The content of this introduction paper is based on the article "Analysis of Induction Motor Used In Electric Vehicle Applications and Comparison of Copper Rotor Bars with Aluminium Rotor Bars Using Finite Element Method" published by Zenodo.
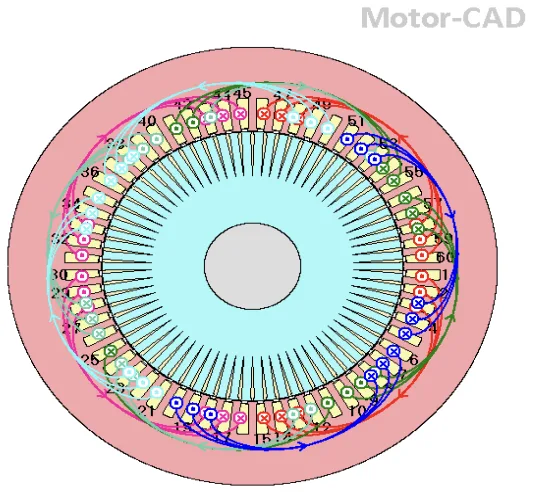
1. Overview:
- Title: Analysis of Induction Motor Used In Electric Vehicle Applications and Comparison of Copper Rotor Bars with Aluminium Rotor Bars Using Finite Element Method
- Author: Doğukan Ayhan
- Year of publication: July 2023
- Journal/academic society of publication: Zenodo
- Keywords: Induction Motor, Aluminium Rotor Bars for Induction Motor, Copper Rotor Bars for Induction Motor, Analysis, Optimization, Finite Element Method, Electric Vehicle, ANSYS Motor-CAD
2. Abstract:
"In this article, induction motor analysis of Tesla Model S was made firstly and then two materials for rotor bars analysis and comparison were made for induction motor of Tesla Model S. These material types of rotor bars are aluminium and copper. The advantages and disadvantages of two different materials for induction motor rotor bars of Tesla Model S were compared. Finally, evaluations and inferences were made with the analyzes and comparisons made."
3. Introduction:
"Thus, the paper aims to analyze to induction motor of Tesla Model S as thermally and electromagnetically and compare Copper Rotor Bars with Aluminium Rotor Bars using finite element element method with all the available data for Tesla Model S induction motor."
4. Summary of the study:
Background of the research topic:
The selection of the appropriate motor for electric vehicles is crucial, necessitating consideration of all motor components. The material selection for rotor bars significantly impacts the efficiency, temperature, and weight of squirrel cage induction motors.
Status of previous research:
The paper references previous work on electric motor models for EV traction, power traction motor systems, and comparative studies of windings in induction motors for automotive applications. It also references a Tesla Model S benchmarking overview.
Purpose of the study:
The study aims to analyze the induction motor of the Tesla Model S, comparing copper and aluminum rotor bars using the finite element method.
Core study:
The core study involves analyzing a squirrel cage induction motor of Tesla Model S with two different rotor bar materials: copper and aluminum. The advantages and disadvantages of each material are compared.
5. Research Methodology
Research Design:
The research uses finite element analysis to compare the performance of induction motors with copper and aluminum rotor bars.
Data Collection and Analysis Methods:
The analysis is completed using ANSYS Motor-CAD software. The maximum temperatures of rotor cage and stator winding were set as 150°C and 180°C at the beginning of analysis, which represents industrial insulation class F and operation temperatures of stator winding, rotor bar and end ring were set as 100°C [5]. The saturation model is created as FEA in the ANSYS Motor-CAD.
Research Topics and Scope:
The study focuses on the electromagnetic and thermal analysis of the Tesla Model S induction motor, specifically comparing the impact of copper versus aluminum rotor bars on motor performance.
6. Key Results:
Key Results:
- A squirrel cage induction motor with copper rotor bars has better performance than squirrel cage induction motor aluminum rotor bars as expected.
