This article introduces the paper"A Review on Casting Defect Minimization Through Simulation".
1. Overview:
- Title: A Review on Casting Defect Minimization Through Simulation
- Authors: Mahipalsinh G. Jadeja, Manojkumar V. Sheladiya, Mayursinh Gohil
- Publication Year: 2016
- Journal/Conference: IJSRD - International Journal for Scientific Research & Development, Vol. 3, Issue 11, 2016, ISSN (online): 2321-0613
- Keywords: Casting, Casting Defect, Shrinkage, Simulation
2. Research Background:
- Social/Academic Context of the Research Topic:
- Casting is a process that carries a risk of failure occurrence during all stages of production, necessitating actions to obtain defect-free parts.
- Casting defects are primarily related to process parameters, requiring control over these parameters to achieve zero defect parts.
- A well-designed feeding system is crucial for ensuring better casting quality, especially for new castings or those with high rejection rates, where feeding system design modification is paramount.
- Traditional manual modifications of feeding systems are time-consuming, costly, and resource-intensive.
- Casting simulation effectively overcomes these difficulties and provides a powerful tool for predicting process outcomes.
- Limitations of Existing Research:
- The paper does not explicitly state limitations of existing research. However, it implies the inefficiency of manual feeding system modification and highlights the need for simulation technology.
- Necessity of Research:
- Casting simulation can predict locations prone to defects in existing feeding systems, enabling design modifications to reduce rejection rates.
- Simulation-based design improvements offer time and cost savings compared to manual methods, enhancing efficiency.
3. Research Objectives and Research Questions:
- Research Objective:
- The objective of this paper is to identify defects in the casting process, analyze the causes of shrinkage defects, and suggest remedies to improve the quality of casting products.
- It also aims to demonstrate how simulation in SOFTCAST software can detect shrinkage defects and how applying discussed remedies can reduce rejection rates.
- Core Research Questions:
- What are the major defects occurring in the casting process, and what are their causes?
- Specifically, what are the causes of shrinkage defects, and what are effective methods to minimize them?
- How can casting simulation be utilized to predict and improve casting defects, particularly shrinkage defects?
- Research Hypothesis:
- This paper is a review paper and does not formulate a specific research hypothesis for verification. However, it implicitly suggests that improving the feeding system using simulation technology will effectively reduce casting defects, especially shrinkage defects.
4. Research Methodology:
- Research Design:
- This research is a review study that comprehensively analyzes existing literature on casting defects, particularly shrinkage defects.
- It categorizes and summarizes various types of casting defects, their causes, and remedies through literature analysis, and explores the potential of simulation technology.
- Data Collection Method:
- Literature data, including academic papers and technical materials related to casting processes and defects, were collected and analyzed.
- The review focused on studies related to the application and effectiveness analysis of casting simulation software.
- Analysis Method:
- Collected literature data were used to classify and organize casting defect types, causes, and remedies.
- The effectiveness of simulation technology in casting process application and defect prediction was analyzed, and its applicability in real casting scenarios was evaluated.
- The shrinkage defect prediction function of SOFTCAST software and the effectiveness of applying remedies were analyzed.
- Research Subject and Scope:
- This study targets various defects occurring throughout the casting process, but focuses particularly on shrinkage defects.
- The scope of the research includes analyzing the causes of casting defects, suggesting remedies, and reviewing simulation technology applications, supported by analyzing actual casting cases and simulation results.
5. Key Research Findings:
- Core Research Findings:
- Major defects identified in the casting process include Shrinkage, Blowhole, Sand Burning, Sand Inclusion, Cold Lap or Cold Shut, Misrun, Gas Porosity, Mismatch, Cracks Or Tears, and Incomplete Casting.
- Detailed Possible Causes and Remedies are presented for each defect.
- Shrinkage: Caused by density change of molten metal, inadequate feeding system design, etc. Remedies include maintaining liquid metal pressure to compensate for solidification shrinkage and proper feeding system design.
- Blowhole: Caused by inadequate core venting, excessive gas release from core, moisture absorption by cores, etc. Remedies include improving core venting, reducing gas generation, and drying/storing cores properly.
