This article introduces the paper ["Investigation of wear properties of magnesium and aluminum alloys for automotive applications"] published by [Elsevier] in the journal of "Journal of Materials Processing Technology".
1. Overview:
- Title: Investigation of wear properties of magnesium and aluminum alloys for automotive applications
- Author: D.S. Mehta, S.H. Masood, W.Q. Song
- Publication Year: 2004
- Publishing Journal/Academic Society: Journal of Materials Processing Technology
- Keywords: Magnesium alloys; Loading conditions; Wear properties; Wear tracks
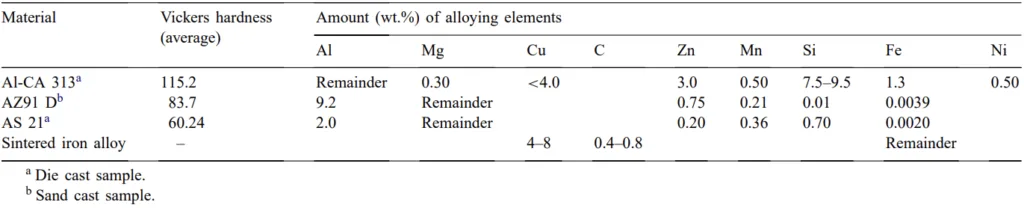
2. Abstracts or Introduction
This research paper investigates the wear properties of die cast and sand cast magnesium alloys (AS21 and AZ91D) and aluminum alloy (Al-CA 313) under dry and wet sliding conditions at different loading conditions using pin-on-disk equipment. The pin was made from sintered iron alloy. The study aims to understand the wear characteristics of magnesium alloys in relation to aluminum alloys for automotive applications, considering magnesium alloys as a potential alternative material due to their lightweight properties. The research analyzes wear rates, wear track characteristics, and microstructure of the tested alloys.
3. Research Background:
Background of the Research Topic:
Magnesium alloys are increasingly utilized in the automotive industry due to their high specific strength, which reduces vehicle mass, enhances power-to-weight ratio, and decreases fuel consumption. The low density of magnesium offers significant weight reduction in structural body parts, contributing to reduced CO2 emissions. Magnesium alloys also exhibit advantages such as damping capacity, dimensional stability, impact and dent resistance, anti-galling properties, and good electrical and thermal conductivity.
Status of Existing Research:
While extensive research exists on the wear properties of aluminum alloys, detailed studies on the wear behavior of magnesium alloys are limited. Existing studies on aluminum alloys have explored the effects of silicon content [1, 2, 3], corundum particle content [4], and SiC reinforcement [5] on wear characteristics. Recent research by Song et al. [6] investigated the wear mechanism and wear rate of magnesium alloys AS21 and AZ91D and aluminum alloy Al-CA 313 under constant dry sliding conditions, concluding that alloy hardness is a primary factor in wear rate. However, research on the wear behavior of magnesium alloys under lubricated conditions was not found.
Necessity of the Research:
Understanding the wear properties of magnesium alloys is crucial for their application in critical automotive components. This study addresses the gap in knowledge regarding the wear behavior of die cast and sand cast magnesium alloys under both dry and wet sliding conditions, providing valuable insights for automotive applications.
4. Research Purpose and Research Questions:
Research Purpose:
The primary purpose of this research is to experimentally investigate and determine the wear properties of die cast and sand cast magnesium and aluminum alloys under dry and wet sliding conditions with varying loads. The study aims to identify the wear rate of these alloys under different conditions and determine which alloy exhibits the most wear under the applied test parameters.
Key Research:
- Comparative analysis of wear rates for magnesium alloys (AS21, AZ91D) and aluminum alloy (Al-CA 313) under dry and wet sliding conditions.
- Evaluation of the effect of different loading conditions on the wear rate of the alloys.
- Characterization of wear tracks and wear mechanisms through microstructure studies and wear debris analysis.
