The content of this introduction paper is based on the article "Effects of Rotor Bar and Cage Numbers Considering Al and Cu Conductors on The Performance of Asynchronous Traction Motors in Hybrid Electric Vehicles" published by ICEMG 2023.
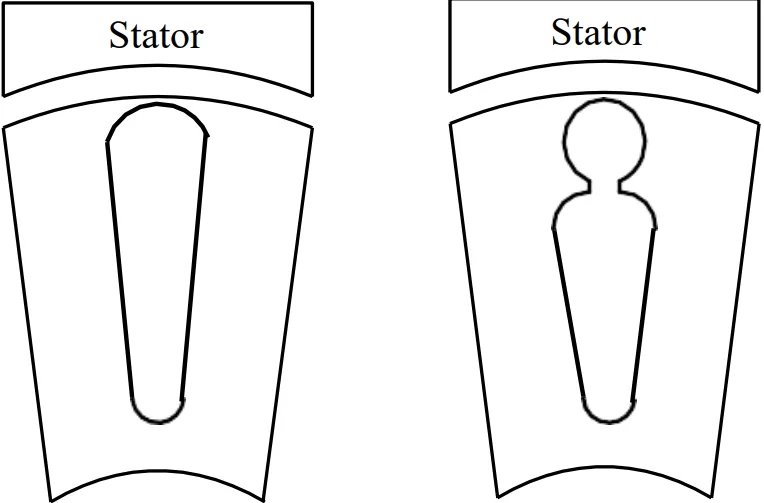
1. Overview:
- Title: Effects of Rotor Bar and Cage Numbers Considering Al and Cu Conductors on The Performance of Asynchronous Traction Motors in Hybrid Electric Vehicles
- Author: A. Mousaei, N. Rostami, M. B. Bannae Sharifian
- Year of publication: 2023
- Journal/academic society of publication: The Second International Conference on Electrical Motors and Generators - ICEMG 2023
- Keywords: Electric Vehicle, Squirrel Cage, Traction Motor, Rotor Slots, Starting Torque.
2. Abstract:
Electric vehicles offer an unmatched experience thanks to their torque profiles. They must be optimized when considering intracity driving cycles (frequent start-stop) by dealing sensitively with the efficiency/performance relationship. Asynchronous motors are commonly used in electric vehicles. Parameters like stator/rotor geometry, number of slots, and materials used are incredibly important in the efficiency/performance relationship. This study has focused on the effect of the change in the number of stator/rotor slots on motor performance by designing an asynchronous motor to be used in primarily urban-use electric vehicles. Afterward, the effect of copper or aluminum cage materials on motor performance was obtained with single- and double-layered squirrel cage structures. The first designed motor has an initial torque value of 96.26 Nm while the optimized motor has a value of 115.34 Nm with its efficiency value and thermal limits being developed by 19.82% without changing. According to the analysis results, the squirrel-cage asynchronous motor with a double-layer, 34/46 structure, and aluminum material exhibited the best performance with initial torque.
3. Introduction:
The development of technology has enabled the design of highly efficient and environmentally friendly products, with electric vehicles (EVs) being a prominent example. Asynchronous Motors (AMs) are widely utilized in EVs due to their advantages such as low maintenance, easy controllability, high-temperature tolerance, easy production, and low costs. While various studies have compared electric motors for EVs, and investigated rotor slot structures and materials, a comprehensive study considering the combined effects of stator/rotor slot numbers, single/double cage structures, and aluminum/copper rotor conductors was lacking. This paper aims to address this gap by optimizing the starting torque and nominal operating efficiency of an asynchronous motor for urban EVs.
4. Summary of the study:
Background of the research topic:
The increasing demand for efficient and environmentally friendly transportation has driven the development of EV technology. Asynchronous motors are crucial components in EV drive systems, and their performance is significantly influenced by design parameters such as stator/rotor geometry, number of slots, and material selection. Optimizing these parameters is essential for enhancing the efficiency and performance of EV traction motors, particularly for urban driving cycles characterized by frequent start-stop operations.
