This introduction paper is based on the paper "DEVELOPMENT AND APPLICATION OF CASTING DISTORTION & COMPENSATION TECHNOLOGY BASED ON AUTOMATIC ITERATION METHOD" published by "INTERNATIONAL JOURNAL OF INNOVATIONS IN ENGINEERING RESEARCH AND TECHNOLOGY [IJIERT] (NOVATEUR PUBLICATIONS)".
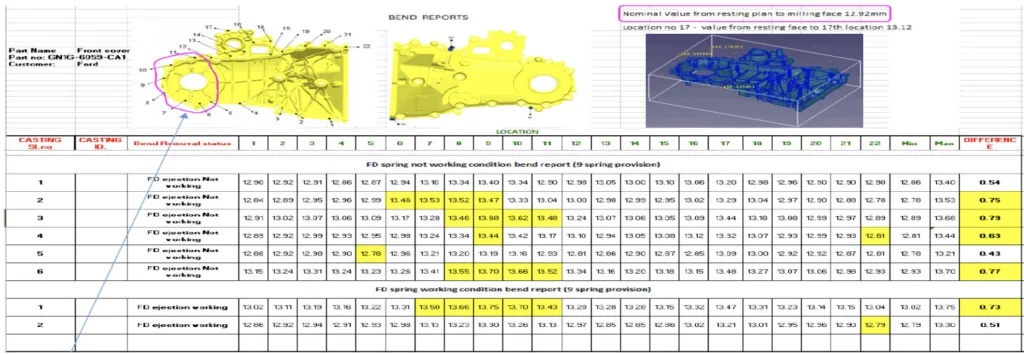
1. Overview:
- Title: DEVELOPMENT AND APPLICATION OF CASTING DISTORTION & COMPENSATION TECHNOLOGY BASED ON AUTOMATIC ITERATION METHOD
- Author: DR. XIAOJUN YANG, MS. RAJESHWARI SANJAY RAWAL
- Year of publication: 2020
- Journal/academic society of publication: INTERNATIONAL JOURNAL OF INNOVATIONS IN ENGINEERING RESEARCH AND TECHNOLOGY [IJIERT] (NOVATEUR PUBLICATIONS)
- Keywords: Die-casting, casting warp, distortion, compensation, automatic iteration, Cast-Designer, DCS (Distortion Compensation Solver), thermal stress, mechanical stress, finite element method.
2. Abstract:
Casting warp or distortion is one of the main defects often encountered in the production of die-casting, it is also quite difficult to solve. The traditional methods have the problems of low efficiency, heavy workload and poor working environment. This paper introduced Cast-Designer's newly developed distortion compensation solver DCS (Distortion Compensation Solver), it can predict the casting distortion and warp in advance and find the casting products meet the tolerance requirements in the automatic iterative optimization technology. With such tools and technology, we can reduce the casting distortion effectively and meet the machining requirements directly.
3. Introduction:
As an advanced manufacturing technology, die casting offers advantages like high dimensional accuracy, good mechanical properties, and high production efficiency, making it suitable for automobile aluminium and aluminium-magnesium alloy parts. However, challenges arise from complex structures, large wall thickness differences, and high precision requirements, often not considered in the initial design stage. Casting distortion and warp defect is a common and difficult problem. Causes include improper casting design, unbalanced ejection, and mould temperature imbalance. Distortion affects quality by: 1) impacting dimensional accuracy; 2) affecting follow-up machining; 3) exposing internal defects (pores, shrinkage) in parts requiring deep machining, which removes the dense surface layer and affects appearance and sealing performance.
4. Summary of the study:
Background of the research topic:
Casting distortion (warp) is a significant and hard-to-solve defect in die casting production. It stems from various causes such as improper casting design, unbalanced forces during ejection, and non-uniform mould temperatures. This defect compromises the dimensional accuracy of castings and complicates necessary follow-up machining operations. For parts requiring significant material removal after casting, distortion can lead to the exposure of internal defects like porosity and shrinkage.
Status of previous research:
Traditional methods for managing casting distortion include:
- Method 1: Process parameter adjustment: Controlling deformation via mould design, spray cooling, and die-casting parameter adjustments. This method may not always achieve the required tolerance and suffers from processing stability issues.
- Method 2: Increase casting allowance: Adding extra material for machining. This increases wall thickness, potentially worsening internal defects (porosity, shrinkage) and increasing the risk of exposing them during machining. It is not considered an ideal solution.
- Method 3: Artificial orthopedic method: Manually correcting dimensions using tools after cooling. This is inefficient, labor-intensive, noisy, yields poor results, risks cracking, and can lead to springback.
- Method 4: Hot Orthotics: Pressing the casting in an orthopedic mould while still hot (around 200 °C) to reduce deformation. This requires complex processes and significant cooling.
These traditional approaches often involve low efficiency, heavy workload, and poor working environments.
Purpose of the study:
This paper introduces Cast-Designer's newly developed Distortion Compensation Solver (DCS). The study aims to demonstrate a technology that can predict casting distortion and warp in advance and utilize automatic iterative optimization to find casting products that meet tolerance requirements. The goal is to effectively reduce casting distortion and meet machining requirements directly, overcoming the limitations of traditional methods.
