This introduction paper is based on the paper "Inhomogeneous Skin Formation and Its Effect on the Tensile Behavior of a High Pressure Die Cast Recycled Secondary AlSi10MnMg(Fe) Alloy" published by "Metallurgical and Materials Transactions A".
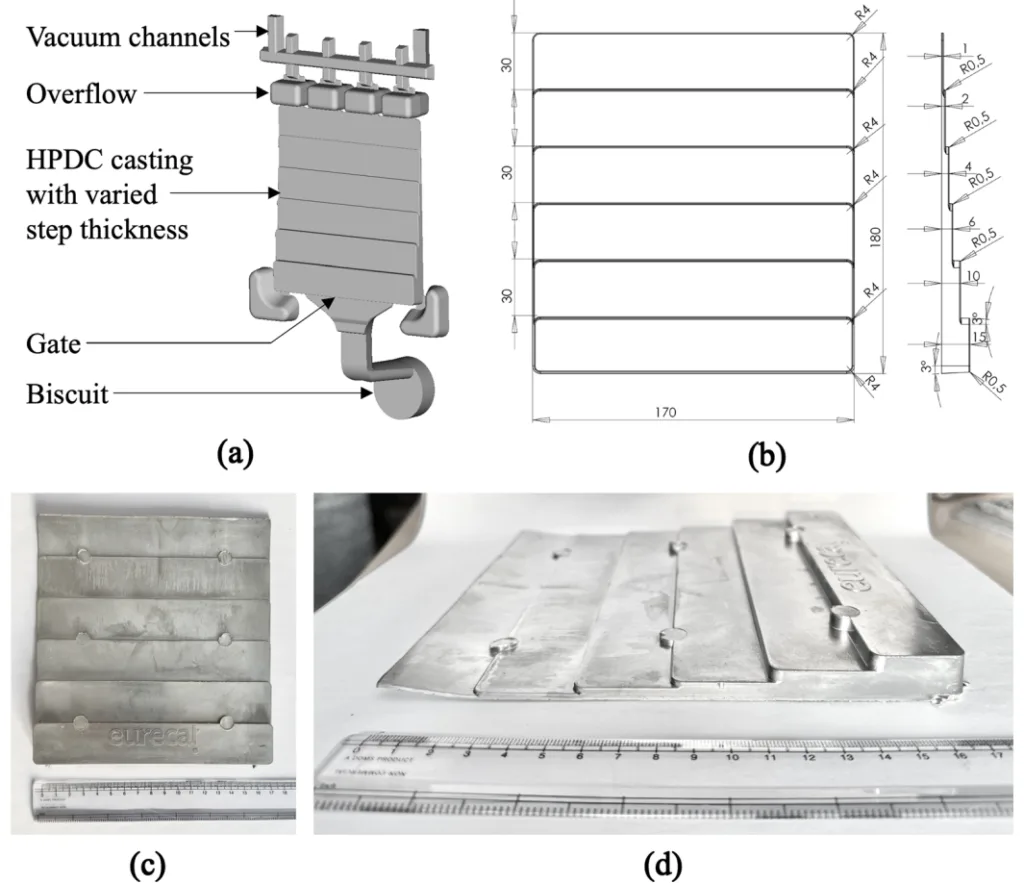
1. Overview:
- Title: Inhomogeneous Skin Formation and Its Effect on the Tensile Behavior of a High Pressure Die Cast Recycled Secondary AlSi10MnMg(Fe) Alloy
- Author: BISWAJIT DALAI, SIMON JONSSON, MANEL DA SILVA, LIANG YU, and JÖRGEN KAJBERG
- Year of publication: 2024
- Journal/academic society of publication: Metallurgical and Materials Transactions A
- Keywords: Not specified in the paper
2. Abstract:
The current study investigated the microstructure evolution, mechanical properties, and fracture behavior of a high pressure die cast (HPDC) novel secondary alloy. The as-cast microstructure comprised (i) Primary α-Al, (ii) α-Al15(FeMn)3Si2 intermetallics, and (iii) Al-Si eutectics. The microstructure starting from the surface through the depth of the HPDC casting consisted of (i) fine-grained skin at surface, (ii) increased Al-Si eutectics at intermediate location, and (iii) coarse α-Al dendrites at center. Accordingly, the hardness increased from skin to the intermediate section and then decreased toward the center of the casting. The formation of skin layer was highly discontinuous, which was attributed to the complicated fluid flow pattern inside the die cavity. The skin layer indicated to slightly improve the strength of the HPDC alloy; however, it restricted the ductility of the material with a large variation. Such ductility behavior resulted from a fracture mechanism triggered by the inhomogeneous skin because of its poor bonding with the adjacent matrix. Even though the secondary alloy contained casting defects and α-Al15(FeMn)3Si2 intermetallics that are known to be driving factors for the fracture in such materials, the effects from the inhomogeneous skin turned out to be predominant in the current study.
