Reference : https://diecasting.com/blog/how-to-avoid-die-casting-defects/
The production of die-castings includes a number of steps, any of which can result in a defective casting if not properly executed. Since repairing bad castings can be expensive, it’s important to avoid defect occurrences if possible. We’ll look at some common to areas of die casting defects — including wall thickness and die surface porosity — their causes, and how to avoid them.
You Can’t Correct and Control Defects if You Can’t Measure and Report Them
Without a scrap reporting system in place, it’ll be difficult to manage the quality aspects of your production line. An effective reporting system makes information available to everybody involved in the production process on a daily basis. The daily scrap report should categorize scrap for easy tracking by:
- defect type
- part number
- die
- shift
- operator
- machine
The report for the previous day’s activities should be available first thing every morning. Your scrap reporting system should capture long-term trends, and, ideally, it should predict customer rejects based on the recent scrap activity. Pareto charts are effective ways of illustrating reject activity. The report should also capture the defects that aren’t identified until the parts have made their way downstream — and you’ll want to develop a system to track these defects to the shift and machinery that produced them. Everything should be included on the scrap report, including warm-up shots and scrap returned to the furnace at the point of machine.
Don’t Ignore the Importance of an Effective Rating System
The die casting manufacturing process is complex, so it’s imperative your reporting system be continuous and provide real-time feedback to help you control defects. Now that you’re armed with accurate, real-time information, how will you decide which of the defects require immediate attention? That’s where a good rating system comes in handy.

An effective rating system will help you understand if you’re successfully reducing defects or if the problem is worsening. Importantly, it will let you know if changes you’ve implemented to reduce defects are having the desired effect. The bottom line is you want to know when corrections are necessary, and you want to know this before the defect levels reach crisis proportions.
Surface quality and porosity are two major die-casting defects, and both require judgments to be made about their severity. Let’s use porosity as an example to see what a rating system might look like.
Let’s rank a porosity defect on a worst to best scale of one to five. You could conduct a simple study as follows:
- Taking six sets of five sequential casting samples, at intervals of roughly one-half to two hours.
- Then rating each casting and averaging the total to give you the average quality level. You can compare these results with the outcomes of similar studies to understand the state of your process.
There’s no doubt defect corrections have to start with an effective scrap reporting system. The age-old adage “you can’t improve it if you can’t measure it” definitely applies to your die-castings.
What Causes Die Casting Defects?
Surface-area defects are a major concern with die casting that can be caused by a number of factors related directly to the casting itself.
Wall Thickness
Different wall thicknesses deliver different results. For example, a thin wall will cause the alloy flow to freeze and facilitate faster cold flow, or deformation. Minimum wall thicknesses for aluminum and magnesium are typically about 1.5 to 2.5 millimeters, while the minimum wall thickness for zinc is about 1.0 millimeter.

For example, there is a noticeable change in the fill time required by different wall thicknesses. A wall thickness of between 2.0 and 1.5 millimeters requires a 25 percent reduction in fill time, while a thickness of 3.5 to 3.0 millimeters requires a 12 percent reduction. So a small variation in fill time for a thin wall casting of 2.0 millimeters has a noticeable effect with no surface defects, while the same fill time for a thicker wall — let’s say 5.0 millimeters — has a less-noticeable effect.
Die temperature is much more critical in a thin wall casting because the reduced mass of the part won’t provide enough heat for the die. That’s not good because the very basis for a sound thin wall casting is very fast fill time in a hot die and high gate velocity.
Fill Time
The fill time begins when the alloy first arrives at the gate and ends after the cavity is filled with metal. Rough guidelines for maximum fill times that are applicable to most castings:
Alloy | Thin Wall <2 millimeters | Average Wall >2 millimeters |
---|---|---|
Aluminum — approximately 2 kg | .09 seconds | .1 seconds |
Zinc — approximately 1.4 kilograms | .03 seconds | .05 seconds |
Magnesium — approximately 1 kilogram | .02 seconds | .03 seconds |
Predicting the fill time is achieved with the PQ2 calculation, which predicts changes in fill times and gate velocities because of changing any of the following:
- Gate area
- Plunger size
- Machine hydraulic pressure
- Plunger speed setting
It is really the only way to predict fill time. The only other way is the more expensive “guess” method, which is not recommended.
