This article introduces the paper "PROPOSAL OF A CLASSIFICATION OF DEFECTS OF HIGH-PRESSURE DIECAST PRODUCTS".
1. Overview:
- Title: PROPOSAL OF A CLASSIFICATION OF DEFECTS OF HIGH-PRESSURE DIECAST PRODUCTS
- Author: E. Gariboldi, F. Bonollo, M. Rosso
- Publication Year: 2007
- Publishing Journal/Academic Society: la metallurgia italiana
- Keywords: high-pressire die-casting, defects, classification
2. Research Background:
- Social/Academic Context of the Research Topic:
The paper addresses the ongoing efforts of the Working Group (WG) "Quality of High Pressure DieCast (HPDC) products" within the Technical Committee (TC) "High pressure diecasting" of the Italian Association of Metallurgy. A primary objective of this WG is to develop and disseminate common tools that enable foundries to establish proper and comparable quality standards for HPDC products. Defects are recognized as a critical feature of die-cast components, significantly impacting their properties and functionality. Numerous studies have documented the prevalence of defects in aluminum low pressure and high pressure diecast products [1, 2, 3, 4a, 5]. A statistical analysis conducted by the "Quality of high pressure diecast products" WG, involving 47 Italian foundries and encompassing 193000 tons of Al alloys annually [6], highlighted the economic importance and application fields of HPDC products (Fig. 1a). This survey underscored the necessity for standardized quality control in the HPDC industry. - Limitations of Existing Research:
An initial review of existing literature and industrially adopted defect classifications for components cast in metallic dies revealed a significant limitation: the prevalent mixing of geometry-based and origin-based approaches. This mixing often results in a wide range of hybrid classifications that can be inconsistent and difficult to apply uniformly across different foundries and applications. Furthermore, existing classifications may not adequately address the specific needs and control operations relevant to HPDC products. - Necessity of the Research:
The preparation and dissemination of common tools for defining quality standards is a crucial target for the WG. The fundamental tool addressed in this paper is a common terminology and classification system for defects in HPDC products. A standardized classification is essential for several reasons:- To enable foundries to define and implement proper, comparable quality standards.
- To facilitate clear communication about defects between foundries, customers, and researchers.
- To provide a basis for analyzing defect data and identifying correlations between defect types, distributions, and origins, ultimately leading to process improvements and enhanced product quality.
- To establish clear criteria for defect identification and rejection of die-cast parts, benefiting both foundries and customers.
3. Research Purpose and Research Questions:
- Research Purpose:
The primary research purpose is to propose a comprehensive, multi-level, hybrid-type classification system specifically for defects in HPDC products. This system aims to provide a structured and practical framework for identifying, categorizing, and understanding defects in HPDC components, ultimately contributing to improved quality control and standardization within the die casting industry. The paper focuses on introducing the general classes of defects defined in Level II of the proposed classification. - Key Research Questions:
- How can defects in HPDC products be effectively classified to support the definition of consistent quality standards across foundries?
- What is the most appropriate structure for a defect classification system that considers both the location/geometry of defects and their underlying metallurgical origins?
- How can a classification system be designed to be practical and user-friendly for foundries, facilitating defect identification and analysis in routine quality control operations?
- Can a common terminology for HPDC defects be established to improve communication and understanding within the industry?
- Research Hypotheses:
While not explicitly stated as formal hypotheses, the research is based on the implicit hypotheses that:- A multi-level, hybrid classification system, incorporating both defect position and metallurgical origin, will provide a more comprehensive and practically useful framework for HPDC defect classification compared to existing mixed approaches.
- A standardized terminology and classification system will enhance communication, facilitate data analysis, and contribute to the establishment of more consistent and comparable quality standards within the HPDC industry.
- Focusing on metallurgical origins in the classification will provide valuable starting points for identifying the root causes of defects and implementing effective corrective actions in the die casting process.
4. Research Methodology
- Research Design:
The research employed a multi-faceted approach, beginning with an initial survey of existing literature and industrially adopted classifications of defects in cast components. This was followed by extensive discussions within the WG "Quality of HPDC products," incorporating valuable contributions from several Italian foundries. The iterative process involved refining and developing a new classification system based on the identified needs and limitations of existing approaches. The proposed classification is presented as a result of this collaborative and analytical design process. - Data Collection Method:
The data collection primarily involved:- Literature Review: Examining published research and existing defect classification systems in die casting and related fields.
