This introduction paper is based on the paper "Examples of Practical Solutions for Aluminium Castings using Quiescent Running Systems and Computer Modelling" published by "Conference Paper".
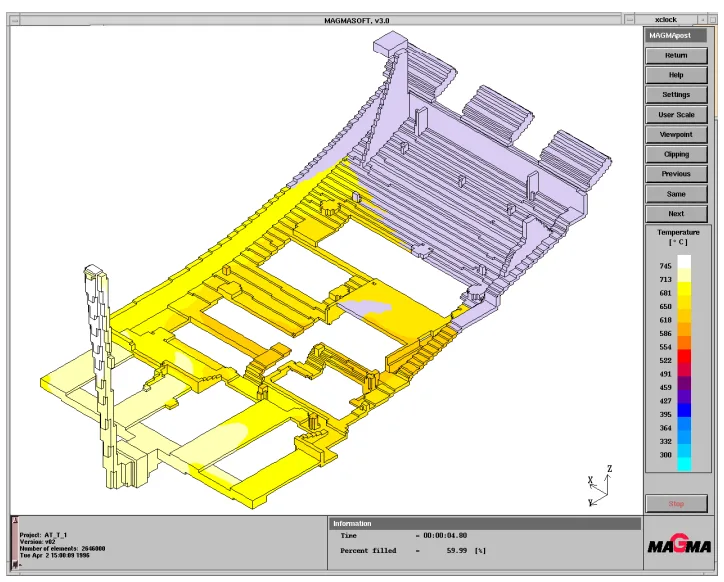
1. Overview:
- Title: Examples of Practical Solutions for Aluminium Castings using Quiescent Running Systems and Computer Modelling
- Author: Mark R Jolly, PhD.
- Year of publication: 1999
- Journal/academic society of publication: Conference Paper
- Keywords: Aluminium Castings, Quiescent Running Systems, Computer Modelling, Gravity Die-Casting, Low-Pressure Die-Casting, Sand Casting
2. Abstract:
The Castings Centre at the University of Birmingham, Birmingham, England has been using a combination of practical rules and computer simulation to supply running system solutions to industry over the past 5 years. The practical rules have come from a distillation of the work carried out by the Castings Research Group directed by Prof. John Campbell using real time x-ray techniques to observe real filling systems. The computer simulation has been carried out on a selection of commercial software packages and for sand, gravity die (permanent-mold) and low-pressure die-castings. A selection of examples will be shown in order to demonstrate the effectiveness of the approaches taken. These cover both automotive and non-automotive applications.
3. Introduction:
The method of handling and distributing liquid metal into a mould cavity is arguably the most critical factor influencing the quality and properties of a casting. Often overlooked in the design process, the fluid dynamics of mould filling are paramount. Work at the University of Birmingham has demonstrated that significant quality improvements can be achieved by focusing on the details of fluid dynamics. When filling is correctly managed, feeding becomes a secondary issue. The paper emphasizes the need for quiescent, non-turbulent filling as a prerequisite for all high-quality castings, not limited to aluminum alloys. It notes that turbulent filling is the primary cause of defects such as slag, entrapped bubbles, and inclusions. Traditional gating systems that "shoot" metal into the cavity are flawed. This paper presents three case studies to illustrate the successful application of theoretical rules, computer simulation, and practical adjustments to create commercially viable casting solutions.
4. Summary of the study:
Background of the research topic:
The research is set against the industrial challenge of producing high-quality metal castings. The quality of a cast part is fundamentally linked to how the molten metal is introduced into the mould. Turbulent filling processes are a primary source of defects that lead to scrap and unreliable final products.
Status of previous research:
The foundation of this work lies in the research conducted by the Castings Research Group at the University of Birmingham, under Prof. John Campbell. This group developed a set of practical rules for designing filling systems based on observations from real-time x-ray imaging of the casting process. The current paper builds on this by integrating these rules with commercial computer simulation software.
Purpose of the study:
The study aims to demonstrate the effectiveness of a combined approach—using practical design rules and computer simulation—to engineer solutions for industrial casting operations. It showcases how this methodology can solve complex filling and solidification problems for both automotive and non-automotive components.
Core study:
The core of the study consists of three detailed industrial case studies:
- Gravity Die-Cast ATM Housing: Designing a running system for a large, complex aluminum housing for an NCR Automated Teller Machine.
- Gravity Die-cast Heat Sink Casting: Developing a manufacturing process for a heat sink with embedded stainless steel tubes for marine gearboxes.
- Low-pressure automotive wheel casting: Resolving porosity defects in a low-pressure die-cast aluminum alloy wheel for Compomotive Ltd.
5. Research Methodology
Research Design:
The research methodology combines theoretical principles with computational analysis. It uses design rules developed by the Casting Research Group (CRG) to create an initial filling system. This design is then implemented and tested using computer simulation to predict and visualize the mould filling and solidification process, allowing for iterative refinement before production.
