensive investigation into micro-segregation patterns in as-cast AA6082 aluminium alloys produced by direct chill casting, with and without grain refiners and melt conditioning. The study successfully differentiated between major and minor micro-segregation bands. Major bands, rich in Fe, Mn, and Si, are primarily located at grain boundaries, while minor bands, enriched in Si and Mg, follow inter-dendritic channels and grain boundaries. The alpha-Al15(FeMn)3Si2 intermetallic phase was identified as the main constituent of major segregation bands. Minor segregation bands, with a typical width of 5-15 µm and Mg/Si concentrations peaking at 0.6-0.8 at.%, serve as preferential sites for precipitation. The dislocation network within the as-cast microstructure is irregular and heterogeneously distributed, influencing heterogeneous precipitation. Both heterogeneous precipitation on dislocations and homogeneous precipitation within the aluminium matrix were observed within minor segregation bands.
Academic Significance of the Research:
This study contributes significantly to the fundamental understanding of micro-segregation in cast aluminium alloys. It provides a detailed multi-scale characterization, from macroscopic segregation patterns to atomic-scale precipitate structures. The differentiation between major and minor micro-segregation and the elucidation of their distinct characteristics and formation mechanisms offer valuable insights into solidification phenomena in Al-Mg-Si alloys.
Practical Implications:
The findings have direct practical implications for the aluminium casting industry. Understanding the formation and characteristics of micro-segregation bands and associated precipitates is crucial for optimizing casting processes and subsequent heat treatments. By controlling micro-segregation, it becomes possible to tailor the precipitation of strengthening phases, ultimately enhancing the mechanical properties of Al-Mg-Si alloy components, particularly for demanding applications in the automotive sector and beyond.
Limitations of the Research
The study acknowledges limitations arising from inherent variations in micro-segregation patterns and the relatively small sampling volumes used. These factors prevented a statistically significant differentiation between the three casting methods employed in terms of their impact on micro-segregation characteristics. Future research with larger sample sizes and more extensive statistical analysis may be necessary to overcome this limitation.
7. Future Follow-up Research:
- Directions for Follow-up Research:
- Further investigation into the formation mechanisms of the irregular dislocation networks observed and their precise role in driving heterogeneous precipitation.
- Quantitative analysis of the various precipitate phases present within major and minor segregation bands to establish a more detailed understanding of phase evolution.
- Exploration of the influence of specific casting parameters, such as cooling rate and melt temperature, on the resulting micro-segregation patterns and precipitate characteristics.
- Areas Requiring Further Exploration:
- The precise mechanisms governing the squeeze-out of solute-enriched melt into grain boundaries and inter-dendritic channels during the final stages of solidification.
- The interplay between major and minor segregation bands and their combined effect on the overall microstructure and material properties.
- Development of predictive models to simulate micro-segregation formation and precipitate evolution in Al-Mg-Si alloys under various casting conditions.
8. References:
- [1] D.G. Eskin, R. Nadella, and L. Katgerman, Effect of different grain structures on center-line macrosegregation during direct-chill casting. Acta Mater. 56 (2008), pp. 1358–1365. doi:10.1016/j.actamat.2007.11.021.
- [2] Z. Yao, Y. Huo, M. Li, and J. Allison, A quantitative study of microsegregation in aluminum-copper alloys. Metall. Mater. Trans. A 53 (2022), pp. 2383–2401. doi:10.1007/s11661-022-06669-3.
- [3] R. Nadella, D.G. Eskin, Q. Du, and L. Katgerman, Macrosegregation in direct-chill casting of aluminium alloys. Prog. Mater. Sci. 53 (2008), pp. 421–480. doi:10.1016/j.pmatsci.2007.10.001.
- [4] X. Doré, H. Combeau, and M. Rappaz, Modelling of microsegregation in ternary alloys: applications to the solidification of Al-Mg-Si. Acta Mater. 48 (2000), pp. 3951–3962. doi:10.1016/S1359-6454(00)00177-4.
- [5] Q. Dong, X. Chen, J. Xia, X. Li, B. Zhang, and H. Nagaumi, Floating grain characterization and its effects on centerline segregation of direct-chill cast Al-Mg-Si alloy billets. Mater. Trans. 61(12) (2020), pp. 2386–2392. doi:10.2320/matertrans.MT-M2020229.
