This introductory paper is the research content of the paper "Injection Parameters Setting in High-Pressure Die Casting" published by STM Journals.
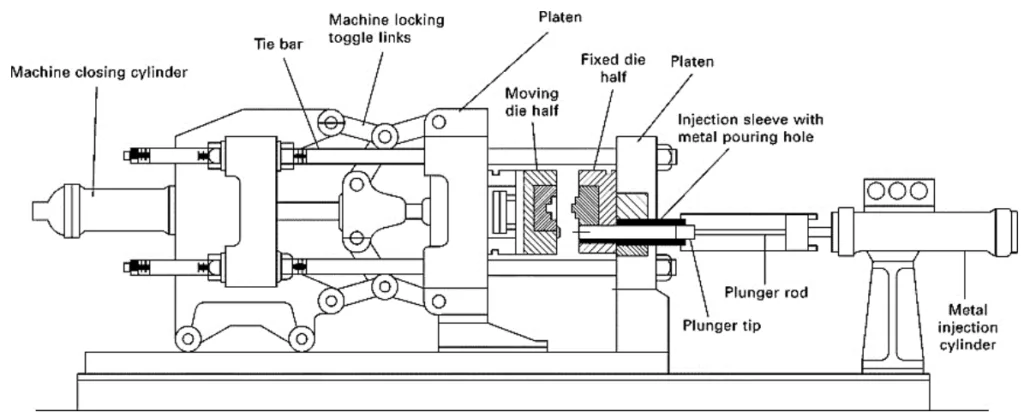
1. Overview:
- Title: Injection Parameters Setting in High-Pressure Die Casting
- Author: Rahul B., Bhaskar M. Reddy, Tamilselvam Nallusamy, W. Brightlin Abisha, Suresh P.
- Publication Year: 2023
- Published Journal/Society: Journal of Polymer & Composites (Volume 11, Special Issue 13)
- Keywords: Casting defects, Cavity pressure, Fill time, Gate area, Injection velocity
2. Abstract
The advancement of science and processing technology is highly essential. Aluminium die-cast components are widely used. Proper process parameters are required. This paper studies optimum injection parameters. The common defects encountered in high pressure die casting process (HPDC) are cold shut, flow line, blowholes, pinholes, shrinkage, gas entrapment porosity, etc. This research analyses the effect of slow speed, fast speed, and intensification features. Optimum value for the injection parameters such 1st phase length, 1st phase velocity, 2nd phase length, 2nd phase velocity, 3rd phase cavity pressure & holding time are estimated.
3. Research Background:
Background of the research topic:
Metals and alloys, especially aluminum, are widely used in engineering applications, including automobiles, composites, and aerospace, due to properties like high strength-to-weight ratio and corrosion resistance [1-6]. Die casting processes are categorized into Gravity Die Casting (GDC), Low Pressure Die Casting (LPDC), and High Pressure Die Casting (HPDC) [7–9].
Status of previous research:
- Gravity Die Casting (GDC): Uses gravitational and atmospheric pressure. Recommended for parts with wall thicknesses greater than 6 mm, casting weights from 3 to 25 kgs, but has a lower production rate than HPDC [10–14].
- Low Pressure Die Casting (LPDC): Uses pressurized gas (0.1-0.3 bar) to fill the mold cavity [9, 17]. Used for automobile parts like wheels and cylinder heads [18].
- High-Pressure Die Casting (HPDC): Involves a piston driving molten metal at high pressure and velocity [19–23]. Die sets are made of H13 steel, hardened to 44-46 HRC, and often nitrided [24, 25, 26].
Need for research:
Variations in injection parameters (slow speed, fast speed, intensification pressure, etc.) can lead to casting defects. Proper settings are essential for high-quality, defect-free castings.
4. Research purpose and research question:
Research purpose:
To study and optimize injection parameters in HPDC to reduce casting defects.
