This technical brief is based on the academic paper "Process Selection on the Basis of Time Cost and Quality for Development Components of Aluminium Bracket" by Piyush Shukla, published in the International Journal for Multidisciplinary Research (IJFMR) (Volume 6, Issue 4, July-August 2024). It is summarized and analyzed for HPDC professionals by the experts at CASTMAN.
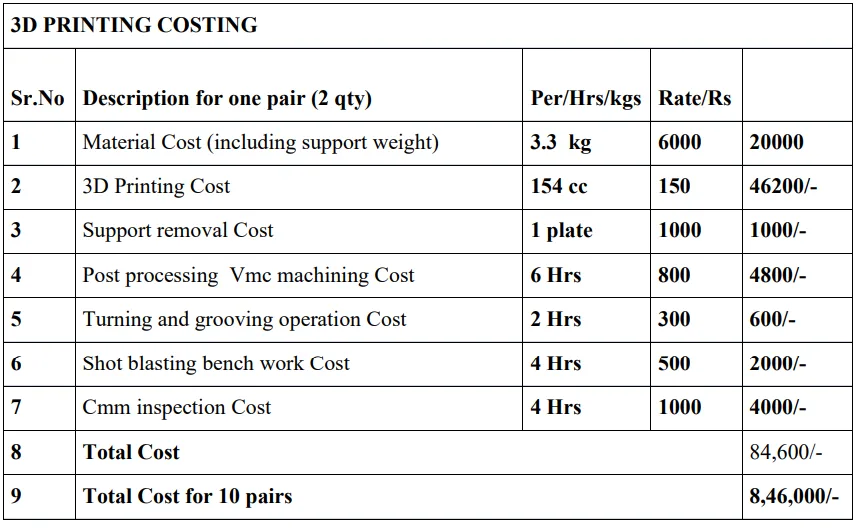
Keywords
- Primary Keyword: Process Selection for Aluminum Prototypes
- Secondary Keywords: Proto Die Casting, Soft Tooling, 3D Printing DMLS, VMC Machining, Aluminum Bracket, Time Cost Quality Analysis, HPDC Prototyping
Executive Summary
- The Challenge: Selecting the most efficient manufacturing process for low-volume "commissioning quantities" (e.g., 10-20 units) of an aluminum bracket needed for assembly trials and testing before committing to expensive mass-production tooling.
- The Method: The research conducted a direct comparison of three processes: Direct Metal Laser Sintering (3D Printing), VMC Machining from a solid block, and Proto Die Casting (DCD) using a soft, unhardened tool. The comparison was based on total time, final cost, and part quality (dimensional accuracy and material properties).
- The Key Breakthrough: While all three methods produced dimensionally accurate parts, Proto Die Casting was the clear winner, delivering components with production-intent material properties at the lowest cost—less than half the cost of 3D printing and more economical than VMC Machining.
- The Bottom Line: For prototype or trial quantities beyond one or two units, Proto Die Casting offers the optimal balance of cost, time, and quality, making it the most strategic choice before scaling to mass production.
The Challenge: Why This Research Matters for HPDC Professionals
Engineers and project managers frequently face a critical decision early in the product development cycle: how to produce a small batch of high-fidelity metal parts for fitment, assembly trials, and functional testing. The choice of manufacturing process at this "proto" or "commissioning" stage has significant implications for project timelines, budget, and the quality of feedback received before freezing a design for mass production.
As the study highlights, processes like 3D printing and CNC machining are common choices. However, they may not produce a part that is truly representative of a final die-cast component, either in cost structure or material properties. This research directly addresses the question: for a commissioning quantity of approximately 20 aluminum brackets, which process provides the best combination of speed, cost-effectiveness, and quality?
The Approach: Unpacking the Methodology
To find a definitive answer, the researcher conducted a practical experiment centered on manufacturing an aluminum alternator bracket. Three distinct manufacturing paths were evaluated:
- 3D Printing (DMLS): An additive manufacturing process (Direct Metal Laser Sintering) where the part is built layer-by-layer from AlSi10Mg powder. This is often perceived as the fastest method for complex, one-off parts.
- VMC Machining: A traditional subtractive process where the bracket was machined from a solid block of Al6061 aluminum using a Vertical Machining Center (VMC).
