The content of this introduction paper is based on the article "Performance Enhancement of BLDC Motor for Electric Vehicle Applications" published by "www.isteonline.in".
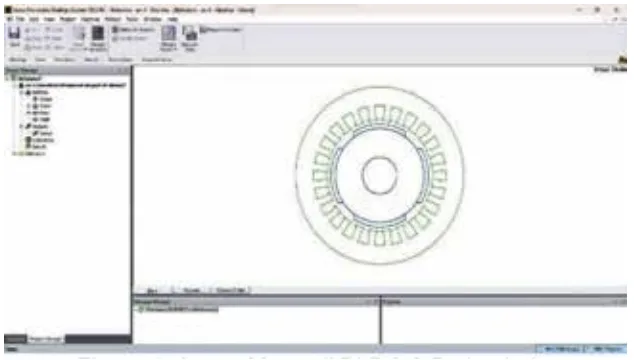
1. Overview:
- Title: Performance Enhancement of BLDC Motor for Electric Vehicle Applications
- Author: Sohel Mulla, Paridhi Dahake, Pranav Shelke, Yogesh B. Mandake, Deepak S. Bankar
- Year of publication: July, 2023
- Journal/academic society of publication: www.isteonline.in, Vol. 46, Special Issue
- Keywords: Ansys maxwell software, BLDC motor, Controller, Efficiency, Electric vehicles, Performance enhancement, Simulation, Speed torque parameters
2. Abstract:
In today's technologically advanced society, people are increasingly seeking out more modern, convenient, and environmentally friendly options. One area where this is particularly evident is the transportation industry, as traditional gasoline-powered vehicles contribute significantly to CO2 emissions posing a high threat to the environment. Hence interest in electric vehicles (EV) has increased recently seeing its environmental advantages, high energy efficiency, and low noise. DC Motors, Induction Motors, Permanent Magnet Synchronous Motors, Switched Reluctance Motors, and Brushless DC Motors are various types of electric motors that have been used in electric vehicles in the past. But because of its high-power density, high power-to-weight ratio, instantaneous speed control and high efficiency Brushless DC motor is the most efficient choice for electric vehicles. In this paper, we present analysis of brushless DC motor of rating 500 W, 2000 rpm & 48 V by proposing various methodologies to improve performance of BLDC motor through simulation using Ansys Maxwell RMxprt. By using Ansys Maxwell we are simulating different design parameters like torque, losses, torque ripple factor, power & efficiency.
3. Introduction:
The transition to electric vehicles (EVs) is crucial for mitigating environmental pollution and reducing reliance on diminishing fossil fuel resources. Brushless DC (BLDC) motors are recognized as a highly efficient option for EVs due to their superior power density, power-to-weight ratio, speed control, and efficiency compared to other motor types like DC Motors, Induction Motors, and Switched Reluctance Motors. The effectiveness of power electronic systems and control techniques is paramount to enhance the efficiency of EVs, especially battery-operated ones. BLDC motors are already widely utilized in industrial and automotive sectors due to their advantageous characteristics. This paper investigates methodologies to enhance the performance of BLDC motors for EV applications, focusing on simulation-based analysis using Ansys Maxwell RMxprt software.
4. Summary of the study:
Background of the research topic:
The increasing environmental concerns associated with traditional gasoline-powered vehicles and the global push towards sustainable transportation have amplified the interest in electric vehicles. BLDC motors are identified as a promising technology for EV propulsion due to their inherent advantages in efficiency and performance.
Status of previous research:
Various types of electric motors, including DC Motors, Induction Motors, Permanent Magnet Synchronous Motors (PMSM), and Switched Reluctance Motors (SRM), have been considered for EV applications. However, BLDC motors stand out due to their high-power density, efficiency, and controllability. Prior research has highlighted the need for effective power electronic systems and control strategies to optimize EV performance.
Purpose of the study:
This study aims to analyze and improve the performance characteristics of BLDC motors specifically for electric vehicle applications. The research focuses on enhancing motor performance through design parameter optimization using simulation tools.
Core study:
The core of this study involves the performance analysis of a BLDC motor with a rating of 500 W, 2000 rpm, and 48 V. Utilizing Ansys Maxwell RMxprt software, the research investigates the impact of various design parameters on motor performance. The key performance indicators under scrutiny include torque, losses, torque ripple factor, power, and efficiency. The study explores different methodologies to optimize these parameters and enhance the overall performance of the BLDC motor for EV applications.
5. Research Methodology
Research Design:
This research employs a simulation-based design approach. Ansys Maxwell RMxprt software is utilized to model and simulate the performance of a BLDC motor. This method allows for the analysis of various design parameters and their impact on motor characteristics without the need for physical prototyping in the initial stages.
