This introduction paper is based on the Doctoral Thesis "Analysis and Reduction of Parasitic Effects in Induction Motors With Die-Cast Rotors" published by "KTH Royal Institute of Technology".
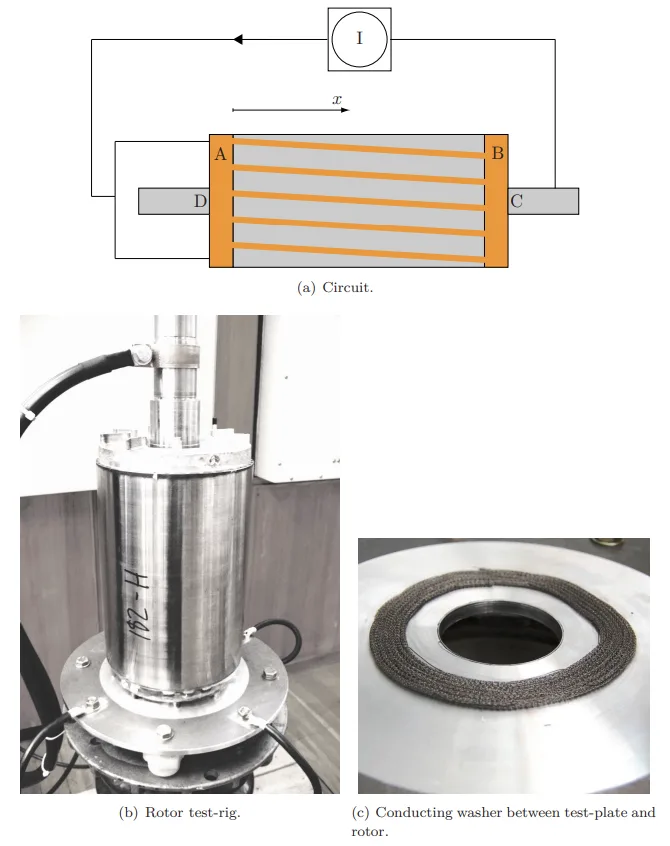
1. Overview:
- Title: Analysis and Reduction of Parasitic Effects in Induction Motors With Die-Cast Rotors
- Author: ALEXANDER STENING
- Year of publication: 2013
- Journal/academic society of publication: KTH Royal Institute of Technology
- Keywords: Aluminium rotors, asynchronous torques, copper rotors, die-cast rotors, induction machines, inter-bar currents, modulated rotors, starting torque, stray losses, synchronous torques.
2. Abstract:
This thesis presents a study of inter-bar current effects on induction motors with die-cast aluminium and die-cast copper rotors. The parasitic effects introduced by these currents are analyzed and possible solutions to these problems are presented. This is realized by developing analytical tools for the simulation of inter-bar current effects. The methods used are verified by measurements on prototype machines. It is shown that the inter-bar currents can have a considerable effect on the motor starting performance, which can result in a reduced pull-out torque. At rated operation, this is seen as increased harmonic rotor currents, having a negative effect on the motor performance.
Results from calorimetric measurements show, that the efficiency gained when substituting a skewed die-cast aluminium rotor with a skewed die-cast copper rotor, is less than the theoretical expectation. It is shown that this is a result of a reduced power factor for the copper rotor. High inter-bar currents are believed to be the origin of this effect, increasing the harmonic content in the rotor magnetomotive force. This would be seen as an increased rotor leakage reactance. Results from locked-rotor tests, and simulations using measured values of inter-bar resistance, support this theory.
It is shown, that these negative effects are suppressed to a negligible level by the use of an unskewed rotor, but to the expense of a large synchronous torque at a low speed. By using a modulated rotor concept, having an asymmetrical rotor slot distribution, an unskewed rotor is designed to reduce this parasitic torque. Measurements on a prototype machine show that the modulated rotor suppresses both the inter-bar currents and the synchronous torque, resulting in an improved starting performance, without any significant change of the motor efficiency. The presented results strengthen the potential of the modulated rotor concept, introducing new possibilities for the reduction of negative effects appearing in induction machines.
3. Introduction:
Induction machines are the most commonly used electrical machines, and improving their efficiency is crucial for energy conservation. Reducing losses involves minimizing not only copper, iron, and friction losses but also additional losses, known as stray-load losses at rated load, which typically range from 0.5% to 3% but can be larger [1, 2, 3]. Small to medium sized induction motors often use cost-effective die-cast aluminium rotors. Advances in casting technology enable die-cast copper rotors, offering higher conductivity and reduced rotor I2R losses (around 40% reduction reported [4]). Further efficiency gains are possible with machine redesign for copper [5, 6, 7, 8].