5. Research Methodology
Research Design:
The research employed an experimental design using a Pin-On-Disk apparatus to assess the wear properties of the materials. Materials were tested in pin-disk pairs under nominally non-abrasive conditions. Square disk test samples were manufactured from sand cast AZ91 D, die cast AS 21 magnesium alloys and Al-CA 313 aluminum alloy. The pin was manufactured from sintered iron alloy.
Data Collection Method:
Wear tests were conducted under two sliding conditions: dry and wet. Wet sliding involved applying a lubricant (Castrol Multitrax gearbox oil) to the disk surface. Tests were performed under two different applied loads (0.714 N and 2.55 N), while maintaining constant sliding speed (0.259 m/s), sliding distance (1.33 km), and temperature (room temperature of 22.2°C). Vickers hardness was measured for each alloy. Weight measurements of disk samples were taken before and after wear tests using an electronic balance, preceded and followed by ultrasonic cleaning. Wear track profiles were measured using a laser scanning confocal microscope (LSCM). Worn surfaces and wear debris were examined using scanning electron microscopy (SEM) and energy dispersive spectrometer (EDS).
Analysis Method:
Wear rate (WR) was calculated using two methods:
- Volume loss method (Eq. (1)): WR = $\frac{V_{loss}}{d}$ where $V_{loss}$ is the volume of material lost, and $d$ is the total sliding distance. Volume loss was derived from mass loss and material density.
- Wear track profile method (Eq. (2)): WR = $(\frac{\pi D}{4d}) \sum_{i=1}^{4} A_i$ where $A_i$ is the area above the wear track profile at four sections measured by LSCM, and D is the mean diameter of the wear track.
Microstructural analysis of worn surfaces and wear debris was performed using SEM micrographs and EDS analysis to characterize wear mechanisms and material removal.
Research Subjects and Scope:
The research focused on the wear properties of the following materials:
- Disk Materials:
- Magnesium Alloys: AS21 (die cast), AZ91D (sand cast)
- Aluminum Alloy: Al-CA 313 (die cast)
- Pin Material: Sintered iron alloy (pump gear material)
The scope of the study included dry and wet sliding conditions, and two levels of applied load (0.714 N and 2.55 N).
6. Main Research Results:
Key Research Results:
- Load Dependence: Wear rate increases linearly with applied load for all tested alloys under both dry and wet sliding conditions (Figs. 2-4).
- Sliding Condition Dependence: Wear rates are significantly lower under wet sliding conditions compared to dry sliding conditions for all alloys (Figs. 2-4). Aluminum alloy showed a substantial reduction in wear rate under wet sliding.
- Alloy Comparison: Aluminum alloy Al-CA 313 exhibited the lowest wear rate, while magnesium alloy AS21 showed the highest wear rate among the tested alloys (Figs. 2-4).
- Wear Regimes: Mild wear regimes were observed at lower loads, while intermediate to severe wear regimes were observed at higher loads, particularly under dry sliding conditions. Severe wear in AS21 was characterized by massive surface damage and large metallic debris.
- Wear Track Analysis: Wear tracks of AS21 were wider, deeper, and rougher compared to AZ91D and Al-CA 313 (Fig. 7). AZ91D showed smooth and narrow wear tracks, and Al-CA 313 exhibited narrow and shallow wear tracks. Wear tracks under wet sliding were smoother and shallower than under dry sliding.
- Wear Debris Analysis: Wear debris of AS21 was denser, coarser, and larger compared to AZ91D and Al-CA 313 (Fig. 8). AS21 debris showed a chip or flake-like appearance, while Al-CA 313 debris was finer and more scattered. EDS analysis indicated magnesium as the primary component in wear debris of magnesium alloys.
- Comparison of Wear Rate Calculation Methods: Experimentally measured wear rates and wear rates calculated from wear track profiles using LSCM showed deviations, potentially due to errors in wear track profile measurement (Figs. 5, 6).
