This article introduces the paper 'Aluminum and Aluminum Alloys' published by 'ASM International'.
1. Overview:
- Title: Aluminum and Aluminum Alloys
- Author: J.R. Davis
- Publication Year: 2001
- Publishing Journal/Academic Society: ASM International®
- Keywords: (Not explicitly provided in the text, but can be inferred from content) Aluminum, Aluminum Alloys, Alloying, Properties, Applications, Casting, Wrought Alloys, Corrosion, Heat Treatment, Welding, Brazing, Soldering, Machining, Forming, Grain Refiners, Phase Formation
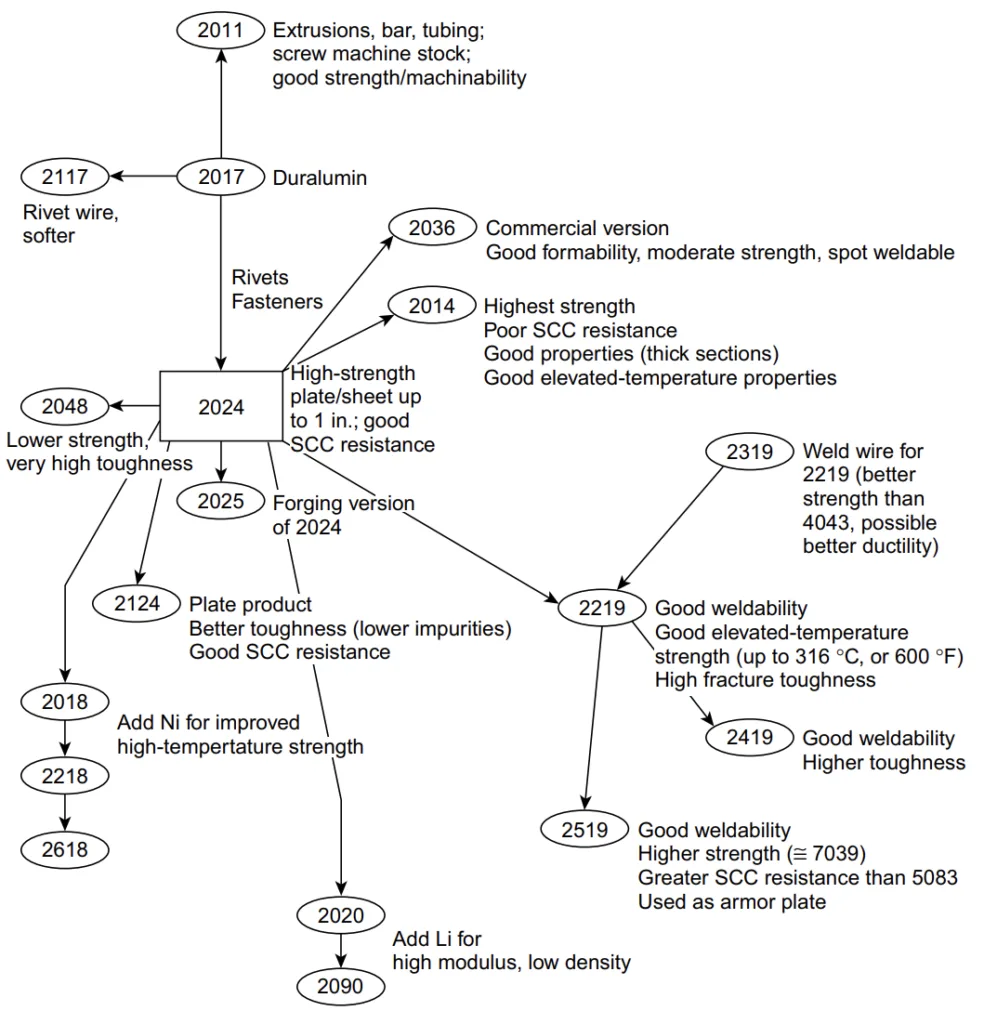
2. Abstracts or Introduction
The article "Aluminum and Aluminum Alloys" provides an introduction and overview of aluminum and its alloys, highlighting their general characteristics and versatile applications. Aluminum and its alloys are presented as highly versatile, economical, and attractive metallic materials suitable for a wide range of uses, from ductile wrapping foil to demanding engineering applications, second only to steels as structural metals. Key attributes include low density (2.7 g/cm³), approximately one-third that of steel, enabling lightweight yet strong structures advantageous for vehicles across various domains (space, air, land, and water). Furthermore, aluminum exhibits resistance to progressive oxidization due to the formation of a thin, inert aluminum oxide film that self-reseals if scratched, unlike iron rust. Appropriately alloyed and treated aluminum demonstrates corrosion resistance against water, salt, environmental factors, and various chemical and physical agents. The article further examines the corrosion characteristics of aluminum alloys in detail within the section “Effects of Alloying on Corrosion Behavior”.
