This article introduces the paper ["D 4.1. MOTOR SYSTEM EFFICIENCY TRENDS"] published by [EU-MORE].
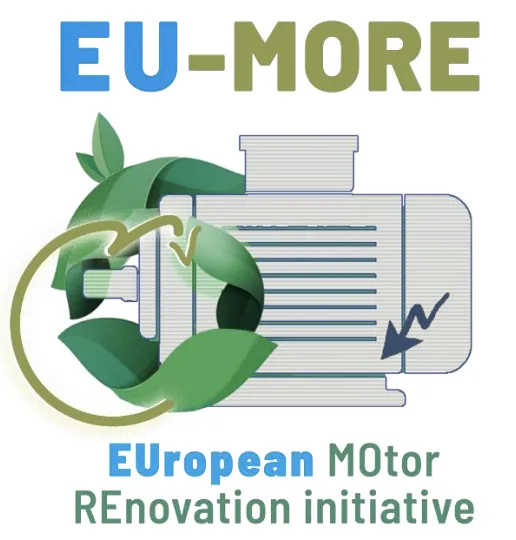
1. Overview:
- Title: D 4.1. MOTOR SYSTEM EFFICIENCY TRENDS
- Author: João Fong, Anibal T. de Almeida, Konstantin Kulterer
- Publication Year: 2024
- Publishing Journal/Academic Society: EU-MORE
- Keywords: Motor efficiency, MEPS, IE4, IE5, Induction Motors, Synchronous Motors, VSD, Digital Technologies
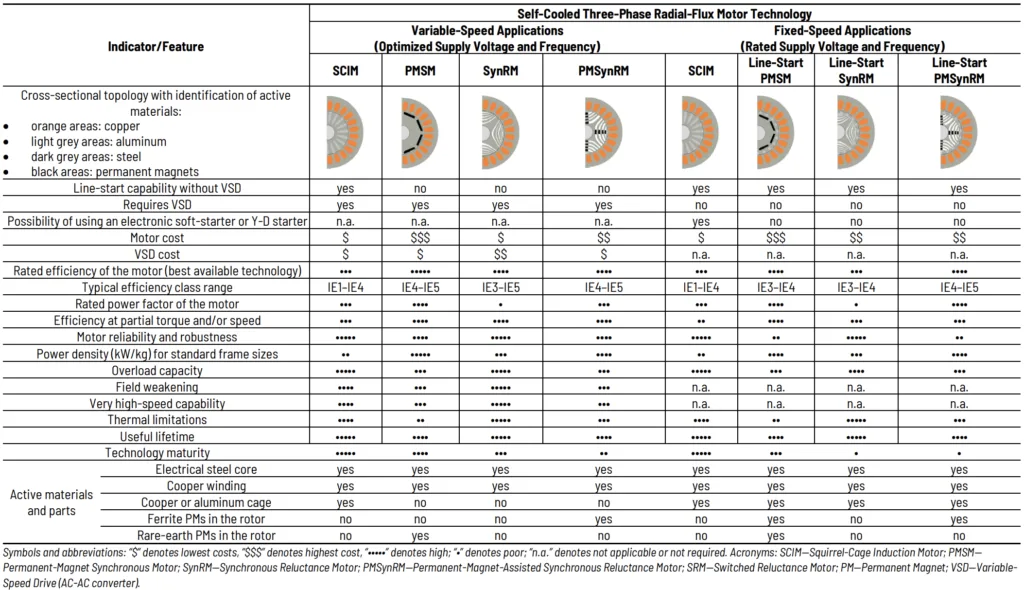
2. Abstracts or Introduction
The paper "D 4.1. MOTOR SYSTEM EFFICIENCY TRENDS" provides an overview of the trends in motor system efficiency, driven by increasing global awareness of energy efficiency and the implementation of Minimum Energy Performance Standards (MEPS). The document highlights the progression of motor efficiency classes, reaching beyond IE3 to super-premium (IE4) and ultra-premium (IE5) levels. It discusses various motor technologies, including induction motors, permanent magnet motors, and synchronous reluctance motors, evaluating their efficiency and applicability in different scenarios, particularly focusing on fixed speed and variable speed applications. The report also explores the role of Variable Speed Drives (VSDs) in optimizing motor system efficiency and delves into the integration of digital technologies for enhanced monitoring, maintenance, and overall system performance.
3. Research Background:
Background of the Research Topic:
The increasing importance of energy-efficiency and its benefits, coupled with the growing number of countries adopting Minimum Energy Performance Standards (MEPS) for motors, forms the core background of this research. This global trend has spurred significant advancements in motor energy efficiency, pushing levels beyond the IE3 standard to achieve super-premium efficiency motors (IE4 and IE5). The paper addresses the need to understand these advancements and their implications for industrial applications.
Status of Existing Research:
Current market availability includes induction motors with IE4 efficiency, and technologies like permanent magnet motors and synchronous reluctance motors are enabling efficiencies beyond IE4 and IE5 limits. Three-phase squirrel cage induction motors (SCIM) remain prevalent for fixed-speed applications due to their reliability. However, technologies like line-start permanent magnet motors (LSPM) and DOL synchronous reluctance motors (SynRM) are emerging as alternatives. For variable speed applications, permanent magnet synchronous motors (PMSM) and Synchronous Reluctance Motors (SynRM) are recognized as efficient and reliable alternatives to induction motors, capable of exceeding IE5 efficiency levels by eliminating rotor losses at synchronous speed.
Necessity of the Research:
Understanding the trends in motor efficiency is crucial for industries to adopt energy-efficient solutions and comply with evolving MEPS regulations. The research is necessary to provide a comprehensive overview of available motor technologies, their efficiency characteristics, and the potential of digital technologies to further optimize motor system performance. This knowledge is essential for making informed decisions regarding motor selection, application, and maintenance to maximize energy savings and operational efficiency.