Metal Flow Pattern
The metal flow pattern is the key in gate design, which is a function of design rules espoused by the North American Die Casting Association:
- Employ the PQ2 calculation to size the gate and plunger — be sure to use the correct gate velocity, fill time and cavity pressure criteria
- Divide the casting into zones
- Proportion the gates so each zone is filled at the same time
- Flow across the casting
- Try to avoid mixing flows
Die Temperature
Low die temperature cools the fluid metal stream, affecting surface defects by increasing the amount of solidified metal in the stream. If the percent amount of solid metal is high enough, the stream becomes stiff and solid and doesn’t mix effectively, causing the flow to form cold-flow “wrinkles.” You can compensate for a cold die with a shorter fill time, which means increasing the plunger speed. The takeaway is you can exchange plunger speed for die temperature.
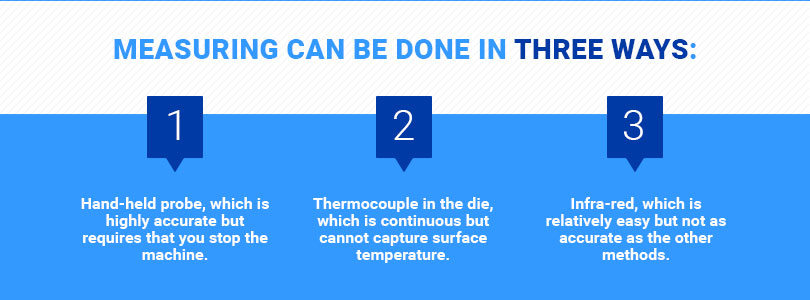
Because die temperature is so important to minimizing surface defects, measuring it should be a regular part of the production process. In general, measuring can be done three ways:
- Hand-held probe, which is highly accurate but requires that you stop the machine
- Thermocouple in the die, which is continuous but cannot capture surface temperature
- Infra-red, which is relatively easy but not as accurate as the other methods
Here are approximate temperature ranges that will ensure good surface finishes:
Metal | Good Finish | Average Finish |
---|---|---|
Aluminum | 250 - 315° C | 190 - 315° C |
Zinc | 230 - 290° C | 190 - 290° C |
Cycle time is another key aspect of die temperature. The temperature is directly influenced by the number of pounds of metal fed through the die in the previous one or two hours. Maintaining a consistent cycle time is one of the most important things you can do to control die casting defects.
Laminations
Laminations are usually the result of metal flow conditions in which one flow sits on the top of another and they are both too cold to mix. The way the metal flows inside the casting, which may be influenced by the casting’s geometry, may cause this layering effect. If geometry were the problem, changing the flow pattern via gate modifications would be very difficult. Instead, consider these:
- Decrease the fill time
- Increase the die temperature
- Increase the metal temperature
Of these options, a change to the fill time is generally most effective. Laminations often occur when metal is splashed into the cavity while the plunger operates at minimal speed. The remedy is to increase the length of fast shot, moving the switch closer to the pour hole. Die flexing can also cause laminations, caused by flexing of the die, which can result in an additional layer of metal outside the original casting skin. The fix here added support to the die.
Issues with Oxide Skins
Oxide skins are also known to cause lamination. These skins are generated in the holding furnace, or they may be created during injection in the cold chamber. They’ll be located randomly and are typically very small — 2 millimeters — and can be mistaken for porosity when dislodged by machining or sanding. There are a number of corrective actions you can take if oxide skins are the problem:
- Proper skimming of the holding pot
- Minimizing the amount of time in the cold chamber
- Filtering
- Proper fluxing and degassing
Another cause of laminations: Flash in the casting. This occurs when the die is dirty and the flash residue left on the die falls into the cavity as the die closes. The flash will not be remelted by the incoming metal, and therefore will not mix with the rest of the casting. The molten metal may in fact be barely able to adhere to the flash, making the flash a weak spot and causing cracks in the casting and layers on or near the surface. Corrective actions to reduce flash include:
- Keep the die clean in between shots
- Maintain a regular die maintenance and repair schedule
- Implement good process designs to ensure proper metal selection
- Maintain proper intensifier settings
- Keep dies expansion even by engineering the die cooling
Porosity
Porosity is another major die casting problem, and there are two types:
- Shrinkage
- Gas
It’s important to determine the type of porosity before trying to fix it, because each requires a completely different approach, although they can look similar. To be sure you’ve accurately identified the type of porosity defect you’re dealing with, use five- to ten-power magnification.
