This article introduces the paper "Advanced Thermal Management for High-Power ICs: Optimizing Heatsink and Airflow Design" presented at the Applied Sciences (MDPI)
1. Overview:
- Title: Advanced Thermal Management for High-Power ICs: Optimizing Heatsink and Airflow Design
- Authors: Ali Jebelli, Nafiseh Lotfi, Mohammad Saeid Zare, and Mustapha C. E. Yagoub
- Publication Year: 2024
- Publishing Journal/Academic Society: Applied Sciences (MDPI)
- Keywords: power amplifier (PA); Gallium Nitride (GaN); integrated circuit (IC); heatsink; computational fluid dynamics (CFD); thermal management
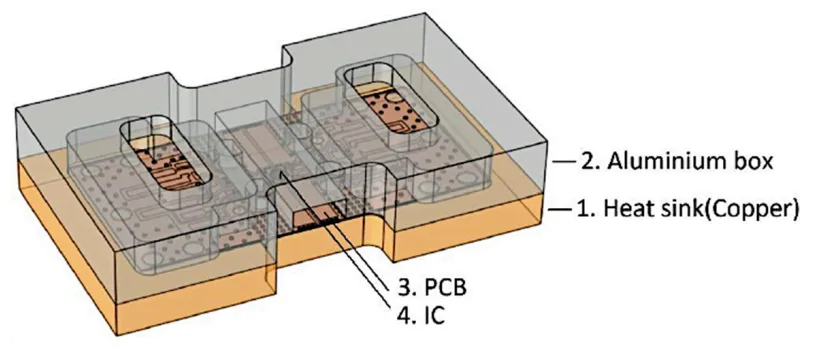
2. Research Background:
- Social/Academic Context of the Research Topic:
In the rapidly evolving landscape of 5G technology, efficient thermal management for high-power-density integrated circuits (ICs) has become paramount. Industries such as telecommunications and data centers are increasingly demanding superior cooling solutions. Computational Fluid Dynamics (CFD) has emerged as an indispensable tool for simulating and optimizing heat dissipation in these critical electronic components. - Limitations of Existing Research:
Prior research efforts have explored broad thermal management strategies. However, these studies often lack specific focus on the nuanced optimization of heatsink geometry and airflow configurations tailored for ICs. Existing approaches may not fully address the unique challenges associated with heat dissipation at the component level through refined geometric and airflow adjustments. - Necessity of the Research:
To meet the escalating thermal management demands of high-power ICs, particularly within advanced 5G systems, there is a critical need for innovative and practical solutions. Optimizing heatsink and airflow designs offers a pathway to streamline the cooling process, potentially reducing reliance on complex and expensive cooling equipment. This research aims to establish new benchmarks in thermal management, fostering the development of more efficient and reliable electronic systems.
3. Research Purpose and Research Questions:
- Research Purpose:
The primary research purpose is to introduce and validate an innovative approach to thermal management for high-power ICs. This approach centers on optimizing heatsink and fan configurations through systematic experimentation, aiming to surpass the limitations of traditional cooling methodologies. - Key Research Questions:
- What is the impact of varying fin shapes, heatsink dimensions, and fan speeds on the thermal performance of high-power ICs?
- How can heatsink geometry and airflow be optimized to minimize IC temperatures and maximize heat dissipation efficiency?
- What are the critical factors in heatsink and fan design that contribute to measurable improvements in efficiency and scalability for high-power 5G systems?
- Research Hypotheses:
The central hypothesis is that by strategically optimizing fan velocity and heatsink geometry, significant reductions in IC operating temperatures can be achieved. This optimization is hypothesized to lead to enhanced heat dissipation efficiency, offering a practical and scalable alternative to more complex and costly thermal management solutions, such as liquid cooling.
