This article introduces the paper "Casting Simulation-Based Design for Manufacturing Backward-Curved Fan with High Shape Difficulty" presented at Metals, MDPI
1. Overview:
- Title: Casting Simulation-Based Design for Manufacturing Backward-Curved Fan with High Shape Difficulty
- Author: Chul Kyu Jin
- Publication Year: 2025
- Publishing Journal/Academic Society: Metals, MDPI
- Keywords: casting simulation; gating system design; sand casting; centrifugal fan; backward fan; blade
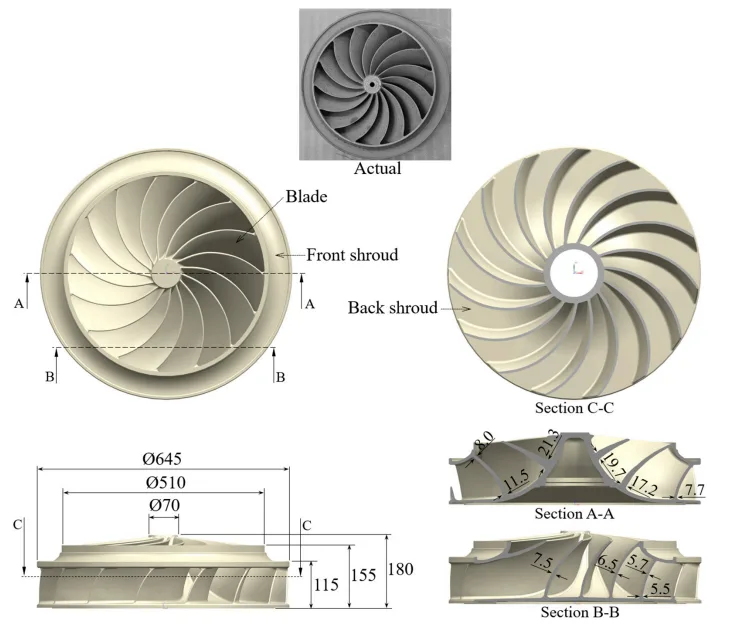
2. Research Background:
In contemporary engineering, centrifugal fans, particularly backward-curved fans, are critical components in high-performance applications, such as engine cooling systems operating at elevated rotational speeds. Manufacturing these complex geometries often presents significant challenges. Sand casting emerges as a viable manufacturing method for producing these intricate shapes as integrated units, circumventing the need for multi-part fabrication and assembly.
However, the existing body of research exhibits a notable gap in the domain of casting mold design and simulation specifically tailored for centrifugal backward-curved fans. This lacuna is particularly pronounced for large-scale applications, with a conspicuous absence of studies addressing the unique demands of sizable fan castings.
This research is necessitated by the industrial demand for efficient manufacturing methodologies for large, complex backward-curved fans. Addressing the limitations of current knowledge, this study aims to leverage casting simulation to design and optimize a gating system for sand casting, ultimately enabling the production of a large-sized backward-curved fan characterized by high shape complexity and casting integrity.
3. Research Purpose and Research Questions:
Research Purpose:
The primary research purpose is to devise and validate a casting simulation-driven design methodology for manufacturing a large-sized aluminum backward-curved fan. This objective is achieved through the optimization of the gating system in a sand casting process, aiming to eliminate casting defects and ensure the structural soundness of the final product.
Key Research Questions:
- What constitutes an optimal gating system design for the sand casting of a large-sized backward-curved fan exhibiting complex geometric features?
- How do different gating system configurations influence the molten metal flow pattern and solidification process within the mold cavity?
- Which gating system design effectively yields a sound casting, free from casting-related defects such as porosity and misruns?
Research Hypotheses:
While not explicitly stated as formal hypotheses, the research implicitly posits that a top-down gating system will outperform bottom-up gating system configurations for casting this complex fan geometry. This expectation is based on the anticipated advantages of top-down systems in promoting more uniform temperature distribution and directional solidification, crucial for minimizing defects in intricate castings.
