This introduction paper is based on the paper "Mould Design for Clutch Housing Parts using a Casting Simulation of High Pressure Die Casting" published by "International Journal of Precision Engineering and Manufacturing".
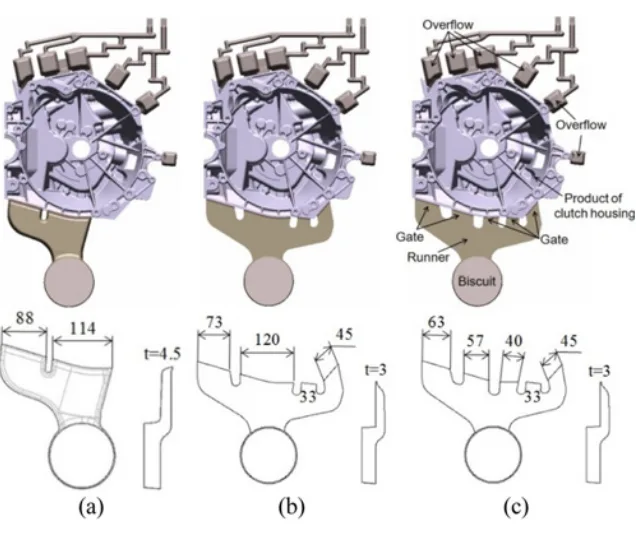
1. Overview:
- Title: Mould Design for Clutch Housing Parts using a Casting Simulation of High Pressure Die Casting
- Author: Seong Il Jeong, Chul Kyu Jin, Hyung Yoon Seo, Jong Deok Kim, and Chung Gil Kang
- Year of publication: 2016
- Journal/academic society of publication: International Journal of Precision Engineering and Manufacturing
- Keywords: High pressure die casting, Gate system, Casting simulation, Casting aluminium alloy, Casting defects
2. Abstract:
To manufacture automotive clutch housing parts in application of high pressure die casting, the following three gating system designs were taken into account. Since adopting these gating system designs in actual experiment would require too much cost and time, a casting simulation program was used instead: Analyzed were flow behaviors as elements filled the mould. Based on the air pressure and air pocket after the melt was completely filled in mould, the final gating system design was selected. The third gating system design with 5 gates was expected to involve less defects than others was even and uniform. A cooling channel and a chill vent were designed. In a real casting test, five products in total were produced. All of them were sound and involved neither any spot of insufficient filling nor defect on the surface. The real test expected to involve shrinkage porosities based on the analysis and those of the manufactured products that actually involved shrinkage porosities did not exactly correspond to each other but were similar. The hardness was about 84 HV regardless of location.
3. Introduction:
High pressure die casting is casting process using at high speed and high pressure. Nonferrous metals are rapidly filled into a mould and then being solidified, the castings are removed from the mould. This method is appropriate for mass production of products with complicated and precise shapes and with uniform quality. In addition, it is possible to produce the product of a thin plate type. The applicable areas continue increasing. High pressure die casting is often applied to aluminum alloys, and recently, a automobile manufacturer is conducting its research on mass production in application of high pressure and high vacuum die casting with magnesium alloy.
Defects of high pressure die casting that may occur include flow defects such as inclusion of air or other substances, and micro porosity (blow holes or pin hole) during the filling process, shrinkage porosities in the solidification process, etc. . In the past mould design, the trial and error method of mould designers and onsite technicians have a lot of difficulties, but in the recent high pressure casting mould design adopts Computer Aided Engineering (CAE) for the filling and solidification processes right from the initial development stage, which makes it possible to establish the optimal mould design plan based on the prediction and evaluation of product quality. In addition, as many designers adopt mould design methods in combination with CAE based on their onsite experiences, the fraction defective have decreased with the costs reduced and the development period shortened. Most of the published theses in this area focus on casting simulations or casting techniques and improvement methods to reduce the manufacturing costs in a way of mass production. In contrast, there are few researches on mould design that decides the quality of products.
This study includes a casting simulation for clutch housing products that control or deliver the dynamic force of an automotive engine by means of MAGMA, a casting software. First of all, the optimal gating system design and casting conditions were sought to mass-produce items by predicting or preventing possible casting defects in the filling and solidification processes. Based on the database, ways to minimize casting costs are then sought. The optimal gating system design was applied to the mould design, and the best possible quality products were manufactured with defects minimized in the casting process after mould production.
4. Summary of the study:
Background of the research topic:
High pressure die casting (HPDC) is a widely used manufacturing process for mass production of complex, precise, and uniform quality parts, particularly thin-walled components from nonferrous alloys like aluminum and magnesium, often for the automotive industry. However, HPDC processes are prone to defects such as flow defects (air inclusion), micro porosity (blow holes, pin holes), and shrinkage porosities.