- The weight of a squirrel cage induction motor with copper rotor bars is significantly heavier and more expensive in cost than a squirrel cage induction motor with aluminum rotor bars.
- The total losses are less, so squirrel cage induction motor with copper bars is much more efficient than squirrel cage induction motor with aluminum bars.
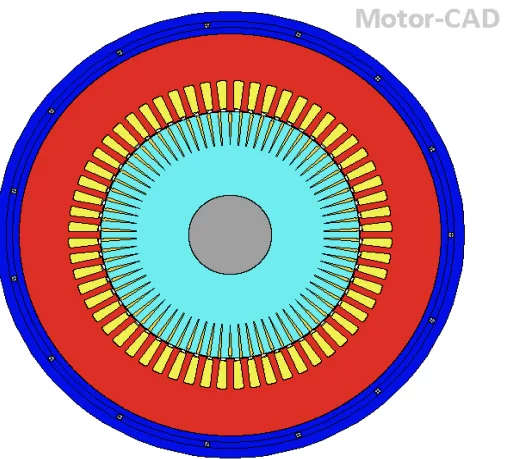
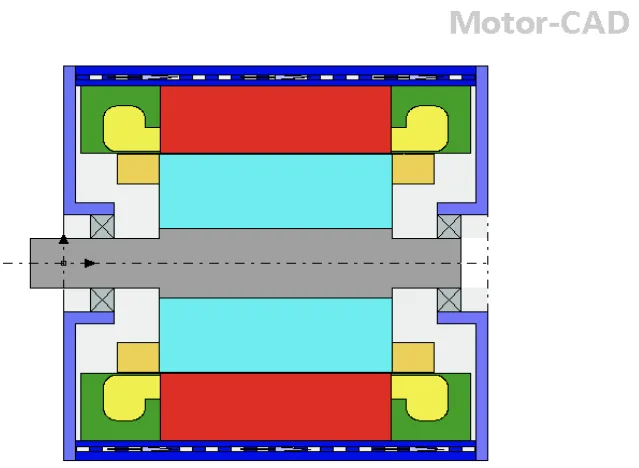
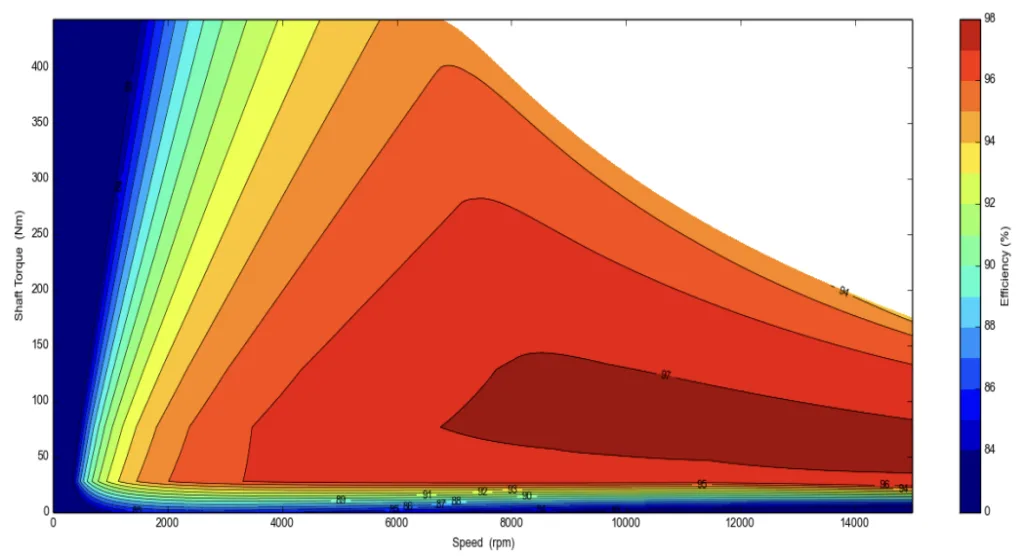
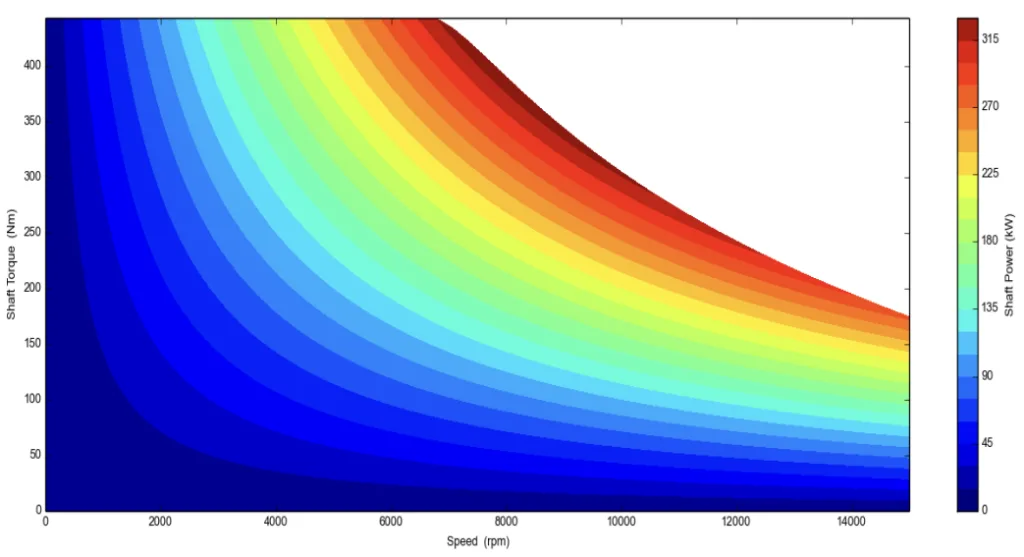
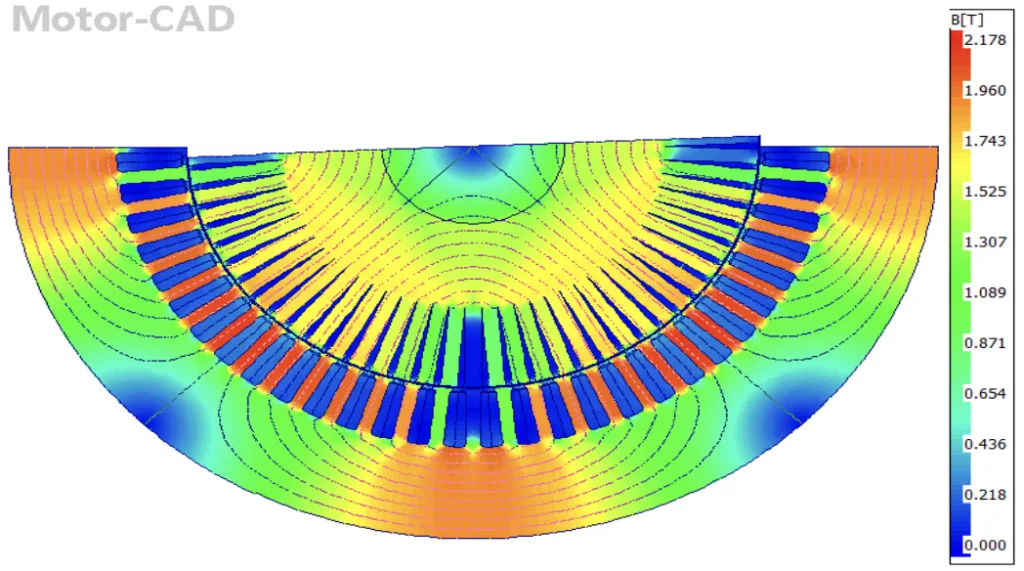
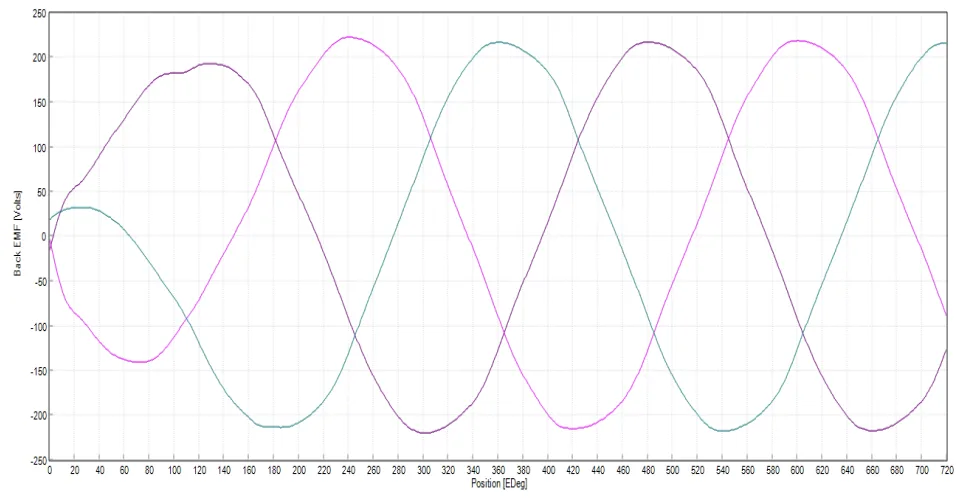
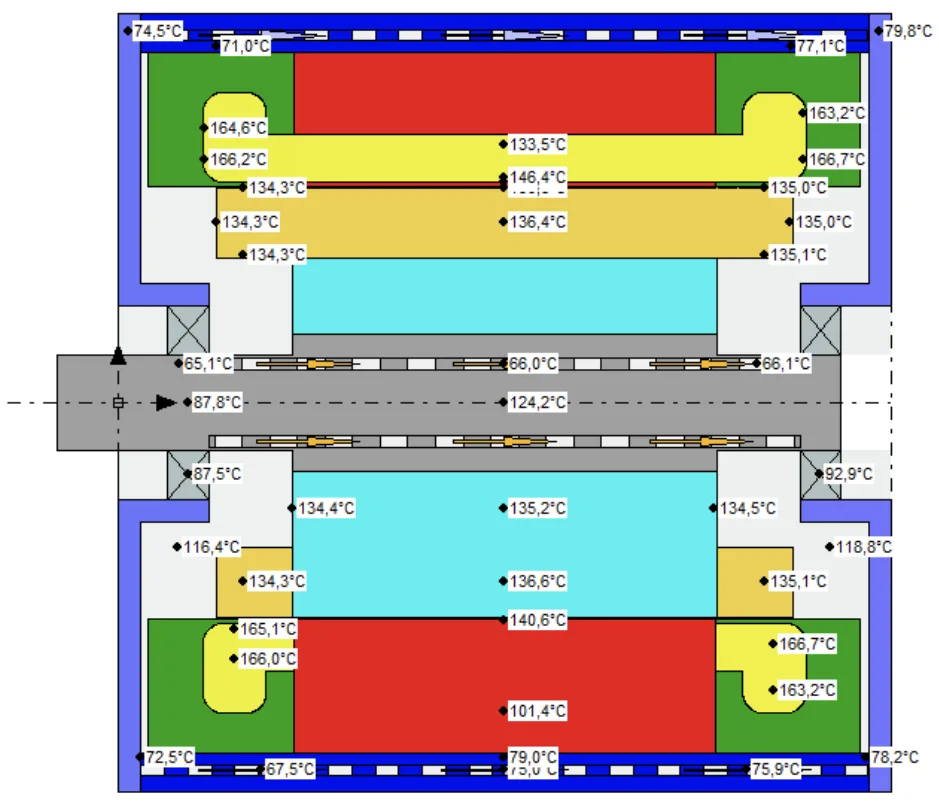
Figure Name List:
- Fig.2.Winding pattern of stator
- Fig.3.IM 2D radial view
- Fig.4.IM 2D axial view
- Fig.5.FE model Efficiency map of first model
- Fig.6.FE model mechanical power map of first model
- Fig.7. 2D FE model with flux density levels and field lines of first model
- Fig.8.Mechanical power map of the maximum normal operation region of first model
