This article introduces the paper "The Aluminium Automotive MANUAL" published by the European Aluminium Association. It focuses on the applications of die casting technology in manufacturing car body and body components using aluminum.
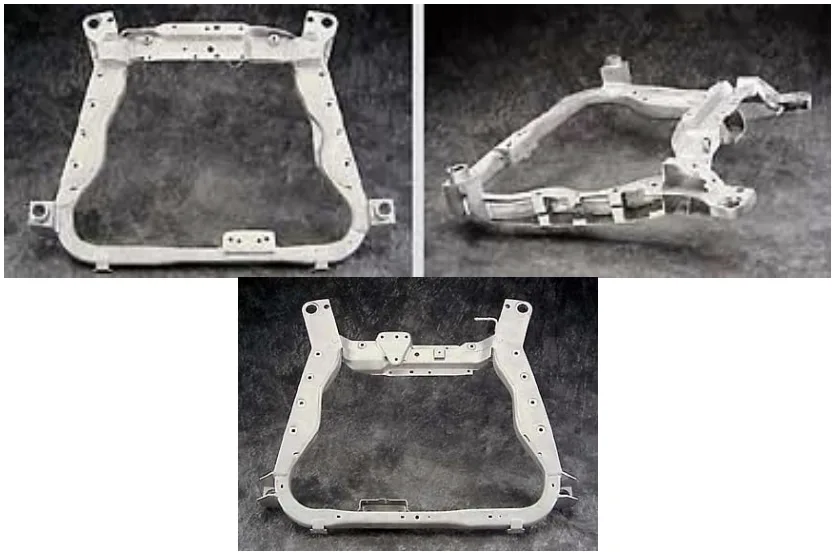
1. Body Components and Modules:
- Integration: Aluminum components can be integrated into steel body structures using various joining methods.
- Considerations: Galvanic corrosion between aluminum and steel must be avoided through design and protection. Differences in thermal expansion coefficients of steel and aluminum need to be considered in the design process.
- Lacquering: Installation of aluminum components into lacquered body-in-white (BIW) generally presents no problems under normal service conditions. Integrating aluminum components ahead of lacquering requires preventing residual internal stresses or geometrical distortions.
2. Engine Cradles and Engine Mounts:
- Function: Engine cradles provide structural support for subsystems, locate components (powertrain, front suspension, steering system), protect powertrain components, and contribute to structural rigidity.
- Lightweighting: Aluminum engine cradles offer weight reduction opportunities.
- Examples:
- Sheet-intensive aluminum engine cradle (Ford P2000): Assembled using castings, hydroformed tubes, and formed sheet parts. Weight reduction from 21.7 kg (steel) to 14.4 kg (aluminum).
- Extrusion-based engine cradle (General Motors): Weight reduction of 32% compared to steel.
- Extrusion-based engine cradle (Chevrolet Monte Carlo and Impala): Consisted of machined extrusions and sheet stampings assembled by robotic MIG welding.
- Cast aluminum engine cradle (Mercedes-Benz C class (C204)): Produced from Silafont®-36 alloy with age hardening treatment.
- Aluminum engine cradle (Cadillac CTS): Combining a large hollow casting with extrusions.
- Bimetallic engine cradle (Cosma): Steel tubes with aluminum A356 cast over the tube ends.
- Cast aluminum front cross member (Porsche Panamera): (Photo: GF Automotive).
- Cast aluminum engine brackets for engine mounts. Examples:
- Aluminium engine bracket produced by high pressure die casting: The bracket shown above has a weight of 1.5 kg and is produced from the alloy Silafont®-36 (AISI9MgMn) for the BMW 6-cylinder engine N52. It is used in the as-cast state. The application of high quality aluminium casting alloys like Silafont®-36 is necessary as the brackets for modern, high-performance engines have to fulfil highest requirements with respects to dynamic loads (i.e. the cast material must show high fracture toughness).