Status of previous research:
Traditionally, mould design relied heavily on the trial-and-error experience of designers and technicians. More recently, Computer Aided Engineering (CAE) tools are increasingly adopted from the initial design stage to simulate filling and solidification processes. This allows for prediction, evaluation, and optimization of mould designs, leading to reduced defects, costs, and development time. While many studies focus on simulation techniques or cost reduction, research specifically targeting how mould design influences product quality is less common.
Purpose of the study:
The study aimed to utilize casting simulation software (MAGMAsoft) to design an optimal mould for automotive clutch housing parts made of ALDC 12 aluminum alloy via HPDC. The specific goals were to determine the best gating system design and casting conditions, predict and prevent potential casting defects during filling and solidification, minimize manufacturing costs based on simulation data, and ultimately produce high-quality parts with minimized defects through an optimized mould design.
Core study:
The core of the study involved designing and simulating three different gating systems (Case I, II, III) for the clutch housing part using Pro/ENGINEER and MAGMAsoft. Case I featured a vertical gate, Case II used four gates including side gates, and Case III modified Case II with five gates to control flow. Cooling channels were designed based on calculated heat loads (Eqs. 1-8), mixing spot and line cooling. A wave-shaped chill vent was designed (STD 61 material) to facilitate gas escape. Casting simulations were performed using MAGMAsoft, analyzing filling behavior, temperature distribution, air contact, air pressure, and solidification patterns for each gating design under defined HPDC conditions (ALDC 12 alloy, STD 61 mould, specific temperatures, speeds, 1600 ton machine). Based on simulation results predicting the most uniform fill and fewest defects, Case III was selected. Finally, actual casting experiments were conducted using the Case III mould design to validate the simulation findings by producing parts and analyzing their quality (visual inspection, microstructure, hardness) and comparing predicted defects (shrinkage porosity) with actual occurrences.
5. Research Methodology
Research Design:
The study employed a comparative approach combining computational simulation and experimental validation. Three distinct gating system designs for a clutch housing mould were modeled and simulated. The design predicted to yield the best results (Case III) was selected, manufactured, and used in actual high pressure die casting trials to verify the simulation predictions and assess the final product quality.
Data Collection and Analysis Methods:
- Simulation: MAGMAsoft casting simulation software was used. The analysis relied on governing equations for fluid flow and heat transfer (mass conservation Eq. (9), momentum conservation/Navier-stokes Eq. (10), energy conservation Eq. (11), volume of fluid Eq. (12)), solved using the Finite Volume Method (FVM) with a specific mesh resolution (over 1 million metal cells). Simulation outputs analyzed included melt flow patterns (filling behavior, velocity), temperature distribution, air contact, air pressure distribution, and solidification progression to predict potential defects like insufficient filling, air entrapment, and shrinkage porosity.
- Experiment: Actual HPDC was performed using a 1600 ton cold chamber machine with ALDC 12 aluminum alloy and the optimized mould (Case III design). Process parameters mirrored the simulation settings. Mould pre-heating temperatures were measured using a non-contact thermo-graphic camera. Five cast parts were produced and inspected visually for defects (incomplete filling, cracks, flow marks). The shape of the filled chill vent was examined. Microstructure analysis was conducted on sections from average and thick areas of the part. Vickers hardness was measured at seven different locations on a sample part using a 200 g load.
- Comparison: Simulation predictions, particularly regarding filling uniformity, defect locations (air pockets, shrinkage porosity), were compared qualitatively and quantitatively (where applicable) with the results obtained from the experimental castings.
Research Topics and Scope:
The research focused on the mould design for an automotive clutch housing part manufactured using high pressure die casting with ALDC 12 aluminum alloy. The scope included:
- Design and comparison of three different gating systems (runner, gate, overflow).
- Design of mould cooling channels based on thermal calculations.
- Design of a chill vent for gas evacuation.
- Casting simulation using MAGMAsoft to predict filling, solidification, and potential defects.
- Selection of the optimal gating system based on simulation results.
- Experimental validation through actual casting trials (5 shots).
- Analysis of the cast product quality, including visual inspection, microstructure, and hardness testing.
- Comparison between simulation predictions (especially porosity) and experimental results.
6. Key Results:
Key Results:
- Simulation analysis of three gating systems (Case I, II, III) showed that Case III (5 gates) provided the most uniform filling pattern and temperature distribution, with potentially less air contact and better air pressure management compared to Case I and Case II (Fig. 5, Fig. 6, Table 5).
