This introduction paper is based on the paper "[High-Temperature Mechanical Properties of NaCl-Na2CO3 Salt-Mixture Removable Cores for Aluminum Die-Casting]" published by "[The Japan Institute of Metals and Materials]".
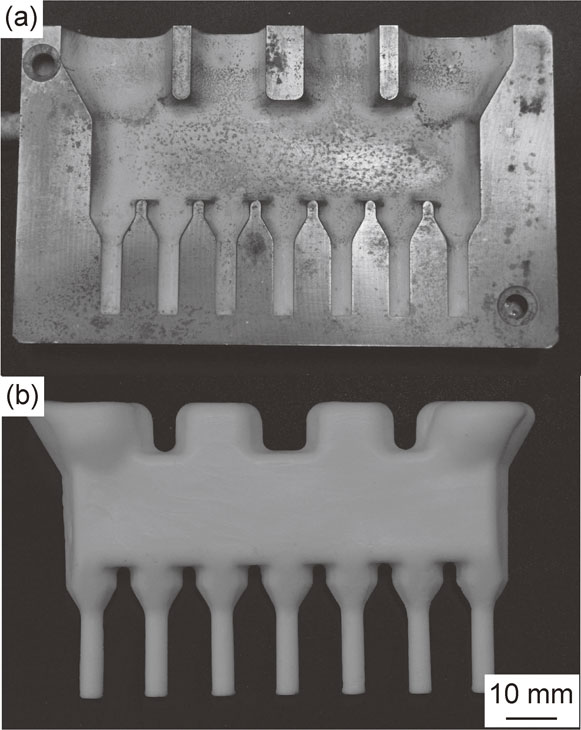
1. Overview:
- Title: High-Temperature Mechanical Properties of NaCl-Na2CO3 Salt-Mixture Removable Cores for Aluminum Die-Casting
- Author: Katsunari Oikawa, Kazuhiro Sakakibara, Youji Yamada and Koichi Anzai
- Year of publication: 2019
- Journal/academic society of publication: Materials Transactions (The Japan Institute of Metals and Materials)
- Keywords: salt mixture, removable core, mechanical property, compression test, Vickers hardness, lamellar structure, high temperature
2. Abstract:
The NaCl-Na2CO3 salt mixture is proposed as a water-soluble core material for aluminum die-casting processes. The mechanical properties and microstructures of NaCl-Na2CO3 samples prepared by gravity casting were investigated. The salt mixtures had superior properties compared to those of the pure salts. Plastic deformation occurred during compression tests at high temperatures because the eutectic region changed from lamellar to granular. Salt mixtures with NaCl primary phase and eutectic regions were found to be the most suitable core material.
3. Introduction:
Die-cast aluminum components are integral to the automotive industry due to their high productivity and excellent mechanical properties. To enhance component performance and reduce costs, complex shapes and parts with internal cavities are often required, necessitating the use of cores. While metal or sand cores are common, water-soluble salt cores offer an advantage due to their easy removal from inaccessible cavities. Salt cores formed by high-pressure compaction of NaCl powder are frequently used but are generally limited to gravity or low-pressure casting due to their insufficient strength.
Consequently, various high-strength salt cores have been developed for high-pressure die-casting. Previous research includes salt-ceramic composites and NaCl or KCl cores formed by high-pressure squeezing with alkali silicate. The authors' research group has also contributed by developing high-strength salt-mixture cores, such as the KCl–NaCl–K2CO3-Na2CO3 system and the KBr-NaBr-K2CO3-Na2CO3 system, which showed good removability. However, the mechanical properties of these earlier salt mixtures were primarily evaluated at room temperature.
Understanding the high-temperature mechanical properties of salt mixtures is crucial for casting design, as cores are exposed to high-speed molten aluminum alloy during the die-casting process. While the high-temperature behavior of pure NaCl has been studied, indicating plastic deformation above half its melting point, the mechanical properties of salt mixtures at elevated temperatures have not been well-documented. This study aims to fill that gap by investigating the high-temperature mechanical properties of cast NaCl-Na2CO3 salt-mixture cores.
