This article introduces the paper "Development of Composite Salt Cores for Foundry Applications" presented at the Materials and technology
1. Overview:
- Title: DEVELOPMENT OF COMPOSITE SALT CORES FOR FOUNDRY APPLICATIONS
- Authors: Jaroslav Beňo, Eliška Adámková, František Mikšovský, Petr Jelínek
- Publication Year: 2015
- Publishing Journal/Academic Society: Materials and technology
- Keywords: non-ferrous alloys, salt cores, inorganic salts, die casting, PUR Cold Box, Warm Box, core solubility and stability
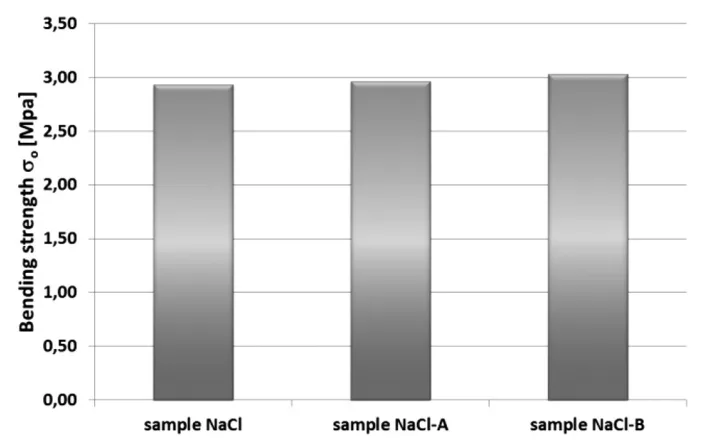
2. Research Background:
- Social/Academic Context of the Research Topic: The increasing demand for complex shapes in non-ferrous alloy castings, particularly in die casting, necessitates improved core technologies. Traditional metal cores are being challenged by the growing shape complexity and the need for easier removal of core material from intricate internal cavities. Salt core technology, known since the 1970s and already used in gravity and low-pressure casting (e.g., for cooling channels in engine pistons), offers advantages in terms of cleanability, dimensional complexity, environmental friendliness, and closed-loop recycling.
- Limitations of Existing Research: While salt cores are beneficial, their application in high-pressure die casting is limited due to the extreme conditions. These conditions include high mold filling rates causing core erosion, metal penetration, and dimensional inaccuracies due to the high temperatures of cast alloys approaching salt melting points. Cores made solely of salt matrixes may not be sufficient for die casting.
- Necessity of the Research: To overcome the limitations of pure salt cores in die casting, composite salt cores are proposed. These cores enhance the base salt matrix with additives to improve properties like heat resistance and strength. This research is necessary to determine the influence of specific additives on the performance of composite salt cores manufactured using different methods (shooting and squeezing) for high surface quality pre-cast holes in die castings.
3. Research Purpose and Research Questions:
- Research Purpose: The primary purpose is to investigate the impact of various additives on the behavior of composite salt cores during the production of castings with high surface quality pre-cast holes. The study focuses on cores prepared using two different methods: shooting (injection into core boxes with binders) and squeezing (high-pressure squeezing of moistened salt).
- Key Research Questions:
- How do different additives affect the bending strength (primary, hot, and residual) of composite salt cores prepared by shooting and squeezing methods?
- What is the influence of additives on the porosity, bench life (hygroscopicity), and solubility of composite salt cores?
- How do additives and surface coatings affect the surface quality (roughness) of pre-cast holes in die castings produced using composite salt cores?
- Research Hypotheses: The research hypothesizes that incorporating specific additives into the salt matrix will improve the mechanical and thermal properties of salt cores, making them more suitable for high-pressure die casting applications and enhancing the surface quality of pre-cast holes.
4. Research Methodology
- Research Design: The study employs an experimental research design to evaluate the properties of composite salt cores. It involves preparing salt cores with different additives using two manufacturing methods (shooting and squeezing) and testing their physical and mechanical properties. Die casting experiments are conducted to assess the performance of these cores in a real casting environment and evaluate the surface quality of the resulting pre-cast holes.
- Data Collection Method:
- Bending Strength Tests: Primary strength (48h after preparation), hot strength (after 1h at 650 °C), and residual strength (after cooling from 650 °C) were measured using a universal testing machine.
- Porosity Measurement: Seeming porosity was calculated based on the density of the KCl matrix and the core density.
- Roughness Measurement: Surface roughness (Ra) of pre-cast holes was measured using a roughness meter according to ISO 1997 standards. Ten measurements were taken per sample, and the average was used.
- Hygroscopicity (Bench Life) Test: The increase in mass fraction (%) of cores stored at 100% relative humidity and 26 °C was measured over time.
- Solubility Test: The weight loss of cores immersed in water at 20 °C was measured over time to determine solubility.
