This introduction paper is based on the paper "Efficiency and Cost Tradeoffs Between Aluminum and Zinc-Aluminum Die Cast Heatsinks" published by "[Journal/academic society of publication not specified in the paper]".
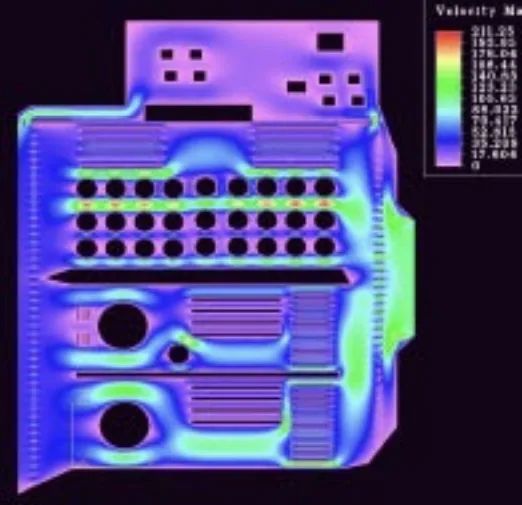
1. Overview:
- Title: Efficiency and Cost Tradeoffs Between Aluminum and Zinc-Aluminum Die Cast Heatsinks
- Author: Kurtis P. Keller
- Year of publication: [Not specified in the paper]
- Journal/academic society of publication: [Not specified in the paper]
- Keywords: Heatsink, Die Casting, Aluminum, Zinc-Aluminum, Thermal Conductivity, Cost Analysis, Electronic Cooling, PixelFlow
2. Abstract:
High purity aluminum has always been a good heatsink material for removing heat from electronic components. However, the manufacturing of specialty shaped, non-extrusion based heatsinks, causes many material-based problems. High purity aluminum is very difficult to die cast and impurities must normally be added to aid in the die casting process. These small amounts of impurities cause the thermal conduction coefficient of the material to drop almost in half. The resultant thermal conductivity closely matches that of many zinc die cast materials. A cost and performance analysis comparing die cost, per piece cost, efficiency drop between high and low power densities will be examined between various commercial zinc, zinc-aluminum, and aluminum die casting materials. This examination was performed in connection with the design of the cooling system for UNC's PixelFlow, the worlds fastest graphics computer that utilizes 44 custom chips, 5 watts to 55 watts per die. This 9 kW air-cooled system is very compact, and measures 18" by 42". Short, high-speed signal path lengths require an innovative and cost effective method of removing heat between the closely spaced chips and cards.
3. Introduction:
Increasing power densities in computers and electronic equipment diminish the effectiveness and choices for off-the-shelf heatsinks. While simple clip-on heatsinks suffice for low power (up to 3 watts), higher power components like processors require more expensive cast or extruded fin heatsinks. The most demanding applications may need liquid, conduction, or immersion cooling, which are often cost-prohibitive. Modern electronic packaging pushes the limits of affordable air cooling, necessitating careful attention to airflow and heatsink design to remain commercially viable. Off-the-shelf extrusions, while inexpensive, have shortcomings in high-density applications due to relatively low thermal conductivity for their surface area and potential for significant back pressure when used in series (as illustrated by cooling issues on an early PixelFlow board design, Figure 2). Custom-designed heatsinks become necessary when off-the-shelf options are unavailable or inadequate. The paper specifically addresses the cooling challenges in UNC's PixelFlow graphics computer, which required a cost-effective custom solution (Figure 3) costing $0.73 per unit compared to $2.50 for an ineffective off-the-shelf design.
4. Summary of the study:
Background of the research topic:
The trend of increasing power density in electronic components necessitates more advanced thermal management solutions than simple off-the-shelf heatsinks. Air cooling remains the preferred method for cost reasons, but its effectiveness is challenged in densely packed systems. Custom heatsink design becomes crucial.
Status of previous research:
Standard solutions include off-the-shelf extruded aluminum heatsinks, which are cost-effective but limited by 2D geometry, thermal performance, and airflow blockage (back pressure) in dense configurations. More expensive options like liquid or conduction cooling exist but are often not commercially viable for mainstream products. Custom options include machined parts, cast/machined fins, and fully cast heatsinks.