4. Summary of the study:
Background of the research topic:
The research addresses the need for robust water-soluble core materials for aluminum die-casting, particularly for high-pressure processes. Existing NaCl powder cores lack sufficient strength, and the performance of salt cores at high temperatures, encountered during melt interaction, is a critical design consideration that has not been adequately explored for salt mixtures.
Status of previous research:
Previous efforts to develop high-strength salt cores include salt-ceramic composites and pressure-squeezed salt cores. The authors' group had developed multi-component salt mixtures with good room-temperature properties. However, a knowledge gap existed regarding the mechanical behavior of these salt mixtures at the elevated temperatures experienced during die-casting. Studies on pure NaCl indicated a brittle-to-ductile transition at high temperatures, but data on salt mixtures was lacking.
Purpose of the study:
The primary purpose of this study was to investigate the high-temperature mechanical properties of cast salt-mixture cores based on the NaCl-Na2CO3 system. This investigation aimed to provide essential data for the design and application of these cores in aluminum die-casting processes, particularly considering their exposure to molten metal.
Core study:
The core of the study involved preparing NaCl-Na2CO3 salt mixtures with varying compositions by gravity casting. These samples were then subjected to compression tests at a range of temperatures (room temperature to 250°C) to evaluate their mechanical properties, including maximum stress and fracture strain. Micro Vickers hardness measurements were performed at room temperature. Furthermore, the microstructures of the samples, both as-cast and after high-temperature compression, were analyzed using scanning electron microscopy (SEM) to understand the deformation mechanisms, with a focus on changes within the eutectic structure.
5. Research Methodology
Research Design:
The research was designed to evaluate the high-temperature mechanical performance of NaCl-Na2CO3 salt mixtures. Various compositions, including eutectic and off-eutectic, were prepared via gravity casting into a preheated steel mold. Cylindrical samples were then subjected to compression tests across a temperature spectrum. Microstructural analysis was employed to correlate the observed mechanical behavior with structural features and their changes under thermal and mechanical loads.
Data Collection and Analysis Methods:
- Sample Preparation: Salt mixtures were created by melting high-purity NaCl (99.5%) and Na2CO3 (99.5%) in an electric furnace and gravity casting them. The melting temperature was 10°C above the liquidus temperature for each composition. Seven distinct compositions were prepared, as detailed in Table 1.
- Mechanical Testing:
- Compression Tests: Conducted on cylindrical samples (5 mm diameter, 12 mm high) at temperatures ranging from room temperature to 250°C in air, using a cross-head speed of 5 mm/s. True stress-true strain (σ-ε) curves were recorded (Fig. 4). From these curves, maximum stress (σmax) and fracture strain (εf) were determined (Fig. 5).
- Vickers Hardness: Measured on the as-cast sample surfaces at room temperature using a 4.9 N load applied for 30 seconds. Results are presented in Fig. 6.
- Microstructural Analysis:
- SEM Analysis: Scanning electron microscopy (SEM) was used to examine the microstructures of as-cast samples and samples after compression to a strain of 0.15 or 0.2 at 250°C (Figs. 8, 9, 10).
- Effect of Heat Treatment: To distinguish between the effects of temperature and compression, a 6CO3 sample was annealed at 250°C for 1 hour, and its microstructure was compared to as-cast and compressed samples (Fig. 7).
- Surface Preparation: Samples for microstructural observation were polished using grade #4000 SiC paper and then etched with methanol (99.8%).
Research Topics and Scope:
- Materials: The study focused on NaCl-Na2CO3 salt mixtures. Compositions varied, with Na2CO3 mole fractions ranging from 0.2 to 1.0. This included the eutectic composition (ECO3, with 0.454 mole fraction Na2CO3), NaCl-rich compositions (2CO3), Na2CO3-rich compositions (6CO3, 8CO3, 9CO3), and pure Na2CO3 (see Table 1).
- Properties Investigated:
- High-temperature mechanical behavior under compression, specifically true stress-strain response, maximum stress, and fracture strain.
