This article introduces the paper "Comparison of Micro-Pin-Fin and Microchannel Heat Sinks Considering Thermal-Hydraulic Performance and Manufacturability" presented at the IEEE TRANSACTIONS ON COMPONENTS AND PACKAGING TECHNOLOGY
1. Overview:
- Title: Comparison of Micro-Pin-Fin and Microchannel Heat Sinks Considering Thermal-Hydraulic Performance and Manufacturability
- Author: Benjamin A. Jasperson, Yongho Jeon, Kevin T. Turner, Frank E. Pfefferkorn, and Weilin Qu
- Publication Year: March 2010
- Publishing Journal/Academic Society: IEEE TRANSACTIONS ON COMPONENTS AND PACKAGING TECHNOLOGY
- Keywords: Micro heat sink, micro-manufacturing, micro-machining, pin-fin heat sink.
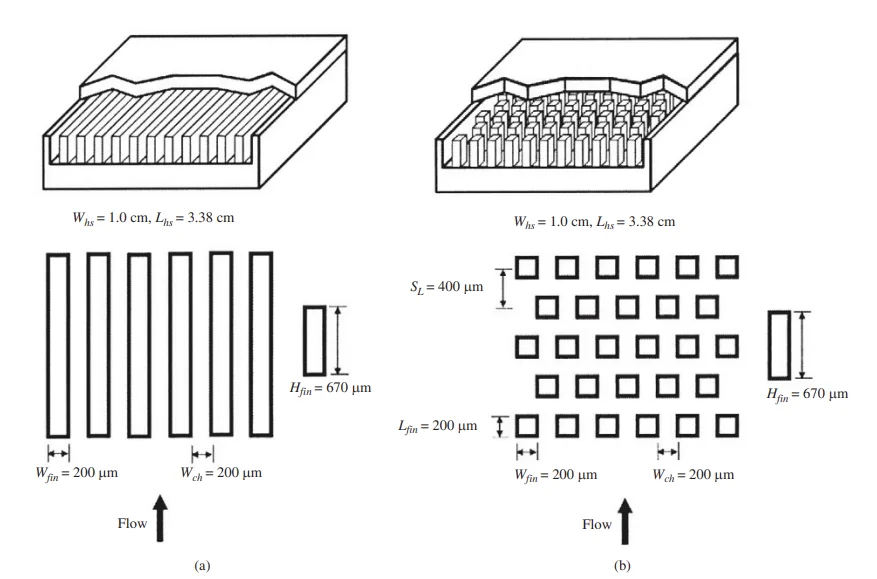
- Social/Academic Context of the Research Topic:
- The increasing heat loads in micro-electronic devices demand highly efficient thermal management techniques for dissipating high heat fluxes from small areas.
- Single-phase liquid-cooled miniature heat sinks with microscale enhancement structures have emerged as a solution. Parallel-plate fins have been widely studied.
- Recent advances in microfabrication enable more complex 3-D enhancement structures like staggered micro-pin-fin arrays.
- Limitations of Existing Research:
- While microchannel heat sinks have well-established thermal-hydraulic performance models, reliable models for micro-pin-fin heat sinks are lacking due to complex flow and heat transfer. Existing studies are mostly empirical.
- Economics and realistic microfabrication options are critical for the viability of micro-pin-fin heat sinks compared to microchannel heat sinks.
- Necessity of the Research:
- To compare the thermo-hydraulic performance of micro-pin-fin heat sinks with microchannel heat sinks.
- To evaluate the manufacturability and cost-effectiveness of both designs using micro-end-milling.
- To provide a comprehensive comparison considering thermal performance, hydraulic performance, and manufacturing cost.
3. Research Purpose and Research Questions:
- Research Purpose:
- To simultaneously compare the thermo-hydraulic performance and manufacturability of micro-pin-fin and microchannel heat sinks as alternatives for dissipating high heat fluxes.
- Key Research Questions:
- Does the micro-pin-fin design outperform the microchannel design in terms of thermo-hydraulic performance?
- What are the manufacturing methods suitable for fabricating micro heat sinks out of metals?
- What is the difference in manufacturing cost between micro-pin-fin and microchannel heat sink designs using micro-end-milling?