- [6] L. Lodgaard and N. Ryum, Precipitation of dispersoids containing Mn and/or Cr in Al–Mg-Si alloys. Mater. Sci. Eng. 283 (2000), pp. 144–152. doi:10.1016/S0921-5093(00)00734-6.
- [7] R. Hu, T. Ogura, H. Tezuka, T. Sato, and Q. Liu, Dispersoid formation and recrystallization behavior in an Al-Mg-Si-Mn alloy. J. Mater. Sci. Technol. 26(3) (2010), pp. 237–243. doi:10.1016/S1005-0302(10)60040-0.
- [8] M. Kenyon, J. Robson, J. Fellowes, and Z. Liang, Effect of dispersoids on the microstructure evolution in Al-Mg-Si alloys. Adv. Eng. Mater. 21 (2019), pp. 1800494. doi:10.1002/adem.201800494.
- [9] T. Dorin, M. Ramajayam, S. Babaniaris, and T.J. Langan, Micro-segregation and precipitates in as-solidified Al-Sc-Zr-(Mg)-(Si)-(Cu) alloys. Mater. Charact. 154 (2019), pp. 353-362. doi:10.1016/j.matchar.2019.06.021.
- [10] Y.S. Park, S.B. Lee, and N.J. Kim, Microstructure and mechanical properties of strip cast Al-Mg-Si-X alloys. Mater. Trans. 44(12) (2003), pp. 2617-2624. doi:10.2320/matertrans.44.2617.
- [11] M. Ganesan, L. Thuinet, D. Dye, and P.D. Lee, Quantification of microsegregation in cast Al-Si-Cu alloys. Metall. Mater. Trans. 38 (2007), pp. 557–566. doi:10.1007/s11663-007-9071-0.
- [12] G. Scamans, Electric vehicle spike demand for high strength aluminum extrusions. Light Met. Age 76 (2018), pp. 6-12.
- [13] C.D. Marioara, S.J. Andersen, J. Jansen, and H.W. Zandbergen, The influence of temperature and storage time at RT on nucleation of the β" phase in a 6082 Al-Mg-Si alloy. Acta Mater. 51 (2003), pp. 789–796. doi:10.1016/S1359-6454(02)00470-6.
- [14] A. Cibula, The grain refinement of aluminium alloy castings by additions of titatnium and boron. J. Inst. Met. 80 (1951), pp. 1–16.
- [15] Z. Fan, Y. Wang, Y. Zhang, T. Qin, X.R. Zhou, G.E. Thompson, T. Pennycook, and T. Hashimoto, Grain refining mechanism in the Al/Al-Ti-B system. Acta Mater. 84 (2015), pp. 292-304. doi:10.1016/j.actamat.2014.10.055.
- [16] Z. Fan, An epitaxial model for heterogenous nucleation on potent substrates. Metall. Mater. Trans. A 44 (2013), pp. 1409–1418. doi:10.1007/s11661-012-1495-8.
- [17] Z. Fan, B. Jiang, and Y. Zuo. Apparatus and method for liquid metals treatment. WO/2012/035357 and 2013 US 20130228045 A1.
- [18] G. Scamans, H.T. Li, J.L. Nebreda, J. Patel, I. Stone, Y. Wang, X. Yang, and Z. Fan, Advanced casting technologies using high shear melt conditioning. Fundam. Alum. Metall., Chapter 8 (2018), pp. 249–277. doi:10.1016/B978-0-08-102063-0.00008-4.
- [19] J.B. Patel, H.T. Li, X. Mingxu, and S. Jones, Melt conditioned direct chill casting (MC-DC) process for production of high-quality aluminum alloy billets. Mater. Sci. Forum 794-796 (2014), pp. 149–154. doi:10.4028/www.scientific.net/MSF.794-796.149.
- [20] K.M.S. Manu, N.S. Barekar, J.L. Nebreda, J.B. Patel, and Z. Fan, In-situ microstructural control of A6082 alloy to modify second phase particles by melt conditioned direct chill
- [21] G. Scamans, H.T. Li, and Z. Fan, Melt conditioned casting of aluminum alloys, 13th International Conference on Aluminum Alloys (ICAA13), 2012. doi:10.1007/978-3-319-48761-8_213.
- [22] S. Kumar and K.A.Q. O'Reilly, Influence of Al grain structure on Fe bearing intermetallics during DC casting of an Al-Mg-Si alloy. Mater. Charact. 120 (2016), pp. 311–322. doi:10.1016/j.matchar.2016.09.017.