Rotor skewing is common practice to reduce noise [9] and, if bars are insulated, suppress asynchronous torques and harmonic losses [10]. However, die-cast rotors lack slot insulation, leading to undesired inter-bar currents in skewed designs. These currents increase asynchronous torques during starting [11] and can increase stray-load losses [12, 13], potentially accounting for a large part of them [3].
Industrial experience indicated that substituting die-cast aluminium rotors with die-cast copper rotors yielded less efficiency gain than theoretically expected. This discrepancy was suspected to be due to inter-bar currents, which are strongly influenced by inter-bar resistance, a property likely dependent on cage material and the die-casting process, suggesting differences between aluminium and copper rotors.
4. Summary of the study:
Background of the research topic:
Die-cast rotors are prevalent in induction motors. While copper rotors offer higher conductivity than aluminium, potentially improving efficiency, their implementation, especially with rotor skewing (a common technique), introduces parasitic effects. The lack of insulation in die-cast rotors allows inter-bar currents when skewed, negatively impacting performance (torque characteristics, losses). Understanding and mitigating these effects, particularly the differences between aluminium and copper die-cast rotors, is essential for designing high-efficiency motors.
Status of previous research:
Previous studies confirmed the potential of die-cast copper rotors for loss reduction [4, 5, 6, 7, 8] and analyzed the negative impacts of inter-bar currents in skewed rotors [11, 12, 13]. Methods for measuring inter-bar resistance existed [14, 15, 16]. However, a direct comparison of inter-bar current effects between die-cast aluminium and copper rotors, and the explanation for the lower-than-expected efficiency gains observed with copper, needed further investigation. The concept of modulated rotors to address issues in unskewed designs had been proposed [31] but required evaluation regarding starting performance and losses.
Purpose of the study:
The primary objectives were to evaluate the effects of inter-bar currents on both die-cast aluminium and die-cast copper rotors, determine if the observed lower efficiency of copper rotors compared to theoretical expectations was due to these effects, and propose and verify solutions to mitigate the identified parasitic effects, such as reduced pull-out torque and increased synchronous torques.
Core study:
The research involved measuring inter-bar resistance on aluminium and copper rotors, revealing significantly lower resistance in copper. An analytical model was developed to simulate inter-bar current effects, incorporating saturation and skin effect. Comparative studies (simulations and experiments on 11 kW and 15 kW machines) were conducted on skewed aluminium and copper rotors. These showed that copper rotors exhibited lower pull-out torque and a reduced power factor, leading to lower-than-expected efficiency gains. This was attributed to higher harmonic rotor currents due to lower inter-bar resistance, increasing leakage inductance. The study also investigated unskewed rotors, confirming the suppression of inter-bar currents but highlighting the issue of large synchronous torques. To address this, an unskewed "modulated rotor" concept with an asymmetrical slot distribution was designed, simulated, and tested. This prototype successfully reduced both inter-bar currents and synchronous torques, improving starting performance without significantly impacting rated efficiency.
5. Research Methodology
Research Design:
The study employed a combination of analytical modeling, numerical simulation (including FEM), and experimental verification. It compared the performance of induction motors equipped with different die-cast rotor types: skewed aluminium, skewed copper, unskewed symmetrical aluminium, and a novel unskewed modulated (asymmetrical) aluminium rotor. Two main motor frames were used: an 11 kW machine for Al/Cu comparison and a 15 kW machine for evaluating skew effects and the modulated rotor concept.
Data Collection and Analysis Methods:
- Inter-Bar Resistance Measurement: A dedicated test rig (Fig. 2.1) was developed based on methods by Odok [14] and Dabala [15, 16] to measure inter-bar resistance.
- Analytical Modeling: An analytical model derived from Behdashti's work [17, 11] was used to calculate inter-bar currents and their effects on motor performance (Fig. 2.2). The model included considerations for MMF space harmonics, stator slotting permeance variation, skin effect in rotor bars [18], and saturation of leakage paths (derived from FEM/locked-rotor tests).
- Experimental Testing:
- Direct-on-line starting tests to measure torque-speed characteristics (Fig. 3.1, 4.8, 4.9).
- Calorimetric measurements for accurate determination of total losses and stray-load losses (Table 3.2, Fig. 3.3), with loss separation according to IEC 60034-2-1 [27].