We’ll focus on gas porosity, since it’s the bigger problem of the two.
Gas porosity is one of the most significant problems in die casting. High gas content eliminates heat-treating or welding steps and makes the strength of the casting unpredictable. Here are three major sources of gas porosity in die-castings:
- Trapped air
- Steam
- Gas from lubricant
Trapped Air
Turbulence may allow air bubbles to be trapped in the metal. The problem is that the bubbles remain trapped when the casting solidifies. Air can be trapped as follows:
- Shot sleeve
- Runners
If Air Becomes Trapped in the Shot Sleeve
Your first step should be to maintain the same pour rate and shot delay time. This is particularly important at times when the fill is below 50%, because at this percentage of fill a wave may be generated by the act of pouring. The
air wave may travel from the parting line to the shot to and back again. When the plunger tip starts to move, its speed and acceleration are pre-designed to prevent trapped air bubbles.
If the wave collides as it moves forward, extra splashing is generated, capturing some bubbles. However, if the tip starts to move forward after the wave has been redirected away, the tip follows the wave, providing your best opportunity to minimize trapped air. A timer that establishes the time delay between end of pour and commencement of the shot will influence when the tip starts to move forward in relationship to the wave.
The acceleration of the plunger to slow shot speed is another contributor to trapped air. The plunger’s rate of acceleration should be slow enough to keep the metal from tumbling over, or surfing, but fast enough to stop air from getting trapped between the wave that’s generated and those waves that are redirected away from the die.
The acceleration rate will vary based on the percent of fill and length of the sleeve. The typical range is between two and less than three inches per second, per inch of travel.

How to Reduce Air in the Shot Sleeve
If you need to reduce air trapped in the shot sleeve, adjust the following settings until you have the problem resolved. Each of these settings alone may not seem significant, but there are interactions between them, and we recommend that you be as consistent as possible once you find a combination of settings that works for you:
- Fast shot starting point
- Rate of pour
- Shot delay time before the shot
- Speed of pour hole
- Pour hole to slow shot changeover speed
- Acceleration of slow shot
- Speed of slow shot
If Air Becomes Trapped in the Runners
Sharp corners and area changes in runner systems’ metal flow path can cause air to be trapped. Generally, the runner has smooth, rounded corners and is always decreasing in area from plunger to gate. As the metal starts entering the cavity, it will typically flow at high-velocity, extremely turbulent flow conditions, trapping some of the air as gas porosity.
A remedy is to design the flow pattern so that the metal tends to direct the air through the cavity and to the vents. A lot of the air in the shot sleeve and the cavity can be directed out of the vents or vacuum system, but the vents need to be sized correctly, extend to the edge of the die, and be cleaned routinely to avoid flash and lubricant buildup.
Working With a Pro to Avoid Die Casting Defects
We’ve just scratched the surface of die defects, their causes and the impact on castings. There’s a lot more to know, and it pays to work with a company that’s an expert in all aspects of die casting production and trouble shooting.
Castman has been helping our customers produce the best products they want, and contact Castman to find out how we can help.
다이 캐스팅 결함을 방지하는 방법
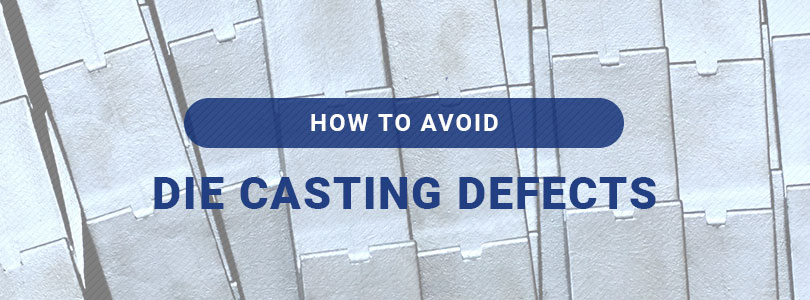
이동 :
- 효과적인 평가 시스템의 중요성
- 다이 캐스팅 결함의 원인은 무엇입니까?
- 샷 슬리브에 공기가 갇히는 경우
- 샷 슬리브의 공기를 줄이는 방법
- 공기가 런너에 갇히면
- 전문가와 협력하여 다이 캐스팅 결함 방지
다이캐스팅 생산에는 여러 단계가 포함되며,이 중 하나라도 제대로 실행되지 않으면 주조 결함이 발생할 수 있습니다. 불량 주물을 수리하는 것은 비용이 많이 들 수 있으므로 가능하면 결함 발생을 피하는 것이 중요합니다. 벽 두께 및 다이 표면 다공성을 포함하여 다이 캐스팅 결함 영역에 공통적인 몇 가지 원인과 이를 방지하는 방법을 살펴 보겠습니다.
