This article introduces the paper "Magnesium casting technology for structural applications".
![Fig. 19. Magnesium powertrain components from the USCAR magnesium powertrain cast components project; (a) LPDC cylinder block, (b) Thixomolded front engine cover, (c) HPDC oil pan and (d) HPDC rear seal carrier [54].](https://castman.co.kr/wp-content/uploads/image-108-png.webp)
Overview:
- Core Objective of the Research: To provide a comprehensive overview of magnesium alloy melting and casting processes, examine the historical development, current status, and potential applications of structural magnesium castings, primarily focusing on the automotive industry, and discuss associated technological challenges. The increasing global demand for energy, environmental protection initiatives, and government regulations are expected to drive the adoption of lightweight magnesium castings in the coming decades.
- Main Methodology: The study employs a literature review and analysis of magnesium alloy melting and casting processes. It examines the historical development of magnesium casting technology, current casting techniques, structural applications in automotive, aerospace, and power tool industries, and assesses the opportunities and challenges associated with using magnesium alloys for structural applications.
- Key Results: The research provides a detailed overview of various magnesium casting processes, including high-pressure die casting (HPDC), low-pressure die casting (LPC), vacuum-assisted HPDC, super-vacuum die casting (SVDC), squeeze casting, lost foam casting, ablation casting, and semi-solid casting. It offers an in-depth analysis of magnesium's use in structural applications, particularly in the automotive sector, highlighting the advantages of magnesium alloys (excellent castability, lightweight nature) and the challenges (porosity, corrosion susceptibility, fatigue strength). Alternative casting processes, like vacuum die casting and super-vacuum die casting, are presented as potential solutions to address porosity issues. The development and application of Integrated Computational Materials Engineering (ICME) tools are anticipated to accelerate the adoption of magnesium castings in structural applications.
Researcher Information
- Affiliation: The paper does not explicitly state the author's specific affiliation beyond what is shown in the paper itself.
- Author: Alan A. Luo
- Main Research Area: Magnesium casting technology
Research Background and Objectives
- Industrial Context: Growing demand for lightweight materials across various sectors, including automotive, aerospace, and power tools.
- Specific Technological Challenges: Magnesium's inherent challenges in casting (high porosity, susceptibility to oxidation and burning), and the need for environmentally friendly alternatives to traditional protective gases (e.g., SF6). Also noted are the issues of corrosion resistance, fatigue strength, and crashworthiness.
- Research Goals: To comprehensively review magnesium alloy melting and casting processes, analyze the historical development and current trends in structural magnesium casting (with automotive applications as a key focus), identify and address technical challenges, and offer insights into future prospects for magnesium alloys in structural applications.
Main Objectives and Research Content of the Paper
- Main Objectives: To provide a complete overview of magnesium alloy casting technologies, analyze the challenges and opportunities associated with their application in structural components (especially within the automotive industry), and to provide future directions for research and development.
- Problems Addressed: The research directly addresses the challenges of porosity, corrosion resistance, and fatigue strength inherent in magnesium castings. It also notes the environmental concerns related to traditional casting processes.
- Stepwise Approach to Problem Solving: The paper systematically addresses the challenges by:
- Providing a detailed overview of existing magnesium casting methods, including their specific characteristics, advantages, and limitations.
- Thoroughly analyzing the historical development of magnesium castings in major industrial sectors, primarily focusing on automotive applications.
- Examining current applications of magnesium castings in various industries, especially those in the automotive sector.
- Identifying and discussing the key technological challenges associated with wider adoption of magnesium castings, focusing on porosity, corrosion, and fatigue performance.
- Proposing and explaining alternative casting methods (vacuum die casting, super-vacuum die casting, squeeze casting) as potential solutions to address the aforementioned limitations.
- Discussing the role of ICME tools in accelerating the adoption of magnesium castings in structural applications.