4. Research Methodology
Research Design:
This research employs a simulation-based design approach, integrating computational fluid dynamics (CFD) and casting simulation software to design and optimize gating systems. The simulation findings are subsequently validated through experimental casting and material characterization.
Data Collection Method:
Data acquisition is multifaceted, encompassing:
- Casting Simulation: Utilizing MAGMA V5 software to simulate the casting process for different gating system designs.
- Experimental Casting: Fabricating a backward-curved fan using the optimized gating system in a sand casting setup.
- Mechanical Testing: Conducting tensile and Vickers hardness tests on specimens extracted from the cast fan.
- Non-Destructive Testing: Employing X-ray imaging to assess internal casting soundness and detect porosity.
- Microstructural Analysis: Examining the microstructure of the cast material at various locations using microscopy.
Analysis Method:
The analytical framework comprises:
- Flow Analysis: Employing Ansys Fluent to predict fan performance and derive pressure loads for structural analysis.
- Structural Analysis: Utilizing Ansys Static Structural to evaluate fan deformation and stress under operational loads.
- Casting Simulation Analysis: MAGMA V5 simulations are analyzed to assess molten metal flow velocity, temperature distribution, solidification patterns, air entrapment, hotspot formation, and porosity.
- Mechanical Property Evaluation: Analyzing tensile strength, yield strength, elongation, and hardness from mechanical tests.
- Microstructure Characterization: Identifying and quantifying phases present in the microstructure to correlate with solidification behavior and mechanical properties.
Research Subjects and Scope:
The subject of this research is a large-sized backward-curved fan designed for demanding applications. The scope is defined by:
- Component: A large-sized backward-curved fan with 15 blades, manufactured from Al-Si-Mg alloy (A360).
- Manufacturing Process: Sand casting.
- Gating Systems: Three distinct gating system designs are investigated: bottom-up with four gates, bottom-up with ten gates, and top-down with a feeder.
5. Main Research Results:
Key Research Results:
The study's findings underscore the efficacy of casting simulation in optimizing gating system design for complex sand castings. The top-down gating system emerged as the superior configuration, yielding a sound casting validated experimentally. Key results for different gating systems are summarized below:
- Bottom-up with Four Gates: Simulation revealed significant temperature loss during molten metal flow into thin blades, leading to non-uniform solidification and potential for unfilled sections. A temperature range below the liquidus temperature was observed.
- Bottom-up with Ten Gates: While exhibiting similar flow and solidification patterns to the four-gate system, this design showed a marginal reduction in molten metal temperature loss.
- Top-down Gating System: This configuration demonstrated significantly reduced temperature loss during mold filling, promoting directional solidification. The feeder effectively acted as a riser, substantially mitigating porosity. Simulation results indicated a sound casting without unfilled parts, which was experimentally confirmed.
- Experimental Validation: The fan cast using the top-down gating system exhibited excellent soundness, devoid of unfilled sections, corroborating the simulation predictions.
- Mechanical Properties: Tensile testing on specimens from the top-down cast fan yielded a yield strength of 154.6 MPa, a tensile strength of 299.8 MPa, and an elongation of 3.6%. The Vickers hardness was measured at 65 HV.
Statistical/Qualitative Analysis Results:
- Fluid Dynamics and Structural Analysis:
- Static pressure drop across the fan: 8674.5 Pa.
- Calculated required power: 138.2 kW.
- Maximum total deformation under load: 0.00078 mm.
- Maximum equivalent stress: 0.241 MPa.
- Gating System Performance Metrics:
- Recovery Rate (Fan weight / Total casting weight): Bottom-up 4 gates (84.6%), Bottom-up 10 gates (71.6%), Top-down (72.5%).
- Sprue:Runner:Gate (SRG) Ratio: Bottom-up 4 gates (1.00:1.75:2.00), Bottom-up 10 gates (1.00:1.75:2.71).
