This introductory paper is the research content of the paper ["Manufacturing of Thin-walled Impeller Based on Optimization of Sand Mold 3D Printing Forming Process"] published by ["Special Casting & Nonferrous Alloys"].
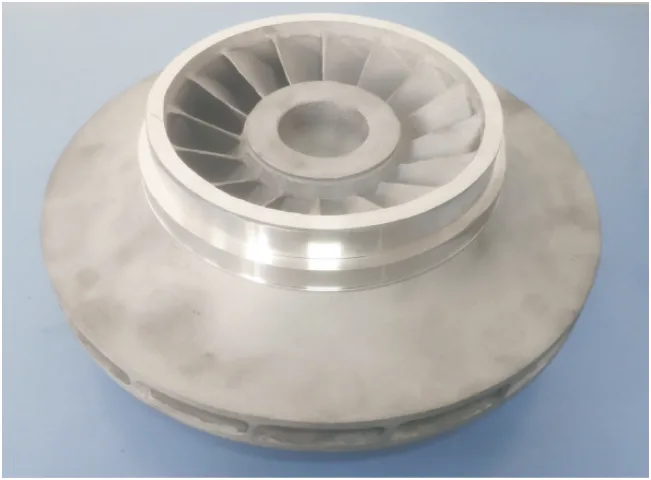
1. Overview:
- Title: Manufacturing of Thin-walled Impeller Based on Optimization of Sand Mold 3D Printing Forming Process
- Author: AI Yumeng, YOU Zhiyong, LIU Shilong, ZHANG Shenghui, ZHANG Yaofeng, LI Chengkun, TAN Rui
- Publication Year: 2025
- Publishing Journal/Academic Society: Special Casting & Nonferrous Alloys
- Keywords: 3D Printing Sand Mold, Forming Process, Response Surface Method, Low Pressure Die Casting
2. Abstracts / Introduction
In this study, the Box-Behnken response surface method was employed to optimize the sand mold 3D printing forming process. The research focused on determining the horizontal range of resin inkjet content, activator content, and printing layer thickness, using tensile strength and gas evolution as performance responses. Numerical simulation was utilized to identify the optimal process parameter combination, which was subsequently validated through the trial production of thin-walled impellers using the low pressure die casting process. The results indicated that with a resin inkjet content of 1.44%, an activator content of 0.21%, and a printing layer thickness of 0.30 mm, the printed sand mold achieved a tensile strength of 2.15 MPa and a gas evolution of 8.92 mL/g, closely aligning with predicted values. Under these optimized conditions, the impeller casting exhibited a complete and clear profile, meeting the required technical specifications. This research aims to provide a valuable reference for the production of similar products by optimizing 3D printing sand mold forming process to achieve high strength, low gas evolution, and reduced material consumption.
3. Research Background:
Background of the Research Topic:
The application of sand mold 3D printing technology in the casting field is expanding, allowing for more complex, thin-walled, lightweight, and precise casting designs, particularly in aerospace, automotive, and shipbuilding industries. This necessitates 3D printed casting sand molds with superior technological performance to ensure high-quality component formation. Traditional methods involve mixing additives with raw sand and compacting the mold manually or mechanically within a mold box. In contrast, sand mold 3D printing relies on powder-based discrete accumulation and micro-droplet jetting principles.
Status of Existing Research:
Existing optimization methods often use single-variable approaches, failing to capture the interaction effects between parameters. This limitation has driven the adoption of multivariate statistical techniques, particularly Response Surface Methodology (RSM). Prior research has demonstrated the effectiveness of RSM in optimizing casting processes. For instance, Li Ning et al. [8] used RSM to optimize low-pressure casting parameters for aluminum alloy wheels, considering mold life and casting efficiency. Wang Yanfeng et al. [9] optimized metal mold casting of A357 aluminum alloy using Box-Behnken RSM and numerical simulation. Zhan Quan Quan et al. [10] employed RSM to determine optimal parameters for 3D printing furan resin sand, maximizing tensile strength.
