This article introduces the paper "NUMERICAL SIMULATIONS OF FILLING FLOWS IN DIE-CASTING MOLDING OF THE THIN-WALLED LED HEAT SINK".
Abstracts
- Core Objective of the Research: To numerically simulate the filling flows in die-casting of a thin-walled LED heat sink to optimize the mold design and process parameters.
- Main Methodology: Numerical simulations using FLOW-3D software. The study analyzed the effects of various molding conditions (thermal conductivity, vacuum pumping pressure, mold temperature, filling velocity) and geometrical parameters (fin thicknesses of the LED heat sink, dimensions of the vacuum shut-off valve) on the casting quality.
- Key Findings: Higher vacuum pumping pressure resulted in denser castings with fewer defects. Low vacuum pressure led to reduced pumping efficiency and increased porosity defects. A vacuum pumping pressure of 100 Torr was found to be optimal for the thin-walled LED heat sink.
Researcher Information
- Affiliation: National Formosa University
- Author: Rong-Yuan Jou
- Main Research Area: Mechanical Design Engineering
Research Background and Objectives
- Industrial Context: The need for increased efficiency in vacuum die-casting, particularly for lightweight and complex components in modern automotive applications.
- Specific Technical Challenges: Gas porosity defects in castings due to low vacuum levels in conventional vacuum die-casting. Difficulties in producing high-quality thin-walled components with complex geometries, specifically thin-walled LED heat sinks.
- Research Goals: To numerically analyze the filling flows in vacuum die-casting of a thin-walled LED heat sink and determine optimal mold design and process parameters to improve casting quality and efficiency.
Main Objectives and Research Content of the Paper
- Main Objectives and Research Content: Analysis of mold filling in a thin-walled LED heat sink with a vacuum valve runner, investigating the influence of molding parameters and geometrical dimensions on casting quality.
- Problem Addressed: Understanding and mitigating the effects of molding parameters and geometrical features on defect formation (porosity, etc.) in thin-walled LED heat sink castings.
- Step-by-Step Approach to Problem Solving:
- Conducted numerical simulations varying molding parameters (thermal conductivity, vacuum pressure, mold temperature, filling velocity).
- Conducted simulations altering geometrical parameters (fin thicknesses, vacuum valve dimensions).
- Analyzed simulation results to identify optimal molding parameters and geometrical designs.
- Key Figures:
- Fig. 1: Schematic diagram of the LED heat sink structure incorporating the vacuum valve runner and design parameters of the typhoon vacuum valve runner.
- Fig. 2: Three-dimensional model of the vacuum valve and LED heat sink.
- Fig. 3: Data extraction points for numerical analysis.
- Fig. 4: Comparison of entrained air volume fraction for different vacuum pressures (750 Torr vs. 200 Torr).
- Fig. 5: Comparison of entrained air volume fraction for different vacuum pressures (200 Torr vs. 10 Torr).
- Fig. 6: Filling process comparison for different vacuum pressures.
- Fig. 7: Graph showing filling time versus fin thickness.
- Fig. 8: Relationship between heat conduction coefficient and gas content.
- Fig. 9: Relationship between mold temperature and gas content.
- Fig. 10: Relationship between vacuum degree and gas content.
- Fig. 11: Relationship between heat conduction coefficient and molten metal pressure.
- Fig. 12: Relationship between mold temperature and molten metal pressure.
- Fig. 13: Relationship between vacuum degree and molten metal pressure.
- Fig. 14: Relationship between sprue ejection speed and molten metal pressure.
