The content of this introduction paper is based on the article "For different industrial applications: Outer rotor and low speed induction machine design" published by "Journal of the Faculty of Engineering and Architecture of Gazi University".
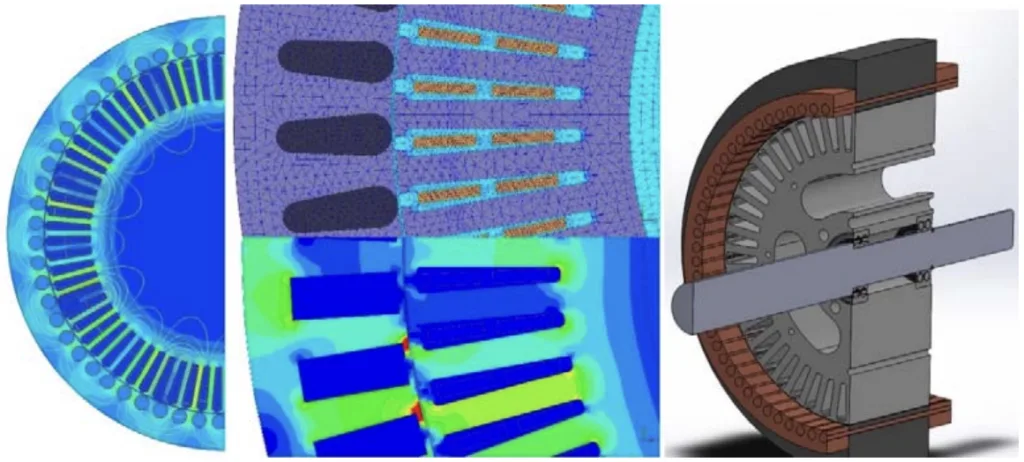
1. Overview:
- Title: For different industrial applications: Outer rotor and low speed induction machine design
- Author: Hakan Çelik, Numan Sabit Çetin
- Year of publication: 2023
- Journal/academic society of publication: Journal of the Faculty of Engineering and Architecture of Gazi University, 38:4 (2023) 2009-2023
- Keywords: Induction machine, Outer rotor, Design, Optimization, Finite element method
2. Abstract:
"Today, with the developing new technologies, in addition to the traditional usage areas of asynchronous machines, their usage areas as motors and generators are gradually expanding. In recent years, the use of induction generator in areas such as motor/generator in electric vehicles, wind turbines and micro-hydroelectric generation has started to widespread. This study aims to design a low-speed and high-torque outer rotor induction machine that can be used in outer rotor induction motor applications and optionally as a direct-drive generator. The design, optimization and electromagnetic analysis of a 16-pole, 50 Hz frequency, 375 rpm synchronous speed, 1 kW outer rotor induction machine were carried out and six different models were developed for the analyses in this study. One slot type and 72 slot were used in the stator designs, 59 slot and three different slot types were used in the rotor design. Copper and Aluminum materials were preferred for the squirrel cage rotor and the study was carried out with the Ansys Maxwell electromagnetic package program. In the study, machine foundation sizes, air gap and slot dimensions were optimized to obtain the highest efficiency using the Rmxprt-optimetrics module. Afterwards, electromagnetic analyzes were performed using the Finite Element Method. As a result of the analyzes made for the motor operating area of the machine, an efficiency higher than the efficiency of 8-pole inner rotor asynchronous motors with 1.1 kW power in IE2 and IE3 classes according to IEC 60034-30-1 was obtained. According to this result, it was found that an outer rotor, low speed and high torque induction machine can be produced and used as a motor."
3. Introduction:
Asynchronous machines, also known as induction machines, are experiencing increased popularity and expanding applications beyond traditional industrial uses to include motor and generator roles in emerging technologies. Specifically, their application as induction generators in electric vehicles, wind turbines, and micro-hydroelectric systems has become increasingly prevalent. This research focuses on Outer Rotor Induction Machines (DRAMAK), aiming to address the growing demand for low-speed, high-torque machines suitable for direct-drive applications and various industrial contexts. While conventional Inner Rotor Asynchronous Machines (İRAMAK) are widely used, DRAMAKs, historically limited to applications like cooling fans, are gaining attention, particularly for electric vehicle powertrains. This study introduces a novel DRAMAK design, emphasizing its potential for high efficiency and performance in demanding industrial applications.
