This introductory paper is the research content of the paper ["Development of High Performance Copper Alloy Chill Vent for High Pressure Die Casting"] published by ['International Journal of Mechanical Engineering and Robotics Research'].
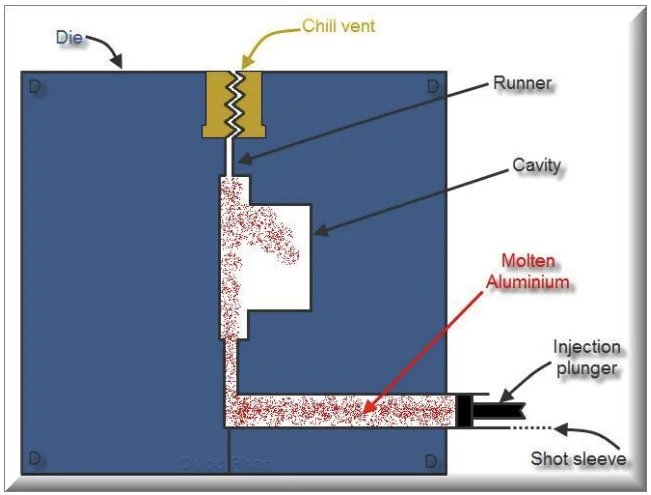
1. Overview:
- Title: Development of High Performance Copper Alloy Chill Vent for High Pressure Die Casting
- Author: Duoc T Phan, Syed H Masood, Syed H Riza, and Harsh Modi
- Publication Year: July 2020
- Publishing Journal/Academic Society: International Journal of Mechanical Engineering and Robotics Research, Vol. 9, No. 7
- Keywords: High pressure die casting; Chill vents; Thermal analysis; Copper alloy; Thermal conductivity; Cooling rates
2. Abstracts / Introduction
In High Pressure Die Casting (HPDC), chill vents are crucial for removing residual air and gases from the mould cavity. This paper investigates the design and development of a high-performance chill vent utilizing a novel copper alloy material, which exhibits superior strength and thermal conductivity compared to conventional tool steel. Finite element analysis is employed to develop and validate a numerical heat transfer model for the chill vent through experimental results. The validated model facilitates a comparative performance analysis between the copper alloy chill vent and a conventional steel chill vent. The findings reveal that altering the chill vent material significantly enhances cooling time, cooling rate, and internal die temperature distribution. Notably, the copper chill vent demonstrates a substantial increase in the cooling efficiency of solidifying aluminium alloy, approximately 158% greater than conventional steel chill vents. The study concludes that employing high strength copper alloy chill vents improves the efficiency and effectiveness of the HPDC process by enabling rapid heat transfer and faster gas release, thereby mitigating porosity and flashing defects in cast parts.
3. Research Background:
Background of the Research Topic:
High Pressure Die Casting (HPDC) is extensively utilized in the automotive sector for manufacturing lightweight metal components, particularly with the increasing adoption of lightweight aluminium alloys like ADC12. Chill vents are a common technique in HPDC to evacuate air from the die cavity, typically constructed from steel blocks with zigzag venting paths. However, conventional steel chill vents suffer from limitations due to steel's low thermal conductivity, sometimes leading to molten metal flushing and difficulty in preventing defects.
Status of Existing Research:
Prior research has extensively explored numerical and finite element modelling of solidification and thermal processes in HPDC to enhance process efficiency and reduce cooling time. Simulation studies have analyzed various process parameters critical for accurate thermal analysis and defect reduction. However, as noted in the paper, "Although several factors have been studied using simulation methods, little attention is paid to the design and development of chill vents and air venting problem in a HDPC process."
Necessity of the Research:
The research identifies a gap in the existing literature concerning the design and optimization of chill vents in HPDC. The limitations of conventional steel chill vents, particularly their low thermal conductivity, necessitate the exploration of alternative materials. The study emphasizes the need for improved chill vent designs to address air venting problems and enhance the overall efficiency of the HPDC process, specifically targeting porosity and flashing defects.
