This introduction paper is based on the paper "New generation of high strength aluminum casting alloys" published by "Light Metal Age".
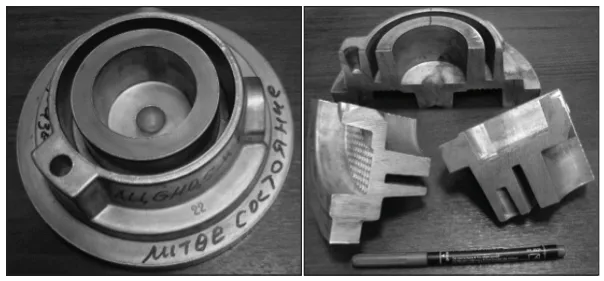
1. Overview:
- Title: New generation of high strength aluminum casting alloys
- Author: V.Kh. Mann, A.N.Alabin, A.Yu. Krokhin, A.V. Frolov, and N.A. Belov
- Year of publication: 2015 (October issue)
- Journal/academic society of publication: Light Metal Age
- Keywords: Al-Zn-Mg-Ni-Fe system, Nickalyn-AZ6NF, high strength aluminum casting alloys, mechanical properties, microstructure, phase composition.
2. Abstract:
The article represents the research results for phase composition, structure, and mechanical properties of the new sparingly alloyed high strength alloy of the Al-Zn-Mg-Ni-Fe system (Nickalyn-AZ6NF). The main advantages of the new aluminum alloy are the high level of mechanical properties (UTS of about 500 MPa), good workability during casting, and relatively low cost price. The alloy is intended for production of relatively sophisticated mold castings, including critical die castings, and may be used as an alternative of foundry steel and cast iron grades and some current aluminum casting alloys.
3. Introduction:
Alloys based on the Al-Si system are the most common aluminum die casting alloys, but the strength properties of strong silumins like A354 type typically do not exceed 350-380 MPa. High strength Al-Cu system alloys (2xxx series) present difficulties due to low workability during casting. Sparingly alloyed high strength aluminum alloys based on the Al-Zn-Mg-Fe-Ni system are promising for replacing conventional casting materials. These new alloys are developed based on eutectic (Al)+Al9FeNi, building upon previous positive results with Al-Zn-Mg-Ni system alloys based on eutectic (Al)+Al3Ni. While the Al-Zn-Mg-Ni alloys showed high strength (UTS=600-620 MPa), their high nickel content (about 4%) and strict iron limitation (<0.1%) were obstacles. Alloys with elevated iron content based on (Al) and eutectic (Al)+Al9FeNi are more cost-effective, containing 5-8 times lower nickel. These new alloys aim for a high level of mechanical properties and good workability during casting, attributed to the eutectic (Al)+Al9FeNi. This paper presents a comparative analysis of the structure and mechanical properties of the new high strength aluminum casting alloy Nickalyn-AZ6NF and an industrial aluminum casting alloy of type A356.
4. Summary of the study:
Background of the research topic:
There is a need for aluminum casting alloys with improved mechanical properties, good castability, and cost-effectiveness to replace conventional materials like foundry steel, cast iron, and some existing aluminum alloys in demanding applications.
Status of previous research:
Previous research on Al-Zn-Mg-Ni alloys showed record-breaking strength but suffered from high nickel content and low iron tolerance. Alloys based on the Al-Zn-Mg-Fe-Ni system with eutectic (Al)+Al9FeNi were proposed as a more cost-effective alternative with good workability.
Purpose of the study:
The aim of this paper is to present a comparative analysis of the structure and mechanical properties of a new sparingly alloyed high strength aluminum casting alloy of the Al-Zn-Mg-Ni-Fe system, designated Nickalyn-AZ6NF, with the conventional A356 alloy.
Core study:
The core of the study involves the experimental investigation of the phase composition, microstructure, and mechanical properties of the Nickalyn-AZ6NF alloy. This includes determining optimal alloy compositions, understanding microstructural features after heat treatment, and evaluating its tensile properties in comparison to A356.
5. Research Methodology
Research Design:
The study employed an experimental research design. Two experimental alloys from the Al-Zn-Mg-Fe-Ni system (specifically Nickalyn-AZ6NF with varying Fe content, though Table I lists one composition for AZ6NF) and a reference A356 alloy were prepared and characterized. Their properties were compared after different heat treatments.
Data Collection and Analysis Methods:
- Alloy Preparation: Experimental alloys were prepared in an electric furnace in graphite-chamotte crucibles using 99.5 and 99.95% pure Al, 99.9% pure Zn, 99.9% pure Mg, and master alloys Al–20%Ni, Al-10% Fe.
- Casting: Alloys were cast in steel molds at 720-740°C, with a cooling rate (Vc) of about 10 K s⁻¹.
- Chemical Analysis: Chemical compositions were analyzed using an ARL 4460 emission spectrometer. (See Table I).
- Heat Treatment: Solution heat treatment (T4) was performed (AZ6NF: 540°C, 3 hours, water quenching; A356: 535°C, 3 hours, water quenching) followed by aging to maximum strength (T6) in a drying oven.
- Microstructural Analysis: Structure was examined using optical microscopy (OM, Axiovert 200 MMAT), transmission electron microscopy (TEM, JEM-2100), and scanning electron microscopy (SEM, JSM-6610LV). Electrolytic polishing was used for sample preparation.
- Mechanical Testing: Uniaxial tension tests were conducted on a Zwick Z250 testing machine (loading velocity 4 mm/min, 5 mm diameter specimens, 25 mm length) to determine ultimate tensile strength (UTS), yield strength (YS), and relative elongation (El).