3. Research Background:
Background of the Research Topic:
Aluminum and its alloys are critical engineering materials due to their unique combination of properties. Their low density and high strength-to-weight ratio, coupled with excellent corrosion resistance and versatile workability, make them indispensable in numerous industries. This article addresses the fundamental characteristics of aluminum alloys, providing a foundational understanding for engineers and experts in materials science and related fields.
Status of Existing Research:
The understanding of aluminum metallurgy is well-established, with extensive research into alloying principles, processing techniques, and property optimization. The Aluminum Association system for alloy designation is widely recognized and used, indicating a standardized body of knowledge. Existing literature, such as the "Metals Handbook Desk Edition," provides comprehensive data on chemical compositions and international designations, demonstrating a mature field of study.
Necessity of the Research:
Despite the mature status of aluminum alloy technology, a comprehensive handbook-level overview remains crucial. This is essential for disseminating fundamental knowledge, guiding material selection, and optimizing manufacturing processes in various engineering applications. The article serves as a consolidated resource, integrating key aspects of aluminum alloy metallurgy into a single, accessible document for experts and practitioners in the field.
4. Research Purpose and Research Questions:
Research Purpose:
The primary purpose of this article is to provide a handbook-level overview of aluminum and aluminum alloys, detailing their properties, classifications, processing characteristics, and applications. It aims to consolidate essential information for experts in die casting technology and related engineering disciplines, offering a readily accessible resource on this critical material system.
Key Research:
This article synthesizes existing knowledge and established research findings on aluminum alloys. It systematically categorizes and describes various alloy systems, wrought and cast alloys, and the influence of alloying elements on material properties and processing behaviors. Key research areas covered include:
- Classification of aluminum alloys based on alloying elements and strengthening mechanisms.
- Detailed examination of wrought and cast alloy series (1xxx to 8xxx).
- Effects of alloying elements on mechanical properties, corrosion resistance, and processing characteristics (forming, machining, welding, brazing, soldering).
- Discussion of grain refiners and modification of hypoeutectic Al-Si alloys.
- Analysis of phase formation in aluminum alloys and its impact on material behavior.
Research Hypotheses:
As a handbook-level overview, this article does not present novel research hypotheses. Instead, it operates on established principles of materials science and metallurgy to explain and categorize the behavior of aluminum alloys. The underlying premise is that the properties and processing characteristics of aluminum alloys are fundamentally determined by their composition, microstructure, and processing history, which are systematically explored and explained throughout the article.
5. Research Methodology
Research Design:
This article employs a descriptive and expository research design, characteristic of a handbook chapter. It systematically presents information on aluminum alloys based on established metallurgical principles and industry standards. The design is structured to provide a comprehensive overview, categorizing alloys and properties for clarity and ease of understanding.
Data Collection Method:
The article synthesizes data and information from existing literature, handbooks, and established knowledge in the field of aluminum metallurgy. Data is presented in the form of tables (Tables 1-11), figures (Figures 1-36), and descriptive text, all directly derived from established sources and prior research.
Analysis Method:
The analysis method is primarily qualitative and descriptive, focusing on explaining the relationships between alloy composition, microstructure, processing, and properties. The article uses phase diagrams (Figure 5, Figure 7), graphical representations of strength and elongation (Figures 8, 9, 10, 11, 12, 13, 14, 15, 16, 17, 18, 19, 20, 21, 22, 23, 26, 28, 33, 34, 35, 36), and microstructural images (Figures 24, 25, 29, 31, 32) to illustrate key concepts and trends. The analysis involves categorizing alloys, explaining property variations based on alloying elements and processing, and summarizing established knowledge in a structured format.
