This introduction paper is based on the paper "Newly Developed Magnesium Alloys for Powertrain Applications" published by "JOM: the journal of the Minerals, Metals & Materials Society".
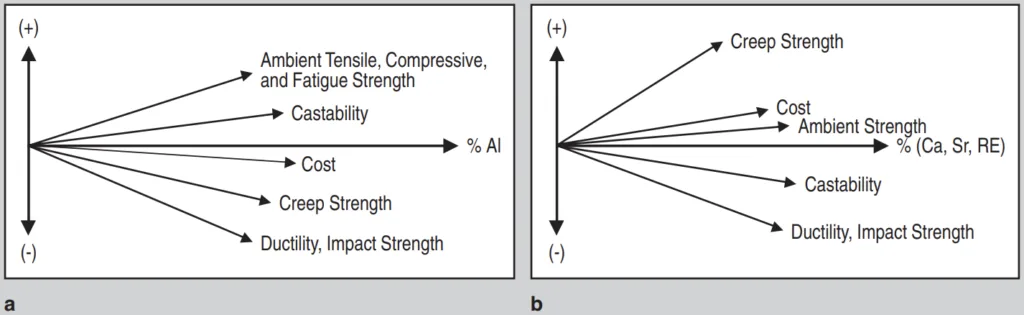
1. Overview:
- Title: Newly Developed Magnesium Alloys for Powertrain Applications
- Author: E. Aghion, B. Bronfin, F. Von Buch, S. Schumann, and H. Friedrich
- Year of publication: 2003 (November)
- Journal/academic society of publication: JOM: the journal of the Minerals, Metals & Materials Society
- Keywords: Magnesium alloys, Powertrain applications, High-temperature, Creep resistance, Die casting, Gravity casting, MRI 153M, MRI 230D, MRI 201S, MRI 202S
2. Abstract:
Several new magnesium alloys have been developed recently for high-temperature applications to obtain an optimal combination of die castability, creep resistance, mechanical properties, corrosion performance, and affordability. Unfortunately, it is difficult to achieve an adequate combination of properties and, in fact, most of the new alloys can only partially meet the required performance and cost. The ZE41 alloy, which is used for most gravity-casting applications, has moderate strength and creep resistance combined with good castability. Although this alloy exhibits poor corrosion resistance, it is still preferred for certain applications.
3. Introduction:
As the lightest structural materials, magnesium alloys are well suited for the car industry where low vehicle weight and, consequently, good fuel economy are essential.
The selection of a new alloy for a vehicle component should be based on technical requirements and targeted cost. In reality, this selection process is complicated and very much depends on the relative weight given to a specific property, which is part of the combined desired properties and final targeted cost. This task becomes even more complicated if alternative material systems such as aluminum alloys are considered for the same applications.
4. Summary of the study:
Background of the research topic:
Magnesium alloys are attractive for automotive applications due to their low density. However, powertrain components (e.g., gearbox housing, oil pans, crankcases) operate at elevated temperatures, requiring alloys with improved creep resistance and bolt load retention compared to standard alloys like AZ91D, AM60B, and AM50A. Insufficient creep strength can lead to clamping load reduction, oil leaks, noise, and vibration. Existing commercial magnesium alloys often lack the necessary combination of properties for these demanding applications.
Status of previous research:
Common die-casting alloys (AZ and AM series) are unsuitable for temperatures above 130°C. Earlier creep-resistant alloys like AS21, AS41, and AE42 had limitations such as poor castability, corrosion resistance, increased cost, or low strength. Gravity casting alloys like ZE41 offer moderate properties but poor corrosion resistance, while high-performance alloys like WE43 and WE54 are very expensive. Recent developments included AS21X (Hydro Magnesium, based on AS21 with RE addition), AJ52X (Noranda, AM50 + Sr), ACM522 (Honda, AM50 + Ce-misch metal + Ca), AXJ alloy (General Motors, AM50 + Ca + Sr), and MEZ (Magnesium Electron, RE + Zn + Mn + Zr/Ca). These alloys showed improvements in some areas but still faced challenges regarding cost, castability, ductility, impact strength, hot-cracking susceptibility, or handling.