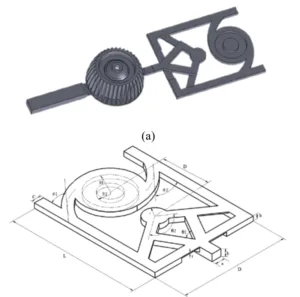
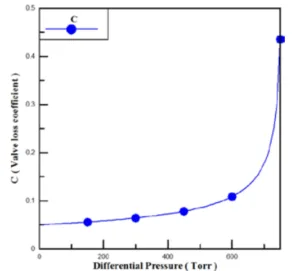
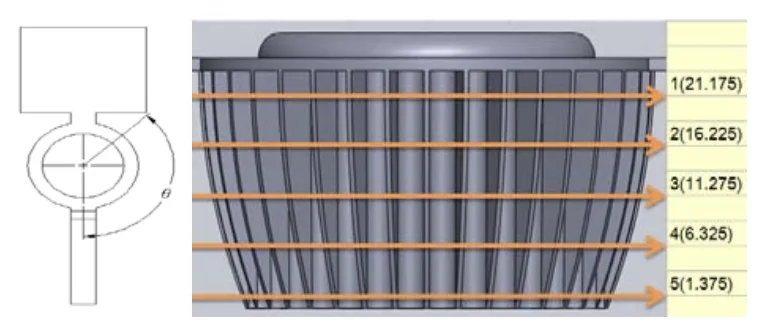
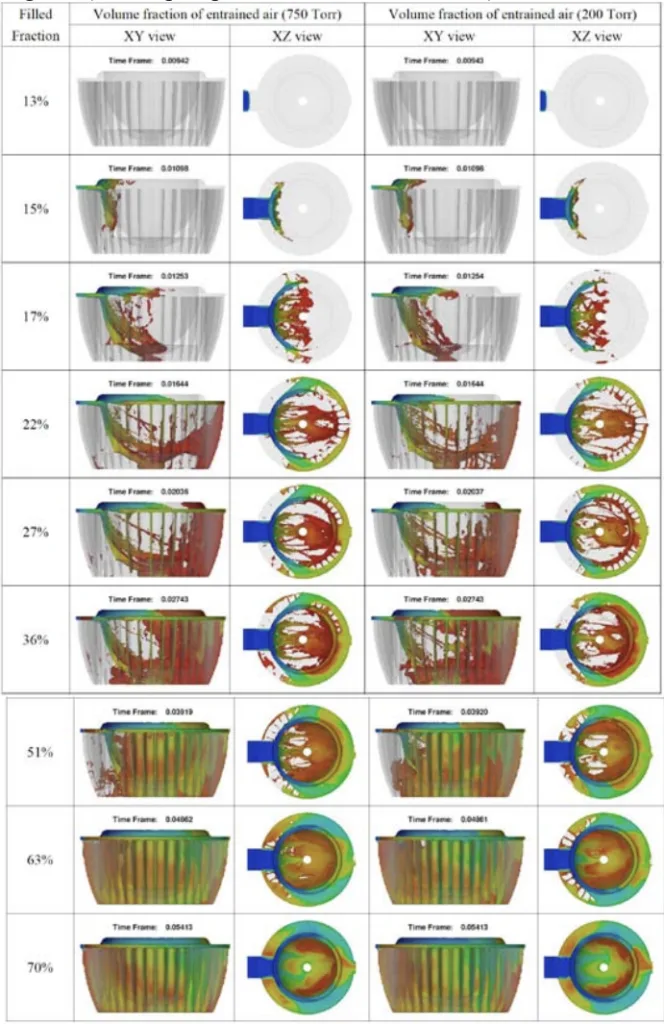
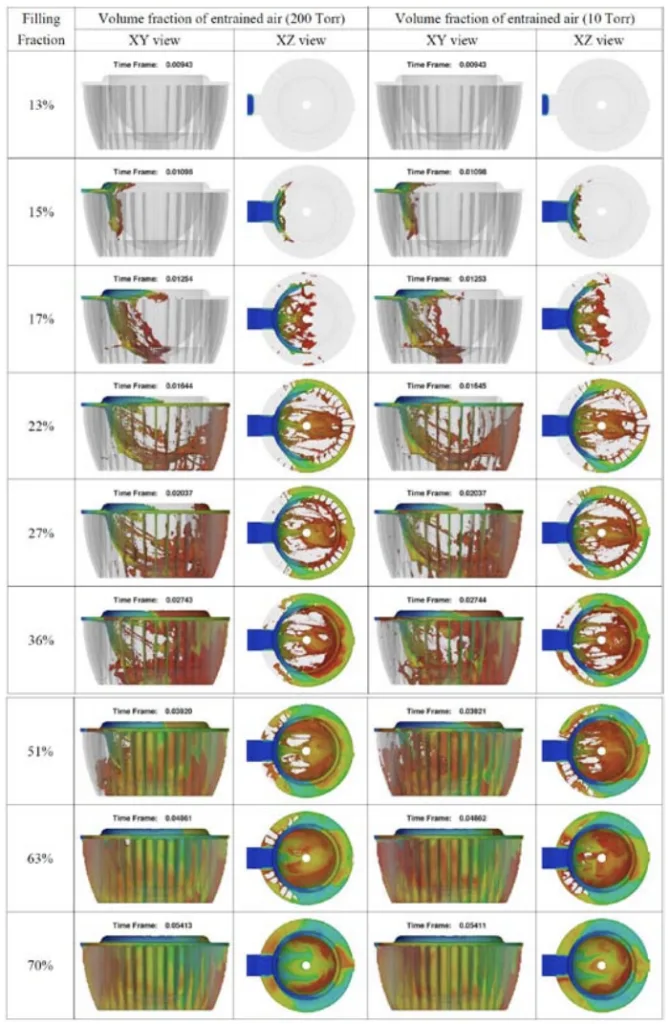
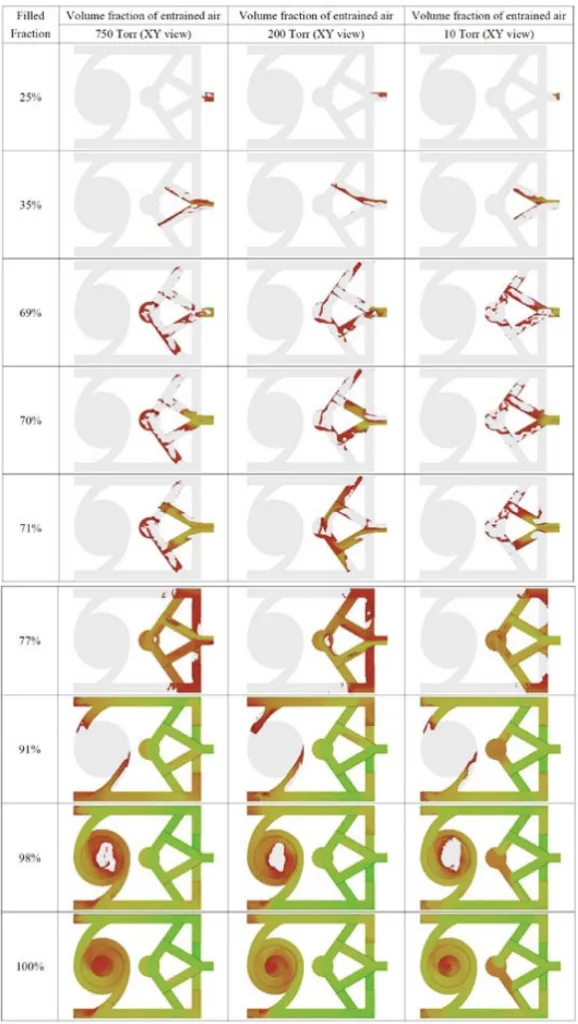
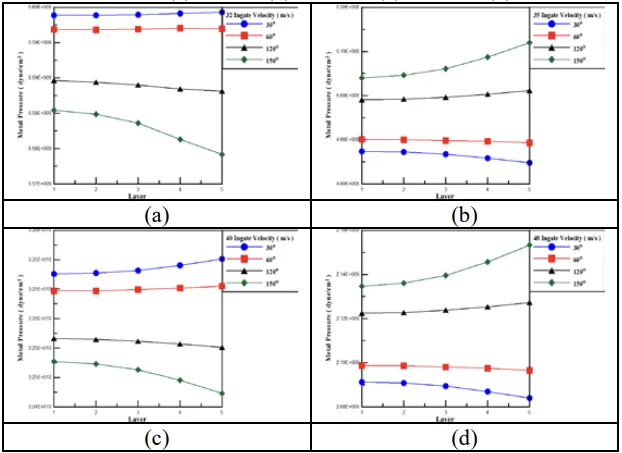
Results and Achievements:
- Quantitative Results: Quantified the influence of various parameters on gas content and filling time. Reported gas residual percentages at various vacuum pressures (0.311%, 0.174%, 0.008% for 760 Torr, 200 Torr, and 100 Torr, respectively).
- Qualitative Results: Observed trends in casting density and defect formation relating to process parameters and geometrical design.
- Technical Achievements: Provided optimized molding parameters and geometrical designs for the vacuum die-casting of thin-walled LED heat sinks, contributing to improved casting quality and process efficiency.
Copyright and References
This material is based on the paper "NUMERICAL SIMULATIONS OF FILLING FLOWS IN DIE-CASTING MOLDING OF THE THIN-WALLED LED HEAT SINK" by Rong-Yuan Jou.
Paper Source: Proceedings of the ASME 2014 12th Biennial Conference on Engineering Systems Design and Analysis (Specific DOI information not provided in original text).
This material is a summary based on the aforementioned paper and should not be used for commercial purposes without permission.