Necessity of the Research:
While increasing binder and curing agent content enhances the strength of 3D printed sand molds, it also elevates gas evolution and potentially reduces forming accuracy [5]. Furthermore, increased material consumption raises printing costs. Conversely, adjusting layer thickness in the sand laying process affects both printing efficiency and mold strength [6]. Thinner layers increase printing time, while thicker layers can weaken inter-particle bonding. Therefore, optimizing the 3D printing process is crucial to balance performance, material usage, and cost-effectiveness.
4. Research Purpose and Research Questions:
Research Purpose:
This research aims to optimize the forming process of 3D printed sand molds using Response Surface Methodology (RSM). The goal is to identify the optimal combination of resin inkjet content, curing agent content, and printing layer thickness to achieve high tensile strength, low gas evolution, and reduced material consumption in 3D printed sand molds for thin-walled impeller castings. The study also seeks to validate the optimized process through low-pressure casting of impeller prototypes, providing a reference for similar applications.
Key Research:
- To investigate the effects of resin inkjet content, curing agent content, and printing layer thickness on the tensile strength and gas evolution of 3D printed sand molds.
- To establish a predictive model for tensile strength and gas evolution using Box-Behnken Design (BBD) and Response Surface Methodology (RSM).
- To determine the optimal process parameters for 3D printing sand molds that balance tensile strength and gas evolution for thin-walled impeller casting.
- To validate the optimized process parameters by manufacturing and testing a thin-walled impeller using low-pressure die casting.
5. Research Methodology
Research Design:
The study employed a Box-Behnken Design (BBD) approach within Response Surface Methodology (RSM) to optimize the 3D printing process. A three-factor, three-level experimental design was utilized, with resin inkjet content (A), curing agent content (B), and printing layer thickness (C) as independent variables. Tensile strength and gas evolution were selected as the response variables.
Data Collection Method:
"8"字 shaped test blocks were printed using an ExOne S-Max Pro 3D printer, with varying parameters according to the BBD matrix (Table 5 in the paper). The raw material was silica sand, the binder was 3D printing furan resin, and the curing agent was a 3D printing curing agent (specifications in Table 1-3).
Analysis Method:
Analysis of Variance (ANOVA) was used to evaluate the significance of the model and process parameters. Response surface plots and contour plots were generated to visualize the relationships between variables and responses. Numerical optimization was performed to predict the optimal process parameter combination. Tensile strength was tested using a SWY-B digital display hydraulic strength testing machine, and gas evolution was measured using a GET-II intelligent gas evolution tester.
Research Subjects and Scope:
The research focused on optimizing the 3D printing process for sand molds used in casting thin-walled impellers made of ZL101A alloy. The study was conducted using specific materials (silica sand, furan resin, and curing agent) and equipment (ExOne S-Max Pro printer, SWY-B tensile tester, GET-II gas evolution tester). The findings are specific to the tested parameter ranges and material system.
6. Main Research Results:
Key Research Results:
- Optimal Parameters: The optimized process parameters were determined to be: resin inkjet content of 1.44%, curing agent content of 0.21%, and printing layer thickness of 0.30 mm.
- Tensile Strength and Gas Evolution: Under these optimized conditions, the printed sand mold achieved a tensile strength of 2.15 MPa and a gas evolution of 8.92 mL/g, closely matching the predicted values.
- Impeller Casting Quality: The thin-walled impeller casting produced using the optimized 3D printed sand mold exhibited a complete and clear profile, meeting technical requirements. X-ray inspection revealed no casting defects in critical areas, and dimensional accuracy was within ±0.9 mm, satisfying DCTG6 tolerance standards (Figure 8).
Analysis of presented data:
- Tensile Strength Optimization: RSM analysis indicated that resin inkjet content and printing layer thickness significantly influence tensile strength (Table 6, Figure 2, Figure 3). Higher resin content generally increases tensile strength, while increased layer thickness tends to decrease it. Curing agent content showed a less significant effect within the tested range.