- Molten Metal Flow Velocity: Analysis of flow velocity at gates and feeder revealed variations across different gating designs, impacting mold filling characteristics.
- Temperature Distribution and Solidification: Simulation visually represented temperature gradients and solidification progression, highlighting the superior uniformity and directional solidification achieved with the top-down system.
- Hotspot and Porosity Distribution: Hotspot and porosity simulations indicated reduced defect potential with the top-down design compared to bottom-up configurations.
Data Interpretation:
The simulation data robustly indicates that the top-down gating system provides a more favorable casting process for the complex backward-curved fan. The reduced temperature loss, directional solidification, and minimized porosity predicted by simulation directly translated to a sound casting in experimental validation. The bottom-up systems, particularly the four-gate design, exhibited limitations in maintaining melt temperature and achieving uniform solidification, increasing the risk of casting defects.
Figure Name List:
- Figure 1. Two-dimensional dimensions of the backward-curved fan.
- Figure 2. Simulation results by Ansys Fluent: (a) static pressure; (b) velocity.
- Figure 3. Simulation results by Ansys Static structural: (a) total deformation; (b) equivalent stress.
- Figure 4. Three types of gating systems for the backward-curved fan: (a) bottom-up with four gates; (b) bottom-up with ten gates; (c) top-down (unit: mm).
- Figure 5. The division plane of mold for the backward-curved fan: (a) bottom-up with four gates; (b) bottom-up with ten gates; (c) top-down.
