This introduction paper is based on the paper "OPTIMIZATION PRODUCT PARTS IN HIGH PRESSURE DIE CASTING PROCESS" published by "Mälardalen University Press Licentiate Theses".
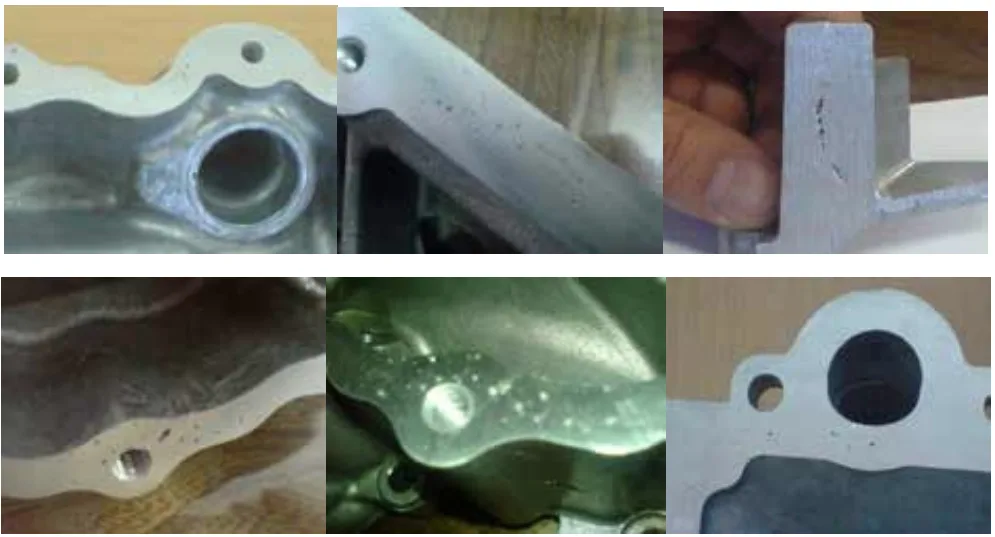
1. Overview:
- Title: OPTIMIZATION PRODUCT PARTS IN HIGH PRESSURE DIE CASTING PROCESS
- Author: Mohammad Sadeghi
- Year of publication: 2015
- Journal/academic society of publication: Mälardalen University Press Licentiate Theses, No. 197
- Keywords: High Pressure Die Casting (HPDC), Die Temperature Optimization, A380 Aluminum Alloy, Numerical Simulation, Experimental Observation, Defect Minimization
2. Abstract:
This thesis describes optimization of die temperature in high pressure die-casting (HPDC) of A380 alloy by experimental observation and numerical simulationwith the use of statistical tools.The goal of this research is to determine the optimum die temperature to minimize incidence of these defects and thus maximize production of parts without defects.
In HPDC, molten metal is injected into the die at high speed (40-60 m/s for aluminum alloys). Die temperature plays an important role on the rate of rejected parts. Therefore, flow patterns of molten metal in HPDC of an automotive component with very complex geometry (the ladder framefrom the EF7 motor) were examined to determine the optimal die temperature.
Defects in the production process fall into three categories, including surface, internal and dimensional defects. Samples produced in the experiments were classified according to any present defects.
Another important parameter that influences casting defects is the cooling rate. Die temperatures were measured at the initial step and final filling positions. Experiments were performed with die temperatures ranging from 150 °C to 250 °C. The results show that the melt temperature difference in the die between the initial step and the final filling position was between 20 and 25 °C.
Statistical tools such as regressions, relationships, max, min, correlations, ANOVA, T-test, Principal Component Analysis (PCA) and descriptive statistics were used to facilitate interpretation of data from the die-cast experiments.
Perform some case studies in order to study the process behavior, take a better knowledge of effecting parameters, and measure the required parameters. The collected data are utilized to:
- Set the model
- Validate/ verify the model
ProCast software was used to simulate the fluid flow and solidification step, and the results were verified by experimental measurements. The optimal die temperature for this alloy was found to be above 200 °C.
Statistical analysis of the experimental results found that defects were minimized and confirmed parts were maximized in HPDC of the ladder frame within a die temperature range of 210° C to 215° С.
