This technical brief is based on the academic paper "Preventive Maintenance Modeling on Die Casting Machines with Information Systems" by Tri Pujadi, Bahtiar H. Simamora, Vikas Kumar, Yulia Magdalena, Witarsjah, Yunita Kartika Sari, and Satya Windy, published in the Proceedings of the International Conference on Industrial Engineering and Operations Management (2021). It is summarized and analyzed for HPDC professionals by the experts at CASTMAN.
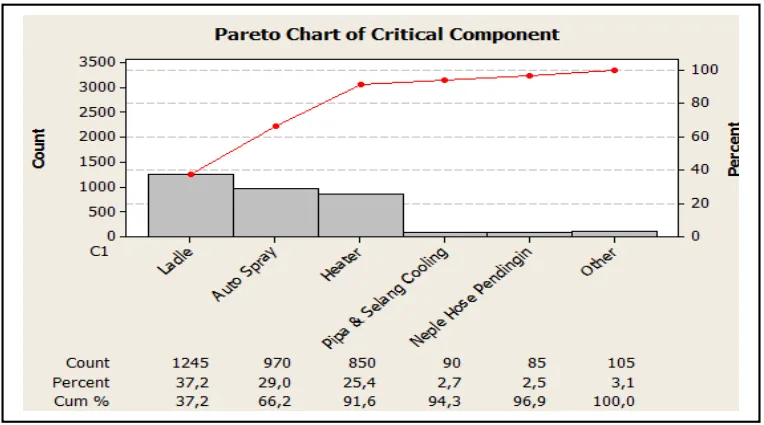
Keywords
- Primary Keyword: Preventive Maintenance Die Casting Machines
- Secondary Keywords: Die Casting Downtime, MTTF (Mean Time To Failure), MTTR (Mean Time To Repair), Age Replacement Method, Maintenance Information System, Critical Component Analysis, Failure Mode Effect Analysis
Executive Summary
- The Challenge: Tight production schedules often lead to a "run-to-failure" maintenance approach for die casting machines, causing costly, sudden breakdowns and significant unplanned downtime.
- The Method: Researchers applied a quantitative, data-driven approach using the age replacement method. They analyzed historical breakdown data to calculate the optimal replacement time for critical components based on Mean Time To Failure (MTTF) and Mean Time To Repair (MTTR).
- The Key Breakthrough: The study identified the most critical machine (DC-07) and its key failure components (ladle, auto spray, heater), establishing precise, optimal intervals for preventive replacement.
- The Bottom Line: Implementing the proposed preventive maintenance schedule resulted in a 53.04% reduction in total downtime, a reliability increase of up to 129% for key components, and significant cost savings.
The Challenge: Why This Research Matters for HPDC Professionals
In high-pressure die casting, the relentless pace of production often pushes machine maintenance to the back burner. As the paper highlights, many facilities only replace components "when the machine is damaged suddenly." This reactive approach is a gamble that frequently results in unexpected, catastrophic failures during production runs. The consequences are severe: lost production, missed deadlines, and inflated repair costs. The core problem identified is the lack of a data-driven system to determine when to perform maintenance before a failure occurs, moving from a reactive to a proactive, predictive strategy.
The Approach: Unpacking the Methodology
To solve this problem, the researchers employed a quantitative case study method focused on preventive maintenance. The analysis was a multi-step process:
- Identify the Critical Machine: They first analyzed downtime data across 16 die casting machines to identify the one with the highest total downtime, which was the DC-07 machine.
- Pinpoint Critical Components: Using a Pareto analysis on the DC-07 machine's failure data, they determined the components responsible for the vast majority of its downtime: the ladle, auto spray, and heater.
- Calculate Failure & Repair Times: For these critical components, they calculated the Mean Time To Failure (MTTF) and Mean Time To Repair (MTTR) from historical data.
- Model Optimal Replacement: They applied the age replacement method to calculate the optimal time (tp) to replace each component to minimize downtime and maximize availability and reliability. This was then compared against the existing "run-to-failure" baseline.
The Breakthrough: Key Findings & Data
The study produced clear, quantifiable results that demonstrate the power of a data-driven maintenance strategy.
Finding 1: Optimal Replacement Intervals Identified: The analysis determined the ideal service life for preventive replacement. The ladle component should be replaced after 108 hours, the auto spray after 506 hours, and the heater after 320 hours to prevent in-service failure (Table 4).
Finding 2: Massive Reliability Improvement: Implementing this schedule dramatically increased component reliability. Compared to the previous approach, the ladle's reliability improved by 92.44%, the auto spray's by 129.25%, and the heater's by 80.07% (Table 6).