- Key Figures (Refer to the figure captions/alt text within the original paper for detailed descriptions): The paper includes numerous figures illustrating various aspects of magnesium casting processes, equipment, and resulting components. These figures are crucial for understanding the processes and results discussed.
![Fig. 1. Cross section of a stationary fuel-fired furnace used for the open crucible melting of magnesium alloys [2].](https://castman.co.kr/wp-content/uploads/image-90-png.webp)
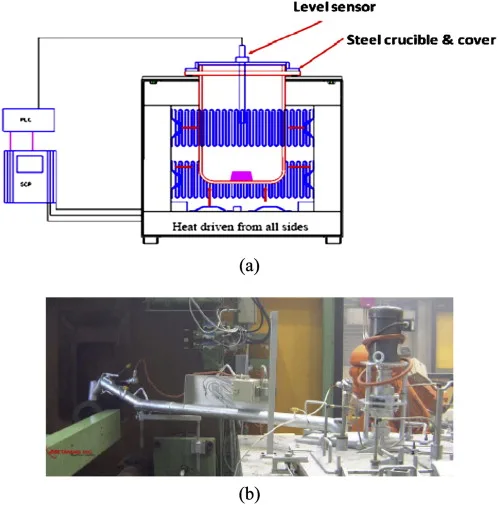
![Fig. 3. Schematics of hot chamber die casting [8].](https://castman.co.kr/wp-content/uploads/image-92-png.webp)
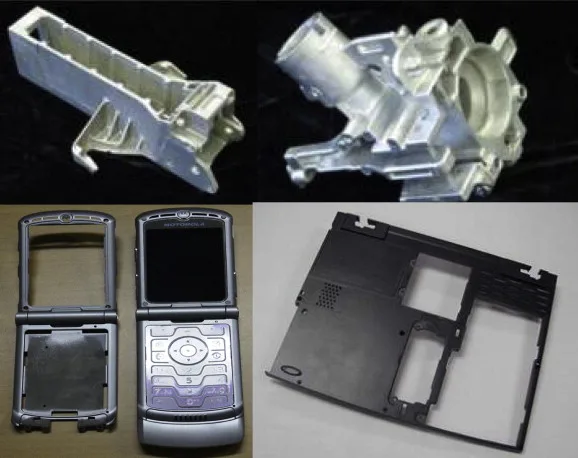
![Fig. 5. Schematics of cold chamber die casting [8].](https://castman.co.kr/wp-content/uploads/image-94-png.webp)

![Fig. 7. Gibbs vertical vacuum assisted die casting process (Courtesy of Gibbs Die Casting, Henderson, KY, USA [11]).](https://castman.co.kr/wp-content/uploads/image-96-png.webp)
![Fig. 8. A schematic diagram of a typical low pressure casting machine [17].](https://castman.co.kr/wp-content/uploads/image-97-png.webp)
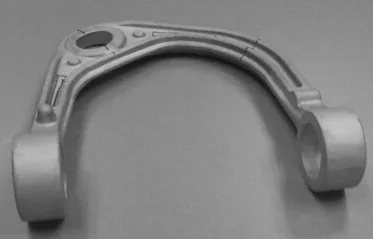
![Fig. 10. A schematic diagram of a Thixomolding machine [21].](https://castman.co.kr/wp-content/uploads/image-99-png.webp)
![Fig. 11. Schematic illustrating direct squeeze casting process operations: (a) melt into die cavity; (b) close tooling, solidify melt under pressure; and (c) eject casting [8].](https://castman.co.kr/wp-content/uploads/image-100-png.webp)
![Fig. 12. Schematic illustrating metal flow in (a) conventional die casting; and (b) indirect squeeze casting process [8].](https://castman.co.kr/wp-content/uploads/image-101-png.webp)
![Fig. 13. Ablation casting process for aluminum and magnesium casting [26].](https://castman.co.kr/wp-content/uploads/image-102-png.webp)
![Fig. 14. Pratt & Whitney F119 auxiliary casing in ELEKTRON WE43 alloy [37].](https://castman.co.kr/wp-content/uploads/image-103-png.webp)
![Fig. 15. Rolls Royce tray in ELEKTRON ZRE1 alloy [37].](https://castman.co.kr/wp-content/uploads/image-104-png.webp)