Purpose of the study:
To conduct a cost and performance analysis comparing various die-cast materials (zinc, zinc-aluminum, aluminum) for custom heatsinks. The study aims to evaluate the trade-offs between thermal efficiency (primarily thermal conductivity) and cost (tooling, piece price) in the context of designing a cooling solution for a high-power, densely packed system (UNC's PixelFlow).
Core study:
The study focuses on the suitability of die casting for creating complex, 3D-shaped heatsinks optimized for specific airflow conditions, contrasting this with simpler 2D extrusions. It examines the material properties relevant to heatsink performance and manufacturing:
- Aluminum: High-purity extruded aluminum offers excellent thermal conductivity (160-180 W/m°C). However, die-cast aluminum requires additives (like silicon) and suffers from porosity, reducing conductivity significantly (approx. 96 W/m°C). Processes like hot isostatic pressing can improve conductivity but are slow and costly. Aluminum also requires plating, adding cost.
- Zinc and Zinc-Aluminum Alloys: Standard zinc (Zamak 3) has conductivity (~113 W/m°C) better than die-cast aluminum. Zinc-aluminum alloys (ZA-8, ZA-12, ZA-27) offer improved properties. ZA-8 (~115 W/m°C) provides conductivity comparable to die-cast aluminum but with significant advantages: lower porosity, better castability (allowing cheaper, non-steel molds and faster cycles), no need for plating, a coefficient of thermal expansion closely matching chip carriers, and greater strength. ZA-27 offers higher conductivity (~125 W/m°C) but has a less favorable thermal expansion coefficient.
- Brass: Considered for its low coefficient of thermal expansion but has poor thermal conductivity (61 W/m°C), casting difficulties similar to aluminum, and high cost.
- Cost vs. Performance Trade-off: The study questions the necessity of maximizing thermal conductivity in medium-power applications (3-7W), where the temperature difference between using a high-conductivity material versus a slightly lower one (e.g., zinc-aluminum) might be minimal (1-2°C) but the cost savings substantial. It highlights that the case-to-air thermal resistance is often the dominant factor, not the internal resistance of the heatsink.
- Manufacturing Advantages: Die casting allows for complex 3D shapes (like the airfoil design in Figure 3) that can optimize airflow and cooling efficiency, potentially outweighing the lower bulk thermal conductivity compared to extruded aluminum. Zinc alloys offer manufacturing cost advantages due to lower melting points.
5. Research Methodology
Research Design:
The study employs a comparative analysis methodology, evaluating different heatsink materials (primarily die-cast options vs. aluminum extrusion benchmark) based on thermal performance, manufacturing characteristics, and cost. It uses a case-study approach, drawing heavily on the design requirements and experiences from the UNC PixelFlow graphics supercomputer project.
Data Collection and Analysis Methods:
Data was gathered on material properties (thermal conductivity, thermal expansion, density, melting point, tensile strength) for various alloys (Zamak 3, ZA-8, ZA-27, Aluminum 357, Aluminum 380, Brass 360). Cost data (tooling, material, piece price for a 5,000-unit run) was collected, likely through quotes from die casters (as implied by Table Notes). Thermal performance was assessed, including analysis of temperature gradients (e.g., Figure 2 - Heatsink Temperature Gradient) and likely informed by thermal simulations (FEA is mentioned for chassis airflow analysis, Figure 4). A "Heatsink Material Comparison Table" was compiled to summarize key properties and costs.
Research Topics and Scope:
The research focuses on air-cooled, custom die-cast heatsinks for electronic components, particularly in high-density, high-power applications. The scope includes a direct comparison of aluminum, zinc, and zinc-aluminum die-casting alloys, considering thermal efficiency, cost-effectiveness, manufacturability, and mechanical properties (like CTE match and strength). The analysis is framed by the practical requirements of cooling the PixelFlow system (44 chips, 5-55W each).
6. Key Results:
Key Results:
- Die casting aluminum requires impurities (e.g., silicon) that significantly reduce its thermal conductivity (to ~96 W/m°C) compared to high-purity extruded aluminum (160-180 W/m°C).
