This article introduces the paper ['A Comparative Analysis of Grain Size and Mechanical Properties of Al-Si Alloy Components Produced by Different Casting Methods'] published by ['AU J.T.'].
1. Overview:
- Title: A Comparative Analysis of Grain Size and Mechanical Properties of Al-Si Alloy Components Produced by Different Casting Methods
- Author: Abdulkabir Raji
- Publication Year: Jan. 2010
- Publishing Journal/Academic Society: AU J.T. 13(3): 158-164
- Keywords: Chill casting, microstructure, refinement, sand casting, squeeze casting.
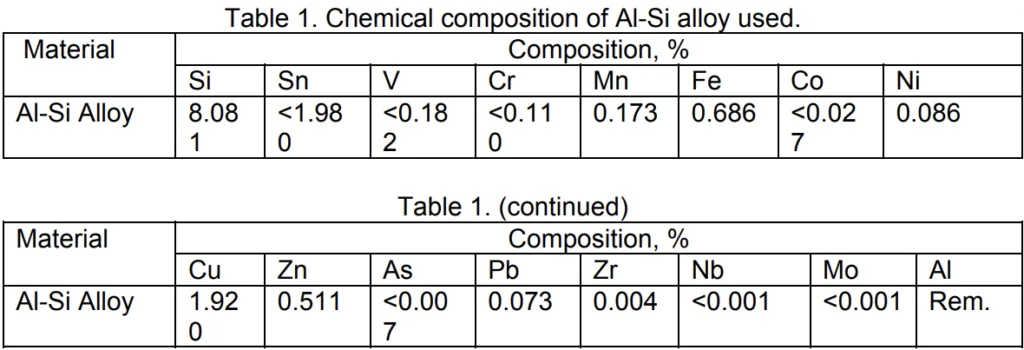
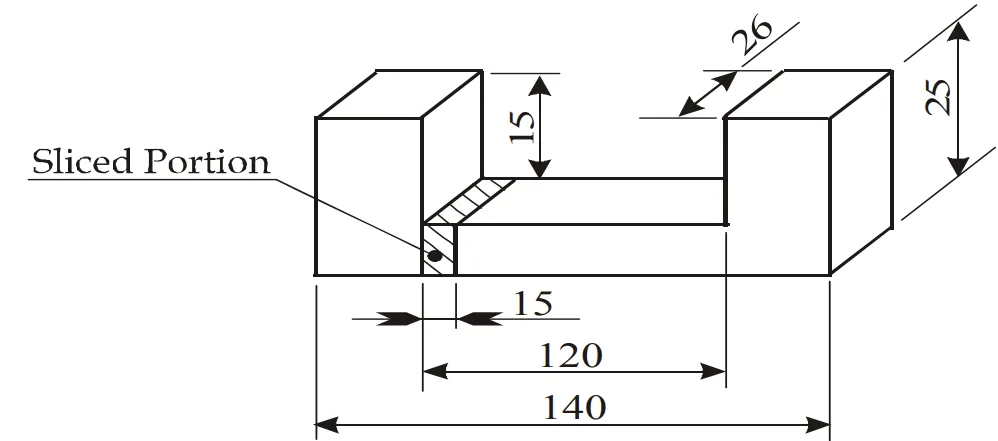
2. Abstracts or Introduction
Abstract
This study was carried out to compare cast microstructures and mechanical properties of aluminium silicon alloy components cast by various means. For this purpose, sand casting, chill casting and squeeze casting methods were used to produce similar articles of the same shape and size from an Al-8%Si alloy. It was observed that the grain size of the microstructures of the cast products increased from those of squeeze casting through chill casting to sand casting. Conversely, the mechanical properties of the cast products improved from those of sand casting through chill casting to squeeze casting. Therefore, squeeze cast products could be used in as cast condition in engineering applications requiring high quality parts while chill castings and sand castings may be used in as cast condition for non-engineering applications or engineering applications requiring less quality parts.