- Research Hypotheses:
- Micro-pin-fin heat sinks have the potential for improved heat transfer compared to microchannel heat sinks, but with a trade-off in pressure drop and manufacturing cost.
- Machining time is the primary factor determining the manufacturing cost difference between the two designs when using micro-end-milling.
4. Research Methodology
- Research Design:
- Comparative experimental study of thermal-hydraulic performance for micro-pin-fin and microchannel heat sinks.
- Case study on micro-end-milling to compare manufacturing costs.
- Review of various manufacturing techniques for micro heat sinks.
- Data Collection Method:
- Experimental measurements of thermal resistance and pressure drop for both heat sink designs using single-phase water cooling.
- Analytical models for microchannel heat sink performance based on existing literature.
- Cost analysis based on machining time and tool path calculations for micro-end-milling.
- Analysis Method:
- Comparison of experimental thermal resistance and pressure drop data for both designs across varying flow rates.
- Calculation of machining time and cost based on tool path length and manufacturing parameters.
- Qualitative assessment of different manufacturing methods based on mass production suitability, prototyping suitability and cost.
- Research Subjects and Scope:
- Copper (110) micro heat sinks with channel/pin width of 200 µm and height of 670 µm.
- Micro-pin-fin heat sink: staggered array of 1950 micro-pins.
- Microchannel heat sink: parallel channels.
- Single-phase water as coolant.
- Manufacturing method focus: micro-end-milling.
5. Main Research Results:
- Key Research Results:
- Thermal Performance: Micro-pin-fin heat sink exhibits lower convection thermal resistance at liquid flow rates above approximately 60g/min compared to microchannel heat sink. Below 60g/min, microchannel heat sink shows lower thermal resistance. (Refer to Fig. 10. Comparison of micro-pin-fin heat sink and microchannel heat sink average convection thermal resistance).
- Hydraulic Performance: Micro-pin-fin heat sink has a significantly higher pressure drop than microchannel heat sink across all tested flow rates. (Refer to Fig. 11. Comparison of micro-pin-fin heat sink and microchannel heat sink pressure drop).
- Manufacturing Cost: Micro-pin-fin heat sinks are approximately three times more expensive to manufacture than microchannel heat sinks using micro-end-milling, primarily due to the longer machining time required for the more complex pin-fin geometry. Machining time is the primary cost factor. (Refer to Fig. 14. Total machining distance (tool path as a function of pin/wall width for a 1 cm x 3.38 cm area)).
- Statistical/Qualitative Analysis Results:
- Analytical models for microchannel heat sinks show good agreement with expected trends.
- Review of manufacturing techniques (Table I. POTENTIAL MANUFACTURING METHODS FOR MICRO HEAT SINKS) indicates micro-EDM, micro laser machining, and micro casting as viable for mass manufacturing.
- Data Interpretation:
- The enhanced thermal performance of micro-pin-fin heat sink at higher flow rates is attributed to more tortuous flow and stronger vortices, improving heat transfer.
- Higher pressure drop in micro-pin-fin design is due to increased drag from pin arrays.
- Machining time difference is directly linked to the complexity of tool path, which is significantly longer for staggered pin-fin geometry.
- Figure Name List:
- Fig. 1. Structure and dimension of (a) microchannel heat sink and (b) micro-pin-fin heat sink.
- Fig. 2. Illustrations of three electrodischarge machining techniques: (a) wire EDM, (b) die sinking, and (c) EDM milling.
- Fig. 3. Schematic of LIGA process.
- Fig. 4. Schematic of die casting.
- Fig. 5. Schematic of extrusion process.
- Fig. 6. Schematic of micro powder injection molding.
- Fig. 7. Schematics of milling: (a) slot milling and (b) end milling.
- Fig. 8. Schematic of chip load.
- Fig. 9. Photographs of (a) copper heat sink and (b) pin fin geometry created by micro-end-milling.
- Fig. 10. Comparison of micro-pin-fin heat sink and microchannel heat sink average convection thermal resistance for (a) Tin = 30 °C and (b) Tin = 60 °C.
- Fig. 11. Comparison of micro-pin-fin heat sink and microchannel heat sink pressure drop for (a) Tin = 30 °C and (b) Tin = 60 °C.