Status of previous research:
Previous research has explored various aspects of asynchronous motor design for EVs, including comparisons of different motor types, optimization of air gap and rotor bar geometry, and analysis of single and double-cage rotor structures. Studies have also investigated the impact of rotor slot structure on current harmonics and the effect of varying rotor slot numbers on motor performance. However, a gap exists in the literature regarding a comprehensive analysis that simultaneously considers the effects of stator/rotor slot number combinations, rotor cage structure (single vs. double), and rotor conductor material (aluminum vs. copper).
Purpose of the study:
The primary purpose of this study is to optimize the starting torque and nominal operating efficiency of an asynchronous motor specifically designed for urban electric vehicles. The research investigates different combinations of stator-rotor slot numbers and compares single and double cage rotor structures. Furthermore, it examines the impact of using aluminum and copper as rotor conductor materials on the overall motor performance. The study aims to identify the most suitable rotor structure for asynchronous motors in EV applications by considering these variables in conjunction.
Core study:
The core of this study involves designing and analyzing asynchronous motors with varying stator/rotor slot number combinations (36/26, 36/28, 36/30, 36/34, 36/44, 36/46) and both single and double squirrel cage rotor structures. The analysis is conducted using both aluminum and copper as cage materials. The performance metrics evaluated include efficiency, rated torque, and starting torque. The study utilizes Finite Element Analysis (FEA) to simulate and compare the electromagnetic performance of different motor configurations. The initial design is based on NEMA Class B motor characteristics, and the optimization focuses on maximizing starting torque and maintaining high efficiency.
5. Research Methodology
Research Design:
The research employs a comparative simulation-based design study. Initial motor design parameters were established using analytical methods. Different configurations of asynchronous motors were designed by varying the number of rotor slots and the cage structure (single and double layer). Two materials, aluminum and copper, were considered for the squirrel cage. The stator slot number was kept constant at 36. The rotor slot numbers investigated were 26, 28, 30, 34, 44, and 46. Both single and double cage rotor designs were analyzed for each slot number combination and material.
Data Collection and Analysis Methods:
Performance data was collected through Finite Element Analysis (FEA) simulations. The 2D and 3D models of the motors were created for simulation. The key performance indicators extracted from the simulations include efficiency, rated torque, starting torque, and rotor ohmic losses. The torque-speed characteristics and phase current waveforms were also analyzed. The results were then compared across different rotor slot numbers, cage structures, and conductor materials to determine the optimal configuration.
Research Topics and Scope:
The research focuses on the electromagnetic performance analysis of squirrel-cage asynchronous motors for electric vehicle traction applications. The scope includes:
- Investigating the effect of varying rotor slot numbers on motor performance for both single and double cage rotor structures.
- Comparing the performance of aluminum and copper rotor conductors in both single and double cage configurations.
- Optimizing the rotor design to enhance starting torque while maintaining high efficiency for urban EV applications.
- Analyzing torque-speed characteristics and magnetic flux density distributions for different motor designs.
6. Key Results:
Key Results:
- Optimal Rotor Configuration: The squirrel-cage asynchronous motor with a double-layer, 34/46 structure, and aluminum material exhibited the best performance in terms of initial torque.
- Starting Torque Improvement: The optimized motor (double-cage 36/46 aluminum) achieved a starting torque of 115.34 Nm, a 19.82% increase compared to the initial single-cage 36/30 design (96.26 Nm), without compromising efficiency.
- Efficiency: Efficiency values remained relatively consistent across different rotor slot numbers for both single and double cage designs. The optimized double-cage 36/46 aluminum motor maintained an efficiency of 86.6%, similar to the initial design.
- Material Impact: Motors with aluminum cages exhibited higher rotor resistance and starting torque compared to copper cage motors. Copper cage motors showed lower rotor losses but lower starting torque.
- Slot Number Effect: Increasing the number of rotor slots, while keeping stator slots constant, generally increased the starting torque for both single and double cage designs. Double cage rotor motors demonstrated higher starting torque compared to single cage motors with the same stator/rotor slot combination.
- Flux Density: FEA analysis showed that the optimized design maintained appropriate flux densities in the core material, with a reduced flux density in rotor teeth compared to the initial design (Figure 7).