Core research:
To analyze the effects of the three phases of injection (slow speed, high speed, and intensification) and determine optimal values for:
- 1st phase length and velocity
- 2nd phase length and velocity
- 3rd phase cavity pressure and holding time
5. Research methodology
The research analyzes the three-phase injection system (Figure 2) in HPDC, focusing on:
- Filling Ratio: The ratio of poured liquid metal volume to the total injection sleeve volume. A 60-70% filling ratio is recommended to minimize gas entrapment porosity [33–36].
- 1st Phase (Prefilling Phase): Plunger moves molten metal to near the in-gate at low velocity (0.1 m/sec to 0.6 m/sec) [37]. The 1st phase length and velocity are calculated using formulas provided by the North American Die Casting Society (NADCA).
- 2nd Phase (Die Cavity Filling Phase): Liquid metal is injected at high speed (0.4 m/sec–6 m/sec). Mold filling time is very short (5 to 100 milliseconds). 2nd phase length and velocity are calculated based on die design data, gate area, and gate velocity.
- 3rd Phase (Intensification Phase): Extra metal is pushed in during solidification to compensate for shrinkage. Intensification pressure (cavity pressure) is calculated, and different pressures are recommended for different types of castings [38-42].
The study uses these principles to analyze an engine housing component, with specific data provided for shot weight, casting weight, gate area, plunger diameter, and active sleeve length.
6. Key research results:
Key research results and presented data analysis:
The study calculated the injection parameters for the engine housing component step-by-step:
- Shot Weight Volume, Casting Weight Volume, and Shot Sleeve Volume: Calculated based on provided data.
- Fill Ratio: Calculated as 58.53%, close to the optimal 60-70%.
- 2nd Phase Length: Calculated as 12.03 cm.
- 1st Phase Length: Calculated as 16.97 cm.
- 1st Phase Velocity: Calculated as 0.077 m/sec, within the recommended range.
- 2nd Phase Velocity: Calculated as 1.55 m/sec.
- Intensification (Cavity) Pressure: Calculated as 933 kg/cm², within the recommended range for pressure-tight castings.
These optimized parameters were then implemented in a production setting.
Table 1 summarizes the parameters before and after the research, showing improvements in air entrapment, cavity filling time, pressure tightness, and a reduction in rejection rates from 8% to 1.2%.