Data Collection and Analysis Methods:
The study utilizes commercial simulation software packages to model fluid flow and solidification. Analysis of simulation results, such as metal velocity, temperature distribution (as seen in Figure 17), and porosity prediction (as shown in Figure 9 and Figure 12), is the primary method for identifying potential defects. These predictions are validated by comparing them with the results of actual casting trials, as demonstrated in Figure 2.
Research Topics and Scope:
The research covers a range of common casting processes, including gravity die-casting (permanent-mold), sand casting, and low-pressure die-casting. The applications are diverse, spanning non-automotive (ATM housing) and automotive (heat sink, wheels) components, demonstrating the broad applicability of the methods.
6. Key Results:
Key Results:
The paper presents three case studies demonstrating the successful application of quiescent running systems and computer modeling.
- In Case Study 1, a quiescent filling system was designed for a complex gravity die-cast ATM housing. Simulation using design rules from the Casting Research Group (CRG) was essential to achieving a fill time of 8 seconds, which prevented misruns. The simulation accurately predicted a potential filling defect and air entrapment in a flat area of the casting (Figure 2a), which was confirmed in the actual casting (Figure 2b) and subsequently resolved by modifying the design to include bridges and venting (Figure 3).
- In Case Study 2, the initial gravity die-casting approach for a heat sink with embedded steel tubes failed, producing castings with large air pockets due to turbulent filling. Simulation revealed that the steel tubes were heating up during filling, creating a central hot spot that prevented proper feeding and caused porosity (Figure 9, Figure 11). The solution, guided by further analysis, was to switch to sand casting, which allowed for a slower, more controlled fill and resulted in castings of better than class 3 quality with no scrap (Figure 12, Figure 13).
- In Case Study 3, a low-pressure die-cast automotive wheel suffered from scrap due to porosity at the spoke-rim junction. Simulation accurately predicted this gross porosity and also identified micro-porosity in the central hub that had not been previously identified by the foundry (Figure 18b). The problems were mitigated by applying targeted solutions based on the simulation: the hub porosity was reduced by changing the spreader design, and the spoke-rim porosity was dramatically reduced by adding cooling fins (Figure 19).
Figure Name List:
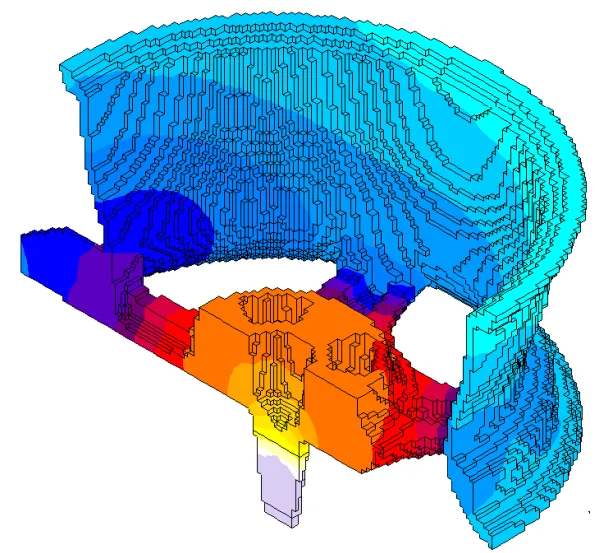
- Figure 1: Isometric, top and side views of ATM module interface castings and rigging.
- Figure 2a): Filling simulation showing potential filling problem and air entrapment.
- Figure 2b): Casting showing problem predicted in figure 2a).
- Figure 3: a) Simulation of module filling with wide bridges b) Simulation of module filling with narrow bridges.
- Figure 4: Simulations of flow off junctions a) & b) foundry preferred methods – 10 mm and 15mm thickness respectively with witness c) Castings Centre preferred method 15 mm no witness.
- Figure 5: ATM housing castings in product.
- Figure 6: Diagram of the 150 mm wide heat sink casting.
- Figure 7: Die-cast heat sink component first running system.
- Figure 8: Cross sections through first heat sink simulation showing the low level turbulence problem at a) 40 % full and no turbulence at b) 80% full.
- Figure 9: Porosity levels in the die-cast heat sink a) complete casting and rigging b) zoom in on region between tubes.
- Figure 10: a) CAD drawing of 5th version of rigging showing bubble trap, filter placed at 45° and shaped feeder b) Solidification results showing porosity distribution demonstrating that the change of alloy has no effect and feeder does not work.
- Figure 11: a) and b) showing progression of recalescence up the casting between the tubes c) and d) showing temperature rise between the tubes as the casting fills.
- Figure 12: a) Complete sand cast heat sink showing the redistribution of porosity compared with die-casting. b) Temperature distribution across the casting after filling showing no recalescence.
- Figure 13: Final configuration of rigging for heat sink component for sand casting.
- Figure 14: Low-pressure die-cast automotive wheel.
- Figure 15: Process pressure cycle for LPDC auto wheel.
- Figure 16a: Finite difference mesh for LPDC wheel casting.