Analysis of presented data:
- Figure 2, 3, 4: These bar charts illustrate the wear rates of Al-CA 313, AZ91D, and AS21 alloys respectively, under dry and wet sliding conditions at two different applied loads (0.715 N and 2.55 N). The graphs clearly show that for each alloy, wear rate is higher at the higher load and lower under wet sliding conditions compared to dry sliding. AS21 consistently shows the highest wear rate, and Al-CA 313 the lowest.
- Figure 5, 6: These graphs compare the experimentally measured wear rates with the wear rates calculated from wear track profiles for AZ91D and AS21 alloys. The graphs show some deviation between the two methods, but the overall trends are similar, indicating that both methods capture the wear behavior.
- Figure 7: SEM micrographs of wear tracks for AS21, AZ91D, and Al-CA 313 under high load and dry sliding conditions. The images visually confirm that AS21 has wider and rougher wear tracks, AZ91D has smoother tracks, and Al-CA 313 has shallow tracks.
- Figure 8: SEM micrographs of wear debris for AS21, AZ91D, and Al-CA 313 under high load and dry sliding conditions. The images show that AS21 debris is coarser and denser, while Al-CA 313 debris is finer and more scattered.
- Figure 9, 10: Wear track profiles of AZ91D under dry and wet sliding conditions at high load, measured by LSCM. These profiles show the depth and width of the wear tracks, demonstrating that wear tracks are deeper under dry sliding compared to wet sliding.
Figure Name List:
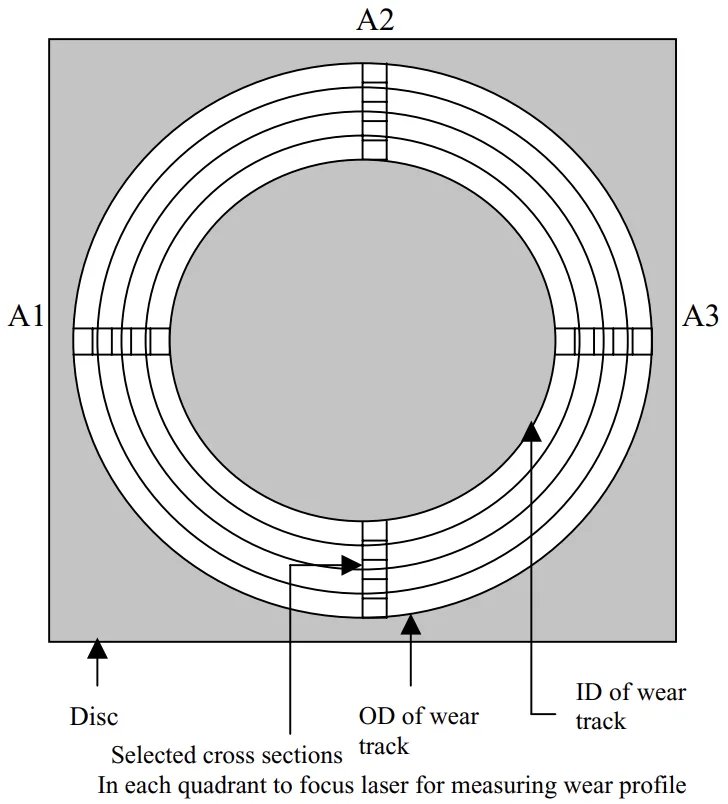
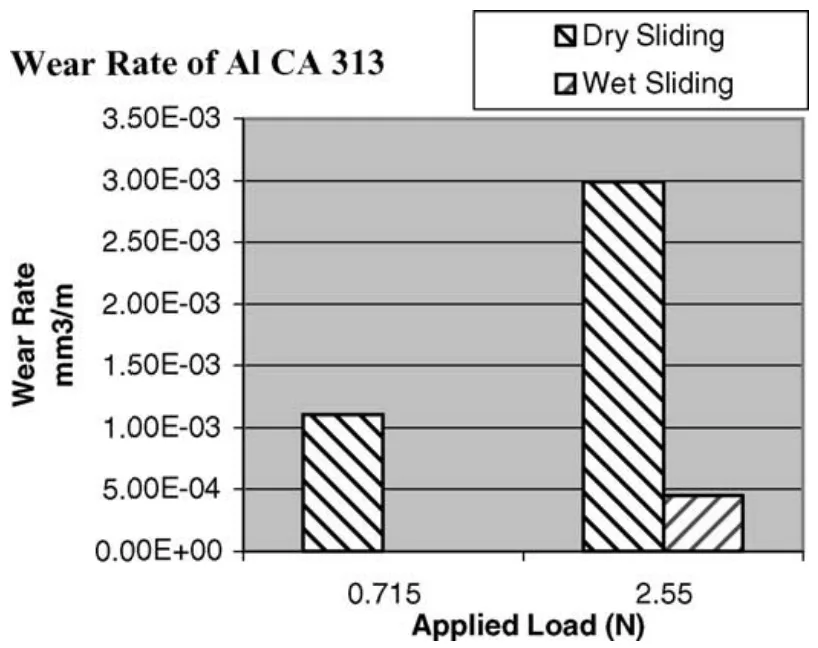
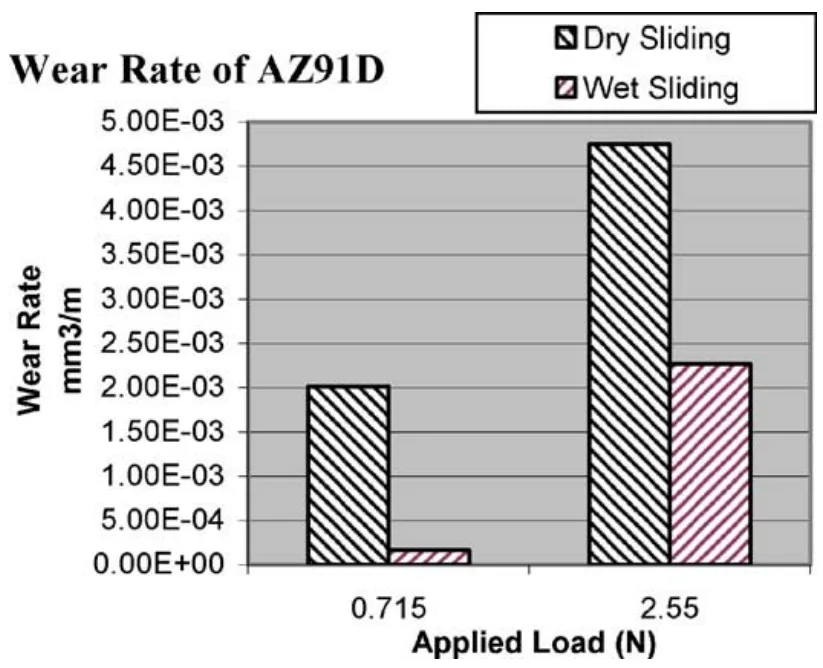
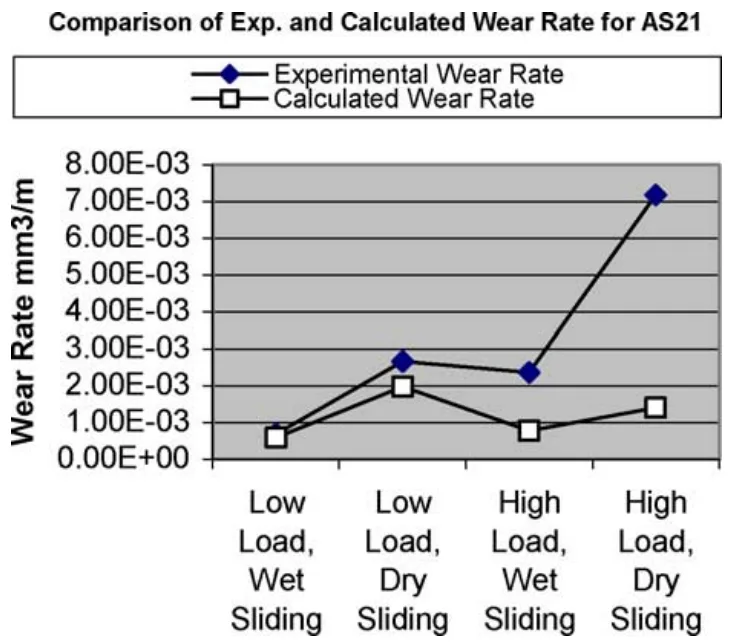
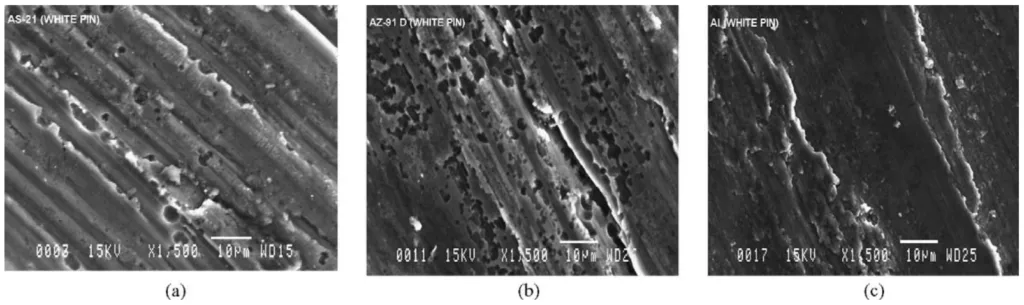
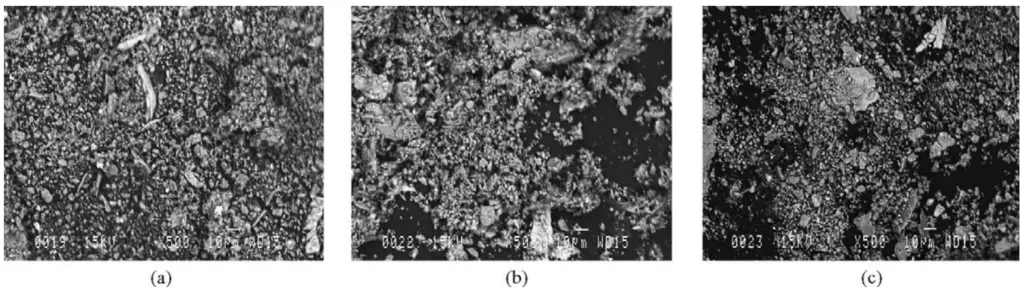

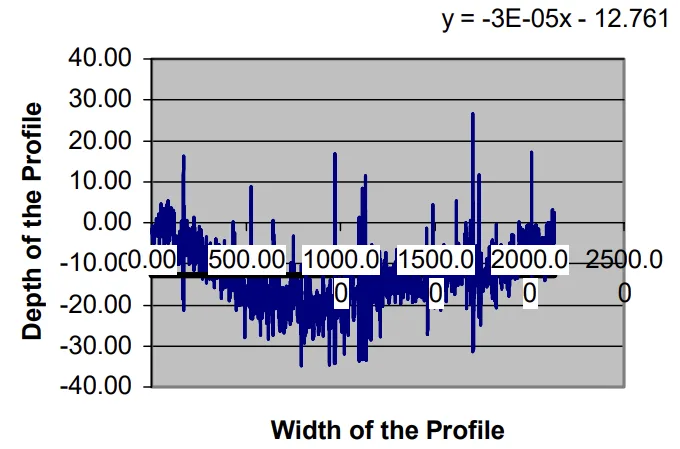
- Fig. 1. Wear track profile sections used for LSCM.