3. Introduction:
High pressure die casting (HPDC) is a high-productivity process used extensively in the automotive industry for producing geometrically accurate, thin-walled components like chassis and body-in-white (BIW) structures. Conventional HPDC alloys are often based on the Al-Si-Mg system. These alloys typically contain Fe (0.8-1.1 wt pct) as an impurity, which helps prevent die sticking but leads to the formation of detrimental needle-shaped β-Al5FeSi compounds, negatively impacting mechanical properties, especially ductility. To mitigate this, primary AlSi10MnMg alloys (e.g., EN AC-43500) were developed with restricted Fe (<0.25 wt pct) and added Mn (0.4-0.8 wt pct). Mn acts as an "iron corrector," promoting the formation of less harmful α-Fe intermetallics instead of β-Fe, and also compensates for the reduced Fe in preventing die sticking. However, achieving low Fe levels increases production costs due to the need for dilution. With the growing emphasis on sustainability and cost reduction, there is increasing interest in using secondary (recycled) Al-Si alloys, which inherently contain higher Fe levels due to scrap recycling. This study focuses on understanding the microstructure, mechanical behavior, and fracture mechanisms of a recycled secondary AlSi10MnMg(Fe) alloy processed by HPDC, paying particular attention to the often-overlooked phenomenon of surface skin formation and its potential inhomogeneity.
4. Summary of the study:
Background of the research topic:
The automotive industry utilizes HPDC for producing lightweight Al-Si alloy components. Managing Fe content is crucial; high Fe forms harmful β-Fe phases, while low Fe increases cost and die sticking potential. Primary alloys use low Fe and Mn additions (forming α-Fe) to balance properties and castability. Secondary (recycled) alloys offer cost and environmental benefits but have higher Fe content, necessitating careful control (e.g., Mn:Fe ratio) to avoid β-Fe. Microstructural features like intermetallics, defects, and surface skin significantly influence the final properties of HPDC parts.
Status of previous research:
Studies on primary AlSi10MnMg HPDC alloys have characterized the typical microstructure (α-Al, α-Fe, Al-Si eutectics), its variation from surface (fine) to center (coarse), and different α-Fe morphologies. Fracture is often linked to large pores, surface defects, or α-Fe particles acting as stress concentrators. Research on secondary AlSi10MnMg(Fe) alloys has focused on optimizing Mn:Fe ratios (typically 0.58-1.3) to suppress β-Fe formation. Their microstructure is similar to primary alloys, with fracture also initiating at large α-Fe compounds or casting defects like laminations. However, the formation and influence of inhomogeneous surface skin, although sometimes implicitly observed in fracture surfaces, have not been systematically investigated, representing a knowledge gap.
Purpose of the study:
The study aimed to investigate the microstructure evolution, mechanical properties, and fracture behavior of a novel recycled secondary AlSi10MnMg(Fe) alloy produced by vacuum-assisted HPDC. A special focus was placed on characterizing the surface skin formation, its potential inhomogeneity, and its effects on the alloy's tensile response, particularly for thin-walled (2-mm) castings relevant to recent structural applications.
Core study:
The core of the study involved:
- Characterizing the as-cast microstructure of the secondary AlSi10MnMg(Fe) alloy using OM, SEM, and EDS, focusing on phase identification (α-Al, α-Fe, eutectics), morphology, and distribution through the 2-mm thickness.
- Investigating the formation and homogeneity of the surface skin layer at different locations.
- Identifying casting defects present in the HPDC parts.
- Measuring the hardness profile across the casting thickness.
- Performing uniaxial tensile tests on specimens with the original skin and specimens with the skin removed to evaluate the skin's effect on strength and ductility.
- Conducting detailed fracture analysis using high-speed camera imaging, SEM fractography, and OM of lateral surfaces to understand crack initiation and propagation mechanisms, specifically linking them to the observed microstructure and skin inhomogeneity.
5. Research Methodology
Research Design:
The research employed an experimental approach. A recycled secondary AlSi10MnMg(Fe) alloy was cast into step-shaped parts using a vacuum-assisted HPDC process. Samples from the 2-mm thick section were subjected to microstructural characterization, hardness testing, and uniaxial tensile testing (comparing samples with and without surface skin). Fracture surfaces and adjacent lateral surfaces were analyzed to correlate mechanical behavior with microstructural features, especially skin inhomogeneity.
