FuchuLiuabSuoTubXiaolongGongbGuanjinLibWenmingJiangbXinwangLiubZitianFanb
aSchool of Mechanical Engineering and Electronic Information, China University of Geosciences, Wuhan, 430074, China
bState Key Laboratory of Materials Processing and Die & Mould Technology, Huazhong University of Science and Technology, Wuhan, 430074, China
Highlights
- A high-strength water-soluble composite KNO3-20 mol% KCl salt core material was successfully fabricated.
- Bauxite and glass-fiber powder were added and acted as reinforcer.
- The strengthening-toughening mechanisms of the salt core material was revealed.
- A hollow-structure zinc alloy component was casting using the developed salt core material.
Abstract
The water-soluble salt core material has been successfully used for manufacturing hollow aluminum and magnesium alloy castings. However, there is rare report about the water-soluble salt core being used for lower melting point and higher density hollow zinc alloy castings. In order to obtain a high-performance composite water-soluble salt core material (CWSSC) which is suitable for manufacturing hollow-structure zinc alloy castings via high pressure die casting process, the comparative study on performance and microstructure of the salt cores fabricated by gravity casting technology was investigated using KNO3 and KCl as the base salt material with the reinforcements of bauxite or glass-fiber powder. The results show that CWSSC strengthened by reinforcements possesses many advantages of good surface quality and water-solubility rate, high bending strength and impact toughness, low shrinkage and moisture-absorption rate, and CWSSC composed of KNO3-20 mol% KCl with 15 wt% bauxite powder and 15 wt% glass-fiber powder has the better comprehensive performance, whose surface roughness is 0.4758 μm, bending strength is 46.6 MPa, impact toughness is 21.72 kJ/m2, and water-solubility rate is 178.21 kg/(min·m2) in still water at 80 °C with relatively low shrinkage and 24 h moisture-absorption rate. The scanning electron microscope analysis shows that the strengthening-toughening mechanisms of CWSSC mainly include refinement of the grain and deflection of the crack caused by KCl dendritic crystal and the rigid enhanced powders. A practical casting test has been conducted to prove that the developed CWSSC can be used to manufacture hollow-structure zinc alloy castings.
고압 다이캐스팅 공정을 통한 아연 합금 주조, 중력 주조 기술로 제작된 염심의 성능 및 미세 구조에 대한 비교 연구는 보크사이트 또는 유리 섬유 분말의 보강과 함께 기본 염 재료로 KNO3와 KCl을 사용하여 조사되었습니다.
그 결과, 보강재로 강화된 CWSSC는 우수한 표면 품질 및 수용성, 높은 굽힘 강도 및 충격 인성, 낮은 수축률 및 흡습율, 15wt%의 KNO3-20mol% KCl로 구성된 CWSSC의 많은 장점을 가지고 있음을 보여줍니다.
보크사이트 분말 및 15wt% 유리 섬유 분말은 표면 거칠기가 0.4758μm, 굽힘 강도가 46.6MPa, 충격 인성이 21.72kJ/m2, 수용성 비율이 178.21kg/(min·m2인 더 나은 종합 성능을 가지고 있습니다.
80°C의 정수에서 상대적으로 수축이 적고 24시간 수분 흡수율이 있습니다. 주사 전자 현미경 분석은 CWSSC의 강화 강화 메커니즘이 주로 KCl 수지상 결정 및 강성 강화 분말로 인한 균열의 편향 및 결정립의 미세화를 포함함을 보여줍니다.
개발된 CWSSC가 중공 구조의 아연 합금 주물을 제조하는 데 사용할 수 있음을 증명하기 위해 실제 주조 테스트가 수행되었습니다.