- Room temperature Vickers hardness of the constituent phases (primary NaCl, primary Na2CO3, eutectic).
- Microstructural characterization and evolution, particularly the transformation of the eutectic structure under high-temperature compression.
- Temperature Range: Compression tests were performed from room temperature up to 250°C.
6. Key Results:
Key Results:
- Mechanical Properties (summarized from Fig. 4 and Fig. 5):
- At room temperature, the salt mixtures generally exhibited brittle fracture. However, at elevated temperatures, they showed plastic deformation.
- Sample 2CO3, which has a primary NaCl phase, demonstrated improved ductility at temperatures above 50°C. Other mixtures (ECO3, 6CO3, 8CO3, 9CO3) showed enhanced ductility above 150°C.
- The maximum stress (σmax) for 2CO3 and ECO3 samples was observed at 50°C. For samples 6CO3, 8CO3, and 9CO3, σmax was generally measured above 150°C, accompanied by an increase in fracture strain (εf).
- Pure Na2CO3 samples exhibited very low σmax and εf.
- Overall, the salt mixtures displayed significantly higher maximum stress and fracture strain compared to the pure constituent salts (NaCl and Na2CO3).
- Vickers Hardness (summarized from Fig. 6):
- At room temperature, the primary NaCl phase was found to be considerably softer than the primary Na2CO3 phase.
- The eutectic region exhibited an intermediate hardness value.
- Microstructure (summarized from Fig. 7, Fig. 8, Fig. 9, and Fig. 10):
- Annealing the 6CO3 sample at 250°C for 1 hour without compression did not lead to significant microstructural changes compared to the as-cast state (Fig. 7). This indicates that microstructural alterations observed after compression tests are primarily due to the deformation process rather than solely the effect of temperature.
