This introduction paper is based on the paper "Monitoring of the microstructure and mechanical properties of the magnesium alloy used for steering wheel manufacturing" published by "MANUFACTURING TECHNOLOGY".
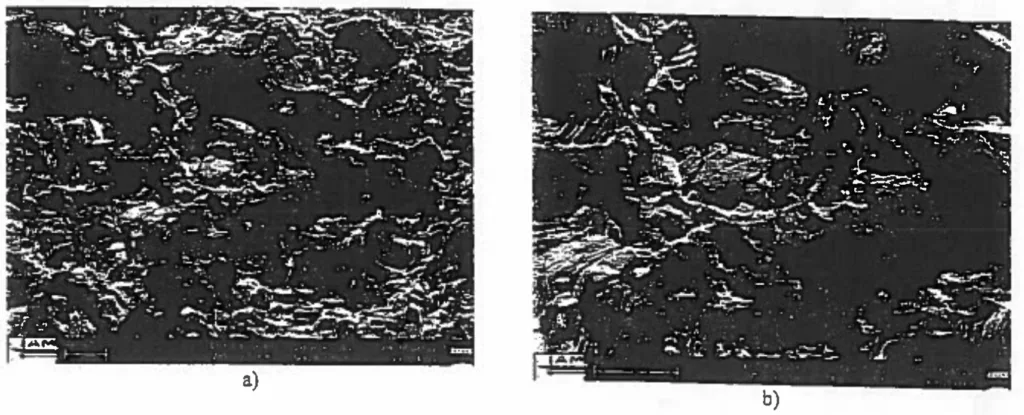
1. Overview:
- Title: Monitoring of the microstructure and mechanical properties of the magnesium alloy used for steering wheel manufacturing
- Author: Iva Nová, Jiří Machuta
- Year of publication: 2013
- Journal/academic society of publication: MANUFACTURING TECHNOLOGY
- Keywords: magnesium alloy MgAl5Mn, high pressure die casting, structure, mechanical properties
2. Abstract:
The article presents the microstructure and mechanical properties of magnesium steering wheels. These steering wheels are manufactured by high pressure die casting. High-pressure die casting (HPDC) is a very good process for making complex mechanical parts out of light metals like magnesium and aluminium alloys. However, in recent times, another light metal has come to the forefront in the quest for lighter vehicles and improved fuel economy. The most commonly used magnesium alloy for die casting automotive components is of the Mg-Al-Mn type. MgAl5Mn is a good purity magnesium alloy with good corrosion resistance, very good mechanical properties and good castability. Mg-Al-Mn based alloys such as MgAl5Mn and MgAl6Mn have better elongation and impact strength than MgAl9Zn, and they are mainly used for auto safety systems like wheel rims and steering wheels. Alloy MgAl5Mn is an alloy with outstanding ductility and energy absorbing properties combined with good strength. This alloy, in the solid state, contains a solid solution α and the intermediate phase Mg17 Al12.
3. Introduction:
Considerable attention has been given to low density, high ductility casting materials for the automotive industry, particularly for safety components like steering wheels. Magnesium alloys are among the lightest engineering metals, offering significant weight advantages over aluminium (density 1800 kg.m⁻³ vs 2700 kg.m⁻³). Aluminium is the principal alloying element in magnesium casting alloys, often with small amounts of zinc and manganese. High pressure die casting (HPDC) is the most common process for magnesium alloys due to their low melting point and specific heat, allowing for thinner walls compared to aluminium castings. The use of magnesium die castings is growing in automotive applications (e.g., instrument panels, cross car beams, seat frames) to reduce vehicle weight. Mg-Al-Mn and Mg-Al-Zn alloys are common, though magnesium's high affinity with oxygen presents processability challenges. This study focuses on the properties of magnesium alloys used for complex, thin-walled automotive castings like steering wheels.
4. Summary of the study:
Background of the research topic:
Magnesium alloys, particularly the Mg-Al-Mn type like MgAl5Mn, are increasingly used in automotive components due to their low density, good mechanical properties (especially ductility), and suitability for high pressure die casting (HPDC). Steering wheels are a key application where these properties contribute to vehicle weight reduction and safety. Monitoring the microstructure and mechanical properties of these alloys as-cast is crucial for ensuring component quality and performance.
Status of previous research:
Existing knowledge includes the characteristics of common magnesium casting alloys (e.g., AZ91, AM-series like AM50, AM60), their phase diagrams (Mg-Al, Mg-Al-Mn), and standard designations (ASTM, EN). Alloys with lower aluminium and zinc but higher manganese content (like AM50, corresponding to the studied MgAl5Mn) are known to exhibit higher ductility, making them suitable for safety-critical parts. HPDC is established as the primary manufacturing method for such components.
