This introductory paper is the research content of the paper ["INDUSTRIAL SCALE DIE FILLING AND THE USE OF SHORT SHOTS TO UNDERSTAND THERMAL AND FLOW EFFECTS"] published by [Fifth International Conference on CFD in the Process Industries, CSIRO].
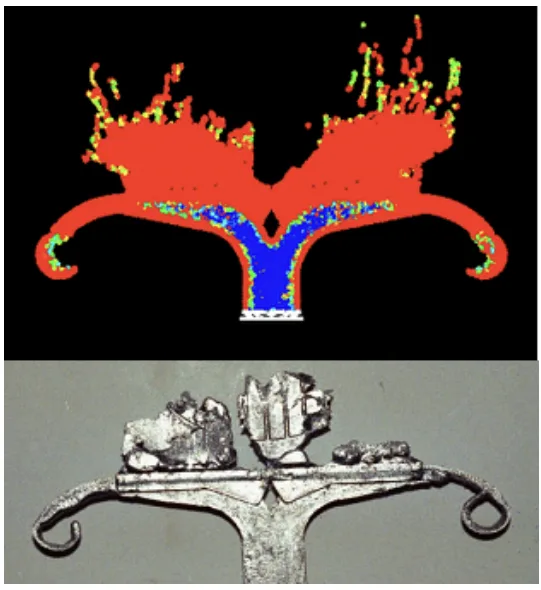
1. Overview:
- Title: INDUSTRIAL SCALE DIE FILLING AND THE USE OF SHORT SHOTS TO UNDERSTAND THERMAL AND FLOW EFFECTS
- Author: Paul W. CLEARY, Joseph HA, Mahesh PRAKASH, and Thang NGUYEN
- Publication Year: 2006
- Published Journal/Society: Fifth International Conference on CFD in the Process Industries
- Keywords: High Pressure Die Casting(HPDC), Smoothed Particle Hydrodynamics(SPH), Short Shots, free surface fragmentation, splashing, solidification, Thermal flow
2. Abstract
The geometric complexity and high fluid speeds involved in High Pressure Die Casting (HPDC) combine to give strongly three dimensional fluid flow with significant free surface fragmentation and splashing. A simulation method that has proved particularly suited to modelling HPDC is Smoothed Particle Hydrodynamics (SPH). Materials are approximated by particles that are free to move around rather than by fixed grids, enabling more accurate prediction of fluid flows involving complex free surface motion. Three practical industrial examples of SPH simulated HPDC flows are presented; aluminium casting of a differential cover (automotive), an electronic housing and zinc casting of a door lock plate. These show significant detail in the fragmented fluid free surfaces.
The validation of flow predictions coupled with heat transfer and solidification is an important area for such modelling. One approach is to use short shots, where insufficient metal is used in the casting or the casting shot is halted part way through to leave the die cavity partially filled. The frozen partial castings capture significant detail of the order of fill and about the flow structures occurring during filling. Validation can occur by matching experimental and simulated short shots. Here we explore the effect of die temperature, metal super-heat and volume fill on the short shots. The bulk features of the final solid castings are found to be in good agreement with the predictions, but the fine details appear to depend on surface behaviour of the solidifying metals.
3. Research Background:
Background of the research topic:
High Pressure Die Casting (HPDC) is a crucial manufacturing process for high-volume, low-cost components in various industries (automotive, household products, electronics). It involves injecting liquid metal (aluminum, magnesium, or zinc) at high speeds (30-100 m/s) and pressures into a die.
Status of previous research:
Previous research has utilized Smoothed Particle Hydrodynamics (SPH) for modeling HPDC. SPH is a Lagrangian (grid-free) method well-suited for simulating complex free surface flows. Prior work includes validation against water analogue experiments and applications to gravity die casting (Ha et al., 1999). Complicated physics such as multiple phases, realistic equations of state, compressibility, solidification, fracturing, porous media flow, electro-magnetics and history dependence of material properties are also easier to implement.