4. Research Purpose and Research Questions:
Research Purpose:
The primary purpose of this report is to analyze and present the current trends in motor system efficiency, focusing on technological advancements in motor designs, the role of variable speed drives, and the integration of digital technologies. It aims to provide a handbook-level overview of motor technologies and efficiency improvements to inform stakeholders about the latest developments and opportunities in this field.
Key Research:
- To outline the evolution of motor efficiency classes and the technologies enabling IE4 and IE5 levels.
- To compare different motor technologies, including induction motors, permanent magnet motors, and synchronous reluctance motors, in terms of efficiency, performance, and application suitability.
- To investigate the contribution of Variable Speed Drives (VSDs) to motor system efficiency and the advancements in VSD technology.
- To explore the opportunities and challenges associated with integrating digital technologies for motor system optimization, including condition monitoring, predictive maintenance, and process optimization.
Research Hypotheses:
This report is descriptive and analytical in nature, focusing on presenting trends and technological overviews rather than testing specific hypotheses. Therefore, research hypotheses are not explicitly formulated.
5. Research Methodology
Research Design:
This report employs a descriptive research design, based on a review of existing literature, industry standards, and market data related to motor technologies and efficiency trends. It synthesizes information to provide a comprehensive overview of the current state and future directions in motor system efficiency.
Data Collection Method:
The data is collected from catalogue data, technical literature, industry reports, and standards documents related to electric motors, variable speed drives, and digital technologies in motor systems. Specific sources are referenced throughout the document, including ISR-UC based on catalogue data, and IEA-4EMSA for VSD efficiency.
Analysis Method:
The analysis is qualitative, involving a comparative assessment of different motor technologies and efficiency classes. Data is presented through figures and tables to illustrate efficiency trends, technology comparisons, and the impact of various factors on motor system performance. The report synthesizes information to identify key trends, opportunities, and challenges in motor system efficiency.
Research Subjects and Scope:
The research scope encompasses various electric motor technologies relevant to industrial applications, with a focus on three-phase radial-flux motors. It includes induction motors, synchronous motors (permanent magnet and synchronous reluctance), and line-start versions of these technologies. The scope also extends to variable speed drives and digital technologies applicable to motor systems. The geographical scope is primarily focused on the European context, considering EU regulations and initiatives like EU-MORE.
6. Main Research Results:
Key Research Results:
- Motor Efficiency Classes: Motor efficiency has progressed significantly, reaching IE4 and IE5 levels with technologies like permanent magnet and synchronous reluctance motors. Induction motors with IE4 efficiency are widely available.
- Induction Motor Improvements: Efficiency improvements in induction motors are achieved through superior materials, optimized design, and advanced winding techniques like hairpin windings, increasing slot fill factor and reducing losses. (Figure 3, Figure 4, Figure 5)
- Synchronous Motors Advantages: Synchronous motors (PMSM, SynRM) offer higher efficiency than induction motors, especially in variable speed applications, by eliminating rotor losses. Axial flux motors provide high power density and compact design. (Figure 6, Figure 8, Figure 9, Figure 10, Figure 11, Figure 12, Figure 13, Figure 14)
- Line-Start Motors: Line-start permanent magnet motors (LSPM) and line-start synchronous reluctance motors (LSSynRM) offer high efficiency and direct-on-line starting capability, providing alternatives to induction motors in specific applications. (Figure 15, Figure 19)
- Variable Speed Drives (VSDs): VSDs are crucial for optimizing motor system efficiency in variable load applications. Wide Band Gap (WBG) materials (GaN, SiC) in VSDs further reduce losses and improve performance. (Figure 20, Figure 21, Figure 22, Figure 23)
- Motor System Efficiency Approach: Optimizing motor system efficiency requires a holistic approach, considering the entire motor driven unit (MDU) and motor system, including power supply, controls, transmission, driven equipment, and process components. (Figure 24, Figure 25)
- Digital Technologies for Optimization: Digital technologies, including smart sensors and IIoT, offer opportunities for real-time monitoring, condition-based maintenance, predictive maintenance, and process optimization, leading to improved efficiency and reliability. (Figure 30, Figure 31, Figure 32, Figure 33, Figure 34, Figure 35)
Analysis of presented data:
- Figure 1: Illustrates the efficiency classes defined by IEC600-34-30-1 and commercially available motor efficiencies, showing that LSPM and PM motors can reach IE5 efficiency, while SCIM and SynRM typically align with IE4/IE5.
- Figure 2: Shows the breakdown of induction motor losses by type, indicating that stator I²R losses and rotor I²R losses are significant contributors.
- Figure 6: Compares the total motor weight of different motor technologies, demonstrating the weight advantages of synchronous reluctance motors and permanent magnet motors.
- Figure 12: Presents commercial motors power density for vehicle applications, highlighting the high power density of axial flux motors.
- Figure 15: Shows the efficiency of commercially available LSPM IE4 motors, demonstrating high efficiency across different frame sizes and power outputs.
- Figure 18: Compares the efficiency of 110kW PDS with IE3-class SCIM and IE5-class SynRM, showing the superior part-load efficiency of SynRM.
- Figure 26: Displays bands of typical power factor and energy efficiency versus loading for cage-induction motors, illustrating efficiency drop at partial load.
- Figure 29: Shows power requirement curves for different static proportions in pump systems, demonstrating the impact of static head on energy consumption and VSD effectiveness.
- Figure 33: Presents the distribution of failed components in electric motors, indicating bearings as the dominant failure origin.
- Figure 35: Exemplifies the yearly energy consumption in a smart sensor installed in a motor, showing minimal energy consumption compared to potential savings.