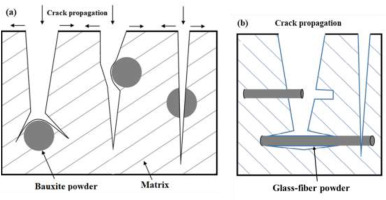
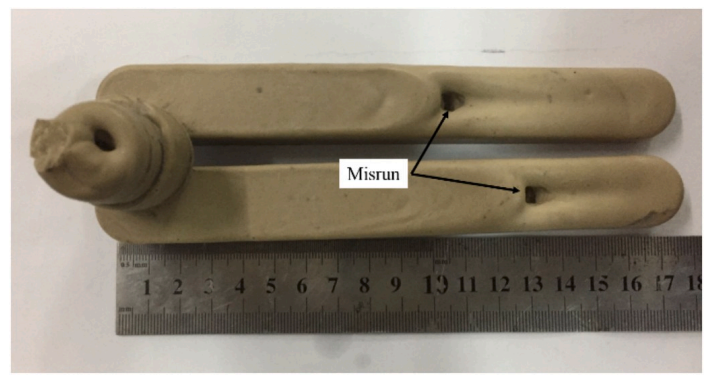
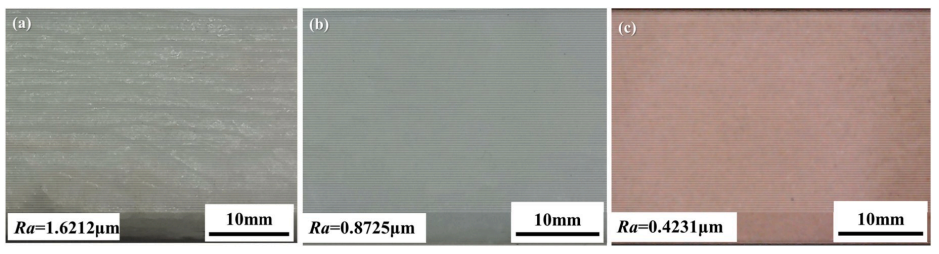
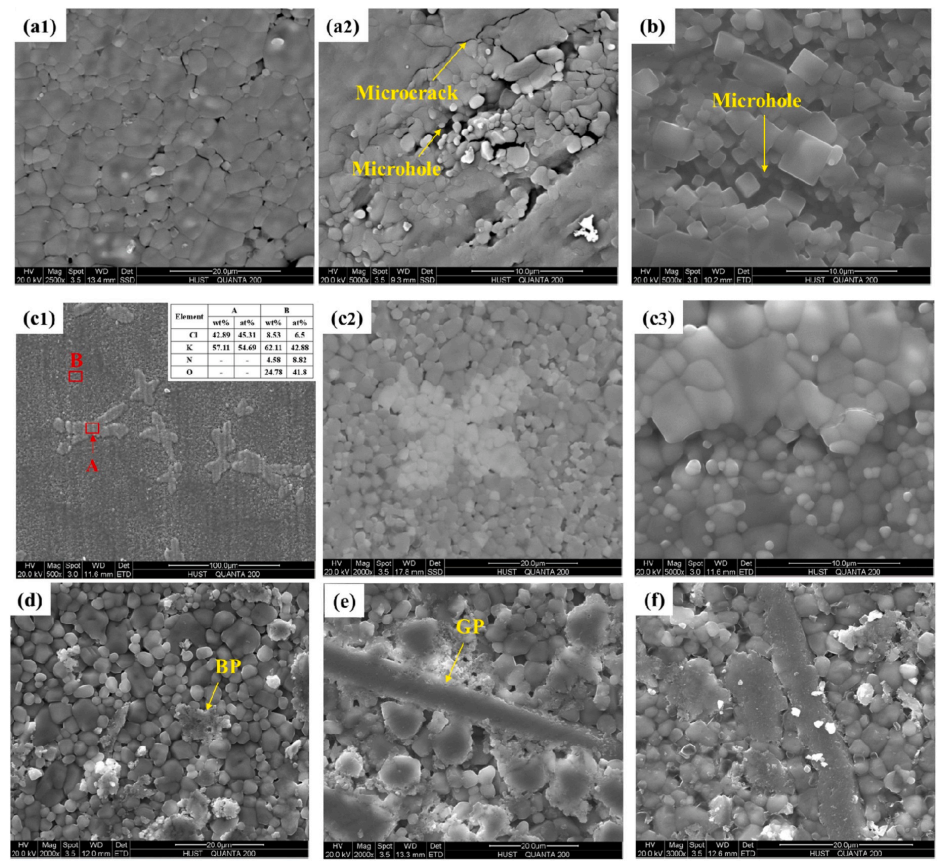