- Industrial Survey: Gathering information on defect classifications currently used by foundries, including customer and foundry specifications for aluminum alloy castings.
- Expert Consultation: Collecting input and feedback from members of the WG, representing diverse expertise from foundries and academia. The statistical analysis on HPDC production by Italian foundries [6] also provided valuable context and data on the industry landscape.
- Analysis Method:
The analysis method was primarily qualitative and focused on:- Comparative Analysis: Analyzing and comparing different existing defect classification approaches, identifying their strengths and weaknesses, and recognizing common themes and hybrid methodologies.
- System Synthesis: Developing a new classification system by synthesizing insights from the literature review, industrial survey, and expert consultation. This involved structuring the classification into multiple levels and defining categories based on defect position and metallurgical origin.
- Logical Deduction: Reasoning about the relationships between defect origins, manifestations, and detection methods to create a coherent and practical classification framework.
- Research Subjects and Scope:
The research specifically focused on defects in High Pressure DieCast (HPDC) products made from aluminum alloys. The scope was limited to metallurgically-based defects, excluding defects directly related to post-ejection operations such as handling, finishing, and machining, although acknowledging their potential contribution to product rejection. The classification aims to be applicable to a broad range of HPDC components and production scenarios within the Italian die casting industry.
5. Main Research Results:
- Key Research Results:
The primary outcome of the research is the proposed multi-level, hybrid-type classification of defects for HPDC products, schematically illustrated in Fig. 5 (Italian version) and Fig. 6 (English version). This classification system is structured into three levels:- Level I: Defect Position (Geometry/Location Approach): Defects are initially grouped based on their location within the component and the typical control operations used for detection. This level defines three broad categories:
- Internal Defects (DIFETTI INTERNI / INTERNAL DEFECTS): Defects located within the bulk of the casting.
- Surface Defects (DIFETTI SUPERFICIALI / SURFACE DEFECTS): Defects observable on the surface of the casting, including sub-surface defects close enough to affect surface features.
- Geometry Defects (DIFETTI DI GEOMETRIA / GEOMETRAL DEFECTS): Defects related to deviations from the intended shape and dimensions of the casting.
- Level II: Metallurgical Origin Approach: Defects are further classified into classes based on their general metallurgical origin. Analogous classes are defined for both internal and surface defects, highlighting the shared origins. These classes include:
- Shrinkage defects (Difetti da ritiro / Shrinkage defects): Related to material volume contraction during solidification.
- Gas-related defects (Difetti da gas / Gas-related defects): Related to the presence of gas (e.g., hydrogen, air entrapment).
- Filling-related defects (Difetti di riempimento / Filling-related defects): Related to incorrect or anomalous liquid metal flow during die filling.
- Undesired phases (Fasi indesiderate / Undesired phases): Related to the presence of phases different from the desired microstructure.
- Thermal contraction defects (Difetti da contrazione termica contrastata / Thermal contraction defects): Related to thermal stresses during solidification and cooling.
- Metal/die interaction defects (Difetti da interazione metallo/stampo / Metal/die interaction defects): (Surface defects only) Related to interactions between the molten metal and the die material.
- Level III: Specific Defects: This level provides a detailed terminology and definition for specific defect types within each Level II class. The terminology often further specifies the metallurgical origin. Examples include:
- Level II: Gas-related defects; Level III (Internal): Hydrogen porosity, Air/vapour/die lubricant entrapment porosity.
- Level II: Filling-related defects; Level III (Surface): Flow defects (veins, porosity) laminations, cold shots.
- Level II: Shrinkage defects; Level III (Internal): Interdendritic/ layer porosity/ blowhole.
- Level II: Metal/die interaction defects; Level III (Surface): Erosion, ejection marks, soldering, corrosion of the die, in cavity build-up.
- Level I: Defect Position (Geometry/Location Approach): Defects are initially grouped based on their location within the component and the typical control operations used for detection. This level defines three broad categories:
- Statistical/Qualitative Analysis Results:
- Figure 1: Presents data from a statistical analysis [6] showing:
- Fig. 1a: Turnover for Italian and foreign markets for different application fields of Al-alloy HPDC products. The automotive sector represents a significant portion of the turnover, followed by electromechanics and domestic appliances.
