This article introduces the paper ['Analysis of alloying elements and Mechanical properties of T6 treated Aluminium Silicon Alloys'] published by ['International Journal of Engineering Research & Technology (IJERT)'].
1. Overview:
- Title: Analysis of alloying elements and Mechanical properties of T6 treated Aluminium Silicon Alloys
- Author: V. Sankar, Dr. Shiva Shankare Gowda. A.S, Dr. A. Ramesha, Dr. P. Maniiarasan
- Publication Year: 2014
- Publishing Journal/Academic Society: International Journal of Engineering Research & Technology (IJERT)
- Keywords: Microstructure, Tensile strength, SEM, Wear
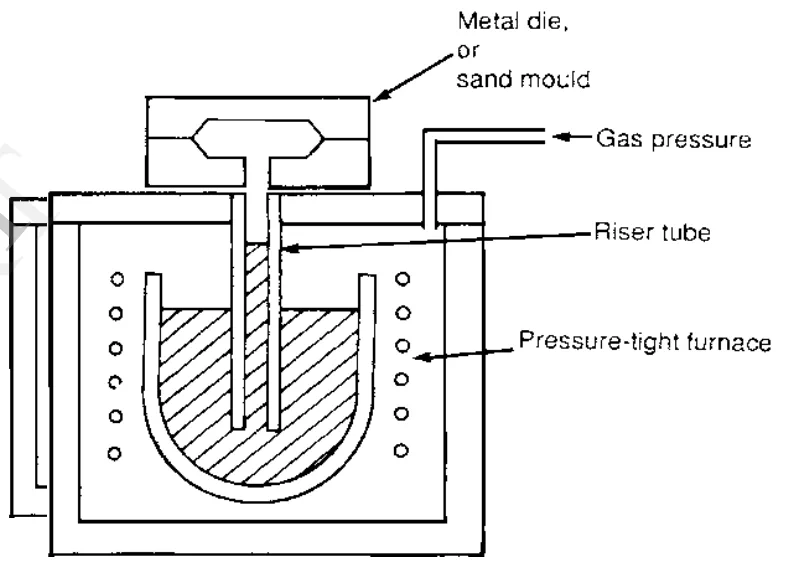
2. Abstracts or Introduction
Abstract
In last decade there has been a rapid increase in the utilization of aluminium-silicon alloys, particularly in automobile industries due to high specific strength, high wear resistance, low density and low coefficient of thermal expansion. The advancements in the field of application prompted to study wear and tensile behaviour of these alloys utmost importance. Aluminium based alloys containing 7%, 12% and 14% weight of silicon were synthesized using casting methods. Compositional analysis and Microstructural studies of different samples of same composition have shown near uniform distribution of Si in the present alloys. Study of microstructure has showed the presence of the primary silicon. Tensile tests were carried out with universal testing machine. Yield strength and ultimate tensile strength has increased with increase in silicon percentage. Wear behaviour were studied by using computerized pin on disc wear testing machine. Resistance to wear has increased with increase in silicon amount. The worn surfaces were analyzed using scanning electron microscope.
1. Introduction
In last decade there has been a rapid increase in the utilization of aluminium-silicon alloys, particularly in automobile industries due to high strength to weight ratio( specific strength), high wear resistance, low density and low coefficient of thermal expansion. The advancements in the field of application prompted to study wear and tensile behaviour of these alloys. Aluminium based alloys containing 7%, 12% and 14% weight of silicon were synthesized using casting methods. Compositional analysis and Microstructural studies of different samples of same composition have shown near uniform distribution of Si in the present alloys. Tensile tests were carried out with universal testing machine. Yield strength and ultimate tensile strength has increased with increase in silicon percentage. This paper carries out review of the of Al cast alloys, followed by a discussion of the various enabling tools available to the industry, which were not available to the metal casting industry ten years ago or so.