- Figure 6. Flow velocity of molten metal at each gate: (a) bottom-up type with four gates; (b) bottom-up type with ten gates.
- Figure 7. Temperature change distribution of molten metal in mold cavity: (a) bottom-up with four gates; (b) bottom-up with ten gates; (c) top-down type.
- Figure 8. Air entrapment in mold cavity: (a) bottom-up with four gates; (b) bottom-up with ten gates; (c) top-down type.
- Figure 9. Solidification pattern of molten metal in mold cavity: (a) bottom-up with four gates; (b) bottom-up with ten gates; (c) bottom-up with ten gates and risers; (d) top-down type.
- Figure 10. Distribution of hotspot and porosity after solidification: (a) bottom-up with four gates; (b) bottom-up with ten gates; (c) bottom-up with ten gates and risers; (d) top-down type.
- Figure 11. Backward-curved fan manufactured by sand casting with top-down gating system: (a) front; (b) back.
- Figure 12. X-ray image of tensile specimens machined in back shroud.
- Figure 13. Microstructures of the backward-curved fan manufactured by sand casting with a top-down gating system: (a) front shroud; (b) back shroud; (c) blade.
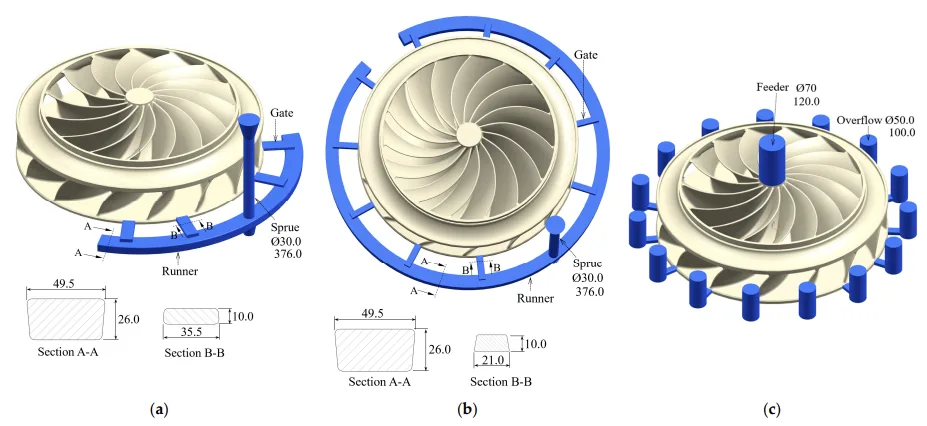
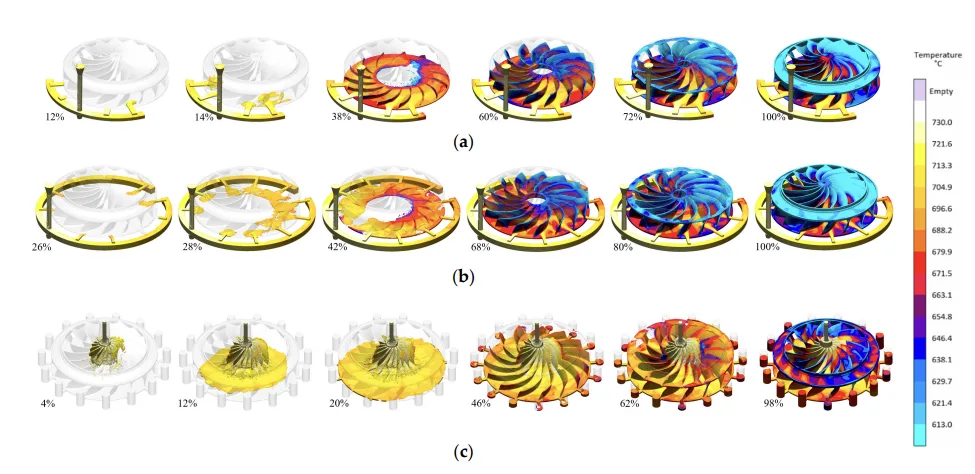
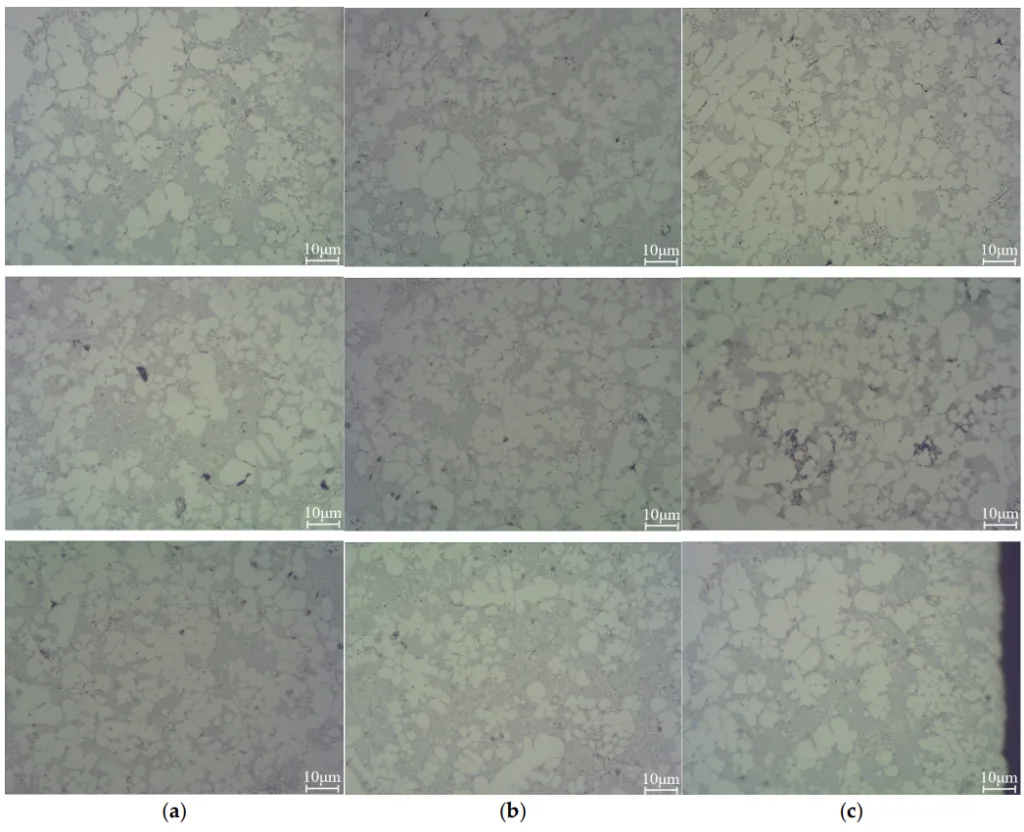
6. Conclusion and Discussion:
Summary of Main Results:
This research successfully demonstrated the application of casting simulation for the design and optimization of gating systems for sand casting a large and geometrically complex backward-curved fan. The top-down gating system was identified as the optimal design through simulation, resulting in a sound casting, which was subsequently validated through experimental casting and material property evaluation.