- Fig. 1b: Distribution of HPDC production (raw material) among five families of die casting parts. "Other diecastings not belonging to previous families" constitutes the largest portion (48.8%), followed by "thin wall (from 0.8 to 3 mm) diecastings" (23.2%) and "diecastings for safety components" (12.3%).
- Figure 2: Illustrates requirements and control methods for two different families of HPDC products [6]: "thin wall (from 0.8 to 3 mm) diecastings" and "Diecastings for safety components." It highlights the varying importance of requirements like pressure tightness, safety, visual aspect, mechanical properties, absence of porosity, and dimensional requirements for these different product families. Correspondingly, the control methods employed (Destructive testing, Dye penetrant, Pressure tightness, Dimensional control, X-rays, Visual Inspection) also differ in emphasis.
- Figure 3: Displays results from an analysis of rejection causes of HPDC products [7]. It shows that a significant portion of rejections are attributed to visually detected imperfections on machined surfaces (52%) and castings failing pressurized leak tests (28%). The analysis further breaks down the metallurgical origins of defects causing rejections during machining operations and fracture during machining/assembly, highlighting the prevalence of Gas Porosity, Cold Laps, and Shrinkage Porosity. For example, Gas Porosity is identified as a major contributor to castings displaying problems during machining (75%), castings that fractured during machining or assembly (85%), and visually detected imperfections (57.1%).
- Figure 4: Presents examples of existing defect classifications:
- Fig. 4a: Classification of casting defects according to Campbell [8]. This classification broadly categorizes defects into Gas Porosity, Shrinkage Porosity, and Hot Tearing, cracks.
- Fig. 4b: Classification of defects in Light Alloys castings according to Cocks [9]. This classification is more detailed, categorizing defects into Surface defects (Cold shut, Smooth irregularities, Rough surface) and Internal defects (Gas porosity, Shrink porosity), with further sub-types within each category.
- Figures 5 & 6: Present the proposed HPDC defect classification in Italian and English versions, respectively, outlining the three levels of classification and providing examples of defect types within each category.
- Figure 1: Presents data from a statistical analysis [6] showing:
- Data Interpretation:
The proposed classification system is designed to be practically relevant for foundries by:- Level I (Position): Aligning with typical inspection operations and considering the functional impact of defects based on their location.
- Level II (Metallurgical Origin): Providing insights into the underlying causes of defects, offering starting points for process optimization and corrective actions.
- Level III (Specific Defects): Offering a detailed and standardized terminology for precise defect identification and communication.
The analysis of rejection causes (Fig. 3) reinforces the importance of addressing metallurgical defects, particularly gas porosity, shrinkage porosity, and cold laps, to reduce product rejections in HPDC manufacturing. The existing classifications (Fig. 4) demonstrate the need for a more structured and comprehensive system, which the proposed multi-level classification aims to provide.
- Figure Name List:
- Fig. 1: a) Turnover for Italian and foreign markets for different application fields of Al-alloy HPDC products; b) Distribution of HPDC production (raw material) among the 5 family of die casting parts. [6].
- Fig. 2: Requirements (top) and control methods (bottom) for two different families of HPDC products [6].
- Fig. 3: Results of an analisys of the rejection causes of HPDC products [7].
- Fig. 4: Classification of casting defects according to Campbell 8 and Cocks 9.
- Fig. 5: Proposed classification of HPDC defects (Italian version).
- Fig. 6: Proposed classification of HPDC defects (English version).
- Fig. 7: Example of gas-related internal and surface defects.
- Fig. 8: Example of filling-related internal and surface defects.
- Fig. 9: Example of shrinkage-related internal and surface defects.
- Fig. 10: Example of metal/die interaction surface defects.