Figure Name List:
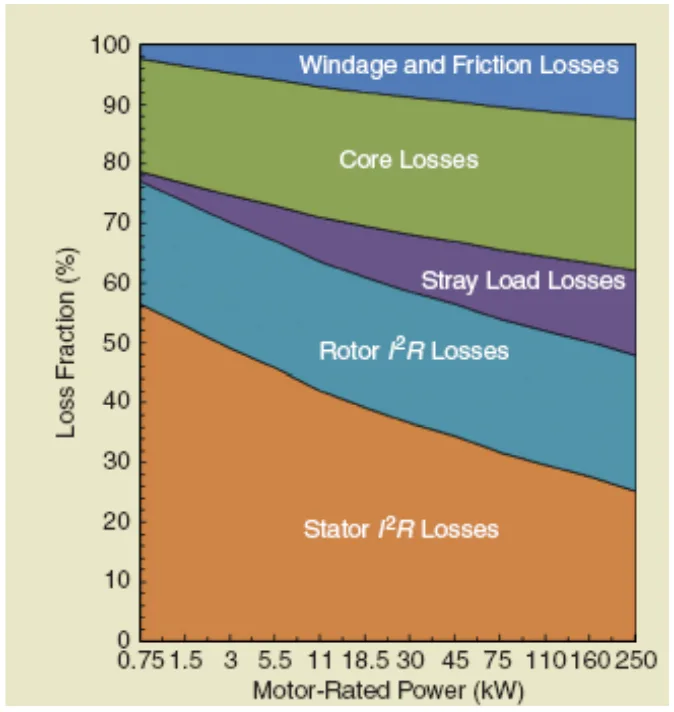

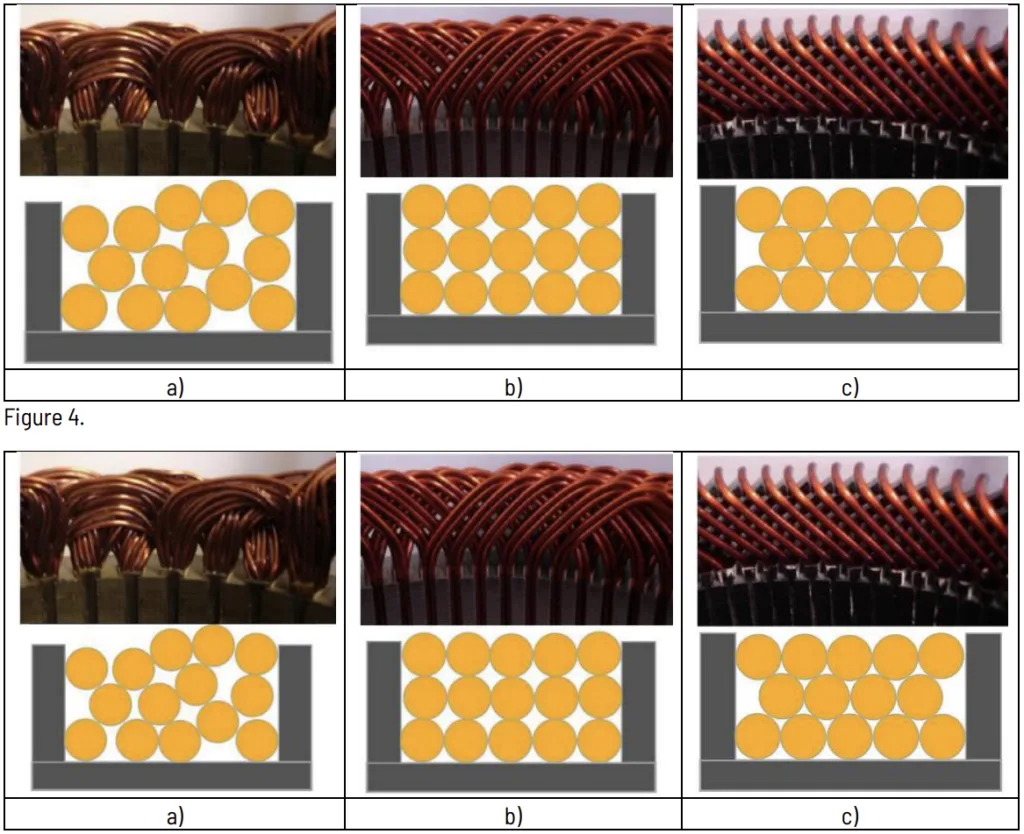
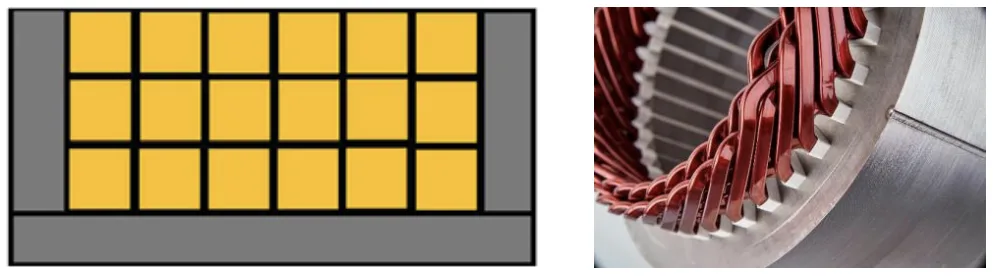
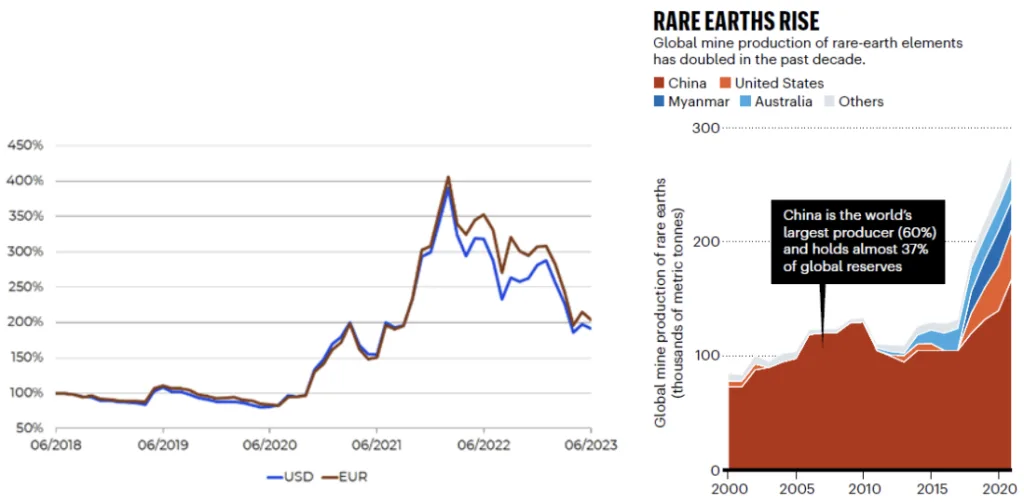
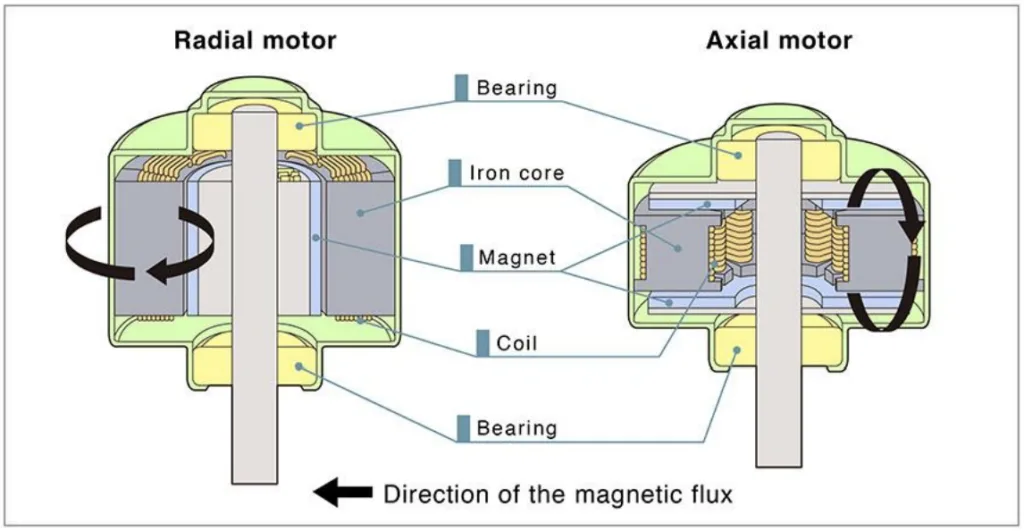
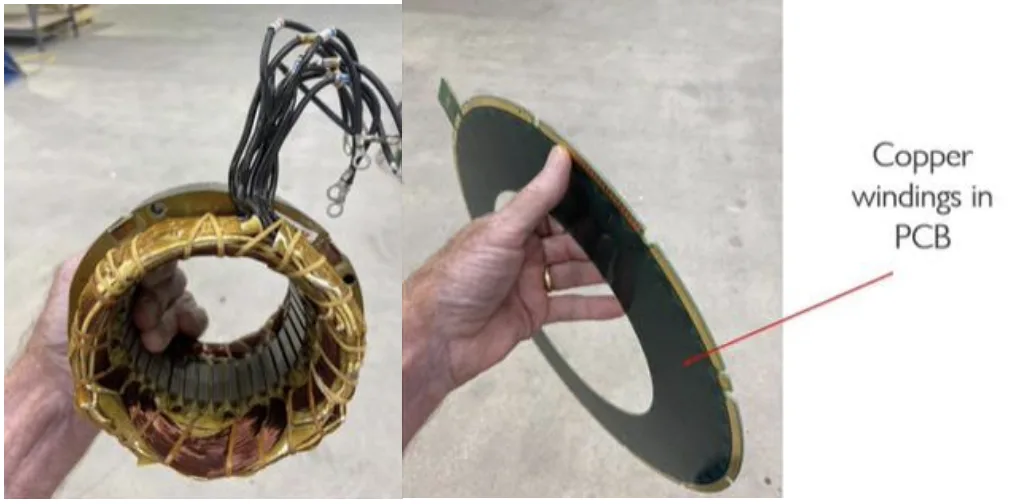
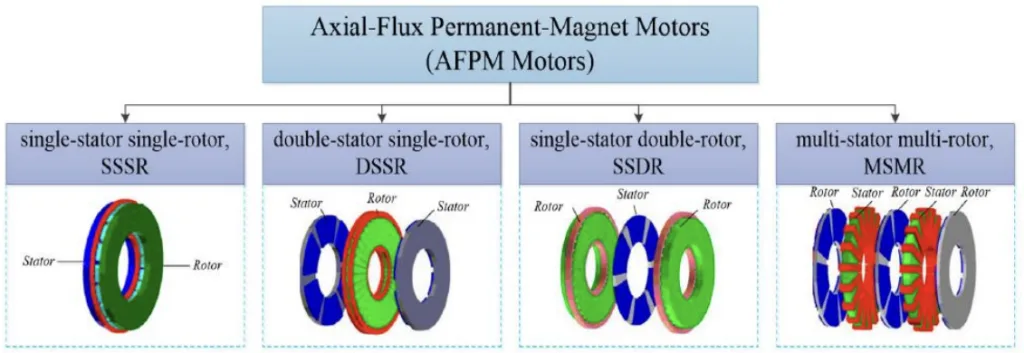
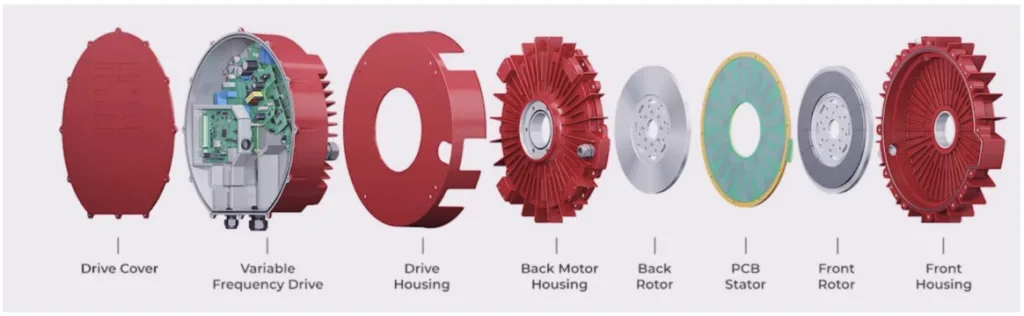
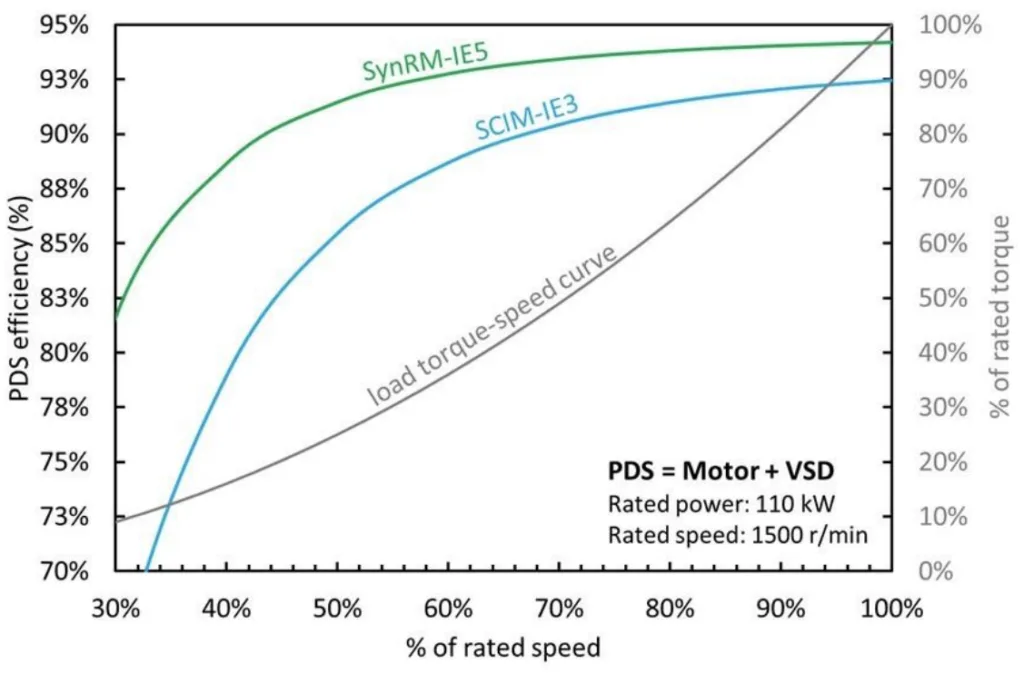
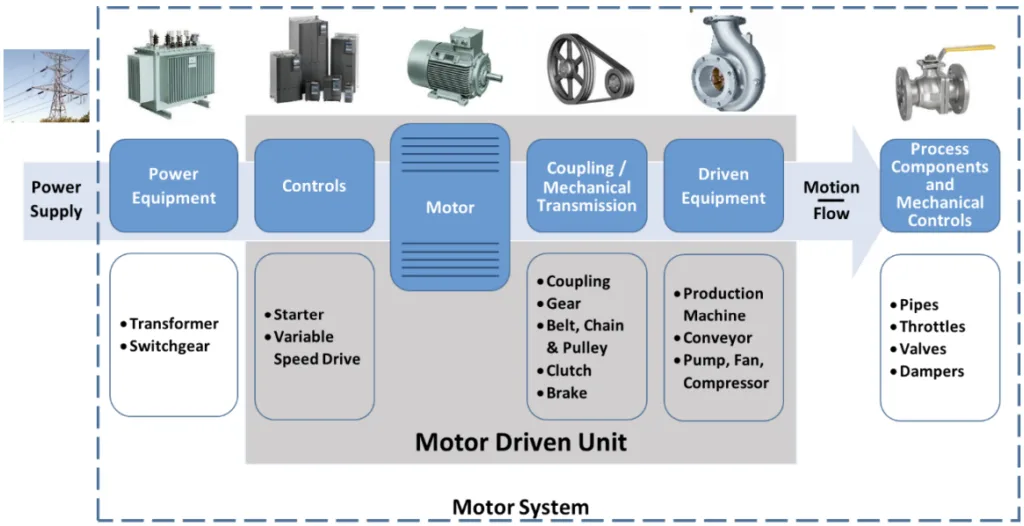
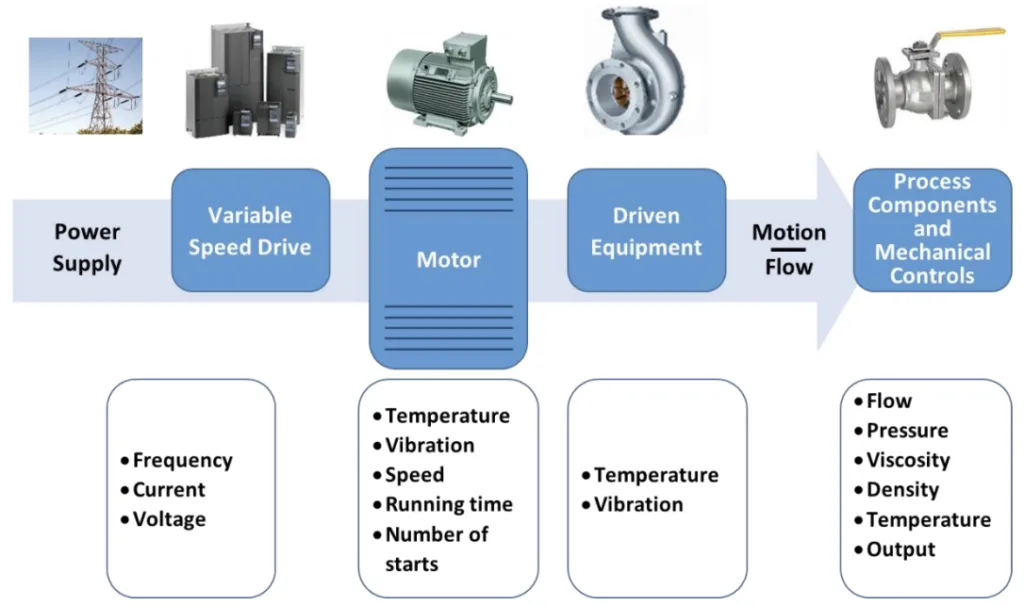
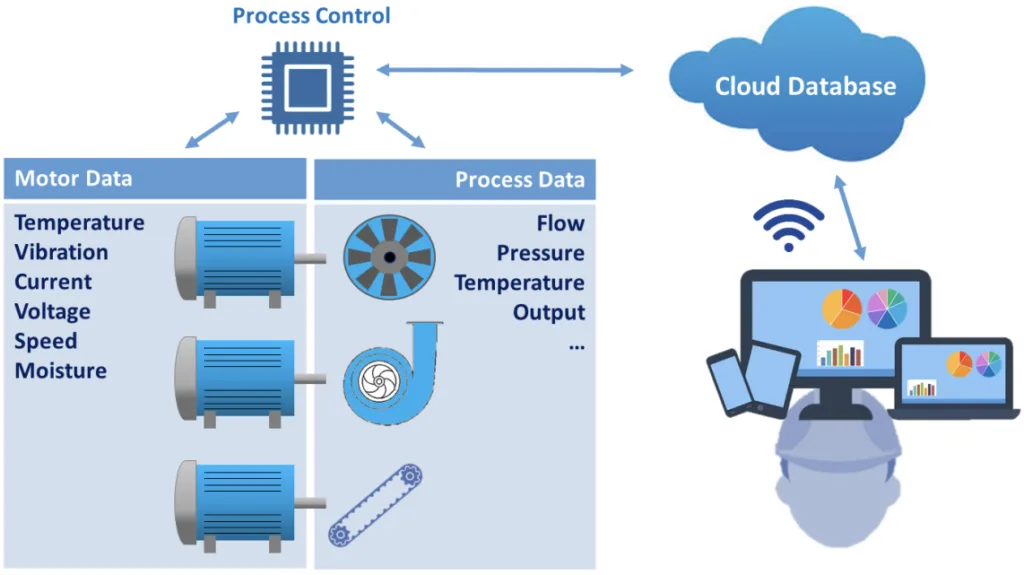
- FIGURE 1: OVERVIEW OF THE MOTOR EFFICIENCY CLASSES DEFINED BY IEC600-34-30-1 AND OF THE COMMERCIALLY AVAILABLE MOTOR EFFICIENCIES (SOURCE: ISR-UC BASED ON CATALOGUE DATA)