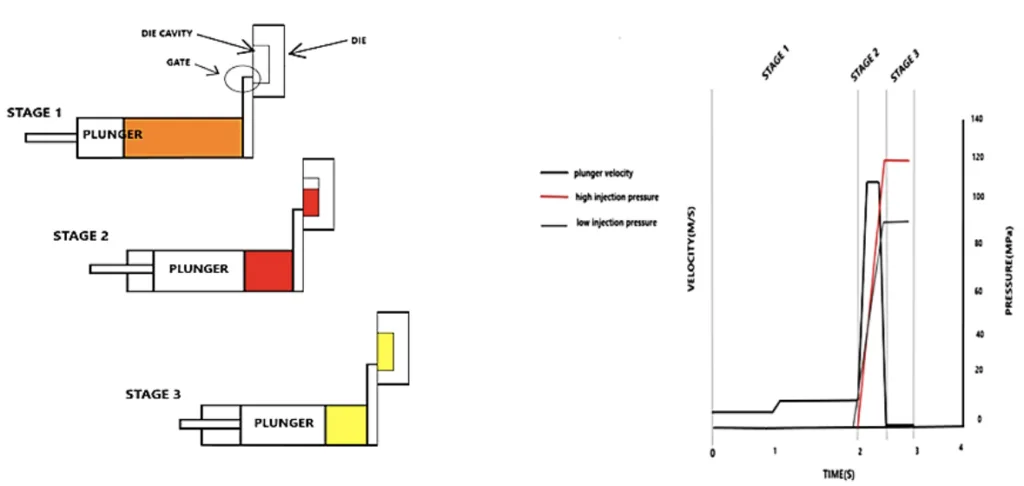
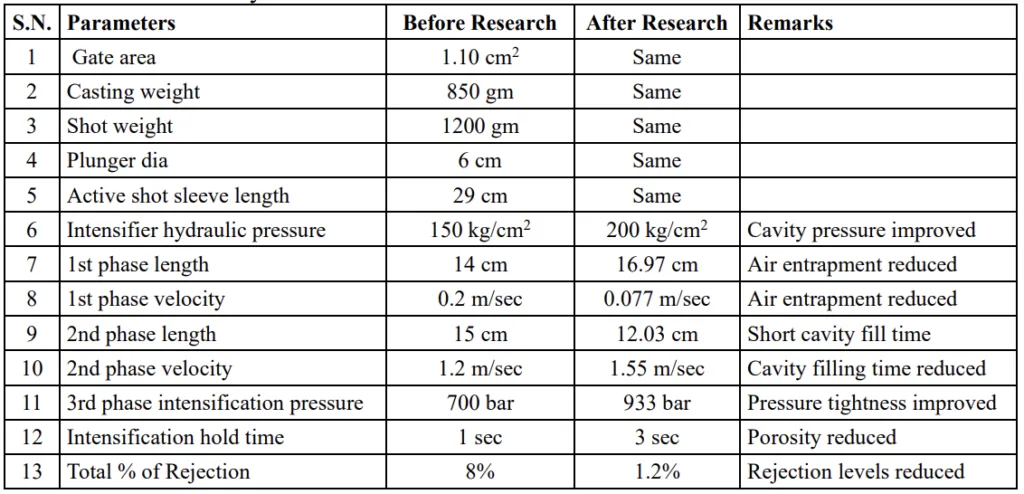
List of figure names:
- Figure 1. Cold chamber horizontal high pressure die casting machine.
- Figure 2. Three-phase injection system.
7. Conclusion:
Summary of key findings:
By optimizing the injection parameters (1st phase length & velocity, 2nd phase length & velocity, and 3rd phase cavity pressure & holding time), the rejection rate of castings was significantly reduced from 8% to 1.2%.
The research demonstrates that careful control and calculation of injection parameters in HPDC are crucial for producing high-quality, defect-free castings. The practical implication is a significant reduction in scrap and improved production efficiency, leading to increased profit and customer satisfaction.
8. References:
- [1] Koli D K, Agnihotri G, Purohit R. Advanced aluminium matrix composites: the critical need of automotive and aerospace engineering fields. Materials Today: Proceedings. 2015; 2(4-5): 3032-041p.
- [2] Sharma A K, Rakesh Bhandari, Amit Aherwar, et al. A study of advancement in application opportunities of aluminum metal matrix composites. Materials Today: Proceedings. 2020; 26: 2419-2424p.
- [3] Eliasson J, Sandström R. Applications of Aluminium Matrix Composites. Key Engineering Materials. 1995; 104–107: 3-36p.
- [4] Ashkenazi D. How aluminum changed the world: A metallurgical revolution through technological and cultural perspectives. Technological Forecasting and Social Change. 2019; 143: 101–113р.
- [5] Richards J W. Aluminium: its history, occurrence, properties, metallurgy and applications, including its alloys. Walnut Street, U S A: HC Baird & Company; 1890.
- [6] Sukiman N L, Zhou X, Birbilis N, et al. Durability and corrosion of aluminium and its alloys: overview, property space, techniques and developments. In: Zaki Ahmad, editor. Aluminium Alloys-New Trends in Fabrication and Applications. London: Intech Open Limited; 2012; 5: 47–97p.
- [7] Alok Singh Chauhan, Boddapati Anirudh, Satyanarayana A, et al. FEA optimization of injection parameters in ceramic core development for investment casting of a gas turbine blade. Materials Today: Proceedings. 2020; 26: 2190–2199p.
- [8] He Li, Yongsheng Liu, Yansong Liu, et al. Influence of debinding holding time on mechanical properties of 3D-printed alumina ceramic cores. Ceramics International. 2021; 47(4): 4884–4894p.
