This article introduces the paper "Characterization of Magnesium Automotive Components Produced by Super-Vacuum Die Casting Process".
1. Overview:
- Title: Characterization of Magnesium Automotive Components Produced by Super-Vacuum Die Casting Process
- Authors: K. Sadayappan, W. Kasprzak, Z. Brown, L. Ouimet, and A.A. Luo
- Publication Year: 2009
- Journal/Conference: Materials Science Forum Vols 618-619
- Keywords: high pressure die casting, heat treatment, high vacuum, material characterisation
2. Research Background:
- Social/Academic Context of the Research Topic: Magnesium automotive components are currently produced by high pressure die casting. However, casting imperfections such as porosity and inclusions hinder heat treatment to improve strength and ductility, limiting their application in highly stressed components. Recent advancements in aluminum die casting, like Alcan's High-Q process, have enabled the use of high-integrity aluminum die castings in automotive body structures.
- Limitations of Existing Research: Existing magnesium die casting processes faced challenges in producing heat-treatable and weldable castings.
- Necessity of Research: There was a need to develop magnesium alloy casting processes that are heat-treatable, weldable, and economical. The USAMP (United States Automotive Materials Partnership) casting team developed a Super-Vacuum Die Casting (SVDC) process. This study evaluates the characteristics of automotive shock tower castings produced by the SVDC process as part of the Canada-China-USA collaborative project 'Magnesium Front End Research and Development'.
3. Research Objectives and Research Questions:
- Research Objective: To evaluate the characteristics of AZ91D magnesium automotive shock tower castings produced by the Super-Vacuum Die Casting (SVDC) process and to demonstrate the potential of the SVDC process for producing high-quality magnesium castings.
- Core Research Questions: Can the SVDC process produce high-quality magnesium castings with reduced porosity and heat treatability compared to conventional high-pressure die casting? How do the mechanical properties of SVDC AZ91D castings change with different heat treatment conditions?
- Research Hypothesis: The SVDC process will minimize air entrapment, reducing porosity in magnesium castings, thereby enabling heat treatment and improving mechanical properties.
4. Research Methodology:
- Research Design: Experimental study
- Data Collection Methods:
- Radiography: Evaluation of casting defects and porosity according to ASTM standard E505.
- Tensile Testing: Measurement of tensile strength, yield strength, and elongation according to ASTM Standard B557.
- Thermal Analysis: Analysis of solidification process using Universal Metallurgical Simulator and Analyzer (UMSA).
- Analysis Methods:
- Analysis of radiographs to evaluate casting defects and porosity.
- Statistical analysis of tensile test results (mean and standard deviation).
- Analysis of thermal analysis curves (first derivative, fraction liquid, fraction solid curves) to determine phase transformation temperatures and liquid fraction changes.
- Research Subjects and Scope: AZ91D shock tower castings produced by the SVDC process at Contech US LLC. Ten tensile specimens were extracted from each shock tower casting. Heat treatment conditions: T4, T5, T6, fluidized bed treatment.
5. Main Research Findings:
- Key Findings: AZ91D castings produced by the SVDC process exhibit very low porosity and can be heat-treated without blisters. The tensile properties of the castings are satisfactory, and conventional heat treatment processes need to be optimized for thin-sectioned and rapidly solidified castings with very fine microstructures. Fluidized bed treatment can reduce heat treatment cycle times.
- Statistical/Qualitative Analysis Results:
- Quality Testing: All coupons passed Level 1 radiographic inspection of ASTM standard E155. Some coupons revealed minor defects like cracks and inclusions, but these were related to metal flow rather than porosity (Figure 2). No blistering was observed in heat-treated coupons even after 16 hours of solutionizing treatment.
- Tensile Properties:
- As-cast specimens showed elongation ranging from 2% to 5% with an average of 3.5%. Yield strength was high, and tensile strength was moderate.
- After T4 heat treatment, elongation significantly improved to an average above 6%, with some specimens reaching 12%. However, yield strength decreased to below 110MPa.
- T5 heat treatment did not significantly improve yield strength, and elongation and tensile strength decreased considerably.
- T6 heat treatment showed similar trends in elongation and tensile strength to T5. Yield strength after T6 treatment was lower than T5 but higher than T4 coupons.
- Sub-size coupons generally exhibited better elongation and tensile strength compared to full-size coupons.