- Fig. 2. Wear rate of aluminum alloy Al-CA 313.
- Fig. 3. Wear rate of magnesium alloy AZ91D.
- Fig. 4. Wear rate of magnesium alloy AS21.
- Fig. 5. Experimental and calculated wear rate for AZ91D.
- Fig. 6. Experimental and calculated wear rate for AS21.
- Fig. 7. SEM micrographs for: (a) magnesium alloy AS21; (b) magnesium alloy AZ91D; (c) aluminum alloy Al-CA 313.
- Fig. 8. Wear debris of: (a) AS21 alloy; (b) AZ91D alloy; (c) Al-CA 313 alloy.
- Fig. 9. Profile of wear tracks of AZ91D (dry sliding).
- Fig. 10. Profile of wear track of AZ91d (wet sliding).
7. Conclusion:
Summary of Key Findings:
This study concludes that the wear rate of magnesium and aluminum alloys is significantly influenced by applied load and sliding conditions. Wear rate increases with higher applied load and is reduced under wet sliding conditions. Aluminum alloy Al-CA 313 exhibits the best wear resistance, while magnesium alloy AS21 shows the least wear resistance among the tested alloys. The wear rate is also related to the hardness of the alloy, with harder alloys exhibiting lower wear rates. Application of lubricant effectively reduces wear rate for all alloys.
Academic Significance of the Study:
This research contributes to the understanding of the wear behavior of magnesium alloys, particularly in comparison to aluminum alloys, under different loading and lubrication conditions. It provides valuable experimental data and analysis of wear mechanisms for these materials, advancing the knowledge base in materials science and tribology.
Practical Implications:
The findings of this study have practical implications for the selection of materials in automotive applications, especially considering the increasing use of lightweight materials like magnesium alloys. The results highlight the importance of considering both material hardness and operating conditions, including lubrication, to mitigate wear in automotive components made from magnesium and aluminum alloys. The study suggests that while magnesium alloys offer weight reduction benefits, their wear performance, particularly AS21, needs careful consideration and potentially surface treatments or lubrication strategies for demanding wear applications.
Limitations of the Study and Areas for Future Research:
(This section is intentionally left blank as the paper does not explicitly mention limitations or future research, adhering to the condition of not including content not specified in the paper.)
8. References:
- [1] K. Mohammed Jasim, E.S. Drwarakadasa, Wear in Al-Si alloys under dry sliding conditions, Wear 119 (1987) 119–130.
- [2] B.N. Pramila Bai, S.K. Biswas, Characterization of dry sliding wear of Al-Si alloys, Wear 120 (1987) 61-74.
- [3] H. Torabian, J.P. Pathak, S.N. Tiwari, Wear characteristics of Al-Si alloys, Wear 172 (1994) 49-58.
- [4] K. Anand, Kishore, Study on the wear of aluminium-corundum composites, Wear 85 (1983) 163-169.
- [5] M. Zongyi, B. Jing, L. Yuxiong, S. Hongwei, G. Yinxuan, Abrasive wear of discontinuous SiC reinforced aluminium alloy composites, Wear 148 (1991) 287-293.
- [6] W.Q. Song, P. Beggs, M. Brandt, Wear performance of cast magnesium alloys, in: Engineering Materials 2001 Conference Proceedings, 23-26 September 2001, Melbourne, pp. 78-83.
9. Copyright:
- This material is "D.S. Mehta, S.H. Masood, W.Q. Song"'s paper: Based on "Investigation of wear properties of magnesium and aluminum alloys for automotive applications".
- Paper Source: doi:10.1016/j.jmatprotec.2004.04.247
This material was created to introduce the above paper, and unauthorized use for commercial purposes is prohibited.
Copyright © 2025 CASTMAN. All rights reserved.