- Other examples of cast aluminium engine brackets(Photo: Aluminium Rheinfelden)
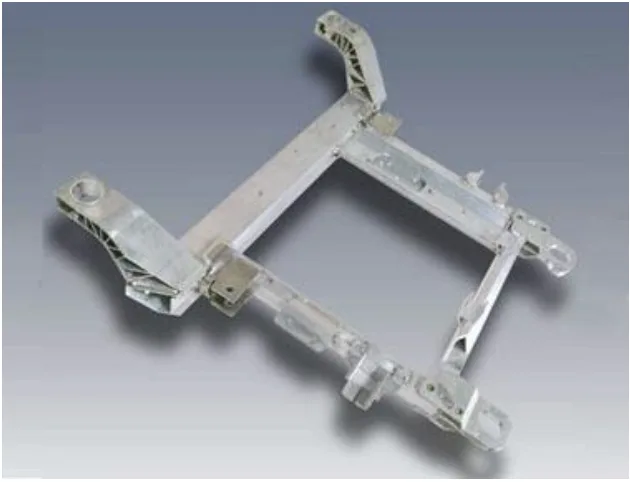
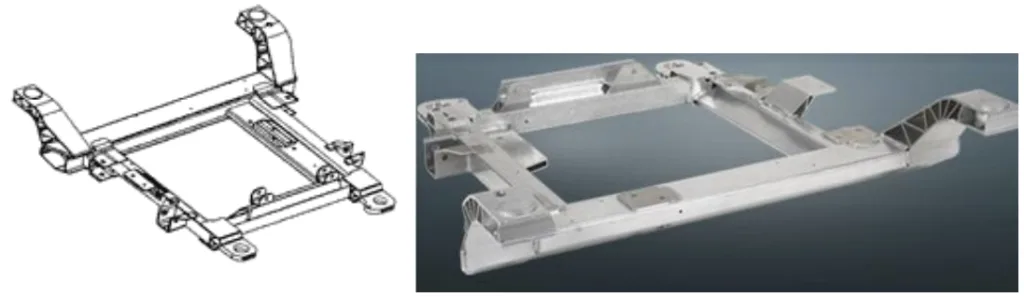
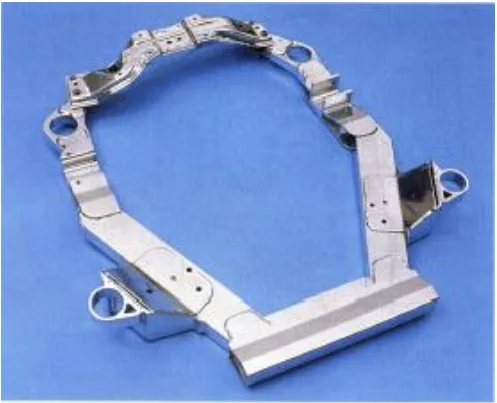
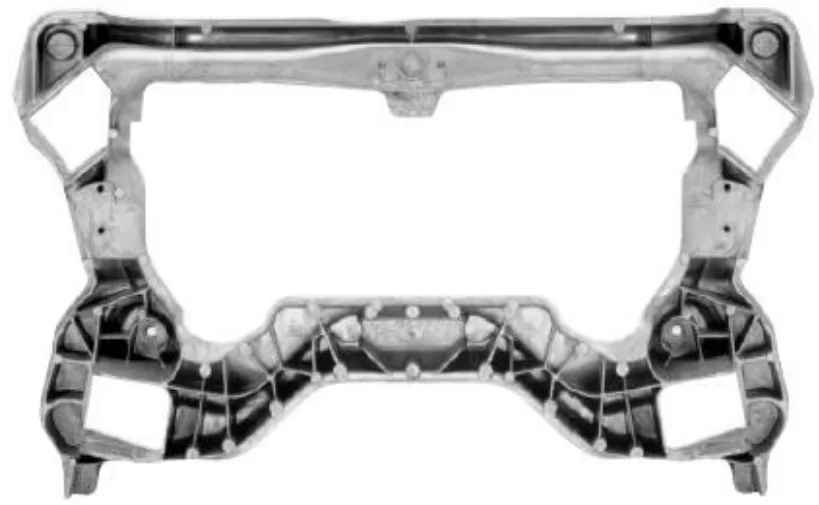
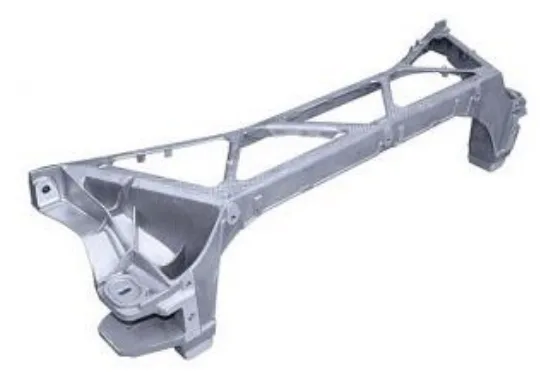
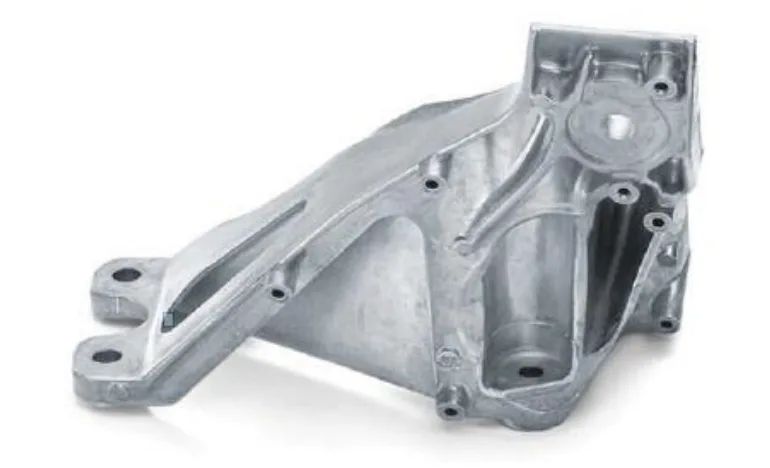
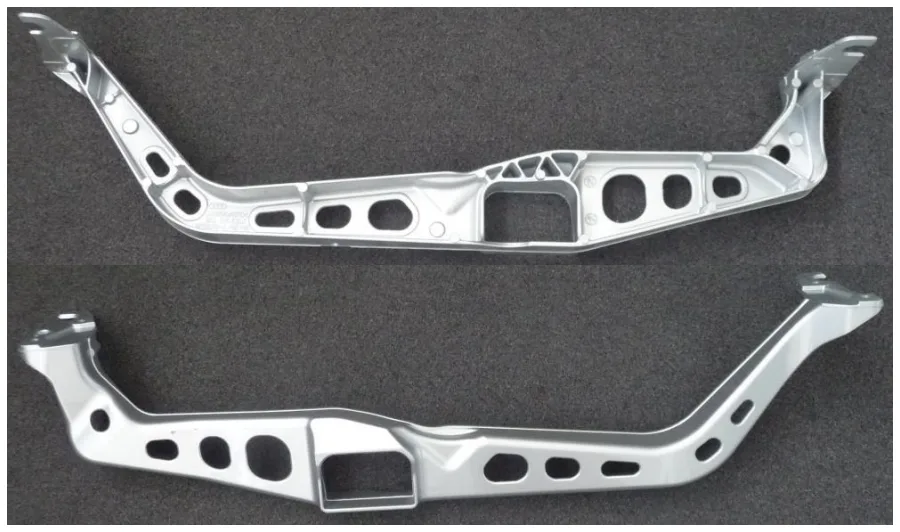
3. Suspension Strut Domes:
- Function: Attaches suspension strut to the vehicle, supports shock absorbers and springs, and may contain a steering pivot.
- Manufacturing: Aluminum casting can replace multi-piece steel assemblies, offering weight reduction and eliminating manufacturing steps.
- Examples:
- Suspension strut dome produced by vacuum high pressure die casting (alloy: GD-AlSi10Mg (A239)).
- Aluminum suspension strut dome for BMW 5 series models (alloy AlMg5Si2Mn).
- Aluminum suspension strut dome for Porsche Panamera (alloy: AlMg5Si2Mn) with structure arm connecting to the A pillar.
4. Front End Carriers:
- Function: Houses front-end components (headlights, radiator, cooling fan), contributes to safety, and affects torsion stiffness.
- Materials: Traditionally steel or aluminum, now often mixed material designs.
- Examples:
- Front end carrier of the BMW 3 series convertible produced from Silafont®-36 alloy.
- Front end carrier manufactured as a plastic-aluminium composite structure for the Audi TT.
5. Cross Car Beam (Instrument Panel Support):
- Function: Mounts instruments, connects A pillars, and provides structural support.
- Requirements: High structural rigidity and safety performance are needed.
- Benefits: Aluminum instrument panels offer weight reduction compared to steel.
