Porosity Control in Copper Rotor Die Castings
E. F. Brush, Jr., S. P. Midson, W. G. Walkington, D. T. Peters and J. G. Cowie
Abstract
This paper reports on the results of an investigation to minimize and control the distribution
of porosity in edge-gated copper rotor die castings. A Flow 3-D computer modeling
exercise was used to simulate shot profiles that result in formation of large pores in the end
rings, as well as to predict improved profiles that will reduce or eliminate the residual
porosity. These model results were then tested by die casting a series of copper rotors using
an existing edge-gated rotor die set on a Buhler 750-ton real time shot controlled die
casting machine. Shot profiles are shown to be very instrumental in controlling porosity.
Profiles designed to pre-fill a portion of the gate end ring at the slow shot speed prior to
accelerating to the fast velocity to fill the conductor bars and ejector end ring are shown to
be very effective in minimizing and controlling porosity and to achieve a fairly uniform
distribution of small pores present largely in the end rings. Thermal management of the
entire system is also important to casting quality including metal superheat, and shot sleeve
and die temperatures.
Introduction
High pressure die casting is the most economical process for production of a variety of
complex parts because of its ability to achieve high production rates, final shape with little
machining required, excellent surface finish and adequate properties for many applications.
Certainly these advantages are important to producing the squirrel cage rotor structure of
the induction motor rotor whether cast in aluminum or copper. The high rate of
introduction of liquid metal through the gates into the die cavity filled with air generally
results in some distributed porosity in the structure. As reported at the 2002 Die Casting
Congress, die-cast copper motor rotors built into motors and tested by motor manufacturers
showed little evidence that porosity in the end rings or conductor bars was an issue.1
Rotors were easily balanced and required little in the way of balancing weights. Porosity in
the far end ring of copper rotors appeared to be 2 to 3 percent but did not extend into the
conductor bars. Motor electrical tests consistently showed a 30 to 40 percent reduction in
rotor I2
R losses and overall losses reduced by 14 to 23%. There was remarkable
consistency in rotor-to-rotor results. Low stray load losses determined in the IEEE
Standard 112B test indicated no significant porosity in the conductor bars of the copper
rotors tested. In subsequent work, a set of larger rotors tested by a motor manufacturer was
difficult to balance. Sectioning of the end rings revealed large porosity especially in the
end ring at the ejector end showing as much as 25% voids in some castings and about 8
to10% voids in the rotors selected for electrical tests. Therefore, additional work, reported in this paper, was carried out to determine the origin of the porosity. Both modeling and
experimental casting trials were performed to determine the process conditions required to
significantly reduce porosity to acceptable levels.
Modeling Study
Flow-3D software using computational fluid dynamics methods was used by Walkington
Engineering to model the metal flow to simulate metal flow conditions. Review of the
flow videos and other data from the simulations were used to evaluate the conditions that
would cause large pores in the end rings and conductor bars and to identify process
conditions that would eliminate the large porosity conditions. These simulation methods
were viewed as being a less expensive and less time consuming way to find the optimum
conditions than an extended series of die casting trials. Selected predictions from the
modeling simulations were tested by making a few experimental castings. The model
predicted the location of the larger trapped bubbles. The objective was to find operating
conditions that will eliminate these. The die-cast copper shape modeled is shown in Figure
- The part consists of an end ring at the gate end and an end ring at the ejector end connected
by a series of conductor bars. The bars are formed by channels through the stack of
punched iron rotor laminations (Figure 2). Thus the lamination stack plays the role of the
die for the conductor bars.
The part is edge gated with four approximately semi-circular gates on each side of the
vertical runner. In the die used to produce copper rotors, the cross sectional area of the
gates is 80% of the runner cross section. Several different gating systems were examined
by modeling them and simulating flow conditions to see if they would reduce porosity.
None of these alternative gating systems, which included larger solid gates to eliminate the
reduced gate area, caliper gates to redirect flow entering the gate end ring and tapered pin
gates, showed any benefit, at least within the limited set of parameters tested, and are not
discussed in this paper. Most of the emphasis in the modeling study discussed here involves variation in the
plunger position – speed profile (shot profile). Two approaches were examined. The first
relies on die casting experience to the effect that, while at high speed there is much
turbulence as metal enters the gate and beyond (atomized flow), this turbulence results in a
proliferation of very small and widely dispersed pores but generally tends to keep the large
bubbles from forming. This situation was considered to be of much less concern than
having a few large bubbles or voids. A problem with this approach is the high metal
velocity through the gates which may result in excessive erosion and short die life,
especially when die casting copper at 2200ºF or above.