4. Research Methodology
- Research Design:
This research employed a systematic experimental design centered around Computational Fluid Dynamics (CFD) simulations, complemented by physical prototype validation. The study systematically varied heatsink configurations and fan speeds to evaluate their impact on thermal performance. - Data Collection Method:
CFD simulations were conducted using ANSYS Fluent, employing a structured mesh and the V2-f turbulence model to accurately simulate airflow patterns. Fan speeds were systematically adjusted from 0.5 m/s to 8.38 m/s. Experimental validation was performed using a constructed prototype to empirically verify simulation results. - Analysis Method:
Quantitative analysis of temperature distributions and heat dissipation efficiency was performed across various configurations. Statistical analyses were conducted to determine the significance of design modifications. Time-varying temperature comparisons were utilized to assess the dynamic interplay between fan speed, geometry, and cooling performance. Mesh independence studies were performed to ensure the reliability of CFD results. - Research Subjects and Scope:
The research focused on thermal management solutions for high-power integrated circuits (ICs), specifically Gallium Nitride (GaN) ICs. The scope of the study was limited to the optimization of heatsink geometry, including fin design and heatsink dimensions, and airflow management through fan speed adjustments within an air-cooled system. The geometry consisted of a set of circuit boards and holder compartments, including copper heatsink, aluminum frame, electronic board (PCB), and Gallium Nitride IC.
5. Main Research Results:
- Key Research Results:
The research findings underscore the critical role of fan velocity in effectively reducing IC temperatures. "The results demonstrate that fan velocity is the most critical factor in reducing IC temperatures, as increased airflow dramatically lowers thermal output." Expanding the heatsink surface area and utilizing a larger copper heatsink were also shown to enhance heat dissipation. "Expanding the heatsink surface area further improves heat dissipation by enhancing airflow interaction, while a larger copper heatsink boosts thermal conduction, effectively reducing the final IC temperature." The optimized configurations streamlined cooling, minimizing the need for complex equipment. - Statistical/Qualitative Analysis Results:
Increasing the heatsink surface area by 20% led to a notable 15% reduction in the maximum operating temperature of the IC. Furthermore, the optimal configuration achieved a "30% improvement in heat dissipation compared to that in traditional setups." - Data Interpretation:
The results indicate that relatively simple modifications to heatsink geometry and fan speed are highly effective in achieving significant thermal management improvements. These optimizations provide a practical alternative to complex and expensive cooling solutions, such as liquid cooling, for high-power ICs. - Figure Name List:
- Figure 1. First and main geometry.
- Figure 2. System prototype (a) top view and (b) bottom view.
- Figure 3. IC location: the IC (in blue) is located at the center of the circuit board.
- Figure 4. The surfaces around the designed box exchange heat with the surrounding environment through radiation.
- Figure 5. First geometry: (a) temperature contour and; (b) isothermal levels in Kelvin.
- Figure 6. Second geometry (finned box): gray represents the aluminum part and orange represents the copper part of the box.
- Figure 7. Second geometry: (a) isothermal levels and; (b) temperature contour of second geometry in Celsius.
- Figure 8. Use of a cooling box to optimize fan airflow.
- Figure 9. Third geometry: boundary conditions.
- Figure 10. Velocity contour on the center-plane sections, which are xy and yz planes.
- Figure 11. Velocity field (black) and inlet direction (blue).
- Figure 12. Surface temperature: Tmax = 286 °C and Tmin = 276.4 °C.
- Figure 13. Needle conical heatsink cooling fin.
- Figure 14. Classification of heatsink box levels based on border air velocity.
- Figure 15. Temperature contour of the needle conical heatsink cooling fin.
- Figure 16. Fifth geometry.