- Fluidized bed treatment resulted in similar mechanical properties but achieved in shorter heat treatment times (Table 2).
- Microstructure: As-cast microstructure showed fine grain structure and divorced eutectic (Figure 3a). After T4 heat treatment, B-Mg17Al12 precipitates dissolved into the matrix, but grain growth was observed (Figure 3b). Grain growth and precipitates were observed after T6 treatment (Figure 3d).
- Thermal Analysis: Melting of AZ91D alloy started at 422.8±1.5°C (#1 in Figure 4) and completed at 615.2±0.9°C (#3). Dissolution of a(Mg)-β(Mg17Al12) eutectic completed at 446.6±0.3°C (#2 in Figure 4), with approximately 8% liquid fraction at this point. Liquidus temperature was measured at 606.6±0.8°C (#4 in Figure 4), and solidus temperature at 404.2±0.6°C (#6 in Figure 4).
- Data Interpretation: The SVDC process is effective in producing high-quality magnesium castings, and heat treatment allows for controlling mechanical properties. T4 heat treatment is effective in improving elongation but reduces yield strength. Fluidized bed treatment can contribute to reducing heat treatment time and cost.
- Figure Name List:
- Figure 1. Shock Tower Casting.
- Figure 2. Radiographs showing inclusions and flow marks in the casting.
- Figure 3. Microstructures of Super Vacuum Die Cast AZ91D castings
- Figure 4. First Derivative vs. Temperature curves of the AZ91D alloy test samples recorded during melting and solidification at~1°C/s.
- Figure 5. Fraction Solid and Fraction Liquid vs. Temperature curves of the AZ91D alloy test samples.
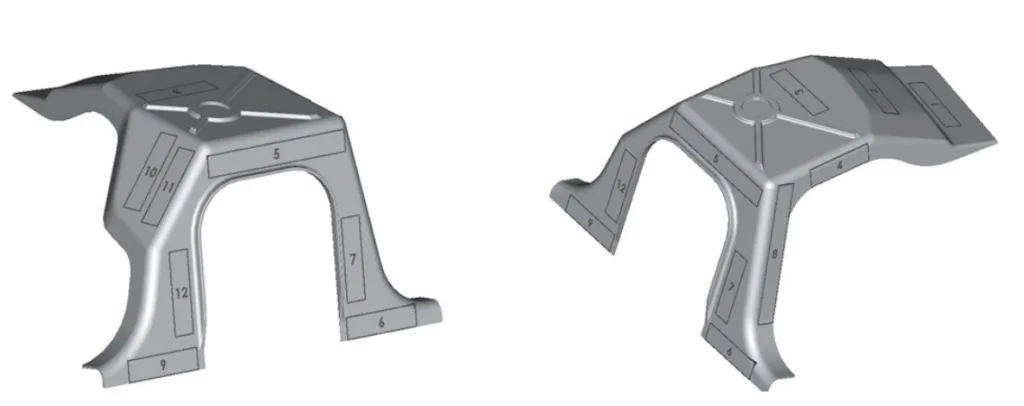
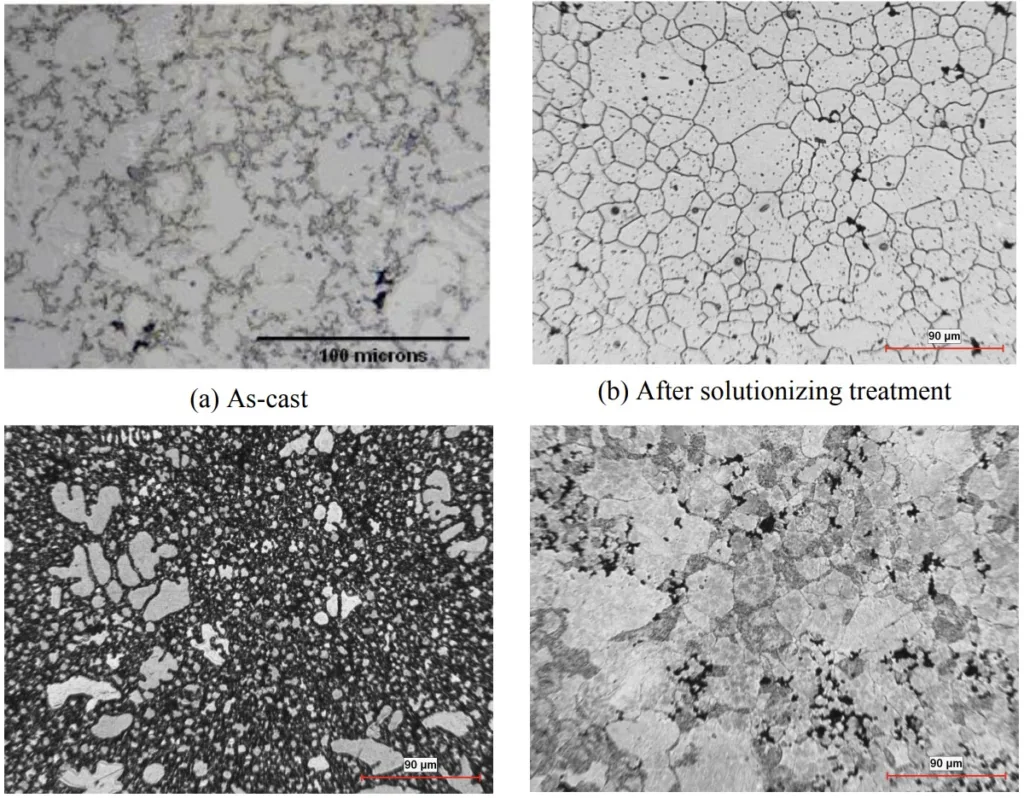
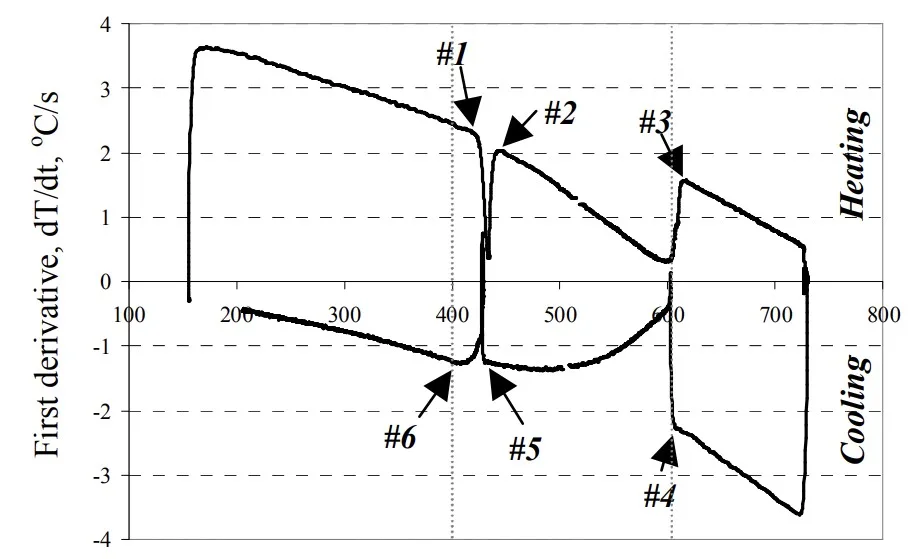
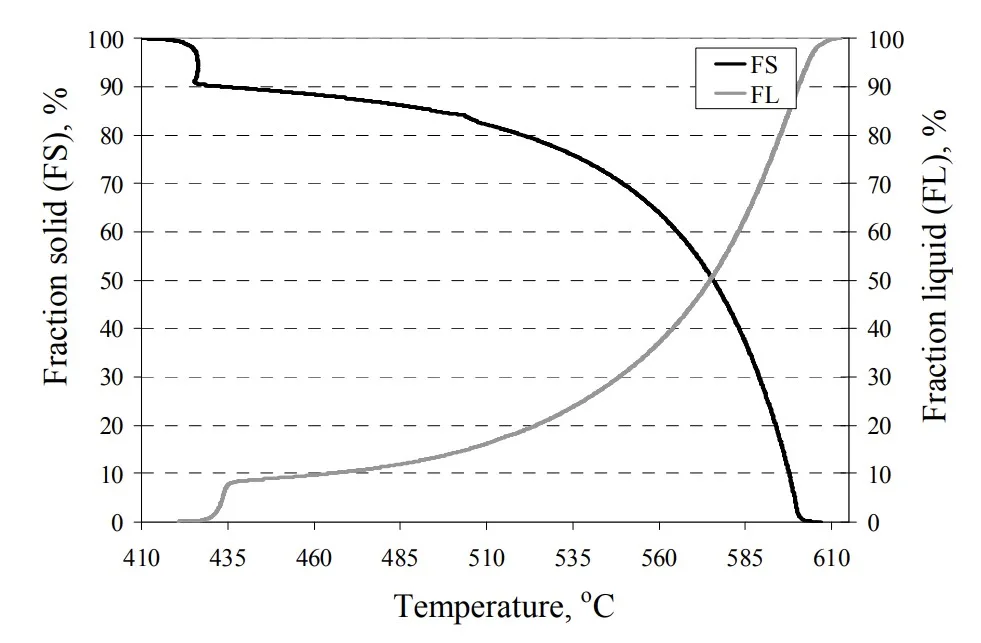