Research Subjects and Scope:
The subject of this article is aluminum and its alloys, encompassing both wrought and cast compositions. The scope is broad, covering alloy classifications, strengthening mechanisms, processing techniques (forming, machining, joining), corrosion behavior, and wear resistance. The article focuses on commercially significant aluminum alloys and their applications across various industries.
6. Main Research Results:
Key Research Results:
The article systematically presents a wealth of information regarding aluminum alloys, with key results summarized as follows:
- Alloy Classification: Aluminum alloys are categorized into wrought and cast alloys, further divided into families based on principal alloying elements (1xxx to 8xxx series for wrought alloys, 1xx.x to 9xx.x series for cast alloys).
- Wrought Alloy Classes: Detailed descriptions of each wrought alloy series (1xxx-9xxx) are provided, outlining their characteristic alloying elements, properties, and typical applications. For example, 2xxx series alloys (Al-Cu) are highlighted for high strength in aircraft applications, while 6xxx series alloys (Al-Mg-Si) are noted for good extrudability and weldability.
- Cast Alloy Classes: Descriptions of cast alloy series (1xx.x-9xx.x) are presented, emphasizing the 3xx.x series (Al-Si-based) as the most common for shaped castings, and 2xx.x series (Al-Cu) for high-strength casting applications.
- Alloying Element Effects: The article details the effects of various alloying elements (Copper, Magnesium, Silicon, Zinc, Manganese, etc.) and impurities (Iron, Silicon) on the properties of aluminum alloys, including strength, corrosion resistance, workability, and weldability. Figures 1, 2, 3, and 4 visually represent relationships among commonly used alloys within 2xxx, 5xxx, 6xxx, and 7xxx series respectively.
- Processing Characteristics: Comprehensive overviews are provided for forming, machining, welding, brazing, and soldering of aluminum alloys, highlighting the influence of alloy composition and processing parameters on each technique.
- Grain Refinement and Modification: The article discusses grain refiners (Titanium, Boron) and modifiers (Sodium, Strontium, Antimony, Phosphorus) used to control microstructure and enhance properties in aluminum alloys, particularly in Al-Si systems. Figures 22, 23, 24, 25, 26, 28 illustrate the effectiveness of grain refiners and modifiers.
- Corrosion and Wear Behavior: Detailed sections address the corrosion behavior of different aluminum alloy series and the effects of alloying elements on corrosion resistance. The article also examines wear resistance in aluminum-silicon alloys, emphasizing the role of silicon phase.
Analysis of presented data:
The presented data, including tables and figures, consistently supports the descriptive explanations throughout the article. Strength ranges for various wrought and cast alloys (Tables 2 and 3) quantify the property variations across different alloy systems. Composition ranges for common wrought and cast alloys (Tables 4 and 5) provide practical guidance for alloy selection. Figures illustrating alloy relationships (Figures 1-4) and the effects of alloying elements (Figures 7-21, 30) visually reinforce the textual descriptions of alloy behavior and property trends. Microstructural images (Figures 24, 25, 29, 31, 32) provide visual evidence of the impact of grain refinement and modification techniques.