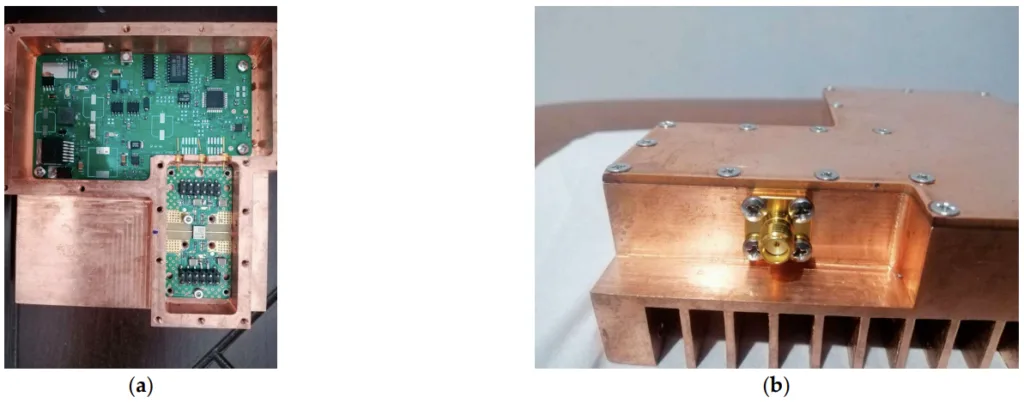

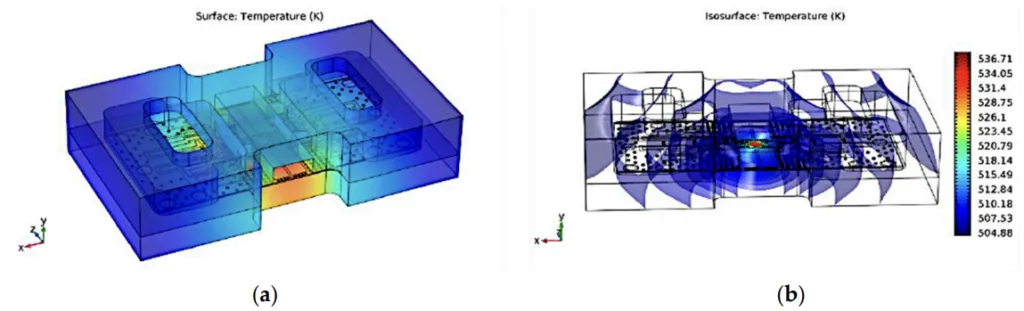
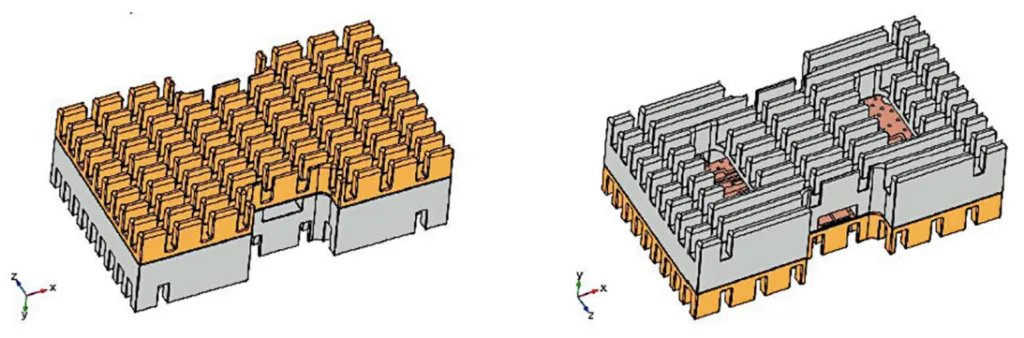
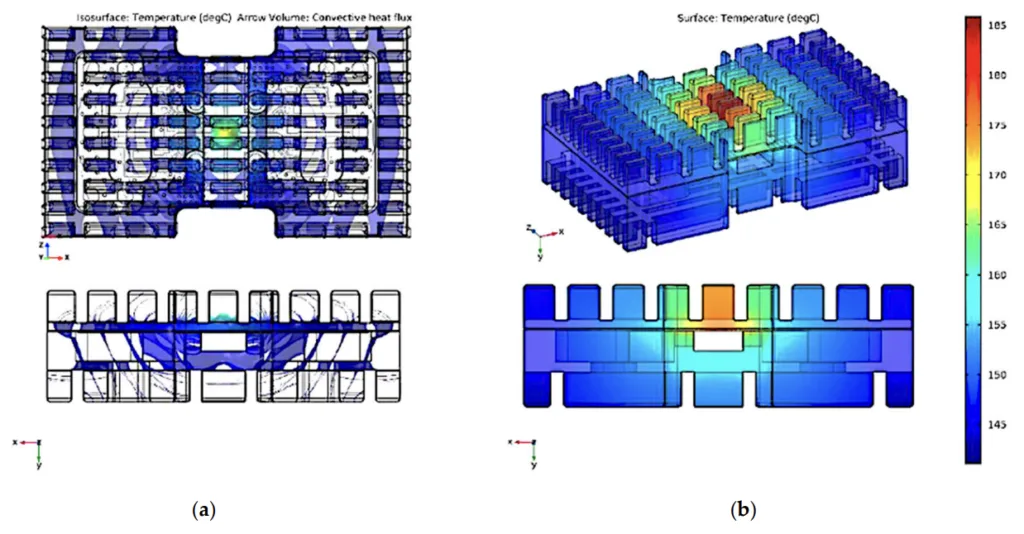
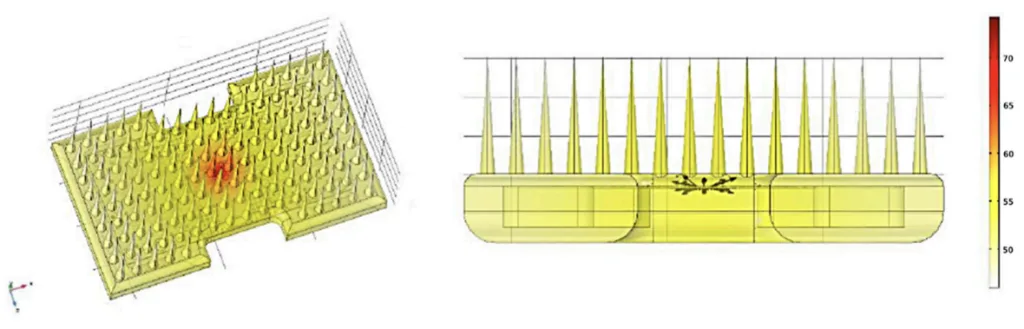
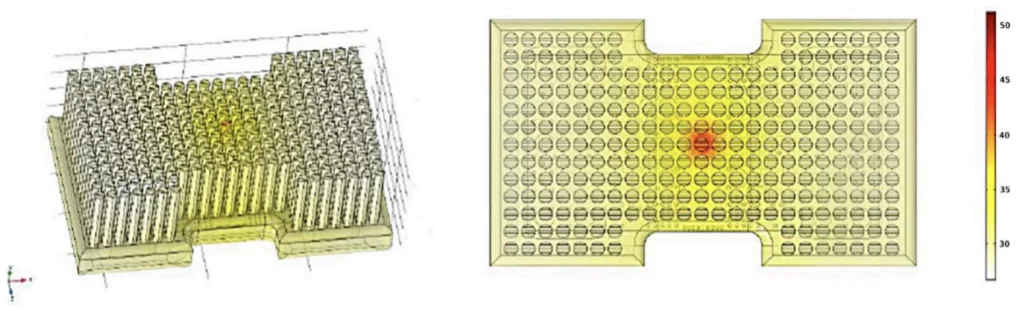
6. Conclusion and Discussion:
- Summary of Main Results:
This research conclusively demonstrates that optimizing heatsink and airflow configurations is a highly effective strategy for enhancing IC cooling performance. Fine-tuning fan speed and heatsink geometry leads to substantial reductions in operating temperatures, thereby significantly improving the reliability and longevity of high-power integrated circuits. - Academic Significance of the Research:
This study introduces a novel perspective by specifically focusing on heatsink and airflow optimization for ICs, contrasting with prior research that often addresses broader thermal management strategies. The approach, validated through both CFD simulations and experimental testing, provides a robust and scalable methodology for optimizing thermal performance. The research "sets a new benchmark in thermal management, fostering the development of more efficient and reliable electronic systems". - Practical Implications:
The findings offer practical and scalable solutions to the thermal challenges confronting next-generation electronics, particularly in the context of 5G technology and other high-power systems. By demonstrating that cost-effective and efficient solutions can be achieved through innovative optimization of basic cooling components like heatsinks and fans, this research provides valuable guidance for industry standards and contributes to more reliable, efficient, and sustainable electronic systems. - Limitations of the Research:
The study acknowledges limitations related to convergence issues encountered with complex geometries in CFD simulations. Additionally, software limitations restricted the testing of higher input flows, which could further explore the performance boundaries of the optimized cooling solutions. "Although it would have been preferable to analyze the geometry with dedicated air inlet and outlet channels, the boundary conditions were modeled accurately based on the real-world problem, despite the convergence issues caused by complex geometries."