결함을 측정하고보고 할 수 없으면 결함을 수정하고 제어 할 수 없습니다.
스크랩보고 시스템이 없으면 생산 라인의 품질 측면을 관리하기가 어렵습니다. 효과적인 보고 시스템은 생산 프로세스에 관련된 모든 사람이 매일 정보를 사용할 수 있도록 합니다. 일일 스크랩 보고서는 쉽게 추적 할 수 있도록 스크랩을 다음과 같이 분류해야 합니다.
- 결함 유형
- 부품 번호
- 다이
- 시프트
- 운영자
- 기계
전날의 활동에 대한 보고서는 매일 아침 가장 먼저 사용할 수 있어야합니다. 스크랩보고 시스템은 장기적인 추세를 포착해야하며, 이상적으로는 최근 스크랩 활동을 기반으로 고객 거부를 예측해야합니다. 파레토 차트는 거부 활동을 설명하는 효과적인 방법입니다. 보고서는 또한 부품이 다운 스트림으로 이동할 때까지 식별되지 않은 결함을 캡처해야합니다. 이러한 결함을 생산한 담당 및 기계에 대해 이러한 결함을 추적하는 시스템을 개발해야 합니다. 예열 샷과 기계 지점에서 용광로로 반환되는 스크랩을 포함하여 모든 것이 스크랩 보고서에 포함되어야 합니다.
효과적인 평가 시스템의 중요성을 무시하지 마십시오
다이 캐스팅 제조 프로세스는 복잡하므로, 보고 시스템이 지속적으로 유지되고 실시간 피드백을 제공하여 결함을 제어하는 것이 중요합니다. 이제 정확한 실시간 정보로 무장 했으므로 즉각적인 주의가 필요한 결함을 어떻게 결정 하시겠습니까? 좋은 평가 시스템이 유용합니다.

효과적인 평가 시스템은 결함을 성공적으로 줄이고 문제가 악화되고 있는지 이해하는 데 도움이됩니다. 중요한 것은 결함을 줄이기 위해 구현한 변경 사항이 원하는 효과가 있는지 여부를 알려줍니다. 결론은 언제 수정이 필요한지 알고 싶고 결함 수준이 위기 비율에 도달하기 전에 이를 알고 싶어한다는 것입니다.
표면 품질과 다공성은 두 가지 주요 다이캐스팅 결함이며, 둘 다 심각도에 대한 판단이 필요합니다. 등급 시스템이 어떻게 생겼는지 보기 위해 다공성을 예로 사용하겠습니다.
다공성 결함의 등급을 1 ~ 5의 최악에서 최고 등급으로 분류 해 보겠습니다. 다음과 같이 간단한 연구를 수행 할 수 있습니다.
- 대략 1.5 ~ 2 시간 간격으로 5 개의 연속 주조 샘플 6 세트를 채취합니다.
- 그런 다음 각 캐스팅을 평가하고 총계를 평균하여 평균 품질 수준을 제공합니다. 이러한 결과를 유사한 연구의 결과와 비교하여 프로세스 상태를 이해할 수 있습니다.
결함 수정은 효과적인 스크랩보고 시스템에서 시작해야한다는 데 의심의 여지가 없습니다. "측정 할 수 없으면 개선 할 수 없습니다"라는 오래된 격언이 다이캐스팅에 확실히 적용됩니다.
다이 캐스팅 결함의 원인은 무엇입니까?
표면적 결함은 주조 자체와 직접 관련된 여러 요인으로 인해 발생할 수있는 다이캐스팅의 주요 관심사입니다.
벽 두께
벽 두께가 다르면 결과도 다릅니다. 예를 들어, 얇은 벽은 합금 흐름을 동결시키고 더 빠른 저온 흐름 또는 변형을 촉진합니다. 알루미늄과 마그네슘의 최소 벽 두께는 일반적으로 약 1.5 ~ 2.5mm이고 아연의 최소 벽 두께는 약 1.0mm입니다.