Need for research:
The complex geometry of dies leads to 3D fluid flow with significant fragmentation and splashing. Accurate simulation is needed to optimize die design, filling processes, and to predict and minimize defects like porosity. Validation of simulations, especially considering heat transfer and solidification, is critical.
4. Research purpose and research question:
Research purpose:
To demonstrate the capability of SPH simulations for industrial-scale HPDC, and to investigate the use of short shots for validation, exploring the influence of operating parameters.
Core research:
- How do die temperature, metal superheat, and fill volume affect the characteristics of short shots?
- How well do SPH simulations, including coupled heat transfer and solidification, match experimental short shots?
- Can SPH predict the detail in the filling predictions is high and the last locations to fill correlate well with porosity/voidage observation?
5. Research methodology
The research employs Smoothed Particle Hydrodynamics (SPH) simulations to model the HPDC process.
-Research Design: Computational fluid dynamics (CFD) simulations using the SPH method.
-Data Collection: Three industrial case studies (differential cover, electronic housing, door lock plates) were simulated. Short shot experiments were conducted using a thin-walled coaster casting.
-Analysis Method: Comparison of simulated filling patterns and final short shot shapes with experimental results. The effects of varying die temperature, metal superheat, and fill volume were analyzed.
-Research Scope: The study focuses on the filling stage of HPDC, including heat transfer and solidification effects. The simulations are fully coupled thermal and flow solutions.
6. Key research results:
Key research results and presented data analysis:
- SPH simulations captured the complex, fragmented flow patterns in the three industrial examples, showing details like jetting, backfilling, and void formation.
- Short shot simulations showed good agreement with experiments for the bulk features of the castings.
- The simulations and experiments revealed that the early stages of filling, especially near the gate, are highly sensitive to surface effects (potentially surface tension or oxide skin formation).