- Gas Evolution Optimization: RSM analysis showed that resin inkjet content is the most significant factor affecting gas evolution (Table 7, Figure 4, Figure 5). Gas evolution increases with higher resin content. Printing layer thickness and curing agent content had less pronounced effects on gas evolution.
- Model Validation: The predicted values from the RSM models for both tensile strength and gas evolution were in close agreement with the experimentally measured values under optimized conditions, validating the models' accuracy (Table 8).
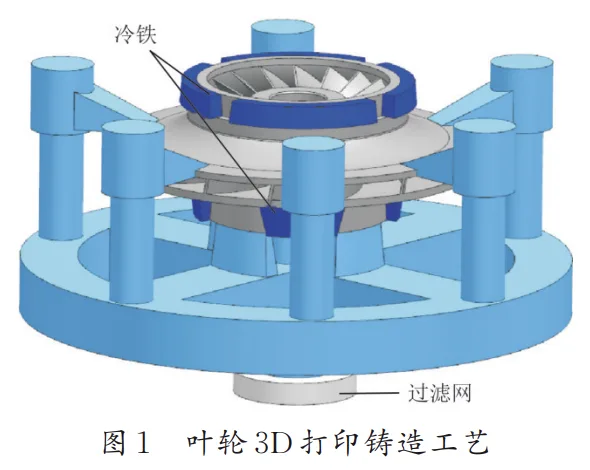
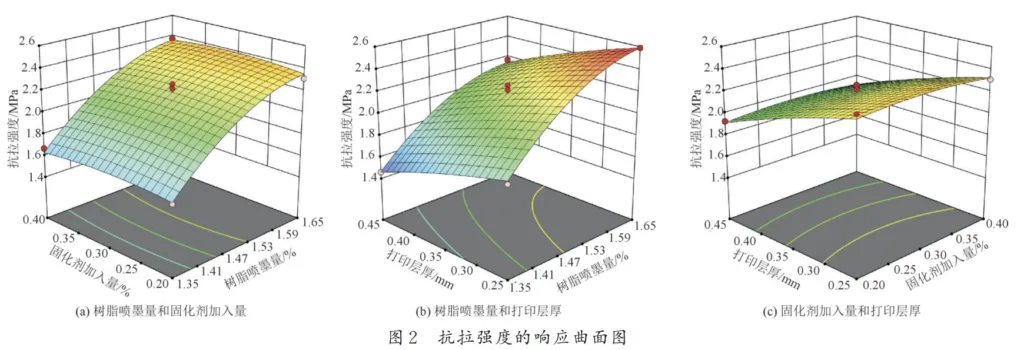
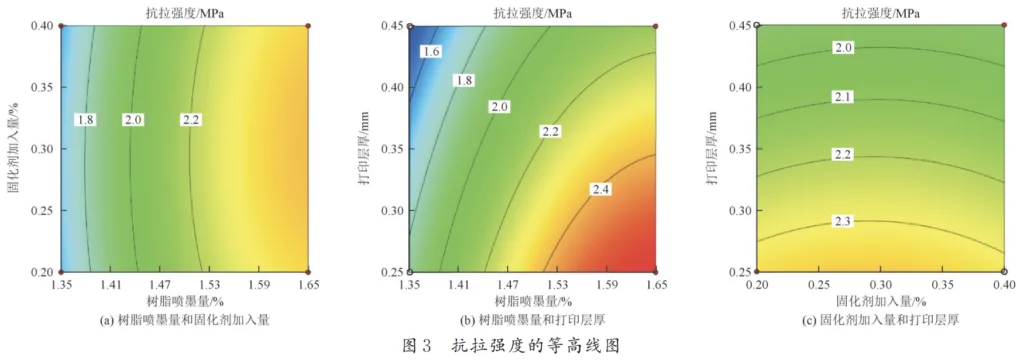
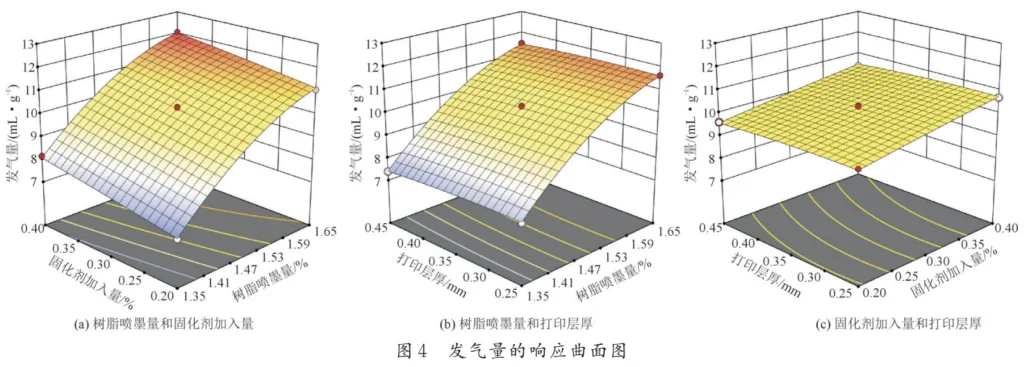
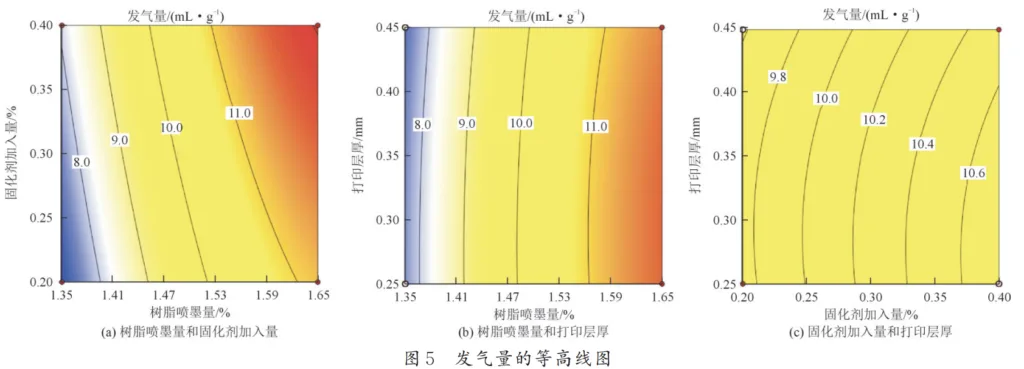
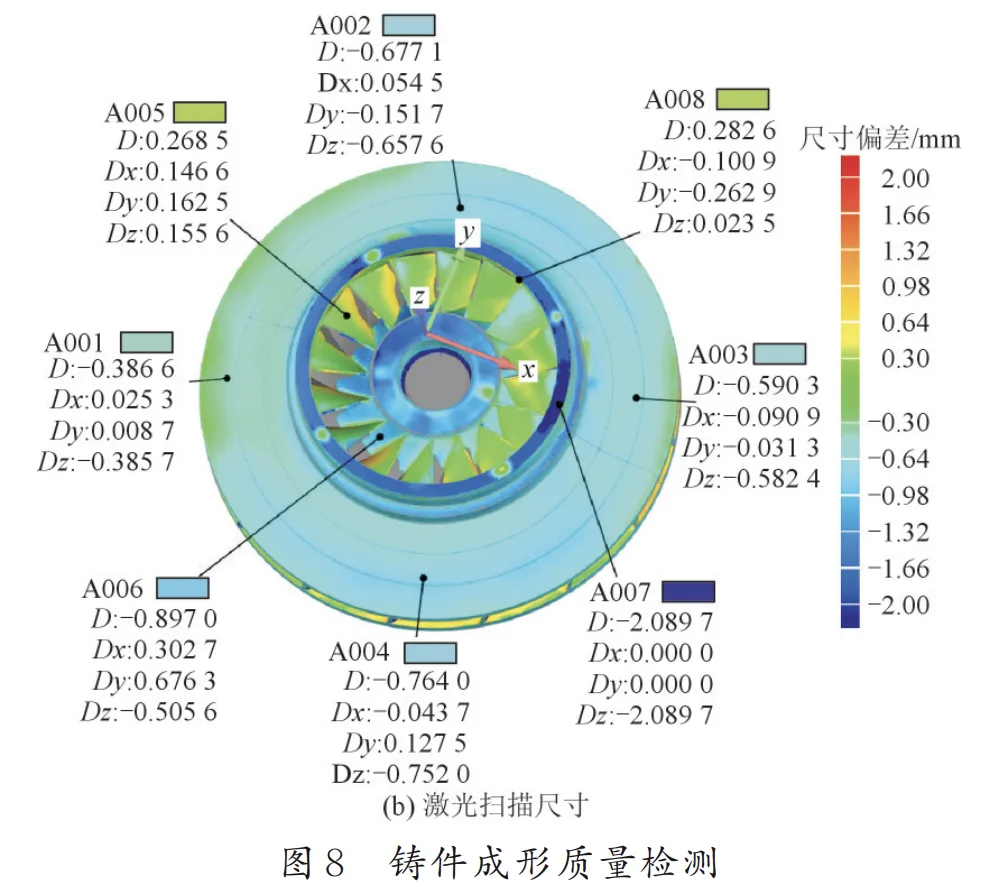
Figure Name List:
- Fig.1 3D printing casting technique for impeller
- Fig.2 Response surface plot of tensile strength
- Fig.3 Contour plot of tensile strength
- Fig.4 Response surface plot of gas evolution
- Fig.5 Contour plot of gas evolution
- Fig.6 Design of 3D printed sand core structure for impeller casting
- Fig.7 Product of impeller casting
- Fig.8 Quality inspection of casting forming
7. Conclusion:
Summary of Key Findings:
This study successfully optimized the 3D printing process for sand molds used in thin-walled impeller casting using Box-Behnken Response Surface Methodology. The optimal parameters identified were a resin inkjet content of 1.44%, a curing agent content of 0.21%, and a printing layer thickness of 0.30 mm. These parameters yielded a sand mold with a tensile strength of 2.14 MPa and a gas evolution of 8.92 mL/g. Validation through low-pressure casting of a thin-walled impeller demonstrated the effectiveness of the optimized process in producing high-quality castings with good dimensional accuracy and minimal defects.
Academic Significance of the Study:
This research contributes to the understanding of process parameter optimization in sand mold 3D printing. It demonstrates the effective application of RSM in optimizing multiple conflicting performance metrics (tensile strength and gas evolution) in additive manufacturing for casting. The study provides valuable insights into the individual and interactive effects of key process parameters, enhancing the scientific knowledge base in this field.
Practical Implications:
The optimized 3D printing process offers practical benefits for manufacturing thin-walled impeller castings and similar components. By reducing material consumption (resin and curing agent) and improving printing efficiency (increased layer thickness), the process becomes more cost-effective and environmentally friendly. The achieved mold strength and low gas evolution ensure high casting quality, reducing defects and improving overall production yield.
Limitations of the Study and Areas for Future Research:
The study is limited to a specific material system (silica sand, furan resin, and curing agent) and a particular 3D printer model. Further research could explore the applicability of these findings to other materials and printing systems. Additionally, future studies could investigate other performance metrics, such as surface finish and permeability, and explore the optimization of post-processing steps for 3D printed sand molds. The long-term performance and durability of castings produced with optimized 3D printed molds could also be areas for future investigation.
8. References:
- [1] MOHIUDDEN M V, HUSSAINY SF, KRISHNAIAH A, et al. Experimental investigation to produce thin-walled sand casting using combination of casting simulation and additive manufacturing techniques [J]. The International Journal of Advanced Manufacturing Technology, 2017, 90(9-12): 3 147-3 157.