6. Conclusion and Discussion:
- Summary of Main Findings: The Super-Vacuum Die Casting (SVDC) process was successfully applied to produce high-quality magnesium castings with minimal porosity and heat treatability without blisters. Mechanical properties of SVDC AZ91D castings were consistent with minimal scatter. High elongation can be achieved after solution treatment, but strength improvement was limited, possibly due to grain growth. Optimization of heat treatment processes for rapidly solidified magnesium castings is necessary. Fluidized bed treatment is effective in reducing heat treatment cycle time.
- Academic Significance of Research: The study demonstrates the potential of the SVDC process for producing high-quality magnesium castings and provides data on the heat treatment characteristics and thermal behavior of AZ91D alloy.
- Practical Implications: The SVDC process is a promising technology for magnesium automotive component production, and fluidized bed heat treatment can improve production efficiency. Optimized heat treatment processes are crucial for achieving desired mechanical properties.
- Limitations of Research: This study is limited to AZ91D alloy and shock tower castings, and generalization to other alloys and component shapes may be limited. Grain growth during heat treatment was identified as a limiting factor for strength improvement, and further research on microstructure control is needed.
7. Future Follow-up Research:
- Directions for Future Research: Optimization of heat treatment processes for rapidly solidified magnesium castings, especially for thin-walled components. Further research on fluidized bed treatment. Research on microstructure control to suppress grain growth during heat treatment.