- In the 2CO3 sample (primary NaCl and eutectic), compression at 250°C caused slight distortion in the primary NaCl regions. More notably, the lamellar structure of the eutectic region transformed dramatically into a granular structure (Fig. 8).
- For the ECO3 sample (predominantly eutectic), compression at 250°C resulted in the coarsening of parts of the fine lamellar eutectic structure, which also changed to a granular structure (Fig. 9).
- In the 8CO3 sample (primary Na2CO3 and eutectic), the primary Na2CO3 phase remained largely unchanged after compression. However, similar to other mixtures, the lamellar eutectic structure transformed into a granular structure (Fig. 10).
- These observed microstructural changes in the eutectic region, specifically the transition from a lamellar to a granular morphology, are considered responsible for the increased plasticity of the salt mixtures at elevated temperatures.

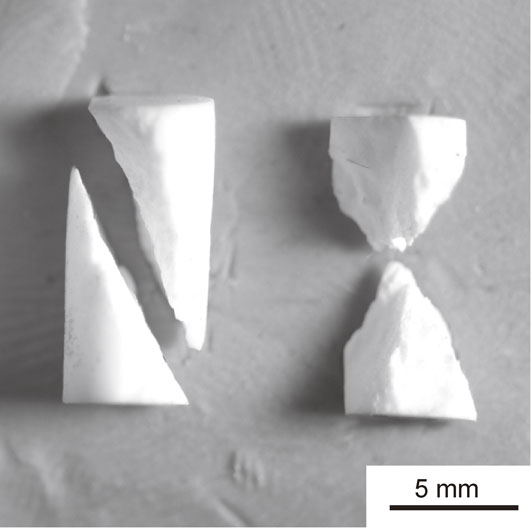
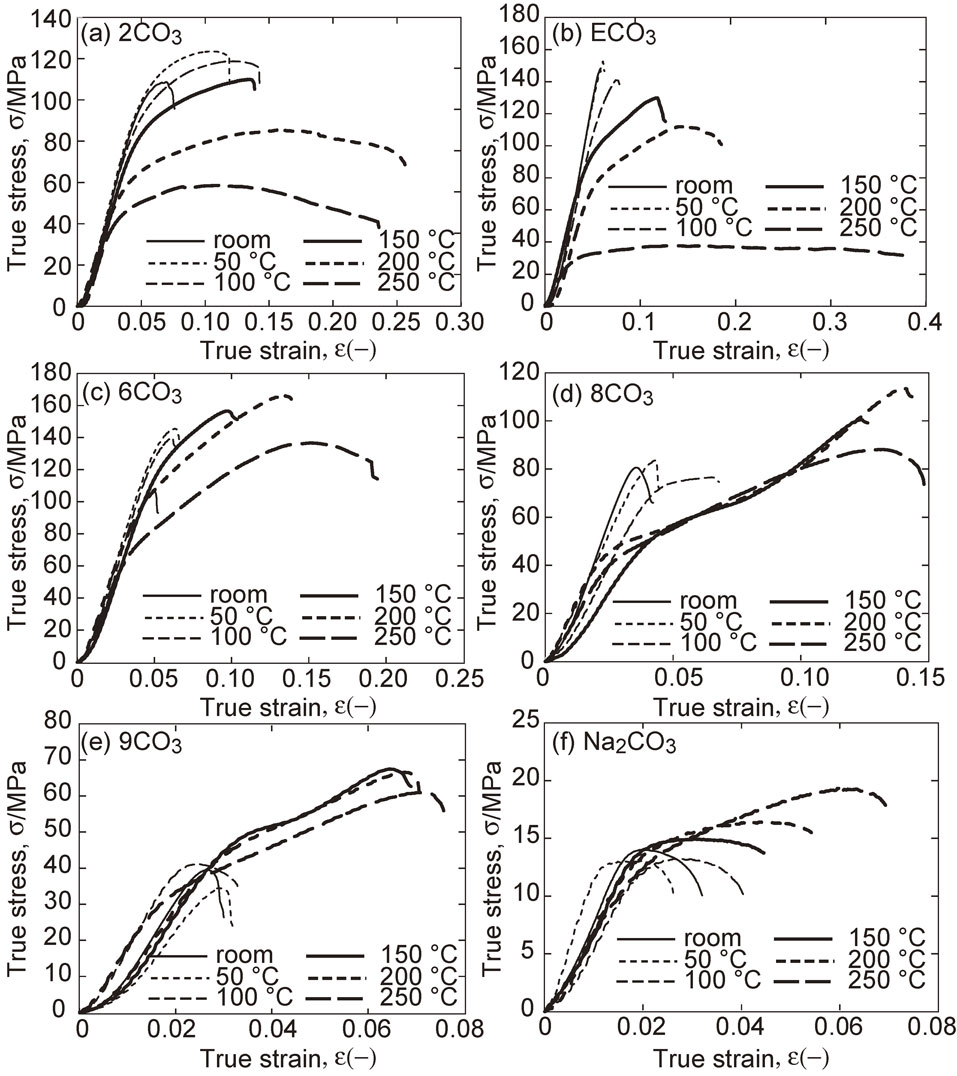
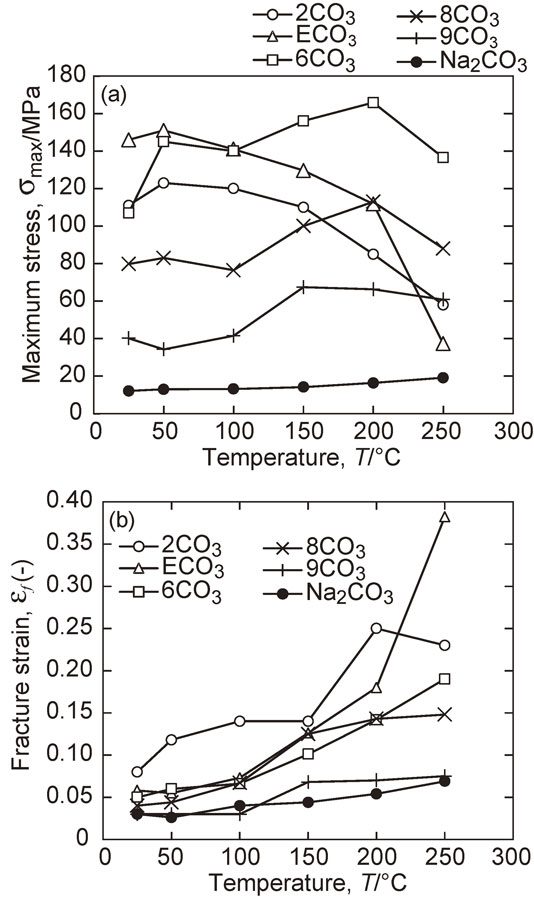
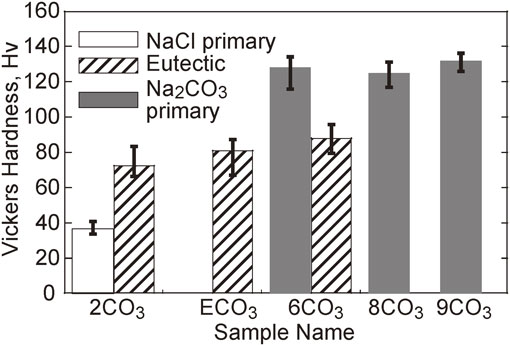

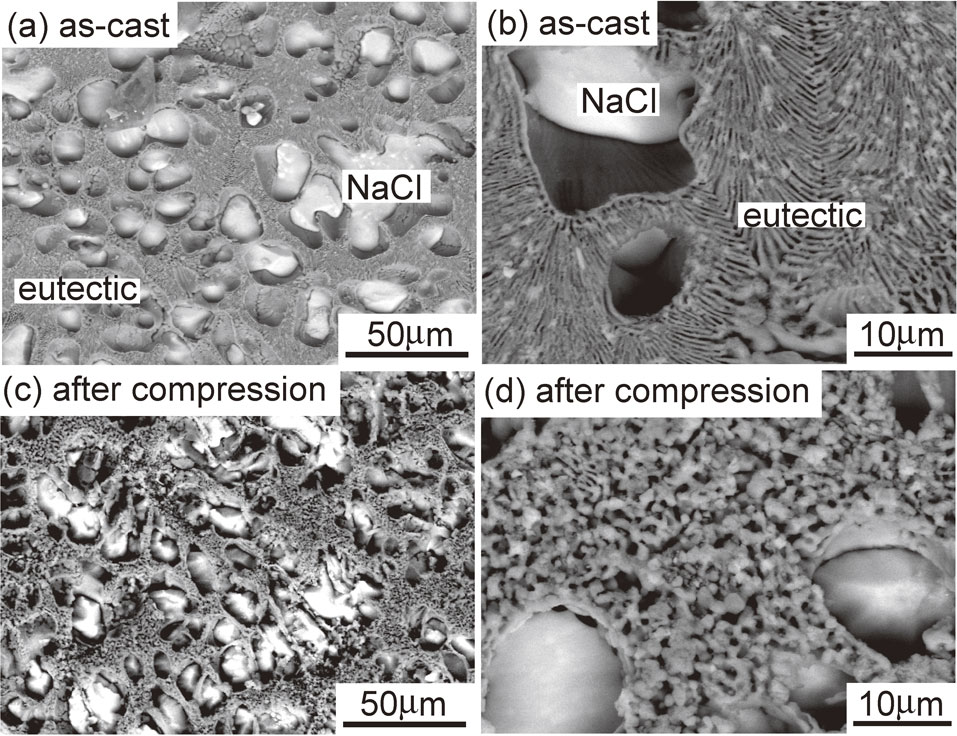
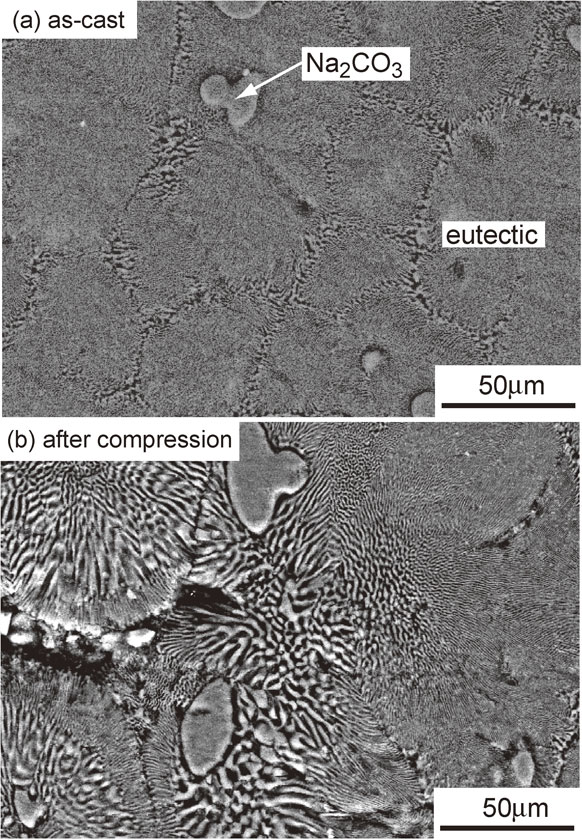
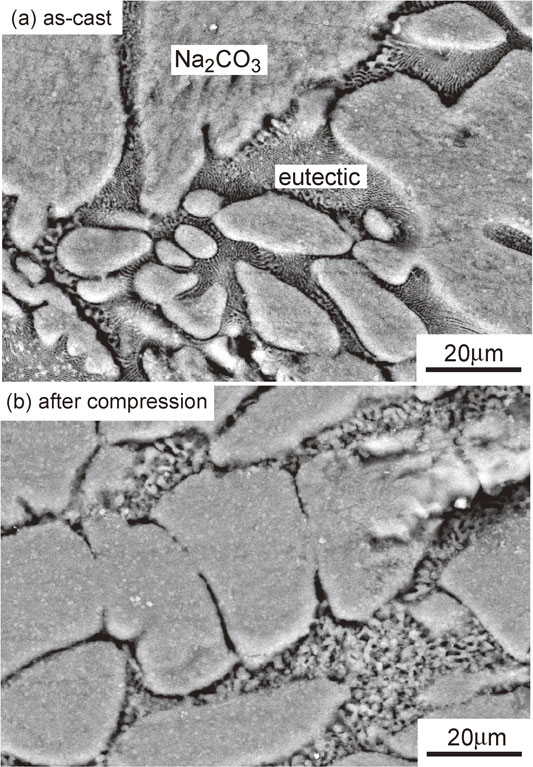
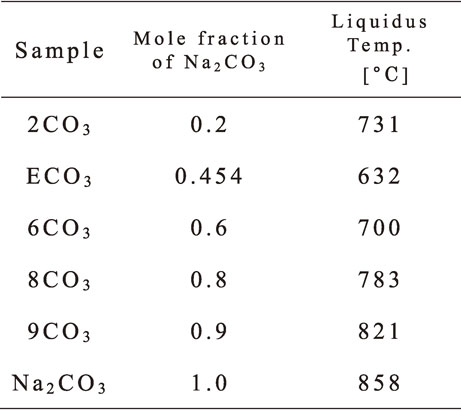
Figure Name List:
- Fig. 1 Appearance of (a) permanent die and (b) cast salt mixture.
- Fig. 2 Calculated phase diagram of NaCl-Na2CO3 with liquidus temperatures of specimens.
- Fig. 3 Typical appearance of sample after compressive test.
- Fig. 4 True stress-true strain (σ-ε) curves at various temperatures.
- Fig. 5 Temperature dependence of the maximum stress and fracture strain.
- Fig. 6 Micro-vickers hardness at room temperature.
- Fig. 7 Microstructure of sample 6CO3: (a), (b) as-cast condition and (c), (d) after annealing at 250°C for 1 h.