4. Research Purpose and Research Questions:
Research Purpose:
The primary research purpose is "to fill this research gap and investigate the performance of a new chill vent configuration using MoldMAX instead of conventional tool steel." This involves designing and developing a high-performance chill vent using MoldMAX, a beryllium copper alloy, and comparing its performance against conventional tool steel (H13) chill vents in HPDC.
Key Research:
The key research focuses on evaluating the performance of beryllium copper alloy (MoldMAX) chill vents in comparison to tool steel (H13) chill vents. This evaluation is conducted through numerical simulation using Finite Element Analysis and validated by experimental testing. The performance metrics include cooling time, cooling rate, and temperature distribution within the die.
5. Research Methodology
Research Design:
The research employs a numerical simulation approach using Finite Element Analysis (FEA) to model heat transfer in chill vents. "Finite element analysis is applied to develop a numerical heat transfer model for chill vent and validated by experimental results." The model was designed to compare the thermal performance of different chill vent materials.
Data Collection Method:
Experimental validation was conducted using "real-time experimental test of aluminium alloy casting performed on a commercial 800 tonne die casting machine." Temperature distribution on the chill vent surface was measured using a "high-speed infrared camera, FLIR PM850 at the HPDC machine" at the ejection time of 15.9 seconds.
Analysis Method:
The simulated temperature results were compared with the experimental measurements to validate the FEA heat transfer model. Subsequently, the validated model was used to compare the performance of MoldMAX copper alloy chill vents against tool steel (H13) chill vents by analyzing cooling time, cooling rate, and temperature distribution.
Research Subjects and Scope:
The research focuses on chill vents used in HPDC. The materials investigated are conventional tool steel (H13) and MoldMAX beryllium copper alloy. The casting material used in the experimental validation and simulation is aluminium alloy ADC12. The scope is limited to the thermal performance of the chill vents in removing heat from the solidifying aluminium alloy.
6. Main Research Results:
Key Research Results:
The key research result is that "the copper chill vent increases the cooling efficiency of the solidifying aluminium alloy by about 158% compared to the conventional steel chill vents." Specifically, the time taken for the copper alloy chill vent to cool to the ejection temperature was significantly shorter (6.70 seconds) compared to the steel chill vent (15.9 seconds). The cooling rates were also significantly higher for the copper alloy chill vent (77°C/s) compared to the steel chill vent (32.5°C/s).
Analysis of presented data:
- Temperature Distribution: Figure 4 and Figure 6 illustrate the temperature distribution on the surface of the moving block for steel and copper alloy chill vents, respectively. Figure 4 shows that for the steel chill vent at 15.9 seconds, the maximum temperature is 98.67°C. Figure 6 shows that the copper alloy chill vent reaches a similar maximum temperature (98.675°C) in just 6.7021 seconds, demonstrating faster cooling.
- Cooling Curves: Figure 7 presents a comparison of cooling time curves for steel (H13) and MoldMAX chill vents. The curves visually demonstrate the significantly faster cooling rate of the MoldMAX chill vent compared to the H13 steel chill vent throughout the casting process. The graph shows "the same temperature at different times," highlighting the time advantage of copper alloy.