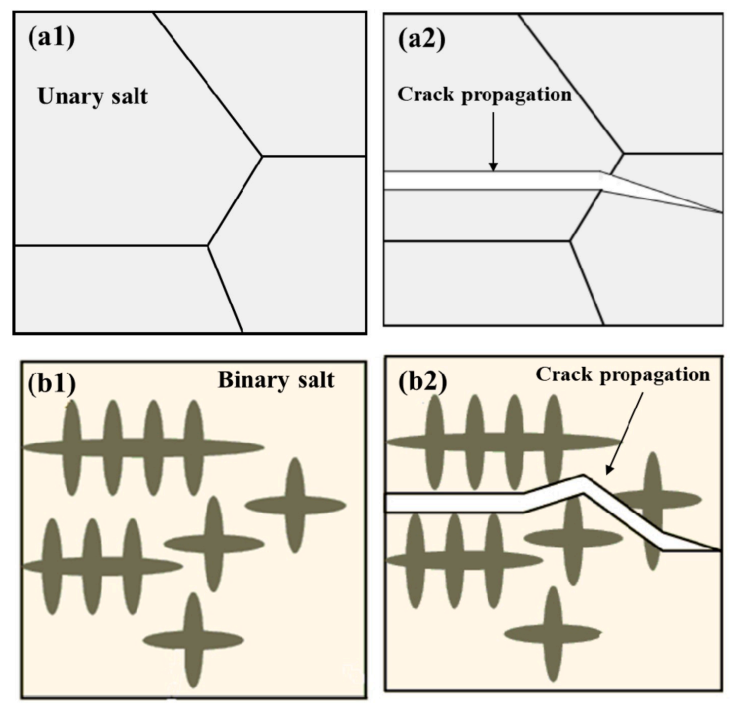
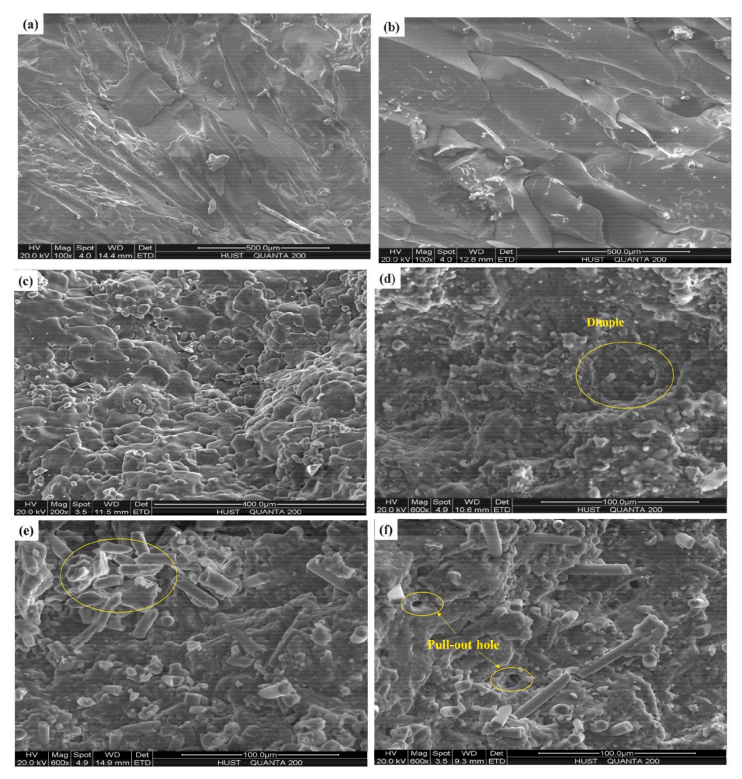
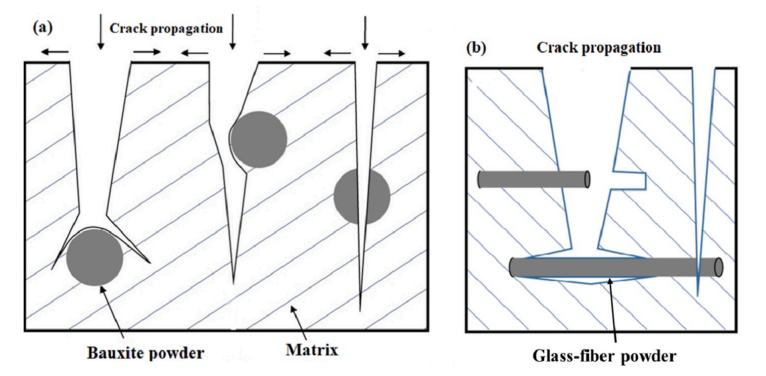
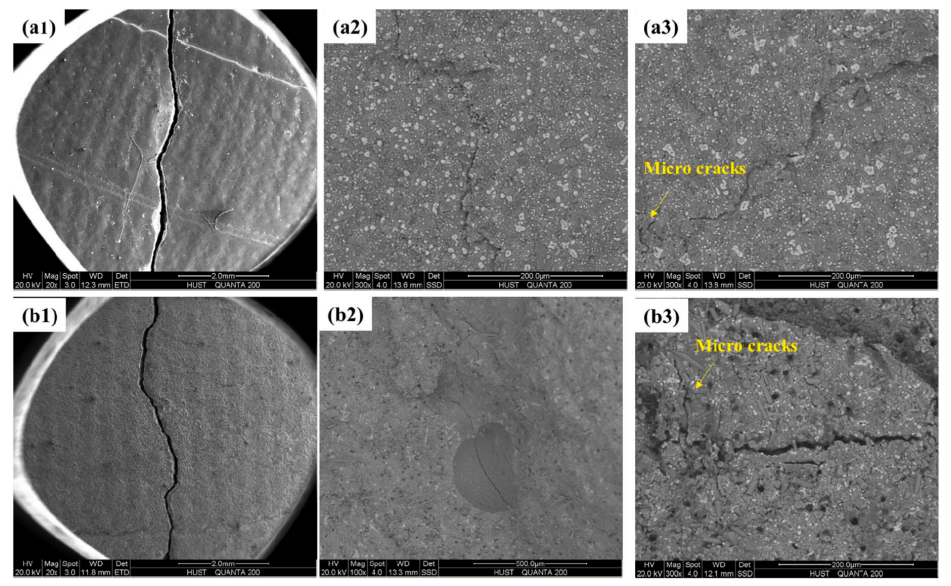
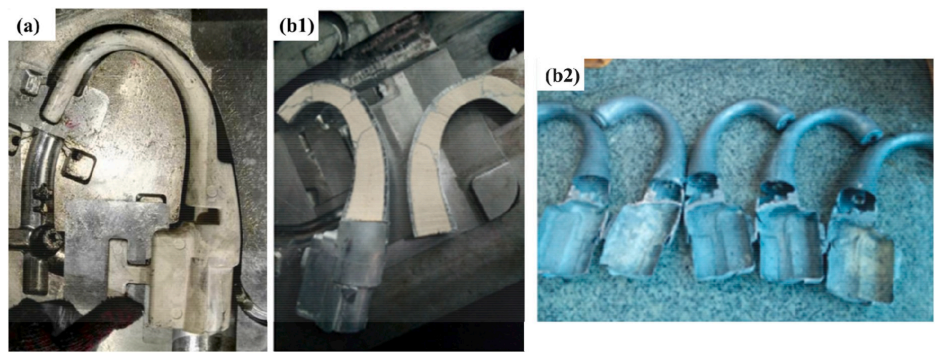
References
[1] L. Cao, D.M. Liao, F. Sun, et al., Prediction of gas entrapment defects during zinc
alloy high-pressure die casting based on gas-liquid multiphase flow model, Int. J.