- Figure 16b: Finite difference mesh of dies for LPDC wheel casting.
- Figure 17: Simulated warming cycles showing increases in die temperature.
- Figure 18a): Solidification time contour plot showing thermal isolations.
- Figure 18b): Porosity prediction showing macro- and micro-graphs confirming the predictions.
- Figure 19a): Solidification time contours for LPDC after modification showing better directional solidification and no thermal isolations.
- Figure 19b): Porosity prediction in LPDC after modification showing substantial reduction of porosity in hub and spoke rim junction.
7. Conclusion:
The paper concludes that while design rules provide a crucial starting point for designing turbulence-free filling systems, they are not a definitive "rule book" for every casting scenario. The use of sophisticated casting simulation tools is invaluable, allowing for trial and error to be performed computationally rather than on the foundry floor with expensive physical dies. This approach not only helps refine the running system but also proves essential in determining the correct and most viable manufacturing route to ensure acceptable quality. The case studies demonstrate that once turbulence-related defects are eliminated through proper, quiescent filling design, they do not reappear during solidification, preventing them from becoming undetectable "cancers" in the final product.
8. References:
The paper does not contain a formal list of numbered references. The following organizations were acknowledged for their support:
- NCR (Scotland)
- Johnston Engineering & Castings
- CEGELEC
- Barton Aluminium
- Compomotive 73
9. Copyright:
- This material is a paper by "Mark R Jolly". Based on "Examples of Practical Solutions for Aluminium Castings using Quiescent Running Systems and Computer Modelling".
- Source of the paper: https://www.researchgate.net/publication/281816640_Examples_of_Practical_Solutions_for_Aluminium_Castings_using_Quiescent_Running_Systems_and_Computer_Modelling (DOI: 10.13140/RG.2.1.4121.3529)
This material is summarized based on the above paper, and unauthorized use for commercial purposes is prohibited.
Copyright © 2025 CASTMAN. All rights reserved.
Paper Summarize:
Key questions and answers about the research:
This research demonstrates how combining practical design rules with computer simulation provides effective solutions for producing high-quality aluminium castings. It uses three industrial case studies—an ATM housing, a heat sink, and an automotive wheel—to show how this approach can predict and solve defects like turbulence, porosity, and filling problems. The key takeaway is that proper, quiescent filling system design, validated by simulation, is crucial and often more important than feeding considerations.
Q1. What does the paper identify as the most critical factor affecting the quality of a casting?
A1. The paper identifies the way liquid metal is handled and distributed into the mould cavity as "the single most important factor affecting the quality and properties of a casting". (Source: "Examples of Practical Solutions for Aluminium Castings using Quiescent Running Systems and Computer Modelling", Introduction).
Q2. Why is quiescent (non-turbulent) filling essential for quality castings?
A2. Quiescent filling is a prerequisite for quality castings because turbulent filling is the source of most defects, such as slag defects, lustrous carbon films, entrapped bubbles, and sand inclusions, which arise regardless of the alloy being used. (Source: "Examples of Practical Solutions for Aluminium Castings using Quiescent Running Systems and Computer Modelling", Introduction).
Q3. In Case Study 2 (Heat Sink Casting), why did the initial gravity die-casting method fail?
A3. The initial method failed because turbulent filling entrained air, and the stainless steel tubes within the casting heated up, acting as an insulator and creating a "massive hot spot" at the center. This prevented proper feeding and resulted in large air pockets and unacceptable porosity. (Source: "Examples of Practical Solutions for Aluminium Castings using Quiescent Running Systems and Computer Modelling", Case study 2).
Q4. What was the solution to the porosity problem in the heat sink casting (Case Study 2)?
A4. The solution was to change the manufacturing process from gravity die-casting to sand casting. This allowed for a longer filling time and established a more favorable temperature gradient, enabling directional solidification and allowing the casting to be fed properly, thus eliminating the porosity. (Source: "Examples of Practical Solutions for Aluminium Castings using Quiescent Running Systems and Computer Modelling", Case study 2).
Q5. How did computer simulation help improve the low-pressure automotive wheel in Case Study 3?
A5. Simulation accurately predicted shrinkage porosity at the spoke-rim junction and micro-porosity in the hub, which had been causing scrap. Based on the simulation, the spoke-rim porosity was reduced by adding cooling fins, and the hub porosity was lessened through slight geometry changes. (Source: "Examples of Practical Solutions for Aluminium Castings using Quiescent Running Systems and Computer Modelling", Case study 3).
Q6. What is the paper's main conclusion about developing a "right first time" casting process?
A6. The paper concludes that while a definitive “rule book” does not exist, the use of sophisticated casting simulation tools allows trial and error to be done on a computer. This helps determine the correct manufacturing route and a turbulence-free running system design before expensive dies are manufactured, making it possible to get the process right the first time. (Source: "Examples of Practical Solutions for Aluminium Castings using Quiescent Running Systems and Computer Modelling", Conclusions).