Introduction
Foundry or metal casting, an ancient metal shaping technique dating back to 2000 B.C., has evolved into a diverse industry. Modern casting processes are broadly categorized into sand casting and special casting, the latter encompassing die, gravity, investment, centrifugal, and pressure castings. Sand casting remains prevalent, accounting for approximately 80% of total castings. Engineering and consumer goods manufacturing utilizes various techniques, including sand casting and die casting, each characterized by distinct capabilities and costs. This study focuses on comparing squeeze casting, pressure die casting, chill casting, and sand casting for component production. Prior research has compared sand casting and squeeze casting, noting sand casting's rough surface finish but cost-effectiveness and suitability for complex geometries. Squeeze casting offers advantages like full-density parts, smoother surfaces, and tighter tolerances. It is also a cost-effective process with high production rates and metal utilization. Squeeze casting is considered a relatively new method with the ability to manipulate microstructure through process control. This research aims to compare the grain size and mechanical properties of aluminium silicon alloy components produced by sand, chill, and squeeze casting methods to further understand these processes.
3. Research Background:
Background of the Research Topic:
Metal casting, also known as foundry, is one of the earliest metal shaping methods. Originating around 2000 B.C., the fundamental principles of casting have remained consistent over millennia. Modern foundry practices have expanded into numerous casting processes, broadly classified into sand casting and special casting. Special casting methods include die casting, gravity casting, investment casting, centrifugal casting, and pressure casting, each with unique advantages and disadvantages. Sand casting is a widely used method, representing approximately 80% of total casting production.
Status of Existing Research:
Engineering and consumer goods are manufactured using various techniques, notably sand casting and die casting. Each technique possesses distinct capabilities and cost profiles, dictating specific application areas. Previous studies have compared sand casting and squeeze casting. Lynch et al. (1975) observed that while sand casting is characterized by rough surface finishes, it offers a cost-effective fabrication method suitable for complex geometries. Squeeze casting, conversely, yields full-density parts with enhanced surface finish and dimensional tolerance. Clegg (1991) and Yue and Chadwick (1996) have highlighted the maximum weight obtainable by squeeze casting for aluminium-base alloys as 19kg.
Necessity of the Research:
Despite extensive research aimed at improving casting processes, further investigation is required for a more comprehensive understanding. Specifically, a comparative study focusing on grain size and mechanical properties across different casting methods is needed. This study is designed to compare the effects of sand casting, chill casting, and squeeze casting on the microstructure and mechanical properties of aluminium silicon alloy components.
4. Research Purpose and Research Questions:
Research Purpose:
The primary research purpose is to conduct a comparative analysis of the grain size of microstructures and mechanical properties of aluminium silicon alloy components produced using sand casting, chill casting, and squeeze casting methods.
Key Research:
The key research focuses on evaluating and comparing:
- The grain size variations in Al-Si alloy microstructures resulting from sand casting, chill casting, and squeeze casting.
- The mechanical properties, specifically hardness, Ultimate Tensile Strength (UTS), proof stress, and elongation, of Al-Si alloy components produced by each of the three casting methods.
Research Hypotheses:
The study implicitly hypothesizes that:
- Squeeze casting will result in the finest grain size in the microstructure of Al-Si alloy components, followed by chill casting, and then sand casting, which will exhibit the coarsest grain size.
- Mechanical properties, including hardness, UTS, proof stress, and elongation, will be superior in squeeze cast components, followed by chill cast components, with sand cast components exhibiting the lowest mechanical properties.
5. Research Methodology
Research Design:
This research employed a comparative experimental design. Aluminium-silicon alloy components were produced using three different casting methods: sand casting, chill casting, and squeeze casting. The study then compared the resulting microstructures and mechanical properties of the cast components.
Data Collection Method:
- Material Preparation: An Al-Si alloy scrap was utilized, and its composition was verified using energy dispersive X-ray fluorescence (EDXRF) and classical wet analysis.
- Casting Process: Sand casting, chill casting, and squeeze casting were performed using specified pouring temperatures and, for squeeze casting, varying squeeze pressures (75MPa, 100MPa, 125MPa, 150MPa). The methods described by Raji and Khan (2005; 2006) were followed for controlling casting parameters.
- Metallographic Examination: Samples were prepared through sectioning, grinding, polishing, and etching with 0.24% Hydrofluoric acid (HF). Microstructures were observed and photographed using a Pol Jenalab optical microscope at x125 magnification.
- Mechanical Testing: Tensile tests were conducted using a universal testing machine, and hardness was measured using a Rockwell hardness tester, following procedures outlined by Raji and Khan (2006).
Analysis Method:
- Quantitative Grain Size Analysis: Grain sizes were quantitatively assessed using the American Society for Testing and Materials (ASTM) grain size number (n), calculated using equations based on grain counts at specific magnifications.