Figure Name List:
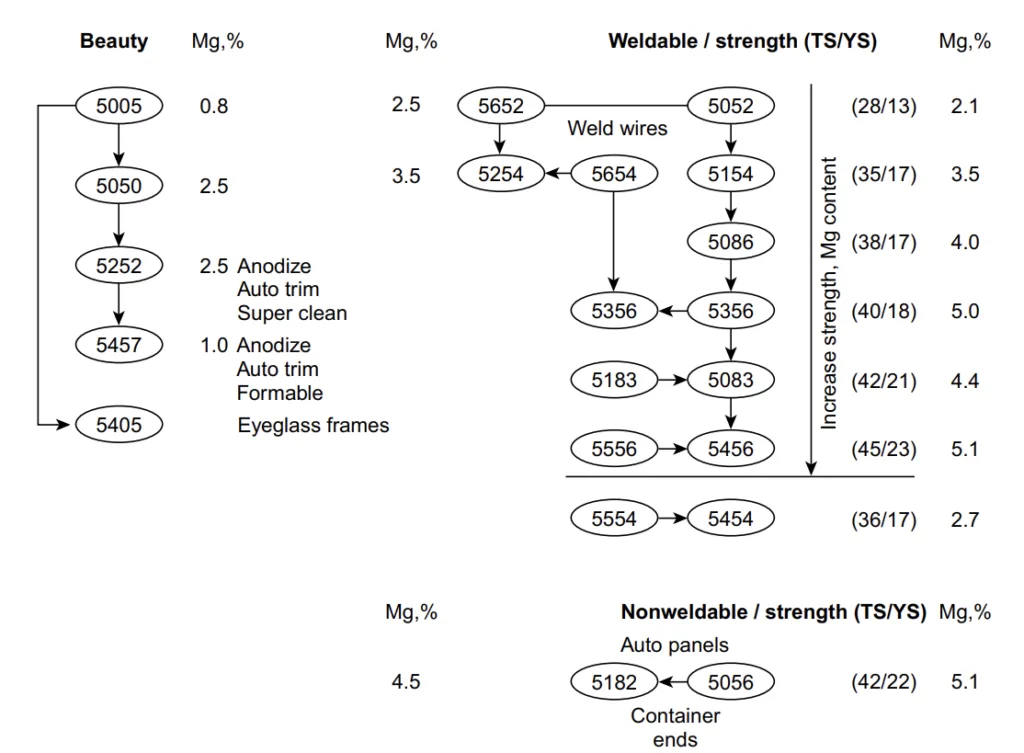
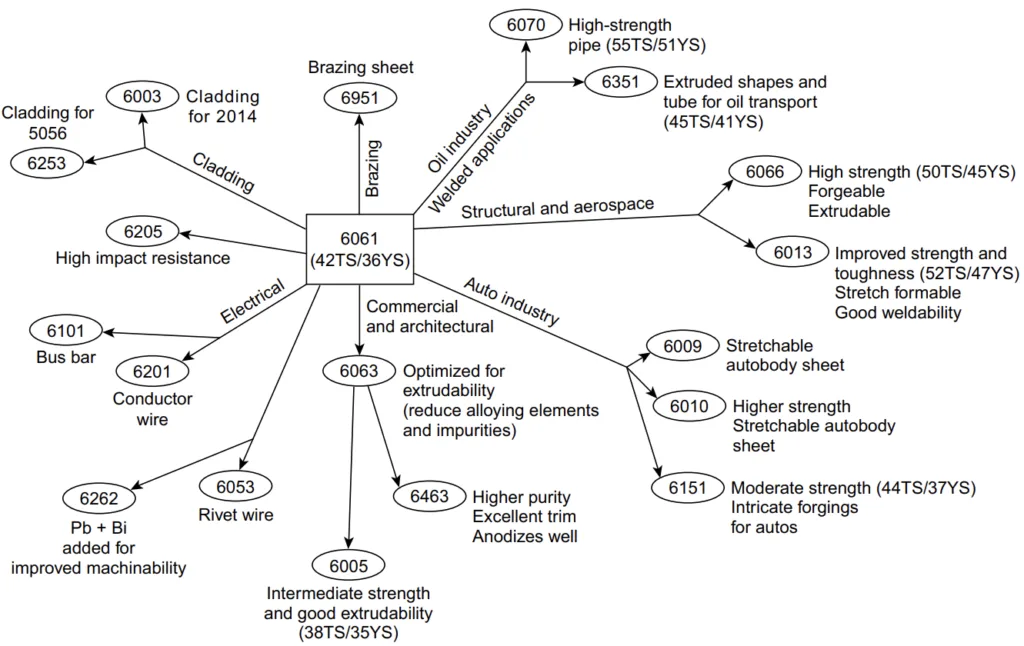
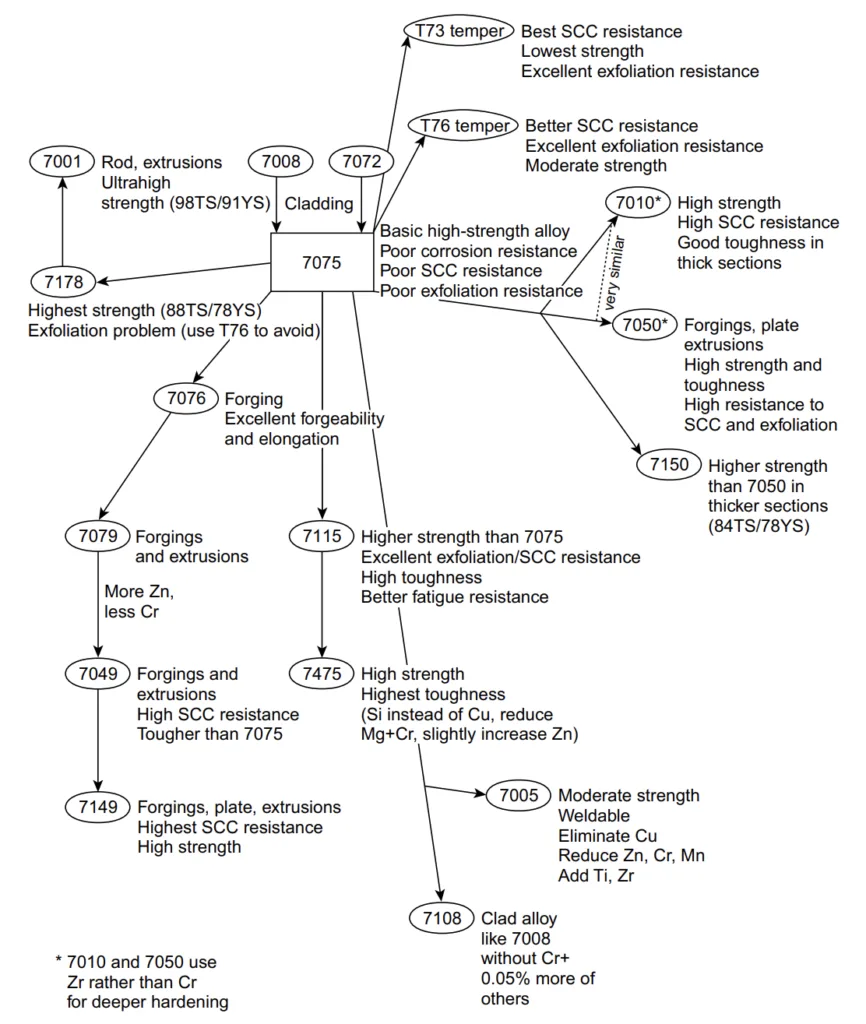
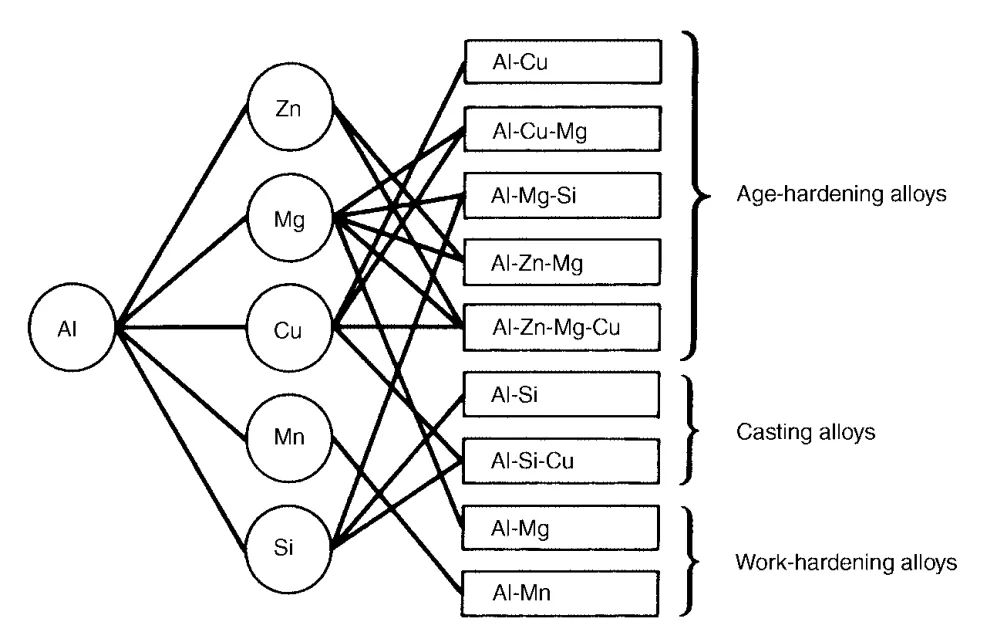