4. Summary of the study:
Background of the research topic:
The expanding application landscape of asynchronous machines, driven by technological advancements, necessitates exploring and optimizing machine designs for diverse operational requirements. The increasing demand for motors and generators in sectors like electric vehicles and renewable energy systems highlights the importance of efficient and adaptable machine technologies.
Status of previous research:
Prior research on DRAMAKs has largely focused on single-phase motors for low-performance applications like ceiling fans. These designs often exhibit low efficiency and high slip. While studies have explored performance improvements through various techniques, a gap exists in the literature concerning high-efficiency, three-phase DRAMAK designs suitable for industrial applications and direct-drive generator systems.
Purpose of the study:
This study aims to design and optimize a three-phase, low-speed, high-torque, and high-efficiency outer rotor induction machine. The intended applications include motor/generators for electric vehicles, direct drive generators in wind turbines and hydroelectric applications, and fan motors.
Core study:
The core of this research involves the analytical design, optimization, and 2D Finite Element Analysis (FEA) of a 1 kW, 16-pole outer rotor induction machine operating at 50 Hz. Six distinct models were developed and analyzed using Ansys Maxwell software. The study investigates the impact of varying rotor slot types (round, drop cage, rectangular) and squirrel cage materials (copper and aluminum) on machine performance, with a focus on achieving high efficiency according to IEC 60034-30-1 standards.
5. Research Methodology
Research Design:
The research employs a multi-faceted approach encompassing analytical design, parametric optimization, and finite element analysis. Initially, an analytical design framework was established, followed by optimization using the RMxprt optimetrics module within Ansys Maxwell to maximize efficiency. Subsequently, 2D Finite Element Analysis (FEA) was conducted using Ansys Maxwell to validate the analytical models and assess electromagnetic performance. A 3D mechanical design was conceived based on the 2D machine geometry for comprehensive visualization. Six distinct machine models were designed, systematically varying rotor slot geometries and cage materials to evaluate their respective impacts.
Data Collection and Analysis Methods:
Data collection and analysis were primarily conducted using the Ansys Maxwell software suite. The RMxprt optimetrics module facilitated the optimization of stator and rotor dimensions, air gap, and slot parameters. Electromagnetic analyses were performed using 2D FEA to simulate machine behavior under motor operating conditions. Performance metrics such as efficiency, torque, power factor, and current characteristics were extracted from the simulations and compared across the six models. The results were then evaluated against the IEC 60034-30-1 standard for efficiency classification.
Research Topics and Scope:
The research specifically focused on the design and optimization of a 1 kW, 16-pole, three-phase outer rotor induction machine. The scope included:
- Investigating the influence of three different rotor slot types: round (Tip I), drop cage (Tip II), and rectangular (Tip III).
- Analyzing the performance with two different rotor cage materials: copper (Cu) and aluminum (Al).
- Optimizing machine parameters for maximum efficiency using the RMxprt optimetrics module.
- Verifying analytical designs through 2D electromagnetic analysis using FEA.
- Assessing the efficiency class according to IEC 60034-30-1 standard (IE2 and IE3 efficiency classes).
6. Key Results:
Key Results:
The analysis revealed significant performance variations across the six designed models. Key findings include:
- Highest Efficiency: The M3 model, featuring a drop cage slot (Tip II) and copper cage material, achieved the highest efficiency of %η=78.38.
- Highest Torque and Best Power Coefficient: The M2 model, utilizing a round slot (Tip I) and aluminum cage material, demonstrated the highest torque (Tm=27.36 Nm) and best power coefficient (Cosp=0.73). This model also exhibited the lowest speed (nr=348.99 rpm) and a high efficiency of %η=74.75.