- Sand Burning: Caused by high mold temperature, low melting point of molding material, etc. Remedies include improving molding material and controlling pouring temperature.
- Cold Lap or Cold Shut: Caused by lack of fluidity in molten metal, inadequate gating system design, etc. Remedies include adjusting pouring temperature and improving gating system.
- Misrun: Defect where molten metal fails to completely fill the mold cavity, with similar causes and remedies as Cold Lap.
- Gas Porosity: Caused by trapped air, hydrogen, moisture, etc. Remedies include increasing pouring temperature, improving fluidity, controlling pouring speed, improving molding material, and ensuring adequate venting.
- Mismatch: Defect due to mold shifting, caused by misalignment of cope and drag. Remedies include checking pattern mounting, rectifying dowels, and using proper molding box and closing pins.
- Cracks Or Tears: Occur in die castings due to various causes like shrinkage, die cavity damage, uneven cooling, etc. Remedies include reducing dry strength, adding sawdust/coal dust, reducing pouring temperature, preventing superheating, using chills, providing feeders, and ensuring sufficient cooling time.
- Incomplete Casting: Caused by insufficient molten metal, operator error, etc. Remedies include ensuring sufficient molten metal, checking gating system, and improving operator training and supervision.
- Simulation using SOFTCAST software is effective in predicting shrinkage defects, and improving the feeding system based on simulation results can minimize shrinkage defects.
- Simulation analysis of an actual casting case (EP20 component) predicted shrinkage defect locations, and suggested the potential to reduce rejection rates by improving the feeding system.
- Statistical/Qualitative Analysis Results:
- This paper is a review paper, and no statistical analysis results are presented.
- Qualitative analysis results systematically organize the types, causes, and remedies of various casting defects and analyze the defect prediction and improvement effects of simulation technology.
- Data Interpretation:
- Casting simulation is an effective tool for predicting and improving casting defects, especially shrinkage defects, and can contribute to reducing rejection rates and improving quality in actual casting production.
- FEM-based simulation software like SOFTCAST provides powerful solutions for optimizing casting processes and minimizing defects.
- Figure Name List:
- Fig. 1: Actual casting EP20
- Fig. 2: Monthly rejection rate of EP 20
- Fig. 3: Solid Model of Casting EP20
- Fig. 4: Simulation Result of the Casting EP 20.
- Fig. 5: Shrinkage porosity (macro-red, micro-orange).
- Fig. 6: Framework for feeder design and optimisation
- Fig. 7: Liquid-solid interface (solid lines) and feed-paths (dotted lines) inside stepped casting.
- Fig. 8: Distribution of Lower Bainite (volume fraction) (a) ideal case; (b) the case considering the results of casting.
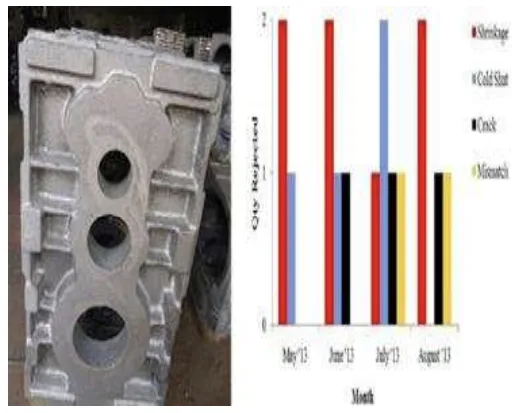
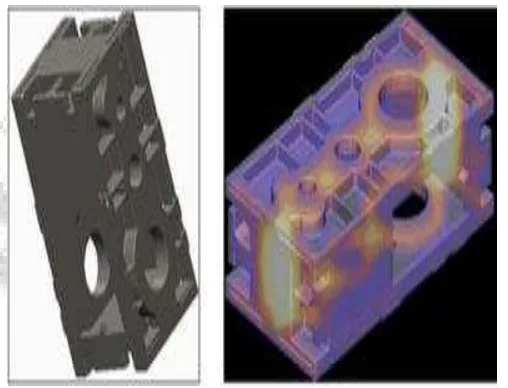
6. Conclusion and Discussion:
- Summary of Main Findings:
- This study comprehensively reviewed various defects occurring in the casting process, their causes, and remedies through literature analysis.