Finding 3: Downtime Slashed by More Than Half: The most significant operational benefit was a massive reduction in machine downtime. The proposed model cut total downtime from 4,258 hours to 2,258 hours, a 53.04% improvement (Table 7).
Finding 4: Significant Cost Savings: The reduction in unplanned failures and emergency repairs translated directly to the bottom line. The study calculated cost savings of 24.73% for the ladle, 31.11% for the auto spray, and 38.90% for the heater component maintenance (Table 8).
Practical Implications for HPDC Products
This research offers a practical blueprint for any die casting facility looking to move beyond reactive maintenance.
- For Maintenance & Process Engineers: The findings provide a clear methodology to stop guessing and start calculating. By analyzing your own machine data for MTTF and MTTR, you can establish optimal, cost-effective replacement schedules for your most critical components, as demonstrated for the ladle, auto spray, and heater.
- For Operations & Plant Managers: The data presents a compelling business case. A 53.04% reduction in downtime (Table 7) directly translates to increased production capacity and throughput. The significant cost savings (Table 8) further justify the investment in a more structured maintenance program and the information systems needed to support it.
- For System Integration: The paper proposes an information system to manage this process (Figure 4). This suggests that integrating maintenance data collection and analysis into your existing ERP or MES can automate these calculations, ensuring maintenance schedules are always optimized and easily accessible to technicians and leaders.
Paper Details
Preventive Maintenance Modeling on Die Casting Machines with Information Systems
1. Overview:
- Title: Preventive Maintenance Modeling on Die Casting Machines with Information Systems
- Author: Tri Pujadi, Bahtiar H. Simamora, Vikas Kumar, Yulia Magdalena, Witarsjah, Yunita Kartika Sari, Satya Windy
- Year of publication: 2021
- Journal/academic society of publication: Proceedings of the International Conference on Industrial Engineering and Operations Management
- Keywords: Risk, procurement, supply chain, failure mode effect analysis, mitigate risk, scrm
2. Abstract:
From the results of observations at the company, the main problem found is that maintenance activities have not been carried out properly due to the tight production schedule. It is the reason for replacing components, only when the machine is damaged suddenly. The purpose of the study is to determine the type of machine that requires periodic maintenance, and critical components, along with how much reliability if applied through an information system. The case study method carried out is a quantitative method by processing data according to preventive maintenance. The analysis is carried out by determining the engine and critical components and then calculating the meantime to failure (MTTF) and mean time to repair (MTTR) to get the value of age replacement, availability, reliability, and downtime. The results achieved are increased availability and reliability and decreased total downtime by implementing proposed preventive maintenance for ladle, auto spray and heater components.
3. Introduction:
Various efforts were made by manufacturing companies to improve performance, by conducting timely production processes, controlling raw material supplies, and distributing products to distributors on time, thus improving service to customers. The production process was based on good scheduling, material control to prevent the occurrence of material running out, product distribution according to the needs of distributors and customers. In manufacturing companies, the smoothness of the production process affects the achievement of their targets. To achieve good performance, machines must have a maintenance system so that they can have optimal operation when used. However, in practice, many manufacturing industries still focus more on the production process and pay less attention to preventive measures to reduce machine damage during the production process. The object studied is a company where the tight production schedule causes maintenance activities to get less priority. Replacement of components is often only done when there is a sudden machine breakdown. This causes many die casting machines to experience disturbances when operated, which is why it is essential to implement a preventive maintenance system.
4. Summary of the study:
Background of the research topic:
The research addresses the common industrial problem where tight production schedules lead to neglected preventive maintenance, resulting in sudden and costly machine breakdowns. The study focuses on a die casting department where 16 machines are essential for production.
Status of previous research:
The paper acknowledges that while maintenance systems exist, many companies, like the one studied, still rely on reactive maintenance (fixing things after they break) rather than proactive, preventive measures. It also notes the potential for information systems to automate data processing and calculations for maintenance scheduling.
Purpose of the study:
The study aims to:
1. Determine which die casting machine requires the most urgent periodic maintenance.
2. Identify the critical components on that machine that cause the most frequent breakdowns.
3. Calculate the optimal time interval for preventive maintenance and replacement of these components.
4. Quantify the potential increase in reliability and decrease in downtime if this new maintenance plan is implemented, supported by an information system.
Core study:
The core of the study is the application of the age replacement method to historical failure and repair data from a die casting facility. By calculating MTTF and MTTR for critical components, the researchers developed a data-driven preventive maintenance schedule designed to minimize downtime, increase reliability, and reduce costs compared to the existing reactive maintenance policy.