Core study:
The core of the study focuses on the Distortion Compensation Solver (DCS) technology developed within the Cast-Designer software suite. This technology employs an automatic iteration method. It begins with an accurate simulation of the casting process, calculating thermal and mechanical stresses and the resulting deformation using finite element analysis. Based on the predicted distortion, the DCS iteratively modifies the mould cavity geometry by applying compensation in the opposite direction of the predicted deformation. This process aims to produce a final casting that falls within the specified dimensional tolerances after solidification and cooling.
5. Research Methodology
Research Design:
The research methodology involved simulating the die casting process of a specific automotive part using the Cast-Designer software. The simulation focused on accurately predicting thermal and mechanical stresses and the resulting deformation. These simulation results were then validated by comparing them against flatness measurements taken from actual cast parts. Subsequently, the Distortion Compensation Solver (DCS) was applied, using an automatic iterative approach to modify the part geometry based on the predicted deformation, aiming to minimize the final distortion of the cast part.
Data Collection and Analysis Methods:
- Data Collection:
- Simulation data was generated using Cast-Designer's stress module, performing a full-coupling analysis of thermal, flow, and stress phenomena. The simulation considered mould constraints, mould opening, material properties (elastic-plastic models), and process parameters (e.g., mould opening time, ejection temperature, cooling).
- Physical data was collected by measuring the flatness of six randomly selected cast parts from one batch using 22 defined measurement points.
- Analysis Methods:
- The simulated deformation (flatness) results were compared with the actual flatness measurements from the physical test pieces (specifically samples No. 2, 3, and 4) to validate the simulation accuracy.
- The DCS utilized an automatic iterative compensation method. Based on the deformation calculated in one iteration, a compensation factor was applied to adjust the mesh node coordinates for the next iteration. This process was repeated until the predicted deformation of the final casting met the user-defined tolerance requirements.
Research Topics and Scope:
- Research Topics: The study investigated the prediction of casting distortion and warp in high-pressure die casting and the application of an automatic iterative compensation method (DCS) to minimize these defects. Key topics included accurate stress/strain simulation (thermal and mechanical), simulation validation, and geometry modification for compensation.
- Scope: The research was applied to a specific complex automotive casting part identified as "Front cover" (Part no: GN1G-6059-CA1) for Ford. The part dimensions were 438 X 350 X 145 mm with an average wall thickness of 3.3mm. The study focused on achieving a flatness requirement of 0.5mm on a specific surface after casting and cooling.
6. Key Results:
Key Results:
- Accurate simulation of stress (thermal and mechanical) and deformation during the die casting process was achieved using Cast-Designer, considering factors like heat transfer, solidification, mould constraints, and mould opening.