- Material and Slot Type Impact: The choice of rotor cage material and slot type significantly influences machine performance, particularly efficiency and torque characteristics. Copper generally yielded higher efficiency, while round slot configurations contributed to higher torque in the analyzed models.
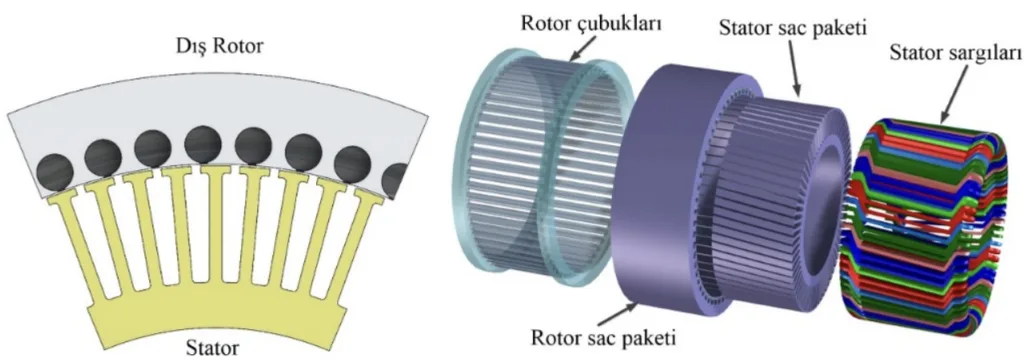
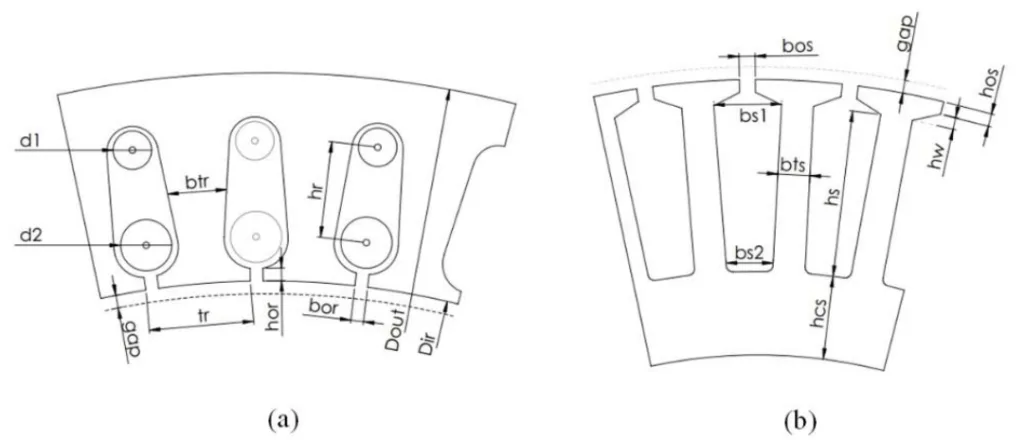
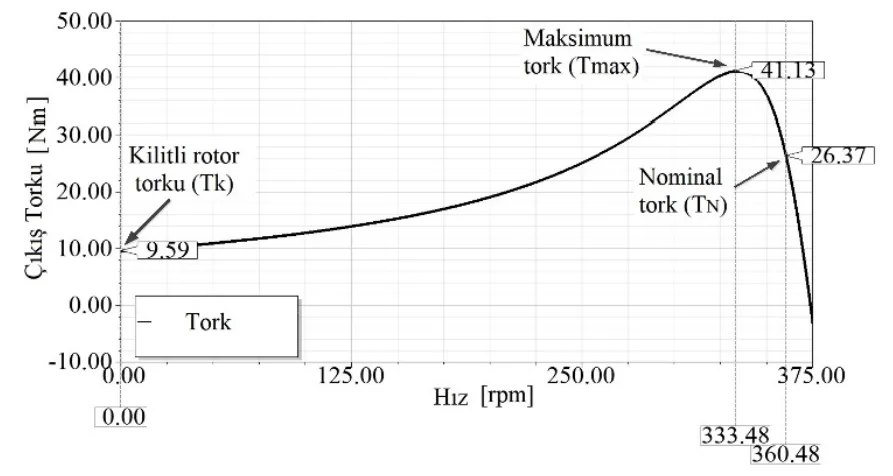
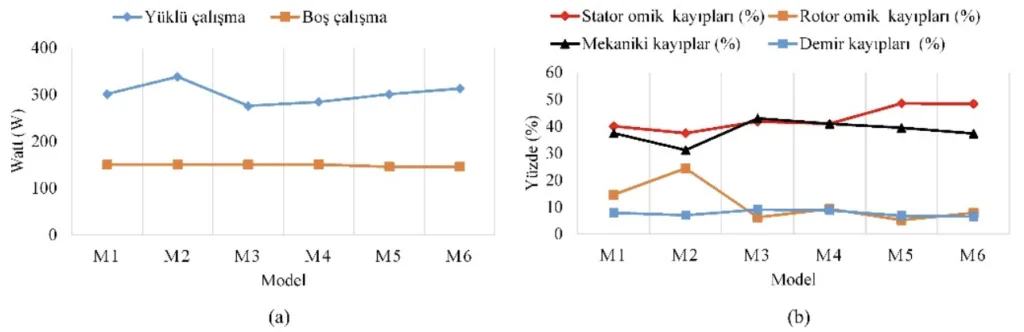
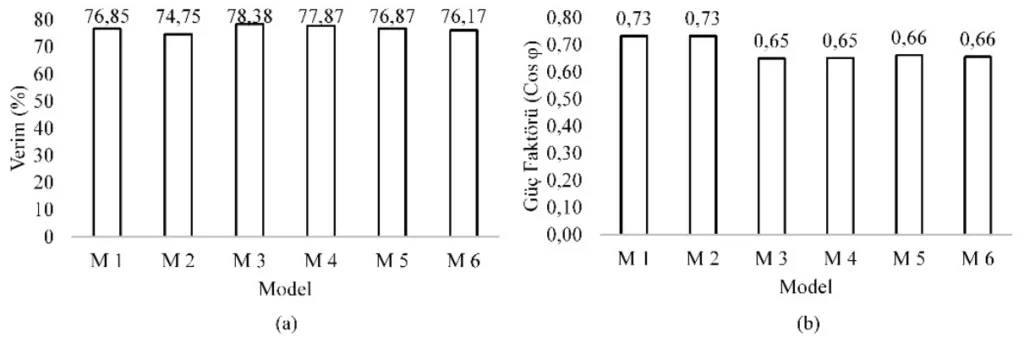
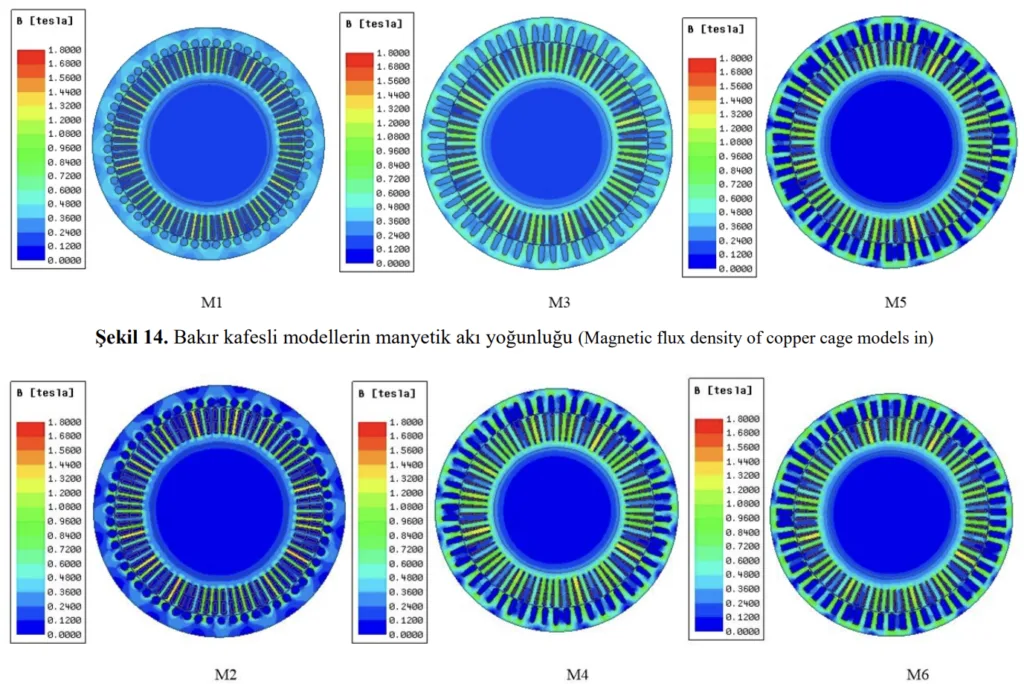
Figure Name List:
- Figure A. Outer rotor induction motor mesh operation and 2D FEA
- Figure 5. M1 Hava aralığı-verim optimizasyon grafiği (M1 Air gap - efficiency optimization graph)
- Figure 7. Eşdeğer devre parametreleri; a) R1 ve R2, b) X1 ve X2, c) Xm (Equivalent circuit parameters a) R1 and R2, b) X1 and X2, c) Xm )
- Figure 8. Faz akımları (Phase current)
- Figure 9. M1 Tork-Hız eğrisi (M1 torque-speed graphic)
- Figure 10. Tork değerleri (Torque values)
- Figure 11. a) Toplam kayıplar, b) Detaylı kayıp oranları (a)Total losses, b) Detailed loss rates)