3. Introduction:
The high pressure die-cast (HPDC) process is a widely used manufacturing method for producing parts from aluminum, magnesium, copper, and zinc, offering advantages such as accurate die conformity, favorable mechanical properties, low cost, and the ability to produce complex shapes. This process is integral to various industries, including automotive and aerospace. However, the quality of HPDC parts is influenced by numerous parameters, including melt temperature, injection pressure, die temperature, part complexity, and injection speed. This research focuses on investigating the effect of die temperature on defects in produced parts. With the increasing complexity of components and the need for optimization, numerical methods are becoming essential tools for solving physical problems related to production processes, offering significant reductions in time and cost compared to traditional trial-and-error approaches. This thesis specifically addresses die-cast aluminum alloys and their application in the automobile industry, aiming to understand and optimize the relationships between casting shape, production parameters, and die-cast process components to reduce waste and minimize faults.
4. Summary of the study:
Background of the research topic:
High pressure die casting (HPDC) is a critical manufacturing process for producing complex metallic components, particularly in the automotive sector, using alloys like A380 aluminum. The process involves injecting molten metal into a die at high velocity and pressure. While HPDC offers advantages like near-net-shape production and good mechanical properties, the final part quality is highly sensitive to process parameters. Defects can arise from suboptimal conditions, leading to increased costs and waste. Optimizing these parameters, especially die temperature, is crucial for ensuring sound castings. Numerical simulation tools are increasingly employed to understand and optimize the complex interplay of these parameters.
Status of previous research:
This study builds upon the existing body of knowledge concerning HPDC process physics, solidification theory, and defect formation mechanisms. Established theories of nucleation (e.g., classical Gibbs model, non-classical models) and solidification microstructure development form the scientific underpinning of the research. The use of computational tools like ProCast for simulating fluid flow, heat transfer, and solidification in casting processes is a well-developed field. This research applies these established principles and tools to address the specific challenge of optimizing die temperature for a newly designed, complex automotive component (ladder frame for the EF7 engine), aiming to minimize defects.
Purpose of the study:
The primary goal of this research is to determine the optimum die temperature in the high pressure die-casting (HPDC) of A380 aluminum alloy to minimize the incidence of defects and thereby maximize the production of acceptable parts. The specific objectives include:
- To understand the parameters that affect the production process and the design parameters of the die-cast method.
- To determine the relationships between components of the die-cast design, the location of runners and overflows, and the geometric complexity of the parts.
- To investigate the relationship between design parameters and manufacturing parameters and to optimize them to reduce the number of faults and thus unusable parts.
Core study:
The core of this study involves a comprehensive investigation into the optimization of die temperature for an A380 aluminum alloy automotive component (ladder frame from the EF7 motor) produced by the HPDC process. This was achieved through a combination of experimental observations and numerical simulations. Experiments were conducted by systematically varying die temperatures (from 150 °C to 250 °C) and melt temperatures, while monitoring defect formation. The ladder frame, chosen for its complex geometry, served as the test part. Numerical simulations using ProCast software were performed to model the fluid flow and solidification stages, and the results were validated against experimental measurements. Statistical tools, including regressions, ANOVA, and PCA, were employed to analyze the experimental data and identify optimal process conditions.
5. Research Methodology
Research Design:
The research employed a combined experimental and numerical simulation approach. Experimental trials were conducted on an industrial HPDC machine (IDRA1600) using A380 aluminum alloy to produce a complex automotive part, the "ladder frame" from the EF7 motor. The primary variable investigated was die temperature, ranging from 150 °C to 250 °C, with melt temperature also being monitored and controlled. Numerical simulations were performed using ProCast software to model the mold filling and solidification processes under varying conditions. The simulation results were then verified by experimental measurements to ensure accuracy and reliability.
Data Collection and Analysis Methods:
Data collection involved measuring die temperatures at the initial step and final filling positions, and melt temperatures at the die entrance (injection start) and at the end of the die (time out injection). A total of 800 experiments were performed, with triplicate runs for each condition to ensure reliability. Defective parts were identified, and the type of defects (surface, internal, dimensional) were determined using various analytical techniques, including X-ray inspection, Coordinate Measuring Machine (CMM), metallography, and visual examinations.