- Proto Die Casting (Soft Tooling): This process uses a die casting die with its core and cavity components left in a "soft" (unhardened) condition. This drastically reduces tooling cost and time compared to a fully hardened production die, making it suitable for lower-volume runs. The cast parts were made from an aluminum alloy intended for the final product.
Each process was meticulously evaluated against three core parameters: Time (total lead time for 10 pairs/20 components), Cost (detailed breakdown of material, tooling, and processing), and Quality (dimensional accuracy measured by CMM and material properties including composition and hardness).
The Breakthrough: Key Findings & Data
The results of the comparative study provide a clear, data-driven framework for process selection.
Finding 1: Cost - Proto Die Casting is Dramatically More Economical.
For a batch of 10 pairs (20 parts), Proto Die Casting was the undisputed cost leader at ₹3,75,900. VMC Machining was slightly more expensive at ₹3,98,300. 3D Printing was prohibitively expensive by comparison, costing ₹8,50,000—more than double the cost of the other methods. This finding directly challenges the perception that additive manufacturing is always a cost-effective solution for low volumes.Finding 2: Time - 3D Printing is Fastest, but Proto DCD is Highly Competitive.
3D printing had the shortest lead time at 15 days. However, both VMC Machining and Proto Die Casting were completed in a very comparable 17 days. The two-day difference is often negligible in a development timeline, especially when weighed against the massive cost savings offered by die casting.Finding 3: Quality - Proto Die Casting Delivers the Most Representative Part.
This is where the most critical distinction lies for functional testing.- Dimensional Accuracy: All three processes successfully produced parts within the required geometrical tolerances, as confirmed by CMM inspection (Table 2.0).
- Material Properties: The Proto Die Cast sample delivered a hardness of 97 HB, falling perfectly within the target range (95-100 HB) for the final component. The VMC machined part (from Al6061) had a lower hardness of 81 HB, while the 3D printed part had a significantly higher hardness of 121 HB. For tests where mechanical performance is key, the Proto DCD part is the only one that truly reflects the final production intent.
The overall results are powerfully summarized in the paper's result chart (Graph 1.3), which visually confirms Proto Die Casting's superior balance of low cost, competitive timing, and top-ranked quality.
Graph 1.3 from the paper, visually comparing the three processes on Quality Rank, Cost, and Days.
Practical Implications for HPDC Products
Based strictly on the paper's results and conclusions, these findings have direct, actionable implications for your manufacturing and product development strategies.
- For Process Engineers: The findings in "5.3 Result on time cost and quality" suggest that for any commissioning run larger than a few units, Proto Die Casting should be the default consideration. It provides the most realistic data on part performance and manufacturability before committing to six-figure, hardened tooling.
- For Quality Control: The material comparison in Table 2.1 is critical. It proves that prototypes from different processes are not interchangeable for performance testing. Relying on a 3D printed or machined prototype for validation could lead to inaccurate conclusions about the final product's strength and durability. Proto DCD provides the most reliable samples.
- For Die Design & Procurement: This study validates soft tooling as a powerful strategy. As noted in the abstract, the Proto DCD process is viable for up to one thousand parts. This opens a new tier of "bridge production" that is faster and cheaper than full-scale tooling, allowing you to get to market faster or fulfill early orders while the main die is being manufactured.
Paper Details
Process Selection on the Basis of Time Cost and Quality for Development Components of Aluminium Bracket
1. Overview:
- Title: Process Selection on the Basis of Time Cost and Quality for Development Components of Aluminium Bracket
- Author: Piyush Shukla
- Year of publication: 2024
- Journal/academic society of publication: International Journal for Multidisciplinary Research (IJFMR), Volume 6, Issue 4, July-August 2024
- Keywords: Proto DCD, Die Casting, 3D printing, VMC machining, Time, Cost, Quality
2. Abstract:
Development of various new processes has reduced the development of tooling while Designing of Aluminium Component before going to mass production by Dies. The selection of the Process to manufacture Proto quality of Aluminium is not significant. In present research is an attempt to prove that Die Casting Die in soft condition die is also recommended process for commissioning quantity of aluminium component because for prototyping one or two quantity are sufficient. Proto DCD process is also Compared with Time, Cost & quality parameters on this basis process can be selected only for maximum one thousand quantity requirement.