Data Collection and Analysis Methods:
- Material: A secondary AlSi10MnMg(Fe) alloy supplied by Raffmetal (composition in Table I, notably Si: 9.547, Fe: 0.297, Mn: 0.65, Mg: 0.218 wt pct, Mn:Fe ≈ 2.1).
- HPDC Process: A Buhler cold chamber machine (5250 kN locking force) was used to cast step parts (Fig 1b). Key parameters included melt temperature 700-720 °C, plunger velocity 4 m/s (filling phase), calculated ingate velocity 42 m/s, VDS vacuum system (85-100 mbar), and final pressure 900-950 bar.
- Microstructure Characterization: Samples from 2-mm steps were sectioned, mounted, ground (P120 to P4000 SiC paper), and polished (1-µm diamond, 0.05-µm OPS). Optical Microscopy (OM) was performed using a Nikon Eclipse MA200. Scanning Electron Microscopy (SEM) with Energy Dispersive X-ray Spectroscopy (EDS) was done using an FEI Magellan 400 XHR SEM for phase composition analysis.
- Mechanical Testing:
- Hardness: Vickers microhardness (Struers Duramin-40, 0.05 kgf load, 10 s dwell time) measured across the polished cross-section.
- Tensile Testing: Flat specimens (Fig 3a) machined from the center of 2-mm steps. Two sets tested: 'with skin' (surface ground with P1200 paper) and 'without skin' (~150 µm removed from each surface by grinding up to P1200 paper, followed by P1200 grinding on gauge). Tests performed on an Instron 1272 machine at 2 mm/min (strain rate 0.001 s⁻¹) with an extensometer (25 mm gauge length). A Phantom V2512 high-speed camera (96,000 frames/s) recorded crack initiation.
- Fracture Analysis: SEM (Magellan, 3 kV, 0.8 nA, ETD detector) used for fractography. OM (Nikon) used on polished lateral surfaces adjacent to the fracture (Fig 4).
- Solidification Time/Cooling Rate Estimation: Secondary Dendrite Arm Spacing (SDAS, d) measured from OM images (Fig 9). Local solidification time (ts) and cooling rate (q) estimated using empirical equations (Eq. [1]-[3]) based on Han and Zhang [41], using measured SDAS and approximated TL (600 °C) and TS (590 °C).
Research Topics and Scope:
The study focused on a specific recycled secondary AlSi10MnMg(Fe) alloy processed by HPDC into 2-mm thick castings. The scope included:
- Detailed analysis of the as-cast microstructure: phase constituents, morphology, distribution through thickness.
- Investigation of surface skin formation, its characteristics, and particularly its inhomogeneity.
- Identification of common casting defects.
- Correlation of microstructure with hardness distribution.
- Assessment of the influence of the surface skin on tensile properties (YS, UTS, elongation).
- Elucidation of fracture mechanisms, emphasizing the role of inhomogeneous skin versus other factors like defects and intermetallics.
6. Key Results:
Key Results:
- Microstructure: The as-cast microstructure consisted of primary α-Al (dendritic (α-Al)I and globular (α-Al)II), α-Al15(FeMn)3Si2 intermetallics (polygonal (α-Fe)I, fine polygonal (α-Fe)II, and Chinese script), and Al-Si eutectics (Fig 5). The Mn:Fe ratio of ~2.1 successfully suppressed the formation of detrimental β-Al5FeSi. EDS analysis confirmed the composition of α-Fe phases (Table II).
- Microstructure Gradient: A distinct microstructural gradient existed through the 2-mm thickness: fine-grained α-Al skin (Region 1, ~30-150 µm thick), an intermediate zone with increased Al-Si eutectics (Region 2), and a center dominated by coarse α-Al dendrites ((α-Al)I) (Region 3) (Fig 6).
- Inhomogeneous Skin: Skin formation was found to be highly inhomogeneous. Observations included abrupt cessation of the skin layer, skin appearing to move inwards from the surface, and complete absence of skin on some surfaces (Fig 7).
- Casting Defects: Various defects were identified, including cold flakes, cold shots, shrinkage pores, and lamination associated with inhomogeneous skin (Fig 8).
- SDAS and Cooling Rate: Mean SDAS increased from 3.6 µm in the skin (Region 1) to 14.6 µm in the center (Region 3) (Fig 9). Estimated cooling rates were ~33 °C/s at the skin and ~0.5 °C/s at the center (Table III), though these are order-of-magnitude estimates.