- Examples:
- Cast aluminum cross car beam.
- Extruded instrument panel support (SAPA Aluminium).
- All-aluminium instrument support produced for the VW PQ24 platform.
- Aluminium product forms used in the instrument panel support for the VW PQ24 platform.
- Aluminium cockpit carrier for the Audi A6/A7 (C7)
- Instrument panel support for the Mercedes-Benz A class model.
6. Rear Frame:
- Example:
- In the Corvette ZR-1/LT-1 (C5), the rear frame (which supports the spare wheel and the fuel tank) was assembled using aluminium extrusions of the alloys EN AW-6061 and EN AW-6063.
7. Other Aluminum Components in Body Structure:
- Applications: Floor structure, spare wheel recess, internal dividing walls.
- Examples:
- Trunk recess of the Mercedes-Benz SL (R231) (alloy EN AW-6016)
- Aluminium firewall of the Mercedes-Benz SL (R231).
- Floor structure of the Audi A8 (D4) made from Novelis Fusion™™-AS250.
- Tunnel of the Mercedes-Benz SL (R231) made using a tailor-welded blank.
- Application of the alloy Anticorodal®-300 in T61 temper in the Range Rover (L405).
- B pillar made using a 7xxx series ultra-high strength aluminium alloy.
- Door sill made using an AlMgSi extrusion, used in the Mercedes-Benz SL (R231).
- Rear longitudinal set for the Mercedes-Benz SL (R231) (extrusion alloy: EN AW-6106).
- B post outer set for the Jaguar XK & F type model (EN AW-6014 extrusion and EN AW-5754 attachment).
- Extruded aluminium door sill cover (alloy EN AW-6063).
- Floor structure panel for the Mercedes-Benz SL (R231).
- Cast front aluminium longitudinal member for the Audi A8 (alloy AlSi10MgMnSr).
- Cast aluminium rear longitudinal frame of the Mercedes-Benz SL (R231).