A second approach examined was to have the molten metal approach and pass the gates at
a relatively slow speed and pre-fill the gate end ring to some extent before increasing the
plunger speed to fill the rest of the die cavity. The idea here was to minimize the turbulence
initially so that the air is pushed ahead of the molten metal front to the vents located on the gate end ring, thereby reducing the trapping of air and formation of large pores. In this
case, the slow initial fill could result in freezing at the gates and an incomplete fill. This
was thought to be a manageable problem with the die system developed for casting the
copper motor rotor. The die system developed for extending die life while die casting
copper uses nickel-base alloy dies that are first preheated and then operated in the
temperature range 1160 to 1200ºF with heat supplied by electrical resistance cartridge
heaters.1
The high operating temperature greatly minimizes the temperature and strain
gradients between the die surface and its interior that lead to heat checking and die failure.
These hot dies allow a somewhat longer casting cycle. A schematic of this die system is
shown in Figure 3.
Simulation of the Base-Line Shot Profile
Sectioning of the end rings from a 15 Hp motor die-cast copper rotor produced with the
shot speed profile of Figure 4 and Table 1 often resulted in the inclusion of a number of
large voids as shown in Figure 5. A modeling run was done to determine if the void pattern
could be predicted.
Basically this profile extends the slow shot so that it will pre-fill about 10% of the gate end
ring before the fast shot speed is reached. Results are shown as frames from Flow 3D
videos. (Note that symmetry of the part allows a simulation to be done on half of the model
thereby reducing computer run time.) It is important to note that these videos show only the
skin of the casting which is shown next to the cavity wall and surrounding any bubbles
present. Thus the casting appears empty where there actually is metal. The videos are then
examined for the skin formation around air bubbles. Porosity was judged by the estimated
bubble content of the gate end ring, the ejector end ring and the conductor bars. The fill
time for a given model (which includes a small amount of time in the runner) is reported as
this is an important factor in controlling surface quality, and is an issue in terms of
premature solidification.
Figure 6 shows the simulation for the gate end ring using this base-line shot profile. The
arrows show the predicted porosity in about the same locations as seen on the sawed cross
section of Figure 5. Figure 7 shows the simulation for the ejector end ring. There are no
large bubbles, but there is considerable trapped air in the bars (arrows) that will get pushed
into the end ring later in the fill. There is some bubble formation in the end ring, but no
bubbles as large as would be expected from the porosity actually found to be present. The
results seem to verify that the simulation is predicting the porosity condition actually
observed in the end rings. However the simulation apparently predicts some air trapped in
the conductor bars because this is the last point to fill, although no large bubbles were
shown at this location by the simulation. Machining by turning a number of rotors ODs to
the point of largest bar thickness invariably showed essentially pore-free conductor bars
with only a few pin head size pores found (see Figure 8). This apparently explains the
excellent properties of motors built with copper rotors, in particular the low stray load loss
component. We conclude that the trapped air in the bars seen in the videos is actually in the
form of small dispersed bubbles. 20% Pre-fill Simulations
Two simulations were done with a slow pre-fill to 20% followed by rapid acceleration. In
the first case, a very fast speed of 450 cm/sec. was used for the fast shot (Figure 9 and
Table 2). The fill time was a rather long 296 msec. because of the slow pre-fill. Figure 10
shows the model simulation with the gate end ring almost full. No bubbles are present
although the area at the arrow might develop some porosity. The ejector end ring also
appears to be pore-free (Figure 11) at this point in the shot, although the simulation
suggests that there would be some trapped air in the conductor bars. This shot profile
appeared to be promising. Bubble formation in the end rings, although not eliminated, had
been reduced to one medium sized bubble in the gate end ring and one fair size bubble in
the ejector end ring.
Another simulation run at 20% pre-fill was done to try to eliminate the trapped air in the
conductor bars. It appeared from the videos of the previous run described in the last
paragraph that the metal would flow rapidly down the gate ring and flow into the bars
further away from the gate at a higher flow rate than for the bars closer to the gate. The
bars further from the gate would catch up and pass the bars closer to the gate trapping air in
the bars. The concept behind this new run was that a slower acceleration to the fast shot
speed would allow more time to develop the flow in the bars adjacent to the gate. In the
previous run, the acceleration from the initial speed to the final fast shot was extremely
rapid. It was hoped that a slower acceleration would give good end rings and reduce the
apparent porosity in the conductor bars. The speed was increased at the end to compensate
for the slower acceleration, but the fill time was still long at 343 msec. The shot profile is
pictured in Figure 12 and Table 3.