3. Research Background:
Background of the Research Topic:
The utilization of aluminium-silicon alloys has seen a rapid increase in the last decade, particularly within the automotive industry. This surge is attributed to the inherent advantages of these alloys, including high specific strength, exceptional wear resistance, low density, and a low coefficient of thermal expansion. These properties make aluminium-silicon alloys highly desirable for demanding applications. The advancements in the application of these alloys have necessitated a deeper understanding of their wear and tensile behavior, making this area of study critically important.
Status of Existing Research:
The paper indicates that the advancements in the application domain of aluminium-silicon alloys have driven the need to investigate their wear and tensile characteristics. Furthermore, it is mentioned that the study includes a review of aluminium cast alloys and a discussion on the enabling tools currently available to the industry. The paper also emphasizes the industry's need for tailored alloy optimization for specific performance requirements and the shift from trial-and-error alloy development to more predictive, science-based approaches.
Necessity of the Research:
The research is necessary due to the increasing demand for optimized performance from aluminium alloys in specific applications. Traditional trial-and-error methods for alloy development are inefficient and economically unsustainable. The casting industry requires the means to tailor and optimize alloys for specific performance criteria, such as low cycle fatigue or thermal management. There is a need to optimize alloy processes to fully leverage the advantages of specific casting methods and to utilize predictive tools for more intelligent and effective alloy development and post-processing operations.
4. Research Purpose and Research Questions:
Research Purpose:
The primary purpose of this research is to analyze the influence of alloying elements, specifically silicon content, on the mechanical properties of T6 treated Aluminium Silicon Alloys. The study aims to evaluate the tensile strength and wear resistance of Aluminium based alloys with varying silicon percentages (7%, 12%, and 14% by weight) synthesized using casting methods.
Key Research:
The key research areas investigated in this study are:
- The effect of varying silicon content (7%, 12%, and 14% wt%) on the microstructure of cast Aluminium Silicon Alloys.
- The impact of silicon percentage on the tensile properties, specifically Yield strength and Ultimate tensile strength, of T6 treated Aluminium Silicon Alloys.
- The influence of silicon content on the wear behavior and wear resistance of T6 treated Aluminium Silicon Alloys.
- Microstructural analysis to observe the distribution of silicon and the presence of primary silicon in the alloys.
Research Hypotheses:
Based on the introduction and objectives, the research hypotheses can be inferred as follows:
- Increasing the silicon percentage in Aluminium Silicon Alloys will lead to an increase in Yield strength and Ultimate tensile strength after T6 heat treatment.
- Higher silicon content in Aluminium Silicon Alloys will result in improved resistance to wear.
- T6 heat treatment will enhance the tensile strength and reduce the aspect ratio of eutectic silicon particles in the Aluminium Silicon Alloys.
5. Research Methodology
Research Design:
The research employs an experimental design involving the synthesis of Aluminium based alloys with varying silicon content (7%, 12%, and 14% weight of silicon) using casting methods. These alloys were then subjected to T6 heat treatment. The study investigates the mechanical properties and microstructure of these alloys through a series of tests.
Data Collection Method:
The following methods were used for data collection:
- Compositional Analysis: Performed to verify the chemical composition of the synthesized alloys and ensure near uniform distribution of silicon.
- Microstructural Studies: Conducted to examine the microstructure of the alloys, including the distribution of silicon and the presence of primary silicon, using techniques such as Scanning Electron Microscopy (SEM).
- Tensile Tests: Carried out using a universal testing machine to determine the Yield strength and Ultimate tensile strength of the alloys.
- Wear Tests: Performed using a computerized pin on disc wear testing machine to evaluate the wear behavior and resistance of the alloys.
- SEM Analysis of Worn Surfaces: Utilized to analyze the worn surfaces after wear testing to understand the wear mechanisms.
Analysis Method:
The analysis methods employed in this research include:
- Comparative Analysis: Comparing the mechanical properties (Yield strength, Ultimate tensile strength, and wear resistance) of the alloys with different silicon percentages to determine the effect of silicon content.
- Microstructural Analysis Interpretation: Analyzing SEM micrographs to assess the silicon distribution, presence of primary silicon, and the impact of T6 treatment on the microstructure.
- Correlation Analysis: Establishing correlations between silicon content, microstructure, tensile properties, and wear resistance.