Data Collection and Analysis Methods:
Data is collected through simulations conducted in Ansys Maxwell RMxprt. Different design parameters, such as stator and rotor materials, wire gauge, and air gap, are varied within the simulation environment. The software calculates and provides data on key performance metrics including efficiency, speed, torque, and losses. This data is then analyzed to evaluate the impact of each parameter variation on the BLDC motor's performance.
Research Topics and Scope:
The research focuses on the performance enhancement of BLDC motors by investigating the following topics:
- Material Optimization: Analyzing different stator and rotor materials to minimize losses and improve efficiency. Materials considered include Cold Rolled Steel, Aluminium Steel, and Proposed Steel (Steel_1010, Steel_1008, M43_29G, DW540_50).
- Gauge Size Variation: Evaluating the effect of different wire gauge sizes on motor performance, specifically efficiency and torque. Wire gauges from 22 to 18 AWG are examined.
- Air Gap Adjustment: Studying the influence of air gap variations on torque, efficiency, and speed characteristics. Air gaps ranging from 0.6 mm to 0.375 mm are simulated.
- Cogging Torque Reduction Techniques: Exploring methods like skewing and magnetic pole shaping to mitigate cogging torque, although the simulation results primarily focus on material and dimensional optimizations.
6. Key Results:
Key Results:
The simulation results indicate that optimizing material selection, wire gauge, and air gap significantly impacts BLDC motor performance.
- Material Selection: Steel_1010 was identified as the preferred stator and rotor material, achieving an efficiency of 85.259%, a speed rating of 1986.66 rpm, and a torque rating of 2.40307 N.m with total losses of 86.438 W (Table 2).
- Wire Gauge: Using a wire gauge of 21 AWG resulted in an efficiency of 85.259%, a speed rating of 1986.66 rpm, and a torque rating of 2.40307 N.m with total losses of 86.438 W (Table 3). Decreasing gauge size increased efficiency and speed but reduced torque.
- Air Gap: An air gap of 0.6 mm yielded an efficiency of 85.259%, a speed rating of 1986.66 rpm, and a torque rating of 2.40307 N.m with total losses of 86.438 W (Table 4). Increasing the air gap generally increased torque and efficiency but decreased speed.
- The optimized BLDC motor configuration achieved an efficiency of 85.259% at a rated speed of 2000 rpm (Figure 3) and delivered an output power of 0.49 kW at 2000 rpm (Figure 4) and an output torque of 2.40307 Nm at the rated speed (Figure 5).
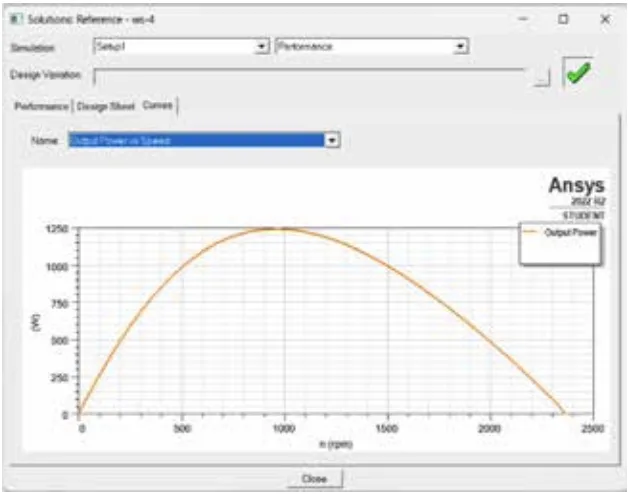
Table 2: BLDC stator and rotor material comparison
Material | Efficiency (%) | Speed Rating (rpm) | Torque Rating (N.m) | Total Loss (W) |
---|---|---|---|---|
Steel_1010 | 85.259 | 1986.66 | 2.40307 | 86.438 |
Steel_1008 | 85.3001 | 1957.87 | 2.43838 | 86.1545 |
M43_29G | 82.7972 | 1982.28 | 2.40834 | 103.871 |
DW540_50 | 82.2257 | 1957.10 | 2.43937 | 108.07 |
Table 3: BLDC motor wire gauge comparison
Wire Gauge | Wire Diameter (mm) | Efficiency (%) | Speed Rating (rpm) | Torque Rating (N.m) | Total Loss (W) |
---|---|---|---|---|---|
22 | 0.6438 | 82.7467 | 1925.92 | 2.48027 | 104.301 |
21 | 0.7229 | 85.259 | 1986.66 | 2.40307 | 86.438 |
20 | 0.8118 | 87.1319 | 2031.57 | 2.35261 | 73.9176 |
19 | 0.9116 | 88.5713 | 2067.37 | 2.30961 | 64.519 |
18 | 1.024 | 89.6673 | 2100.88 | 2.27115 | 57.5777 |
Table 4: BLDC motor air gap comparison
Air Gap (mm) | Efficiency (%) | Speed Rating (rpm) | Torque Rating (N.m) | Total Loss (W) |
---|---|---|---|---|
0.6 | 85.259 | 1986.66 | 2.40307 | 86.438 |
0.5 | 85.3075 | 1950.16 | 2.44815 | 86.1082 |
0.45 | 85.3318 | 1931.53 | 2.47183 | 85.9433 |
0.4 | 85.3424 | 1916.53 | 2.49332 | 85.9448 |
