This article introduces the paper [Added Value of Process Modelling in Development of Automotive Die Casting Parts] presented at the [Japan Die Casting Congress]
1. Overview:
- Title: Added Value of Process Modelling in Development of Automotive Die Casting Parts
- Authors: Andre Le-Nezet, Nicolas De Reviere, Loic Calba, Badarinath Kalkunte
- Publication Year: 2018
- Publishing Journal/Academic Society: Japan Die Casting Congress
- Keywords: Die Casting, HPDC, part design, die design, casting development loop, digital tuning, die cycling, simulation, Porosity, Workflow, Macros, Automatization, Renault, ESI

2. Research Background:
The automotive industry increasingly demands high-performance castings with superior mechanical properties and structural integrity. While Gravity and Low Pressure Die Casting are traditionally used for such applications, High Pressure Die Casting (HPDC) offers advantages in mass production due to reduced shot times and cost-effectiveness. However, HPDC's inherent process limitations make it challenging to consistently meet these elevated performance demands. Innovations and technological advancements are continuously being developed to enhance HPDC's capabilities and maintain its competitiveness.
Historically, the utilization of process simulation software in die casting development was limited. Graphical User Interfaces (GUI) were not user-friendly or process-oriented, hindering wider adoption. Consequently, simulations were primarily employed for problem-solving after issues arose (curative actions) rather than proactively preventing them during the design phase.
The evolution of computer hardware, coupled with advancements in user-friendly and foundry-focused GUI design, and the increasing complexity of product designs and materials for lightweight castings, has elevated the importance of process simulation. Embedding simulation early in the product development cycle is now crucial for reducing lead times, optimizing costs, and ensuring the production of high-quality castings.
3. Research Purpose and Research Questions:
This research aims to demonstrate the added value of process modeling in the development of automotive die casting parts. Specifically, it investigates the application of state-of-the-art simulation methodology, exemplified by Renault's approach, to achieve digital tuning of both part and die designs.
The key research question addressed is: How can modern simulation methodology enhance the development process of automotive die casting parts, moving from physical trial and error to a more predictive and efficient digital approach?
The underlying hypothesis is that process modeling, when integrated into the early stages of design, enables casting engineers to predict defects, optimize process parameters, and ultimately improve both the design and the final quality of HPDC components.
4. Research Methodology:
This paper presents a case study based on a 2011 AlSi9Cu3 Gearbox Housing developed by Renault. The research employs a four-step digital study methodology using ESI ProCAST 2018.0 software. This methodology is structured as follows:
- Step 1: Manufacturability Check (Bare Casting): This initial step assesses the part's manufacturability by simulating the filling process with a simplified die representation. The goal is to quickly identify potential issues like air entrapment and hot spots early in the product design phase.
- Step 2: Injection System Design (Biscuit/Runner/Ingate/Overflows): This step focuses on designing and validating the injection system, including runners, ingates, and overflows. Simulation at this stage evaluates the filling pattern and potential risks of air entrapment and shrinkage related to the injection system design.
- Step 3: Die Design (without cooling lines): Here, the complete die shape is designed, excluding the cooling system initially. Thermal cycling simulations are performed to understand the die temperature distribution and identify hot spots that will require cooling.
- Step 4: Die Design & Process Validation (Full Die Design): In the final step, the cooling system is incorporated into the die design. Comprehensive simulations are conducted to validate the complete die design and process parameters, including thermal cycling, filling, and solidification, to predict part quality.
Data Collection Method: The research relies on simulation data generated by ESI ProCAST 2018.0 at each step of the methodology.
Analysis Method: The analysis is primarily qualitative, focusing on the interpretation of simulation results visualized through plots of filling time, shrinkage porosity, and temperature distribution. The effectiveness of each design iteration is evaluated based on these simulation outputs. A visual comparison between simulated shrinkage porosity and real part cut sections is also presented to validate the simulation results.