Purpose of the study:
The study aimed to monitor and characterize the microstructure and mechanical properties of a specific magnesium alloy, MgAl5Mn (VDA 260 - MgAl, similar to ASTM AM50), used in the manufacturing of automotive steering wheels via the high pressure die casting process.
Core study:
The core of the study involved producing steering wheels using HPDC with the MgAl5Mn alloy. The resulting castings were then subjected to detailed analysis, including:
- Chemical composition verification.
- Microstructural examination using optical (confocal laser) and electron microscopy (SEM) combined with EDX analysis to identify phases and structure.
- Mechanical property evaluation through tensile testing (strength, yield point, elongation) and hardness measurements.
- Relating the observed microstructure and properties to the HPDC process parameters.
5. Research Methodology
Research Design:
The research employed an experimental approach. Steering wheels were manufactured using industrial HPDC equipment and a specific magnesium alloy (MgAl5Mn). Samples were extracted from these castings for subsequent material characterization to evaluate the influence of the manufacturing process on the final properties.
Data Collection and Analysis Methods:
- Material: Magnesium alloy MgAl5Mn (VDA 260 - MgAl), chemical composition specified in Tab. 3.
- Casting: High pressure die casting (HPDC) on a 400-tonne machine using parameters detailed in Tab. 5 (e.g., plunger velocities, casting temperature 660 °C, pressure 60 MPa, die temperature 200 °C).
- Chemical Analysis: Melt composition monitored by Q4 TASMAN analyzer. Solidified sample composition analyzed by EDX (Energy Dispersive X-ray spectroscopy) - results in Tab. 6, example spectrum Fig. 3a, point analysis Fig. 7.
- Microstructural Analysis: Samples prepared from longitudinal and transverse sections. Analyzed using Confocal Laser Microscopy (Fig. 6) and Scanning Electron Microscopy (SEM) (Fig. 5, Fig. 8).
- Mechanical Testing:
- Tensile tests performed on TIRA test 2300 equipment according to EN ISO 6892-1 (test piece Fig. 2, results Fig. 3b, Tab. 4).
- Hardness tests using Vickers method (HV 0.5) with CSM equipment, measurements spaced 200 microns apart (results Tab. 7).
Research Topics and Scope:
The research focused specifically on the MgAl5Mn alloy (equivalent to ASTM AM50) cast into steering wheel bodies via HPDC. The scope covered:
- Determination of the final chemical composition.
- Characterization of the as-cast microstructure, including grain structure, phase identification (α solid solution, β-phase Mg17Al12 eutectic, intermetallic compounds like Mg8Al2Mn), and morphology.
- Measurement of key mechanical properties: tensile strength (Rm), yield strength (Rp0.2), elongation (A 50 mm), Young's Modulus (E), and Vickers hardness (HV 0.5).
6. Key Results:
Key Results:
- The studied alloy was confirmed as MgAl5Mn (specifically 5.2% Al, 0.30% Mn, Tab. 3), corresponding to VDA 260 - MgAl and ASTM AM50.
- HPDC produced castings with good mechanical properties: Rp0.2 = 127 MPa, Rm = 226 MPa, Elongation A 50 mm = 13.9%, E = 44700 MPa (Tab. 4). Average hardness HV 0.5 was 55.3 (Tab. 7).
- The microstructure consisted of fine grains of α solid solution (magnesium matrix). A less significant netting of divorced eutectic α + β (where β is the intermetallic phase Mg17Al12) was observed around the α grains (Fig. 5, Fig. 6).
- EDX analysis confirmed the composition of the α phase and the eutectic. It also identified the presence of Mn, partly in the intermetallic phase Mg17Al12(Mn) and potentially as Mg8Al2Mn (Fig. 7, Tab. 6). Mn content in the intermetallic phase Mg17Al12(Mn) ranged from 0.2 to 0.6% (Tab. 6).
- The HPDC process, particularly the high pressure (60 MPa, Tab. 5), resulted in a fine-grained, compact structure with minimal internal defects or porosity, contributing to the observed ductility and strength.
- Fracture surfaces observed via SEM showed characteristics typical of the alloy's structure (Fig. 8).