- [23] S. Kumar, P.S. Grant, and K.A.Q. O'Reilly, Evolution of Fe bearing intermetallics during DC casting and homogenization of an Al-Mg-Si Al alloy. Metall. Mater. Trans. A 47 (2016), pp. 3000–3014. doi:10.1007/s11661-016-3451-5.
- [24] S. Kumar, P.S. Grant, and K.A.Q. O'Reilly, Fe bearing intermetallic phase formation in a wrought Al-Mg-Si alloy. Trans. Indian Inst. Met. 65(6) (2012), pp. 553–557. doi:10.1007/s12666-012-0221-y.
- [25] A. Verma, S. Kumar, P.S. Grant, and K.A.Q. O'Reilly, Influence of cooling rate on the Fe intermetallic formation in an AA6063 Al alloy. J. Alloys Compd. 555 (2013), pp. 274–282. doi:10.1016/j.jallcom.2012.12.077.
- [26] T. Hashimoto, G.E. Thompson, M. Curioni, X. Zhou, and P. Skeldon, Three-dimensional imaging of light metals using serial block face scanning electron microscopy (SBFSEM). Mat. Sci. Forum 765 (2013), pp. 501–505. doi:10.4028/www.scientific.net/MSF.765.501.
- [27] J.M. Yu, T. Hashimoto, H.T. Li, N. Wanderka, Z. Zhang, C. Cai, X.L. Zhong, J. Qin, Q.P. Dong, H. Nagaumi, and X.N. Wang, Formation of intermetallic phases in unrefined and refined AA6082 Al alloys investigated by using SEM-based ultramicrotomy tomography. J. Mater. Sci. Technol. 120 (2022), pp. 118–128. doi:10.1016/j.jmst.2022.02.007.
- [28] C.M. Dinnis, J.A. Taylor, and A.K. Dahle, As-cast morphology of iron-intermetallics in Al-Si foundry alloys. Scr. Mater. 53 (2005), pp. 955–958. doi:10.1016/j.scriptamat.2005.06.028.
- [29] Z. Que and C.L. Mendis, Heterogenous nucleation and phase transformation of Fe-rich intermetallic compounds in Al-Mg-Si alloys. J. Alloys Compd. 836 (2020), pp. 155515. doi:10.1016/j.jallcom.2020.155515.
- [30] Z. Que, Y. Wang, and Z. Fan, Formation of the Fe-containing intermetallic compounds during solidification of Al-5Mg-2Si-0.7Mn-1.1Fe alloy. Metall. Mater. Trans. A 49 (2018), pp. 2173–2181. doi:10.1007/s11661-018-4591-6.
- [31] Y.L. Liu and S.B. Kang, The solidification process of Al-Mg-Si alloys. J. Mater. Sci. 32 (1997), pp. 1443–1447. doi:10.1023/A:1018545732009.
- [32] Y.L. Liu, S.B. Kang, and H.W. Kim, The complex microstructures in an as-cast Al-Mg-Si alloy. Mater. Lett. 41 (1999), pp. 267–272. doi:10.1016/S0167-577X(99)00141-X.
- [33] Z. Fan, M. Xia, H. Zhang, G. Liu, J.B. Patel, Z. Bian, I. Bayandorian, Y. Wang, H.T. Li, and G.M. Scamans, Melt conditioning by advanced shear technology (MCAST) for refining solidification microstructure. Int. J. Cast Met. Res. 22(1-4) (2009), pp. 103–107. doi:10.1179/136404609X367443.
- [34] Z. Fan, Y. Wang, Z.F. Zhang, M. Xia, H.T. Li, J. Xu, L. Granas, and G.M. Scamans, Shear enhanced heterogenous nucleation in some Mg-and Al-alloys. Int. J. Cast Met. Res. 22(1-4) (2009), pp. 318–322. doi:10.1179/136404609X367452.
- [35] D. Luo, I. Chang, J.B. Patel, K. Al-Helal, Y. Huang, G.M. Scamans, and Z. Fan, Microstructure and mechanical properties of recycled AA6111 alloy processed by melt conditioned direct chill (MC-DC) casting. M&Ns-19 (17-19 July 2019), pp. 81–85.
