This introductory paper is the research content of the paper "Experimental and Theoretical Studies on the Effect of Die Temperature on the Quality of the Products in High-Pressure Die-Casting Process" published by Hindawi Publishing Corporation.
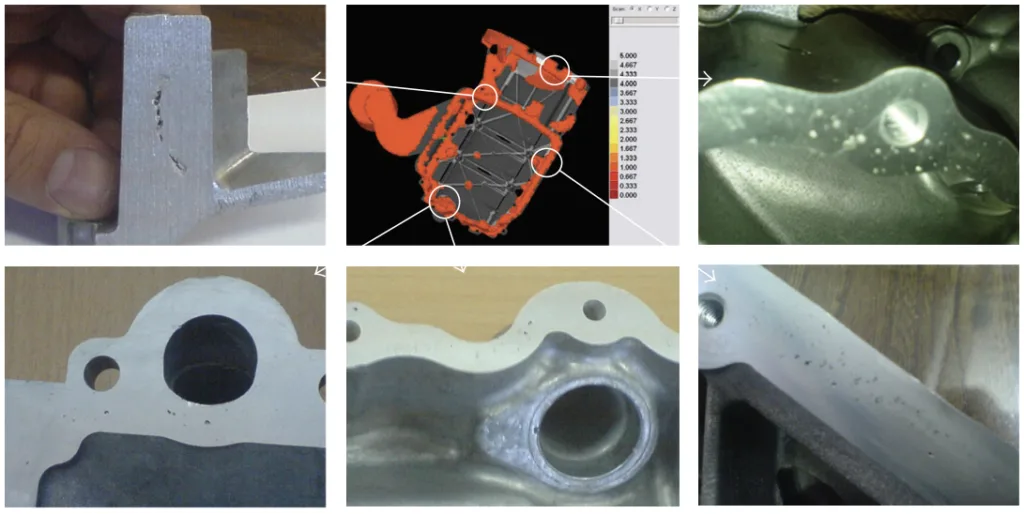
1. Overview:
- Title: Experimental and Theoretical Studies on the Effect of Die Temperature on the Quality of the Products in High-Pressure Die-Casting Process
- Author: Mohammad Sadeghi and Jafar Mahmoudi
- Publication Year: 2012
- Published Journal/Society: Advances in Materials Science and Engineering
- Keywords: Die Temperature, High-Pressure Die-Casting (HPDC), A380 Alloy, Numerical Simulation, ProCAST, cold flow defects, air porosities.
2. Abstract
Die temperature in high-pressure die casting of A380 alloy is optimized by experimental observation and numerical simulation. Ladder frame (one part of the new motor EF7) with a very complicated geometry was chosen as an experimental sample. Die temperature and melt temperature were examined to produce a sound part. Die temperatures at the initial step and the final filling positions were measured and the difference between these values was calculated. ProCAST software was used to simulate the fluid flow and solidification step of the part, and the results were verified by experimental measurements. It is shown that the proper die temperature for this alloy is above 200°C.
3. Research Background:
Background of the research topic:
High-pressure die-casting (HPDC) is a widely used manufacturing process known for its high dimensional accuracy, productivity, and ability to produce components with low surface roughness. It is particularly important in the production of aluminum automotive components [1-7].
Status of previous research:
Previous research has focused on various aspects of HPDC, including process optimization, defect control, and simulation. Researchers have used software like FLOW-3D and ProCAST to simulate filling and solidification [10, 12]. Others have investigated flow conditions and their impact on casting defects [11], and optimized process parameters like die temperature, melt temperature, and plunger velocity [13].
Need for research:
Although HPDC is a high-speed process, its complexity and the numerous variables involved necessitate optimization. Many existing studies focus on simpler geometries, with fewer researches on very complex parts used in industry.
4. Research purpose and research question:
Research purpose:
To optimize process parameters, specifically die temperature, in the high-pressure die casting of a complex automotive component (a ladder frame).
Core research:
Investigating the effect of die temperature on the quality of the products, specifically focusing on minimizing defects.
5. Research methodology
- Research Design: A combination of experimental observation and numerical simulation.