- Rated and partial-load tests to determine efficiency and power factor (Fig. 3.4, Table 3.3, Table 3.4, Table 4.1).
- Locked-rotor tests.
- Simulation: FEM simulations were used to verify leakage path saturation factors and analyze modulated rotor performance (e.g., locked rotor torque variation Fig. 4.4, starting torque Fig. 4.7). Fourier analysis was applied to rotor permeance for modulated designs (Fig. 4.3, 4.5).
Research Topics and Scope:
The research focused on:
- Quantifying inter-bar resistance in die-cast aluminium and copper rotors.
- Analyzing the impact of inter-bar currents on:
- Starting performance (pull-out torque, asynchronous torques, synchronous torques).
- Rated performance (efficiency, power factor, stray-load losses, harmonic rotor currents).
- Comparing performance differences between skewed aluminium and skewed copper rotors.
- Evaluating the trade-offs of using unskewed rotors (reduced inter-bar currents vs. increased synchronous torques).
- Developing and evaluating the "modulated rotor" concept (specifically Progressive Sinusoidal modulation) as a method to reduce synchronous torques in unskewed rotors while maintaining acceptable performance.
- The study was primarily based on 4-pole, 11 kW (shaft height 132 mm, 36 stator/28 rotor slots) and 15 kW (shaft height 160 mm, 36 stator/28 rotor slots) induction motors.
6. Key Results:
Key Results:
- Measurements showed the inter-bar resistivity in the studied die-cast copper rotors is at least ten times lower than in the studied die-cast aluminium rotors (Table 3.1).
- Simulations and measurements confirmed that the pull-out torque is lower for the skewed copper rotor compared to the equivalent skewed aluminium rotor (Fig. 3.1).
- Calorimetric measurements on the 11 kW machine showed the efficiency gain obtained when substituting a skewed aluminium rotor with a skewed copper rotor (0.6 percentage points) was less than the theoretical expectation (1.1 percentage points). This was attributed to a reduced power factor for the copper rotor (Fig. 3.4, Table 3.3).
- The lower power factor in the copper rotor is believed to be caused by high harmonic rotor currents due to low inter-bar resistivity, increasing the harmonic content in the rotor MMF and thus the rotor leakage inductance. Locked-rotor tests supported this.
- For the 11 kW machine, stray-load losses were similar for skewed Al and skewed Cu rotors, suggesting a redistribution rather than reduction of these losses when using copper (Fig 3.3).
- Removing rotor skew eliminates significant inter-bar currents but introduces large synchronous torques, potentially preventing successful starting (Fig 2.3, Fig 4.8).
- A novel unskewed modulated rotor design (asymmetrical slot distribution) was developed and tested on the 15 kW machine.
- Measurements on the prototype modulated rotor showed it successfully suppressed synchronous torques compared to the symmetrical unskewed rotor (Fig 4.8, Fig 4.9), resulting in improved starting performance.
- The modulated rotor achieved this improvement without significant change in rated motor efficiency compared to the standard skewed rotor (Table 4.1).
Figure Name List:
- Figure 1.1: Slot shape for the rotors used in the 11 kW machine.
- Figure 1.2: Slot shape for the rotors used in the 15 kW machine.
- Figure 2.1: Rotor test setup for measurements of inter-bar resistance.
- Figure 2.2: Procedure for the calculation of motor performance at different slip and inter-bar resistivity.
- Figure 2.3: Starting torque for the 15 kW machine at different inter-bar resistivities Rtn.
- Figure 2.4: Additional rotor losses for the 15 kW machine at rated power as a function of inter-bar resistivity.
- Figure 3.1: Starting torque at rated voltage for the studied aluminium and copper rotors skewed by one stator slot pitch.
- Figure 3.2: Additional rotor cage losses simulated as a function of inter-bar resistivity for the skewed rotors at the rated shaft power of 11 kW.
- Figure 3.3: Residual losses as a function of normalized torque squared.
- Figure 3.4: Efficiency (a) and power factor (b) as a function of normalized shaft power.
- Figure 4.1: One quarter of a Dual 24:32 machine having 28 rotor slots and pole symmetry.
- Figure 4.2: One quarter of a PS-rotor having 36 rotor slots and pole symmetry.
- Figure 4.3: Dominating slot numbers for the 36 slot rotor, without PS modulation (black) and with PS modulation (grey).
- Figure 4.4: Locked rotor torque as a function of the rotor position for the 36 slot rotor at different levels of PS modulation.