- Comparative Analysis of Mechanical Properties: The obtained data for hardness, UTS, proof stress, and elongation were tabulated and compared across the different casting methods and process parameters (pouring temperature, squeeze pressure). Statistical analysis was implicitly used through data presentation in tables to show trends and differences.
Research Subjects and Scope:
- Material: Aluminium-silicon (Al-Si) alloy, specifically an Al-8%Si alloy.
- Casting Methods: Sand casting, chill casting, and squeeze casting.
- Process Parameters: Pouring temperatures (650°C, 700°C, 750°C, 800°C for sand casting, 650°C, 700°C, 750°C for chill and squeeze casting), squeeze pressures (75MPa, 100MPa, 125MPa, 150MPa for squeeze casting).
- Scope: The study is limited to the comparison of these three casting methods on the specified Al-Si alloy and the evaluation of grain size and selected mechanical properties.
6. Main Research Results:
Key Research Results:
- Grain Size: Microstructural analysis revealed that grain size increased in the order of squeeze casting < chill casting < sand casting. Squeeze castings exhibited the finest grains, while sand castings showed the coarsest grains. Increasing squeeze pressure in squeeze casting led to finer grain sizes.
- Hardness: Squeeze cast components demonstrated the highest hardness values, reaching up to HRF58.0, a 43-47% increase over chill castings. Chill castings had higher hardness than sand castings. Sand castings exhibited the lowest hardness, ranging from HRF33.0 to HRF35.5.
- Ultimate Tensile Strength (UTS): Squeeze castings showed the highest UTS, ranging from 146 to 232 MPa, depending on temperature and pressure. Chill castings had a UTS of approximately 115 MPa. Sand castings had the lowest UTS, ranging from 65 to 102 MPa.
- Proof Stress: The trend in proof stress mirrored that of UTS, with squeeze castings exhibiting the highest values, followed by chill castings, and then sand castings.
- Elongation: Squeeze castings showed the highest percentage elongation (3.4-3.8%), followed by chill castings (2.4-2.7%), and sand castings (2.0-2.3%).
Analysis of presented data:
Table 2 presents the properties of Aluminium-Silicon alloy produced by various casting methods. It shows a clear trend: as the casting method changes from sand casting to chill casting and then to squeeze casting, the ASTM grain size number (n*) increases, indicating finer grain size. Conversely, UTS, Proof Stress, and Hardness values increase in the same order, demonstrating improved mechanical properties with finer grain structures achieved through squeeze casting. Elongation also follows a similar trend, albeit less pronounced.
The data indicates that for sand casting (0 MPa squeeze pressure), increasing pouring temperature from 650°C to 800°C leads to a decrease in grain refinement (lower n*) and a reduction in UTS, Proof Stress, and Hardness.
For squeeze casting, increasing squeeze pressure generally results in finer grain sizes (higher n*) and improved mechanical properties. However, the effect of pouring temperature within the tested range (650°C to 750°C) is less consistent compared to the significant impact of squeeze pressure.
Figures 2-5 visually confirm the grain size differences. Figure 2 (Sand Cast), Figure 3 (Chill Cast), Figure 4 & 5 (Squeeze Cast) show micrographs at x125 magnification. The micrographs illustrate that sand castings have coarser grains (Fig. 2), chill castings have finer grains (Fig. 3), and squeeze castings exhibit the finest grain structures (Fig. 4 & 5). The white patches represent primary alpha solid solution of silicon in aluminium (α), and the dark patches represent eutectic (α+Si).