![Fig. 16. HPDC magnesium casting Lincoln MKT liftgate inner (photo courtesy of Meridian Lightweight Technologies) [49].](https://castman.co.kr/wp-content/uploads/image-111-png.webp)
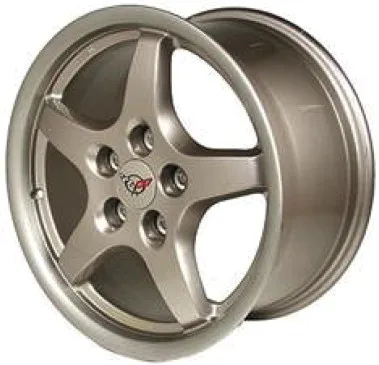
![Fig. 18. The BMW composite engine block showing a cutaway of the magnesium exterior revealing the aluminum interior [35].](https://castman.co.kr/wp-content/uploads/image-109-png.webp)
![Fig. 20. Aluminum isolator locations for Chevrolet Corvette Z06 magnesium cradle (bottom & top views) [50].](https://castman.co.kr/wp-content/uploads/image-107-png.webp)
![Fig. 21. USCAR demo structure build using (a) FSLW (friction stir linear welding); and (b) LSPR (laser-assisted self-pierce rivet) joining processes [67].](https://castman.co.kr/wp-content/uploads/image-106-png.webp)
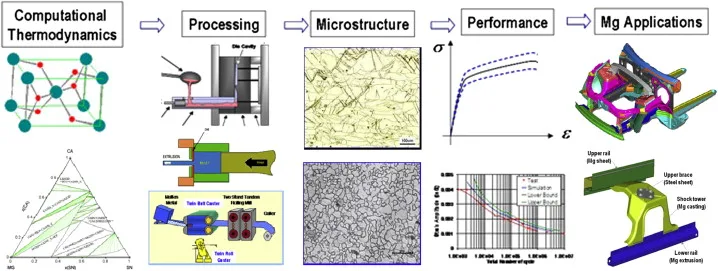
Results and Achievements
- Quantitative Results: The paper presents numerous quantitative data points, including dimensional tolerances, minimum wall thicknesses, casting/molding cycle times, die life, and tensile properties (yield strength, ultimate tensile strength, elongation) for different magnesium alloys and casting processes. These values are reported in Tables 1, 3, 4, and 5.
- Qualitative Results: The paper offers a thorough qualitative analysis of the historical development of magnesium castings, their current and potential applications in various industries (automotive, aerospace, power tools), the technological challenges associated with their use, and potential solutions to overcome these challenges.
- Technological Achievements: The paper highlights advancements in magnesium casting technology, including the development of vacuum die casting, super-vacuum die casting, and squeeze casting methods to mitigate porosity issues. It also discusses advancements in alloys that address corrosion resistance and improved mechanical properties. The integration of ICME tools is presented as a significant step towards accelerating the adoption of magnesium castings.
Copyright and References
This document summarizes Alan A. Luo's paper "Magnesium casting technology for structural applications".
Paper Source: https://doi.org/10.1016/j.jma.2013.02.002
This document is a summary and is not intended for commercial use without permission.