Academic Significance of the Research:
This study contributes to the academic body of knowledge by highlighting the effectiveness of casting simulation as a predictive tool for gating system design, particularly for intricate geometries like large centrifugal fans. The comparative analysis of different gating configurations provides valuable insights into molten metal flow behavior and solidification dynamics in complex sand castings.
Practical Implications:
The findings offer a practical and robust methodology for manufacturing large-sized backward-curved fans with high shape difficulty using sand casting. The recommended top-down gating system design provides a blueprint for minimizing casting defects and enhancing the quality and reliability of these critical components in industrial applications.
Limitations of the Research:
The scope of this research is primarily limited to the specific fan design and Al-Si-Mg alloy (A360) material investigated. Further research is warranted to assess the generalizability of these findings to other fan designs, alternative materials, and different casting processes.
7. Future Follow-up Research:
Directions for Follow-up Research:
Future research should focus on refining the top-down gating system further, specifically investigating the impact of varying the overflow inlet area to optimize porosity reduction.
Areas Requiring Further Exploration:
- Comprehensive optimization of gating system parameters, including feeder and overflow dimensions and placement.
- Exploration of alternative casting processes, such as investment casting or die casting, for manufacturing similar fan designs.
- Performance testing of the manufactured fan to validate its operational efficiency and durability under intended service conditions.
8. References:
- [1] Son, K.J. Thermo-Electro-Fluidic Simulation Study of Impact of Blower Motor Heat on Performance of Peltier Cooler for Protective Clothing. Energies 2023, 16, 4052.
- [2] Zinchenko, A.; Baiul, K.; Krot, P.; Khudyakov, A.; Vashchenko, S.; Banasiewicz, A.; Wróblewski, A. Materials Selection and Design Options Analysis for a Centrifugal Fan Impeller in a Horizontal Conveyor Dryer. Materials 2021, 14, 6696.
- [3] Le, T.L.; Nghia, T.T.; Thong, H.D.; Son, M.H.K. Numerical study of aerodynamic performance and flow characteristics of a centrifugal blower. Int. J. Intell. Unmanned Syst. 2023, 11, 396–406.
- [4] Lee, Y.T.; Lim, H.C. Performance assessment of various fans ribs inside a centrifugal blower. Energy 2016, 94, 609–622.
- [5] Amer, M. A novel bionic impeller for laptop cooling fan system. Results Eng. 2023, 20, 101558.
- [6] Hsu, Y.S.; Zheng, X.; Cooper, E.; Gillott, M.; Wood, C.J. Evaluation of the indoor pressure distribution during building airtightness tests using the pulse and blower door methods. Build. Environ. 2021, 195, 107742.
- [7] Cattanei, A.; Zecchin, F.M.; Pasquali, A.D.; PhD, A.L. Effect of the uneven blade spacing on the noise annoyance of axial-flow fans and side channel blowers. Appl. Acoust. 2021, 177, 107924.