Research Subjects and Scope: The study focuses on the development process of automotive HPDC parts within Renault Process Engineering, using a specific gearbox housing as a case study. The scope is limited to the application of the described four-step digital simulation methodology using ESI ProCAST.
5. Main Research Results:
The four-step simulation methodology yielded valuable insights at each stage of the die casting part development process.
- Step 1: Manufacturability Check (Bare Casting): Simulation of cavity filling time (Fig 1a) identified the last regions to fill, suggesting appropriate locations for overflows to facilitate air removal. Shrinkage porosity analysis (Fig 1b) highlighted significant hot spots in the casting, indicating potential porosity risks. "Fig 1a, shows the last regions to fill." "Fig 1b, highlights massive hot spots in the casting, which may lead to porosity."
- Step 2: Injection System Design (Biscuit/Runner/Ingate/Overflows): Progressive filling simulation (Fig 2a) validated the positioning of initial overflows. Filling time analysis (Fig 2b left) confirmed the effectiveness of overflow locations. Shrinkage porosity prediction (Fig 2b right) showed similar risk areas as Step 1, with some additional porosity regions potentially arising from the altered thermal gradients and filling profile due to the inclusion of the biscuit and runner in the simulation. "The progressive filling in Fig 2a confirms good positioning of the initial overflows…" "Shrinkage Porosity plot in Fig 2b (right) shows mostly similar risks than what was observed in Step 1."
- Step 3: Die Design (without cooling lines): Thermal die cycling simulation (Fig 3a) provided temperature profiles at the hottest mold/casting interface, indicating die temperature stabilization over cycles. Hot spot analysis (Fig 3b) revealed hot spot locations in both mobile and fixed dies, as well as the positions of existing cooling circuits from the 2011 die design. "Fig 3a shows a temperature profile through the shots taken on the hottest mold/casting interface." "Fig 3b shows the hot spots in the both the mobile & fixed dies…"
- Step 4: Die Design & Process Validation (Full Die Design): Thermal cycling simulation with cooling circuits (Fig 4b left) demonstrated that die thermal steady state is achieved similarly to simulations without cooling. However, internal die cooling resulted in a significant temperature decrease of approximately 70°C at the die skin in hot spot areas. Progressive filling simulation (Fig 4c) showed smooth sleeve filling with minimal turbulence. Air entrapment analysis (Fig 4d) indicated potential air entrapment locations near core pins and overflows. Part fill time plot (Fig 4e left) showed consistent filling behavior across simulation steps.
- Comparison with Reality: Comparison of simulated shrinkage porosity with real part cut sections (Fig 5b) for three critical zones (bosses) showed good agreement, validating the predictive capability of the simulation methodology. "Fig 5b summarizes the shrinkage porosity comparison vs reality for all thee bosses at different steps of simulation loop and confirms good alignment with reality."