References
- [1]A.A. Luo, K. SadayappanTechnology for Magnesium CastingsAmerican Foundry Society, Schaumburg, IL (2011)pp. 29–47Google Scholar
- [2]M.M. Avedesian, H. BakerMagnesium and Magnesium AlloysASM International, Materials Park, OH (1999)Google Scholar
- [3]J.W. Freuling, J.D. HanawaltTransactions of the American Foundrymen's Society, 77 (1969), pp. 159-164
- [4]J.W. Freuling, Protective Atmospheres for Molten Magnesium, Ph.D. Dissertation, University of Michigan, Ann Arbor, MI, USA, 1970.Google Scholar
- [5]J.F. King, Environmental Challenges Facing the Magnesium Industry – SF6 Replacement, in: Proceedings of the 60th Annual World Magnesium Conference, The International Magnesium Association, Wauconda, IL, USA, 10–16.Google Scholar
- [6]R.E. Brown, Future of Magnesium Developments in 21st Century, in: Presentation at Materials Science & Technology Conference, Pittsburgh, PA, USA, October 5–9, 2008.Google Scholar
- [7]T. Ruden, Magnesium vs. Plastics: A Comparative Study, (Paper G-T89-113), in: Presented at the 15th International Die Casting Congress & Exposition, St. Louis, MO, 1989.Google Scholar
- [8]E.J. VinarcikHigh Integrity Die Casting ProcessesJohn Wiley & Sons, Inc., New York, NY (2003)Google Scholar
- [9]M. Nehan, R. MaloneyMagnesium AM60B Instrument Panel Structure for Crashworthiness FMVSS 204 and 208 Compliance(1996)SAE Paper No. 960419, Warrendale, PAGoogle Scholar
- [10]Die Casting Industry Capability Directory, North American Die Casting Association, Rosemont, IL, USA (2000)
- [11]http://www.gibbsdc.com/.Google Scholar
- [12]A.A. Luo, P.H. Fu, Y.D. Yu, H.Y. Jiang, L.M. Peng, C.Q. Zhai, A.K. SachdevVacuum-assisted High Pressure Die Casting of AZ91 Magnesium AlloyNorth American Die Casting Association Transactions, T08-083(2008)Google Scholar
- [13]Z. Brown, B. Szymanowski, M. Musser, D. Saha, S. Seaver, Manufacturing of Thin Wall Structural Automotive Components Through High Vacuum Die Casting Technology, 2007 Metal Casting Congress.Google Scholar
- [14]H. Koch, A.J. FrankeDuctile Pressure Die Castings for Automotive ApplicationS.K. Das (Ed.), Automotive Alloys, TMS (The Minerals, Metals and Materials Society), Warrendale, PA (1997), pp. 185-198View in ScopusGoogle Scholar
- [15]Z. Brown, A.A. Luo, K. Sadayappan, L.J. Ouimet, J. Zindel, R. Beals, M. MusserDevelopment of Super Vacuum Die Casting Process for Magnesium AlloysNorth American Die Casting Association Transactions, T09-043(2009)Google Scholar
- [16]M. Sahoo, D. Weiss, M. Marlatt, Factors Affecting Successful Permanent Mold Casting of Magnesium, in: Presented at International Conference on Permanent Mold Casting of Al and Mg, February 11–12, 2008, Dallas, Texas, USA.Google Scholar
- [17]P. Fu, A.A. Luo, H. Jiang, L. Peng, Y. Yu, C. Zhai, A.K. SachdevJournal of Materials Processing Technology, 205 (2008), pp. 224-234View PDFView articleView in Scopus
- [18]H. Westengen, O. HoltaFoundry Trade Journal (1989), pp. 738-742
- [19]S.T. Robison, D. Weiss, G. Gegel, G. Woycik, M. Marlatt, B. CoxMagnesium Casting Process Development: Designing an Engine Cradle for Magnesium Semi-permanent Mold CastingAFS Paper 05-217American Foundry Society, Schaumburg, IL (2005)Google Scholar