- FIGURE 2: TYPICAL BREAKDOWN BY TYPE OF LOSSES IN 50-HZ, FOUR-POLE IMS (ALMEIDA, FERREIRA, & BAOMING, 2014)
- FIGURE 3: HIGH EFFICIENCY INDUCTION MOTOR IMPROVEMENTS (SOURCE ISR-UC)
- FIGURE 4: EXAMPLES OF CONVENTIONAL AND ADVANCED WINDING TECHNIQUES (GIRAUD & PLASSE, 2017)
- FIGURE 5 RECTANGULAR SECTION WIRE
- FIGURE 6: TOTAL MOTOR WEIGHT (11 KW; 1500 RPM; CAST IRON FRAME; CATALOGUE DATA)
- FIGURE 7: EVOLUTION OF NEODYMIUM PRICES (2018-2023)(100% = 70US$/KG)(STRATEGIC METALS INVEST, 2023); GLOBAL MINE PRODUCTION OF RARE-EARTHS (GENG, SARKIS, & BLEISCHWITZ, 2023)
- FIGURE 8: RADIAL AND AXIAL FLUX MOTOR CONFIGURATION (NIDEQ CORPORATION)
- FIGURE 9: IRON CORE IN A STATOR OF A RADIAL FLUX MOTOR VS PCB STATOR OF AN AXIAL FLUX MOTOR (FALTER, 2023)
- FIGURE 10: TYPICAL TYPES OF TOPOLOGIES FOR AXIAL-FLUX MOTORS (HAO, MA, WANG, LUO, & CHEN, 2022)
- FIGURE 11: LAYERED COMPONENTS OF AN INFINITUM ELECTRIC AXIAL-FLUX MOTOR WITH TWO ROTORS AND PRINTED CIRCUIT STATOR (GUEDES-PINTO, 2022)
- FIGURE 12 COMMERCIAL MOTORS POWER DENSITY (FOR VEHICLE APPLICATIONS) (IDTECHEх, 2022)
- FIGURE 13: COMPACT INTEGRATED MOTOR+VSD+PUMP/FAN+IoT - SEVERAL MODELS
- FIGURE 14: DIRECT DRIVE IN AN ELEVATOR (SOURCE: KONE)
- FIGURE 15: EFFICIENCY OF COMMERCIALLY AVAILABLE LSPSM IE4 (SOURCE: WEG)
- FIGURE 16: SYNRM MOTOR PRINCIPLE (SOURCE: ABB)
- FIGURE 17: POTENTIAL EFFICIENCY INCREASE DUE TO ROTOR LOSS REDUCTION IN SYNR MOTORS (SOURCE: ABB)
- FIGURE 18: EFFICIENCY COMPARISON OF AN 110-KW PDS (POWER DRIVE SYSTEM) WITH IE3-CLASS SCIM AND WITH IE5-CLASS SYNRM CONSIDERING A QUADRATIC-TORQUE LOAD FAN OR PUMPING SYSTEM WITHOUT STATIC HEAD. (ALMEIDA, FERREIRA, & FONG, 2023)
- FIGURE 19: TYPICAL CONFIGURATION OF LSSYNRM ROTOR.