Purpose of the study:
To address the limitations of existing alloys, Dead Sea Magnesium Ltd. (DSM) and Volkswagen AG (VW), with academic partners, initiated a program to develop creep-resistant and cost-effective die-casting and gravity-casting magnesium alloys suitable for powertrain components operating at elevated temperatures.
Core study:
The research focused on developing and characterizing new magnesium alloys. Four alloys resulted from this work:
- MRI 153M: A beryllium-free, low-cost, creep-resistant die-casting alloy for operation up to 150°C.
- MRI 230D: A die-casting alloy for higher temperatures (up to 190°C), intended for applications like engine blocks.
- MRI 201S: A gravity-casting alloy developed as a cost-effective alternative to WE43, offering excellent mechanical properties and creep resistance in T6 condition.
- MRI 202S: A high-purity, corrosion-resistant gravity-casting alloy with moderate strength and excellent creep performance, positioned as superior to ZE41.
The study involved evaluating the mechanical properties (tensile, compression, fatigue, impact), creep resistance, corrosion performance, and castability of these new alloys and comparing them with established commercial magnesium alloys (AZ91D, AE42, AS21, ZE41-T5, WE43-T6) and an aluminum alloy (A380). The effects of alloying elements (Al, Ca, Sr, RE misch metal) on properties and cost were analyzed.
5. Research Methodology
Research Design:
The study employed an alloy development approach, combining industrial requirements (from DSM and VW) with materials science principles. The design focused on optimizing the balance between creep resistance, castability, mechanical properties, corrosion resistance, and cost, primarily through controlled additions of alloying elements like aluminum, calcium, strontium, and rare earth (RE) misch metal for die-casting alloys, and zirconium as a grain refiner for gravity-casting alloys.
Data Collection and Analysis Methods:
- Material Preparation: Development and production of the new MRI series alloys.
- Casting: High-pressure die casting (including trials of complex components like transmission housings) and gravity casting (sand or permanent mold).
- Mechanical Testing: Tensile testing (yield strength, ultimate tensile strength, elongation) and compression yield strength testing at room temperature (20°C) and elevated temperatures (e.g., 150°C). Impact strength testing. Fatigue strength testing (rotating bending, 5 × 10⁷ cycles).
- Creep Testing: Determination of stress required to produce 0.2% creep strain at elevated temperatures (e.g., 150°C, 175°C, 200°C, 250°C).
- Corrosion Testing: Salt-spray testing (200 h, ASTM Standard B-117) to determine corrosion rate (mg/cm²/day).
- Comparative Analysis: Properties of the new alloys were systematically compared with existing commercial magnesium alloys (AZ91D, AE42, AS21, ZE41-T5, WE43-T6) and aluminum alloy A380 using data tables (Table I, Table II, Table III) and property diagrams (Figure 1, Figure 2, Figure 3).
Research Topics and Scope:
The research scope covered the development, characterization, and comparative evaluation of new magnesium alloys specifically designed for high-temperature powertrain applications. The topics included:
- Alloy design for die casting and gravity casting.
- Influence of alloying elements (Al, Ca, Sr, RE, Zr) on properties and cost.
- Evaluation of die castability, mechanical properties (ambient and elevated temperature), creep resistance, corrosion performance.
- Comparison with benchmark commercial magnesium and aluminum alloys.
- Positioning the new alloys (MRI 153M, MRI 230D, MRI 201S, MRI 202S) based on performance and cost trade-offs.
6. Key Results:
Key Results:
- Four new magnesium alloys were developed: MRI 153M, MRI 230D (die-casting), MRI 201S, MRI 202S (gravity-casting).