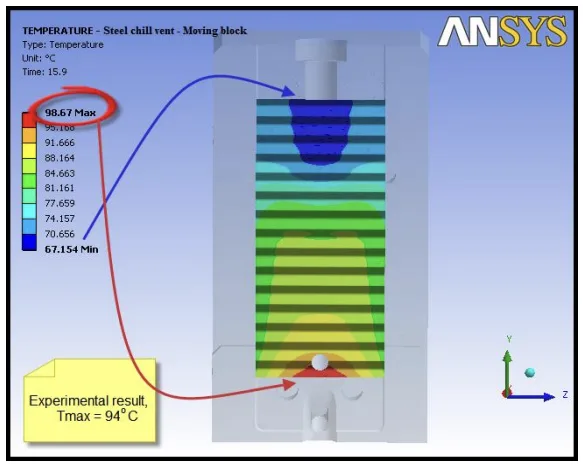
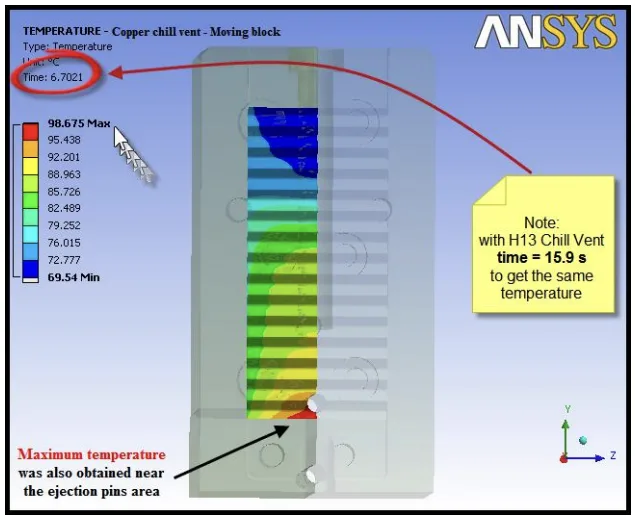
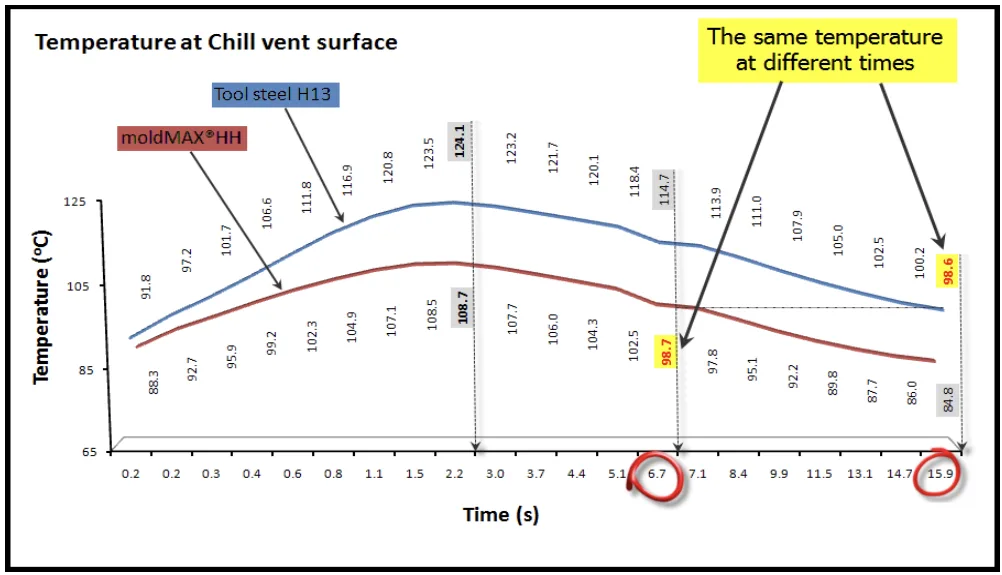
Figure Name List:
- Figure 1. Schematic diagram of a typical HPDC process.
- Figure 2. A CAD model of the chill vent used in HPDC
- Figure 3. Heat generation rate and Heat flux values used for thermal analysis.
- Figure 4. Temperature distribution at the surface of moving block - Steel chill vent.
- Figure 5. Experimental temperature distribution on the chill vent surface measured by infrared camera
- Figure 6. Temperature distribution at the surface of moving block - MoldMAX copper alloy chill vent
- Figure 7. Comparison of cooling time curves during casting process using the steel and copper chill vents.
7. Conclusion:
Summary of Key Findings:
The study concludes that utilizing a high strength, high thermal conductivity copper alloy (MoldMAX) for chill vents in HPDC significantly improves cooling performance. Key findings include:
- Enhanced Cooling Efficiency: Copper alloy chill vents increase cooling efficiency by approximately 158% compared to steel chill vents.
- Reduced Cooling Time: The cooling time to reach ejection temperature is significantly reduced with copper alloy chill vents.
- Improved Heat Transfer: Copper alloy's higher thermal conductivity facilitates rapid heat transfer.
- Faster Gas Release: Enhanced heat transfer contributes to faster gas release from the die cavity.
- Defect Reduction: Improved cooling and gas release contribute to reducing porosity and flashing defects in HPDC parts.