- FIGURE 20: CONFIGURATION OF AN INVERTER BASED VSD.
- FIGURE 21: EFFICIENCY LEVELS AND CDM CLASSIFICATION AS DEFINED IN IEC 61800-9-2.
- FIGURE 22: VSD EFFICIENCY AT THE (90:100) DUTY POINT (SOURCE: IEA-4EMSA).
- FIGURE 23: OVERVIEW OF WIDE BAND GAP (WBG) PERFORMANCE CHARACTERISTICS (SOURCE: IEA PECTA).
- FIGURE 24: EXAMPLE OF A MOTOR SYSTEM INCLUDING THE MOTOR DRIVEN UNIT.
- FIGURE 25: THE ENERGY EFFICIENCY OF AN ELECTRIC MOTOR SYSTEM AND ITS IMPROVEMENT POTENTIAL (DE ALMEIDA, FERREIRA, & BOTH).
- FIGURE 26: BANDS OF A) TYPICAL POWER FACTOR, AND B) ENERGY EFFICIENCY, VERSUS LOADING FOR FOUR-POLE, THREE-PHASE, CAGE-INDUCTION MOTORS OF DIFFERENT OUTPUT POWERS (IEC60034-31).
- FIGURE 27: TYPES OF TORQUE-SPEED CURVES:
- FIGURE 28: EXAMPLE OF PUMP AND SYSTEM CHARACTERISTIC CURVES FOR DIFFERENT SHARES OF STATIC HEAD (KULTERER, DIMOV, HOFMANN, TESCH, & ANGERMAYR, 2022).
- FIGURE 29: EXAMPLE OF POWER REQUIREMENT CURVES FOR DIFFERENT STATIC PROPORTIONS (KULTERER, DIMOV, HOFMANN, TESCH, & ANGERMAYR, 2022).
- FIGURE 30: POTENTIAL AREAS OF MEASUREMENTS AND OF APPLICATION OF SENSORS IN MOTOR DRIVEN SYSTEMS (ADAPTED FROM (KULTERER, DAWODY, WIDERSTROM, & WERKHOVEN, 2022)).
- FIGURE 31: DIGITISATION IN MOTOR SYSTEMS (SOURCE: ISR-UC).
- FIGURE 32: EXAMPLES OF SMART SENSORS FOR ELECTRIC MOTORS (SOURCE: ABB & WEG).
- FIGURE 33: DISTRIBUTION OF FAILED COMPONENTS IN ELECTRIC MOTORS (BONNETT, 2012).
- FIGURE 34: CONDITION BASED MONITORING IN ELECTRIC MOTORS (SOURCE: STMICROELECTRONICS).
- FIGURE 35: EXAMPLE OF THE YEARLY ENERGY CONSUMPTION IN A SMART SENSOR INSTALLED IN A MOTOR.
7. Conclusion:
Summary of Key Findings:
The study concludes that motor efficiency is continuously improving, driven by technological advancements and regulatory pressures. Synchronous motor technologies and advanced induction motor designs are key to achieving IE4 and IE5 efficiency levels. Variable Speed Drives and emerging Wide Band Gap semiconductors play a critical role in optimizing motor system efficiency, particularly in variable load applications. Digital technologies offer significant potential for further efficiency gains through enhanced monitoring, maintenance, and process optimization. However, realizing these gains requires a system-level approach, considering all components of the motor-driven unit and addressing barriers to the implementation of digital technologies.
Academic Significance of the Study:
This report provides a valuable handbook-level overview of the latest trends in motor efficiency, consolidating information from diverse sources into a structured and accessible format. It contributes to the academic understanding of motor technology evolution, highlighting the interplay between motor design, control strategies, and digital integration in achieving high efficiency. The comprehensive analysis of different motor types and their performance characteristics adds to the body of knowledge in electrical engineering and energy efficiency.
Practical Implications:
The findings have significant practical implications for industries seeking to improve energy efficiency and reduce operational costs. The report guides engineers and decision-makers in selecting appropriate motor technologies and VSDs for specific applications. It emphasizes the importance of a system-level approach to motor system design and optimization. Furthermore, it highlights the benefits of adopting digital technologies for condition monitoring, predictive maintenance, and process optimization, providing a roadmap for implementing smart motor systems in industrial settings.
Limitations of the Study and Areas for Future Research:
This report is primarily a review and synthesis of existing information, and does not involve original empirical research. The analysis is limited by the availability and scope of the referenced materials. Future research could focus on quantifying the energy savings potential of specific motor technologies and digital solutions in real-world industrial applications. Further investigation is needed to address the barriers to implementing digital technologies in motor systems and to develop strategies for overcoming these challenges. Detailed life cycle assessments of different motor technologies and VSDs, considering material usage and environmental impact, would also be a valuable area for future research.
8. References:
- Almeida, A. d., Ferreira, F. J., & Baoming, G. (2014). Beyond Induction Motors – Technology Trends to Move Up Efficiency. IEEE Transactions on Industry Applications, 20(3), 2103 - 2114.
- Almeida, A. d., Ferreira, J. T., & Fong, J. (2011). Standards for efficiency of electric motors - Permanent magnet synchronous motor technology. IEEE Industry Applications Magazine, 17, n.1, 12-19.
- Almeida, A. T., Ferreira, F. J., & Fong, J. (2023). Perspectives on Electric Motor Market Transformation for a Net Zero Carbon Economy. Energies, 16, 1298.