- Metal superheat and die temperature significantly influenced the short shot characteristics. Lower superheat and die temperature led to more rapid solidification and reduced fragmentation.
- A hypothesis was proposed that the bursting of a solid skin forming over the gate during runner filling could explain the observed variability in experimental short shots.
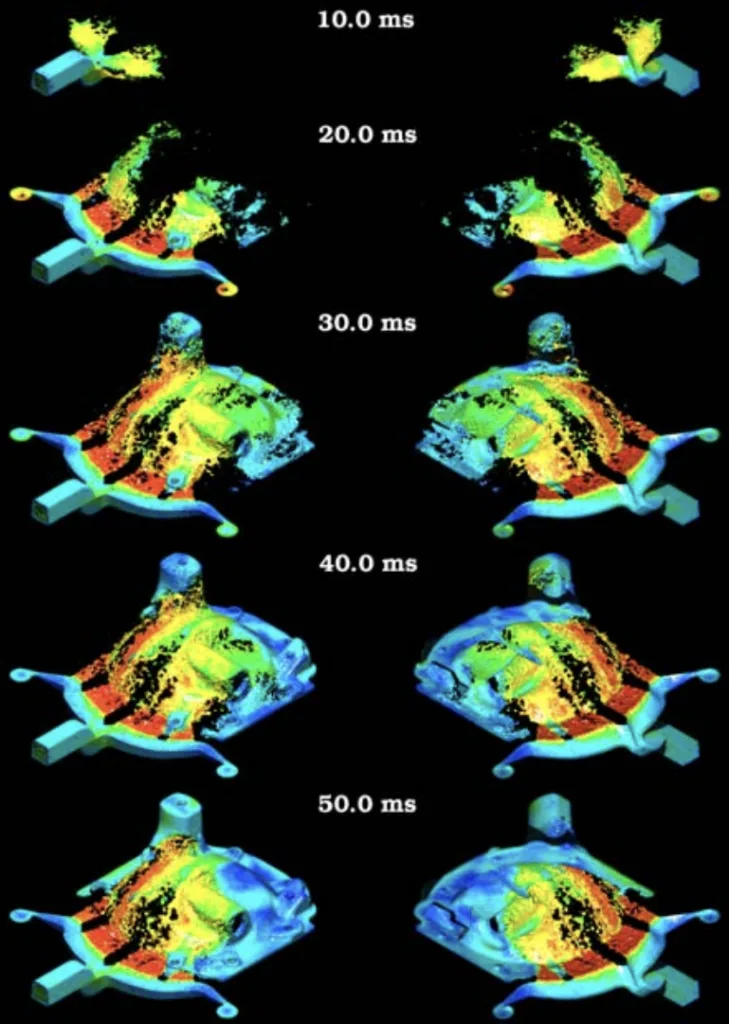
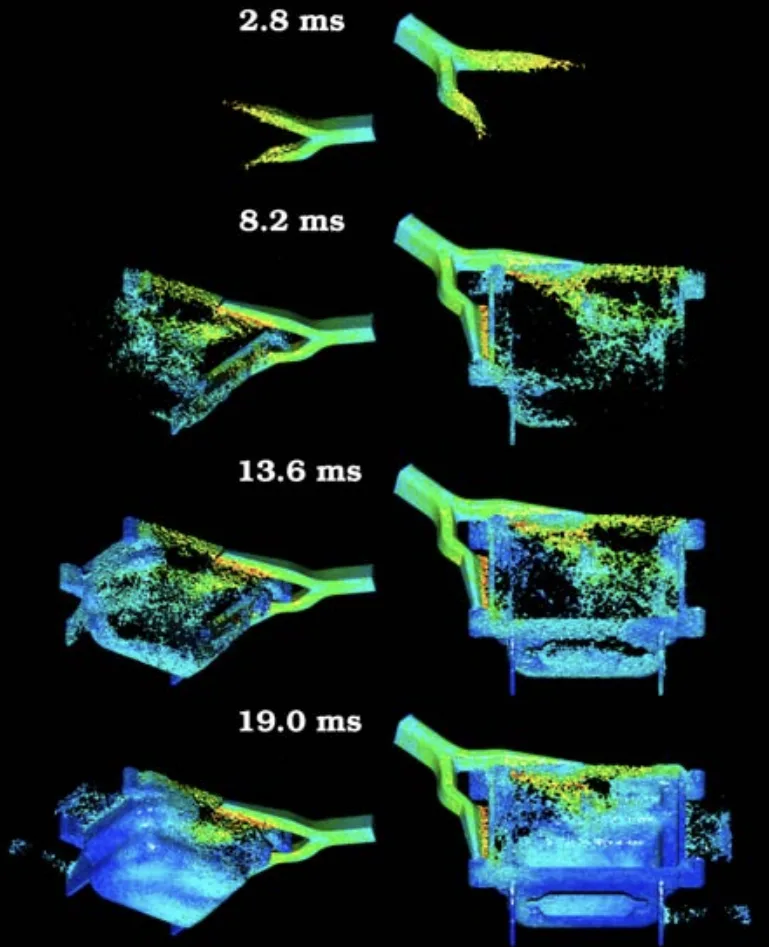
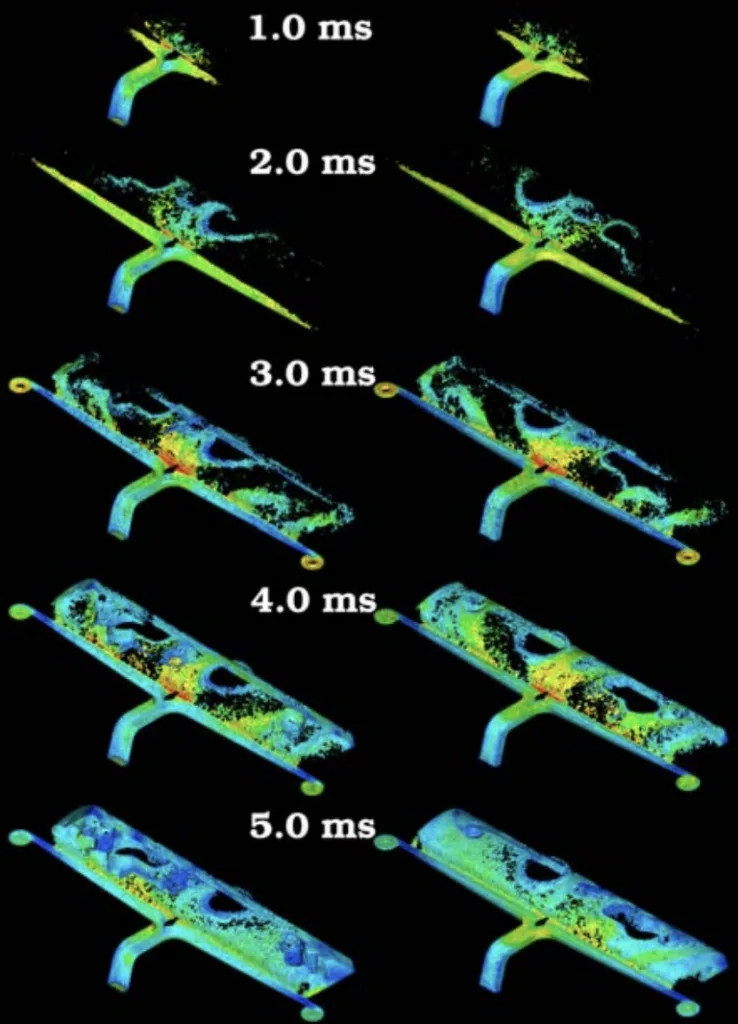
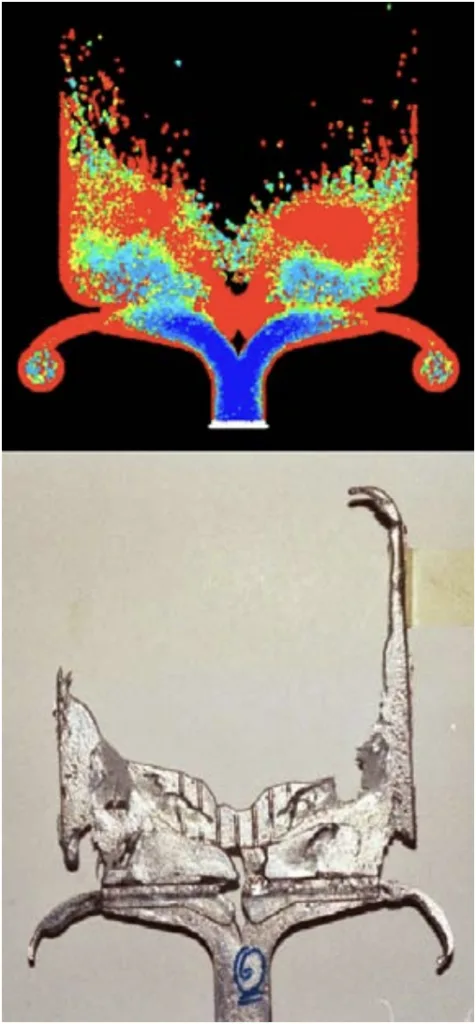
List of figure names:
- Figure 1: Filling of differential cover with the fluid coloured by speed with blue being slow and red being fast.
- Figure 2: An electronic housing filled from a Y shaped runner (coloured by speed).
- Figure 3: Filling by zinc of the front and back plates of a door lock (coloured by speed).
- Figure 4: Filling of coaster (including heat transfer and solidification) with fluid coloured by temperature.
- Figure 5: Short shot with 25% volume fill: (top), simulation (bottom) experiment. For TDIE = 27°C and metal super-heat TAL = 0°C.