- Data Collection:
- Experimental: Measurement of die and melt temperatures at various stages of the process using thermocouples and a Laser pyrometer (model chy 110). Casting trials were performed using an IDRA1600 die-cast machine.
- Simulation: ProCAST software was used to simulate fluid flow and solidification. A 3D model of the ladder frame was imported in Parasolid format (Figure 1).
- Analysis Method: Comparison of simulation results with experimental measurements. Analysis of filling patterns, temperature distributions, and defect formation.
- Research Subject and Scope: Optimization of die temperature for HPDC of A380 alloy using a ladder frame component. Material properties are listed in Table 1. Initial and boundary conditions, including varied die and melt temperatures, are detailed in Table 2. Two different mesh sizes were used to ensure mesh independency.
6. Key research results:
Key research results and presented data analysis:
- The relationship between melt temperature and die temperature was established (Figure 2).
- The reduction in melt temperature from the start of injection to the end of filling was quantified for different die temperatures (Figure 3, Figure 4, Table 3).
- Cold flow surface defects were observed at a die temperature of 150°C, occurring at the final filling positions (Figure 5).
- The simulation accurately predicted the location of cold shot defects.
- Gas porosities caused by entrapped air were identified (Figure 7).
- Turbulent flow patterns and potential air entrapment locations were identified through simulation (Figure 8, Figure 9(d)).
- Temperature distribution in the melt was analyzed for different die temperatures (Figure 10).
- Final solidification positions and potential shrinkage defects were predicted by the simulation and verified experimentally (Figure 11, Figure 12).
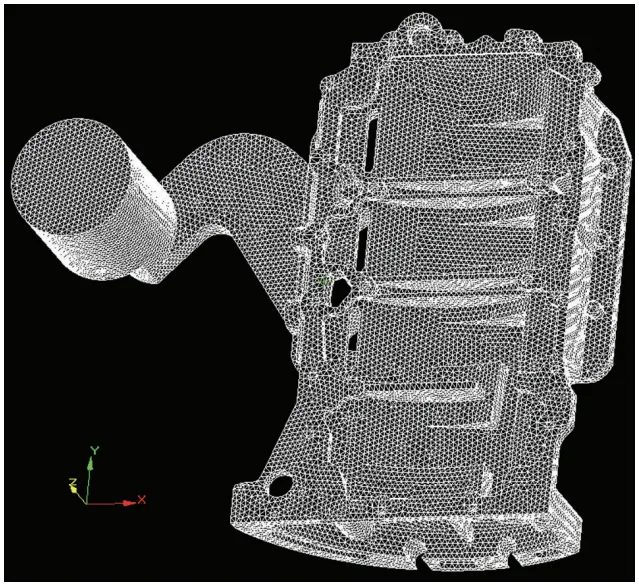
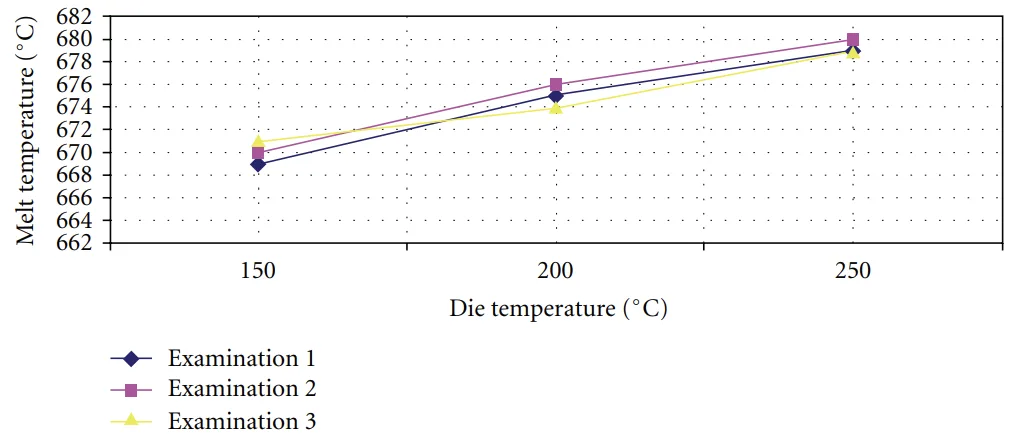
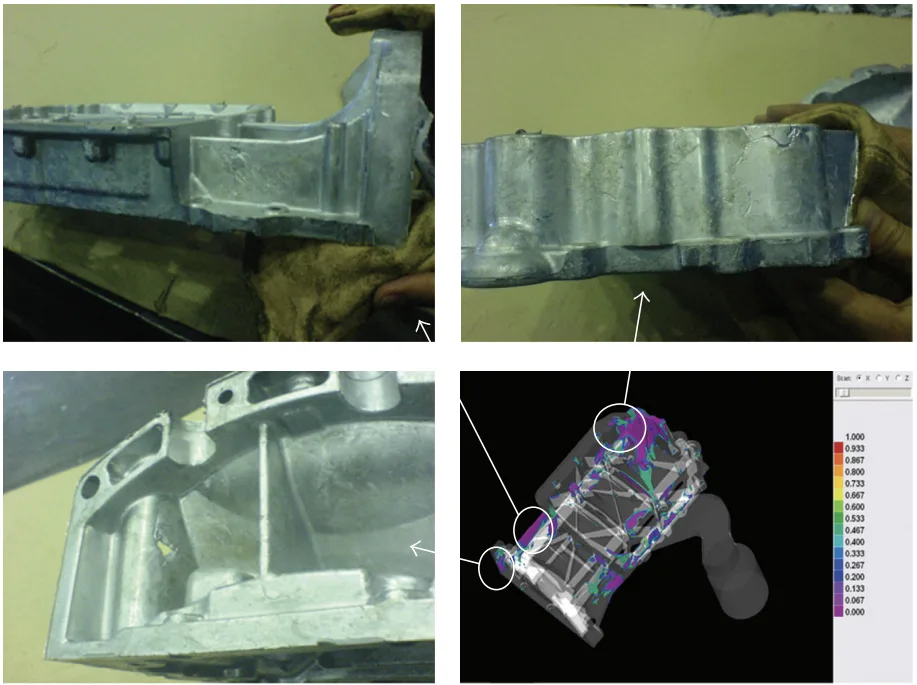
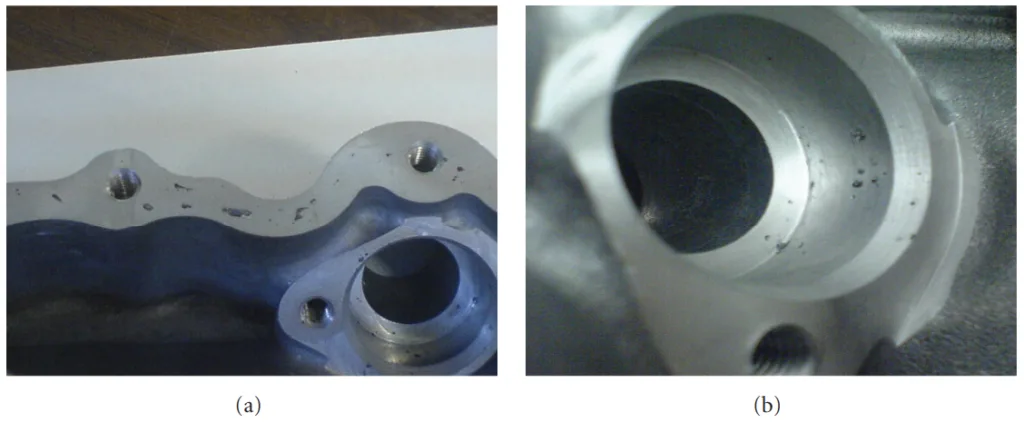
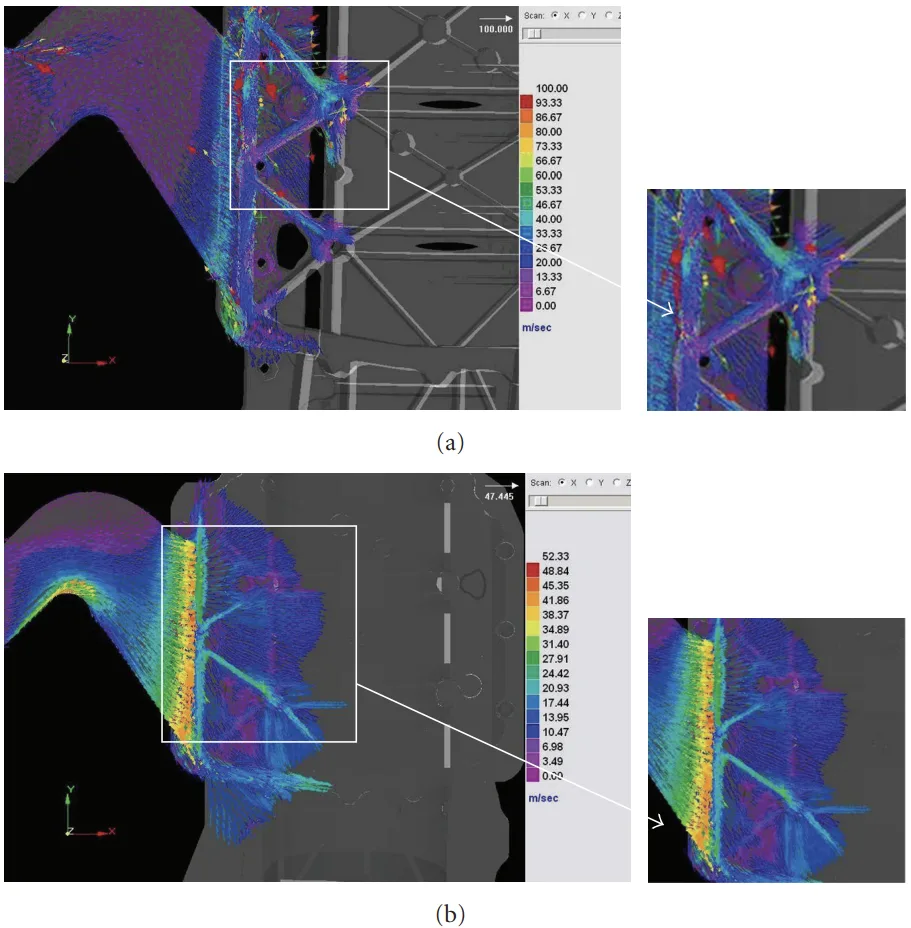
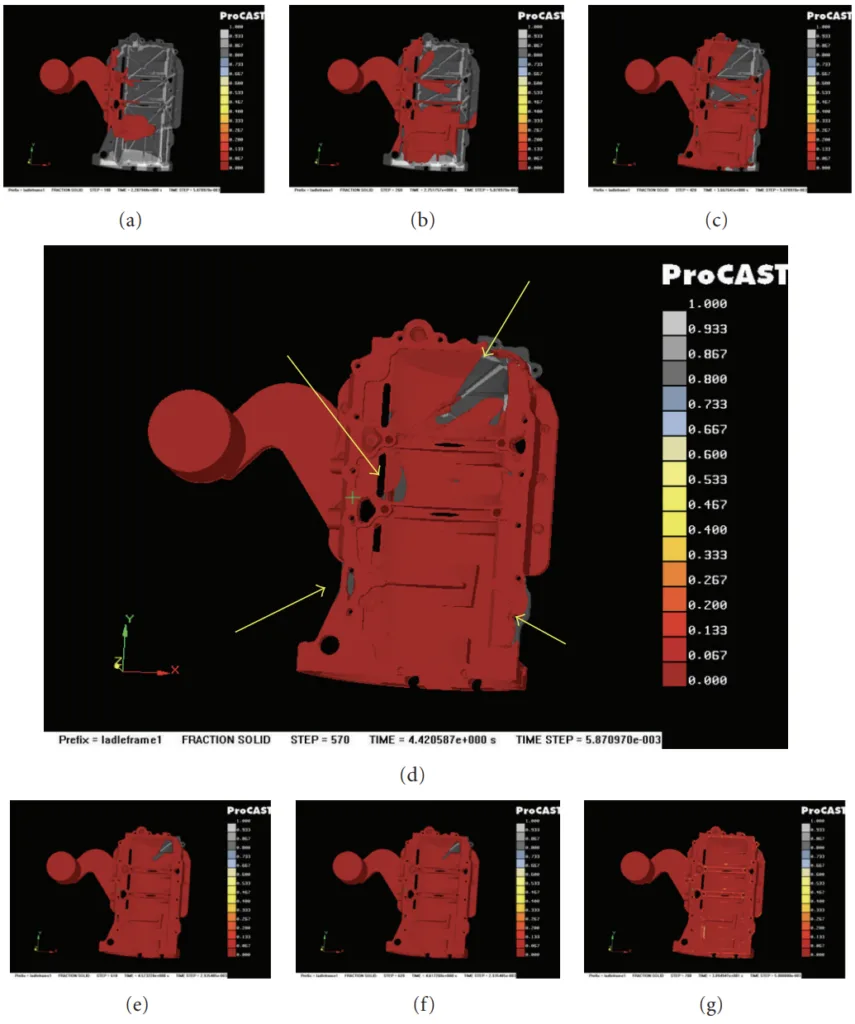
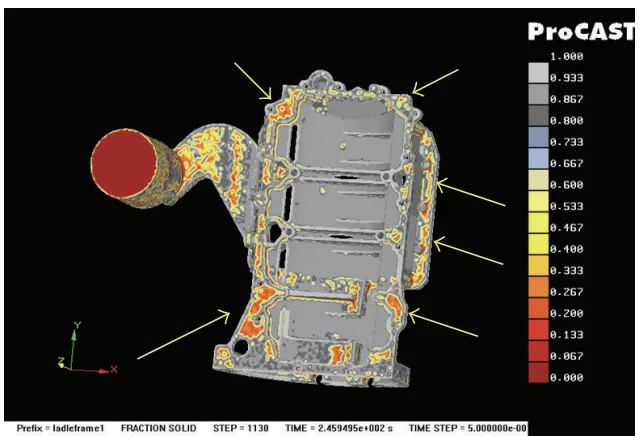
List of figure names:
- Figure 1: Geometry of ladder frame product.