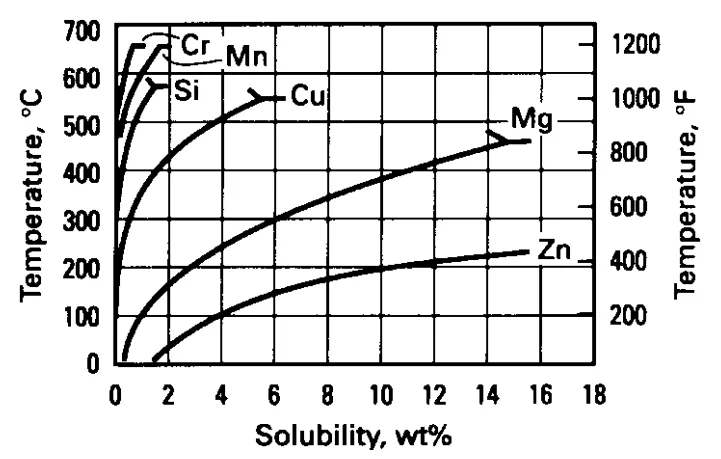
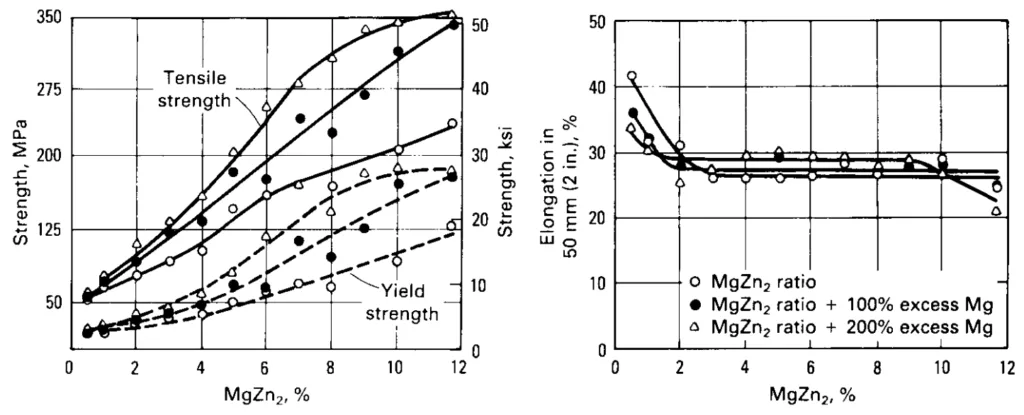
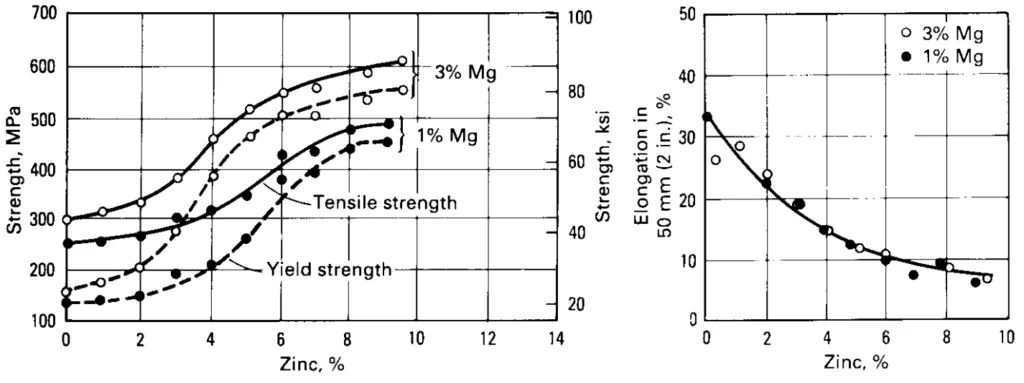
- Fig. 1 Relationships among commonly used alloys in the 2xxx series (Al-Cu)
- Fig. 2 Relationships among commonly used alloys in the 5xxx series (Al-Mg). Tensile strength (TS) and yield strength (YS) are in ksi units.