- Arzillo, A., Braglia, P., Nuzzo, S., Barater, D., Franceschini, G., Gerada, D., & Gerada, C. (2020). Challenges and Future opportunities of Hairpin Technologies. 2020 IEEE 29th International Symposium on Industrial Electronics (ISIE)(pp. 277-282). Delft, Netherlands: IEEE. doi:10.1109/ISIE45063.2020.9152417
- Bonnett, A. H. (2012, Nov-Dec). Root Cause Methodology for Induction Motors: A Step-by-Step Guide to Examining Failure. IEEE Industry Applications Magazine, 18(6).
- de Almeida, A., Ferreira, J. T., & Both, D. (January/February 2005). Technical and Economical Considerations in the Application of Variable-Speed Drives With Electric Motor Systems. IEEE Transactions On Industry Applications, 41(1).
- Falter, M. (2023, January 5). Smaller, Lighter Axial Flux Electric Motor Extends EV Range. Retrieved July 2023, from Infinitum: https://goinfinitum.com/smaller-lighter-axial-flux-electric-motor-extends-ev-range/
- Geng, Y., Sarkis, J., & Bleischwitz, R. (2023). How to build a circular for rare-earth elements. Nature, 619, 248-251.
- Giraud, R., & Plasse, C. (2017). Technology to support Circular Economy: will standardization limits the outstanding benefits of new motor technology with or without drive and the use of raw material content of electric motors. Nideq - Leroy somer.
- Glaessel, T., Seefried, J., & Franke, J. (2017). Challenges in the manufacturing of hairpin windings and application opportunities of infrared lasers for the contacting process. 2017 7th International Electric Drives Production Conference (EDPC)(pp. 1-7). Würzburg, Germany: IEEE. doi:10.1109/EDPC.2017.8328150
- Guedes-Pinto, P. (2022, March). This Axial-Flux Motor with a PCB stator is ripe for an electrified world. IEEE Spectrum.
- Guizani, M. (2019). The Industrial Internet of Things. IEEE Network,, 33(5), 4–4. doi: https://doi.org/10.1109/MNET.2019.8863716
- Håkansson, L., & Höckerman, J. (2020). Impact of digitalization on electrical motor systems, . School of Business, Society and Engineering, Mälardalens University.
- Hannan, M. A., Ali, J. A., Mohamed, A., & Hussain, A. (January 2018). Optimization techniques to enhance the performance of induction motor drives: A review. Renewable and Sustainable Energy Reviews, 81, Part 2, 1611-1626.
- Hao, Z., Ma, Y., Wang, P., Luo, G., & Chen, Y. (2022). A Review of Axial-Flux Permanent-Magnet Motors: Topological Structures, Design, Optimization and Control Techniques. Machines 2022, 10. doi:https://doi.org/10.3390/machines10121178
- IDTechEx. (2022). Electric Motors for Electric Vehicles 2022-2032. Retrieved 7 2023, from IDTechEx: https://www.idtechex.com/en/research-report/electric-motors-for-electric-vehicles-2022-2032/842
- ITU. (2013). Overview of the Internet of things - Recommendation ITU-T Y.2060. Genéve: International Telecommunication Union.
- Knight, A. M., & McClay, C. I. (2000, Nov-Dec). The design of high-efficiency line-start motors. IEEE Transactions on Industry Applications, 36(6), 1555-1562.
- Kulterer, K. (2021). Report on the EMSA Survey on digitalization in electric motor driven systems. Zurich: IEA-EMSA.
- Kulterer, K., Dawody, J., Widerstrom, G., & Werkhoven, M. v. (2022). Classification of digitalisation technologies for electric motor driven systems. IEA EMSA.
- Kulterer, K., Dimov, D., Hofmann, M., Tesch, J., & Angermayr, R. (2022). Leitfaden für Energieaudits für Pumpensysteme; published: . Wien: Klimaaktiv. Retrieved from https://www.klimaaktiv.at/dam/jcr:eb39bcc2-96b0-4fc1-b8f1-0c478748b15f/klimaaktiv%20Pumpenleitfaden%202023.pdf
- Naxatra Labs. (2022, May 7). Applications of Axial Flux Technology. Retrieved July 2023, from Naxatra Labs: https://www.naxatralabs.com/post/technology-applications
- Nideq Corporation. (n.d.). Fundamental Technology for Innovative Motors. Retrieved September 2023, from Nideq Corporation: https://www.nidec.com/en/technology/capability/innovative_motor/
- Sisinni, E., Saifullah, A., Han, S., Jennehag, U., & Gidlund, M. (2018). Industrial Internet of Things: Challenges, Opportunities, and Directions. IEEE Transactions on Industrial Informatics, 4724-4734. doi:https://doi.org/10.1109/TII.2018.2852491
- Strategic Metals Invest. (2023, July 27). Neodymium Prices. Retrieved from https://strategicmetalsinvest.com/neodymium-prices/
- VHK, & Maagøe, V. (2020). ICT Impact study. European Commission.
- Vogel, K., & Rossa, A. J. (20 – 22 May 2014). Improving Efficiency in AC drives: Comparison of Topologies and Device Technologies. PCIM Europe 2014. Nuremberg.
- Wang, Z., Enomoto, Y., Tokoi, H., Komura, A., Obata, T., & Soma, K. (September 2015). Development of IE5 High Efficiency Motor with Iron-base Amorphous Magnetic Cores. EEMODS'15. Helsinky.
9. Copyright:
- This material is "João Fong, Anibal T. de Almeida, Konstantin Kulterer"'s paper: Based on "D 4.1. MOTOR SYSTEM EFFICIENCY TRENDS".
- Paper Source: [DOI URL]
This material was created to introduce the above paper, and unauthorized use for commercial purposes is prohibited.
Copyright © 2025 CASTMAN. All rights reserved.