- Hardness Profile: Hardness increased from the skin (~86 HV) to the intermediate region (due to more eutectics) and then decreased towards the center (due to coarse α-Al) (Fig 10). Significant local variations in hardness were observed, correlating with the phase mixture under the indenter.
- Tensile Properties: Samples with skin showed slightly higher average YS (117.6 MPa vs 111.3 MPa) but lower average UTS (221.8 MPa vs 237 MPa) and significantly lower average total elongation (TE) (4.2% vs 6.2%) compared to samples without skin (Fig 11, 12). Crucially, samples with skin exhibited much larger variation (scatter) in both UTS and TE.
- Fracture Behavior: High-speed imaging showed crack initiation occurred at the specimen edge for samples with skin, but on the flat surface for samples without skin (Fig 13). SEM fractography revealed brittle fracture initiation features at the corners/edges corresponding to inhomogeneous skin presence (Fig 14). OM analysis of lateral surfaces confirmed the presence of irregular or inwardly migrated skin layers adjacent to the crack initiation sites in samples B and C, which failed at low elongation (Fig 15, 16). Delamination along the poorly bonded interface between the inhomogeneous skin and the underlying matrix was identified as the primary failure initiation mechanism in these cases (Fig 14c, 15c3, 16b). Crack propagation occurred primarily through the Al-Si eutectic regions, fracturing Si particles and α-Fe intermetallics (Fig 18).
- Dominant Factor: The study concluded that the inhomogeneous skin formation, leading to poor bonding and delamination, was the predominant factor controlling the fracture behavior and limiting the ductility (causing large scatter) in the tested HPDC secondary alloy samples with skin, overriding the effects of casting defects and α-Fe particles in those specific cases. Removal of the skin layer led to improved and more consistent ductility.
Figure Name List:
- Fig. 1—(a) Diagram of HPDC configuration showing different parts, (b) Schematic diagram showing the dimensions of the die used in the HPDC process, (c) Top view of an actual cast part, and (d) Side view of an actual cast part showing the steps with different wall thicknesses.
- Fig. 2—Graphical representation of an as-cast part of 2-mm wall thickness, with green and red colored boxes, respectively, indicating the locations used for microscopic analysis and hardness measurements. The pink arrows indicate the two casting surfaces on which the skin layer is supposedly formed (Color figure online).
- Fig. 3—(a) Schematic diagram showing the dimensions of specimen used for uniaxial tensile tests, and (b) An actual tensile specimen machined from the as-cast part with 2-mm wall thickness.
- Fig. 4—Graphical representation of a tensile tested specimen indicating the fractured and lateral surface on which SEM and OM analyses were performed, respectively.
- Fig. 5—OM image showing different features formed in the as-cast AlSi10MnMg(Fe) alloy with 2-mm wall thickness.
- Fig. 6—OM image showing the microstructure evolution through the thickness of a 2-mm-thick as-cast part of AlSi10MnMg(Fe) alloy.
- Fig. 7—OM images showing inhomogeneous formation of skin layer in 2-mm-thick as-cast step of AlSi10MnMg(Fe) alloy: (a) Sudden disappearance of surface skin, indicated by red arrow marks, (b) Formation of skin layer moving through the depth away from the surface, indicated by purple arrow marks, and (c) Absence of skin layer on one of the casting surfaces (Color figure online).
- Fig. 8—OM images showing different casting defects produced in 2-mm-thick as-cast step part of AlSi10MnMg(Fe) alloy: (a) Cold flake with conspicuous flat edge indicated by red arrow marks, (b) Cold shot, (c) Shrinkage pore, and (d) Lamination due to inhomogeneous skin formation, indicated by purple arrow marks (Color figure online).
- Fig. 9—OM images on a 2-mm-thick as-cast step part of AlSi10MnMg(Fe) alloy showing the SDAS measurements taken in (a) Region 1: skin, and (b) Region 3: center.
- Fig. 10—(a) OM image on the indentations created during the microhardness test on 2-mm-thick as-cast step part of AlSi10MnMg(Fe) alloy, indicating their relative positions with respect to different microstructural regions, and (b) the corresponding hardness distribution through the depth. The red and purple arrow marks in (b) indicate the relatively large variation in the corresponding hardness values (Color figure online).