- Fig. 12. Illustration of tool path for milling channel heat sink.
- Fig. 13. Illustration of tool path for milling staggered pin heat sink.
- Fig. 14. Total machining distance (tool path as a function of pin/wall width for a 1 cm x 3.38 cm area).
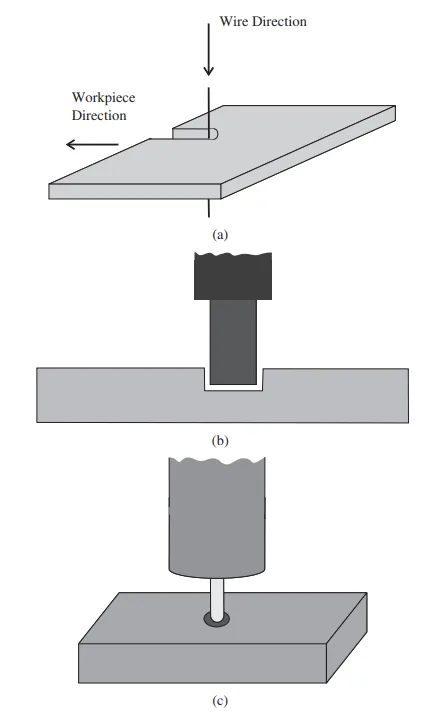
2. Research Background:
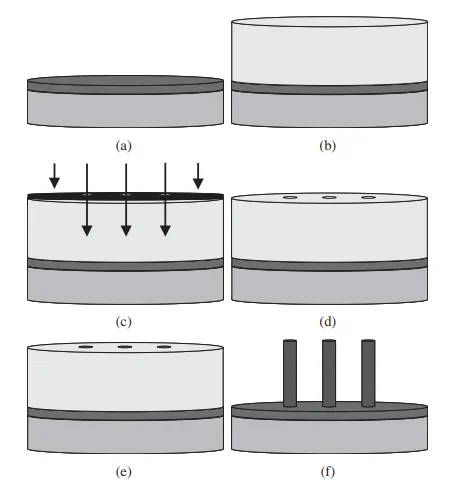
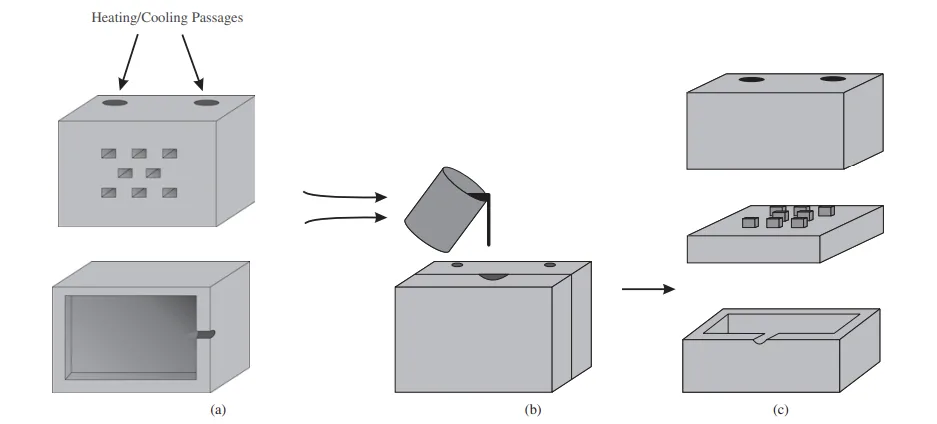
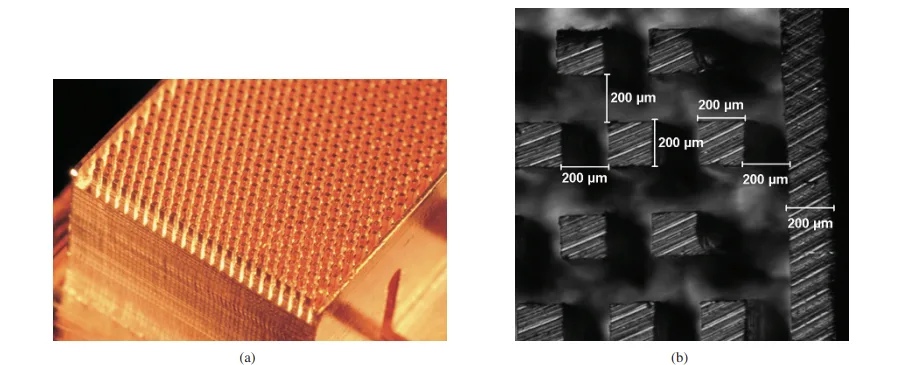
6. Conclusion and Discussion:
- Summary of Main Results:
- Micro-pin-fin heat sinks offer better thermal performance at higher flow rates (>60g/min) but with increased pressure drop and manufacturing cost compared to microchannel heat sinks.