- Fig. 3 Relationships among commonly used alloys in the 6xxx series (Al-Mg-Si). Tensile strength (TS) and yield strength (YS) are in ksi units
- Fig. 4 Relationships among commonly used alloys in the 7xxx series (Al-Zn-Cu-Mg-Cr). Tensile strength (TS) and yield strength (YS) are in ksi units
- Fig. 5 Aluminum-silicon phase diagram and cast microstructures of pure components and of alloys of various compositions. Alloys with less than 12% Si are referred to as hypoeutectic, those with close to 12% Si as eutectic, and those with over 12% Si as hypereutectic
- Fig. 6 The principal aluminum alloys
- Fig. 7 Equilibrium binary solid solubility as a function of temperature for alloying elements most frequently added to aluminum
- Fig. 8 Correlation between tensile yield, strength elongation, and magnesium content for some commercial aluminum alloys
- Fig. 9 Tensile properties in Al-Mg-Mn alloys in the form of annealed (O temper) plate 13 mm (0.5 in.) thick
- Fig. 10 Tensile properties of high-purity, wrought aluminum-copper alloys. Sheet specimen was 13 mm (0.5 in.) wide and 1.59 mm (0.0625 in.) thick. O, annealed; W, tested immediately after water quenching from a solution heat treatment; T4, as in W, but aged at room temperature; T6, as in T4, followed by precipitation treatment at elevated temperature
- Fig. 11 Effect of cold work and Mg addition on alloy 2419. (a) The effect of cold work on the yield strength response to aging at 149 °C (300 °F) for the alloy with 0.18 at.% Mg. (b) The effect of cold work on the yield strength response to aging at 149 °C (300 °F) for the alloy without Mg.
- Fig. 12 The effect of cold work on yield strength of aluminum-copper alloy 2419 in naturally aged materials
- Fig. 13 Relationship between tensile properties and manganese content of Al-4%Cu-0.5%Mg alloy, heat treated at 525 °C (980 °F)
- Fig. 14 Variation of tensile properties with copper content in Al-0.3%Mn-0.2%Zr-0.1%V alloy in the T6 temper
- Fig. 15 Ultimate tensile strength versus hydrogen porosity for sand-cast bars of three aluminum alloys
- Fig. 16 Influence of gas content on the tensile and yield strengths of aluminum alloy 356
- Fig. 17 Effect of iron plus silicon impurities on tensile strength and yield strength of aluminum
- Fig. 18 Tensile properties of 13 mm (0.5 in.) aluminum-magnesium-manganese plate in H321 temper
- Fig. 19 Effect of manganese on tensile properties of wrought 99.95% Al, 1.6 mm (0.064 in.) thick specimens, quenched in cold water from 565 °C (1050 °F)
- Fig. 20 Effect of MgZn, and MgZn, with excess magnesium on tensile properties of wrought 95% Al; 1.59 mm (0.0625 in.) specimens, quenched in cold water from 470 °C (875 °F)
- Fig. 21 Effect of zinc on aluminum alloy containing 1.5% Cu and 1 and 3% Mg; 1.6 mm (0.064 in.) thick sheet. Alloy with 1% Mg heat treated at 495°C (920 °F); that with 3% Mg heat treated at 460 °C (860 °F). All specimens quenched in cold water, aged 12 h at 135 °C (275 °F)
- Fig. 22 Comparison of the effectiveness of various master alloy grain refiners in aluminum alloy 356
- Fig. 23 Effectiveness of titanium-boron grain refiners in aluminum alloys 356 and 319
- Fig. 24 As-cast Al-7Si ingots showing the effects of grain refinement. (a) No grain refiner. (b) Grain-refined. Both etched using Poulton's etch; both 2x
- Fig. 25 Varying degrees of aluminum-silicon eutectic modification ranging from unmodified (A) to well modified (F). See Fig. 26 for the effectiveness of various modifiers
- Fig. 26 Effectiveness of sodium and strontium modifiers as a function of time. See Fig. 25 for degrees of modification
- Fig. 27 Hydrogen content as a function of holding temperature for aluminum alloy 356 melts with various modifiers.