5. Research Methodology
Research Design:
The research is a descriptive analytic study using a quantitative method. It follows a structured sequence: a preliminary study to identify problems, scoping of preventive maintenance theories, data collection, data processing and analysis using the age replacement method, and finally, the design of a supporting information system.
Data Collection and Analysis Methods:
Data on engine damage, component failures, repair times, and operational costs were collected for the period of January 2019 to December 2020. The analysis involved:
- Calculating total downtime for each machine to identify the most critical one.
- Using a Pareto chart to identify the critical components of that machine.
- Calculating Mean Time To Failure (MTTF) and Mean Time To Repair (MTTR) for the critical components.
- Using the age replacement model to determine the optimal preventive replacement time (tp) that minimizes the downtime rate D(tp).
Research Topics and Scope:
The study is focused on preventive maintenance modeling for die casting machines in a specific automotive parts manufacturing company. The scope is limited to analyzing historical breakdown data to propose an optimal maintenance schedule for the most critical machine and its key components, and designing a conceptual information system to support this process.
6. Key Results:
Key Results:
- The Die Casting-07 (DC-07) machine was identified as the most critical, with the highest total downtime of 5,745 minutes (12.20% of the total). (Table 1)
- A Pareto analysis of the DC-07 machine identified the ladle, auto spray, and heater as the critical components, accounting for 91.6% of its failures. (Figure 2)
- Optimal preventive replacement intervals were calculated: 108 hours for the ladle, 506 hours for the auto spray, and 320 hours for the heater. (Table 4)
- The proposed schedule increased component reliability by 92.44% (ladle), 129.25% (auto spray), and 80.07% (heater). (Table 6)
- Total downtime for these components was reduced by 53.04%. (Table 7)
- Significant cost savings were achieved, ranging from 24.73% to 38.90% depending on the component. (Table 8)
Figure Name List:
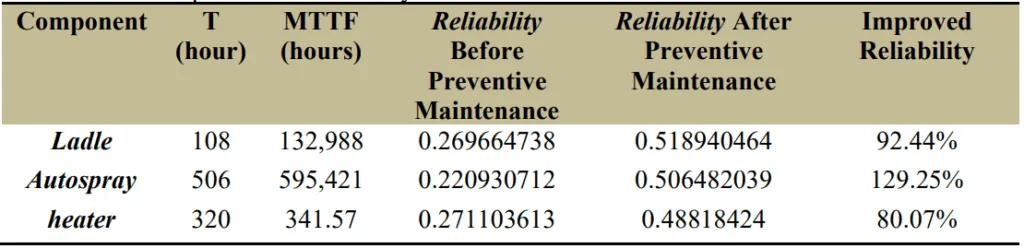


- Figure 1 Methodology Research
- Figure 2. The critical components of damage
- Figure 3. [No Figure 3 is present in the document]
- Figure 4 Use Case Diagram
7. Conclusion:
Based on the calculations, the die casting machine-07 is a critical machine with ladle, auto spray, and heater identified as its critical components. The study determined that preventive replacement should occur at 108 hours for the ladle, 506 hours for the auto spray, and 320 hours for the heater. By implementing this schedule, reliability is significantly increased (92.44% for ladle, 129.25% for auto spray, and 80.07% for heater). The authors conclude that an information system application can support these maintenance activities by streamlining data collection and performance calculations. The company is advised to pay close attention to the DC-07 machine and its components to maintain performance.
8. References:
- Ab-samat, H., L. N. Jeikumar, E. I. Basri, N. A. Harun, “Effective Preventive Maintenance Scheduling: A Case Study," Proc. 2012 Int. Conf. Ind. Eng. Oper. Manag. Istanbul, Turkey, pp. 1249–1257, 2012.