- Micro-end-milling cost for micro-pin-fin heat sinks is approximately three times higher due to longer machining time.
- Academic Significance of the Research:
- Provides a direct comparison of thermal-hydraulic performance and manufacturability for micro-pin-fin and microchannel heat sinks.
- Offers insights into the flow behavior and heat transfer mechanisms in micro-pin-fin arrays.
- Contributes to the understanding of cost factors in micro-manufacturing of heat sinks using micro-end-milling.
- Practical Implications:
- Guides the selection of heat sink design based on application requirements, considering trade-offs between thermal performance, pressure drop, and cost.
- Highlights the importance of machining time in micro-manufacturing cost and potential areas for cost reduction through process improvements (e.g., higher spindle speeds, advanced tool coatings).
- Suggests casting as a potential cost-effective method for mass production of micro-pin-fin heat sinks, minimizing the cost difference compared to microchannel designs.
- Limitations of the Research:
- Cost analysis is specific to micro-end-milling and may vary for other manufacturing methods.
- Assumes constant feed rate and tool life for cost comparison, which may not be entirely accurate in real-world scenarios.
- Focuses on specific geometries and may not be generalizable to all micro-pin-fin and microchannel designs.
7. Future Follow-up Research:
- Directions for Follow-up Research:
- Explore other pin fin designs (diamond, circular, airfoil) to optimize thermal performance and pressure drop.
- Investigate the impact of improved productivity (higher feed rates, spindle speeds, advanced tool coatings) on reducing manufacturing cost and the cost difference between designs.
- Further research into casting and other mass production methods for micro-pin-fin heat sinks to reduce unit cost.
- Areas Requiring Further Exploration:
- Optimization of micro-pin-fin geometry for specific applications and flow conditions.
- Development of more accurate and comprehensive models for predicting thermal-hydraulic performance of micro-pin-fin heat sinks.
- Detailed cost analysis considering various manufacturing methods and production volumes.
8. References:
- [1] T. M. Harms, M. J. Kazmierczak, and F. M. Gerner, "Developing convective heat transfer in deep rectangular microchannels," Int. J. Heat Fluid Flow, vol. 20, no. 2, pp. 149-157, 1999.
- [2] K. Kawano, K. Minakami, H. Iwasaki, and M. Ishizuka, "Microchannel heat exchanger for cooling electrical equipment," presented at Proc. ASME Int. Mech. Eng. Congr. Expo., Fairfield, NJ, 1998.
- [3] P.-S. Lee, S. V. Garimella, and D. Liu, "Investigation of heat transfer in rectangular microchannels," Int. J. Heat Mass Transfer, vol. 48, no. 9, pp. 1688-1704, 2005.
- [4] W. Qu and I. Mudawar, "Experimental and numerical study of pressure drop and heat transfer in a single-phase microchannel heat sink," Int. J. Heat Mass Transfer, vol. 45, no. 12, pp. 2549-2565, Jun. 2002.
- [5] D. B. Tuckerman and R. F. W. Pease, "High-performance heat sinking for VLSI," IEEE Electron. Devices Lett., vol. 2, no. 5, pp. 126-129, May 1981.
- [6] A. Kosar, C.-J. Kuo, and Y. Peles, "Hydoroil-based micro-pin-fin heat sink," in Proc. 2006 ASME Int. Mech. Eng. Congr. Expo., (IMECE'06) Microelectromech. Syst., Chicago, pp. 563-570.