- Figure 2: Melt temperatures at die entrance and start injection versus die temperatures.
- Figure 3: Melt temperatures at the end of the die and end injection versus die temperatures.
- Figure 4: Reduction of melt temperature at various die temperatures at the initial and the end of injection.
- Figure 5: Cold flow surface defects at final filling positions.
- Figure 6: positions of added overflows to the mold.
- Figure 7: Some porosity defects.
- Figure 8: Velocity vectors of the melt at the three holes in the front of the gate.
- Figure 9: Steps filled die by the melt and show End points.
- Figure 10: Flow pattern of melt with die temperature (a) 150°C and (b) 250°C in same time. Time a1 = b1, a2 = b2, and a3 = b3.
- Figure 11: Hot spots at the end of solidification step, which are susceptible to casting defects.
- Figure 12: Defects occurred in final solidification positions.
7. Conclusion:
Summary of key findings:
- Experimental and simulation results showed good agreement, with defects occurring at locations predicted by the simulation.
- The optimum die temperature for the A380 alloy and H13 die material, in this specific case, was determined to be around 200°C.
- Reducing the die temperature below the optimum range increases the probability of cold flow defects and air porosities.
- Simulation was effectively used to determine optimized locations for overflows, reducing casting defects like cold shots and air porosities.
Academic significance of the research:
This research provides a practical example of using simulation to optimize die temperature in HPDC for a complex geometry, validating the simulation results with experimental data.
Practical implications of the research:
The findings can be used to improve the quality of die-cast parts by optimizing die temperature and overflow placement, leading to reduced defects and improved process efficiency.
8. References:
- [1] M. S. Dargusch, G. Dour, N. Schauer, C. M. Dinnis, and G. Savage, "The influence of pressure during solidification of high pressure die cast aluminium telecommunications components," Journal of Materials Processing Technology, vol. 180, no. 1-3, pp. 37-43, 2006.