Research Subjects and Scope:
The research subjects are Aluminium based alloys containing 7%, 12%, and 14% weight of silicon. These alloys are synthesized using casting methods and are based on the Alloy 356 – AlSi7Mg system. The scope of the study is limited to the analysis of compositional, microstructural, tensile, and wear properties of these specific alloys after T6 heat treatment. The casting method employed for alloy synthesis is low pressure and gravity die casting.
6. Main Research Results:
Key Research Results:
The key research findings are:
- Silicon Distribution: Compositional analysis and Microstructural studies revealed a near uniform distribution of silicon (Si) in the synthesized alloys. The study of microstructure also indicated the presence of primary silicon.
- Tensile Strength Improvement: Tensile tests demonstrated that both Yield strength and Ultimate tensile strength increased with an increase in silicon percentage in the Aluminium Silicon Alloys.
- Enhanced Wear Resistance: Wear behavior studies, conducted using a computerized pin on disc wear testing machine, showed that resistance to wear increased with an increase in silicon content.
- T6 Heat Treatment Effectiveness: T6 heat treatment was found to be effective in achieving maximum tensile strength and fracture elongation for the A356 alloy.
- Spheroidization of Si Particles: The study concluded that solutionization at 535 °C for 8 hours followed by aging for 6 hours can achieve full spheroidization of Si particles.
- Reduction in Aspect Ratio: T6 treatment resulted in a reduction in the aspect ratio of eutectic Si particles.
Analysis of presented data:
The presented data includes tensile properties of A356 alloys with T6 heat treatment in Table 3.
Table 3 Tensile properties of A356 alloys with T6 heat treatment
Heat treatment | ob/Mpa | ot / Mpa | δ% |
---|---|---|---|
T6 | 228 | 324 | 2.0 |
Table 3 shows the tensile properties of T6 treated A356 alloys. 'ob/Mpa' represents Yield Strength, 'ot/Mpa' represents Ultimate Tensile Strength and 'δ%' represents elongation. The data indicates that after T6 heat treatment, the A356 alloy achieved a Yield Strength of 228 MPa, an Ultimate Tensile Strength of 324 MPa, and an elongation of 2.0%. This data supports the conclusion that T6 treatment enhances the tensile properties of A356 alloy.
Figure Name List:
- Figure. The principle of a low pressure die casting machine.
7. Conclusion:
Summary of Key Findings:
This research concluded that increasing silicon content in Aluminium Silicon Alloys enhances both tensile strength and wear resistance. Specifically, Yield strength and Ultimate tensile strength were found to increase with higher silicon percentages. Furthermore, wear resistance also improved with increased silicon content. T6 heat treatment was identified as an effective method to maximize tensile strength and fracture elongation in A356 alloy, and it also aids in achieving full spheroidization of silicon particles and reducing the aspect ratio of eutectic silicon.
Academic Significance of the Study:
This study contributes to the fundamental understanding of the relationship between alloying elements, heat treatment, microstructure, and mechanical properties in Aluminium Silicon Alloys. It provides valuable insights into how silicon content and T6 heat treatment can be manipulated to tailor the properties of these alloys. The findings are significant for materials science and engineering, particularly in the context of light metal alloys and their applications.
Practical Implications:
The findings of this research have practical implications for the die casting industry, particularly in the production of components for the automotive and aerospace sectors. By optimizing silicon content and employing T6 heat treatment, manufacturers can produce Aluminium Silicon Alloy castings with enhanced strength and wear resistance. This can lead to improved component performance, increased service life, and potential weight reduction in various applications. The study also highlights the effectiveness of low pressure die casting for producing high-quality castings.
Limitations of the Study and Areas for Future Research:
The study notes that samples treated with T6 heat treatment did not perform as expected in terms of elongation, potentially due to higher entrapped gas content (0.25 cm3 per 100 g Al). This suggests a limitation related to porosity in the cast samples. Future research should focus on developing methods to purify Al-Si alloys to reduce gas porosity and further improve their mechanical properties. Further investigation into the optimization of T6 heat treatment parameters for different silicon contents could also be beneficial.