- MRI 153M exhibits die castability similar to AZ91D but with substantially superior elevated-temperature strength and creep resistance (at 130-150°C, 50-85 MPa) and better corrosion resistance than AE42/AS21. It is positioned as a low-cost option for applications up to 150°C. (Table I)
- MRI 230D offers excellent creep resistance (comparable to A380 aluminum at 150-175°C, 70 MPa), good castability, high strength, and superior corrosion behavior, suitable for applications up to 190°C. (Table I)
- MRI 201S (T6 condition) provides excellent mechanical properties, creep resistance, castability, pressure tightness, weldability, dimensional stability, and corrosion resistance, making it a potential cost-effective substitute for WE43. (Table II)
- MRI 202S is a high-purity, corrosion-resistant gravity-casting alloy with moderate strength but excellent creep performance, significantly superior to ZE41 in creep and corrosion. (Table II)
- The study confirmed the trade-offs in alloy design: increasing aluminum improves castability, ambient strength, and corrosion resistance but degrades creep, ductility, and impact strength (Figure 1a). Alloying with alkaline earth elements (Ca, Sr) and RE misch metal improves creep resistance and ambient strength but can deteriorate castability, ductility, impact strength, and increase cost (Figure 1b).
- Calcium was identified as providing the maximum increase in creep and yield strength per dollar of cost increase compared to Sr and RE, but concentrations >0.3% negatively impact castability and ductility.
- Comparative diagrams (Figure 2, Figure 3) and a rating table (Table III) were presented to visualize the relative positioning of the new and existing alloys based on combined properties (creep, castability, tensile, fatigue, ductility, corrosion) versus cost for applications at 150°C and 180°C.
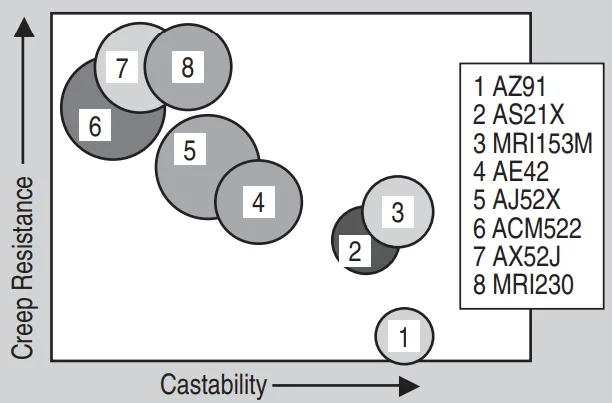
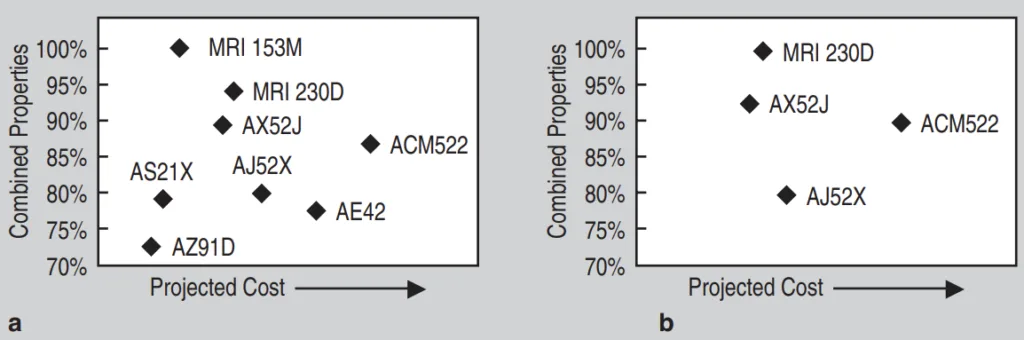
Figure Name List:
- Figure 1. The effect of (a) aluminum and (b) alloying elements on the properties and cost of magnesium die-casting alloys.
- Figure 2. The creep resistance vs. castability and cost (represented by the relative size of a circle that is larger with increasing costs) of reviewed magnesium alloys.
- Figure 3. The combined properties rating vs. projected cost of new magnesium alloys designated for applications at (a) 150°C and (b) 180°C.