- Figure 4.5: Dominating slot numbers included in the rotor permeance for the modulated prototype rotor.
- Figure 4.6: One quarter of the modulated prototype rotor, having pole symmetry.
- Figure 4.7: FEM-simulated starting torques for the two unskewed rotors.
- Figure 4.8: Measured torque as a function of speed for the different rotors tested in the same 15 kW stator.
- Figure 4.9: Measured torque during deceleration from no-load to stand-still for the three rotors tested in the same stator.
7. Conclusion:
The study demonstrated that inter-bar resistivity in die-cast copper rotors is significantly lower than in aluminium rotors. This leads to higher inter-bar currents in skewed copper rotors, resulting in a lower pull-out torque compared to equivalent aluminium rotors, as verified by simulations and measurements. Calorimetric tests revealed that the efficiency improvement from using skewed copper instead of skewed aluminium was less than theoretically expected. This derating was linked to a lower power factor in the copper rotor, likely caused by increased rotor leakage inductance due to harmonic currents amplified by the low inter-bar resistance.
Investigating a 15 kW aluminium rotor showed that removing skew reduced pull-out torque by 11%. Simulations indicated skew leakage accounted for only 5%, suggesting inter-bar currents in the skewed rotor created significant braking torques. While the unskewed rotor offered slightly higher efficiency, it suffered from large synchronous torques.
To address these issues, an unskewed modulated rotor with asymmetrical slots was designed and tested. This prototype successfully reduced both inter-bar currents (by being unskewed) and synchronous torques (via modulation), leading to improved starting performance. Importantly, this was achieved without a significant change in motor efficiency compared to the standard skewed rotor, despite some manufacturing imperfections. These findings confirm the potential of the modulated rotor concept as a flexible solution to mitigate parasitic effects in induction machines.
8. References:
- [1] A.R. Hagen, A. Binder, M. Aoulkadi, T. Knopik, and K. Bradley. Comparison of measured and analytically calculated stray load losses in standard cage induction machines. Proc. of International Conference on Electrical Machines, pages 1–6, 2008.
- [2] A.A. Jimoh, R.D. Findlay, and M. Poloujadoff. Stray losses in induction machines: Part i, definition, origin and measurement. IEEE Trans. on Power Apparatus and Systems, PAS-104:1500–1505, 1985.
- [3] H. Nishizawa, K. Itomi, S. Hibino, and F. Ishibashi. Study on reliable reduction of stray load losses in three-phase induction motor for mass production. IEEE Trans. on Energy Conversion, EC-2:489–495, 1987.
- [4] D. T. Peters, D. J. Van Son, J. G. Cowi, and E. F. Brush. Improved motor energy efficiency and performance through the die-cast copper rotor. In Proc. of International Conference on Electrical Machines, Aug. 2002.
- [5] S. Lie and C. Di Pietro. Copper die-cast rotor efficiency improvement and economic consideration. IEEE Trans. on Energy Conversion, 10(3):419–424, Sep 1995.
- [6] R. Kimmich, M. Doppelbauer, D. T. Peters, J. G. Cowi, and E. F. Brush. Die-cast copper rotor motors via simple substitution and motor redesign for copper. In Proc. of International Conference on Electrical Machines, Sept. 2006.
- [7] J. L. Kirtley, J. G. Cowie, E. F. Brush, D. T. Peters, and R. Kimmich. Improving induction motor efficiency with die-cast copper rotor cages. In Proc. of IEEE PES General Meeting, pages 1–6, June 2007.
- [8] D. T. Peters, E. F. Jr Brush, and J. L. Kirtley. Die-cast copper rotors as strategy for improving induction motor efficiency. In Proc. of Electrical Insulation Conference and Electrical Manufacturing, pages 322–327, Oct. 2007.
- [9] P. Vijayraghavan and R. Krishnan. Noise in electric machines: a review. IEEE Trans. on Industry Applications, 35(5):1007–1013, sep/oct 1999.
- [10] P. L. Alger. Induction Machines: Their Behavior and Uses. Taylor & Francis, 1995.
- [11] A. Behdashti and M. Poloujadoff. A new method for the study of inter-bar currents in polyphase squirrel-cage induction motors. IEEE Trans. on Power Apparatus and Systems, PAS-98(3):902–911, 1979.
- [12] Y.N. Feng, J. Apsley, S. Williamson, A.C. Smith, and D.M. Ionel. Reduced losses in die-cast machines with insulated rotors. IEEE Trans. on Industry Applications, 46(3):928–936, May-June 2010.