예를 들어, 벽 두께에 따라 필요한 충전 시간이 눈에 띄게 변경됩니다. 벽 두께가 2.0 ~ 1.5mm이면 충전 시간이 25 % 감소해야하며 두께가 3.5 ~ 3.0mm이면 12 % 감소해야합니다. 따라서 2.0mm의 얇은 벽 주조에 대한 충전 시간의 작은 변화는 표면 결함없이 눈에 띄는 효과를 가지며, 더 두꺼운 벽 (예 : 5.0mm)에 대해 동일한 충전 시간은 덜 눈에 띄는 효과를 갖습니다.
부품의 감소된 질량이 다이에 충분한 열을 제공하지 않기 때문에 얇은 벽 주조에서는 다이 온도가 훨씬 더 중요합니다. 건전한 얇은 벽 주조의 기본은 핫 다이에서 매우 빠른 충전 시간과 높은 게이트 속도이기 때문에 좋지 않습니다.
충전 시간
충전 시간은 합금이 게이트에 처음 도착할 때 시작되고 캐비티가 금속으로 채워진 후에 끝납니다. 대부분의 주물에 적용되는 최대 충전 시간에 대한 대략적인 지침 :
합금 | 얇은 벽 <2mm | 평균 벽 > 2mm |
---|---|---|
알루미늄 — 약 2kg | .09 초 | .1 초 |
아연 — 약 1.4 킬로그램 | .03 초 | .05 초 |
마그네슘 — 약 1kg | .02 초 | .03 초 |
충전 시간을 예측하는 것은 PQ2 계산을 통해 이루어지며, 이는 다음 중 하나를 변경하기 때문에 충전 시간과 게이트 속도의 변화를 예측합니다.
- 게이트 영역
- 플런저 크기
- 기계 유압
- 플런저 속도 설정
충전 시간을 예측하는 유일한 방법입니다. 유일한 다른 방법은 권장되지 않는 더 비싼 "추측"방법입니다.
금속 흐름 패턴
금속 흐름 패턴은 북미 다이캐스팅 협회 (North American Die Casting Association)에서 채택한 설계 규칙의 기능인 게이트 설계의 핵심입니다.
- PQ2 계산을 사용하여 게이트 및 플런저의 크기를 지정합니다. 올바른 게이트 속도, 충전 시간 및 캐비티 압력 기준을 사용해야합니다.
- 주조물을 구역으로 분할
- 각 구역이 동시에 채워지도록 게이트 비율을 지정합니다.
- 캐스팅을 가로 지르는 흐름
- 혼합 흐름을 피하십시오
다이 온도
낮은 다이 온도는 유체 금속 흐름을 냉각시켜 흐름에서 고체화된 금속의 양을 증가시켜 표면 결함에 영향을 줍니다. 고체 금속의 비율이 충분히 높으면 흐름이 뻣뻣하고 단단해지며 효과적으로 혼합되지 않아 흐름이 차가운 흐름 "주름"을 형성하게 됩니다. 더 짧은 충전 시간으로 콜드 다이를 보정 할 수 있습니다. 즉, 플런저 속도가 증가합니다. 요점은 플런저 속도를 다이 온도로 바꿀 수 있다는 것입니다.
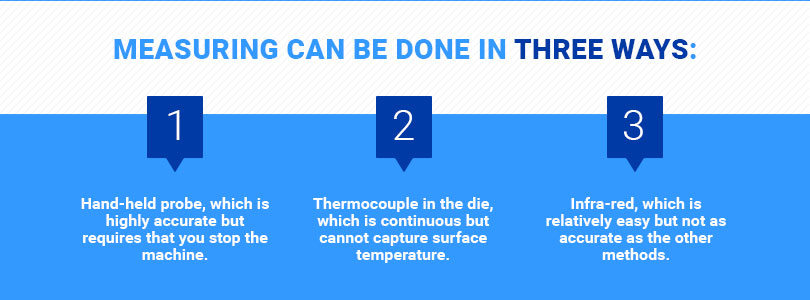
다이 온도는 표면 결함을 최소화하는데 매우 중요하므로 생산 공정에서 이를 측정하는 것이 규칙적인 부분이어야 합니다. 일반적으로 측정은 세 가지 방법으로 수행 할 수 있습니다.
- 매우 정확하지만 기계를 정지해야하는 휴대용 프로브
- 연속적이지만 표면 온도를 캡처 할 수없는 다이의 열전대
- 상대적으로 쉽지만 다른 방법만큼 정확하지는 않은 적외선
다음은 우수한 표면 마감을 보장하는 대략적인 온도 범위입니다.