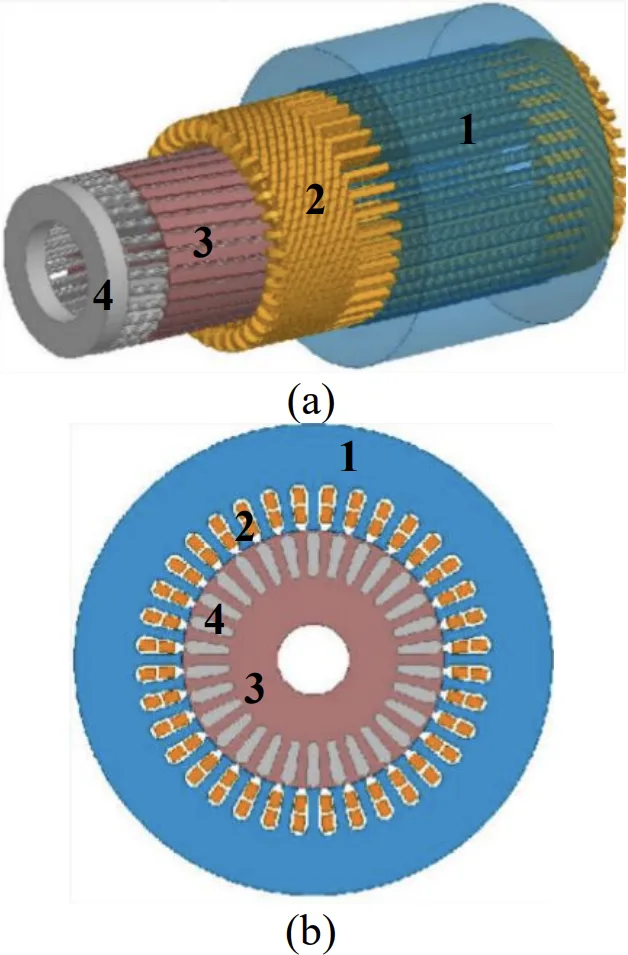
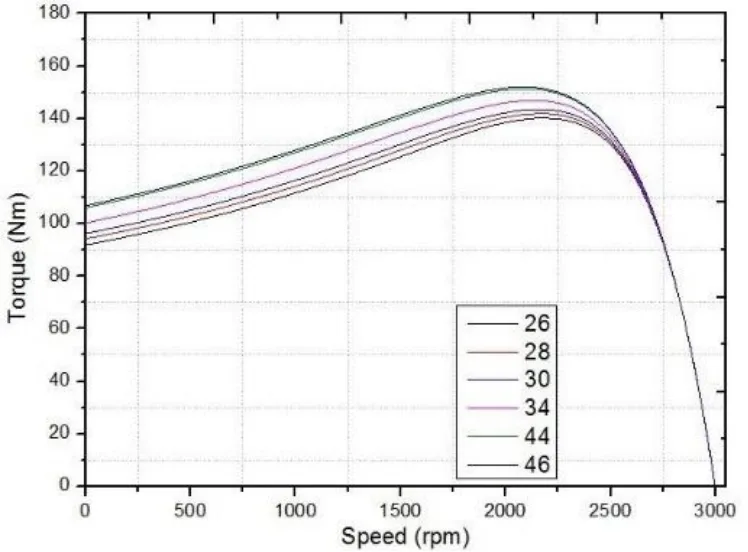
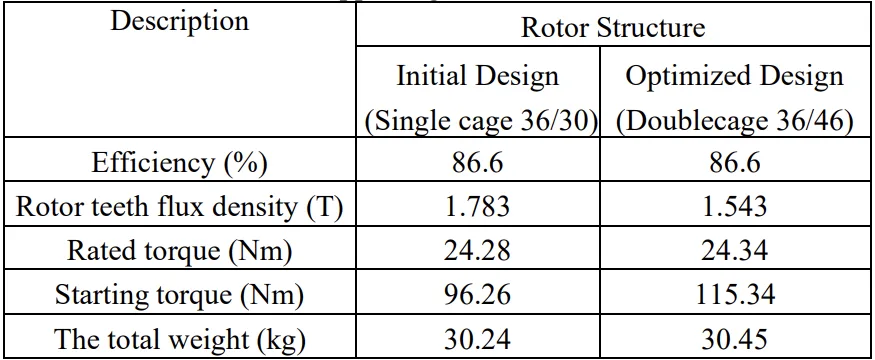
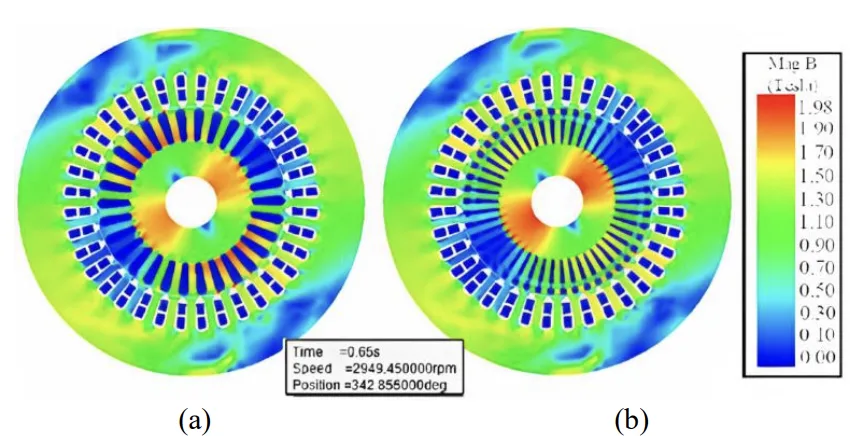
Figure Name List:
- Figure 1. Slot structure
- Figure 2. Model of Initial Design (1-Stator, 2-Winding, 3-Rotor, 4- Squirrel Cage): a) 2D, b) 3D
- Fig. 3. Torque-speed characteristic curves in a single cage rotor
- Fig. 4. Torque-speed characteristic curves in a double cage rotor
- Fig. 5. Torque-speed characteristic curves a) single cage, b) double cage
- Fig. 6. Motor model a) initial design, b) optimized motor
- Fig. 7. Magnetic flux density distributions, a) initial design, b) optimized design
- Fig. 8. Torque-speed characteristic curves
- Fig. 9. Phase current waveforms of the motors in transient-state
7. Conclusion:
This study demonstrates that optimizing the rotor design, specifically by employing a double-cage structure with a 36/46 stator/rotor slot combination and utilizing aluminum as the cage material, significantly enhances the starting torque of asynchronous motors for electric vehicles. The optimized design achieves a substantial increase in starting torque while maintaining high efficiency. The findings suggest that double-cage aluminum rotor asynchronous motors with carefully selected slot numbers are well-suited for urban EV applications requiring frequent start-stop operations and high starting torque. The research provides valuable insights into the trade-offs between rotor design parameters and motor performance, offering guidance for the design of efficient and high-performance asynchronous traction motors.