- [9] Bonollo F, Urban J, Bonatto B, et al. Gravity and low pressure die casting of aluminium alloys: a technical and economical benchmark. la metallurgia italiana. 2005; 6: 23–31р.
- [10] Prosenjit Das, Bikash Bhuniya, Sudip K. Samanta, et al. Studies on die filling of A356 Al alloy and development of a steering knuckle component using rheo pressure die casting system. Journal of Materials Processing Technology. 2019; 271: 293-311p.
- [11] Byoung Hee Choi, Young Soo Jang, Jae Gi Sim, et al. Application of rheo-diecasting of a high strength Al-Si-Mg alloy to automotive suspension arms. ISIJ international. 2013; 53(3): 502-510p.
- [12] Reddy A C, Rajanna C. Design of gravity die casting process parameters of Al-Si-Mg alloys. Journal of Machining and Forming Technologies. 2009; 1(1/2): 1–25p.
- [13] Malhotra V, Kumar Y. Study of process parameters of gravity die casting defects. Int. J. Mech. Eng. Technol. 2016; 7: 208-211p.
- [14] Teng X, Mae H, Bai Y, et al. Pore size and fracture ductility of aluminum low pressure die casting. Engineering Fracture Mechanics. 2009; 76(8): 983–996p.
- [15] Dou K, Lordan E, Zhang Y J, et al. A complete computer aided engineering (CAE) modelling and optimization of high pressure die casting (HPDC) process. Journal of Manufacturing Processes. 2020; 60: 435-446p.
- [16] Yang H, Ji S, Watson D, et al. Repeatability of tensile properties in high pressure die-castings of an Al-Mg-Si-Mn alloy. Metals and Materials International. 2015; 21(5): 936–943p.
- [17] Fu M W, Zheng J Y. Die Casting for Fabrication of Metallic Components and Structures. In: Encyclopedia of Materials-Metals and Alloys. Elsevier; 2021: 54–72p.
- [18] Chen Hu, Haidong Zhao, Xueling Wang, et al. Microstructure and properties of AlSi12Fe alloy high pressure die-castings under different vacuum levels. Vacuит. 2020; 180: 109561p.
- [19] Jadhav A R, Hujare D P, Hujare P P. Design and optimization of gating system, modification of cooling system position and flow simulation for cold chamber high pressure die casting machine. Materials Today: Proceedings. 2021; 46(17): 7175–7181p.
- [20] Patnaik L, Saravanan I, Kumar S. Die casting parameters and simulations for crankcase of automobile using MAGMAsoft. Materials Today: Proceedings. 2020; 22: 563-571p.
- [21] Chavan R and Kulkarni P. Die design and optimization of cooling channel position for cold chamber high pressure die casting machine. IOP Conference Series: Materials Science and Engineering. 2020; 810: 012017р.
- [22] Niu X P, Hu B H, Pinwill I, et al. Vacuum assisted high pressure die casting of aluminium alloys. Journal of Materials Processing Technology. 2000; 105(1-2): 119–127р.
- [23] Bonollo F, Gramegna N, Timelli G. High-pressure die-casting: contradictions and challenges. JOM. 2015; 67(5): 901–908p.
- [24] Kohlstädt S, Vynnycky M, Jäckel J. Towards the modelling of fluid-structure interactive lost core deformation in high-pressure die casting. Applied Mathematical Modelling. 2020; 80: 319–333p.
- [25] Kohlstädt S, Vynnycky M, Neubauer A, et al. Comparative RANS turbulence modelling of lost salt core viability in high pressure die casting. Progress in Computational Fluid Dynamics, an International Journal. 2019; 19(5): 316–327р.
- [26] Kohlstädt S, Vynnycky M, Goeke S, et al. On Determining the Critical Velocity in the Shot Sleeve of a High-Pressure Die Casting Machine Using Open Source CFD. Fluids. 2021; 6(11): 386p.