3. Introduction:
In new product development, selecting the right manufacturing process for an assembly part is crucial for checking feasibility and for trial commissioning. The best approach is to consider manufacturing throughout the design process to create a design that is easier and less costly to produce. While hundreds of processes exist, the choice depends on drivers like product quality, tooling cost, processing time, labor skill, and material availability. This study focuses on selecting a process for developing an aluminum alternator cover for the automotive industry, specifically for the "part development process" that precedes mass production.
4. Summary of the study:
Background of the research topic:
Before mass production via die casting, it is necessary to produce a small number of "tryout parts" for assembly checks. The selection of a manufacturing process for these prototypes is a critical decision. This study investigates the best method for producing a commissioning quantity (minimum 20 components) of an aluminum bracket.
Status of previous research:
The paper notes a research gap in direct, practical comparisons of 3D printing, VMC machining, and soft tool die casting specifically on the basis of time, cost, and quality for prototype development. While these processes are known, their comparative performance for this specific application has not been well-documented.
Purpose of the study:
The objective is to determine which manufacturing process—3D printing, VMC machining, or Proto Die Casting (soft tool)—is most suitable for producing more than one prototype (specifically a commissioning quantity of 20 components). The selection is based on three key parameters: process time, comparative cost, and final part quality (material and dimensional).
Core study:
The study performs a hands-on comparison of the three manufacturing processes to produce an aluminum bracket. It includes detailed time calculations (Table 1.2, 1.5, 1.9), comprehensive cost breakdowns (Table 1.4, 1.8, and the 3D printing cost table on page 5), and quality analysis through CMM dimensional reports (Table 2.0) and material/mechanical property comparisons (Table 2.1).
5. Research Methodology
Research Design:
The study employs a comparative experimental design. A single component, an aluminum bracket, is manufactured using three different methods:
1. Direct Metal Laser Sintering (DMLS) 3D Printing.
2. VMC Machining from a solid block.
3. Proto Die Casting using a soft (unhardened) tool.
Data Collection and Analysis Methods:
- Time: Total job time was calculated by summing the hours for each step in the process, from design and preparation to finishing and inspection.
- Cost: Detailed Bill of Materials (BOM) and costing sheets were created for each process, accounting for material, machine time, labor, tooling, and other expenses.
- Quality:
- Dimensional: Parts from all three processes were measured on a Coordinate Measuring Machine (CMM) to compare against nominal dimensions and tolerances.
- Material: The chemical composition and mechanical properties (specifically Tensile Strength, Yield Strength, Elongation, and Brinell Hardness) of the final parts were tested and compared.
Research Topics and Scope:
The research is specifically focused on process selection for a commissioning trial quantity of 20 aluminum brackets. The findings are intended to guide decisions for similar low-to-medium volume prototyping needs (up to 1000 pieces as per the abstract) before investing in hardened tooling for mass production.
6. Key Results:
Key Results:
The study found that for a commissioning quantity of 20 aluminum brackets:
- Cost: Proto Die Casting (₹3,75,900) is the most cost-effective method, followed by VMC Machining (₹3,98,300). 3D Printing is the most expensive by a large margin (₹8,50,000).
- Time: 3D Printing is the fastest (15 days), but Proto Die Casting and VMC Machining are very close behind (17 days).
- Quality: All processes met dimensional requirements. However, the Proto Die Cast part was superior in material quality, with its hardness (97 HB) and composition being the most representative of a final mass-produced component.
Figure Name List:
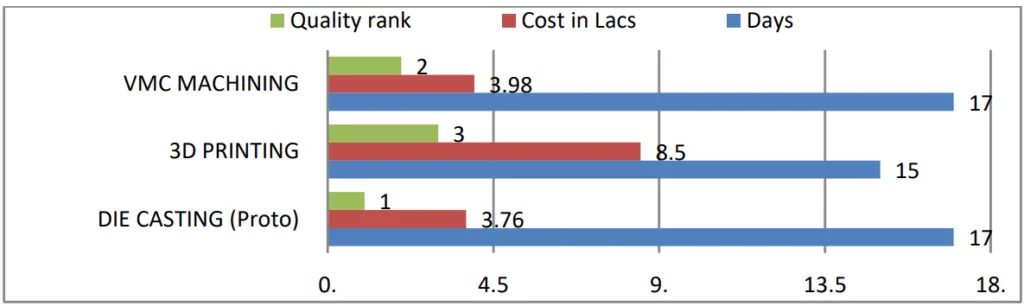
- Figure 2.2 Die casting machine
- Table 1.1 component specification
- Table 1.2 3D printing time calculation
- Table 1.4 Macining Cost
- Table 1.5 Machining time calculation
- Table 1.6 feasibility specifications of Die castings
- Table 1.7 Detailed BOM and costing
- Table 1.8 Proto Dcd Costing
- Table 1.9 Proto Dcd time calculations
- Table 2.0 Comparison of Dimensions
- Table 2.1 Comparison of Material properties.