- Shrinkage defects are identified as a major cause of casting defects, and simulation technology-based feeding system improvement is presented as an effective way to reduce them.
- Simulation based on SOFTCAST software is confirmed to be a useful tool for predicting shrinkage defects and optimizing casting processes.
- Academic Significance of the Research:
- This research provides systematic information on casting defects, especially shrinkage defects, and presents the applicability of simulation technology in casting processes, holding academic value.
- It contributes to the development of research fields related to casting processes and defects and can be used as foundational data for future simulation-based casting process research.
- Practical Implications:
- The findings of this study can contribute to reducing rejection rates and improving productivity in casting production by utilizing simulation technology to predict casting defects and improve feeding systems in real casting scenarios.
- Simulation software like SOFTCAST is a useful tool that can provide practical assistance to casting technicians.
- Limitations of the Research:
- This research is a literature review study, focused on the analysis of a specific simulation software (SOFTCAST), which may limit the generalization to various simulation technologies and casting conditions.
- Validation studies through actual casting experiments are lacking, and further research is needed using various casting conditions and simulation software.
7. Future Follow-up Research:
- Directions for Future Research:
- Further research is needed to verify the prediction accuracy and improvement effects of shrinkage defects in various simulation software and casting conditions.
- Validation of simulation prediction results through actual casting experiments and development of simulation-based feeding system design optimization methodologies are needed.
- Expansion of simulation prediction and improvement research for casting defects other than shrinkage defects is needed.
- Areas Requiring Further Exploration:
- Research on developing AI and ML technology-based casting defect prediction and automatic improvement systems.
- Research on analyzing the correlation between casting process variables and defect occurrence and developing data-based defect prediction models.
- Research on utilizing 3D printing technology for casting mold production and simulation linkage.
8. References:
- [1] Harshil Bhatta, Rakesh Barota, Kamlesh Bhatta, Hardik Beravalaa, Jay Shah "Design Optimization of Feeding System and Solidification Simulation for Cast Iron" 2nd International Conference on Innovations in Automation and Mechatronics Engineering, ICIAME 2014 Elsevier volume 14 (2014) 357 – 364
- [2] C. M. Choudhari, B. E. Narkhede, S. K. Mahajan "Methoding and Simulation of LM 6 Sand Casting for Defect Minimization with its Experimental Validation" 12th Global Congress On Manufacturing And Management, GCMM 2014 Elsevier volume 97 (2014) 1145-1154
- [3] Dr. B Ravi, Durgesh Joshi "Feedability Analysis and Optimisation Driven by Casting Simulation” Technical paper submitted to the Indian Foundry Journal Indian Foundry Journal April 2007
- [4] Mayur Sutaria, Vinesh H. Gada, Atul Sharma, B. Ravi "Computation of feed-paths for casting solidification using level-set-method” Journal of Materials Processing Technology Elsevier volume 212 (2012) 1236-1249
- [5] Χ. Sua, G. Wang, Y.T. Zhang,J.F.Li, Y.M.Rong "Modeling on stress evolution of step part for casting-heat treatment processes" International Federation for Heat Treatment and Surface Engineering 20th Congress Beijing Elsevier volume 50 (2013) 360 – 367
- [6] E. Anglada, A. Meléndez, L.Maestro, I. Domiguez "Adjustment of Numerical Simulation Model to the Investment Casting Process” The Manufacturing Engineering Society International Conference, MESIC 2013 Elsevier volume 63 (2013) 75 – 83
- [7] F. J. Bradley, M. Samonds "A comparison of source term and enthalpy approaches to the numerical simulation of the solidification of ductile irons" Applied mathematics modeling, volume 16, (1992).
9. Copyright:
*This material is based on the paper by Mahipalsinh G. Jadeja, Manojkumar V. Sheladiya, Mayursinh Gohil: A Review on Casting Defect Minimization Through Simulation.
This material is a summarized version of the above paper, and unauthorized use for commercial purposes is prohibited.
Copyright © 2025 CASTMAN. All rights reserved.