- [27] Li Zixin, Li Dejiang, Zhou Wenke, et al. Characterization on the formation of porosity and tensile properties prediction in die casting Mg alloys. Journal of Magnesium and Alloys. 2022; 10(7): 1857-1867p.
- [28] Ewan Lordan, Jaime Lazaro-Nebreda, Yijie Zhang, et al. On the relationship between internal porosity and the tensile ductility of aluminium alloy die-castings. Materials Science and Engineering: A. 2020; 778; 139107p.
- [29] Mahesh N Adke, Shrikant V Karanjkar. Optimization of die-casting process parameters to identify optimized level for cycle time using Taguchi method. International Journal of Innovations in Engineering and Technology. 2014; 4(4): 365–375p.
- [30] Singh R. Modeling of surface hardness in hot chamber die casting using Buckingham's π approach. Journal of Mechanical Science and Technology. 2014; 28(2): 699–704p.
- [31] Dańko J, Stojek J, Dańko R. Model testing of casting process in cold-chamber die casting machine. Archives of Metallurgy and Materials. 2007; 52(3): 503–513p.
- [32] Singh R, Singh H. Effect of Some Parameters on the Cast Component Properties in Hot Chamber Die Casting. Journal of The Institution of Engineers (India): Series C. 2016; 97(2): 131–139p.
- [33] Lee J, Lee Y C, Kim J T. Migration from the traditional to the smart factory in the die casting industry: Novel process data acquisition and fault detection based on artificial neural network. Journal of Materials Processing Technology. 2021; 290: 116972p.
- [34] Bataineh O, Al-Dwairi A. Application of statistical process control tools to improve product quality in manufacturing processes. Applied Mechanics and Materials. 2012; 110–116: 4023-4027р.
- [35] Bruckmeier L, Ringel A, Vroomen U. Influence of High-Pressure Die Casting Process Parameters on the Compound Strength of Hybrid Components with Undercut Sheet Metal. Metals. 2023; 13(10): 1717р.
- [36] Wan Mahmood W H, Mohd Rosdi M N H, Muhamad M R. A Conceptual Framework in Determining Manufacturing Complexity. Applied Mechanics and Materials. 2015; 761: 550–554p.
- [37] Outmani, I, Laurence Fouilland-Paille, Jérôme Isselin, et al. Effect of Si, Cu and processing parameters on Al-Si-Cu HPDC castings. Journal of Materials Processing Technology. 2017; 249: 559-569p.
- [38] Rathinam N, Dhinakaran R, Sharath E. Optimizing process parameters to reduce blowholes in high pressure die casting using Taguchi methodology. Materials Today: Proceedings. 2021; 38: 2871–2877р.
- [39] Mohd U, Pandulu G, Jayaseelan R. Strength evaluation of eco-friendly concrete using Taguchi method. Materials Today: Proceedings. 2020; 22: 937–947p.
- [40] Balikai V G, Siddlingeshwar I, Gorwar M. Optimization of process parameters of High Pressure Die Casting process for ADC12 Aluminium alloy using Taguchi method. International Journal of Pure and Applied Mathematics. 2018; 120(6): 959–969p.
- [41] Anilchandra R. Adamane, Lars Arnberg, Elena Fiorese, et al. Influence of injection parameters on the porosity and tensile properties of highpressure die cast Al-Si alloys: a review. International Journal of Metalcasting. 2015; 9(1): 43–53р.
- [42] Karthik A, Karunanithi R, Srinivasan S A, et al. The optimization of squeeze casting process parameter for AA2219 alloy by using the Taguchi method. Materials Today: Proceedings. 2020; 27: 2556-2561р.
9. Copyright:
- This material is a paper by "Rahul B., Bhaskar M. Reddy, Tamilselvam Nallusamy, W. Brightlin Abisha, Suresh P.": Based on "Injection Parameters Setting in High-Pressure Die Casting".
- Source of paper: DOI (Journal): 10.37591/JoPC
This material was created to introduce the above paper, and unauthorized use for commercial purposes is prohibited. Copyright © 2025 CASTMAN. All rights reserved.