- [8] Jerchel, M. Leopard 2 Main Battle Tank 1979–1998. New Vanguard 1998, 1, 1–48.
- [9] Aigboje, E.O.; Odiamenhi, A.M. Design and Fabrication of Centrifugal Blower using Locally Sourced Materials. J. Electr. Control Technol. Res. 2021, 3, 11–19.
- [10] Draghici, S.; Vintila, I.S.; Mihalache, R.; Petrescu, H.A.; Tuta, C.S.; Hadar, A. Design and Fabrication of Thermoplastic Moulds for Manufacturing CFRP Composite Impeller Blades. Mater. Plast. 2020, 57, 290–298.
- [11] Aung, K.; Sein, N.W.; Nyi, N. Design and Fabrication of impeller for Single Suction Centrifugal Pump. Int. J. Sci. Res. Publ. 2019, 9, 799–805.
- [12] Hernández, F.; Fragoso, A. Fabrication of a Stainless-Steel Pump Impeller by Integrated 3D Sand Printing and Casting: Mechanical Characterization and Performance Study in a Chemical Plant. Appl. Sci. 2022, 12, 3539.
- [13] Kim, J.T.; Kim, S.I.; Choi, J.Y.; Koo, C.W. A 3D Miniaturized Glass Magnetic-Active Centrifugal Micropump Fabricated by SLE Process and Laser Welding. Micromachines 2022, 13, 1331.
- [14] Iqbal, H.; Sheikh, A.K.; Al-Yousef, A.H.; Younas, M. Mold Design Optimization for Sand Casting of Complex Geometries Using Advance Simulation Tools. Mater. Manuf. Process 2012, 27, 775–785.
- [15] Kim, E.H.; Choi, H.H.; Jung, Y.G. Fabrication of a ceramic core for an impeller blade using a 3D printing technique and inorganic binder. J. Manuf. Process 2020, 53, 43–47.
- [16] Pratesa, Y.; Munir, B.; Najamuddin, S. Application of Casting Simulation in Failure Analysis of Impeller. J. Fail. Anal. Prev. 2019, 19, 431–437.
- [17] Anggono, A.D.; Prihtiantoro, D.; Siswanto, W.A. Casting Design, Simulation and Manufacturing Validation of Air Compressor Fan Blade. Int. J. Mech. Mechatron. Eng. 2020, 20, 181–189.
- [18] Khan, M.A.A.; Sheikh, A.K.; Asad, M. Mold Design and Casting of an Impeller Using MAGMASoft. Int. J. Mech. Eng. Robot. Res. 2020, 9, 1579–1583.
- [19] CHEN, L.; LING, Y.; KANG, X.; XIA, L.; LI, K. Numerical Simulation of Stress and Deformation for a Duplex Stainless Steel Impeller during Casting and Heat Treatment Processes. J. Mater. Sci. Technol. 2008, 24, 364–368.
- [20] Dermawan, A.; Pramono, A.E. Engineering and Process of Investment Casting for Pump Impellers. RiESTech 2023, 1, 11–19.
- [21] Wang, D.; Dong, A.; Zhu, G.; Shu, D.; Sun, J.; Li, F.; Sun, B. Rapid casting of complex impeller based on 3D printing wax pattern and simulation optimization. Int. J. Adv. Manuf. Technol. 2016, 100, 2629–2635.
- [22] Choe, C.M.; Yang, W.C.; Kim, U.K.; Ri, B.G.; Om, M.S. Manufacture of centrifugal compressor impeller using FDM and investment casting. Int. J. Adv. Manuf. Technol. 2022, 118, 173–181.
- [23] Kuo, J.K.; Huang, P.H.; Lai, H.Y.; Chen, J.R. Optimal gating system design for investment casting of 17-4PH stainless steel enclosed impeller by numerical simulation and experimental verification. Int. J. Adv. Manuf. Technol. 2017, 92, 1093–1103.