- Figure 12. a) Verim b) Güç faktörü (a-Efficiency, b-Power factor)
- Figure 13. M3 Mesh işlemi ve M5 Manyetik alan dağılım (M3 Mesh operation and M5 magnetics field disturibition)
- Figure 14. Bakır kafesli modellerin manyetik akı yoğunluğu (Magnetic flux density of copper cage models in)
- Figure 15. Alüminyum kafesli modellerin manyetik akı yoğunluğu (Magnetic flux density of aluminium cage models)
- Figure 16. Tork-zaman eğrisi; a) M-M2, b) M3-M4, c) M5-M6, Akım zaman eğrisi; d) M1-M2, e) M3-M4, f) M5-M6 (Torque-time graphic; a) M1-M2, b) M3-M4, c) M5-M6, Current-time graphic; d) M1-M2, e) M3-M4, f) M5-M6)
- Figure 17. Hız-Zaman eğrileri (Speed-time graphic)
7. Conclusion:
This study demonstrates the feasibility of achieving high efficiency in Outer Rotor Induction Machines (ORIM) with a high pole number. The research highlights the novelty that a 16-pole 1kW ORIM can be manufactured with an efficiency exceeding the limits of 8-pole 1.1kW Inner Rotor Induction Machines (IRIM) of IE2 and IE3 efficiency classes according to the IEC 60034-30-1 standard. The findings suggest that outer rotor, low-speed, and high-torque induction machines are viable for production and practical application as motors, offering a promising avenue for advanced industrial and electric vehicle drive systems.
8. References:
- [1] Bortoni, E. C., Bernardes Jr, J. V., da Silva, P. V., Faria, V. A., Vieira, P. A., Evaluation of manufacturers strategies to obtain high-efficient induction motors, Sustainable Energy Technologies and Assessments, 31, 221-227, 2019.
- [2] Kabul A., Ünsal A., Diagnosis of simultaneous broken rotor bars and static eccentricity faults of induction motors by analyzing stator current and vibration signals, Journal of the Faculty of Engineering and Architecture of Gazi University, 36 (4), 2011-2023, 2021.
- [3] Lenin N.C., Padmanaban S., Bhaskar M.S., Mitolo M., Hossain E., Ceiling fan drives-past, present and future, IEEE Access, 9, 44888-44904, 2021.
- [4] Holik P.J., Dorrell D.G., Popescu M., Performance improvement of an external-rotor split-phase induction motor for low-cost drive applications using external rotor can, IEEE Transactions on magnetics, 43 (6), 2549-2551 2007.