- Fig. 28 Mechanical properties of as-cast A356 alloy tensile specimens as a function of modification and grain size
- Fig. 29 Effect of phosphorus refinement on the microstructure of Al-22Si-1Ni-1Cu alloy. (a) Unrefined. (b) Phosphorus-refined. (c) Refined and fluxed. All 100x
- Fig. 30 Effects of principal alloying elements on electrolytic solution potential of aluminum. Potentials are for high-purity binary alloys solution heat treated and quenched. Measured in a solution of 53 g/L NaCl plus 3 g/L H2O2 maintained at 25 °C (77 °F)
- Fig. 31 Typical microstructure of type A357.0 hypoeutectic alloy
- Fig. 32 Microstructure of type A390.0 hypereutectic alloy. (a) Unrefined (Graff-Sargent etch). Dark regions contain coarse primary silicon particles in addition to eutectic silica. (b) Refined (as polished). 120x
- Fig. 33 Effect of volume percent fraction of micronsize intermetallic particles and composition of the matrix on the fracture strain of 5 mm (0.2 in.) diam tensile specimens. A is initial cross-sectional area. A is area of fracture
- Fig. 34 Effect of magnesium and manganese on the formability of aluminum alloys in the annealed and H34 tempers; 1.6 mm (0.064 in.) thick sheet
- Fig. 35 Effect of precipitation on yield strength and elongation in alloy 2036
- Fig. 36 Effect of temperature on relative forgeability of various aluminum alloys. Vertical scale is based on deformation per unit of energy absorbed estimated from production experience.
7. Conclusion:
Summary of Key Findings:
This handbook chapter comprehensively outlines the diverse world of aluminum and aluminum alloys. Key findings emphasize the versatility of aluminum due to its unique properties, which are further tailored through alloying. The classification systems for wrought and cast alloys provide a structured approach to understanding the vast array of available materials. Alloying elements like copper, magnesium, silicon, and zinc are crucial in determining the mechanical properties, corrosion resistance, and processing characteristics of aluminum alloys. Processing techniques such as heat treatment, forming, machining, and joining are significantly influenced by alloy composition, requiring careful consideration for optimal application. Grain refinement and modification techniques are essential for controlling microstructure and enhancing performance, particularly in casting processes.
Academic Significance of the Study:
This article serves as a valuable academic resource by consolidating a wide range of information on aluminum alloy metallurgy into a single, accessible handbook chapter. It provides a structured and systematic overview of alloy classifications, property-composition relationships, and processing considerations. This comprehensive synthesis is academically significant for students, researchers, and experts in materials science, metallurgy, and engineering, offering a foundational understanding of aluminum alloy technology.
Practical Implications:
The practical implications of this article are substantial for engineers and practitioners working with aluminum alloys. It provides essential guidance for material selection based on application requirements, processing method optimization, and performance prediction. The detailed descriptions of alloy classes, property variations, and processing characteristics enable informed decision-making in design, manufacturing, and quality control. The information on corrosion and wear behavior is particularly relevant for ensuring long-term performance and reliability in diverse environments and applications.
Limitations of the Study and Areas for Future Research:
As a handbook chapter, this article provides a broad overview and does not delve into highly specialized or cutting-edge research areas. The depth of coverage for each specific alloy system and processing technique is necessarily limited by the scope of a single article. Future research could expand upon specific aspects, such as:
- In-depth investigations into the latest advancements in aluminum-lithium alloys and other emerging alloy systems.
- Detailed studies on the effects of novel processing techniques on microstructure and properties.
- Further research into the long-term corrosion behavior of advanced aluminum alloys in specific service environments.
- Exploration of computational modeling and simulation tools for alloy design and process optimization.
- Continued development of sustainable and cost-effective aluminum alloy solutions for various industries.
8. References:
- Corrosion of Aluminum and Aluminum Alloys, J.R. Davis, Ed., ASM International, 1999
- ASM Specialty Handbook: Aluminum and Aluminum Alloys, J.R. Davis, Ed., ASM International, 1993
- Aluminum and Aluminum Alloys, in Metals Handbook Desk Edition, 2nd ed., J.R. Davis, Ed., ASM International, 1998, p 417–505
- D.G. Altenpohl, Aluminum: Technology, Applications, and Environment, 6th ed., The Aluminum Association Inc. and TMS, 1998
- Aluminum: Properties and Physical Metallurgy, J.E. Hatch, Ed., American Society for Metals, 1984
9. Copyright:
- This material is "J.R. Davis"'s paper: Based on "Aluminum and Aluminum Alloys".
- Paper Source: DOI:10.1361/autb2001p351
This material was summarized based on the above paper, and unauthorized use for commercial purposes is prohibited.
Copyright © 2025 CASTMAN. All rights reserved.