8. References:
- [1] Ocak, C., “Design, Analysis and Application of a New Three Level Brushless DC Motor for Electric Vehicles", Ph. D. Thesis, Graduate School of Natural and Applied Sciences, Gazi University, Ankara, 2013.
- [2] Tousizadeh, M., Che, H.S., Selvaraj, J., Rahim, N.A., Ooi, B. T., “Performance Comparison of Fault-Tolerant Three-Phase Induction Motor Drives Considering Current and Voltage Limits", IEEE Transactions on Industrial Electronics, Vol. 66, No. 4, pp. 2639-2648, April 2019.
- [3] Nour, M., Said, S.M., Ali, A., and Farkas, C., "Smart Charging of Electric Vehicles According to Electricity Price", International Conference on Innovative Trends in Computer Engineering, Aswan, Egypt, 2019.
- [4] Hori, Y., "Future Vehicle Driven by Electricity and Control-Research on Four-Wheel- Motored "UOT March II", IEEE Transaction on Industrial Electronics, 51(5), pp. 954-962, 2004.
- [5] A. Mousaei and M. B. B. Sharifian, "Design and optimization of a linear induction motor with hybrid secondary for textile applications," 2020 28th Iranian Conference on Electrical Engineering (ICEE), 2020, pp. 1-6, doi: 10.1109/ICEE50131.2020.9260773.
- [6] Ünlü, N., Karahan, Ş., and Tür, O., “Electric Vehicles", Energy Systems and Environmental Research Institute, 6-22, pp. 42-100, 2003.
- [7] Dorrell, D.G., Popescu, M., Evans, L., Staton, D.A., and Knight, A.M., “Comparison of Permanent Magnet Drive Motor with a Cage Induction Motor Design for a Hybrid Electric Vehicle", 2010 International Power Electronics Conference, pp. 1807-1813, 2010.