- Analysis Method: Quantitative analysis was used to evaluate the data collected from bending strength, porosity, roughness, hygroscopicity, and solubility tests. Statistical methods were likely used to determine the significance of the effects of additives and manufacturing methods.
- Research Subjects and Scope:
- Core Materials: Chemically pure salt (KCl), technical salt (NaCl), and three different additives (A, B, C) with varying granulometry were used to create composite salt cores.
- Casting Alloy: Aluminum alloy AlSi9Cu3(Fe) was used for die casting experiments.
- Casting Method: High-pressure die casting using a CLH 400 casting machine with a squeezing pressure of 76.8 MPa and a casting temperature of 690 °C.
- Core Manufacturing Methods: High-pressure squeezing of moistened salt and injection into warm core boxes (190 °C) using Na-silicate binder.
5. Main Research Results:
- Key Research Results:
- Injection into Core Boxes (Warm Box):
- The highest bending strengths for cores produced with Na-silicate binder were achieved with original granulometry salt (NaCl). Modified granulometry (finer salt) resulted in lower strengths.
- Additives A and B did not significantly improve the bending strength of cores produced by injection.
- The bending strength of injected cores was approximately 25% of squeezed cores.
- These cores are deemed suitable only for gravity and low-pressure casting.
- High-Pressure Squeezing:
- KCl salt exhibited higher primary and secondary strengths compared to NaCl.
- Composite salt cores with KCl and additives showed increased primary and secondary strengths and improved thermostability (hot strength).
- Apparent porosity of squeezed cores was maintained below 4%.
- Bench Life and Solubility:
- The bench life of salt cores, even under extreme humidity conditions, was very good, with minimal weight increase for both base salt and composite cores.
- Solubility tests showed high solubility for composite salt cores, dissolving completely within 22 minutes, with no significant difference between cold-hardened and thermally exposed cores.
- Surface Quality:
- Using composite cores (KCl + 15% A and KCl + 15% C) with surface coatings improved the surface quality of pre-cast holes.
- The best surface roughness (Ra = 7.5-10.4 µm) was achieved with KCl + 15% A cores using a zircon silicate-based coating (coating c).
- Injection into Core Boxes (Warm Box):
- Statistical/Qualitative Analysis Results:
- Table 2 shows that for injected cores, original granulometry (composition III & IV) resulted in higher bending strength (2.332 MPa and 2.115 MPa respectively) compared to modified granulometry (composition I, II & V) which ranged from 1.332 MPa to 1.794 MPa.
- Table 3 indicates that for squeezed composite cores, adding 10% of additive A, B, or C to KCl generally increased bending strengths (primary, hot and residual) compared to pure KCl. For example, hot strength increased from > 8.9 MPa for pure KCl to > 13.2 MPa with 10% additive A.
- Table 4 shows the hygroscopicity of composite salt cores. After 32 days, pure KCl (K) showed a weight increase of 0.06%, while K+30% A and K+30% B showed significantly higher increases of 2.20% and 2.73% respectively, and K+30% C showed a minimal increase of 0.08%.
- Table 6 presents the surface roughness (Ra) of test castings. K+15% A with coating c achieved Ra of 7.5-10.4 µm, while K+15% C with coating c resulted in Ra of 15.4 µm, and K+15% C with coating b resulted in Ra of 18.6 µm. K+15% C with coating a achieved Ra of 7.86 µm.
- Data Interpretation: The results suggest that for injection molding of salt cores, controlling salt granulometry is crucial for strength. For high-pressure squeezing, using KCl as the base salt and incorporating additives enhances core strength and thermostability. While additives might slightly increase hygroscopicity in some cases (additives A and B), additive C shows minimal impact. Surface coatings are essential to achieve good surface quality in die castings using composite salt cores, and the choice of coating and additive combination significantly influences the final surface finish.