- Angius, A., M. Colledani, L. Silipo, A. Yemane, “Impact of Preventive Maintenance on the Service Level of Multi-stage Manufacturing Systems with Degrading Machines,” IFAC-PapersOnLine, vol. 49, no. 12, pp. 568–573, 2016, doi: 10.1016/j.ifacol.2016.07.696. 2016
- Basri, E.I., I. H. A. Razak, H. Ab-Samat, S. Kamaruddin, “Preventive maintenance (PM) planning: A review,” J. Qual. Maint. Eng., vol. 23, no. 2, pp. 114-143, doi: 10.1108/JQME-04-2016-0014. 2017
- Duarte, J.A.C., J. C. T. A. Craveiro, T. P. Trigo, "Optimization of the preventive maintenance plan of a series components system,” Int. J. Press. Vessel. Pip., vol. 83, no. 4, pp. 244-248, doi: 10.1016/j.ijpvp.2006.02.016. 2006
- Hardt, F., M. Kotyrba, E. Volna, R. Jarusek, “Innovative approach to preventive maintenance of production equipment based on a modified tpm methodology for industry 4.0," Appl. Sci., vol. 11, no. 15, 2021, doi: 10.3390/app11156953. 2021
- Purnama, C., “Analyze Machine Maintenance Cost With Corrective Method and Preventive Method To Increase Production Result," Int. J. Bus. Rev. (The Jobs Rev., vol. 2, no. 1, pp. 1–8, 2019, doi: 10.17509/tjr.v2i1.15307. 2019
- Qian, F., K. Dong, “The Open Cybernetics & Systemics Optimizing Preventive Maintenance of Used Equipment for Lease Abstract :," no. Cm, doi: 10.2174/1874110X0171101008 2017
- Zahedi, Z., A. Salim, “Integrating Preventive Maintenance Scheduling As Probability Machine Failure And Batch Production Scheduling," ComTech Comput. Math. Eng. Appl., vol. 7, no. 2, p. 105, doi: 10.21512/comtech.v7i2.2247. 2016
Expert Q&A: Your Top Questions Answered
Q1: What was the single biggest benefit identified in this study for improving die casting operations?
A1: The single biggest benefit was a 53.04% reduction in total machine downtime, which directly increases production availability. This is detailed in Table 7 of the paper, "Comparison of Average Total Downtime Components Before and After Preventive Maintenance".
Q2: How does this research compare to the traditional "OEM-recommended" maintenance schedule?
A2: The paper's Conclusion
section notes that maintenance should be based on the machine's actual condition, as each operates in a different environment, making generic OEM predictions less accurate. This study's approach uses real-world failure data from the specific machine to create a tailored, more effective schedule.
Q3: Is this finding applicable to all die casting machines, or just the DC-07 model studied?
A3: The specific replacement times (e.g., 108 hours for the ladle) are for the DC-07 machine under the conditions studied. However, the Methodology
section outlines a quantitative process (identifying critical machines, then components, then calculating MTTF/MTTR) that can be applied to any machine in any die casting facility to find its own optimal maintenance schedule.
Q4: What specific measurement or technique did the researchers use to determine when to replace parts?
A4: The researchers utilized the "age replacement method," as stated in the Abstract
and Methodology
. This involved calculating the Mean Time To Failure (MTTF) and Mean Time To Repair (MTTR) from historical data to find the optimal replacement interval that results in the minimum downtime rate.
Q5: According to the paper, what are the most important components to monitor on a die casting machine to prevent failure?
A5: For the most critical machine studied (DC-07), the Pareto analysis in Figure 2 clearly identifies the ladle, auto spray, and heater as the most critical components, collectively responsible for over 90% of the downtime.
Q6: What is the direct, practical takeaway from this paper for a die casting facility?
A6: The core takeaway is that by systematically collecting and analyzing your own machine failure data, you can create a preventive maintenance schedule that is far superior to a reactive or generic approach, leading to dramatic improvements in reliability, downtime, and cost, as concluded in the paper, "Preventive Maintenance Modeling on Die Casting Machines with Information Systems".
Conclusion & Next Steps
This research provides a valuable roadmap for transforming maintenance from a costly, reactive fire-drill into a strategic, value-adding function. The findings offer a clear, data-driven path toward increasing machine availability, improving component reliability, and optimizing maintenance expenditures.
At CASTMAN, we are dedicated to applying the latest industry research to solve our customers' most challenging die casting problems. If the issues of unplanned downtime and high maintenance costs discussed in this paper resonate with your operational goals, contact our engineering team to discuss how we can help you implement these advanced principles in your components and achieve new levels of production efficiency.
Copyright
- This material is a paper by "Tri Pujadi, Bahtiar H. Simamora, Vikas Kumar, Yulia Magdalena, Witarsjah, Yunita Kartika Sari, Satya Windy". Based on "Preventive Maintenance Modeling on Die Casting Machines with Information Systems".
- Source of the paper: The paper was published in the Proceedings of the International Conference on Industrial Engineering and Operations Management, Monterrey, Mexico, November 3-5, 2021.
This material is for informational purposes only. Unauthorized commercial use is prohibited.
Copyright © 2025 CASTMAN. All rights reserved.