- [8] Grilo, N., Sousa, D.M., and Roque, A., “AC motors for application in a commercial electrical vehicle: Designing aspects", 16th IEEE Mediterranean Electrotechnical Conference, pp.277-280, March 2012.
- [9] Ehsani, M., Gao, Y., and Gay, S., “Characterization of electric motor drives for traction applications”, The 29th Annual Conference of the Industrial Electronics Society, pp. 891-896, 2003.
- [10] Nanda, G., and Kar, N.C., “A survey and comparison of characteristics of motor drives used in electric vehicles", Canadian Conference on Electrical and Computer Engineering, pp. 811-814, 2006.
- [11] Tiecheng, W., Ping, Z., Qianfan, Z., and Shukang, C., "Design Characteristic of the Induction Motor Used for Hybrid Electric Vehicles", 12th Symposium on Electromagnetic Launch Technology, pp. 523-527, 2005.
- [12] Damiano, A., Gatto, G., Marongiu, I., Porru, M., Serpi, A., "Real-time control strategy of energy storage systems for renewable energy sources exploitation," IEEE Transactions on Sustainable Energy, vol. 5, no. 2, pp. 567-576, 2014.
- [13] A. Mousaei, M. B. Bannae Sharifian and N. Rostami, "Direct Thrust Force Control (DTFC) of Optimized Linear Induction Motor with Super Twisting Sliding Mode Controller (STSMC)," 2021 12th Power Electronics, Drive Systems, and Technologies Conference (PEDSTC), 2021, pp. 1-5, doi: 10.1109/PEDSTC52094.2021.9405903.
- [14] Dedid, C., Soebagio, M., Purnomo, M.H., "Induction motor speed control with fast response using the Levenberg Marquardt method for electric cars,” International Journal of Computer Applications, vol. 42, no. 13, pp. 14-18, 2012.
- [15] Xue, X. D., Cheng, K. W. E. and Cheung, N. C., "Selection of electric motor drives for electric vehicles", Australasian Universities Power Engineering Conference, Hong Kong, pp. 170-175, 2008.
- [16] Guzinski, J. and Abu-Rub, H., "Sensorless induction motor drive for electric vehicle application", International Journal of Engineering, Science and Technology, 2 (10), pp. 20-34, 2010.
- [17] A. Mousaei, M. B. Bannae Sharifian and N. Rostami, "An Improved Predictive Current Control Strategy of Linear Induction Motor Based on Ultra-Local Model and Extended State Observer," 2022 13th Power Electronics, Drive Systems, and Technologies Conference (PEDSTC), 2022, pp. 12-18, doi: 10.1109/PEDSTC53976.2022.9767535.
- [18] Kim, K.T., Song, H.E., and Park, G.S., "A study on the design of induction motor in low speed urban electric vehicle", IEEE Transportation Electrification Conference and Expo, pp. 1-4, Korea, 2016.
- [19] Li, K., Cheng, G., Sun, X., Yang, Z., Fan, Y., "Performance optimization design and analysis of bearingless induction motor with different magnetic slot wedges", Results in Physics, 12, pp. 349-356, 2019.
- [20] Yahaya, E. A., Omokhafe, T., Agbachi, E. O., James, A. G., "Advantage of Double Cage Rotor over Single Cage Rotor Induction Motor", Innovative Systems Design and Engineering, Vol.6, No.12, pp. 1-4, 2015.
- [21] Zhou, G. Y., Shen, J. X., “Current Harmonics in Induction Machine with Closed-Slot Rotor", IEEE Transactions on Industry Applications, Vol. 53, No. 1, pp. 134- 142, 2017.
- [22] Gyftakis, K. N., Kappatou, J., “The Impact of the Rotor Slot Number on the Behaviour of the Induction Motor", Advances in Power Electronics, Vol. 2013, pp. 1-9, 2013.
- [23] Elhaija, W.A., Ghorbanian, V., Faiz, J., Nejadi-Koti, H., "Significance of Rotor Slots Number on Induction Motor Operation under Broken Bars", IEEE International Electric Machines and Drives Conference, Miami, May 2017.
- [24] Emadi, A., "Energy-Efficient Electric Motors", Marcel Dekker, New York, 2005.