- Figure Name List:
- Figure 1: Bending strength of the composite salt cores prepared with the WARM-BOX method
- Figure 2: Solubility of composite cores (cold hardened and after thermal exposure), K = KCl
- Figure 3: Area of a pre-cast hole in a model casting for a determination of the mean arithmetic roughness Ra
- Figure 4: Detail of a test casting surface, K+15% A
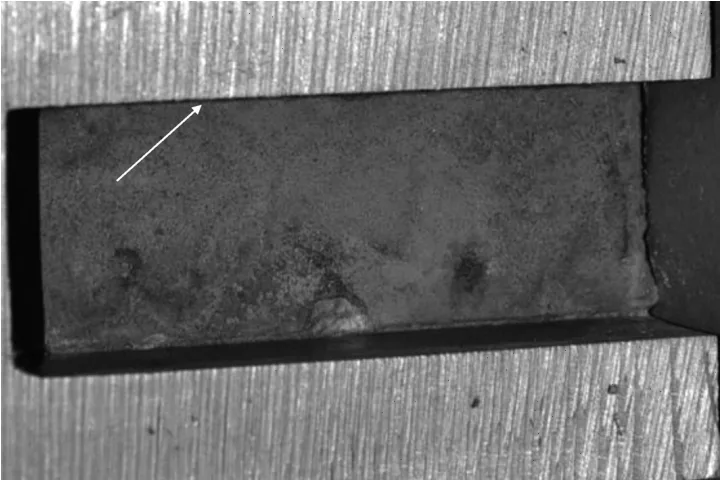
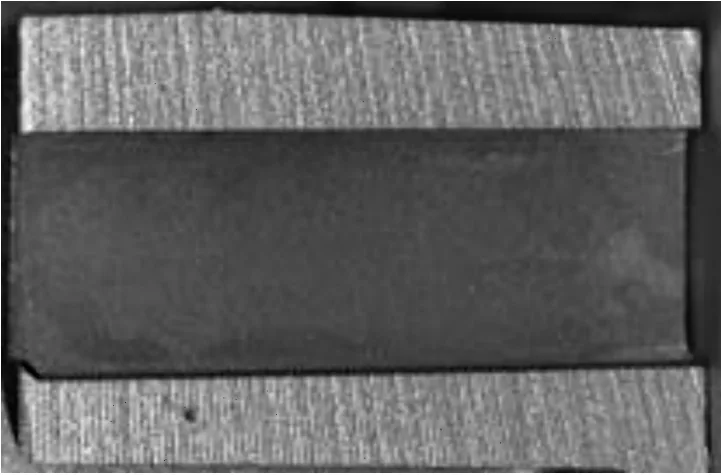
6. Conclusion and Discussion:
- Summary of Main Results: The study demonstrated that composite salt cores, particularly when manufactured by high-pressure squeezing using KCl and specific additives, exhibit improved mechanical and thermal properties suitable for die casting. Injection molding with binders is currently limited to gravity and low-pressure applications. Additives enhance core strength and thermostability, and surface coatings are crucial for achieving high surface quality pre-cast holes. Additive C showed promising results in terms of balancing strength improvement and minimal hygroscopicity.
- Academic Significance of the Research: This research contributes to the understanding of composite salt core technology for foundry applications, specifically in die casting. It provides valuable data on the effects of additives and manufacturing methods on core properties and casting quality. The findings can guide further research and development in this area.
- Practical Implications: The study offers practical guidance for die casting professionals seeking to implement salt core technology. It highlights the potential of composite salt cores for producing complex internal geometries with good surface finish. The research suggests that high-pressure squeezing of KCl-based composite cores with optimized additives and surface coatings is a viable approach for die casting applications. The selection of additive C and zircon silicate-based coating c appears particularly promising for achieving a balance of properties.
- Limitations of the Research: The study focused on specific additives and a limited set of experimental conditions. Further research is needed to explore a wider range of additives, binder systems, and casting parameters. The long-term performance and industrial scalability of these composite salt cores require further investigation.
7. Future Follow-up Research:
- Directions for Follow-up Research:
- Investigate a broader range of additives and their concentrations to optimize core properties further.
- Explore different binder systems for injection molding of composite salt cores to improve their strength for wider applications.
- Conduct more extensive die casting trials under various industrial conditions to validate the performance and scalability of composite salt cores.
- Study the long-term behavior of composite salt cores in industrial storage and handling environments.
- Investigate the recycling and environmental impact of composite salt core materials on a larger scale.
- Areas Requiring Further Exploration: The influence of different coating materials and application techniques on surface quality and core-metal interaction needs further exploration. The optimization of core composition and manufacturing parameters for specific casting alloys and geometries remains an area for future research.
8. References:
- P. Stingl, G. Schiller, Leichte und rückstandfreie Entkernung, Giesserei Erfahrungsaustausch, (2009) 6, 4-8
- P. Jelínek et al., Ověření solných jader na tlakově litém odlitku, Technológ, 4 (2013) 2, 17-22
- P. Lichý, M. Cagala, D. Žáček, Thermomechanical properties of foundry magnesium alloys, Proc. of 20th Anniversary International Metallurgical and Materials Conference METAL 2011, Ostrava, 2011, 890-896
- J. Malík, P. Futaš, I. Vasková, Š. Eperješi, Influence of technological factors of pressure die casting on quality of castings from silumin, Slévárenství, 55 (2007) 5/6, 259-262
- P. Jelínek et al., Influencing the strength characteristics of salt cores soluble in water, Slévárenství, 60 (2012) 3/4, 85-89
9. Copyright:
- This material is Jaroslav Beňo, Eliška Adámková, František Mikšovský, Petr Jelínek's paper: Based on DEVELOPMENT OF COMPOSITE SALT CORES FOR FOUNDRY APPLICATIONS.
- Paper Source: doi:10.17222/mit.2013.160
This material was summarized based on the above paper, and unauthorized use for commercial purposes is prohibited.
Copyright © 2025 CASTMAN. All rights reserved.