- Fig. 5 Alloy MgAl5Mn with the occurrence of finely branched dark phases (x 500)
- Fig. 6 Structure of the MgAl5Mn alloy was observed in confocal laser mode(b)
- Fig. 6 Structure of the MgAl5Mn alloy was observed in confocal laser mode(a)
- Fig. 7 EDX point analysise of the sample in a) longitudinal and b) transverse Sections of MgAl5Mn alloy
- Fig. 2 Drawing of the test sample and the sample itself for the tensile test
- Fig. 3 Testing casting sample of alloy MgAl5Mn a) ADX analysis of alloy MgAl5Mn b) Static tensile test on the MgAl5Mn test-piece
Figure Name List:
- Fig. 1 Equilibrium diagram Mg-Al (Mg17 All2 in its eutectic phase) and the ternary diagram of Mg-Al-Mn in isothermal section at 400 °C [4]
- Fig. 2 Drawing of the test sample and the sample itself for the tensile test
- Fig. 3 Testing casting sample of alloy MgAl5Mn a) ADX analysis of alloy MgAl5Mn b) Static tensile test on the MgAl5Mn test-piece
- Fig. 4 Body of the steering wheel of alloy EN - MB MgAl5Mn
- Fig. 5 Alloy MgAl5Mn with the occurrence of finely branched dark phases (x 500)
- Fig. 6 Structure of the MgAl5Mn alloy was observed in confocal laser mode
- Fig. 7 EDX point analysise of the sample in a) longitudinal and b) transverse Sections of MgAl5Mn alloy
- Fig. 8 Structures fracture surface alloy MgAl5Mn - SEM (x50, x100)
7. Conclusion:
High pressure die casting (HPDC) of Mg alloys offers significant advantages, producing complex shapes with high dimensional accuracy, fine-grained microstructures, and good mechanical properties. The MgAl5Mn alloy, when processed by HPDC for steering wheels, exhibits these benefits. The resulting structure is characterized by fine grains of α solid solution with a fully divorced eutectic network of α + β (intermetallic phase Mg17Al12). The high solidification speed and pressure (around 60 MPa) inherent to HPDC contribute to this fine structure and ensure material compactness, minimizing defects and porosity. Castings made from MgAl5Mn alloy demonstrate very good mechanical properties, especially the ductility (14% elongation) required for safety-critical components like steering wheels, along with a tensile strength of 226 MPa and a yield strength of 127 MPa.
8. References:
- [1] FRIDRICH, E. H., MORDIKE, L.B.: Magnesium Technology. Springer-Verlag Berlin - Heidelberg 2006, ISBN-10 3-540-20599-3.
- [2] AVEDSIAN, M., IAKER, H.: Magnesium and Magnesium Alloys, ASM Specialty Handbook. ISBN 0-87170-657-1.
- [3] FRIDRICH, H., SCHUMANN, S.: Research for a "new age of magnesium" in the automotive industry, Journal of Material Processing Technology, 117, (2001), p. 276-281.
- [4] RAGHAVAN, V.: Al-Mg-Mn (Aluminum-Magnesium-Manganese) Journal of Phase Equilibrium and Diffusion Vol. 31 No. 1, 2010, p. 46.
- [5] BROWN, J.R.: Foseco Non - Ferrous. Foundryman's Handbook. 11th Butterword, Oxford.
- [6] GUPTA, M., SHARON, N.M.L. Magnesium, Magnesium Alloys, Magnesium Composities. Published by John Wiley in Canada, 2011.
- [7] ŻYDEK, A., KAMIENIAK, J., BRASZCYŇSKA, K.N.: Evolution of Mg-5Al-0.4Mn microstructure after rare earth elements addition. Archives of Foundry Engineering. ISSN (1897-3310), Volume 11, Issue 2/2011 pp. 157 – 160.
- [8] KIELBUS, A., RZYCHOŇ, T., CIBIS, R.: Microstructure of AM50 die casting magnesium alloy. Journal of Achievements in Materials and Manufacturing Engineering. Volume 18, Issue 1-2, September-October 2006.
- [9] ASM Handbooks Online, Volume 2, Properties and Selection: Nonferrous Alloys and Special Purpose Materials.
- [10] MICHNA, Š. Strukturní analýza a vlastnosti předslitiny AlCa10. (Structural analysis and properties pre-alloy AlCa10), Strojírenská technologie, 2010, s. 175-176. (in Czech).
- [11] VOJTĚCH, D., KUBÁSEK, J., VODĚROVÁ, M. Structural, mechanical and in vitro corrosion characterization of as cast magnesium based alloy for temporary biodegradable medicial implants. Manufacturing Technology. Vol. 12, No 13 p. 285-292. ISSN 1213-2489.
- [12] Promotional Materials Comparation training documents. ANDREAS STIHL AG & Company, Germany.
- [13] SLÁDEK, A, FABIAN, P., PASTIRČÁK, R., BREZNIČAN, M.: The Roundness and Microstructure of Thin-wall Bearing Rings. Manufacturing Technology. Vol. 12, No 13 p. 237-241. ISSN 1213-2489.
9. Copyright:
- This material is a paper by "Iva Nová, Jiří Machuta". Based on "Monitoring of the microstructure and mechanical properties of the magnesium alloy used for steering wheel manufacturing".
- Source of the paper: https://doi.org/10.21062/ujep/x.2013/a/1213-2489/MT/13/3/385
This material is summarized based on the above paper, and unauthorized use for commercial purposes is prohibited.
Copyright © 2025 CASTMAN. All rights reserved.