- [36] S.H. Oh, Y. Kauffmann, C. Scheu, W.D. Kaplan, and M. Rühle, Ordered liquid aluminum at the interface with sapphire. Science 310(5748) (2005), pp. 661-663. doi:10.1126/science.1118611.
- [37] H.T. Li, Y. Wang, and Z. Fan, Enhanced heterogeneous nucleation on oxides in Al alloys by intensive shearing. IOP Conf. Ser.: Mater. Sci. Eng. 27 (2012), pp. 012047. doi:10.1088/1757-899X/27/1/012047.
- [38] J.L. Nebreda, J.B. Patel, I. Stone, and G.M. Scamans, De-ironing of aluminium alloy scrap by high shear melt conditioning technology, Proceedings of the 6th Decennial International Conference on Solidification Processing, Old Windsor, July 2017. doi:10.3390/met12101579.
- [39] Z.P. Que, Y.P. Zhou, Y. Wang, and Z. Fan, Effect of MgO on phase selection in Al-Mg-Si-Fe-Mn alloys. Trans. Indian Inst. Met. 68(6) (2015), pp. 1167–1172. doi:10.1007/s12666-015-0664-z.
- [40] H.T. Li, S. Ji, Y. Wang, M. Xia, and Z. Fan, Effect of intensive melt shearing on the formation of Fe-containing intermetallics in LM24 Al-alloy. IOP Conf. Ser.: Mater. Sci. Eng. 27 (2012), pp. 012075. doi:10.1088/1757-899X/27/1/012075.
- [41] H.T. Li, M. Xia, P. Jarry, G.M. Scamans, and Z. Fan, Grain refinement in a AlZnMgCuTi alloy by intensive melt shearing: A multi-step nucleation mechanism. J. Cryst. Growth 314 (2011), pp. 285–292. doi:10.1016/j.jcrysgro.2010.10.168.
- [42] M. Cooper, The crystal structure of the ternary alloy a(AlFeSi). Acta Cryst. 23 (1967), pp. 1106-1107. doi:10.1107/S0365110X67004372.
- [43] K. Matsuda, T. Kawabata, Y. Uetani, T. Sato, and S. Ikeno, Hexagonal tabular β-phase in Al-Mg-Si-Cu alloy. Scr. Mater. 47 (2002), pp. 467-471. doi:10.1016/S1359-6462(02)00173-2.
- [44] C. Li, Y.Y. Wu, H. Li, and X.F. Liu, Morphological evolution and growth mechanism of primary Mg2Si phase in Al-Mg2Si alloys. Acta Mater. 59 (2011), pp. 1058–1067. doi:10.1016/j.actamat.2010.10.036.
- [45] E. Cinkilic, M. Moodispaw, J. Zhang, J. Miao, and A.A. Luo, A new recycled Al-Si-Mg alloy for sustainable structural die casting applications. Metall. Mater. Trans. A 53 (2022), pp. 2861–2873. doi:10.1007/s11661-022-06711-4.
- [46] C.J. Simensen, P. Fartum, and A. Andersen, Analysis of intermetallic particles in aluminium by dissolution of the sample in butanol. Fresenius Z. Anal. Chem. 319 (1984), pp. 286-292. doi:10.1007/BF00487273.
- [47] J. Gjønnes, V. Hansen, S.J. Andersen, C.D. Marioara, and X.Z. Li, Electron crystallography of aluminum alloy phases. Z. Kristallogr. 218 (2003), pp. 293–307. doi:10.1524/zkri.218.4.293.20745.
- [48] N.C.W. Kuijpers, F.J. Vermolen, C. Vuik, P.T.G. Koenis, K.E. Nilsen, and S. van der Zwaag, The dependence of the β-AlFeSi to a-Al(FeMn)Si transformation kinetics in Al-Mg-Si alloys on the alloying elements. Mat. Sci. Eng. A 394 (2005), pp. 9–19. doi:10.1016/j.msea.2004.09.073.
- [49] K. Al-Helal, J.L. Nebreda, J.B. Patel, and G.M. Scamans, High-shear de-gassing and de-ironing of an aluminum casting alloy made directly from aluminum end-of-life vehicle scrap. Recycling 6 (2021), pp. 66. doi:10.3390/recycling6040066.