- [7] A. Kosar, C. Mishra, and Y. Peles, "Laminar flow across a bank of low aspect ratio micro-pin-fins," J. Fluids Eng., Trans. ASME, vol. 127, no. 3, pp. 419-430, 2005.
- [8] A. Kosar and Y. Peles, "Thermal-hydraulic performance of MEMS-based pin fin heat sink," J. Heat Transfer, vol. 128, no. 2, pp. 121-131, 2006.
- [9] Y. Peles and A. Kosar, "Convective flow of refrigerant (R-123) across a bank of micro-pin-fins," Int. J. Heat Mass Transfer, vol. 49, no. 17-18, pp. 3142-3155, 2006.
- [10] Y. Peles, A. Kosar, C. Mishra, C.-J. Kuo, and B. Schneider, "Forced convective heat transfer across a pin fin micro heat sink," Int. J. Heat Mass Transfer, vol. 48, no. 17, pp. 3615-3627, 2005.
- [11] R. S. Prasher, "Nusselt number and friction factor of staggered arrays of low aspect ratio micro-pin-fins under cross flow for water as fluid," J. Heat Transfer, vol. 129, no. 2, pp. 141-153, 2007.
- [12] A. Siu-Ho, W. Qu, and F. Pfefferkorn, "Experimental study of pressure drop and heat transfer in a single-phase micro-pin-fin heat sink," Trans. ASME. J. Electron. Packaging, vol. 129, no. 4, pp. 479-487, 2007.
- [13] W. Qu and A. Siu Ho, "Liquid single-phase flow in an array of micro-pin-fins. Part I. Heat transfer characteristics," J. Heat Transfer, vol. 130, no. 12, pp. 122402-1-122402-11, Dec. 2008.
- [14] W. Qu and A. Siu Ho, "Liquid single-phase flow in an array of micro-pin-fins. Part II: Pressure drop characteristics," J. Heat Transfer, vol. 130, no. 12, pp. 124501-1-124501-4, 2008.
- [15] J. Eugene, F. Xi, B. Tan, and B. A. Jubran, "An overview on micro-meso manufacturing techniques for micro heat exchangers for turbine blade cooling," Int. J. Manufacturing Res., vol. 3, no. 1, pp. 3-26, 2008.
- [16] K. H. Ho and S. T. Newman, "State of the art electrical discharge machining (EDM)," Int. J. Mach. Tools Manufacture, vol. 43, no. 13, pp. 1287-1300, 2003.
- [17] S. Kalpakjian and S. R. Schmid, “Advanced manufacturing processes," in Manufacturing Engineering and Technology, 5th ed. Upper Saddle River, NJ: Pearson Education, Inc., 2006, ch. 27, pp. 846-850.
- [18] C. S. Lin, Y. S. Liao, and S. T. Chen, "Development of a novel micro wire-EDM mechanism for the fabricating of micro parts," presented at Int. Conf. Advanced Manufacture, Taipei, Taiwan, 2005.
- [19] X. Cheng, "Development of ultraprecision machining system with unique wire EDM tool fabrication system for micro/nano-machining," CIRP Ann. Manufacturing Technol., vol. 57, no. 1, pp. 415-420, 2008.
- [20] D. T. Pham, S. S. Dimov, S. Bigot, A. Ivanov, and K. Popov, "Micro-EDM recent developments and research issues," presented at 14th Int. Symp. Electromach., Edinburgh, Scotland, 2004.
- [21] A. B. M. A. Asad, T. Masaki, M. Rahman, H. S. Lim, and Y. S. Wong, "Tool-based micro-machining," J. Materials Process. Tech., vol. 192-193, pp. 204-211, 2007.
- [22] M. M. Sundaram, S. Billa, and K. P. Rajurkar, "Generation of high aspect ratio micro holes by a hybrid micromachining process," presented at ASME Int. Conf. Manufacturing Sci. Eng., Atlanta, GA, 2007.
- [23] W. Ehrfeld, "Micro electro discharge machining as a technology in micromachining," in Proc. SPIE Int. Soc. Optical Eng., vol. 2879. Austin, TX, 1996, pp. 332-337.