The concept of the slower acceleration did not function as hoped and in fact made things
worse. Although there appeared to be no trapped air in the bars, large pore formation in
both end rings was more pronounced.
Delayed Transition with 40% Pre-fill
Finally in this simulation sequence, a pre-fill shot profile with a delayed transition from
slow to fast shot was used (Figure 13 and Table 4). The pre-fill was increased to 40%. The
objective was to accelerate while the metal was filling the gate end ring because some early
simulations had shown that a completely slow fill generated large bubbles later in the fill
cycle. This strategy was quite successful. Several frames of the video showed an incipient
bubble in the gate end ring but this never completely formed as was shown a few
milliseconds later in the fill in Figure 14. A few small bubbles are seen but the objective
was to eliminate the large bubbles. The ejector end ring was equivalent to the best in other
runs and showed no large bubbles. There was no apparent trapped porosity in the bars.
This simulation work shows that there are shot profiles that predict substantially reduced
formation of large trapped air bubbles and porosity. Other combinations could of course be
tried that might further improve the situation. For example, a little slower pre-fill with the
acceleration dragged out some during the gate ring fill would be an interesting shot profile.Experimental Verification of Simulation Predictions
Experimental Details
The plan was to cast copper rotors to verify the predictions from the Flow 3D simulations.
A number of 5.7 in. diameter by 5.25 in. high lamination stacks using the lamination
design of Figure 2 were available. The 750-ton real time shot control Buhler horizontal die
casting machine at Formcast Development, Inc. was used. The die used for the trials is a
commercial two-plate rotor die, edge gated, with a vertical core pull to assist with rotor
stack insertion and ejection of the die-cast rotor. Copper in the form of chopped C10100
wire rod was melted on a shot-by-shot basis using a push-up crucible induction furnace and
a 60 kW power supply. The shot weight was 24 to 26.5 lbs. A nitrogen cover was used to
prevent excessive oxygen pick-up during melting. The heated nickel-base alloy die set
shown in Figure 3 was not available for these trials, so instead an H-13 die set was used.
The end ring die heating was done with a circulating oil heater augmented by direct heating
with a propane heater. Achievable die temperatures measured prior to each shot at six
points on the die faces ranged from 240 to about 600ºF. This is much colder than die
temperatures now being used for commercial production of copper rotors which are
operated at about 1200ºF to achieve long die life.. The shot sleeve was preheated by a band
heater and a propane torch but the temperature was not monitored in all tests. In
production, plans call for a resistance heated and insulated shot sleeve capable of reaching
quite high temperatures to minimize chilling of the molten copper charge.
The machine was programmed for all of these casts to advance the plunger in the slow shot
region from 26 to 50 cm/sec. and then to accelerate rapidly to 400 cm/sec. The
acceleration to the fast shot speed occurred either in the runner prior to the gate or after
pre-filling the gate end ring. A final metal pressure of 13,250 psi. was reached in the
pressure control portion of the shot.
Effect of Melt Superheat
Prior to examining the impact of pre-fill on rotor quality, it was necessary to identify
optimum casting parameters. One parameter that was found to significantly impact rotor
quality was the superheat of the copper melt. A series of casts were run using a pre-fill of
55%, in which the melt temperature was increased in steps.
Figure 15 shows the gate end ring sections for melt temperatures of 2400, 2490, 2580, and
2670ºF. There is a steady improvement with increasing melt temperature with no large
pores visible on the gate end ring cast at the highest temperature. Obviously 2670o
F is an
extremely high melt temperature and the authors do not expect that such superheats would be required for commercial production. As noted earlier, commercial die sets for the
casting of copper rotors require that the nickel-based die inserts be pre-heated to about
1200o
F, and experience with these dies indicated that lower melt superheats are sufficient
to obtain adequate part quality. However, the results from this study clearly indicate that
heat loss from the liquid copper to the cooler shot sleeve, die inserts and lamination stack
must be controlled in order to minimize porosity in the die cast rotors.