- Figure 6: Short shot with 10% volume fill: (top), simulation (bottom) experiment. For TDIE = 27°C and metal super-heat TAL = -10°C.
- Figure 7: Short shot variation for a 10% fill with different initial metal temperatures (degree of super-heat) a) TAL = +10°C, b) 0°C, c) -10°C, d) -15°C, e) -20°C and f) the actual short shot.
- Figure 8: Short shot variation for a 10% fill for different initial die temperatures, a) 127°C, b) 77°C, c) 27°C and d) the actual short shot. The degree of super-heat in all cases is TAL-10 C/ 580 С.
7. Conclusion:
Summary of key findings:
SPH simulations successfully modeled the complex filling process in industrial HPDC examples. Short shots provide valuable data for validation, but their fine details are influenced by surface phenomena that are not fully captured by current models. The variability in experimental short shots may be due to the formation and bursting of solid skins at the gate.
- Academic significance: The research demonstrates the potential of SPH for simulating complex HPDC flows and highlights the need for incorporating surface effects (surface tension, oxide formation) into the models.
- Practical implications: The findings suggest that controlling the formation of solid skins at the gate could be crucial for reducing variability in HPDC. This has implications for die design, process control, and the development of more accurate simulation models.
8. References:
- CLEARY, P.W., (1998), “Modelling confined multi-material heat and mass flows using SPH", Applied Mathematical Modelling, 22, 981-993.
- CLEARY, P.W. AND HA, J., (1999). "Three dimensional modelling of high pressure die casting", Proc. 2nd Int. Conf. on CFD in Minerals & Process Industries, Melbourne, Australia
- CLEARY, P.W., HA, J., AND AHUJA, V., (2000), "High pressure die casting simulation using smoothed particle hydrodynamics”, Int. J. Cast Metals Research, 12, 335-355.
- CLEARY, P.W., HA, J., PRAKASH, M. AND NGUYEN, T., (2004), "3D SPH Flow Predictions and Validation for High Pressure Die Casting of Automotive Components", Applied Mathematical Modelling, 30, 1406-1427.
- CLEARY, P.W. AND MONAGHAN, J.J., (1999), "Conduction modelling using smoothed particle hydrodynamics", J. Comp. Phys., 148, 227--264.
- HA, J. AND CLEARY, P.W., (2000), “Comparison of SPH simulations of high pressure die casting with the experiments and VOF simulations of Schmid and Klein", Int. J. Cast Metals Research, 12, 409-418.
- HA, J., CLEARY, P. W., ALGUINE, V. AND NGUYEN, T., (1999), “Simulation of die filling in gravity die casting using SPH and MAGMAsoft", Proc. 2nd Int. Conf. on CFD in Minerals and Process Industries, Melbourne, Australia, 423-428.
- MONAGHAN, J.J., (1992), "Smoothed particle hydrodynamics", Annual Review of Astronomy and Astrophysics, 30, 543-574.
- MONAGHAN, J.J., (1994), "Simulating free surface flows with SPH", J. Computational Physics., 110, 399-406.
- THORPE, W., CLEARY, P. HA, J., STOKES, N., AHUJA, V., AND JAHEDI, M., (1999), “Simulation of fluid flow within the die cavity in high pressure die casting using smooth particle hydrodynamics", Proc. 20th Int. Die Casting Congress and Exposition, 23-36.
9. Copyright:
- This material is a paper by "[Paul W. CLEARY, Joseph HA, Mahesh PRAKASH, and Thang NGUYEN]": Based on "[INDUSTRIAL SCALE DIE FILLING AND THE USE OF SHORT SHOTS TO UNDERSTAND THERMAL AND FLOW EFFECTS]".
- Source of paper: [Paper not provided DOI URL]
This material was created to introduce the above paper, and unauthorized use for commercial purposes is prohibited. Copyright © 2025 CASTMAN. All rights reserved.