Data analysis was conducted using a suite of statistical tools such as regressions, relationships, maximum, minimum, correlations, ANOVA, T-test, Principal Component Analysis (PCA), and descriptive statistics. ProCast software was used for simulating fluid flow and solidification, providing insights into temperature distribution, fill patterns, and potential defect locations.
Research Topics and Scope:
The scope of this thesis is focused on the production of parts made from aluminum alloy A380 with complex shapes and minimal defects using the high pressure die cast method. The central research topic is the optimization of die temperature to minimize casting defects. The study investigates the influence of die temperature on the quality of a specific automotive component (ladder frame) with a very complex geometry. The research combines experimental work with numerical simulations using Engineering ProCast software to model experimental results and empirically confirm simulation outcomes. The study also explores the relationship between design parameters (like runner and overflow locations) and manufacturing parameters (like die and melt temperature).
6. Key Results:
Key Results:
The study successfully identified an optimal die temperature range for the HPDC of A380 aluminum alloy to minimize defects and maximize the production of confirmed parts for the complex ladder frame component.
- The optimal die temperature for this alloy was found to be above 200 °C.
- Statistical analysis of experimental results indicated that defects were minimized and confirmed parts were maximized when the die temperature was in the range of 210 °C to 215 °C. The ideal die temperature range is therefore 212.5±2.5 °C.
- Descriptive statistics showed that a die temperature of 210 °C produced the highest rate of accepted parts (99.45% with a 95% confidence level).
- Analysis of Variance (ANOVA) suggested that a die temperature of 210 °C also produced the largest variance, demonstrating its significant effect on accepted parts and minimum defects.
