This article introduces the paper "A Study on Die Casting Process of the Automobile Oil Pan Using the Heat Resistant Magnesium Alloy".
Abstract:
This research paper investigates the die casting process for automobile oil pans using heat-resistant magnesium alloys, aiming to replace the currently used aluminum alloy. The study uses computational fluid dynamics (CFD) simulations and experimental die casting to evaluate the process parameters and material properties for optimal performance and defect reduction. The primary focus is on mitigating defects resulting from the differences in thermal properties between aluminum and magnesium alloys.
1. Introduction:
Automobile oil pans, located at the bottom of the crankcase, collect lubricating oil after its circulation. The high temperatures experienced necessitate the use of heat-resistant materials. Currently, aluminum alloys (ADC12) are employed. This study explores replacing aluminum with magnesium alloys to achieve significant weight reduction (approximately 35% due to the lower density of magnesium (1.8 g/cm³) compared to aluminum (2.8 g/cm³)). However, magnesium alloys exhibit lower elastic modulus (45 GPa vs. 73 GPa for aluminum), necessitating design optimization to maintain sufficient stiffness. While magnesium alloys offer advantages in terms of specific strength and specific modulus, they suffer from lower absolute strength and ductility compared to aluminum. Their limited use in automotive applications is currently restricted to components with less stringent thermal requirements (cylinder head covers, steering wheels, instrument panels, seat frames).
2. Background and Literature Review:
The paper briefly reviews the state of research in magnesium alloy development, focusing on cost-effective alloying strategies to achieve comparable heat resistance. The authors highlight the relatively limited adoption of magnesium alloys in heat-resistant automotive parts within Korea compared to advanced countries. The urgency for developing this technology to enhance Korea's competitiveness in the global automotive market is emphasized.
3. Research Objectives and Questions:
The main objective is to establish optimal die casting parameters for producing magnesium oil pans, using heat-resistant magnesium alloys as a substitute for aluminum. The key research question revolves around identifying the optimal design and processing conditions that minimize defects (such as porosity and shrinkage) during the die casting process of magnesium alloy oil pans. The underlying hypothesis is that optimizing die design (runner, gate, vent, overflow) and casting parameters (temperature, speed, pressure) based on the specific properties of magnesium alloys would lead to successful defect-free production.
4. Research Methodology:
The study employs a combination of simulation and experimentation.
- Simulation: CFD software (FLOW-3D) is used to simulate the die casting process. This includes modeling the temperature distribution in the die during various stages (filling, solidification, ejection, cooling), and analyzing the flow behavior of the molten magnesium alloys within the casting cavity. This helps to optimize the runner, gate, vent, and overflow systems to improve filling and reduce defects. The simulations consider the significant differences in thermal properties (heat capacity, latent heat) between magnesium and aluminum alloys.
- Experimentation: Die casting experiments using AE44 and MRI153M magnesium alloys are conducted to validate the simulation results and to optimize the process parameters further. The key process parameters investigated include: sleeve filling ratio, cavity filling time, shot speed, and die temperature. X-ray inspection and cross-sectional analysis are used to evaluate the quality of the castings and identify any defects.
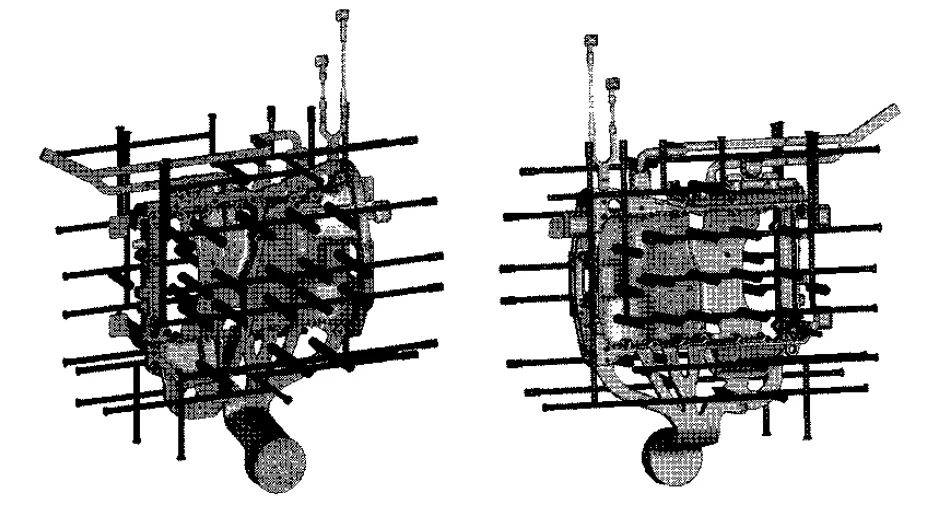
5. Results:
- Die Temperature Distribution Analysis: The analysis revealed that the die temperature decreases significantly faster with magnesium alloys compared to aluminum due to their lower heat capacity and latent heat. This necessitates modifications to the cooling system to prevent premature solidification and defects. The study compared the use of water cooling (for aluminum) versus oil cooling (for magnesium) to maintain optimal die temperature.