- Table 2.2 Result values.
- Graph 1.3 Result chart.
7. Conclusion:
Implementation of 3D printing was the suitable process which was fulfilling the purpose of this experiment in proto type and only for one or two component as the result better time saving process. But in comparison with Casting VMC and Proto die casting, 3D printing is found very Costly. With VMC machining process material composition did not matched with the required material composition. When tried with Proto Die casting (Soft die) Tool cost of ten samples found less than all three process. Final process of mass production is also Die casting Die so more cost and time saving reported by this experimental research.
8. References:
- [The full list of 32 references is available in the original paper on pages 19-20.]
Expert Q&A: Your Top Questions Answered
Q1: What was the single most critical factor identified in this study for selecting a process for commissioning quantities?
A1: The study concluded that the optimal balance of cost, time, and quality was the critical factor. While 3D printing was fastest, its extreme cost and non-representative hardness made it unsuitable. Proto Die Casting provided the best overall value, with the lowest cost and the most accurate material properties, as detailed in the "5.3 Result on time cost and quality" section and Table 2.2.
Q2: How does this research's recommendation of Proto Die Casting compare to the common industry practice of using 3D printing for prototypes?
A2: The paper's conclusion clarifies this perfectly. It states that 3D printing is suitable for "one or two component" prototypes, likely for fitment or visual models. However, for commissioning quantities needed for functional trials, this research proves Proto Die Casting is far superior due to its lower cost and more representative material properties.
Q3: Is this finding applicable to all types of alloys, or a specific one?
A3: The research was specifically conducted comparing parts made from Al6061 (VMC Machining) and AlSi10Mg (3D Printing and Proto Die Casting), as shown in the material comparison in Table 2.1. The direct conclusions are most applicable to these alloys, and applicability to others would require further investigation.
Q4: What specific measurement techniques did the researchers use to verify part quality?
A4: The researchers verified dimensional quality using a CMM (Coordinate Measuring Machine), with results detailed in Table 2.0. Material quality, including chemical composition and mechanical properties like hardness, was evaluated through laboratory testing, with results presented in Table 2.1.
Q5: According to the paper, what is the main area for future development based on these findings?
A5: The "6.2 FUTURE SCOPE" section states that the same proto die can be modified for engineering changes (ECRs) and later upgraded with hardened inserts. This would allow the tool to be treated as a regular die casting die capable of producing up to 100,000 shots, offering a path for significant cost reduction in final tooling.
Q6: What is the direct, practical takeaway from this paper for a die casting facility?
A6: The core takeaway is that offering "Proto Die Casting" with soft tooling is a highly competitive strategy for capturing prototype and low-volume initial production runs. It provides customers with a faster, cheaper, and more accurate alternative to 3D printing and machining for quantities beyond a few pieces, as strongly supported by the overall results of the paper, "Process Selection on the Basis of Time Cost and Quality for Development Components of Aluminium Bracket".
Conclusion & Next Steps
This research provides a valuable, data-driven roadmap for navigating the critical prototyping stage of product development. By moving beyond assumptions and comparing real-world data, the findings offer a clear path toward improving quality, reducing costs, and making more informed decisions before committing to high-volume production. The conclusion is clear: for commissioning-level quantities, Proto Die Casting is not just a viable option; it is the superior one.
At CASTMAN, we are dedicated to applying the latest industry research to solve our customers' most challenging die casting problems. If the issues discussed in this paper resonate with your operational goals, contact our engineering team to discuss how we can help you implement these advanced principles in your components.
Copyright
- This material is a summary of a paper by "Piyush Shukla". Based on "Process Selection on the Basis of Time Cost and Quality for Development Components of Aluminium Bracket".
- Source of the paper: https://www.ijfmr.com/
This material is for informational purposes only. Unauthorized commercial use is prohibited.
Copyright © 2025 CASTMAN. All rights reserved.