Effect of Die Pre-fill
Experience had verified the model simulations that acceleration to the fast shot speed
before the metal reaches the gates invariably resulted in the formation of large pores in
both end rings similar to the cross sections of Figure 5. In the final set of three casting
trials, the amount of pre-fill of the gate end ring was varied. The shot profile was varied so
the speed transition occurred below the gates about half way up the runner, and at pre-fills
of 33% and 55%. The conditions and shot profiles were otherwise as described above
except that the shot sleeve was heated to a higher temperature of about 840ºF. Due to the
high super-heat used in the tests, temperature measurement of the melt was an issue, with
the available thermocouple system unable to measure much above 2350o
F. An estimated
melt temperature of 2600ºF was reached by removing the thermocouple and continuing
heating for 56 seconds past 2350ºF. The results are shown as the sawed cross sections of
Figure 16. Clearly the porosity decreases markedly with pre-fill compared to acceleration
before the metal reaches the gate and is further reduced at the higher pre-fill. This same
series run with a melt temperature of 2400ºF showed considerable porosity with and
without pre-fill. We conclude that, in the die set used in these experiments, the incidence of
large pores in the end rings is reduced with increased melt temperature and with some
degree of pre-fill. Presumably the pre-fill cannot be increased indefinitely with further
increase in part quality. Additional experiments to determine this limit should be
undertaken.
Conclusions
The work reported in this study shows the utility of computer flow simulation in
identifying die casting operating conditions that lead to formation of large pores in the
castings and to predict shot profiles that will significantly minimize or eliminate large
pores caused by trapped air. Simulation showed that operating conditions in use at the time
for developmental studies of die casting the copper motor rotor were likely to result in
large pores as observed. Simulation predicted that changing the shot profile so as to prefill the die cavity beyond the gates to some extent before acceleration of the plunger to the
fast speed would largely eliminate the incidence of large pores in the end rings of the rotor.
Experimental work verified that pre-fill was effective in eliminating the large pores. The
importance of having adequate superheat in the melt was also shown to be an important
factor in minimizing porosity. Rather high melt temperatures were required for casting in
the H-13 dies available for this study. Commercial production of copper rotors uses nickelbase alloy dies operated at 1200ºF and an insulated and heated shot sleeve operated at a
similar temperature. Less superheat is required with this equipment. Acknowledgement
This work was funded by the world copper industry through the International Copper
Association, Ltd. The project was managed by the Copper Development Association Inc.
References
1) D.T. Peters, J.G. Cowie, E.F. Brush, Jr. and S.P. Midson, “Use of High Temperature Die
Materials and Hot Dies for High Pressure Die Casting Pure Copper and Copper Alloys”,
Proceedings of the 2002 Die Casting Congress, Rosemont, IL Sept. 30 – Oct. 2, 2002.
Listing of Figures with Captions
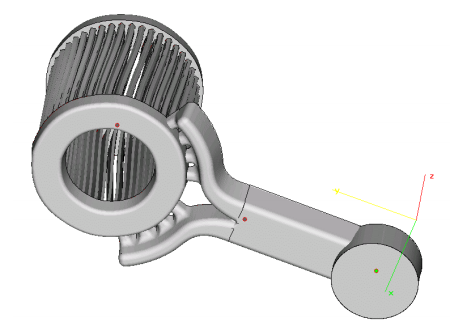
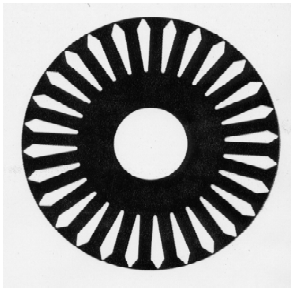
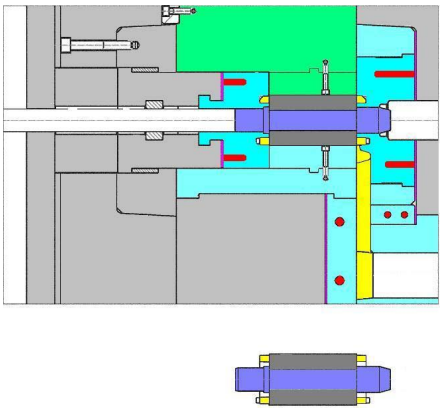
The arbor (dark blue) and the steel laminations (dark grey) are shown as assembled in the insertbelow and in position in the machine. Copper in the biscuit, vertical runner and end rings is
shown in yellow. The nickel alloy end ring inserts and runner die components are shown in
medium blue with electrical resistance heaters in red. These components are backed with
insulation (pink). The vertical core pull is shown in green and the steel platens in light grey.
(Courtesy of DieTec, GmbH).