- Case III was selected as the optimal design due to its predicted "good" overall performance in simulation, particularly in handling potential oxide/insertion discharge issues compared to Case I and offering a more uniform flow than Case II (Table 5).
- Cooling channel design calculations yielded required effective lengths, considering both line and spot cooling (spot cooling being 1.4-2.0 times more effective) (Section 2.1.2, Fig. 2).
- A specific chill vent design with 8 waves of varying thickness (1 mm, 0.8 mm, 0.6 mm) and a cushion part was implemented (Section 2.1.3, Fig. 3).
- Simulation of solidification for Case III predicted slower cooling in the thicker central and left areas, indicating a high probability of shrinkage porosity formation there (Fig. 8).
- Experimental casting using the Case III mould design successfully produced 5 complete clutch housing parts without insufficient filling or surface flow marks (Fig. 11).
- The chill vent in the first experimental shot filled up to the 4th-5th wave, indicating its function in venting gas (Fig. 12).
- Shrinkage porosity was observed in the thick sections of the experimentally cast parts, broadly correlating with the locations predicted by simulation, although not identical, suggesting the influence of real-world process variations (Fig. 13).
- Microstructural analysis revealed differences between average thickness (needle-shaped Si in eutectic network) and thick sections (primary α-Al phase + eutectic phase with less defined Si particles) due to different solidification rates (Fig. 14).
- Vickers hardness measurements showed consistent hardness of approximately 84 HV across various locations on the cast part (Fig. 15).
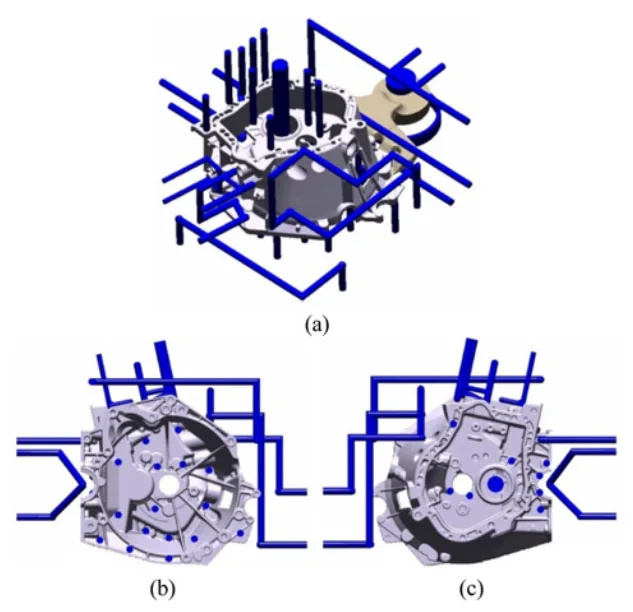
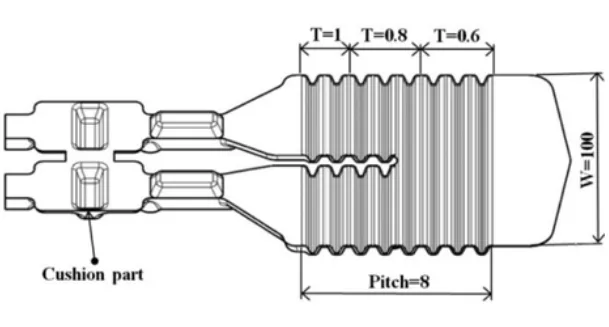
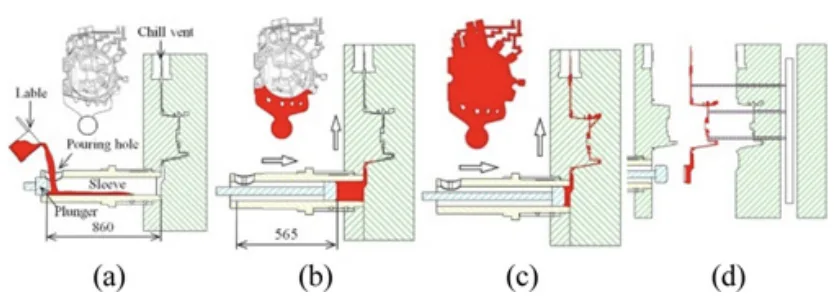
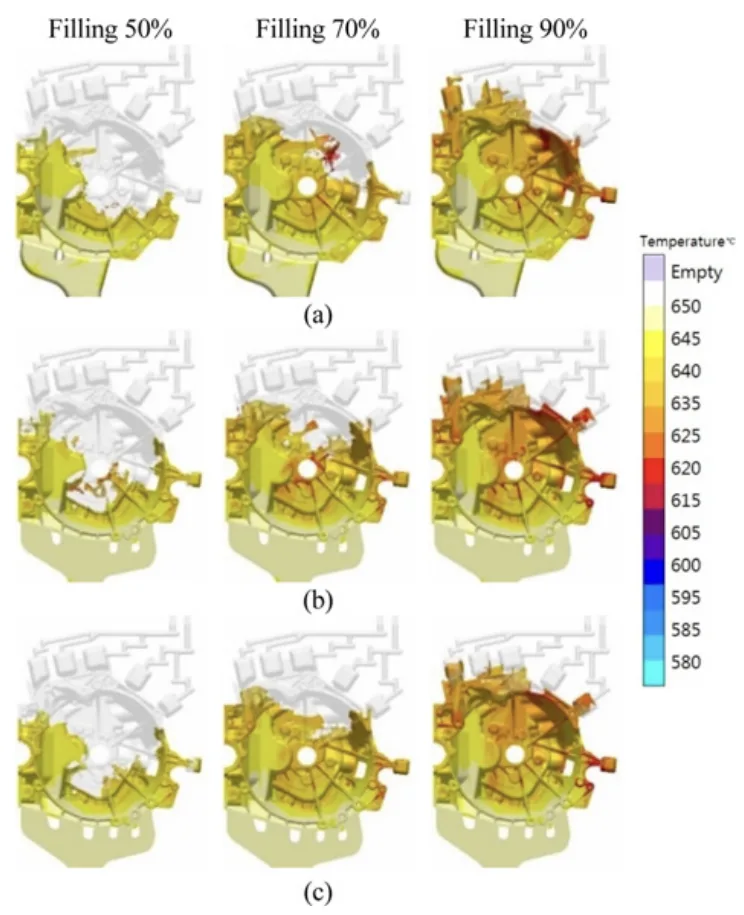
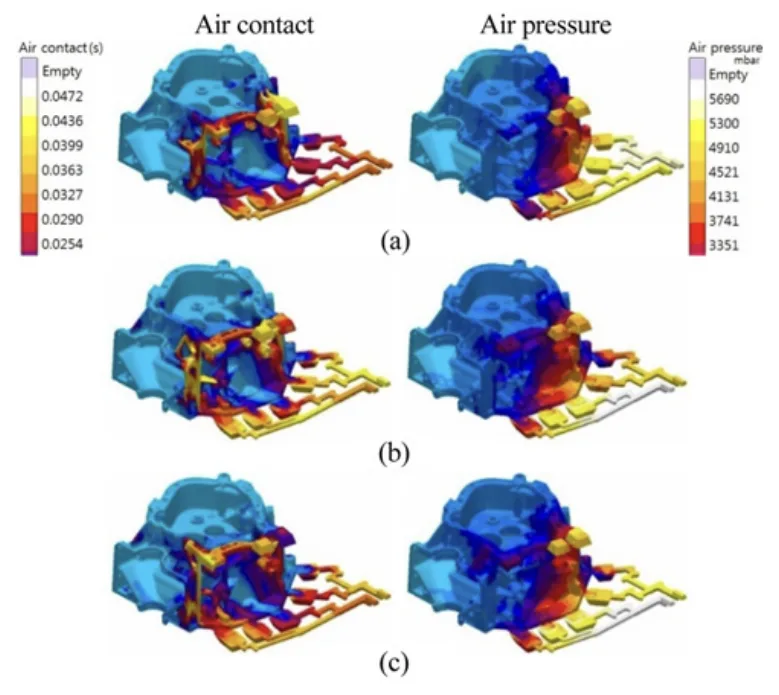
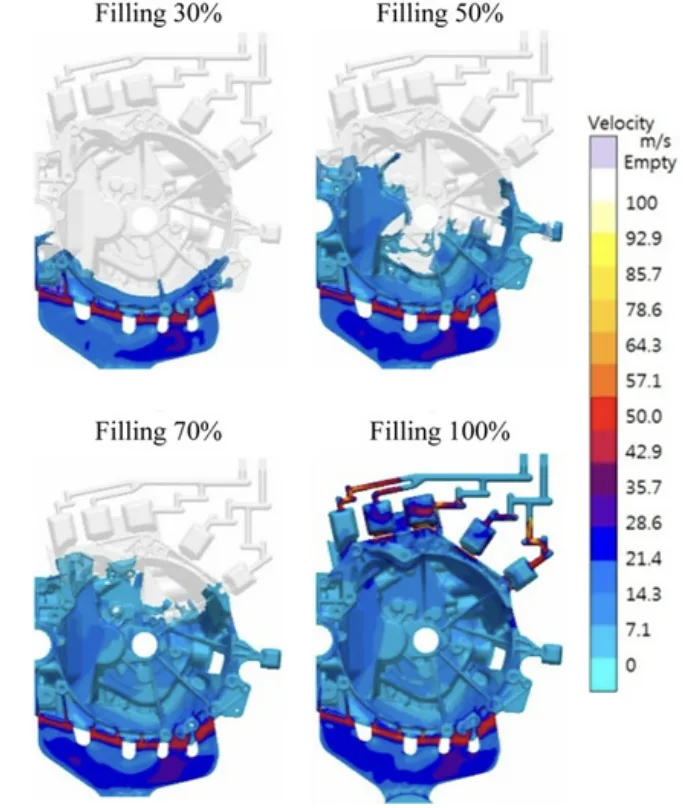
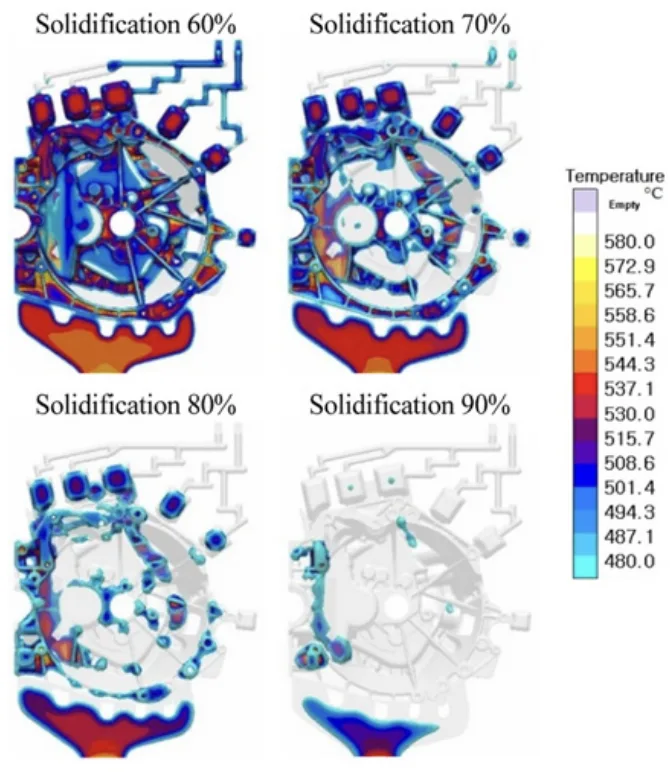
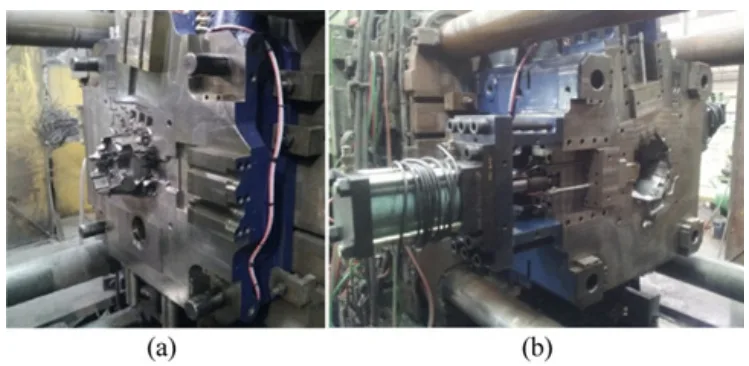
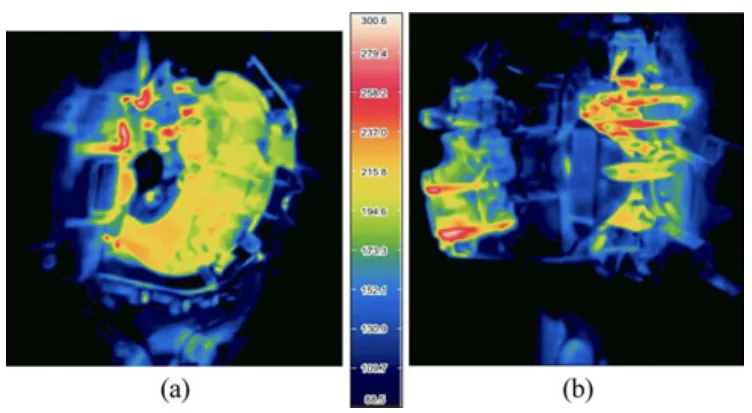
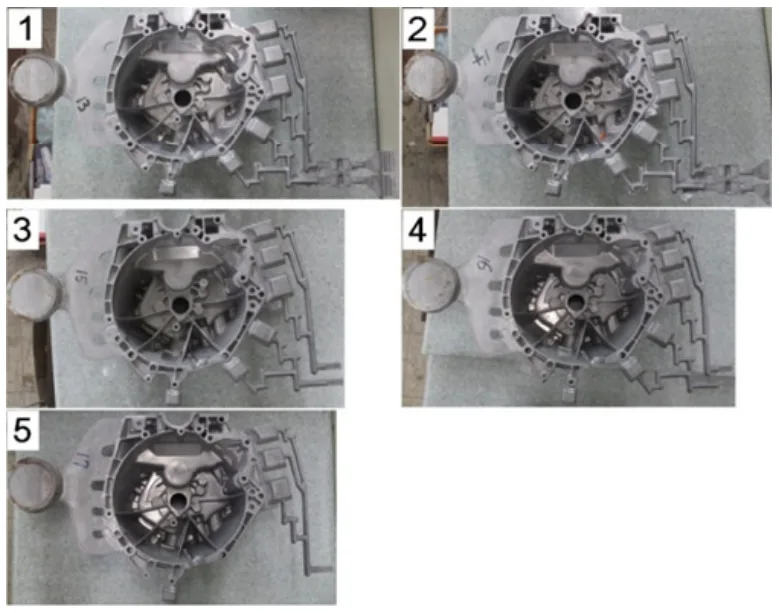
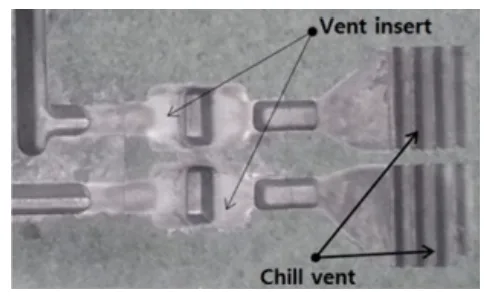
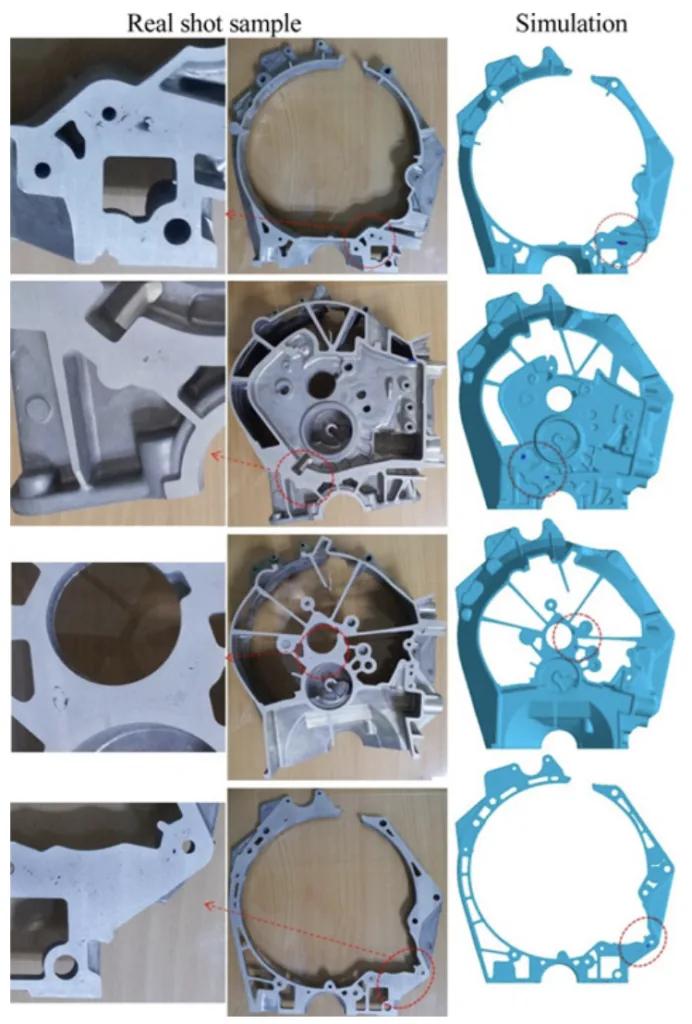
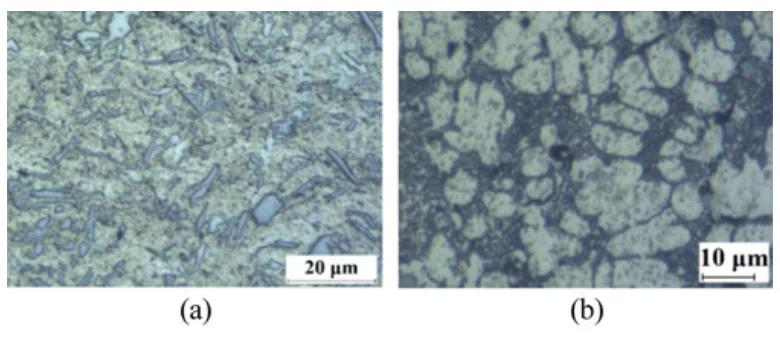
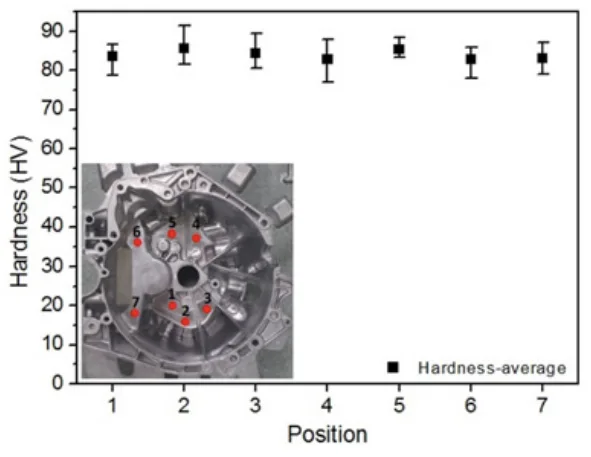
Figure Name List:
- Fig. 1 Gating system design of clutch housing: (a) case I, (b) case II, and (c) case III