- Fig. 8 Microstructure of sample 2CO3: (a), (b) as-cast condition and (c), (d) after compression test at 250°C.
- Fig. 9 Microstructure of ECO3: (a) as-cast condition and (b) after compression test at 250°C.
- Fig. 10 Microstructure of sample 8CO3: (a) as-cast condition and (b) after compression test at 250°C.
7. Conclusion:
The study on NaCl-Na2CO3 salt mixtures prepared by gravity casting and evaluated through compression tests yielded the following main conclusions:
(1) The salt mixtures exhibit significantly greater maximum stress and fracture strain compared to their pure constituent salts. The observed plastic deformation at high temperatures is attributed to a microstructural transformation within the eutectic region, changing from a lamellar to a granular structure.
(2) Salt mixtures containing primary crystal phases along with eutectic regions demonstrate better high-temperature mechanical strength than purely eutectic salt mixtures. Specifically, a salt mixture with primary NaCl is considered more suitable as a core material because it offers better ductility at lower temperatures compared to mixtures with primary Na2CO3.
8. References:
- 1) P. Jelínek, F. Mikšovský, J. Beňo and E. Adámková: Mater. Technol. 47 (2013) 689-693.
- 2) J. Yaokawa, D. Miura, K. Anzai, Y. Yamada and H. Yoshii: Mater. Trans. 48 (2007) 1034-1041.
- 3) P. Jelínek and E. Adámková: Arch. Foundry. Eng. 14 (2014) 101-104.
- 4) J. Yaokawa, D. Miura, K. Oikawa, K. Anzai, Y. Yamada and H. Yoshii: J. Jpn. Foundry. Eng. Soc. 79 (2007) 184-191.
- 5) K. Oikawa, K. Meguro, J. Yaokawa, K. Anzai, Y. Yamada, A. Fujiwara and H. Yoshii: J. Jpn. Foundry Eng. Soc. 81 (2009) 232-237.
- 6) Y. Yamada, H. Yoshii, S. Mochizuki, Y. Bannai, J. Yaokawa, K. Anzai and K. Oikawa: SAE Techical Papers, (2011) 2011-32-0504.
- 7) K. Oikawa, H. Takahashi, K. Anzai, Y. Yamada and H. Yoshii: J. Jpn. Foundry Eng. Soc. 85 (2013) 99-106.
- 8) S. Dommerich: Z. Phys. 90 (1934) 189-196.
- 9) H.G. Müller: Z. Phys. 96 (1935) 321-327.
- 10) W.S. Rothwell and R.G. Greenler: J. Am. Ceram. Soc. 45 (1962) 607-610.
- 11) R.W. Davidge and P.L. Pratt: Phys. Status Solidi B 6 (1964) 759-776.
- 12) J. Hesse: Phys. Status Solidi B 9 (1965) 209-230.
- 13) M. Guillope and J.P. Poirier: J. Geophys. Res. 84 (1979) 5557-5567.
- 14) H. Conrad and D. Yang: J. Mater. Sci. 34 (1999) 821-826.
- 15) T. Sata: J. Ceram. Soc. Jpn. 107 (1999) 166–173.
- 16) J. Yaokawa, K. Oikawa and K. Anzai: Calphad 31 (2007) 155-163.
- 17) R. Ding, Z.X. Guo and A. Wilson: Mater. Sci. Eng. A 327 (2002) 233-245.
- 18) M. Lagler: Die Cast. Eng. (2013) 16-17.
9. Copyright:
- This material is a paper by "Katsunari Oikawa, Kazuhiro Sakakibara, Youji Yamada and Koichi Anzai". Based on "High-Temperature Mechanical Properties of NaCl-Na2CO3 Salt-Mixture Removable Cores for Aluminum Die-Casting".
- Source of the paper: https://doi.org/10.2320/matertrans.MG201804
This material is summarized based on the above paper, and unauthorized use for commercial purposes is prohibited.
Copyright © 2025 CASTMAN. All rights reserved.
Katsunari Oikawa, Kazuhiro Sakakibara, Youji Yamada, Koichi Anzai