- [13] S. C. Englebretson. Induction machine stray loss from inter-bar currents. Ph.d. thesis, Massachusetts Institute of Technology, Sept. 2009.
- [14] A. M. Odok. Stray-load losses and stray torques in induction machines. AIEE Trans. on Power Apparatus and Systems, 77(3):43–53, 1958.
- [15] K. Dabala. A new experimental-computational method to determine rotor bar-iron resistance. Proc. of International Conference on Electrical Machines, 2:69–72, 1996.
- [16] K. Dabala. Modified method to determine rotor bar-iron resistance in three-phase copper casted squirrel-cage induction motors. Proc. of International Conference on Electrical Machines, pages 231–234, 2006.
- [17] A. Behdashti. Contribution a l’etude des pertes supplementaires des machines asynchrones dans une tres large zone de fonctionnement. PhD thesis, L’Institut national polytechnique de Grenoble, June 1975.
- [18] C. Sadarangani. Electrical machines - design and analysis of induction and permanent magnet motors. KTH Hogskoletryckeriet, 2000.
- [19] A. Stening. On Inter-bar Currents in Induction Motors with Cast Aluminium and Cast Copper Rotors. Licentiate thesis, Royal Institute of Technology (KTH), Stockholm, Sweden, June 2010.
- [20] A. C. Smith, S. Williamson, and C. Y. Poh. Distribution of inter-bar currents in cage induction machines. In Proc. of International Conference on Power Electronics Machines and Drives, volume 1, pages 297–302, March 2004.
- [21] S. Williamson and A. C. Smith. Equivalent circuits for cage induction motors with inter-bar currents. Proc. of IEE Electric Power Applications, 149(3):173–183, May 2002.
- [22] O. Aglén. Calorimetric Measurements of Losses in Induction Motors. Licentiate thesis, Royal Institute of Technology, Stockholm, Sweden, 1995.
- [23] D.G. Dorrell, T.J.E. Miller, and C.B. Rasmussen. Inter-bar currents in induction machines. IEEE Trans. on Industry Applications, 39(3):677 – 684, may-june 2003.
- [24] K. J. Bradley, Wenping Cao, and J. Arellano-Padilla. Evaluation of stray load loss in induction motors with a comparison of input-output and calorimetric methods. IEEE Trans. on Energy Conversion, 21(3):682–689, Sept. 2006.
- [25] Wenping Cao, K. J. Bradley, and A. Ferrah. Development of a high-precision calorimeter for measuring power loss in electrical machines. IEEE Trans. on Instrumentation and Measurement, 58(3):570–577, March 2009.
- [26] Wenping Cao. Comparison of IEEE 112 and new IEC standard 60034-2-1. IEEE Trans. on Energy Conversion, 24(3):802–808, Sept. 2009.
- [27] Rotating Electrical Machines – Part 2-1: Standard Methods for Determining Losses and Efficiency From Tests (Excluding Machines for Traction Vehicles), IEC 60034-2-1: 2007 (BS EN 60034-2-1).
- [28] D. Liang, X. Yang, J. Yu, and V. Zhou. Experience in china on the die-casting of copper rotors for induction motors. In Proc. of International Conference on Electrical Machines, Sep. 2012.
- [29] B. Heller and V. Hamata. Harmonic Field Effects in Induction Machines. Elsevier Science Ltd, 1977.
- [30] Ola Aglén. Calorimetric measurements of losses in air-cooled and water-cooled asynchronous motors. In Proc. of International Conference on Electrical Machines, volume 3, pages 256–262, 1996.
- [31] R. Chitroju. Improved Performance Characteristics of Induction Machines with Non-Skewed Asymmetrical Rotor Slots. Licentiate thesis, Royal Institute of Technology, Stockholm, Sweden, 2009.
- [32] C.I. McClay and S. Williamson. The variation of cage motor losses with skew. IEEE Trans. on Industry Applications, 36(6):1563 – 1570, nov/dec 2000.
9. Copyright:
- This material is a paper by "Alexander Stening". Based on "Analysis and Reduction of Parasitic Effects in Induction Motors With Die-Cast Rotors".
- Source of the paper: [DOI URL] (Note: DOI/URL not provided in the source document; typically found in university thesis repositories)
This material is summarized based on the above paper, and unauthorized use for commercial purposes is prohibited.
Copyright © 2025 CASTMAN. All rights reserved.