7. Future Follow-up Research:
- Directions for Follow-up Research:
Future research should explore finned geometries with higher flow rates to further optimize heat transfer. Addressing heat convection issues and investigating more complex heatsink designs and airflow management systems are recommended. Analyzing geometries with dedicated air inlet and outlet channels could also provide deeper insights. - Areas Requiring Further Exploration:
Further investigation into advanced heatsink materials, novel fin designs, and dynamic fan speed control mechanisms could yield additional improvements in thermal management efficiency. Exploring the integration of these optimized air-cooling strategies with other cooling technologies in hybrid systems presents another promising avenue for future research.
8. References:
- [1] Qian, C.; Gheitaghy, A.M.; Fan, J.; Tang, H.; Sun, B.; Ye, H.; Zhang, G. Thermal Management on IGBT Power Electronic Devices and Modules. IEEE Access 2018, 6, 12868–12884.
- [2] Abdel-Motaleb, I.M. An Overview of Design, Fabrication, and Cooling Techniques of 3D-ICs. In Proceedings of the 2021 IEEE 14th International Conference on ASIC (ASICON), Kunming, China, 26–29 October 2021.
- [3] Chu, R.C.; Simons, R.E.; Ellsworth, M.J.; Schmidt, R.R.; Cozzolino, V. Review of Cooling Technologies for Computer Products. IEEE Trans. Device Mater. Reliab. 2004, 4, 568–585.
- [4] Murshed, S.M.S.; de Castro, C.A.N. A critical review of traditional and emerging techniques and fluids for electronics cooling. Renew. Sustain. Energy Rev. 2017, 78, 821–833.
- [5] Timoshenkov, V.; Khlybov, A.; Rodionov, D.; Panteleev, A. Thermal Phenomena Research in RF GaN Dies. In Proceedings of the 2020 IEEE Conference of Russian Young Researchers in Electrical and Electronic Engineering (EIConRus), St. Petersburg/Moscow, Russia, 27–30 January 2020.
- [6] Patil, N.G.; Hotta, T.K. A combined numerical simulation and optimization model for the cooling of IC chips under forced convection. Int. J. Mod. Phys. C 2020, 31, 2050081.
- [7] Joo, Y.; Yeh, H.-C.T.; Dieu, K.; Kim, C. Air cooling of a microelectronic chip with diverging metal microchannels monolithically processed using a single mask. J. Micromechanics Microengineering 2008, 18, 115022.
- [8] Liu, Y.; Yang, Y. Numerical Simulation on the Water-cooled Heat Sink for High-power Semiconductor. In Proceedings of the 2012 International Conference on Computer Application and System Modeling (ICCASM 2012), Taiyuan, China, 27–29 July 2012.
- [9] van Erp, R.; Kampitsis, G.; Nela, L.; Soleimanzadeh, R.; Matioli, E. Embedded Microchannel Cooling for High Power-Density GaN-on-Si Power Integrated Circuits. In Proceedings of the 2020 19th IEEE Intersociety Conference on Thermal and Thermomechanical Phenomena in Electronic Systems (ITherm), Orlando, FL, USA, 21–23 July 2020.
- [10] Islam, S.; Motaleb, I.A. Investigation of the Dynamics of Liquid Cooling of 3D ICs. In Proceedings of the 2019 8th International Symposium on Next Generation Electronics (ISNE), Zhengzhou, China, 9–10 October 2019.