- Fig. 2 Cooling line of mould: (a) 3D view, (b) fixed mould view and (c) movable mould view
- Fig. 3 The chill vent for mould
- Fig. 4 Schematic diagram of the high pressure die casting process: (a) pouring melt, (b) slow shot, (c) fast shot, and (d) casting removal by ejector
- Fig. 5 Filling behavior by different gating systems: (a) case I, (b) case II, and (c) case III
- Fig. 6 Air contact and air pressure by different gating systems: (a) case I, (b) case II, and (c) case III
- Fig. 7 Velocity distribution of case III gating system
- Fig. 8 Solidification behavior of case III gating system
- Fig. 9 Moulds assembled high pressure die casting machine: (a) fixed mould and (b) movable mould
- Fig. 10 Block diagram of multi-modal chatter model of a high speed machining center: (a) fixed mould and (b) movable mould
- Fig. 11 Fabricated clutch housing castings: 1 first shot, 2 second shot, 3 third shot, 4 fourth shot and 5 fifth shot
- Fig. 12 Chill vent connected with first shot castings
- Fig. 13 Comparison of porosity distribution between simulation and real shot test
- Fig. 14 Microstructures of clutch housing in different positions: (a) normal thickness and (b) thick thickness
- Fig. 15 Vickers hardness at different positions
7. Conclusion:
In this study, a gating system for ALDC12-used automotive clutch housing parts was designed by means of MAGMAsoft. Through the real shot, perfect clutch housing samples were manufactured with no part of insufficient filling. The simulation and experiment results are summarized as follows:
- Through the casting simulation program, it was demonstrated that the gating system design with 5 gates had the product filled more thoroughly and evenly than gating system designs with 2 and 4 gates, and that the former involved uniform temperature distribution over the product and involved less air pockets in the product than the other designs. Based on the analysis result, the gating system design with 5 gates was selected.
- As for the effective length of the coolant pipe necessary for the mould, the spot cooling efficiency was 1.4 to 2.0 times better than that of line cooling. Hence, it is expected that shrinkage defect can be minimized when spot cooling is applied to the full.
- All of the 5 clutch housing samples including the overflows manufactured through the shot test were perfectly formed with no part of insufficient formation. There was neither crack or flow mark on the surface either. Vickers hardness was about 84HV regardless of location.
- As solidification was slow at the thick parts of the product, shrinkage porosities were formed within the product. As for the location of shrinkage porosity occurrence, the result of the casting simulation was different from the actual location of occurrence probably because of various factors in the onsite condition. As shown in the result, it is desirable to grasp and predict the tendencies in reference to casting simulations rather than relying on them absolutely.
8. References:
- [1] Jin, C. K. and Kang, C. G, "Fabrication Process Analysis and Experimental Verification for Aluminum Bipolar Plates in Fuel Cells by Vacuum Die-Casting," Journal of Power Sources, Vol. 196, No. 20, pp. 8241-8249, 2011.
- [2] Jin, C. K. and Kang, C. G., "Fabrication by Vacuum Die Casting and Simulation of Aluminum Bipolar Plates with Micro-Channels on Both Sides for Proton Exchange Membrane (PEM) Fuel Cells," International Journal of Hydrogen Energy, Vol. 37, No. 2, pp. 1661-1676, 2012.