Figure Name List:
- Fig1a: Cavity Filling Time
- Fig1b: Shrinkage Porosity plot highlighting the main hot spots in the casting
- Fig2a: Progressive filling in the cavity
- Fig2b: Filling time plot (left), confirming the overflow locations to have filled the last and Shrinkage Porosity (right) highlighting the hot spots in the casting
- Fig 3a: Die temperature profile taken at hottest mold/casting interface
- Fig 3b: Die temperature profile of Mobile Die (Top) and Fixed Die (Bottom) at the end of 8 cycles (shots). Light blue circles and bars indicate the cooling circuits of the 2011 die
- Fig 4a: Die cooling circuits
- Fig 4b (left): Die temperature profile taken at hottest mold/casting interface, (right): cross section of the die showing the influence water coolants just before the mold is opened
- Fig 4c: Progressive filling starting from the sleeve filling and plunger movement in the sleeve to cavity filling
- Fig 4d: Air Entrainment
- Fig 4e: Filling time plot (left), and Shrinkage Porosity (right)
- Fig 5a: Shows the 3 main zones (boss) which are mandatory for this part to be considered porosity free
- Fig 5b: Shows the shrinkage porosity comparison of simulation vs real cut sections for all the 3 main zones
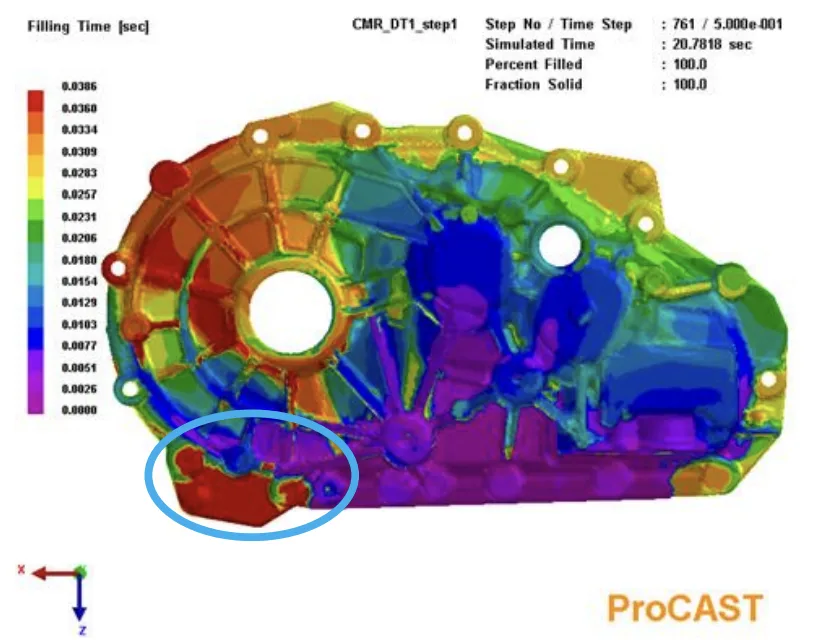
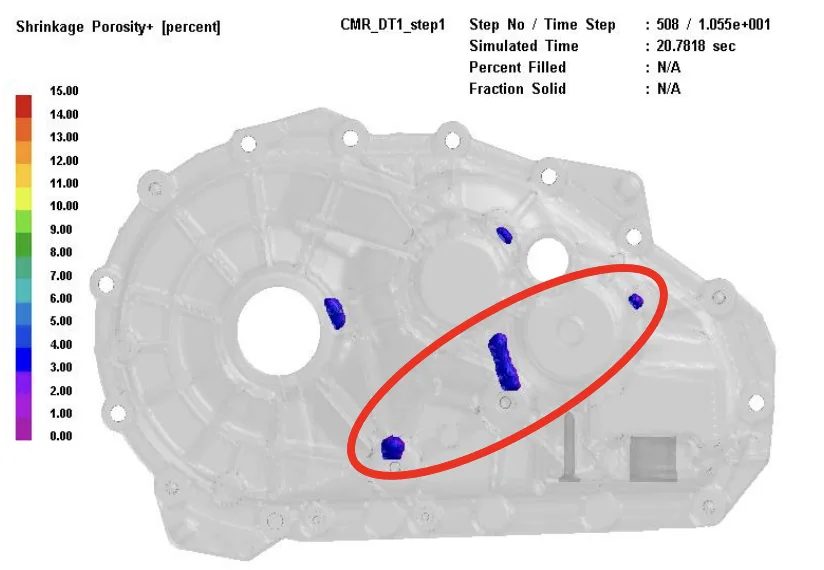
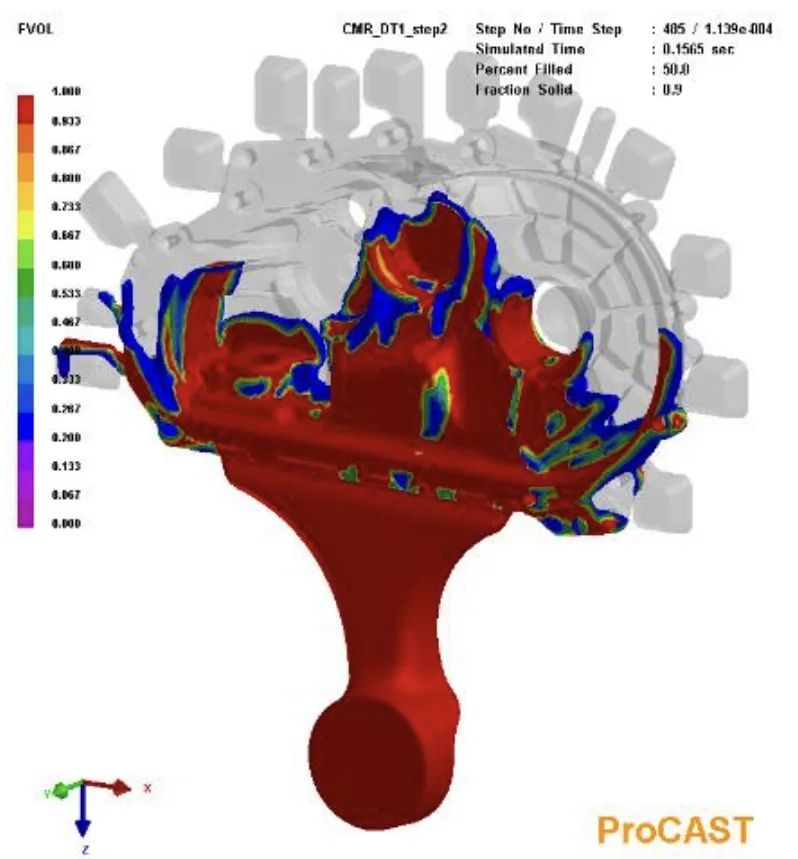
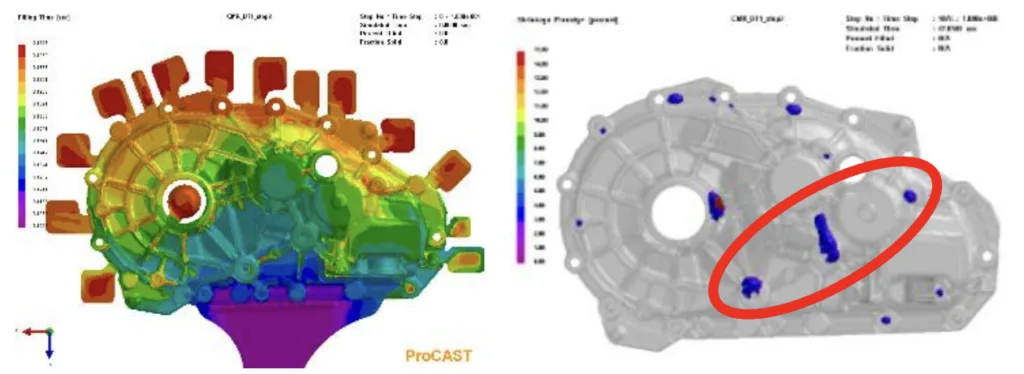
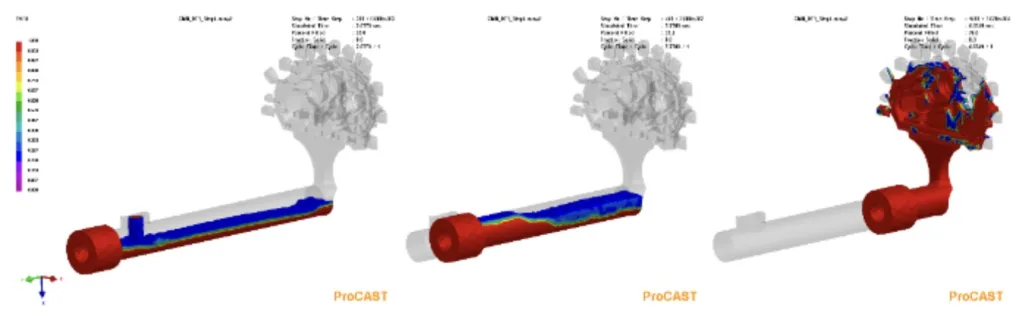
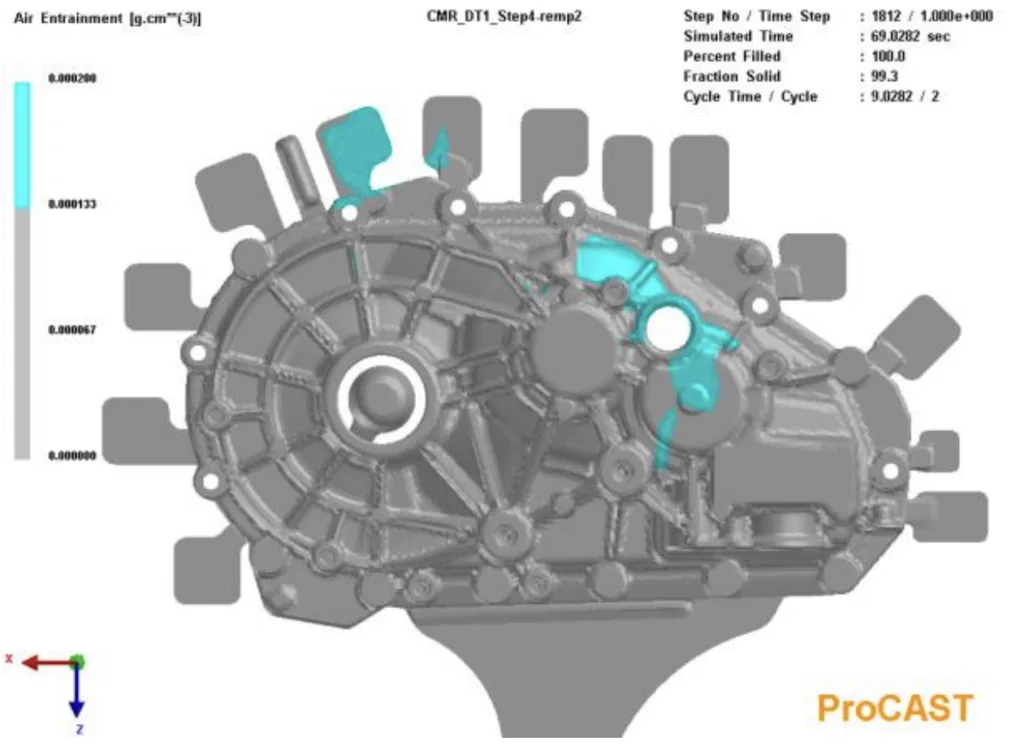
6. Conclusion and Discussion:
Summary of Main Results: This paper successfully demonstrates the added value of process modeling in automotive HPDC part development through a structured four-step simulation methodology using ESI ProCAST. Each step, from manufacturability checks to full die design validation, provides critical insights for optimizing part and die design. The simulation results show good correlation with real-world observations, highlighting the accuracy and predictive power of the approach.
Academic Significance of the Research: The research underscores the academic significance of integrating process simulation into the early stages of die casting development. It validates the effectiveness of digital tuning methodologies in reducing reliance on physical trial and error, paving the way for more efficient and robust design processes.
Practical Implications: The presented four-step methodology offers a practical and valuable framework for die casting engineers in the automotive industry. By adopting this approach, manufacturers can:
- Improve Part Quality: Proactively identify and mitigate potential defects like porosity and air entrapment.
- Reduce Development Time: Shorten development cycles by replacing physical iterations with virtual simulations.
- Optimize Costs: Minimize costly die rework and production delays through upfront simulation-based design optimization.
The emphasis on early manufacturability checks (Step 1) and the strategic design of cooling systems (Step 3 & 4) are particularly highlighted as crucial for achieving high-quality HPDC components.