8. References:
- [1] ZOLOTOREVSKY V, BELOV NA, GLAZOFF MV. Casting aluminum alloys. 1st ed. Oxford: Elsevier; 2007.
- [2] GAO Z G, ZHANG X M, CHEN MA. Influence of strain rate on the precipitate microstructure in impacted aluminum alloy [J]. Scripta Materialia, 2008, 59: 983-986.
- [3] LI H Z, LING X P, LI F F, GUO F F, LI Z, ZHANG X M. Effect of Y on microstructure and mechanical properties of 2519 aluminum alloy [J]. Transaction of Nonferrous Metals Society of China, 2007, 17(6): 1191-1198.
- [4] XIAO D H, WANG JN, DING D Y, YANG HL. Effect of rare earth Ce addition on the microstructure and mechanical properties of an Al-Cu-Mg-Ag alloy [J]. Journal of Alloys and Compounds, 2003, 352: 84-88.
- [5] P.D. Lee, A. Chirazi, R.C. Atwood, W. Wan, Multiscale modelling of solidification microstructures, including microsegregation and microporosity, in an Al-Si-Cu alloy, Materials Science and Engineering A 365 (2004) 57-65.
- [6] L.J. YANG, The effect of casting temperature on the properties of squeeze cast aluminium and zinc alloys, Journal of Materials Processing Technology 140 (2003) 391-396.
- [7] GAO BO, CHEN LEI, SUN SHUCHEN, TU GANFENG, TIAN XIAOMEI, ZHAO TIEJUN, WU WENYUAN, BIAN XUE. Effect of Nd on microstructure and mechanical properties of hypereutectic Al-25Si alloy. Journal of Rare Earths, 2007, 25(spec): 473.
- [8] SHI W X, GAO B, TU GF, LIS W. Effect of Nd on microstructure and wear resistance of hypereutectic Al-20%Si alloy. Journal of Alloys and Compounds, 2010, 508: 480.
- [9] LIU BIN-YI, XUE YA-JUN. Morphology transformation of eutectic Si in Al-Si alloy during solid solution treatment [J]. Special Casting & Nonferrous Alloys, 2006, 26 (12): 802
- [10] ZHANG D L, ZHENG L H, STJOHN D H. Effect of a short solution treatment time on microstructure and mechanical properties of modified Al-7wt.%Si-0.3wt.%Mg alloy [J]. J Light Metals, 2002, 2(1): 27
- [11] YU Z, ZHANG H, SUN B, SHAO G. Optimization of soaking time for T6 treatment of aluminium alloy [J]. Heat Treatment, 2009, 24(5) (17-20)
- [12] EDWARDS G A, STILLER K, DUNLOP G L, COUPER M J. The precipitation sequence in Al-Mg-Si alloys [J]. Acta Mater, 1998, 46(11): 3 893
- [13] RAN G, ZHOU JE, WANG QG. Precipitates and tensile fracture mechanism in a sand cast A356 aluminum alloy [J]. J Mater Process Technol, 2008, 207(1) (46-52)
- [14] LEE K, KWON Y N, LEE S. Effects of eutectic silicon particles on tensile properties and fracture toughness of A356 aluminum alloys fabricated by low-pressure-casting, casting-forging, and squeeze- casting processes [J]. J Alloys Compounds, 2008, 461 (1-2); 532-541
9. Copyright:
- This material is "V. Sankar, Dr. Shiva Shankare Gowda. A.S, Dr. A. Ramesha, Dr. P. Maniiarasan"'s paper: Based on "Analysis of alloying elements and Mechanical properties of T6 treated Aluminium Silicon Alloys".
- Paper Source: https://www.ijert.org/research/analysis-of-alloying-elements-and-mechanical-properties-of-t6-treated-aluminium-silicon-alloys-IJERTV3IS10218.pdf
This material was summarized based on the above paper, and unauthorized use for commercial purposes is prohibited.
Copyright © 2025 CASTMAN. All rights reserved.