- Fig. 11—Engineering stress vs engineering strain curves obtained from the tensile tests of six AlSi10MnMg(Fe) alloy specimens having 2-mm wall thickness: Samples A, B, and C tested in the as-cast state by retaining skin; Samples D, E, and F tested after removing the skin.
- Fig. 12—Mean yield strength (YS) at 0.2 pct offset, mean ultimate tensile strength (UTS), and mean total elongation (TE), obtained from the tensile tests of secondary alloy specimens with and without skin. Error bars here indicate the standard deviations calculated in each case.
- Fig. 13—Images captured by the high-speed camera during the tensile tests of samples: (a) A, (b) B, (c) C, (d) D, (e) E, and (f) F. (a through c) and (d through f), respectively, display the tensile samples with and without skin. The yellow arrow in the images shown in the top row indicates the crack initiation in each case, with the images in the bottom row manifesting the crack propagation at a later time step (Color figure online).
- Fig. 14—SEM images of crack initiation site, marked by red dashed rectangle, in tensile tested samples: (a) A, (b) B, (c) C, and (e) F. The blue arrows in (c) indicate a fringe of delamination. (d) is the zoomed-in image of the area enclosed by yellow rectangle in (c), with the green dashed box indicating the presence of very fine grains (Color figure online).
- Fig. 15—OM images showing the lateral surface of the fractured samples with skin: (a) A, (b) B, and (c) C, with the red arrows in (a through c) indicating the crack initiation site corresponding to Figs. 14(a through c). (a1 through a3) are the magnified images of the areas enclosed by yellow box in (a). (b1, b2) are the magnified images of the areas enclosed by blue box in (b). (c1 through c3) are the magnified images of the areas enclosed by pink box in (c) (Color figure online).
- Fig. 16—OM images on the lateral surface of other fractured part of sample C with skin (complementary of the one already shown in Fig. 15(c)): (a) Depiction of surface skin and a cold flake, and (b) Magnified image of the crack initiation site marked by yellow rectangle in (a), with red and white dashed lines indicating the inhomogeneous skin and initial casting surface, respectively (Color figure online).
- Fig. 17—(a) OM image showing the lateral surface of the fractured sample F without skin. (a1) and (a2) are, respectively the magnified images of the areas enclosed by yellow and blue boxes in (a) (Color figure online).
- Fig. 18—SEM images on the fractured surfaces of tensile tested samples displaying (a) matrix of the fractured surface with yellow and blue arrows indicating primary α-Al and Al-Si eutectics, respectively, (b) Al-Si eutectics, (c) fractured Si particle within Al solid solution, (d) cracked Chinese script α-Fe compound, (e) cracked (α-Fe)II compound along with an uncracked (α-Fe)II compound, (f) uncracked (α-Fe)I compound, and (g) shrinkage pore with white arrows indicating α-Al dendritic arms. The red arrows in (b through e) indicate cracks (Color figure online).
- Fig. 19—Appearance of Chinese script α-Fe compound in: (a) OM image of an as-cast part, and (b) SEM image of a tensile tested part.
- Fig. 20—Still images from simulation of die filling pattern with increasing time from left to right.
- Fig. 21—Yield strength at 0.2 pct offset and total elongation exhibited by the HPDC recycled secondary alloy used in the current study along with the range of properties for the primary trimal®-05 alloy obtained from the datasheet of Trimet[37] (the artwork presented here is original and only the data from the cited source is used).
7. Conclusion:
Based on the investigation of the HPDC-processed recycled secondary AlSi10MnMg(Fe) alloy (2-mm wall thickness), the following conclusions were drawn:
- The alloy's composition (Mn:Fe ≈ 2.1) effectively suppressed detrimental β-Fe formation, favoring less harmful polyhedral and Chinese script α-Fe compounds. The Chinese script structure appears as convoluted arms in 3D.
- The microstructure exhibits a gradient through the thickness: fine-grained skin, then increased Al-Si eutectics, then coarse α-Al dendrites centrally. Mean SDAS increased from 3.6 µm (skin) to 14.6 µm (center), corresponding to estimated cooling rates of ~10 °C/s and ~1 °C/s, respectively. Hardness follows this gradient, increasing from skin to the intermediate layer, then decreasing towards the center.
- Skin layer formation is not continuous or uniform, attributed to complex fluid flow and varying heat transfer within the die cavity. Inhomogeneous skin structures resembling "waves and lakes" defects were observed.
- The skin layer shows some indication of improving yield strength, but this effect may be limited by its discontinuity and restricted thickness. However, the inhomogeneous skin significantly restricts ductility and causes abrupt failure.