- [5] Shastri S., Sharma U., Singh B., Design of Fractional-slot concentrated winding consequent pole motor for ceiling fans, IEEE 5th Int. Conference on Computing Communication and Automation, New Delhi-India, 390-395, 30-31 October, 2020.
- [6] Mohammed K.G., Ramli A.Q., Analyzing the performance of completed designed outer rotor single phase induction motor, IEEE Student Conference on Research and Developement, Putrajaya-Malaysia, 238-242, 16-17 December, 2013.
- [7] Popescu M., Dorrell D.G. and Holik P., Improving the starting torque in external-rotor induction motors using an outer can, 3rd IET International Conference on Power Electronics, Machines and Drives, Dublin- Ireland, 531-535, 4-6 April, 2006.
- [8] György T., Biró K.A., Genetic algorithm based design optimization of a three-phase induction machine with external rotor, 2015 Intl Aegean Conference on Electrical Machines & Power Electronics (ACEMP), 2015 Intl Conference on Optimization of Electrical & Electronic Equipment (OPTIM) & 2015 Intl Symposium on Advanced Electromechanical Motion Systems (ELECTROMOTION), Side-Turkey, 462-467, 2-4 September 2015.
- [9] György T., Biró K.Á., Co-evolutionary optimization design of a three-phase induction machine with external rotor, XXII International Conference on Electrical Machines (ICEM), Lausanne-Switzerland, 1394-1398, 4-7 September, 2016.
- [10] György, T., Biró K.A., Loss analysis of a low power induction machine with external rotor, 6.th International Conference on Modern Power Systems MPS2015, Cluj Napoca-Romania, 117-122, 18-21 May 2015.
- [11] Virlan B., Benelghali S., Simion A., Livadaru L., Outbib R., Munteanu A., Induction motor with outer rotor and ring stator winding for multispeed applications, IEEE Transactions on Energy Conversion, 28 (4), 999-1007, 2013.
- [12] Sundaram V. M., Toliyat H. A., A fractional slot concentrated winding (FSCW) configuration for outer rotor squirrel cage induction motors, IEEE International Electric Machines & Drives Conference (IEMDC), Coeur d'Alene- USA, 20-26, 10-13 May, 2015.
- [13] Dalal A., Kumar P., Design, prototyping, and testing of a dual-rotor motor for electric vehicle application, IEEE Transactions on Industrial Electronics, 65 (9), 7185-7192, 2018.
- [14] Cui S., Han S., Chan C.C., Overview of multi-machine drive systems for electric and hybrid electric vehicles, IEEE Conference and Expo Transportation Electrification Asia-Pacific (ITEC Asia-Pacific), Beijing-China, 1-6, 31 August - 3 September, 2014.
- [15] Wang W., Chen X., Wang J., Motor/generator applications in electrified vehicle chassis-A Survey, IEEE Trans. Transactions on Transportation Electrification, 5 (3), 584-601, 2019.
- [16] Cha A.H.R., Jeong B.T.W., Im C.D.Y., Shin D.K.J., Seo E.Y.J., Design of outer rotor type induction motor having high power density for in-wheel system, 15th International Conference on Electrical Machines and Systems (ICEMS), Sapporo-Japan, 1-4, 21-24 October, 2012.
- [17] Popescu M., Riviere N., Volpe G., Villani M., Fabri G., Leonardo L.D., A copper rotor induction motor solution for electrical vehicles traction system, IEEE Energy Conversion Congress and Exposition, Baltimore MD-USA, 3924-3930, September 29-October 3, 2019.
- [18] Livadaru L., Munteanu A., Simion A., Cantemir C., Design and finite element analysis of high-density torque induction motor for traction applications, 9th International Symposium on Advanced Topics in Electrical Engineering (ATEE), Bucharest-Romania, 211-214, 7-9 May, 2015.
- [19] Munteanu A., Livadaru L., Simion A., Vîrlan B., Single-tooth winding induction motor with external rotor for electric vehicle applications, International Conference and Exposition on Electrical and Power Engineering (EPE), Iasi-Romania, 209-212, October 20-22, 2016.