- [20]A.A. Luo, P.H. Fu, Y.D. Yu, L.M. Peng, H.Y. Jiang, C.Q. Zhai, A.K. SachdevLow Pressure Die Casting of AZ91 and AM50 Magnesium AlloysAFS Paper 08-147American Foundry Society, Schaumburg, IL (2007)Google Scholar
- [21]S.E. LeBeau, M.W. Walukas, R.F. Decker, P. LaBelle, A.R. Moore, J.W. JonesEvaluation of Thixomolded Magnesium Alloy Components for Structural Automotive ApplicationsSAE Technical Paper 2004-01-0137SAE International, Warrendale, PA (2008)Google Scholar
- [22]S. Corbit, R. DasGuptaSqueeze Cast Automotive Applications and Squeeze Cast Aluminum Alloy PropertiesSAE Technical Paper 1999-01-0343SAE, Warrendale, PA (1999)Google Scholar
- [23]R. DasGupta, P. Burton, Z. BrownMicrostructure and Mechanical Properties of Squeeze Cast AZ91D Magnesium AlloySAE Technical Paper 2005-01-0330SAE, Warrendale, PA (2005)Google Scholar
- [24]B. Szymanowski, Magnesium Squeeze Casting Update, in: Presentation at the 111th Metalcasting Congress, Houston, TX, May 15–18, 2007.Google Scholar
- [25]Y. Fasoyinu, M. Sahoo, Lost Foam Casting of Magnesium Alloys for Automotive Applications, in: Proceedings of 64th Annual World Magnesium Conference, International Magnesium Association, Wauconda, IL, USA, 117–134.Google Scholar
- [26]J. Grassi1, J. Campbell, M. Hartlieb, F. MajorMaterials Science Forum, 618–619 (2009), pp. 591-594View in Scopus
- [27]B. Cox, J. Zindel, M. Maj, L. Ouimet, A. Luo, D. Osborne, M. Osborne, R. Beals, E. McCarty, S. Robison, D. Weiss, D. Penrod, High Integrity Magnesium Automotive Components (HIMAC), in: Presentation at the 111th American Foundry Society Metalcasting Congress, Houston, TX, USA, May 15–18, 2007.Google Scholar
- [28]A.I. Taub, P.E. Krajewski, A.A. Luo, J.N. OwensJournal of Metals, 59 (2) (February 2007), pp. 48-57CrossrefView in Scopus
- [29]A.A. LuoChapter 8. Applications: Aerospace, Automotive and Other Structural Applications of Magnesiumbook chapterFundamentals of Magnesium Alloy Metallurgy, Woodhead Publishing Ltd, Cambridge, UK (2012)pp. 393–426Google Scholar
- [30]K.U. KainerMagnesium – Alloys and TechnologiesWiley-VCH, Weinheim, Germany (2003)Google Scholar
- [31]A.A. LuoJournal of Metals, 54 (2) (2002), pp. 42-48View in Scopus
- [32]H.-H. Becker, Status, Potential & Challenges for Automotive Magnesium Applications from the Point of View of an OEM, in: Presentation at 65th Annual World Magnesium Conference, May 18–20, 2008, Warsaw, Poland.Google Scholar
- [33]Y. Michiura, Current Magnesium Research & Application in Automotive Industry in Japan, in: Presentation at International Automotive Body Congress, November 7–8, 2007, Troy, MI, USA.Google Scholar
- [34]J.S. Balzer, P.K. Dellock, M.H. Maj, G.S. Cole, D. Reed, T. Davis, T. Lawson, G. SimondsStructural Magnesium Front End SupportSAE Technical Paper 2003-01-0185SAE International, Warrendale, PA (2003)Google Scholar
- [35]M. Hoeschl, W. Wagener, J. WolfBMW's Magnesium–aluminium Composite Crankcase, State-of-the-art Light Metal Casting and ManufacturingSAE Technical Paper 2006-01-0069SAE International, Warrendale, PA (2006)Google Scholar