- [24] M. Sundaram and K. Rajurkar, "Toward freeform machining by micro electro discharge machining process," Trans. North Amer. Manufacturing Res. Inst., vol. 36, pp. 381-388, 2008.
- [25] J. S. Coursey, J. Kim, and K. T. Kiger, "Spray cooling of high aspect ratio open microchannels,” J. Heat Transfer, vol. 129, no. 8, pp. 1052-1059, 2007.
- [26] M. J. Madou, "Lithography," in Fundamentals of Microfabrication, 2nd ed. Boca Raton, FL: CRC Press, 2002, ch. 1, pp. 1-10, 49-50.
- [27] R. Muwanga and I. Hassan, "Flow boiling oscillations in microchannel heat sinks," presented at 9th AIAA/ASME Joint Thermophysics Heat Transfer Conf., San Francisco, CA, 2006.
- [28] S. Stefanescu, M. Mehregany, J. Leland, and K. Yerkes, "Micro jet array heat sink for power electronics," presented at Proc. IEEE Micro Electro Mechn. Syst., Orlando, FL, 1999.
- [29] X. Wei, C. H. Lee, Z. Jiang, and K. Jiang, "Thick photoresists for electroforming metallic microcomponents," J. Mech. Eng. Sci., vol. 222, no. 1, pp. 37-42, 2008.
- [30] C. H. Ho, K. P. Chin, C. R. Yang, H. M. Wu, and S. L. Chen, "Ultrathick SU-8 mold formation and removal, and its application to the fabrication of LIGA-like micromotors with embedded roots," Sensors and Actuators A (Physical), vol. 102, no. 1-2, pp. 130–138, 2002.
- [31] H. Guckel, "High-aspect-ratio micromachining via deep X-ray lithography," Proc. IEEE, vol. 86, no. 8, pp. 1586-1593, Aug. 1998.
- [32] J. Li, D. Chen, J. Zhang, J. Liu, and J. Zhu, "Indirect removal of SU-8 photoresist using PDMS technique,” Sensors and Actuators A (Physical), vol. 125, no. 2, pp. 586-589, 2006.
- [33] L. T. Romankiw, "Path: From electroplating through lithographic masks in electronics to LIGA in MEMS," Electrochimica Acta, vol. 42, no. 20-22, pp. 2985-3005, 1997.
- [34] R. K. Kupka, F. Bouamrane, C. Cremers, and S. Megtert, "Microfabrication: LIGA-X and applications," Appl. Surface Sci., vol. 164, no. 1-4, pp. 97-110, 2000.
- [35] R. Engelke, "Complete 3-D UV microfabrication technology on strongly sloping topography substrates using epoxy photoresist SU-8," Microelectron. Eng., vol. 73-74, pp. 456-462, 2004.
- [36] A. J. Pang, "Design, manufacture and testing of a low-cost microchannel cooling device," presented at 6th Electron. Packaging Technol. Conf., Piscataway, NJ, 2004.
- [37] L. S. Stephens, K. W. Kelly, D. Kountouris, and J. McLean, "A pin fin microheat sink for cooling macroscale conformal surfaces under the influence of thrust and frictional forces," J. Microelectromech. Syst., vol. 10, no. 2, pp. 222-231, 2001.
- [38] G. Baumeister, R. Ruprecht, and J. Hausselt, "Microcasting of parts made of metal alloys," Microsyst. Technol., vol. 10, no. 3, pp. 261-264, 2004.
- [39] B. S. Li, M. X. Ren, C. Yang, and H. Z. Fu, "Microstructure of Zn-Al4 alloy microcastings by micro precision casting based on metal mold," Trans. Nonferrous Metals Soc. China, vol. 18, no. 2, pp. 327-332, 2008.
- [40] G. Baumeister, K. Mueller, R. Ruprecht, and J. Hausselt, "Production of metallic high aspect ratio microstructures by microcasting," Microsyst. Technol., vol. 8, no. 2-3, pp. 105-108, 2002.
- [41] G. Baumeister, R. Ruprecht, and J. Hausselt, "Replication of LIGA structures using microcasting," Microsyst. Technol., vol. 10, no. 6, pp. 484-488, 2004.