금속 | 좋은 마무리 | 평균 마무리 |
---|---|---|
알류미늄 | 250-315 ° C | 190-315 ° C |
아연 | 230 ~ 290 ° C | 190-290 ° C |
사이클 타임은 다이 온도의 또 다른 핵심 요소입니다. 온도는 이전 1 ~ 2 시간 동안 다이를 통해 공급 된 금속 파운드 수에 직접 영향을받습니다. 일관된 사이클 시간을 유지하는 것은 다이 캐스팅 결함을 제어하기 위해 수행 할 수있는 가장 중요한 작업 중 하나입니다.
라미네이션
라미네이션은 일반적으로 한 흐름이 다른 흐름의 위에 놓여 있고 둘 다 혼합하기에 너무 차가워지는 금속 흐름 조건의 결과입니다. 주물 내부에서 금속이 흐르는 방식은 주물의 형상에 영향을받을 수 있으므로 이러한 레이어링 효과를 유발할 수 있습니다. 지오메트리가 문제라면 게이트 수정을 통해 흐름 패턴을 변경하는 것은 매우 어려울 것입니다. 대신 다음을 고려하십시오.
- 충전 시간 줄이기
- 다이 온도 높이기
- 금속 온도 높이기
이러한 옵션 중 충전 시간을 변경하는 것이 일반적으로 가장 효과적입니다. 플런저가 최소 속도로 작동하는 동안 금속이 캐비티에 튀어 나올 때 라미네이션이 종종 발생합니다. 해결책은 빠른 샷의 길이를 늘리고 스위치를 타설 구멍에 더 가깝게 이동하는 것입니다. 다이 구부림은 다이 구부러짐으로 인해 라미네이션을 유발할 수 있으며, 이로 인해 원래 주조 스킨 외부에 추가 금속 층이 생길 수 있습니다. 여기의 수정은 다이에 대한 지원을 추가했습니다.
산화물 스킨 문제
산화물 스킨은 라미네이션을 유발하는 것으로도 알려져 있습니다. 이러한 스킨은 홀딩로에서 생성되거나 콜드 챔버에서 주입하는 동안 생성 될 수 있습니다. 이들은 무작위로 배치되며 일반적으로 매우 작으며 (2mm) 기계 가공 또는 샌딩으로 제거 할 때 다공성으로 오인될 수 있습니다. 산화 피막이 문제인 경우 취할 수 있는 여러 수정 조치가 있습니다.
- 홀딩 포트의 적절한 스키밍
- 콜드 챔버 시간 최소화
- 필터링
- 적절한 플럭싱 및 탈기
라미네이션의 또 다른 원인 : 주물의 플래시. 이것은 다이가 더러워지고 다이가 닫힐 때 다이에 남아있는 플래시 잔류 물이 캐비티로 떨어질 때 발생합니다. 플래시는 들어오는 금속에 의해 재 용해되지 않으므로 나머지 주조물과 혼합되지 않습니다. 용융된 금속은 실제로 플래시에 거의 부착되지 않아 플래시가 약한 지점이 되어 주물과 표면 위 또는 근처의 층에 균열을 일으킬 수 있습니다. 플래시를 줄이기 위한 수정 조치는 다음과 같습니다.
- 샷 사이에 다이를 깨끗하게 유지하십시오.
- 정기적인 다이 유지 관리 및 수리 일정 유지
- 적절한 금속 선택을 보장하기 위해 우수한 공정 설계 구현
- 적절한 증압기 설정 유지
- 금형 냉각을 설계하여 금형 확장 유지
다공성
다공성은 또 다른 주요 다이 캐스팅 문제이며 두 가지 유형이 있습니다.
- 수축
- 가스
유사하게 보일 수 있지만 각각 완전히 다른 접근 방식이 필요하기 때문에이를 고치기 전에 다공성 유형을 결정하는 것이 중요합니다. 다루고 있는 다공성 결함 유형을 정확하게 식별하려면 5 배에서 10 배 배율을 사용하십시오.
가스 다공성은 둘 중 더 큰 문제이기 때문에 초점을 맞출 것입니다.