- [50] N.C.W. Kuijpers, W.H. Kool, P.T.G. Koenis, K.E. Nilsen, I. Todd, and S. van der Zwaag, Assessment of different techniques for quantification of a-Al(FeMn)Si and β-AlFeSi intermetallics in AA6xxx alloys. Mater. Charact. 49 (2002), pp. 409–420. doi:10.1016/S1044-5803(03)00036-6.
- [51] N.C.W. Kuijpers, F.J. Vermolen, K. Vuik, and S. van der Zwaag, A model of the β-AlFeSi to a-Al(FeMn)Si transformation in Al-Mg-Si alloys. Mater. Trans. 44(7) (2003), pp. 1448–1456. doi:10.2320/matertrans.44.1448.
- [52] H. Tanihata, T. Sugawara, K. Matsuda, and S. Ikeno, Effect of casting and homogenizing treatment conditions on the formation of Al-Fe-Si intermetallic compounds in 6063 Al-Mg-Si alloys. J. Mater. Sci. 34 (1999), pp. 1205–1210. doi:10.1023/A:1004504805781.
- [53] D.T.L. Alexander and A.L. Greer, Solid-state intermetallic phase tranformations in 3XXX aluminium alloys. Acta Mater. 50 (2002), pp. 2571–2583. doi:10.1016/S1359-6454(02)00085-X.
- [54] V.S. Zolotorevsky, N.A. Belov, and M.V. Glazoff, Casting Aluminum Alloys, Chapter 2, Elsevier Science Ltd., Amsterdam, 2007.
- [55] S.J. Andersen, C.D. Marioara, J. Friis, R. Bjørge, Q. Du, I.G. Ringdalen, S. Wenner, E.A. Mørtsell, R. Holmestad, T. Saito, J. Røyset, and O. Reiso, Directionality and column arrangement principles of precipiatetes in Al-Mg-Si-(Cu) and Al-Mg-Cu linked to line defect in Al. Mater. Sci. Forum 877 (2016), pp. 461–470. doi:10.4028/www.scientific.net/MSF.877.461.
- [56] T. Saito, E.A. Mørtsell, S. Wenner, C.D. Marioara, S.J. Andersen, J. Friis, K. Matsuda, and R. Holmestad, Atomic structures of precipitates in Al-Mg-Si alloys with small additions of other elements. Adv. Eng. Mater. 20 (2018), pp. 180015. doi:10.1002/adem.201800125.
- [57] S. Pogatscher, H. Antrekowitsch, M. Werinos, F. Moszner, S.S.A. Gerstl, M.F. Francis, W.A. Curtin, J.F. Löffler, and P.J. Uggowitzer, Diffusion on demand to control precipitation aging: application to Al-Mg-Si alloys. Phys. Rev. Lett. 112 (2014), pp. 225701. doi:10.1103/PhysRevLett.112.225701.
- [58] S. Pogatscher, H. Antrekowitsch, H. Leitner, D. Pöschmann, Z.L. Zhang, and P.J. Uggowitzer, Influence of interrupted quenching on artificial aging of Al-Mg-Si alloys. Acta Mater. 60 (2012), pp. 4496–4505. doi:10.1016/j.actamat.2012.04.026.
- [59] S. Pogatscher, H. Antrekowitsch, H. Leitner, T. Ebner, and P.J. Uggowitzer, Mechanisms controlling the artificial aging of Al-Mg-Si alloys. Acta Mater. 59 (2011), pp. 3352-3363. doi:10.1016/j.actamat.2011.02.010.
- [60] S. Qin, A. Bendo, T. Tsuchiya, S. Lee, and K. Matsuda, Effect of cooling rate on precipitation during homogenization cooling in excess Si type Al-Mg-Si alloy. Mater. Lett. 278 (2020), pp. 128363. doi:10.1016/j.matlet.2020.128363.
- [61] S. Qin, A. Bendo, T. Tsuchiya, S. Lee, Y. Zou, and K. Matsuda, Effect of cooling rate on precipitation during homogenization cooling in balanced Al-Mg2Si alloy. Mater. Trans. 61(11) (2020), pp. 2115–2120. doi:10.2320/matertrans.MT-M2020189.
- [62] M.R. Gazizov, A.V. Dubina, D.A. Zhemchuzhnikova, and R.O. Kaibyshev, Effect of equal channel angular pressing and aging on the microstructure and mechanical properties of an Al-Cu-Mg-Si alloy. Phys. Met. Metallogr. 116(7) (2015), pp. 718–729. doi:10.1134/S0031918X15070066.