- [3] Choi, S., Kim, Y., Cho, J., and Kang, C., "Influence of Die Casting Process Parameters on Castability and Properties of Thin Walled Aluminium Housings," International Journal of Cast Metals Research, Vol. 21, No. 1-4, pp. 330-333, 2008.
- [4] Dørum, C., Hopperstad, O., Berstad, T., and Dispinar, D., "Numerical Modelling of Magnesium Die-Castings using Stochastic Fracture Parameters," Engineering Fracture Mechanics, Vol. 76, No. 14, pp. 2232-2248, 2009.
- [5] Cho, C. Y., Uan, J. Y., and Lin, H. J., "Surface Compositional Inhomogeneity and Subsurface Microstructures in a Thin-Walled AZ91D Plate Formed by Hot-Chamber Die Casting," Materials Science and Engineering: A, Vol. 402, No. 1, pp. 193-202, 2005.
- [6] Timelli, G. and Bonollo, F., "Fluidity of Aluminium Die Castings Alloy," International Journal of Cast Metals Research, Vol. 20, No. 6, pp. 304-311, 2007.
- [7] Zhao, H. D., Wang, F., Li, Y. Y., and Xia, W., "Experimental And Numerical Analysis of Gas Entrapment Defects in Plate ADC12 Die Castings," Journal of Materials Processing Technology, Vol. 209, No. 9, pp. 4537-4542, 2009.
- [8] Tian, C., Law, J., Van Der Touw, J., Murray, M., Yao, J.-Y., Graham, D., and John, D.S., "Effect of Melt Cleanliness on the Formation of Porosity Defects in Automotive Aluminium High Pressure Die Castings," Journal of Materials Processing Technology, Vol. 122, No. 1, pp. 82-93, 2002.
- [9] Kim, Y.-C., Kang, C.-S., Cho, J.-I., Jeong, C.-Y., Choi, S.-W., and Hong, S.-K., "Die Casting Mold Design of the Thin-Walled Aluminum Case by Computational Solidification Simulation," Journal of Materials Science and Technology, Vol. 24, No. 3, pp. 383-388, 2008.
- [10] Chang, Q. M., Chen, C. J., Zhang, S. C., Schwam, D., and Wallace, J. F., "Effects of Process Parameters on Quality of Squeeze Casting A356 Alloy," International Journal of Cast Metals Research, Vol. 23, No. 1, pp. 30-36, 2013.
- [11] Hu, B. H., Tong, K. K., Niu, X. P., and Pinwill, I., "Design and Optimisation of Runner and Gating Systems for the Die Casting of Thin-Walled Magnesium Telecommunication Parts through Numerical Simulation," Journal of Materials Processing Technology, Vol. 105, No. 1-2, pp. 128-133, 2000.
- [12] Hangai, Y. and Kitahara, S., "Quantitative Evaluation of Porosity in Aluminum Alloy Die Castings by Fractal Analysis of Spatial Distribution of Area," Materials & Design, Vol. 30, No. 4, pp. 1169-1173, 2009.
- [13] Chen, J. H., Hwang, W. S., Wu, C. H., and Lu, S. S., "Design of Die Casting Process of Top Cover of Automobile Generator Through Numerical Simulations and Its Experimental Validation," International Journal of Cast Metals Research, Vol. 24, No. 3-4, pp. 163-169, 2011.
- [14] Domkin, K., Hattel, J. H., and Thorborg, J., "Modeling Of High Temperature-and Diffusion-Controlled Die Soldering in Aluminum High Pressure Die Casting," Journal of Materials Processing Technology, Vol. 209, No. 8, pp. 4051-4061, 2009.
- [15] Kim, G.-Y., "Die Casting Die Designing (3)-Design of Die Cooling," Journal of Korea Foundry Society, Vol. 19, No. 4, pp. 369-369, 1999.
- [16] Kang, B.-H., Kim, T.-B., and Kim, K.-Y., "Evaluation on Performance of Chill Vent In High Pressure Die Casting by using a Commercial Software," Journal of Korea Foundry Society, Vol. 32, No. 3, pp. 133-137, 2012.
9. Copyright:
- This material is a paper by "Seong Il Jeong et al.". Based on "Mould Design for Clutch Housing Parts using a Casting Simulation of High Pressure Die Casting".
- Source of the paper: https://doi.org/10.1007/s12541-016-0178-6
This material is summarized based on the above paper, and unauthorized use for commercial purposes is prohibited.
Copyright © 2025 CASTMAN. All rights reserved.