Adv. Manuf. Technol. 94 (1–4) (2018) 807–815.
[2] X.X. Dong, H.L. Yang, X.Z. Zhu, et al., High strength and ductility aluminium alloy
processed by high pressure die casting, J. Alloys Compd. 773 (2019) 86–96.
[3] H. Abdizadeh, M. Ashuri, P.T. Moghadam, et al., Improvement in physical and
mechanical properties of aluminum/zircon composites fabricated by powder
metallurgy method[J], Mater. Des. 32 (8–9) (2011) 4417–4423.
[4] H. Heshmati, M. Ketabchi, A. Kalaki, et al., Production of globular microstructure
of A356 aluminium alloy by cooling channel and strain induced melt activation
processes: morphological and hardness studies[J], Int. J. Cast Metals Res. 26 (2)
(2013) 100–104.
[5] W.J. Ding, P.H. Fu, L.M. Peng, Advanced magnesium alloys and their applications
in aerospace, Spacecraft environment engineering 28 (2011) 103–109 (in Chinese).
[6] S.M. Dobosz, P. Jelinek, K. Major-Gabrys, Development tendencies of moulding
and core sands, China Foundry (4) (2011) 438–446, 08.
[7] P. Jelínek, E. Adamkov
a, F. Miksovský, et al., Advances in technology of soluble
cores for die castings, Arch. Foundry Eng. 15 (2) (2015) 29–34.
[8] Z. Xiao, L.T. Harper, A.R. Kennedy, et al., A water-soluble core material for
manufacturing hollow composite sections, Compos. Struct. 182 (2017) 380–390.
[9] F.C. Liu, L. Yang, Y. Huang, et al., Performance of resin bonded sand for
magnesium alloy casting [J], J. Manuf. Process. 30 (2017) 313–319.
[10] L. Zhang, L.N. Zhang, Y. Li, Effect of kaolin on tensile strength and humidity
resistance of a water-soluble potassium carbonate sand core, China Foundry 13 (1)
(2016) 15–21.
[11] W.G. Jiang, J.S. Dong, L.H. Lou, Preparation and properties of a novel water
soluble core material, J. Mater. Sci. Technol. 26 (2010) 270–275.
[12] M. Ramegowda, Development of Water-Based Core Technology for Light Alloys,
University of Teesside, 2008.
[13] F.C. Liu, P. Jiang, Y. Huang, et al., A water-soluble magnesium sulfate bonded sand
core material for manufacturing hollow composite castings, Compos. Struct. 201
(2018) 553–560.
[14] P. Jiang, F.C. Liu, Z.T. Fan, et al., Performance of water-soluble composite sulfate
sand core for magnesium alloy castings, Arch. Civ. Mech. Eng. 16 (3) (2016)
494–502.
[15] Z.L. Lu, G.Q. Tian, W.J. Wan, et al., Effect of in situ synthesised mullite whiskers on
the high-temperature strength of Al2O3-based ceramic moulds for casting hollow
turbine blades, Ceram. Int. 42 (16) (2016) 18851–18858.