- Table I. Mechanical Properties of MRI 153M and MRI 230D
- Table II. Mechanical Properties of MRI 201S & MRI 202S Alloys
- Table III. Combined Properties Rating of New Mg Alloys for Applications at 150°C and 180°C
7. Conclusion:
The study successfully developed four new magnesium alloys (MRI 153M, MRI 230D for die casting; MRI 201S, MRI 202S for gravity casting) targeted for high-temperature powertrain applications. These alloys offer improved combinations of properties, particularly creep resistance, compared to many existing commercial magnesium alloys, while addressing cost considerations. MRI 153M provides a cost-effective solution for applications up to 150°C with good castability. MRI 230D offers high creep resistance comparable to A380 aluminum up to 190°C. MRI 201S presents a high-performance, cost-effective alternative to WE43 for gravity casting, while MRI 202S offers significantly improved creep and corrosion resistance over ZE41. The research highlights the critical balance required between conflicting properties like creep resistance, castability, and cost, influenced significantly by the choice and concentration of alloying elements (Al, Ca, Sr, RE). The presented data and comparative analyses (Tables I-III, Figures 1-3) provide valuable information for design engineers to select the optimal magnesium alloy based on specific service requirements and cost targets for advanced powertrain components.
8. References:
- [1.] H. Friedrich and S. Schumann, "The Second Age of Magnesium Research Strategies to Bring the Automotive Industry's Vision to Reality," Proceedings of the Second Israeli International Conference on Magnesium Science & Technology, ed. E. Aghion and D. Eliezer (Beer-Sheva, Israel: The Magnesium Research Institute, 2000), pp. 9-18.
- [2.] P. Lyon, J.F. King, and K. Nuttal "A New Magnesium HPDC Alloy for Elevated Temperature Use," Proceedings of the Third International Magnesium Conference, ed. G.W. Lorimer (London: The Institute of Materials, 1996), pp. 99-108.
- [3.] S. Koike et al., "Development of Lightweight Oil Pans Made of a Heat-Resistant Magnesium Alloy for Hybrid Engines," SAE Technical Paper 2000-01-1117 (Warrendale, PA: SAE, 2000).
- [4.] K. Pettersen et al., "Creep-Resistant Magnesium Alloy Development," Magnesium Alloys and Their Applications, ed. K.U. Kainer (Weinheim, Germany: Wiley-VCH Verlag GmbH, 2000), pp. 29-34.
- [5.] B. Powell et al., "Development of Creep-Resistant Magnesium Alloys for Powertrain Applications,” Light Metal Applications for the Automotive Industry: Aluminum and Magnesium, SAE Special Publication SP-1622, paper number 2001-01-0422 (Warrendale, PA: SAE, 2001).
- [6.] M. Pekguleryuz and E. Baril, "Development of Creep Resistant Mg-Al-Sr Alloys,” Magnesium Technology 2001, ed. J.N. Hryn (Warrendale, PA: TMS, 2001), pp. 119-126.
- [7.] B. Bronfín et al., "Die Casting Magnesium Alloys for Elevated Temperature Applications," Magnesium Technology 2001, ed. J.N. Hryn (Warrendale, PA: TMS, 2001), pp. 127-130.
- [8.] D. Argo et al., "Process Parameters and Die Casting of Noranda's AJ52 High Temperature Mg-Al-Sr Alloy," Magnesium Technology 2002, ed. H.I. Kaplan, (Warrendale, PA: TMS, 2002), pp. 87-94.
- [9.] B.R. Powell et al., "The Die Castability of Calcium-Containing Magnesium Alloys: Thin-Wall Computer Case," Magnesium Technology 2002, ed. H.I. Kaplan (Warrendale, PA: TMS, 2002), pp. 123-130.
- [10.] I.J. Polmear, Metallurgy of Light Alloys (New York: Halsted Press, 1996), pp. 196-247.
- [11.] J.F. King, "Development of Practical High Temperature Magnesium Casting Alloys,” Magnesium Alloys and Their Applications, ed. K.U. Kainer (Weinheim, Germany: Wiley-VCH Verlag GmbH, 2000), pp. 14-22.
- [12.] F. Von Buch et al., "New Die Casting Alloy MRI 153 for Power Train Applications," Magnesium Technology 2002, ed. H.I. Kaplan (Warrendale, PA: TMS, 2002), pp. 61-68.
9. Copyright:
- This material is a paper by "E. Aghion, B. Bronfin, F. Von Buch, S. Schumann, and H. Friedrich". Based on "Newly Developed Magnesium Alloys for Powertrain Applications".
- Source of the paper: https://doi.org/10.1007/s11837-003-0206-8
This material is summarized based on the above paper, and unauthorized use for commercial purposes is prohibited.
Copyright © 2025 CASTMAN. All rights reserved.