- [36]C.J. Duke, S. LoganLightweight Magnesium Spare Tire CarrierProceedings of the 64th Annual World Magnesium Conference, International Magnesium Association, Wauconda, IL 60084, USA (2007), pp. 75-80View in ScopusGoogle Scholar
- [37]G.D. Wardlow, A Changing World with Different Rules – New Opportunities for Magnesium Alloys?, in: Presentation at the 64th Annual World Magnesium Conference, Vancouver, BC, Canada, May 13th–15th, 2007.Google Scholar
- [38]O. Pashkova, I. Ostrovsky, Y. Henn, Present State and Future of Magnesium Application in Aerospace Industry, in: Presentation at New Challenges in Aeronautics, Moscow, 2007.Google Scholar
- [39]J. HillisThe Effects of Heavy Metal Contamination on Magnesium Corrosion PerformanceSAE Technical Paper No. 830523SAE International, Warrendale, PA, USA (1983)Google Scholar
- [40]R.E. Brown, E. LeeMagnesium Usage Grew Rapidly in 1930–1950W.J. Poole, K.U. Kainer (Eds.), Proceedings of 9th International Conference on Magnesium Alloys and Their Applications (July 8–12, 2012), pp. 453-460Vancouver, BC, CanadaCrossrefView in Scopus
- [41]B.R. Powell, P.E. Krajewski, A.A. LuoChapter 4: Magnesium Alloysbook chapterMaterials Design and Manufacturing for Lightweight Vehicles, Woodhead Publishing Ltd, Cambridge, UK (2010)pp. 114–168Google Scholar
- [42]E.F. EmleyPrinciples of Magnesium TechnologyPergamon Press (1966)Google Scholar
- [43]S. Schumann, H. FriedrichThe Use of Magnesium in Cars – Today and in the FutureB. Mordike, K. Kainer (Eds.), Magnesium Alloys and Their Applications, Werkstoff-Informationsgesellschaft, Frankfurt, Germany (1998), pp. 3-13Google Scholar
- [44]H. Friedrich, S. SchumannJournal of Materials Processing Technology, 117 (2001), pp. 276-281View PDFView articleView in Scopus
- [45]F. Hollrigl-RostaLight Metal Age (1980), pp. 22-29View in Scopus
- [46]A. Hector, W. HeissMagnesium Die-castings as Structural Members in the Integral Seat of the New Mercedes-Benz RoadsterSAE Technical Paper No. 900798SAE, Warrendale, PA (1990)Google Scholar
- [47]D. AlexanderAutomotive Engineering International (May 2004), pp. 22-24View in Scopus
- [48]L. Riopelle, Magnesium Applications, in: International Magnesium Association (IMA) Annual Magnesium in Automotive Seminar, Livonia, MI, April 20, 2004.Google Scholar
- [49]S. GibbsMetal Casting Design and Purchasing (July/August 2010), pp. 29-33View in Scopus
- [50]J. Aragones, K. Goundan, S. Kolp, R. Osborne, L. Ouimet, W. PinchDevelopment of the 2006 Corvette Z06 Structural Cast Magnesium CrossmemberSAE International Technical Paper No. 2005-01-0340SAE International, Warrendale, Pennsylvania (2005)Google Scholar
- [51]J. Greiner, C. Doerr, H. Nauerz, M. GraeveThe New ‘7G-TRONIC’ of Mercedes-Benz: Innovative Transmission Technology for Better Driving Performance, Comfort, and Fuel EconomySAE Technical Paper No. 2004-01-0649SAE International, Warrendale, PA, USA (2004)Google Scholar
- [52]S. Koike, K. Washizu, S. Tanaka, T. Baba, K. KikawaSAE Technical Paper No. 2000-01-1117SAE International, Warrendale, PA, USA (2000)Google Scholar
- [53]B. Powell, et al., Progress Toward a Magnesium-intensive Engine: The USAMP Magnesium Powertrain Cast Components Project, SAE 2004 Transactions, Journal of Materials & Manufacturing Paper No. 2004-1-0654, SAE International, Warrendale, PA, USA, 250–259.Google Scholar