- [25] Lee, G., Min, A., and Hong, J.P., "Optimal Shape Design of Rotor Slot in Squirrel-Cage Induction Motor Considering Torque Characteristic", IEEE Transactions on Magnetics, Vol. 49, No. 5, pp. 2197-2200, 2013.
- [26] Arash Mousaei, Nasim Bahari, Guo Mieho. Artificial Neural Networks (ANN) of Proposed Linear Induction Motor with Hybrid Secondary (HLIM) Considering the End Effect. American Journal of Electrical and Computer Engineering. Vol. 5, No. 1, 2021, pp. 32-39. doi: 10.11648/j.ajece.20210501.15.
- [27] Vishnu Murthy, K.M., “Computer-Aided Design of Electrical Machines”, BS Publications, Hyderabad, 2008, ISBN:978-81-7800-146-3.
- [28] Saygın, A., Ocak, A., Dalcalı, A., Çelik, E., "Optimum Rotor Design of Small PM BLDC Motor Based on High-Efficiency Criteria", ARPN Journal of Engineering and Applied Sciences, Vol. 10, No. 19, pp. 9127-9132, 2015.
- [29] Dalcalı, A., Ocak, C., "Effect of Different Magnet Materials on The Performance of Surface Mounted Direct Drive PMSM", Journal of Awareness, 3, pp. 217-224, 2018.
- [30] Sundaram, M., Mohanraj, M., Varunraj, P., Kumar, T.D., Sharma, S., "FEA Based Electromagnetic Analysis of Induction Motor Rotor Bars With Improved Starting Torque For Traction Applications", Automatic Control, Mechatronics and Industrial Engineering, pp. 103-110, Taylor&Francis Group, London, ISBN:987-1-138-60427-8.
- [31] Popescu, M., Goss, J., Staton, D.A., Hawkins, D., Chong, Y.C., Boglietti, A., "Electrical Vehicles-Practical Solutions for Power Traction Motor Systems", IEEE Transactions on Industry Applications, Vol. 54, No. 3, pp. 2751-2762, May/June 2018.
- [32] A. Mousaei, M. B. Bannae Sharifian and N. Rostami, "An Improved Fuzzy Logic Control Strategy of an Optimized Linear Induction Motor Using Super Twisting Sliding Mode Controller," 2022 13th Power Electronics, Drive Systems, and Technologies Conference (PEDSTC), 2022, pp. 1-5, doi: 10.1109/PEDSTC53976.2022.9767465.
- [33] Ünlükaya, E., Yetgin, A.G., Çanakoğlu, A.I., and Turan, M., "Effect of Rotor Slot Shapes on Induction Motor Performance", Symposium on Electrical-Electronic-Computer and Biomedical Engineering, pp. 168-172, Bursa, November 2014.
- [34] Besnerais, J. L., Lanfranchi, V., Hecquet, M., Brochet, P., "Optimal Slot Numbers Combination for Magnetic Noise Reduction in Variable-Speed Induction Motors", IEEE Transactions on Magnetics, Vol. 45, No. 8, pp. 3131-3136, 2009.
- [35] Finley, W.R., Hodowanec, M.M., “Selection of Copper vs. Aluminum Rotors for Induction Motors" Industry Applications Society Forty-Seventh Annual Petroleum and Chemical Industry Conference, pp. 1-11, 2000.
- [36] Gieras, J.F, “Advancements in Electric Machines", Springer, 2008.
- [37] Brush E.F., Cowie, J.G., Peters, D.T., and Van Son, D.J., "Die-cast Copper Motor Rotors: Motor Test Results, Copper Compared to Aluminum", Energy Efficiency in Motor Driven Systems, pp. 136-143, 2003.
9. Copyright:
- This material is a paper by "A. Mousaei, N. Rostami, M. B. Bannae Sharifian". Based on "Effects of Rotor Bar and Cage Numbers Considering Al and Cu Conductors on The Performance of Asynchronous Traction Motors in Hybrid Electric Vehicles".
- Source of the paper: https://ieeexplore.ieee.org/xpl/conhome/10109952/proceeding
This material is summarized based on the above paper, and unauthorized use for commercial purposes is prohibited.
Copyright © 2025 CASTMAN. All rights reserved.