Figure Name List:
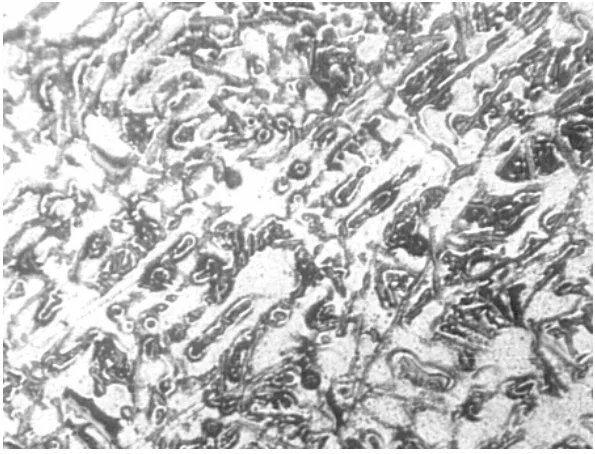
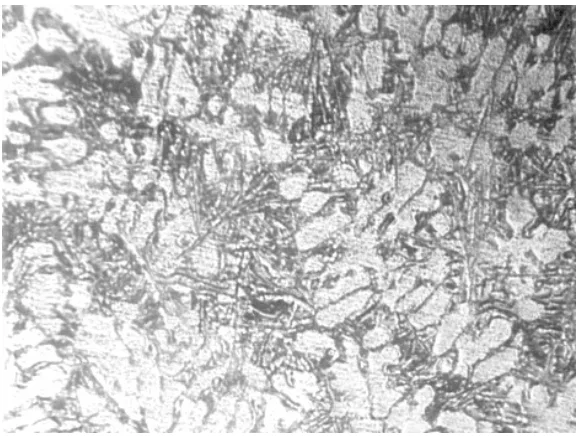
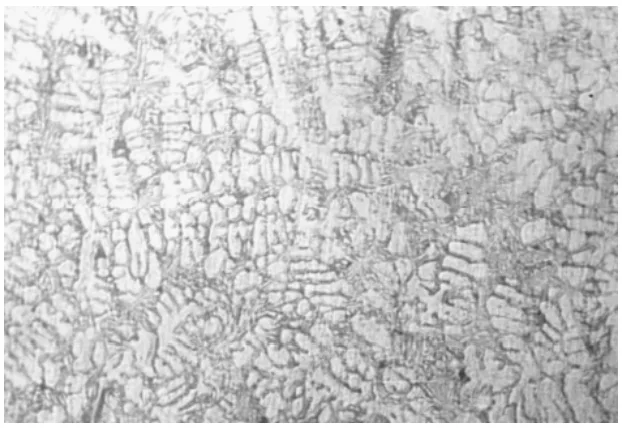
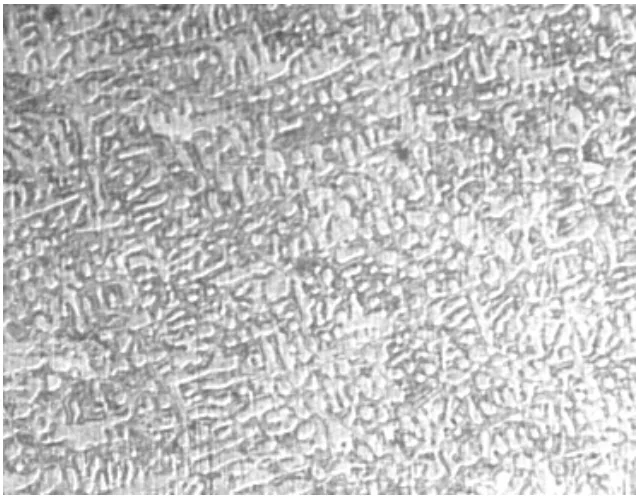
- Fig. 1. Sliced portion of castings for metallographic test; dimensions are in mm.
- Fig. 2. Micrograph of Al-8%Si Alloy Sand Cast at a Pouring Temperature of 700°C (x125); white patches are primary α while dark patches are eutectic, α + Si.
- Fig. 3. Micrograph of Al-8%Si Alloy Chill Cast at a Pouring Temperature of 650°C ( x 125); white patches are primary α while dark patches are eutectic, α + Si.
- Fig. 4. Micrograph of Al-8%Si Alloy Squeeze Cast at a Pouring Temperature of 650°C and a Squeeze Pressure of 100MPa (x 125); white patches are primary α while dark patches are eutectic, α + Si.
- Fig. 5. Micrograph of Al-8%Si Alloy Squeeze Cast at a Pouring Temperature of 750°C and a Squeeze Pressure of 125MPa (x 125); white patches are primary α while dark patches are eutectic, α + Si.
7. Conclusion:
Summary of Key Findings:
The study concluded that:
- The microstructure of Al-Si alloy castings becomes progressively finer when moving from sand casting to chill casting and finally to squeeze casting.
- Mechanical properties generally improve in the order of sand casting < chill casting < squeeze casting, with sand castings exhibiting the lowest overall mechanical properties.
- Squeeze casting significantly enhances the mechanical properties of Al-Si alloy castings compared to chill and sand casting.