- The inhomogeneous skin promotes delamination-induced cracks due to weak bonding with the adjacent matrix. This mechanism can lead to abrupt fracture and appears more detrimental to tensile ductility than other factors like casting defects or α-Fe compounds in the studied samples with skin.
- The recycled secondary alloy demonstrates the potential to achieve strength and ductility levels comparable to the commercial primary alloy, especially if the detrimental effects of inhomogeneous skin formation can be mitigated (e.g., by surface removal or process optimization).
8. References:
- [1] J.G. Kaufman and E.L. Rooy: Aluminum Alloy Castings: Properties, Processes and Applications, ASM International, Detroit, 2004, pp. 7-20.
- [2] T.O. Mbuya, B.O. Odera, and S.P. Ng’ang’a: Int. J. Cast Met. Res., 2003, vol. 16, pp. 451-65. https://doi.org/10.1080/13640461.2003.11819622.
- [3] L. Wang, M. Makhlouf, and D. Apelian: Int. Mater. Rev., 1995, vol. 40, pp. 221-38. https://doi.org/10.1179/imr.1995.40.6.221.
- [4] L. Zhang, J. Gao, L.N.W. Damoah, and D.G. Robertson: Miner. Process. Extr. Metall. Rev., 2012, vol. 33, pp. 99–157. https://doi.org/10.1080/08827508.2010.542211.
- [5] G. Gustafsson, T. Thorvaldsson, and G.L. Dunlop: Metall. Trans. A, 1986, vol. 17, pp. 45-52. https://doi.org/10.1007/BF02644441.
- [6] P. Crepeau: Trans. Am. Foundryman’s Soc., 1995, vol. 103, pp. 361-66.
- [7] D. Apelian: Aluminum Cast Alloys: Enabling Tools for Improved Performance, North American Die Casting Association, Wheeling, 2009, pp. 5-18.
- [8] J.A. Taylor: Procedia Mater. Sci., 2012, vol. 1, pp. 19-33. https://doi.org/10.1016/j.mspro.2012.06.004.
- [9] S.A.V.S. p. A. Società Alluminio Veneto: Aluminium Alloys Ingots for Remelting: Alloy Data Sheet, S.A.V.S. p. A. Società Alluminio Veneto, 2020. https://www.sav-al.com/file?oid=613fle4c10834b044515e1f3. Accessed 26 July 2024.
- [10] Rheinhfelden Alloys: Primary Aluminium Alloys for Pressure Die Casting, Rheinhfelden Alloys, 2015. https://rheinfelden-alloys.eu/wp-content/uploads/2016/01/05-HB-DG_Ci_Sf_Cm_Td_Ma_RHEINFELDEN-ALLOYS_2015_EN.pdf. Accessed 26 July 2024.
- [11] L.A. Narayanan, F.H. Samuel, and J.E. Gruzleski: Metall. Mater. Trans. A, 1994, vol. 25A, pp. 1761-73. https://doi.org/10.1007/BF02668540.
- [12] M. da Silva, J. Pujante, J. Hrabia-Wiśnios, B. Augustyn, D. Kapinos, M. Węgrzyn, and S. Boczkal: Metals, 2024, vol. 14, p. 626. https://doi.org/10.3390/met14060626.
- [13] E. Cinkilic, M. Moodispaw, J. Zhang, J. Miao, and A.A. Luo: Metall. Mater. Trans. A, 2022, vol. 53A, pp. 2861-73. https://doi.org/10.1007/s11661-022-06711-4.
- [14] D. Bösch, S. Pogatscher, M. Hummel, W. Fragner, P.J. Uggowitzer, M. Göken, and H.W. Höppel: Metall. Mater. Trans. A, 2015, vol. 46A, pp. 1035–45. https://doi.org/10.1007/s11661-014-2700-8.
- [15] R. Lumley: JOM, 2019, vol. 71, pp. 382-90. https://doi.org/10.1007/s11837-018-3121-8.
- [16] F. Liu, H. Zhao, R. Yang, and F. Sun: Materials, 2019, vol. 12, p. 2065. https://doi.org/10.3390/ma12132065.
- [17] X.Y. Jiao, Y.X. Liu, J. Wang, W.N. Liu, A.X. Wan, S. Wiesner, and S.M. Xiong: J. Mater. Sci. Technol., 2023, vol. 140, pp. 201-09. https://doi.org/10.1016/j.jmst.2022.09.014.
- [18] R. Liu, J. Zheng, L. Godlewski, J. Zindel, M. Li, W. Li, and S. Huang: Mater. Sci. Eng. A, 2020, vol. 783, p. 139280. https://doi.org/10.1016/j.msea.2020.139280.