- [2] HAWALDAR N, ZHANG J. A comparative study of fabrication of sand casting mold using additive manufacturing and conventional process [J]. The International Journal of Advanced Manufacturing Technology, 2018, 97(1-4): 1037-1 045.
- [3] 李彬, 廖慧敏, 曾明, 等. 3D打印在砂型铸造中的应用及发展现状[J]. 特种铸造及有色合金, 2020, 40(9): 953-957.
- [4] MITRA S, EL MANSORI M, RODRINUEZ DE CASTRO A, et al. Study of the evolution of transport properties induced by additive processing sand mold using X-ray computed tomography [J]. Journal of Materials Processing Technology, 2020, 277: 116 495.
- [5] 余洛生, 刘丰, 刘丽敏, 等. 3D打印呋喃树脂砂型成形精度研究与控制[J]. 铸造, 2022, 71(11): 1407-1412.
- [6] 高桂丽, 张伟坤, 杜志敏, 等. 基于喷墨3D打印的铸造砂型(芯)成形工艺参数应用研究[J]. 铸造, 2020, 69(6): 627-631.
- [7] BEZERA MA, SANTELLI RE, OLOVEIRA E P, et al. Response surface methodology (RSM) as a tool for optimization in analytical chemistry[J]. Talanta, 2008, 76(5): 965-977.
- [8] 李宁, 朱培浩, 胡亚辉, 等. 铝合金轮毂低压铸造的模具设计及工艺优化[J]. 特种铸造及有色合金, 2017, 37(5): 494-497.
- [9] 王彦凤, 杨正, 邱常明, 等. 基于响应面法的A357铝合金金属型铸造工艺优化[J]. 特种铸造及有色合金, 2019, 39(10): 1 137-1 142.
- [10] 詹泉泉, 朱德智, 陈维平, 等. 响应面法优化3D打印呋喃树脂砂工艺条件[J]. 特种铸造及有色合金, 2019, 39(9): 981-983.
- [11] 吴士平, 王晔, 吴光然, 等. ZL205A合金壳体铸件低压铸造工艺研究[J]. 特种铸造及有色合金, 2012, 32(9): 811-813.
- [12] 韩雯雯, 杨洪英, 张勤, 等. 响应曲面法优化黄金氰渣亚硫酸钠-空气氧化法脱氰工艺[J]. 中国有色金属学报, 2023, 33(4): 1278-1 286.
- [13] MITRA S, ANTONIO RDC, MOHAMED E M. On the rapid manufacturing process of functional 3D printed sand molds [J]. Journal of Manufacturing Processes, 2019, 42: 202-212.
- [14] BRYANT N, FRUSH T, THIEL J, et al. Influence of machine parameters on the physical characteristics of 3D-printed sand molds for metal casting [J]. International Journal of Metalcasting, 2021, 15 (2): 361-372.
- [15] WANG Y, YU R L, YIN S K, et al. Effect of gel time of 3D sand printing binder system on quality of sand mold/core [J]. China Foundry, 2021, 18(6): 581-586.
- [16] 彭倩, 陈晓龙, 田超, 等. 不同固化剂加入量对自硬呋喃树脂砂性能的影响[J]. 铸造, 2020, 69(7): 748-751.
- [17] VAEZIM, CHUA C K. Effects of layer thickness and binder saturation level parameters on 3D printing process [J]. The International Journal of Advanced Manufacturing Technology, 2011, 53 (1-4): 275-284.
9. Copyright:
- This material is "AI Yumeng, YOU Zhiyong, LIU Shilong, ZHANG Shenghui, ZHANG Yaofeng, LI Chengkun, TAN Rui"'s paper: Based on "Manufacturing of Thin-walled Impeller Based on Optimization of Sand Mold 3D Printing Forming Process".
- Paper Source: DOI: 10.15980/j.tzzz.T20240194
This material was created to introduce the above paper, and unauthorized use for commercial purposes is prohibited.
Copyright © 2025 CASTMAN. All rights reserved.