- [63] M. Gazizov, C.D. Marioara, J. Friis, S. Wenner, R. Holmestad, and R. Kaibyshev, Precipitation behavior in an Al-Cu-Mg-Si alloy during ageing. Mater. Sci. Eng. A 767 (2019), pp. 138369. doi:10.1016/j.msea.2019.138369.
- [64] Y.X. Lai, W. Fan, M.J. Yin, C.L. Wu, and J.H. Chen, Structures and formation mechanisms of dislocation-induced precipitates in relation to the age-hardening responses of Al-Mg-Si alloys. J. Mater. Sci. Technol. 41 (2020), pp. 127–138. doi:10.1016/j.jmst.2019.11.001.
- [65] K. Matsuda, S. Shimizu, H. Gamada, Y. Uetani, F. Shinagawa, and S. Ikeno, Effect of deformation on the precipitates in Al-Mg2Si alloys containing silicon in excess. Mater. Des. Eng. 48(1) (1999), pp. 10–15. doi:10.2472/jsms.48.10.
- [66] E. Thronsen, C.D. Marioara, J.K. Sunde, K. Minakuchi, T. Katsumi, I. Erga, S.J. Andersen, J. Friis, K. Marthinsen, K. Matsuda, and R. Holmestad, The effect of
- [67] E. Thronsen, H. Morkeseth, C.D. Marioara, K. Minakuchi, T. Katsumi, K. Marthinsen, K. Matsuda, and R. Holmestad, The effect of small additions of Fe and heavy deformation on the precipitation in an Al-1.1Mg-0.5Cu-0.3Si at.% alloy. Metall. Mater. Trans. 53 (2022), pp. 3296–3310. doi:10.1007/s11661-022-06744-9.
- [68] K. Matsuda, S. Tada, S. Ikeno, T. Sato, and A. Kamio, Crystal system of rod-shaped precipitates in an Al-1.0mass%Mg2Si-0.4mass%Si alloy. Scr. Metall. Mater. 32(8) (1995), pp. 1175-1180. doi:10.1016/0956-716X(95)00121-B.
- [69] K. Matsuda, S. Ikeno, T. Sato, and A. Kamio, A metastable phase having the orthorhombic crystal lattice in an Al-1.0mass% Mg2Si-0.4mass% Si alloy. Scr. Mater. 34(11) (1996), pp. 1797–1802. doi:10.1016/1359-6462(96)00057-7.
- [70] K. Matsuda, S. Ikeno, T. Sato, and A. Kamio, Classification of metastable phases in Al-Mg2Si alloys by HRTEM. Mater. Sci. Forum 217-222 (1996), pp. 707–712. doi:10.4028/www.scientific.net/MSF.217-222.707.
- [71] S.J. Andersen, C.D. Marioara, R. Vissers, A. Frøseth, and H.W. Zandbergen, The structural relation between precipitates in Al-Mg-Si alloys, the Al-matrix and diamond silicon, with emphasis on the trigonal phase U1-MgAl2Si2. Mater. Sci. Eng. A 444 (2007), pp. 157–169. doi:10.1016/j.msea.2006.08.084.
- [72] S.J. Andersen, C.D. Marioara, A. Frøseth, R. Vissers, and H.W. Zandbergen, Crystal structure of the orthorhombic U2-Al4Mg4Si4 precipitate in the Al-Mg-Si alloy system and its relation to the β' and β” phases. Mater. Sci. Eng. A 390 (2005), pp. 127–138. doi:10.1016/j.msea.2004.09.019.
- [73] S.J. Andersen, C.D. Marioara, A. Frøseth, R. Vissers, and H.W. Zandbergen, Crystal structures of the trigonal U1-MgAl2Si2 and orthorhombic U2-Mg4Al4Si4 precipitates in the Al-Mg-Si alloy system. I. Phys. Conf. Ser. 179 (2003), pp. 225.
- [74] K. Matsuda, Y. Uetani, T. Sato, and S. Ikeno, Metastable phases in an Al-Mg-Si alloy containing copper. Metall. Mater. Trans. A 32 (2001), pp. 1293–1299. doi:10.1007/s11661-001-0219-2.