Academic Significance of the Study:
This study addresses a research gap by focusing on the design and performance of chill vents, an often-overlooked aspect in HPDC research. It provides valuable insights into the benefits of using high thermal conductivity materials for chill vents and validates these benefits through numerical simulation and experimental verification. The research contributes to a deeper understanding of heat transfer mechanisms in HPDC and offers a pathway for optimizing chill vent design.
Practical Implications:
The practical implications of this study are significant for the die casting industry. Implementing copper alloy chill vents, such as MoldMAX, can lead to:
- Increased Productivity: Reduced cooling times translate to faster cycle times and increased production rates in HPDC.
- Improved Part Quality: Reduced porosity and flashing defects result in higher quality cast parts with improved mechanical properties and surface finish.
- Enhanced Process Efficiency: Overall improvement in the efficiency and effectiveness of the HPDC process.
Limitations of the Study and Areas for Future Research:
The paper suggests that "Future work should consider the influence of other parameters such as pouring temperature, superheat, air gap formation, injection velocity, and pressure intensification." These parameters could further refine the understanding of chill vent performance and optimize the HPDC process.
8. References:
- [1] A Kaye, A Street. Die Casting Metallurgy. Butterworth and Co Ltd., 1982
- [2] F. Bonollo, N. Gramegna, and G. Timelli, "High-pressure die- casting: contradictions and challenges," The Minerals, Metals & Materials Society, JOM, vol. 67, no. 5, pp. 901-908, 2015.
- [3] L. H. Wang. "Mathematical modelling of air evacuation in die casting process via CASTvac and other venting devices," Int Journal of Cast Metals Research, vol. 20 pp. 191-197, 2007.
- [4] MoldMAX HH Material Property Data, Materion Performance Alloys, Materion Corporation 2017.
- [5] I. Rosindale and K. Davey, "Steady state thermal model for the hot chamber injection system in the pressure die casting process," Journal of Materials Processing Technology, vol. 82, no. 1, pp. 27-45, 1998.
- [6] M. T. A. Rasgado, "Bi-metallic dies for rapid die casting," Journal of Materials Processing Technology vol. 175, pp. 109- 116, 2006.
- [7] S. R. Ahmed, K. D. Devi, and S. V. S. Himathejeswini, "Design & analysis of heat sink high-pressure die casting component," International Journal of Current Engineering and Technology, 2016
- [8] H. J. Kwon, H. K. Kwon, "Computer Aided Engineering (CAE) simulation for the design optimization of gate system on high pressure die casting (HPDC) process," Robotics and Computer-Integrated Manufacturing vol. 55 pp. 147-153, 2018.
- [9] W. B. Yu, Y. Y. Cao, X. B. Li et al, "Determination of interfacial heat transfer behavior at the metal/shot sleeve of high pressure die casting process of AZ91D alloy," Journal of Materials Science & Technology vol. 33 pp. 52-58, 2017
- [10] S. I. Jeong, C. K. Jin, H. Y. Seo et al, "Mould design for clutch housing parts using a casting simulation of high pressure die casting," International Journal Of Precision Engineering And Manufacturing, vol. 17, no. 11, pp. 1523-1531, 2016
- [11] R. W. R. W. Jeppson, Analysis of Flow in Pipe Networks, Butterworth Publications, 1976
- [12] MatWeb Material Property Data, Aluminum ADC12 Die Casting Alloy, Automation Creations, Inc 2009.
- [13] K. N. Prabhu, "Casting/mold thermal contact heat transfer during solidification of Al-Cu-Si alloy (LM 21) plates in thick and thin molds," Journal of Materials Engineering and Performance, ASM International vol. 14, no. 5, pp. 604-609, 2005.
9. Copyright:
- This material is "Duoc T Phan, Syed H Masood, Syed H Riza, and Harsh Modi"'s paper: Based on "Development of High Performance Copper Alloy Chill Vent for High Pressure Die Casting".
- Paper Source: doi: 10.18178/ijmerr.9.7.943-948
This material was created to introduce the above paper, and unauthorized use for commercial purposes is prohibited.
Copyright © 2025 CASTMAN. All rights reserved.