0.375 | 85.3496 | 1908.92 | 2.50388 | 85.9164 |
Figure Name List:
- Fig. 1. Ansys Maxwell BLDC 2-D simulation
- Fig. 2. BLDC driver circuit
- Fig. 3: Efficiency vs Speed
- Fig. 4. Output Power vs Speed
- Fig. 5. Output Torque vs Speed
- Fig. 6. Material consumption data
- Fig. 7: Full load operation data
7. Conclusion:
This study successfully demonstrated the performance enhancement of a BLDC motor for electric vehicle applications through simulation-based optimization. By systematically varying and analyzing stator and rotor materials, wire gauge, and air gap using Ansys Maxwell RMxprt, the research identified optimal design parameters that significantly improve motor efficiency, speed, and torque characteristics. The results indicate that Steel_1010 for stator and rotor, 21 AWG wire gauge, and a 0.6 mm air gap provide a superior performance balance for the 500W, 48V BLDC motor under consideration. The achieved efficiency of 85.259% underscores the potential of BLDC motors as a highly efficient propulsion solution for EVs, outperforming induction motors in power ratio and eliminating the need for extra converters. The study suggests that material selection and dimensional optimization are crucial factors in minimizing losses and enhancing the overall performance of BLDC motors for electric vehicle applications.
8. References:
- [1] Pallavi Rodge, Kantilal Joshi, "Electric Vehicles in India: Current Status, Future Trend and Environmental Impact". 2018 International Conference on Smart Electric Drives & Power System.
- [2] Vishnu Sidharthan P, Yashwant Kashyap, "Brushless DC Hub Motor Drive Control for Electric Vehicle Applications", 2020 First International Conference on Power, Control and Computing Technologies (ICPC2T)
- [3] Nasser Hashernnia and Behzad Asaei "Comparative Study of Using Different Electric Motors in the Electric Vehicles" Proceedings of the 2008 International Conference on Electrical Machines.
- [4] Mustafa Yaz and Emrah Cetin, "Brushless Direct Current Motor Design and Analysis" DOI - 10.31031/ COJEC.2021.02.000534, https://www.researchgate.net/publication/35510 7964,
- [5] Praveenkumar CHANDRAN*, Kaliamoorthy MYLSAMY, Prabha UMAPATHY, “Conceptual Design and Material Analysis of BLDC Motor Using FEA Tools for Electric Vehicle Applications" https://doi.org/10.17559/TV- 20210425201219.
- [6] Y.B. Adyapaka Apatya, Aries Subiantoro and Feri Yusivar "Design and Prototyping of 3- Phase BLDC Motor", 2017 IEEE. DOI - 978-602- 50431-1-6/17
- [7] Pranoti K. Khanke and Sangeeta D. Jain “Comparative Analysis of Speed Control of BLDC Motor Using PI, Simple FLC and Fuzzy – PI Controller” International Conference on Energy Systems and Applications (ICESA 2015).
- [8] Shivam Tiwari and S. Rajendran "Four Quadrant Operation and Control of Three Phase BLDC Motor for Electric Vehicles" 2019 IEEE, DOI - 978-1-5386-7434-5/19
- [9] Ramachandran R, Ganeshaperumal D & Subathra B "Closed-loop Control of BLDC Motor in Electric Vehicle Applications” 2019 IEEE, DOI - 978-1-7281-4407-8/19.
- [10] T. A. Anuja, Arun Noyal Doss M., R. Senthilkumar, Rajesh K. S., (Member, Ieee), And R. Brindha "Modification of Pole Pitch and Pole Arc in Rotor Magnets for Cogging Torque Reduction in BLDC Motor" September 2022, DOI-10.1109/ ACCESS.2022.3217233
9. Copyright:
- This material is a paper by "Sohel Mulla, Paridhi Dahake, Pranav Shelke, Yogesh B. Mandake, Deepak S. Bankar". Based on "Performance Enhancement of BLDC Motor for Electric Vehicle Applications".
- Source of the paper: [DOI URL] (Note: DOI URL is not provided in the paper).
This material is summarized based on the above paper, and unauthorized use for commercial purposes is prohibited.
Copyright © 2025 CASTMAN. All rights reserved.