- [2] Z. W. Chen and M. Z. Jahedi, "Die erosion and its effect on soldering formation in high pressure die casting of aluminium alloys," Materials and Design, vol. 20, no. 6, pp. 303-309, 1999.
- [3] P. W. Cleary, J. Ha, M. Prakash, and T. Nguyen, "3D SPH flow predictions and validation for high pressure die casting of automotive components," Applied Mathematical Modelling, vol. 30, no. 11, pp. 1406-1427, 2006.
- [4] K. J. Laws, B. Gun, and M. Ferry, "Effect of die-casting parameters on the production of high quality bulk metallic glass samples," Materials Science and Engineering A, vol. 425, no. 1-2, pp. 114-120, 2006.
- [5] D. McBride, T. N. Croft, and M. Cross, "A coupled finite volume method for the computational modelling of mould filling in very complex geometries," Computers & Fluids, vol. 37, no. 2, pp. 170–180, 2008.
- [6] C. C. Tai and J. C. Lin, “The optimal position for the injection gate of a die-casting die," Journal of Materials Processing Technology, vol. 86, no. 1-3, pp. 87–100, 1998.
- [7] S. W. Youn, C. G. Kang, and P. K. Seo, "Thermal fluid/solidification analysis of automobile part by horizontal squeeze casting process and experimental evaluation," Journal of Materials Processing Technology, vol. 146, no. 3, pp. 294-302, 2004.
- [8] J. X. Zhou, L. L. Chen, D. M. Liao, and R. X. Liu, "High pressure diecasting module of InteCAST software and its applications," Journal of Materials Processing Technology, vol. 192-193, pp. 249-254, 2007.
- [9] S. Yue, G. Wang, F. Yin, Y. Wang, and J. Yang, “Application of an integrated CAD/CAE/CAM system for die casting dies," Journal of Materials Processing Technology, vol. 139, no. 1-3, pp. 465-468, 2003.
- [10] A. Kermanpur, S. Mahmoudi, and A. Hajipour, "Numerical simulation of metal flow and solidification in the multi- cavity casting moulds of automotive components," Journal of Materials Processing Technology, vol. 206, no. 1-3, pp. 62-68, 2008.
- [11] S. Schneiderbauer, S. Pirker, C. Chimani, and R. Kretz, "Studies on flow characteristics at high-pressure die-casting," in Proceedings of the 3rd International Conference on Advances in Solidification Processes.
- [12] M. F. V. T. Pereira, M. Williams, and W. B. du Preez, "Reducing non value adding aluminium alloy in production of parts through high pressure die casting," in Proceedings of the Light Metals Conference, 2010.
- [13] J. K. Rai, A. M. Lajimi, and P. Xirouchakis, "An intelligent system for predicting HPDC process variables in interactive environment," Journal of Materials Processing Technology, vol. 203, no. 1-3, pp. 72-79, 2008.
- [14] B. S. Sung and I. S. Kim, “The molding analysis of automobile parts using the die-casting system," Journal of Materials Processing Technology, vol. 201, pp. 635-639, 2008.
- [15] V. Ilotte, "Die casting for chassis components," in Proceedings of the 4th International High Tech Die Casting Conference, Montichiari, Italy, April 2008.
- [16] Z. Brown, C. Barnes, J. Bigelow, and U. S. Contech, "Squeeze cast automotive applications and design considerations," in Proceedings of the 4th International High Tech Die Casting Conference, Montichiari, Italy, April 2008.
- [17] J. P. Papai, Contact heat transfer coefficients in aluminum alloy die casting: an experimental and numerical investigation? [Ph.D. thesis], The Ohio State University, 1994.
9. Copyright:
- This material is a paper by "Mohammad Sadeghi and Jafar Mahmoudi": Based on "Experimental and Theoretical Studies on the Effect of Die Temperature on the Quality of the Products in High-Pressure Die-Casting Process".
- Source of paper: [doi:10.1155/2012/434605]
This material was created to introduce the above paper, and unauthorized use for commercial purposes is prohibited. Copyright © 2025 CASTMAN. All rights reserved.