- Principal Component Analysis (PCA) further confirmed that a die temperature of 210 °C is optimal for part quality, having the greatest influence among the tested temperatures.
- The study found that experiments with a die temperature of 210 °C and a pouring temperature of 668 °C to 680 °C were optimal with respect to die quality.
- Different defect types were prevalent at different die temperatures: Type 1 (surface defects) were most frequent when die temperature was below 200 °C, while Type 2 (internal defects) and Type 3 (dimensional defects) were more frequent when die temperature was above 200 °C.
- Numerical simulations using ProCast software effectively predicted likely locations of macroscopic and microscopic defects, and flow patterns. Modifications, such as eliminating three holes inside the mold, were shown to improve the flow pattern.
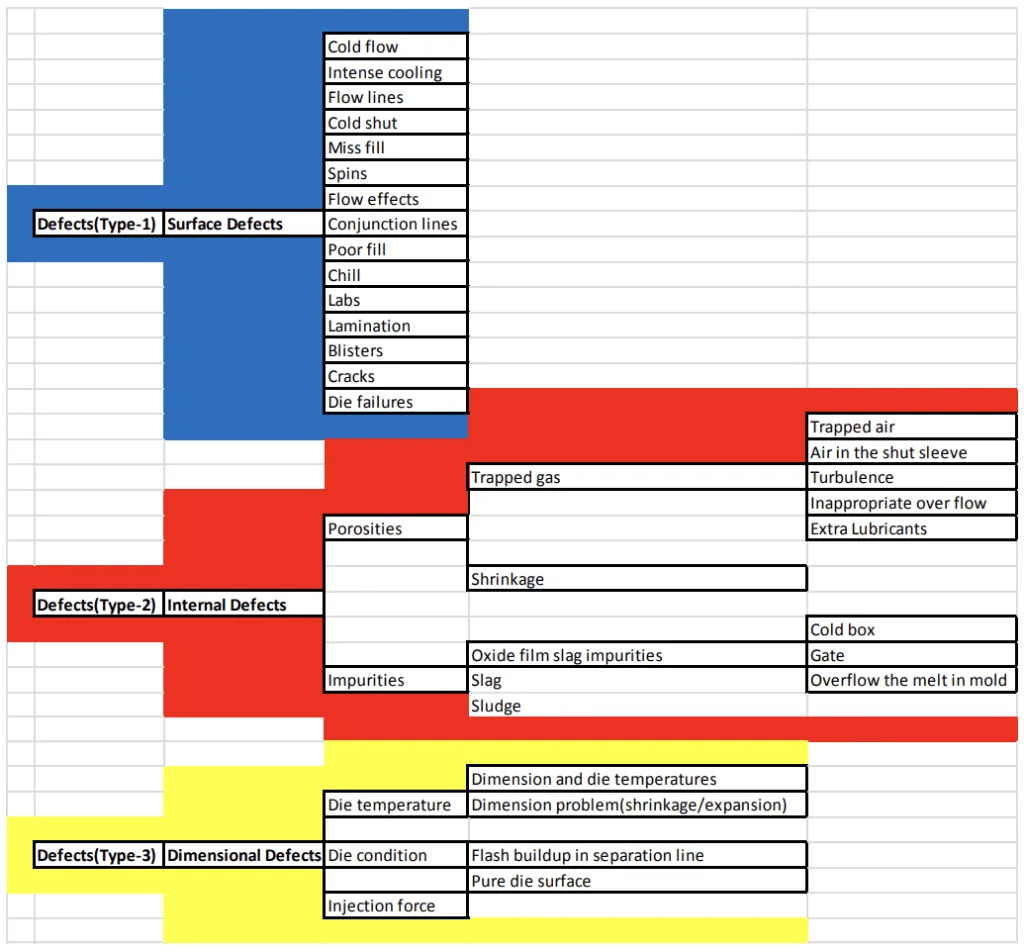
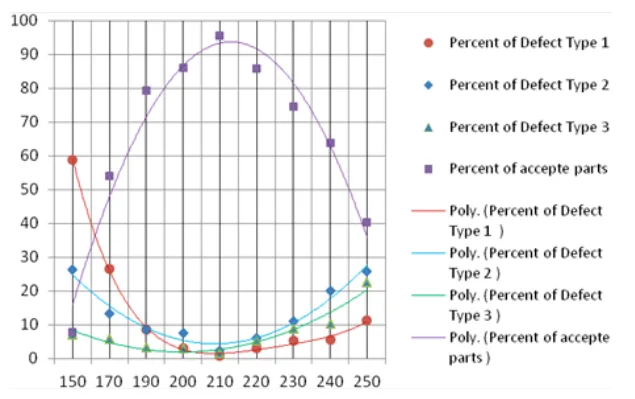
Figure Name List:
- FIGURE 2.1: AL-SI BINARY PHASE DIAGRAM
- FIGURE 2.2: GRAIN MICROSTRUCTURE AFTER SOLIDIFICATION OF CASTING PART SCHEMATIC (LEFT), AND MICROSTRUCTURE OF AL-4%CU BILLET (RIGHT) [1]
- FIGURE 2.3: RELATIONSHIP BETWEEN PHASE DIAGRAM WITH DISTRIBUTION COEFFICIENT K, AND DEVELOPMENT OF CONSTITUTIONAL UNDER COOLING [1]
- FIGURE 2.4: FORMATION OF DIFFERENT PHASE BOUNDARY STRUCTURES ACCORDING TO CONSTITUTIONAL UNDER COOLING: PLANAR (LEFT), CELLULAR (MIDDLE), AND DENDRITIC (RIGHT). THERMAL GRADIENT AND MELTING TEMPERATURE (TOP GRAPHS) AND RESULTING MICROSTRUCTURE (BOTTOM GRAPHS)
- FIGURE 2.5: EFFECT OF GL AND VS ON THE SOLIDIFIED MICROSTRUCTURE [1].
- FIGURE 2.6: VARIATION OF INTERNAL ENERGY OF THE SINGLE-PHASE SYSTEM VERSUS RADIUS OF FORMED NUCLEUS
- FIGURE 2.7: CATEGORIES OF DEFECTS OCCURRING IN THE PRODUCTION OF ALUMINUM PARTS THROUGH HPDC.
- FIGURE 2.8: (A) SCHEMATIC OF A SMALL SOLIDIFYING VOLUME ELEMENT OF UNIFORM TEMPERATURE WITHIN WHICH NUCLEATION AND GROWTH CAN OCCUR FROM THE MOLD WALL AND IN BULK;(B) SCHEMATICS OF THE CELLULAR AUTOMATON USED TO PREDICT MICROSTRUCTURE FORMATION IN THE SMALL SOLIDIFYING SPECIMEN SHOWN IN(A).