- [11] Islam, S.; Abdel-Motaleb, I. Numerical Analysis of Liquid Cooling of 3D-ICs Using Embedded Channels. In Proceedings of the 2020 IEEE International Conference on Electro Information Technology (EIT), Chicago, IL, USA, 31 July–1 August 2020.
- [12] Jebelli, A.; Lotfi, N.; Partovibakhsh, M.; Mahabadi, A.; Zare, M.S.; Yagoub, M.C.E. Innovative Microwave System for Safe and Efficient Coalbed Methane Extraction: Design, Implementation, and Field Applications. Am. J. Min. Metall. 2024, 7, 1–9.
- [13] Soleimanzadeh, R.; Khadar, R.A.; Naamoun, M.; van Erp, R.; Matioli, E. Near-junction heat spreaders for hot spot thermal management of high power density electronic devices. J. Appl. Phys. 2019, 126, 165113.
- [14] Zhang, G.; Pomeroy, J.W.; Navarro, M.E.; Cao, H.; Kuball, M.; Ding, Y. 3-D Printed Microjet Impingement Cooling for Thermal Management of Ultrahigh-Power GaN Transistors. IEEE Trans. Compon. Packag. Manuf. Technol. 2021, 11, 748–754.
- [15] Jebelli, A.; Mahabadi, A.; Ahmad, R. Numerical Simulation and Optimization of Microwave Heating Effect on Coal Seam Permeability Enhancement. Technologies 2022, 10, 70.
- [16] Jebelli, A.; Mahabadi, A.; Zare, M.S.; Ahmad, R. Numerical simulations of lateral input effect in an open channel to reduce disturbances in the mainstream channel using CFD. Water-Energy Nexus 2022, 5, 39–49.
- [17] Jebelli, A.; Mahabadi, A.; Nayak, A.; Ahmad, R. Increasing the operating depth of a Teflon underwater vehicle using a magnetic field. Ocean. Eng. 2022, 250, 111078.
- [18] Mebarek-Oudina, F.; Bessaïh, R. Numerical simulation of natural convection heat transfer of copper-water nanofluid in a vertical cylindrical annulus with heat sources. Thermophys. Aeromech. 2019, 26, 325–334.
- [19] Sharifi, M.; Akbari, M. Experimental investigation of the effect of process parameters on cutting region temperature and cutting edge quality in laser cutting of AL6061T6 alloy. Optik 2019, 184, 457–463.
- [20] Chamkha, A.J.; Dogonchi, A.S.; Ganji, D.D. Magneto-hydrodynamic flow and heat transfer of a hybrid nanofluid in a rotating system among two surfaces in the presence of thermal radiation and Joule heating. AIP Adv. 2019, 9, 025103.
- [21] Feng, S.; Shi, M.; Yan, H.; Sun, S.; Li, F.; Lu, T.J. Natural convection in a cross-fin heat sink. Appl. Therm. Eng. 2018, 132, 30–37.
- [22] Ding, B.; Zhang, Z.-H.; Gong, L.; Xu, M.-H.; Huang, Z.-Q. A novel thermal management scheme for 3D-IC chips with multi-cores and high power density. Appl. Therm. Eng. 2020, 168, 114832.
- [23] Arshad, W.; Ali, H.M. Experimental investigation of heat transfer and pressure drop in a straight minichannel heat sink using TiO2 nanofluid. Int. J. Heat Mass Transf. 2017, 110, 248–256.
- [24] Mandalapu, C.; Abdel-Motaleb, I.; Hong, S.; Patti, R. Design, Fabrication, and Testing of a Liquid Cooling Platform for High Power 3D-ICs. In Proceedings of the 2019 8th International Symposium on Next Generation Electronics (ISNE), Zhengzhou, China, 9–10 October 2019.
9. Copyright:
- This material is "Ali Jebelli et al."'s paper: Based on "Advanced Thermal Management for High-Power ICs: Optimizing Heatsink and Airflow Design".
- Paper Source: https://doi.org/10.3390/app14209406
This material was summarized based on the above paper, and unauthorized use for commercial purposes is prohibited.
Copyright © 2025 CASTMAN. All rights reserved.