- Runner and Gate Design Optimization: The initial simulation using the existing aluminum die casting design revealed potential for air entrapment and oxide inclusion. Subsequent iterations improved runner and gate design (Fig. 6) to facilitate smoother metal flow, enhancing air venting, and minimize oxide formation. The simulations showed improvement in filling efficiency and air entrapment reduction (Fig. 7 and Fig. 10) with the modified design.
- Effect of Casting Parameters: The study investigated the influence of casting parameters (shot speed, cooling time, gate speed, and sleeve filling ratio) on the quality of the castings. The optimal parameter settings are detailed in Table 2, showing differences between AE44 and MRI153M magnesium alloys.
- Comparison of AE44 and MRI153M Alloys: Both AE44 and MRI153M were tested. MRI153M showed a tendency toward internal shrinkage porosity, possibly due to a longer solidification time (around 270°C difference in solidification range compared to AE44). However, optimization of the casting parameters significantly reduced this defect (Fig. 13, Fig. 14).
6. Discussion and Conclusion:
The findings highlight the significant impact of the differences in thermal properties between aluminum and magnesium alloys on the die casting process. The successful production of defect-free magnesium oil pans using optimized die design and casting parameters demonstrates the feasibility of replacing aluminum with magnesium alloys for oil pan applications. The study’s contribution lies in the detailed analysis of the die casting process, including CFD simulations and experimental validation, which provided insights into optimizing the process for magnesium alloys. This leads to substantial weight reduction, a crucial factor in improving fuel efficiency and reducing emissions.
7. Limitations:
The study's scope is limited to the specific magnesium alloys and oil pan geometry examined. Further research with a wider range of magnesium alloys and different geometries is necessary to generalize the findings. Long-term durability testing under various operating conditions would strengthen the conclusions on the practical applicability of magnesium oil pans.
8. Future Research:
Future research should explore a broader range of magnesium alloys, investigate different die designs, and carry out extensive life-cycle testing to evaluate the long-term performance and durability of magnesium oil pans under real-world operating conditions. The effects of various alloying elements on the casting properties and the resulting mechanical performance also require further investigation. The impact of variations in casting conditions beyond those tested (e.g., a wider range of temperatures and pressures) could also be examined.
References:
- D. M. Kim, H. S. Kim, and S. I. Park, "Magnesium for Automotive Application," Journal of KSAE, vol. 18, no. 5, pp. 53-67, 1996.
- J. Hwang and D. Kang, "FE Analysis on the press forging of AZ31 Magnesium alloys,” Transactions of KSAE, vol. 14, no. 1, pp. 86-91, 2006.
- P. Lyon, J. F. King, and K. Nuttal, "A New Magnesium HPDC Alloy for Elevated Temperature Use," Proceedings of the 3rd International Magnesium Conference, ed. G. W. Lorimer, Manchester, UK, pp. 10-12, 1996.
- F. von Buch, S. Schumann, H. Friedrich, E. Aghion, B. Bronfin, B. L. Mordike, M. Bamberger, and D. Eliezer, "New Die Casting Alloy MRI 153 for Power Train Applications," Magnesium Technology 2002, pp. 61-68, 2002.
- M. C. Kang and K. Y. Sohn, "The Trend and Prospects of Magnesium Alloys Consumption for Automotive Parts in Europe," Proceedings of KSAE Autumn Conference, pp. 1569-1576, 2003.
- S. Schumann and H. Friedrich, "The Use of Mg in Cars Today and in Future," Conference Paper at Mg Alloys and Their Applications, Wolfsburg, Germany, 1998.
- W. Sebastian, K. Droder, and S. Schumann, "Properties and Processing of Magnesium Wrought Products for Automotive Applications," Conference Paper at Magnesium Alloys and Their Applications, Munich, Germany, 2000.
- S. Koike, K. Washizu, S. Tanaka, K. Kikawa, and T. Baba, "Development of Lightweight Oil Pans Made of a Heat-Resistant Magnesium Alloy for Hybrid Engines," SAE 2000-01-1117, 2000.
Copyright:
This document is a summary based on the research paper by Shin, Chung, and Kang.
Unauthorized commercial use is prohibited.
Copyright © 2024 CASTMAN. All rights reserved.