- FIGURE 2.9: DETAILS OF THE GROWTH OF ACELLULAR AUTOMATON CELL CORRECTION APPLIED TO ADENDRITE TIP
- FIGURE3.1: GEOMETRY OF LADDER FRAME PART
- FIGURE 3.2: THE INFLUENCE GRAPH
- FIGURE 3.3: THE LOADING GRAPH
- FIGURE 3.4: EFFECT OF DIE TEMPERATURE ON THE PERCENTAGE OF ACCEPTED PARTS AND THE THREE DEFECT TYPES OF THE DIE-CASTING PARTS.
- FIGURE 3.5: EFFECT OF DIE TEMPERATURE ON THE PERCENTAGE OF ACCEPTED PARTS AND THE THREE TYPES OF DEFECT IN THE DIE-CASTING PARTS
- FIGURE 3.6: MELT TEMPERATURES AT DIE ENTRANCE AND START INJECTION VERSUS DIE TEMPERATURES.
- FIGURE 3.7: MELT TEMPERATURES AT THE END OF THE DIE AND END INJECTION VERSUS DIE TEMPERATURES.
- FIGURE 3.8: REDUCTION OF MELT TEMPERATURE AT VARIOUS DIE TEMPERATURES AT THE INITIAL AND THE END OF INJECTION
- FIGURE 3.9: GEOMETRY OF LADDER FRAME PRODUCT
- FIGURE 3.10: TEMPERATURE FIELD IN THE PART DURING FILLING AT DIE TEMPERATURE OF 150°C.
- FIGURE 3.11: TEMPERATURE FIELD IN THE PART DURING FILLING AT DIE TEMPERATURE OF 200°C.
- FIGURE 3.12: TEMPERATURE FIELD IN THE PART DURING FILLING AT DIE TEMPERATURE OF 250°C.
- FIGURE 3.13: FILLING AND SOLIDIFICATION PATTERN AT DIE TEMPERATURE 200°C, MELT TEMPERATURE 680°CAND PISTON VELOCITY3 M/S.
- FIGURE 3.14: RESULT OF EXPERIMENT IN SIMILAR CONDITIONS TO SIMULATION
- FIGURE 3.15: OVERFLOWS LOCATIONS IN THE DIE
- FIGURE 3.16: TEMPERATURE DISTRIBUTION AND FILLING SEQUENCE OF THE MOLD AT200°C
- FIGURE 3.17: FINAL SOLIDIFICATION POSITIONS.
- FIGURE 3.18: GAS AND SHRINKAGE DEFECTS IN THE SECTION SURFACE
- FIGURE 3.19: EFFECT OF THE HOLES ON THE FLOW PATTERN AND SOLIDIFICATION.
- FIGURE 3.20: EFFECT OF THE HOLES LOCATED ON THE VELOCITY VECTORS OF THE MELT
7. Conclusion:
There is a demonstrable relationship between the shape of the cast and mold design, which can be optimized using numerical and statistical methods. The research results suggested a beneficial change in mold design, specifically the removal of three holes, which can lead to improved casting quality by preventing issues like shrinkage in thin sections due to rapid solidification and lack of pressure transmission.
Experiments confirmed that a die temperature of 210°C and a pouring temperature between 668°C and 680°C are optimal for die quality. The study showed that overflow locations can be effectively determined from the predicted flow pattern using simulation. The application of statistical tools such as PCA and ANOVA significantly facilitates the analysis of data from die-cast experiments, making it easier and more accurate.
Die temperatures were shown to have a clear effect on the number and type of defects. Type 1 defects (surface) were most frequent when the die temperature was below 200 °C. Conversely, Type 2 (internal) and Type 3 (dimensional) defects were more frequent when the die temperature was above 200 °C. The optimum die temperature range to minimize overall defects was determined to be 210-215 °C. Therefore, the ideal die temperature range for the studied A380 alloy and component geometry is 212.5±2.5 °C.
8. References:
- [1- W. Kurz and D.J. Fisher. Fundamentals of Solidification. Switzerland: Trans Tech Pub., 4th edition, 1998.]