- Zinc-aluminum alloys, particularly ZA-8, offer thermal conductivity (~115 W/m°C) comparable to or better than die-cast aluminum, but with significant cost and manufacturing advantages (lower tooling cost, faster cycles, no plating needed).
- ZA-8 also provides a closer match for the coefficient of thermal expansion (CTE) to most chip carriers compared to aluminum, reducing thermal stress.
- Zinc-aluminum parts are stronger than aluminum, reducing the risk of fin damage.
- For many applications, the small theoretical thermal performance gain from using higher conductivity materials (like extruded aluminum) may not justify the higher cost, especially when case-to-air resistance dominates and die casting allows for more efficient 3D shapes.
- A larger heatsink cast in zinc or zinc-aluminum can compensate for lower conductivity while remaining cheaper than alternatives like poured aluminum.
- The "Heatsink Material Comparison Table" provides quantitative data comparing Zamak 3, ZA-8, ZA-27, poured Al 357, die-cast Al 380, and Brass 360 across key metrics. For a specific 0.34 in³ heatsink example (Figure 1) in a 5,000-unit run, ZA-8 ($0.41/part) was significantly cheaper than die-cast aluminum ($1.20/part) or poured aluminum ($1.25/part).
Figure Name List:
- Figure 1 - Heatsink
- Figure 2 - Early fin style heatsink
- Figure 3 - Airfoil Zinc/AL Heatsink
- Figure 4 - Velocity Profile
- Figure 2 - Heatsink Temperature Gradient (Note: The paper labels this figure as "Figure 2", distinct from the earlier "Figure 2 - Early fin style heatsink")
- Heatsink Material Comparison Table
7. Conclusion:
When custom heatsinks are required due to economics of scale or specific performance needs, extrusion is not the only option. Die casting enables more efficient and effective 3D heatsink geometries compared to 2D extrusions. While no common casting material matches the thermal conductivity of high-purity extruded aluminum, zinc-aluminum materials like ZA-8 are sufficiently close. The thermal conductivity advantages of a 3D cast design can outweigh the perceived impedance difference from the material itself. Furthermore, zinc-aluminum parts closely match the thermal expansion of most chip carriers and are stronger than aluminum, preventing damage to exposed fins. Therefore, low-cost, high-performance zinc-aluminum die cast heatsinks are recommended for high-power production designs where weight is not a critical factor.
8. References:
- Dash, Glen A., Editor, Compliance Engineering, 1993 Reference Guide, Boxboro, MA, Compliance Engineering, 1993.
- Dow Chemical, “Comparisons of Typical Casting Alloys," data sheets
- Flinn, Richard A. and Paul K. Trojan, Engineering Materials and Their Applications, Boston, Houghton Mifflin Company, 1981
- Keller, Kurtis and John Poulton, “Commercial Packaging Solutions for a Research Oriented Graphics Supercomputer," Advances in Electronic Packaging (Proceedings of the 1995 ASME / JSME Conference on Electronic Packaging), pp. 53 -58.
- Ozisik, Necati M., Heat Transfer a Basic Approach, McGraw-Hill, Inc. 1985.
- Tummala, Rao R. and Eugene J. Rymaszewski, Editors, Microelectronics Packaging Handbook, New York, Van Nostrand Reinhold, 1989.
- Yamaji, Y., Y. Atsumi and Y. Hiruta, "Thermal Characterization of LSI Packages Mounted on PC Boards: Evaluation of the Thermal Effects of PC Boards," Advances in Electronic Packaging (Proceedings of the 1992 ASME / JSME Conference on Electronic Packaging), pp. 199 - 205.
9. Copyright:
- This material is a paper by "Kurtis P. Keller". Based on "Efficiency and Cost Tradeoffs Between Aluminum and Zinc-Aluminum Die Cast Heatsinks".
- Source of the paper: [DOI URL not specified in the paper]
This material is summarized based on the above paper, and unauthorized use for commercial purposes is prohibited.
Copyright © 2025 CASTMAN. All rights reserved.