SHOT SPEED PROFILE
0.00
50.00
100.00
150.00
200.00
250.00
300.00
0 50 100 150 200 250 300 350 400 450 500 550 600
PLUNGER POSITION - MM
PLUNGER SPEED - CM/SEC
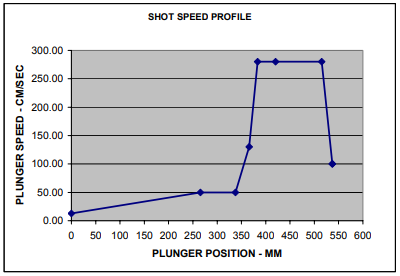
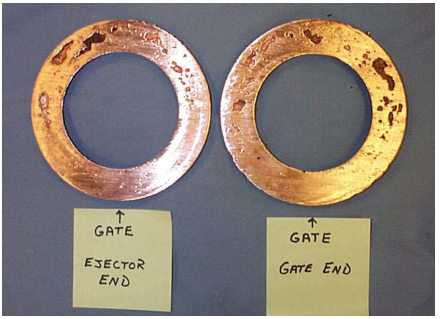
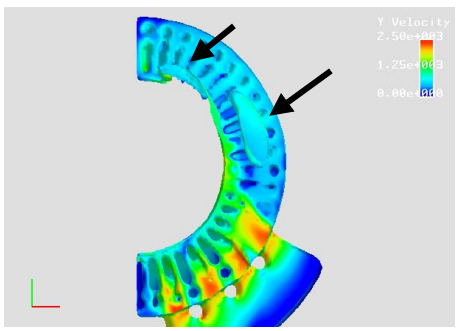
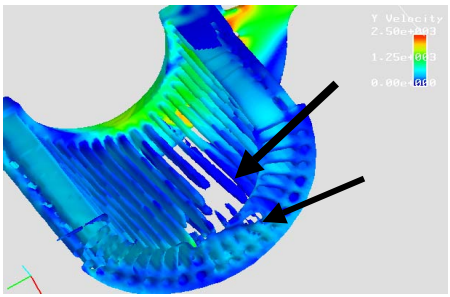
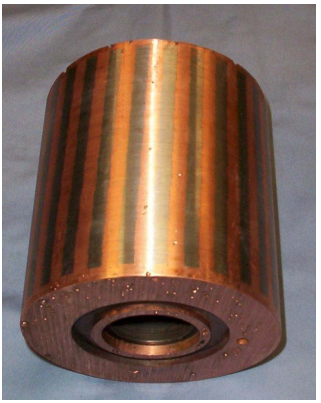
Trapped air bubbles are not seen in the bars but
are clearly visible in the end ring.