- [24] Wang, D.; Sun, J.; Dong, A.; Shu, D.; Zhu, G.; Sun, B. An optimization method of gating system for impeller by RSM and simulation in investment casting. Int. J. Adv. Manuf. Technol. 2018, 98, 3105–3114.
- [25] MA, X.; Zhuang, Y.; Tao, Y. Numerical Simulation of Die-casting Magnesium Alloy Impeller with the Central Gating System. Appl. Mech. Mater. 2011, 55–57, 2126–2129.
- [26] Liu, Y.; He, H.; Gao, J.; Li, G.; Liang, Y.; Li, L. Research on the low-pressure casting process of a double suction impeller in 304 austenitic stainless steel with high performance and thin-wall complex structure. J. Phys. Conf. Ser. 2022, 2390, 012078.
- [27] Wallace, G.; Jackson, A.P.; Midson, S.P.; Zhu, Q. High-quality aluminum turbocharger impellers produced by thixocasting. Trans. Nonferrous Met. Soc. 2010, 20, 1786–1791.
- [28] Hafeez, F.; Ahmed, N.; Ali, M.A.; Farooq, M.U.; Rehman, A.U. A comprehensive efficiency evaluation of conventional and ablation sand casting on the example of the AlSi7Mg alloy impeller. Int. J. Adv. Manuf. Technol. 2022, 121, 3653–3672.
- [29] Caceres, C.H.; Davidson, C.J.; Griffiths, J.R.; Wang, Q.G. The Effect of Mg on the Microstructure and Mechanical Behavior of Al-Si-Mg Casting Alloys. Metall. Mater. Trans. 1999, 30, 2611–2618.
- [30] Seo, H.Y.; Jin, C.K.; Kang, C.G. Design of a gate system and riser optimization for turbine housing and the experimentation and simulation of a sand casting process. Adv. Mech. Eng. 2018, 10, 1–12.
- [31] Sun, J.J.; Le, Q.C.; Wang, T.; Zhao, X.; Shi, W.S.; Huo, H.W.; Wang, C. Investigation on heat-transfer-coefficient between aluminum alloy and organic inorganic sand mold based on inverse method. Res. Dev. 2019, 16, 336–341.
- [32] Yang, H.; Shan, Z.; Wang, Y.; Liu, L. Simulation of temperature field of A356 aluminum alloy in freeze casting. J. Phys. Conf. Ser. 2020, 1600, 012045.
- [33] Wang, Q.G.; Davidson, C.J. Solidification and precipitation behaviour of Al-Si-Mg casting alloys. J. Mater. Sci. 2001, 36, 739–750.
- [34] Shabestari, S.G.; Moemeni, H. Effect of copper and solidification conditions on the microstructure and mechanical properties of Al-Si-Mg alloys. J. Mater. Process. Technol. 2004, 153–154, 193–198.
- [35] Wang, Y.; Liao, H.; Wu, Y.; Yang, J. Effect of Si content on microstructure and mechanical properties of Al-Si-Mg alloys. Mater. Des. 2014, 53, 634–638.
- [36] Cheng, W.; Liu, C.Y.; Huang, H.F.; Zhang, L.; Zhang, B.; Shi, L. High strength and ductility of Al-Si-Mg alloys fabricated by deformation and heat treatment. Mater. Charact. 2021, 178, 111278.
- [37] ASTM E8; Standard Test Methods of Tension Testing of Metallic Materials. American Society for Testing and Materials: Montgomery, PA, USA, 2024; Volume 3.01.
9. Copyright:
- This material is "Chul Kyu Jin"'s paper: Based on "Casting Simulation-Based Design for Manufacturing Backward-Curved Fan with High Shape Difficulty".
- Paper Source: https://doi.org/10.3390/met15020099
This material was summarized based on the above paper, and unauthorized use for commercial purposes is prohibited.
Copyright © 2025 CASTMAN. All rights reserved.