- [19] X.Y. Jiao, Y.F. Zhang, J. Wang, H. Nishat, Y.X. Liu, W.N. Liu, H.X. Chen, and S.M. Xiong: J. Mater. Process. Technol., 2021, vol. 298, p. 117299. https://doi.org/10.1016/j.jmatprotec.2021.117299.
- [20] X.Y. Jiao, C.F. Liu, Z.P. Guo, G.D. Tong, S.L. Ma, Y. Bi, Y.F. Zhang, and S.M. Xiong: J. Mater. Sci. Technol., 2020, vol. 51, pp. 54-62. https://doi.org/10.1016/j.jmst.2020.02.040.
- [21] G. Ubertalli, F. D’Aiuto, S. Plano, and D. De Caro: Procedia Struct. Integr., 2016, vol. 2, pp. 3617-24. https://doi.org/10.1016/j.prostr.2016.06.451.
- [22] E. Fracchia, F.S. Gobber, and M. Rosso: Metals, 2020, vol. 10, p. 618. https://doi.org/10.3390/met10050618.
- [23] X.Y. Jiao, P.Y. Wang, Y.X. Liu, J. Wang, W.N. Liu, A.X. Wan, L.J. Shi, C.G. Wang, and S.M. Xiong: J. Mater. Res. Technol., 2023, vol. 25, pp. 1129-40. https://doi.org/10.1016/j.jmrt.2023.05.281.
- [24] A. Niklas, A. Baquedano, S. Orden, E. Noguès, M. Da Silva, and A.I. Fernández-Calvo: Key Eng. Mater., 2016, vol. 710, pp. 244-49. https://doi.org/10.4028/www.scientific.net/KEM.710.244.
- [25] J.M. Sanchez, M. Arribas, H. Galarraga, M. Garcia de Cortazar, M. Ellero, and F. Girot: Heliyon, 2023, vol. 9, p. e13005. https://doi.org/10.1016/j.heliyon.2023.e13005.
- [26] E. Cinkilic, C.D. Ridgeway, X. Yan, and A.A. Luo: Metall. Mater. Trans. A, 2019, vol. 50A, pp. 5945-56. https://doi.org/10.1007/s11661-019-05469-6.
- [27] J. Piątkowski, M. Hejne, and R. Wieszała: Arch. Mater. Sci. Eng., 2023, vol. 123, pp. 5-12. https://doi.org/10.5604/01.3001.0053.9750.
- [28] L.B. Otani, J. Soyama, G. Zepon, A. Costa e Silva, C.S. Kiminami, W.J. Botta, and C. Bolfarini: J. Phase Equilib. Diffus., 2017, vol. 38, pp. 298-304. https://doi.org/10.1007/s11669-017-0542-y.
- [29] A. Bakedano, R. González-Martínez, A. Niklas, M. Da Silva, M. Garat, and A.I. Fernández-Calvo: 71st World Foundry Congress on Advanced Sustainable Foundry, 2014.
- [30] A. Niklas, A.I. Fernández-Calvo, A. Bakedano, S. Orden, M. Da Silva, E. Nogués, and E. Roset: Metall. Ital., 2016, vol. 108, pp. 9-12.
- [31] A. Niklas, A. Bakedano, S. Orden, M. da Silva, E. Nogués, and A.I. Fernández-Calvo: Mater. Today Proc., 2015, vol. 2, pp. 4931-38. https://doi.org/10.1016/j.matpr.2015.10.059.
- [32] H. Zheng, Y. Jiang, F. Liu, and H. Zhao: J. Alloys Compd., 2024, vol. 976, p. 173167. https://doi.org/10.1016/j.jallcom.2023.173167.
- [33] Z. Yuan, Z. Guo, and S.M. Xiong: J. Mater. Sci. Technol., 2019, vol. 35, pp. 1906–16. https://doi.org/10.1016/j.jmst.2019.05.011.
- [34] H.M. Yang, Z. Guo, and S.M. Xiong: J. Mater. Process. Technol., 2020, vol. 275, p. 116377. https://doi.org/10.1016/j.jmatprotec.2019.116377.
- [35] S. Otarawanna, C.M. Gourlay, H.I. Laukli, and A.K. Dahle: Mater. Chem. Phys., 2011, vol. 130, pp. 251-58. https://doi.org/10.1016/j.matchemphys.2011.06.035.