![Fig1. a) Fatturato relativo al mercato italiano ed estero nei diversi settori di applicazione dei prodotto pressocolati in lega di alluminio. b) Ripartizione dell’Impiego di lega di alluminio nelle 5 famiglie di getti pressocolati [6].](https://castman.co.kr/wp-content/uploads/Fig1.-a-Fatturato-relativo-al-mercato-italiano-ed-estero-nei-diversi-settori-di-applicazione-dei-prodotto-pressocolati-in-lega-di-alluminio-1024x317.webp)
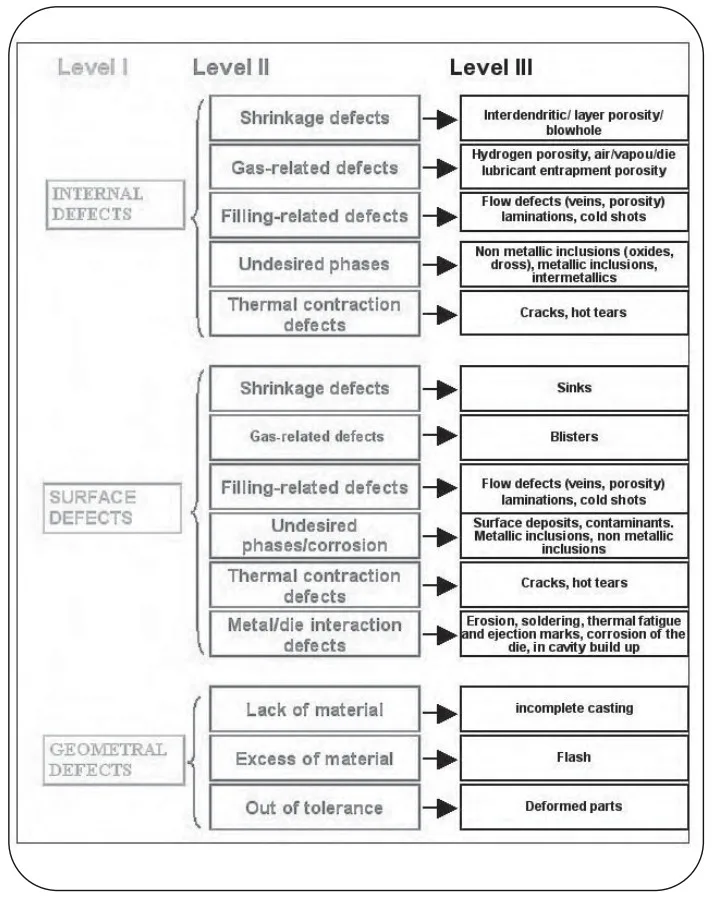
Classificazione proposta per difetti in getti pressocolati (versione inglese).
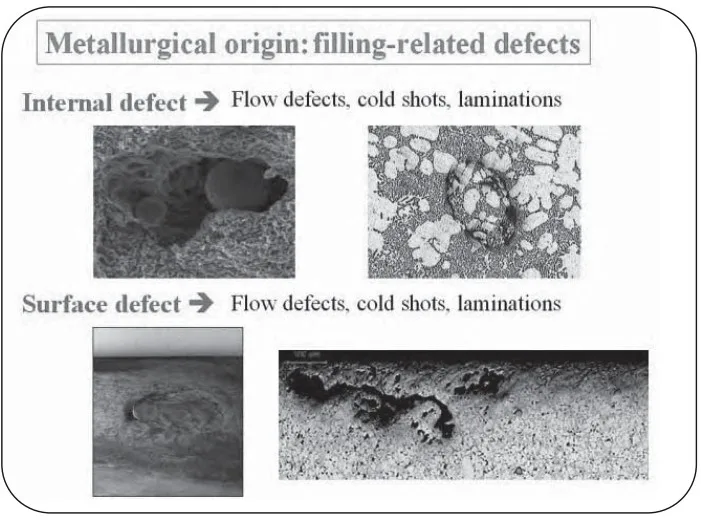
6. Conclusion and Discussion:
- Summary of Main Results:
The paper successfully introduces a multi-level, hybrid classification system for defects in HPDC products. This system classifies defects first by their position (internal, surface, geometry) in Level I, then by their metallurgical origin (gas-related, shrinkage-related, filling-related, thermal contraction, undesired phases, metal/die interaction) in Level II, and finally provides detailed terminology for specific defect types in Level III. The proposed classification aims to address the limitations of existing mixed approaches and provide a more structured and practical tool for the HPDC industry. - Academic Significance of the Research:
The research contributes to the academic field by providing a systematic and comprehensive framework for understanding and classifying defects in HPDC products. It addresses the identified gap in existing literature by moving beyond simple geometry-based or origin-based classifications and proposing a hybrid approach that integrates both perspectives. The work also contributes to the standardization of defect terminology within the die casting research community. - Practical Implications:
The proposed classification system has significant practical implications for the HPDC industry. It offers foundries a valuable tool for:- Defining and implementing consistent quality standards.