- Fig.9.Back EMF waveforms of first model
- Fig.10.Inductances of first model
- Fig.11.Total losses and rotor cage losses maps of first model
- Fig.12. The price change plot of copper and aluminum elements [6]
- Fig.13.Efficiency map of second model
- Fig.14.Mechanical power map of the maximum normal operation region of second model
- Fig.15.The total losses and rotor cage losses maps of second model
- Fig.16.The lumped circuit nodal temperatures
- Fig.17.The 2-D steady state thermal analysis of first model for rotor
- Fig.18.The 2-D steady state thermal analysis of second model for rotor
7. Conclusion:
"It is impossible to pick the best rotor material for every situation. The analysis shows that a squirrel cage induction motor with copper rotor bars has better performance than squirrel cage induction motor aluminum rotor bars as expected. Today, the cost of copper is important. Therefore, instead of the copper conductor bars inside the cage of the squirrel cage induction motor aluminum bars can be preferred various application because of the following advantages."
8. References:
- [1] Staton, D.A.; Goss, J. Open source electric motor models for commercial EV & Hybrid traction motors. Presented at Coil Winding, Insulation & Electrical Manufacturing Exhibition (CWIEME), Berlin, Germany, 20-22 June 2017.
- [2] M. Popescu, J. Goss, D. A. Staton, D. Hawkins, Y. C. Chong and A. Boglietti, "Electrical Vehicles-Practical Solutions for Power Traction Motor Systems," in IEEE Transactions on Industry Applications, vol. 54, no. 3, pp. 2751-2762, May-June 2018.
- [3] H. Koke, "Comparative study of stranded and bar windings in an induction motor for automotive propulsion applications.", M.A.Sc thesis, McMaster University, Hamilton, Ontario, Canada, Aug. 2017.
- [4] Motor Design Limited, "Tesla Model S 60 benchmarking overview_V2," Ricardo eStore, 2013. [Online]. Available: https://estore.ricardo.com/en/tesla-model-s-60-benchmarking-overview---c-23-c-70-p-244. [Accessed: 03-Sep-2022].
- [5] J. Goss, M. Popescu, D. Staton, D. Hawkins and A. Boglietti, "Electrical vehicles practical solutions for power traction drive systems," 2017 IEEE Workshop on Electrical Machines Design, Control and Diagnosis (WEMDCD), 2017, pp. 80-88, doi: 10.1109/WEMDCD.2017.7947728.
- [6] E. Brocklehurst, "Scrap metals and auto recycling commodity performance August 2021," Advanced Remarketing Services, 21-Feb-2022. [Online]. Available: https://ec2-34-193-100-78.compute-1.amazonaws.com/low-value-vehicle-outlook-july-2021-2/. [Accessed: 11-Nov-2022].
9. Copyright:
- This material is a paper by "Doğukan Ayhan". Based on "Analysis of Induction Motor Used In Electric Vehicle Applications and Comparison of Copper Rotor Bars with Aluminium Rotor Bars Using Finite Element Method".
- Source of the paper: [DOI: 10.5281/zenodo.8117591]
This material is summarized based on the above paper, and unauthorized use for commercial purposes is prohibited.
Copyright © 2025 CASTMAN. All rights reserved.