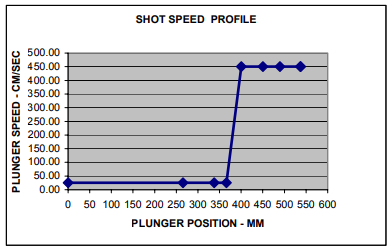
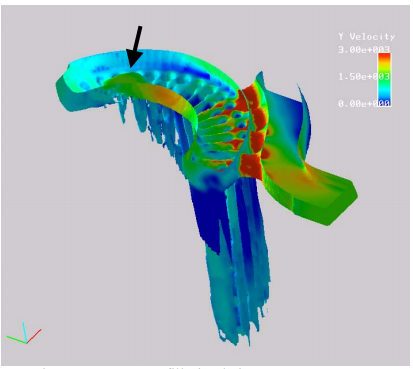
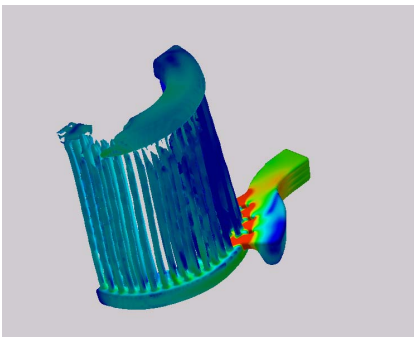
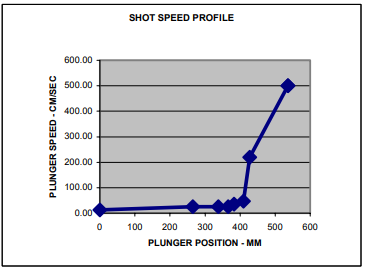
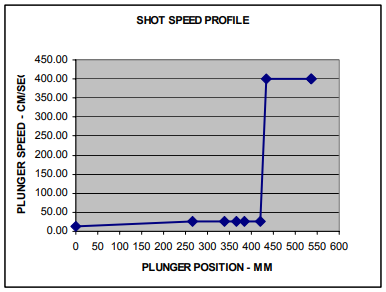
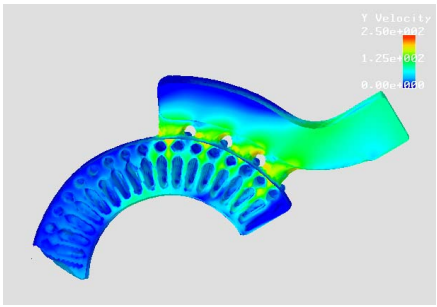
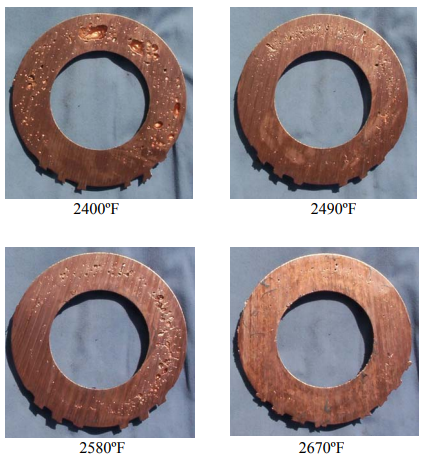
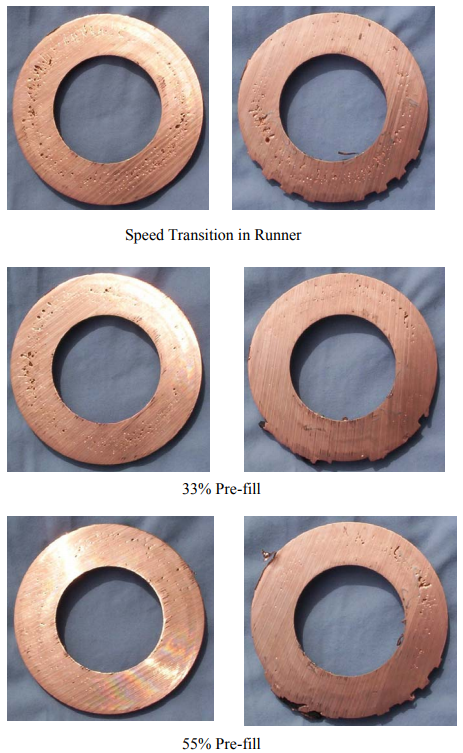
Tables
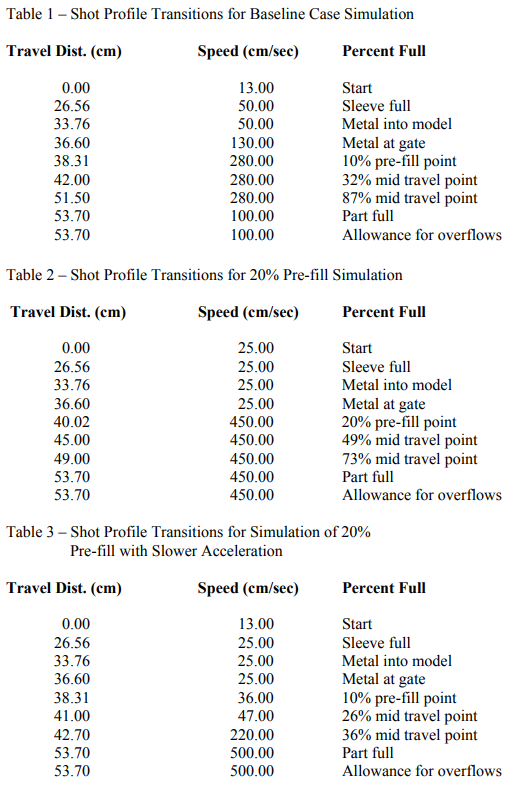
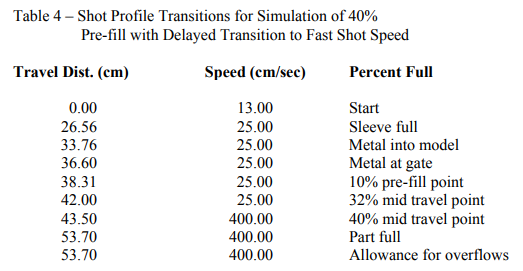