- The simulation results for part flatness showed very good agreement with the actual flatness measurements obtained from physical test pieces (No. 2, 3, and 4), validating the simulation model (Figure 3).
- The Distortion Compensation Solver (DCS) successfully applied an automatic iterative compensation method. The initial simulated deformation exceeded the 0.5mm flatness tolerance (reaching over 0.8mm).
- After four automatic iteration calculations using DCS, the final predicted flatness of the casting after cooling to room temperature was maintained between 0.05mm and 0.15mm.
- This result indicates that the product, when cast using the compensated mould geometry, would 100% meet the requirement for direct supply machining production within the specified tolerance.
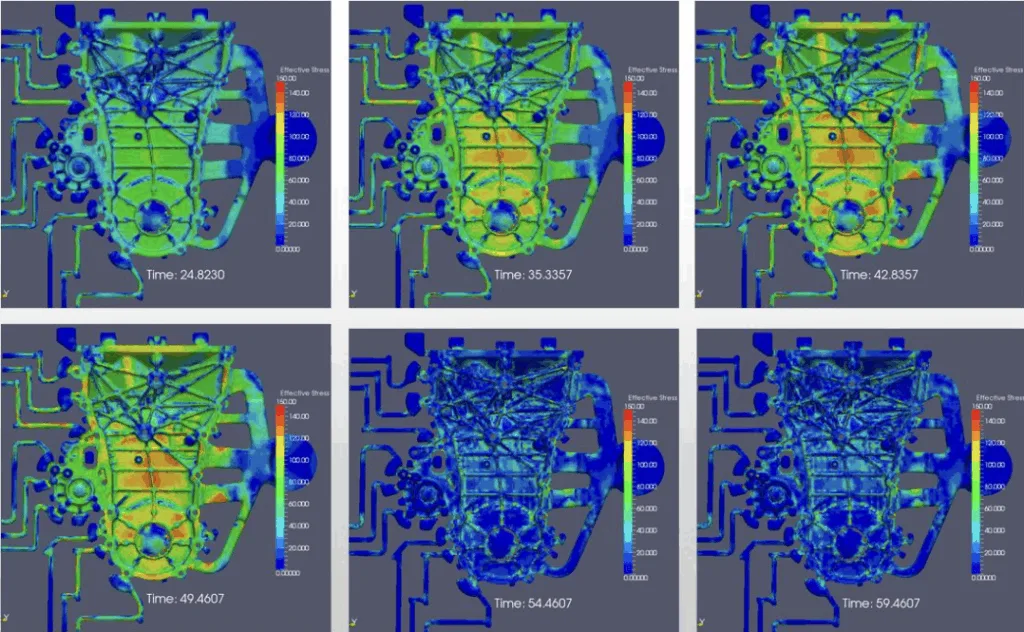
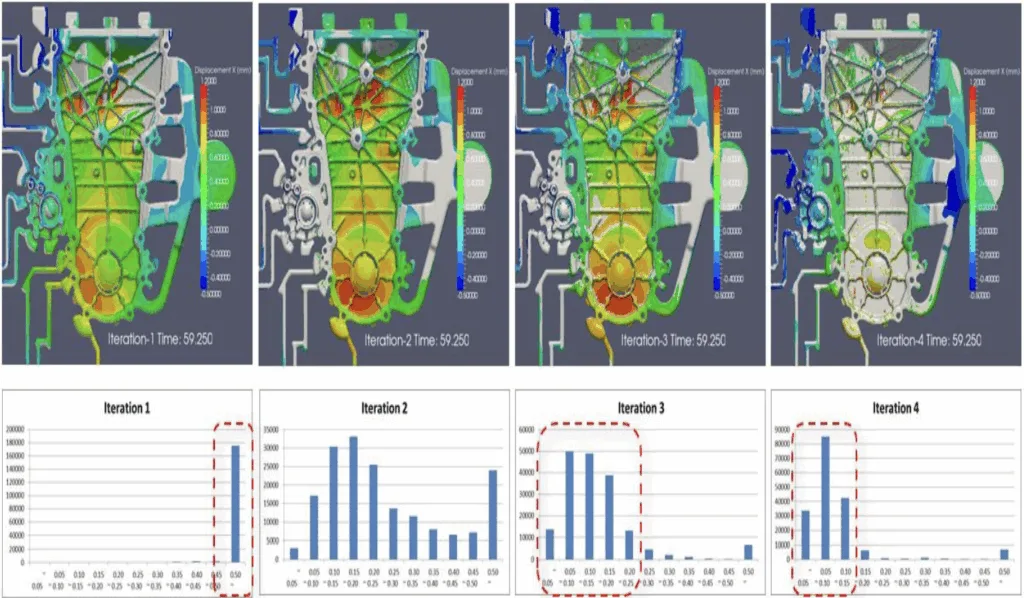
Figure Name List:
- Figure 1 Casting part and dimension after casting, the yellow cells are out of tolerance
- Figure 2 Effective stress contours vs. Time
- Figure 3 Part flatness analysis (simulation results vs. the actual measurement results)
- Figure 4 The first line: left: before casting right: after casting The second line with compensation: left: before casting right: after casting
- Figure 5 The compensation result after four iterations
7. Conclusion:
Using computer simulation and automatic iterative compensation method can effectively solve the casting deformation and distortion problems. With this method, it is effective for the complex geometry casting, such as communication products, heat sinks, covers, automobile parts,etc.
For large orders, or the product has a large flat structure and flatness requirements of automotive parts such as chain cover, oil panel, electric car electrical cover and other castings, the application of deformation compensation technology can improve efficiency and reduce manpower cost.
8. References:
- [1] A.A. Luo, “Magnesium casting technology for structure applications," Journal of Magnesium and Alloys, vol. 1, pp. 2–22, 2013.
- [2] K.K.S. Thong, B.H. Hu, X.P. Nui and I. Pinwill, “Cavity pressure measurements and process monitoring for magnesium die casting of a thin-wall-hand-phone component to improve quality,” J. Mater. Process. Tech., vol. 127, pp. 238–241, 2002.
- [3] Piyanut Meethum, Chakrit Suvanjumrat,“Evaluate of Chill Vent Performance for High Pressure Die-Casting Production and Simulation of Motorcycle Fuel Caps”, MATEC Web of Conferences 95, 07025 (2017) DOI: 10.1051/matecconf/2017950 ,ICMME 2016
- [4] P. Meethum, C. Suvanjumrat, “Porosities Comparison between Production and Simulation in Motorcycle Fuel Caps of Aluminum High Pressure Die Casting", World Academy of Science, Engineering and Technology International Journal of Mechanical and Mechatronics Engineering Vol:9, No:3, 2015.
9. Copyright:
- This material is a paper by "DR. XIAOJUN YANG, MS. RAJESHWARI SANJAY RAWAL". Based on "DEVELOPMENT AND APPLICATION OF CASTING DISTORTION & COMPENSATION TECHNOLOGY BASED ON AUTOMATIC ITERATION METHOD".
- Source of the paper: [DOI Not provided in the paper]
This material is summarized based on the above paper, and unauthorized use for commercial purposes is prohibited.
Copyright © 2025 CASTMAN. All rights reserved.