Limitations of the Research: This study is based on a single case study (a gearbox housing), which may limit the generalizability of the findings. The methodology is also specific to Renault's processes and the use of ESI ProCAST software. Further research across diverse part geometries and with different simulation tools would be beneficial.
7. Future Follow-up Research:
The paper identifies several directions for future research:
- Managing Process Variations: Investigating the impact of manufacturing process variations, such as alloy temperature fluctuations, on part quality and developing robust designs that are less sensitive to these variations.
- Optimization Tools: Exploring the use of optimization tools like ESI PAM-OPT, integrated within ProCAST, to systematically define and optimize manufacturing parameters for improved process control and part quality.
- Industry 4.0 Integration: Continuing to advance the integration of simulation and optimization tools to facilitate the transition of die casting processes towards Industry 4.0 standards, enabling more automated and data-driven manufacturing.
Further exploration is needed in robust design methodologies, the seamless integration of simulation with optimization algorithms, and the broader implementation of Industry 4.0 principles within the die casting sector.
8. References:
- [1] Ch. Pequet, M. Gremaud, and M. Rappaz, "Modelling of microporosity, macroporosity, and pipe-phrinkage formation during the solidification of alloys using a mushy-zone refinement method: applications to aluminium alloys", Met. Mater. Trans., 33A (2002) 2095.
- [2] Imad Khan, M & Frayman, Yakov & Nahavandi, Saeid. (2012). Modelling of porosity defects in high pressure die casting with a neural network.
- [3] G. Couturier, and M. Rappaz, "Effect of volatile elements on porosity formation in solidifying alloys", Mod. Sim. Mater. Sc. Engng., (2005)
- [4] Wang, LH & Nguyen, T & Savage, G & Davidson, C. (2003). Thermal and flow modelling of ladling and injection in high pressure die casting process. International Journal of Cast Metals Research. 16. 409-417. 10.1179/136404603225007863.
- [5] Karban, Robert. (2000). The effects of intensification pressure, gate velocity, and intermediate shot velocity on the internal quality of aluminum die castings. ETD Collection for Purdue University.
- [6] G. Couturier, J.-L. Desbiolles, and M. Rappaz, "A Porosity Model for Multi-Gas Systems in Multi-Component Alloys", MCWASP, Edited by TMS Publ., Warrendale, USA, 2006)
- [7] Tsoukalas, Vasilios. (2003). The Effect of Die Casting Machine Parameters on Porosity of Aluminum Die Castings. International Journal of Cast Metals Research. 15. 581-588. 10.1080/13640461.2003.11819544.
- [8] S. Dargusch, Matthew & Dour, Gilles & Schauer, N & M. Dinnis, C & M. Savage, George. (2006). The influence of pressure during solidification of high pressure die cast aluminium telecommunications components. Journal of Materials Processing Technology. 180. 10.1016/j.jmatprotec.2006.05.001.
- [9] N. Obiekea, Kenneth & Y. Aku, Shekarau & S. Yawas, Danjuma. (2014). Effects of Pressure on the Mechanical Properties and Microstructure of Die Cast Aluminum A380 Alloy. Journal of Minerals and Materials Characterization and Engineering. 02. 248-258. 10.4236/jmmce.2014.23029.
- [10] G. Couturier and M. Rappaz, “Modelling of porosity formation in multicomponent alloys in the presence of several dissolved gases and volatile solute elements", Symposium on Simulation of Aluminum Shape Casting
- [11] ESI ProCAST 2018.0 User Manual 2006
9. Copyright:
- This material is Andre Le-Nezet, Nicolas De Reviere, Loic Calba, Badarinath Kalkunte's paper: Based on Added Value of Process Modelling in Development of Automotive Die Casting Parts.
- Paper Source: Japan Die Casting Congresse paper]
- Copyright © 2025 CASTMAN. All rights reserved.
This material was summarized based on the above paper, and unauthorized use for commercial purposes is prohibited.