- Sand castings are suitable for as-cast applications with non-engineering or low mechanical property requirements. Chill and squeeze castings can be utilized in as-cast conditions for engineering applications demanding medium to high mechanical properties, respectively.
Academic Significance of the Study:
This study contributes to the fundamental understanding of how different casting methods influence the microstructure and mechanical properties of Al-Si alloys. It provides quantitative data on the comparative performance of sand, chill, and squeeze casting, reinforcing the established knowledge that higher cooling rates associated with chill and squeeze casting lead to grain refinement and improved mechanical characteristics. The research validates the effectiveness of squeeze casting in achieving superior material properties in Al-Si alloys.
Practical Implications:
The findings offer practical guidance for engineers and manufacturers in selecting appropriate casting methods based on the desired performance characteristics of Al-Si alloy components. For applications requiring high-quality parts with superior mechanical properties, squeeze casting is the preferred method. Chill casting provides a balance of improved properties over sand casting and may be suitable for medium-performance applications. Sand casting remains a viable option for cost-sensitive applications where lower mechanical properties are acceptable.
Limitations of the Study and Areas for Future Research:
The study is limited to an Al-8%Si alloy and a specific range of casting parameters. Future research could explore:
- The effects of a wider range of alloy compositions on the comparative performance of these casting methods.
- The optimization of squeeze casting parameters (pressure, temperature, velocity) for specific Al-Si alloys to maximize mechanical properties.
- The investigation of other mechanical properties, such as fatigue strength and impact toughness, in components produced by these casting methods.
- The economic analysis of each casting method, considering production costs and achievable mechanical properties, to provide a comprehensive method selection guide.
8. References:
- Amstead, B.H.; Ostwald, P.F.; and Begeman, M.L. 1979. Manufacturing processes. 7th ed., John Wiley and Sons, New York, NY, USA.
- Askeland, D.R. 1985. The science and engineering of materials. PWS Publishing Co., Boston, MA, USA.
- Clegg, A.J. 1991. Precision casting processes. Pergamon Press PLC, Oxford, UK.
- Jain, P.L. 1992. Principles of foundry technology. 3rd ed., Tata Mc Graw-Hill Publishing Co., Ltd., New Delhi, India.
- Lynch, R.F.; Olley, R.P., and Gallagher, P.C.J. 1975. Squeeze casting of brass and bronze. Paper No.75-90. AFS Trans. 83: 561-8.
- Mikhailov, A.M. 1989. Metal casting. Mir Publishers, Moscow, USSR.
- Raji, A.; and Khan, R.H. 2005. Effect of pouring temperature on the properties of Al-8%Si alloy sand cast components. Global J. Engin. Res. 4(1&2): 1-4.
- Raji, A.; and Khan, R.H. 2006. Effects of pouring temperature and squeeze pressure on the properties of Al-8%Si alloy squeeze cast components. AU J.T. 9(4): 229-37, April.
- Rao, P.N. 1992. Manufacturing technology: Foundry, forming and welding. Tata McGraw-Hill Publishing Co., Ltd., New Delhi, India.
- Weiss, R.; and Kleinheyer, U. 1987. Current trends in the use of moulding and core making processes. Casting Plant Technol. 3(4): 10-9.
- West, C.E.; and Gruback, T.E. 1989. Permanent mold casting. In: ASM. 1989. Metals handbook (Casting). vol. 15, pp. 275-85, ASM, Metal Park, OH, USA.
- Williams, R. 1997. The present status and future of green sand in the foundry industry. The British Foundryman 72(6, Special Supplement): 53-62.
- Wright, R.T. 1990. Manufacturing systems. The Goodheart-Willcox Co., Inc., Tinley Park, IL, USA.
- Yong, M.S.; and Clegg, A.J. 2004. Process optimisation for a squeeze cast magnesium alloy. J. Materials Process. Technol. 145(1): 134-41, January.
- Yue, T.M.; and Chadwick, G.A. 1996. Squeeze casting of light alloys and their composites. J. Materials Process. Technol. 58(2-3): 302-7, March.
9. Copyright:
- This material is "Abdulkabir Raji"'s paper: Based on "A Comparative Analysis of Grain Size and Mechanical Properties of Al-Si Alloy Components Produced by Different Casting Methods".
- Paper Source: https://www.ajol.info/index.php/ajt/article/view/54637
This material was summarized based on the above paper, and unauthorized use for commercial purposes is prohibited.
Copyright © 2025 CASTMAN. All rights reserved.