- [2- J.W. Gibbs, H.A. Bumstead, and W.R. Longley. The Collected Works of J. Willard Gibbs. Longmans,Green and Co, 1928.]
- [3- J.D. Van der Waals. Translation of J. D. van der Waals' "The thermodynamic theory of capillarity under the hypothesis of a continuous variation of density”. Journal of Statistical Physics, 20(2):200–244, 1979]
- [4- J.W. Cahn and J.E. Hilliard. Free energy of a nonuniform system. I. Interfacialfreeenergy. The Journal ofChemicalPhysics, 28:258, 1958.]
- [5- J.W. Cahn. Free energy of a nonuniform system. II. Thermodynamic basis. The Journal of Chemical Physics, 30:1121, 1959.]
- [6- J.W. Cahn and J.E. Hilliard. Free energy of a nonuniform system. III. Nucleation in a twocomponent incompressible fluid. The Journal of Chemical Physics, 31:688, 1959.]
- [7- D.W. Oxtoby and R. Evans. Nonclassical nucleation theory for the gas-liquid transition. The Journal ofChemicalPhysics, 89:7521, 1988.]
- [8- D.W. Oxtoby. Density functional methods in the statistical mechanics of materials. Annual Review of Materials Research, 32(1):39–52, 2002.]
- [9- S.F. Jones, G.M. Evans, and K.P. Galvin. Bubble nucleation from gas cavities a review. Advances in colloid and interface science, 80(1):27–50, 1999.]
- [10- E.N. Harvey, W.D. McElroy, and AH Whiteley. On cavity formation in water. Journal ofAppliedPhysics, 18:162, 1947.]
- [11- R.A. Outlaw, D.T. Peterson, and F.A. Schmidt. Hydrogen partitioning in pure cast aluminum as determined by dynamic evolution rate measurements. Metallurgical and Materials Transactions A, 12(10):1809–1816, 1981.]
- [12- J. Campbell. Castings. Butterworth-Heinemann, 2003.]
- [13- R.B. Dean. The formation of bubbles. Journal ofAppliedPhysics, 15:446, 1944.]
- [14- R. Sasikumar, M.J. Walker, S. Savithri, and S. Sundarraj. Initiation of microporosity from preexisting bubbles: a computational study. Modelling and Simulation in Materials Science and Engineering, 16(3):35009, 2008.]
- [15- D. Dispinar and J. Campbell. Critical assessment of reduced pressure test. Part 1: Porosityphenomena. International Journal ofCastMetals Research, 17(5):280–286, 2004.]
- [16- D. Dispinar and J. Campbell. Use of bifilm index as an assessment of liquid metal quality. International Journal ofCastMetals Research, 19(1):5–17, 2006.]
- [17- Z.W. Chen, M.Z. Jahedi., Die erosion and its effect on soldering formation in high pressure die casting of aluminum alloys,Materials and Design ,1999, vol.20,pp.303-309.]
- [18- P.W. Cleary, J. Ha, M. Prakash, T. Nguyen,∃3D SPH flow predictions and validation for high pressure die casting of automotive components∃,Applied Mathematical Modeling,2006, vol.30, pp. 1406–1427.]
- [19- Laws, K.J., Gun, B., Ferry, M.,∃Effect of die-casting parameters on the production of high quality bulk metallic glass samples∃,Mater. Sci. Eng., 2006, A425, pp.114–120.]
- [20- NADCA product specification standards for die castings/1997]
- [21- http://www.ewp.rpi.edu]
- [22- http://www.wtm.uni-erlangen.de]
- [23- ProCAST 2011.User's Manual]
- [24- M. Rappaz,Ch. A. Gandin, “Probabilistic Modelling of Microstructure Formation in Solidification Processes”, Actametallmater,Vol. 41 . No.2, pp.345-360, 1993]
9. Copyright:
- This material is a paper by "Mohammad Sadeghi". Based on "OPTIMIZATION PRODUCT PARTS IN HIGH PRESSURE DIE CASTING PROCESS".
- Source of the paper: http://www.diva-portal.org/smash/record.jsf?pid=diva2:804075
This material is summarized based on the above paper, and unauthorized use for commercial purposes is prohibited.
Copyright © 2025 CASTMAN. All rights reserved.