- [20] Hwang M.H., Lee H.S., Yang S.H., Cha H.R., Park S.J., Electromagnetic field analysis and design of an efficient outer rotor inductor in the low-speed section for driving electric vehicles, Energies, 12 (24), 4615, 2019.
- [21] Matthew H., Jensen B.B., Induction generators for direct-drive wind turbines, IEEE International Electric Machines & Drives Conference (IEMDC), Niagara Falls Ontario-Canada, 1125-1130, 14-17 May, 2011.
- [22] Mellah, H., Hemsas K.E., Design and analysis of an external-rotor internal-stator doubly fed induction generator for small wind turbine application by fem, International Journal of Renewable and Sustainable Energy, 2 (1), 1-11, 2013.
- [23] Hamdi, E. S., Design of small electrical machines, John Wiley & Sons, New York, A.B.D., 1994.
- [24] Dorrell D. G., The challenges of meeting IE4 efficiency standards for induction and other machines, IEEE International Conference on Industrial Technology (ICIT), Busan-Korea (South), 213-218, 26 Feb.-1 March, 2014.
- [25] Kimball J. W., Amrhein M., IEEE Machine design considerations for the future energy challenge, Proceedings Electrical Insulation Conference and Electrical Manufacturing Expo, Indianapolis-USA, 448-453, 24-26 October, 2005.
- [26] Popescu M., Analysis and modelling of single-phase induction motor with external rotor for domestic applications, In Conference Record of the 2000 IEEE Industry Applications Conference, Thirty-Fifth IAS Annual Meeting and World Conference on Industrial Applications of Electrical Energy, Rome Italy, 1-463-470, 8-12 October, 2000.
- [27] Boldea, I., Induction machines handbook, CRC press Taylor & Francis Group, Boca Raton, A.B.D., 2010.
- [28] Demir U., Aküner M.C., Design and optimization of in-wheel asynchronous motor for electric vehicle, Journal of the Faculty of Engineering and Architecture of Gazi University, 33 (4), 1517-1530, 2018.
- [29] Purwanto W., Risfendra, Putra D S., Effect of stator slot geometry on high speed spindle motor performance, 2018 International Conference on Information and Communications Technology (ICOIACT), Yogyakarta- Indonesia, 561-565, 6-7 March, 2018.
- [30] Lipo T.A., Introduction to AC machine design, John Wiley & Sons, New Jersey, A.B.D, 2017.
- [31] Gundogdu T., Zhu Z. Q., Mipo J. C., Farah P., Influence of air-gap length on rotor bar current waveform of squirrel-cage induction motor. 19th International Conference on Electrical Machines and Systems (ICEMS) IEEE, Chiba-Japan, 1-6, 13-16 November, 2016.
- [32] Joksimović G., Kajević A., Mezzarobba M., Tessarolo, A., Optimal rotor bars number in four pole cage induction motor with 36 stator slots-part II: results, International Conference on Electrical Machines (ICEM) IEEE, Gothenburg-Sweden, 1, 509-514. 23-26 August, 2020.
- [33] Babypriya B., Gomathi, S., Numerical analysis on impact of choice of number of rotor slots on performance of three phase induction motor, Materials Today: Proceedings (Article in press), 1-7, 2020.
- [34] Chapman, S., Electric machinery fundamentals, McGraw-Hill Education, New York, A.B.D, 2005.
- [35] Araz H. K., Yılmaz M., Design procedure and implementation of a high-efficiency PMSM with reduced magnet-mass and torque-ripple for electric vehicles, Journal of the Faculty of Engineering and Architecture of Gazi University, 35 (2), 1089-1109, 2020.
9. Copyright:
- This material is a paper by "Hakan Çelik, Numan Sabit Çetin". Based on "For different industrial applications: Outer rotor and low speed induction machine design".
- Source of the paper: https://doi.org/10.17341/gazimmfd.937127
This material is summarized based on the above paper, and unauthorized use for commercial purposes is prohibited.
Copyright © 2025 CASTMAN. All rights reserved.