가스 다공성은 다이캐스팅에서 가장 중요한 문제 중 하나입니다. 높은 가스 함량은 열처리 또는 용접 단계를 제거하고 주조 강도를 예측할 수 없게 만듭니다. 다이캐스팅에서 가스 다공성의 세 가지 주요 원인은 다음과 같습니다.
- 갇힌 공기
- 증기
- 윤활유 가스
갇힌 공기
난류로 인해 금속에 기포가 갇힐 수 있습니다. 문제는 주물이 응고될 때 기포가 갇혀 있다는 것입니다. 공기는 다음과 같이 갇힐 수 있습니다.
- 샷 슬리브
- 런너
샷 슬리브에 공기가 갇히는 경우
첫 번째 단계는 동일한 주입 속도와 샷 지연 시간을 유지하는 것입니다. 이것은 채우기가 50 % 미만인 경우에 특히 중요합니다.이 비율에서는 붓는 행위에 의해 그만큼 물결이 생성 될 수 있기 때문입니다.
파팅 라인에서 샷으로 그리고 다시 뒤로 공기 파동이 이동할 수 있습니다. 플런저 팁이 움직이기 시작하면 기포가 갇히지 않도록 속도와 가속도가 미리 설계되어 있습니다.
파도가 앞으로 나아가면서 충돌하면 추가 튀는 현상이 발생하여 일부 거품이 포착됩니다. 그러나 파도가 방향을 전환 한 후 팁이 앞으로 움직이기 시작하면 팁이 파도를 따라가므로 갇힌 공기를 최소화 할 수있는 최상의 기회를 제공합니다. 타설 종료와 샷 시작 사이의 시간 지연을 설정하는 타이머는 팁이 웨이브와 관련하여 앞으로 이동하기 시작할 때 영향을줍니다.
플런저가 느린 샷 속도로 가속하는 것은 갇힌 공기의 또 다른 원인입니다. 플런저의 가속 속도는 금속이 넘어 지거나 서핑하지 않도록 충분히 느려 야하지만 생성 된 파도와 다이에서 멀어지는 파도 사이에 공기가 갇히지 않도록 충분히 빨라야합니다.
가속 률은 충전 비율과 슬리브 길이에 따라 달라집니다. 일반적인 범위는 이동 1 인치당 초당 2 ~ 3 인치입니다.

샷 슬리브의 공기를 줄이는 방법
샷 슬리브에 갇힌 공기를 줄이려면 문제가 해결 될 때까지 다음 설정을 조정하십시오. 이러한 각 설정만으로는 중요하지 않은 것처럼 보일 수 있지만 상호 작용이 있으므로 적합한 설정 조합을 찾으면 가능한 한 일관성을 유지하는 것이 좋습니다.
- 빠른 샷 시작점
- 붓는 비율
- 촬영 전 촬영 지연 시간
- 주입 구멍의 속도
- 샷 전환 속도를 늦추기 위해 구멍을 붓습니다.
- 슬로우 샷 가속
- 슬로우 샷의 속도
공기가 런너에 갇히면
런너 시스템의 금속 흐름 경로의 날카로운 모서리와 면적 변화로 인해 공기가 갇힐 수 있습니다. 일반적으로 런너는 부드럽고 둥근 모서리를 가지며 플런저에서 게이트까지 면적이 항상 감소합니다. 금속이 캐비티에 들어가기 시작하면 일반적으로 고속의 극도로 난류 상태에서 유동하여 일부 공기를 가스 다공성으로 가두어 둡니다.
해결책은 금속이 공기를 캐비티를 통해 통풍구로 보내는 경향이 있도록 흐름 패턴을 설계하는 것입니다. 샷 슬리브와 캐비티에 있는 많은 공기는 벤트 또는 진공 시스템에서 배출 될 수 있지만 벤트는 정확한 크기를 정하고 다이의 가장자리까지 확장되어야 하며 플래시 및 윤활유 축적을 방지하기 위해 정기적으로 청소해야 합니다. .
전문가와 협력하여 다이 캐스팅 결함 방지
우리는 다이 결함의 표면, 그 원인 및 주물에 미치는 영향을 살펴 보았습니다. 알아야 할 것이 더 많으며 다이 캐스팅 생산 및 문제 해결의 모든 측면에서 전문가인 회사와 협력하는 것이 좋습니다. 캐스트맨은 고객이 원하는 최상의 제품을 생산할 수 있도록 지원해 왔으므로 당사에 문의 하여 어떻게 도와 드릴 수 있는지 알아보십시오.