- [75] K. Matsuda, D. Teguri, Y. Uetani, T. Sato, and S. Ikeno, Cu-seggregation at the Q'/α-Al interface in Al-Mg-Si-Cu alloy. Scr. Mater. 47 (2002), pp. 833–837. doi:10.1016/S1359-6462(02)00325-1.
- [76] S. Wenner, C.D. Marioara, S.J. Andersen, and R. Holmestad, Effect of room temperature storage time on precipitation in Al-Mg-Si(-Cu) alloys with different Mg/Si ratios. Int. J. Mater. Res. 103 (2012), pp. 948–954. doi:10.3139/146.110795.
- [77] H.S. Hasting, J.C. Walmsley, A.T.J. Van Helvoort, C.D. Marioara, S.J. Andersen, and R. Holmestad, Z-contrast imaging of the arrangement of Cu in precipitates in 6XXX-series aluminium alloys. Philos. Mag. Lett. 86(9) (2006), pp. 589–597. doi:10.1080/09500830600938340.
- [78] C.D. Marioara, S.J. Andersen, T.N. Stene, H. Hasting, J. Walmsley, A.T.J. Van Helvoort, and R. Holmestad, The effect of Cu on precipitation in Al-Mg-Si alloys. Philos. Mag. 87(23) (2007), pp. 3385–3413. doi:10.1080/14786430701287377.
- [79] L. Arnberg and B. Aurivillius, The crystal structure of AlxCu2Mg12-xSi7 (h-AlCuMgSi). Acta Chem. Scand. 34a (1980), pp. 1–5.
- [80] M. Torsaeter, R. Vissers, C.D. Marioara, S.J. Andersen, and R. Holmestad, Crystal structure determination of the Q' and C-type plate precipitates in Al-Mg-Si-Cu (6xxx) alloys, in Jürgen Hirsch, Birgit Skrotzki, Günter Gottstein (Eds.), Aluminium Alloys: Their Physical and Mechanical Properties, vol. 2, Wiley-VHC, Aachen, 2008.
- [81] M. Fiawoo, X. Gao, L. Bourgeois, N. Parson, X.Q. Zhang, M. Couper, and J.F. Nie, Formation of multiple orientation relationships of Q precipitates in Al-Mg-Si-Cu alloys. Scr. Mater. 88 (2014), pp. 53–56. doi:10.1016/j.scriptamat.2014.05.013.
- [82] M. Torsaeter, W. Lefebvre, C.D. Marioara, S.J. Andersen, J.C. Walmsley, and R. Holmestad, Study of intergrown L and Q' precipitates in Al-Mg-Si-Cu alloys. Scr. Mater. 64 (2011), pp. 817–820. doi:10.1016/j.scriptamat.2011.01.008.
- [83] G.M. Scamans, N.J.H. Holroyd, and C.D.S. Tuck, The role of magnesium segregation in the intergranular stress corrosion cracking of aluminium alloy. Corros. Sci. 27(4) (1987), pp. 329–347. doi:10.1016/0010-938X(87)90076-Χ.
- [84] X. Sauvage, N. Enikeev, R. Valiev, Y. Nasedkina, and M. Murashkin, Atomic-scale analysis of the segregation and precipitation mechanisms in a severely deformed Al-Mg alloy. Acta Mater. 72 (2014), pp. 125–136. doi:10.1016/j.actamat.2014.03.033.
- [85] M. de Hass and J.T.M. De Hosson, Grain boundary segregation and precipitation in aluminium alloys. Scripta Mater. 44 (2001), pp. 281-286. doi:10.1016/S1359-6462(00)00577-7.
- [86] K. Teichmann, C.D. Marioara, S.J. Andersen, and K. Marthinsen, The effect of preaging deformation on the precipitation behavior of an Al-Mg-Si alloy. Metall. Mater. Trans. A 43 (2012), pp. 4006–4014. doi:10.1007/s11661-012-1235-0.
9. Copyright:
- This material is "Artenis Bendo, Jonathan Fellowes, Matthew Smith, Masoud Moshtaghi, Zelong Jin, Kenji Matsuda, Zhongyun Fan & Xiaorong Zhou"'s paper: Based on "Solute micro-segregation profile and associated precipitation in cast Al-Mg-Si alloy".
- Paper Source: https://doi.org/10.1080/14786435.2024.2336012
This material was summarized based on the above paper, and unauthorized use for commercial purposes is prohibited.
Copyright © 2025 CASTMAN. All rights reserved.