- [54]B.R. PowellMagnesium Powertrain Cast ComponentsPublished in FY2008 Annual Progress Report for Automotive Lightweighting MaterialsU.S. Department of Energy, Washington, D.C (April 2009)
- [55]International Magnesium AssociationMagnesium's Tough Strength Endures Abuse to Protect Portable Electronic DevicesInternational Magnesium Association, Wauconda, IL, USA (2008)Google Scholar
- [56]International Magnesium AssociationLighter Magnesium Improves Power Tool PerformanceInternational Magnesium Association, Wauconda, IL, USA (2008)Google Scholar
- [57]C.L. Mendis, C.J. Bettles, M.A. Gibson, C.R. HutchinsonMaterials Science and Engineering A, 435/436 (2006), pp. 163-171View PDFView articleView in Scopus
- [58]A.A. Luo, P. Fu, L. Peng, X. Kang, Z. Li, T. ZhuMetallurgical and Materials Transactions A, 43A (2012), pp. 360-368CrossrefView in Scopus
- [59]P. Fu, L. Peng, H. Jiang, J. Chang, C. ZhaiMaterials Science and Engineering A, 486 (2008), pp. 183-192Crossref
- [60]A.A. Luo, R.K. Mishra, B.R. Powell, A.K. SachdevMaterials Science Forum, 706–709 (2012), pp. 69-82View in Scopus
- [61]A.A. Luo, W. Shi, K. Sadayappan, E.A. NybergMagnesium Front End Research and Development: Phase I Progress Report of a Canada–China–USA CollaborationProceedings of IMA 67th Annual World Magnesium Conference, International Magnesium Association (IMA), Wauconda, IL, USA (2010)Google Scholar
- [62]M. Easton, A. Beer, M. Barnett, C. Davies, G. Dunlop, Y. Durandet, S. Blacket, T. Hilditch, P. BeggsJOM, 60 (11) (2008), pp. 57-62CrossrefView in Scopus
- [63]F. Zhu, C.C. Chou, K.H. Yang, X. Chen, D. Wagner, S. Bilkhu, A.A. LuoInternational Journal of Crashworthiness, 17 (5) (2012), pp. 540-552CrossrefView in Scopus
- [64]S. Logan, A. Kizyma, C. Patterson, S. RamaLightweight Magnesium-intensive Body StructureSAE International Technical Paper No. 2006-01-0523SAE International, Warrendale, PA, USA (2006)Google Scholar
- [65]W. Wen, A.A. Luo, T. Zhai, Y. Jin, Y.-T. Cheng, I. HoffmannScripta Materialia, 66 (2012), 10.1016/j.scriptamat.2012.08.010View at publisher
- [66]H.A. Patel, N. Rashidi, D.L. Chen, S.D. Bhole, A.A. LuoMaterials Science and Engineering A, 546 (2012), pp. 72-81View PDFView articleView in Scopus
- [67]A.A. Luo, J.F. Quinn, Y.-M. Wang, T.M. Lee, R. Verma, D.A. Wagner, J.H. Forsmark, X. Su, J. Zindel, M. Li, S.D. Logan, S. Bilkhu, R.C. McCuneLight Metal Age (April 2012), pp. 54-58View in Scopus
- [68]National Research CouncilIntegrated Computational Materials Engineering: A Transformational Discipline for Improved Competitiveness and National SecurityThe National Academies Press, Washington, DC, USA (2008)Google Scholar
- [69]M. Li, A.A. Luo, Integrated Computational Materials Engineering for Magnesium, Published in FY2011 Annual Progress Report for Automotive Lightweighting Materials, U.S. Department of Energy, Washington, D.C., USA, http://www1.eere.energy.gov/vehiclesandfuels/pdfs/lm_11/4_usamp_cooperative_research.pdf.Google Scholar
- [70]T.M. PollockScience, 328 (2010), pp. 986-987View at publisherCrossrefView in Scopus