- [42] S. Chung, S. Park, H. Jeong, I. Lee, and D. Cho, "Replication techniques for a metal microcomponent having real 3-D shape by microcasting process," Microsyst. Technol., vol. 11, no. 6, pp. 424-437, 2005.
- [43] J. Cao and N. Krishnan, "Recent advances in microforming: Science, technology and applications," in Proc. Materials Sci. Technol. 2005, Pittsburgh, PA, pp. 225-234.
- [44] N. Krishnan, J. Cao, and K. Dohda, "Study of the size effects on friction conditions in microextrusion Part I: Microextrusion experiments and analysis," J. Manufacturing Sci. Eng., Trans. ASME, vol. 129, no. 4, pp. 669-676, 2007.
- [45] M. Geiger, M. Kleiner, R. Eckstein, N. Tiesler, and U. Engel, "Micro-forming," CIRP Ann. Manufacturing Technol., vol. 50, no. 2, pp. 445-462, 2001.
- [46] N. Krishnan, J. Cao, B. Kinsey, S. A. Paraslz, and M. Li, "Investigation of deformation characteristics of micro-pins fabricated using microextrusion," presented at ASME Int. Mech. Eng. Congr. Expo., Orlando, FL, 2005.
- [47] S. G. Li, "Dimensional variation in production of high-aspect-ratio micro-pillars array by micro powder injection molding," Appl. Physics A-Materials Sci. Process., vol. 89, no. 3, pp. 721-728, 2007.
- [48] G. Fu, "Injection molding, debinding and sintering of 316L stainless steel microstructures," Appl. Physics a-Materials Sci. Process., vol. 81, no. 3, pp. 495-500, 2005.
- [49] J. Chen, J. Yang, and T. Zuo, "Micro fabrication with selective laser micro sintering," presented at 1st IEEE Int. Conf. Nano Micro Eng. Molecular Syst., Zhuhai, China, 2006.
- [50] X. Li, H. Choi, and Y. Yang, "Micro rapid prototyping system for micro components," Thin Solid Films, vol. 420-421, pp. 515-523, 2002.
- [51] Y. Jeon, and F. Pfefferkorn, "Effect of laser preheating the workpiece on micro-end-milling of metals," presented at Proc. ASME Int. Mech. Eng. Congr. Expo., Orlando, FL, 2005.
- [52] E. Oberg, F. D. Jones, H. L. Horton, and H. H. Ryffel, "Aluminum alloys," in Machinery's Handbook, 28th ed. New York: Industrial Press, 2004, p. 1014.
- [53] S. Jahanmir, "Ultra-high-speed micro-milling spindle," Poster MSECICMP2008-72573 presented at ASME Int. Conf. Manufacturing Sci. Eng., Evanston, IL, Oct. 7-10, 2008.
- [54] T. Ozel and T. Altan, "Process simulation using finite element method prediction of cutting forces, tool stresses and temperatures in high-speed flat end milling," Int. J. Mach. Tools Manufacture, vol. 40, no. 5, pp. 713-738, 2000.
- [55] M. P. Vogler, R. E. DeVor, and S. G. Kapoor, "On the modeling and analysis of machining performance in micro-end-milling, Part I: Surface generation," Trans. ASME. J. Manufacturing Sci. Eng., vol. 126, no. 4, pp. 685-694, 2004.
- [56] R. D. Blevins, Applied Fluid Dynamics Handbook, 1st ed. New York: Van Nostrand Reinhold Company, 1984, ch. 6, pp. 38-123.
- [57] R. K. Shah and A. L. London, Laminar Flow Forced Convection in Ducts: A Source Book for Compact Heat Exchanger Analytical Data, Supl. 1, New York: Academic Press, 1978, ch. 7, pp. 196-222.
9. Copyright:
- This material is "Benjamin A. Jasperson, Yongho Jeon, Kevin T. Turner, Frank E. Pfefferkorn, and Weilin Qu"'s paper: Based on "Comparison of Micro-Pin-Fin and Microchannel Heat Sinks Considering Thermal-Hydraulic Performance and Manufacturability".
- Paper Source: 10.1109/TCAPT.2009.2023980
This material was summarized based on the above paper, and unauthorized use for commercial purposes is prohibited.
Copyright © 2025 CASTMAN. All rights reserved.