- Phase Diagram Calculation: Thermo-Calc software (database TTAL5) was used to calculate liquidus and solidus temperatures and vertical sections of phase diagrams.
Research Topics and Scope:
The research focused on:
- The phase composition and optimal alloying element concentrations (Fe, Ni) in the Al-Zn-Mg-Fe-Ni system.
- The microstructure of the Nickalyn-AZ6NF alloy after T4 heat treatment, particularly the morphology of Al9FeNi phase.
- The TEM structure of Nickalyn-AZ6NF after T6 heat treatment, focusing on Al9FeNi inclusions and secondary hardening phases.
- The mechanical properties (UTS, YS, El) of Nickalyn-AZ6NF in T4 and T6 conditions, compared to A356 in T6 condition.
6. Key Results:
Key Results:
- The optimum concentration of alloying elements in the Al-Zn-Mg-Fe-Ni system was determined by analyzing phase diagrams. For alloys with 1% Ni, primary Fe-containing intermetallics are expected above ~0.8% Fe. Reducing Fe to ~0.2% does not change phase composition significantly (Figure 2).
- The microstructure of AZ6NF after T4 treatment shows evenly distributed, spheroidized particles of the Al9FeNi phase (Figure 3a). The higher solidus temperature of AZ6NF (592°C, Table I) compared to A354 or 201 allows for annealing at higher temperatures.
- In the T6 condition, AZ6NF exhibits a uniform distribution of Al9FeNi inclusions (transverse size ≤ 2 µm) and secondary particles of hardener phases (size up to 10 nm) in the aluminum solid solution (Figure 4a, 4b).
- Sparingly alloyed AZ6NF (0.5 wt.% Fe) in the T6 condition achieves a high level of strength (UTS ~491 MPa) with satisfactory ductility (El ~6.1%). In the T4 condition, UTS is 397 MPa and El is 14.5%. These properties are superior to A356 (0.1 wt.% Fe, T6: UTS 310 MPa, El 9.7%) (Table II).
- The chemical compositions of the experimental alloys are detailed in Table I.
Figure Name List:
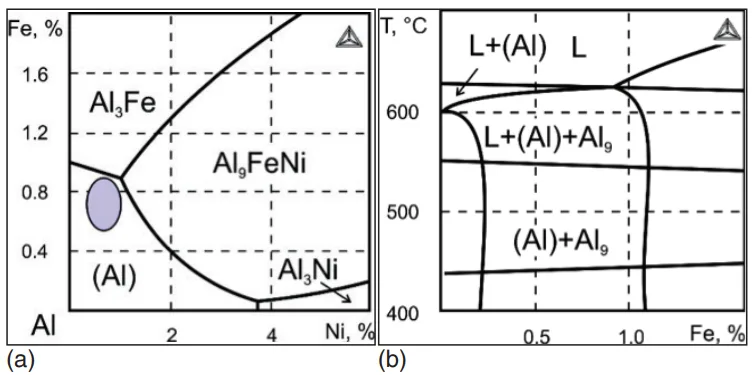

- Figure 1. Examples of alloy AZ6NF castings.
- Figure 2. Calculated liquidus projection (a) and vertical section (b) of the Al-Zn-Mg-Fe-Ni system at 7% Zn, 3% Mg, and 1%Ni (wt.%).
- Figure 3. Microstructure of alloys after heat treatment (T4): a – AZ6NF (SEM) and b – A356 (OM).
- Figure 4. TEM structure of alloy AZ6NF (T6): a – Al9FeNi and b – secondary segregations.
8. References:
- [1] Hatch, J.E. (ed.), Aluminum: Properties and Physical Metallurgy, ASM International, 1984.
- [2] Kaufman, J. Gilbert (ed.), Properties of Aluminum Alloys: Tensile, Creep and Fatigue Data at High and Low Temperatures, Aluminum Association/ASM International, 1999.
- [3] Mondolfo, L.F., Aluminum Alloys: Structure and Properties, Butterworths, 1976.
- [4] Zolotorevskiy, V.S., N.A. Belov, and M.V. Glazoff, Casting Aluminum Alloys, Elsevier, 2007.
- [5] Belov, N.A., D.G. Eskin, and A.A. Aksenov, Multicomponent Phase Diagrams: Applications for Commercial Aluminum Alloys, Elsevier, Amsterdam, 2005.
- [6] Belov, N.A., “Sparingly alloyed high-strength aluminum alloys: principles of optimisation of phase,” Metal Science and Heat Treatment, Vol. 53, No. 9-10, 2011, pp. 420-427.
- [7] Belov, N.A. "Quantitative phase analysis of the Al-Zn-Mg-Cu-Ni phase diagram in the region of compositions of high-strength nickalines,” Russian Journal of Non-Ferrous Metals, Vol. 51, No. 3, 2010, pp. 243–249.
- [8] Marlaud, T., A. Deschamps, F. Bley, et. al., “An Influence of alloy composition and heat treatment on precipitate composition in Al-Zn-Mg-Cu alloys," Acta Mater., Vol. 58, 2010, pp. 248–260.
- [9] LI Jin-feng, PENG Zhuo-wei, LI Chao-xing, et. al., "Mechanical properties, corrosion behaviours and microstructures of 7075 aluminum alloy with various ageing treatments," Transactions of Nonferrous Metals Society of China, Vol. 18, 2008, pp. 755-762.
9. Copyright:
- This material is a paper by "V.Kh. Mann, A.N.Alabin, A.Yu. Krokhin, A.V. Frolov, and N.A. Belov". Based on "New generation of high strength aluminum casting alloys".Source of the paper: https://www.researchgate.net/publication/301362888
Copyright © 2025 CASTMAN. All rights reserved.