- Improving defect identification and communication.
- Analyzing defect data to identify root causes and optimize production processes.
- Establishing clear criteria for defect rejection, benefiting both foundries and customers.
- Facilitating training and knowledge sharing related to defect recognition and prevention.
- Limitations of the Research:
The paper acknowledges that the proposed classification does not directly specify defect/cause correlations. Instead, it provides starting points for identifying potential causes based on the metallurgical origin of defects. The classification is presented as a proposal under development by the WG, and the action of the WG is still ongoing to finalize the multi-language terminology equivalence and compile the official document. Further validation and refinement through broader industry application are anticipated.
7. Future Follow-up Research:
- Directions for Follow-up Research:
Future research and development efforts should focus on:- Completion of the official document: Finalizing the multi-language terminology equivalence and compiling the official document containing the proposed classification and terminology translations.
- Industry Validation and Refinement: Implementing and validating the proposed classification in industrial settings to assess its practicality, effectiveness, and identify areas for further refinement based on real-world application.
- Development of Defect/Cause Correlation Guidelines: Expanding the classification system to include more explicit guidance on defect/cause correlations, potentially through the development of supplementary materials or databases linking specific defects to process parameters and material characteristics.
- Development of Training Materials: Creating training materials and resources for foundries to effectively implement and utilize the proposed classification system in their quality control operations.
- Areas Requiring Further Exploration:
Further exploration is needed in the following areas:- Quantifying the impact of different defect types on the functional performance of HPDC components.
- Developing standardized methods for defect detection and characterization based on the proposed classification.
- Investigating the economic benefits of implementing the proposed classification system in terms of reduced scrap rates and improved product quality.
- Extending the classification system to encompass defects related to post-ejection operations and other aspects of the HPDC manufacturing process.
8. References:
- [1] J.A. FRANCIS. G.M. DELPHINECANTIN. Mat. Sci. Eng., A407 (2005), p. 322.
- [2] C.H. CACARES, B.I. SELLING. Mater. Sci., A220 (1996) р. 109.
- [3] X. YANG, X. HANG, X. DAI, J. Campbell, R.J. Grant. Mater. Sci. Tech., 22 (2006) p. 561.
- [4] J. CAMPBELL. Castings. Butterworth Heinemann, Oxford, 2003. a) p. 204. b) p. 207.
- [5] E. DI RUSSO. "The atlas of microstructures of aluminium casting alloys", Edimet, Brescia 1993.
- [6] F. BONOLLO. Qualità dei getti pressocolati: I risultati di un'indagine svolta nelle fonderie italiane. AIM Seminar "Qualità del pressocolato", Piacenza, 12 April 2006.
- [7] 1, J. BREVICK, “Defect causing rejection of die-casting after machining". NADCA project summary. http://www.diecasting.org/research/results/pdf/ProcessTechnologies.pdf
- [8] J. CAMPBELL, R.A. HARDING. “Casting technology" in TALAT 2.0 cd-rom, EAA, Brossels (2000).
- [9] D.L. COCKS. A proposed simple qualitative classification for die-casting defects. Proceedings Die-casting Conference, Mountreaux, 1997.
- [10] F. BONOLLO, A. TIZIANI. Analisi difettologica di getti in lega leggera e in ghisa. Course AIM "Failure Analysis", Vicenza, 7-8 October 2003.
- [11] W.G. WALKINGTON. Die Casting defects – Causes and solutions, North American Die Casting Association; 1997.
- [12] E. GARIBOLDI. Classificazione di base dei getti pressocolati. Seminary AIM “Qualità del pressocolato: - la situazione attuale e le prospettive di una norma sulle condizioni di fornitura. Piacenza-12 Aprile 2006.
- [13] UNI EN 12258-1 Standard. Aluminiun and amuminium alloys -Terms and difinitions – general terms. February 2001.
9. Copyright:
*This material is E. Gariboldi, F. Bonollo, M. Rosso's paper: Based on PROPOSAL OF A CLASSIFICATION OF DEFECTS OF HIGH-PRESSURE DIECAST PRODUCTS.
*Paper Source: DOI URL (Not available in the provided information)
This material was summarized based on the above paper, and unauthorized use for commercial purposes is prohibited.
Copyright © 2025 CASTMAN. All rights reserved.