- [36] Y. Yang, S. Huang, J. Zheng, L. Yang, X. Cheng, R. Chen, and H. Wei-Jian: Trans. Nonferr. Met. Soc. China, 2024, vol. 34, pp. 378-91. https://doi.org/10.1016/S1003-6326(23)66405-2.
- [37] Trimet-05: Trimal®-05-Die Cast Alloy for Crash-Relevant Applications, Trimet-05, 2008. https://www.trimet.eu/en/products/foundry-alloys/trimal-05. Accessed 26 July 2024.
- [38] C.M. Dinnis, J.A. Taylor, and A.K. Dahle: Scripta Mater., 2005, vol. 53, pp. 955-58. https://doi.org/10.1016/j.scriptamat.2005.06.028.
- [39] J.I. Goldstein, D.E. Newbury, J.R. Michael, N.W.M. Ritchie, J.H.J. Scott, and D.C. Joy: Scanning Electron Microscopy and X-Ray Microanalysis, 4th ed. Springer, New York, 2018. https://doi.org/10.1007/978-1-4939-6676-9.
- [40] B. Dybowski, A. Kiełbus, and Ł Poloczek: Eng. Fail. Anal., 2023, vol. 150, p. 107223. https://doi.org/10.1016/j.engfailanal.2023.107223.
- [41] Q. Han and J. Zhang: Metall. Mater. Trans. B, 2020, vol. 51B, pp. 1795-1804. https://doi.org/10.1007/s11663-020-01858-0.
- [42] H. Yang, S. Ji, and Z. Fan: Mater. Des., 2015, vol. 85, pp. 823-32. https://doi.org/10.1016/j.matdes.2015.07.074.
- [43] X. Dong, X. Zhu, and S. Ji: J. Mater. Process. Technol., 2019, vol. 266, pp. 105-13. https://doi.org/10.1016/j.jmatprotec.2018.10.030.
- [44] X.Y. Jiao, C.F. Liu, Z.P. Guo, H. Nishat, G.D. Tong, S.L. Ma, Y. Bi, Y.F. Zhang, S. Wiesner, and S.M. Xiong: J. Alloys Compd., 2021, vol. 862, p. 158580. https://doi.org/10.1016/j.jallcom.2020.158580.
- [45] S. Otarawanna, C.M. Gourlay, H.I. Laukli, and A.K. Dahle: Metall. Mater. Trans. A, 2009, vol. 40A, pp. 1645-59. https://doi.org/10.1007/s11661-009-9841-1.
- [46] S. Ji, Y. Wang, D. Watson, and Z. Fan: Metall. Mater. Trans. A, 2013, vol. 44A, pp. 3185-97. https://doi.org/10.1007/s11661-013-1663-5.
- [47] S. Ji, W. Yang, F. Gao, D. Watson, and Z. Fan: Mater. Sci. Eng. A, 2013, vol. 564, pp. 130-39. https://doi.org/10.1016/j.msea.2012.11.095.
- [48] H. Becker, T. Bergh, P.E. Vullum, A. Leineweber, and Y. Li: Materialia, 2019, vol. 5, p. 100198. https://doi.org/10.1016/j.mtla.2018.100198.
- [49] Α.Κ.Μ.Α. Ahamed and H. Kato: Mater. Trans., 2008, vol. 49, pp. 1621-28. https://doi.org/10.2320/matertrans.F-MRA2008814.
- [50] H. Kato, T. Suzuki, Y. Annou, and K. Kageyama: Mater. Trans., 2004, vol. 45, pp. 2403-09. https://doi.org/10.2320/matertrans.45.2403.
- [51] Z.W. Chen: Mater. Sci. Eng. A, 2003, vol. 348, pp. 145-53. https://doi.org/10.1016/S0921-5093(02)00747-5.
- [52] S. Midson: Die Casting Defects, North American Die Casting Association. https://pdfcoffee.com/nadca-overview-of-defets-in-die-casting-pdf-free.html. Accessed 4 Sep 2024.
9. Copyright:
- This material is a paper by "BISWAJIT DALAI, SIMON JONSSON, MANEL DA SILVA, LIANG YU, and JÖRGEN KAJBERG". Based on "Inhomogeneous Skin Formation and Its Effect on the Tensile Behavior of a High Pressure Die Cast Recycled Secondary AlSi10MnMg(Fe) Alloy".
- Source of the paper: https://doi.org/10.1007/s11661-024-07631-1
This material is summarized based on the above paper, and unauthorized use for commercial purposes is prohibited.
Copyright © 2025 CASTMAN. All rights reserved.