- Areas for Further Exploration: The effect of microstructure refinement on solution treatment temperature, dissolution kinetics of intermetallic compounds, and heat treatment optimization studies for various SVDC magnesium alloys and component designs.
8. References:
[1] Brown, Z., Szymanowski, B., Musser, M., Saha, D. and Seaver, S. “Manufacturing of Thin Wall Structural Automotive Components Through High Vacuum Die Casting Technology”, Casting Congress, St Louis, 2007.
[2] Brown, Z., Musser, M., Luo, A.A, Sadayappan, K., Zindel, J. and Beals, R. “Development of Super High Vacuum die Casting Process for Magnesium Alloys", 2009 Metal Casting Congress, Las Vegas, 2009 (in press).
[3] Luo, A.A., Nyberg, E.A., Sadayappan, K. and Shi, W. “Magnesium Front End Research and Development: A Canada-China-USA Collaboration,” in Magnesium Technology 2008, eds., M.O. Pekguleryuz, N.R. Neelameggham, R.S. Beals and E.A. Nyberg, TMS Annual Meeting, New Orleans, LA, USA, March 9-13, 2008, pp. 3-10.
[4] Kasprzak, M., Kasprzak, W., Sokolowski, J.H. and Kierkus, W. US Patent No. 7,354,491 B2, 2008.
[5] Kasprzak, W., Sokolowski, J.H., Sahoo, M. and Dobrzanski, L.A. “Thermal and Structural Characteristics of the AM50 Magnesium Alloy”, Journal of Achievements in Materials and Manufacturing Engineering, vol. 28 (2), pp. 131-138, 2008.
9. Copyright:
This material is based on the paper by K. Sadayappan: Characterization of Magnesium Automotive Components Produced by Super-Vacuum Die Casting Process.
Paper Source: doi:10.4028/www.scientific.net/MSF.618-619.381
This material is a summary based on the above paper, and unauthorized use for commercial purposes is prohibited.
Copyright © 2025 CASTMAN. All rights reserved.