[16] Z.F. Gao, B.Q. Wang, J. Yin, et al., Corrosion behavior of alumina-based ceramic
core materials in caustic alkali solutions, Int. J. Appl. Ceram. Technol. 16 (1)
(2019) 335–345.
[17] Youji Yamada, Method of Manufacturing Expendable Salt Core for Casting, 2013-
11-05. US8574476B.
[18] Youji Yamada, Shizuoka, Method of Manufacturing Expendable Salt Core for
Casting: US2011/0062624A1, 2011-04-17.
[19] Groezinger Dieter, Water-soluble salt cores for die casting, 2008-02-14.
US20080035294 A1.
[20] Donahue R J, Degler M T. Congruent melting salt alloys for use as salt cores in high
pressure die casting: U.S. Patent 9878367. 2018-1-30.
[21] M. Renzo, Method for Producing Pressure Die-Cast or Injection Molded Articles
Using Salt Cores, 2002-10-1. US: 6458297B2.
[22] H. Koji, Gumma, Disintegrative Core for High Pressure Casting, Method for
Manufacturing the Same and Method for Extracting the Same, 2004-6-29. US:
6755238B1.
[23] Yuji Hori, Nahiro Miura, Yutaka Kurokawa, et al., Water-soluble Casting Mold and
Method for Manufacturing the Same, 2004-12-02. US20040238157A1.
[24] J.E. Hoffman Jr., Sr R.A. Hoffman, Foundry Mixture and Related Methods for
Casting and Cleaning Cast Metal Parts: US Patent 9963799, 2018-5-8.
[25] Hirokawa K. Disintegrative Core for High Pressure Casting, Method for
Manufacturing the Same, and Method for Extracting the Same: US Patent 6755238.
2004-6-29.
[26] Grebe D E, Potratz M P. Disintegrative core for use in die casting of metallic
components: U.S. Patent 7013948. 2006-3-21.
[27] T.M. Cleary, K.R. Anderson, R.J. Donahue, et al., Slides and expendable cores for
high pressure die cast closed deck engine block, US Patent Application 15453148,
2019-1-29.
[28] S. Zhang, J. Cornie, S. Cornie, Soluble Casting Core for Metal Matrix Composite
Components and Method of Producing Thereof, US Patent Application 11124512,
2006-11-12.
[29] K. Anzai, K. Oikawa, Y. Yamada, Method for Producing Salt Core for Casting, US
Patent Application 13318386, 2012-3-1.
[30] L. Wan, P.C. Xu, J.R. Luo, Properties and forming characters of water soluble saltcore reinforced by ceramic whiskers, Foundry 57 (3) (2008) 234–238 (in Chinese).
[31] W.P. Chen, H.W. Zheng, Progress in research on water soluble salt core used for
high-pressure casting, Foundry Technol. 31 (2) (2010) 241–244 (in Chinese).
[32] J. Yaokawa, K. Anzai, Y. Yamada, et al., Castability and strength of potassium
chloride-ceramic composite salt cores, J. Jpn. Foundry Eng. Soc. 76 (10) (2004)
823–829.
[33] J. Beno, E. Ad
amkova, F. Miksovský, et al., Development of composite salt cores for
foundry applications[J], Mater. Technol. 49 (4) (2015) 619–623.
[34] J. Yaokawa, D. Miura, K. Anzai, et al., Strength of salt core composed of alkali
carbonate and alkali chloride mixtures made by casting technique[J], Mater. Trans.
48 (5) (2007) 1034–1041.
[35] F.E. Goodwin, Zinc and Zinc Alloys, Springer Handbook of Materials Data.
Springer, Cham, 2018, pp. 431–442.
[36] R. Huang, B. Zhang, Study on the composition and properties of salt cores for zinc
alloy die casting [J], Int. J. Metalcast. 11 (3) (2017) 440–447.
[37] Z.T. Fan, S. Tu, F.C. Liu, et al., China: 201611186722, High Strength Composite
Salt Core Material for Low Melting Point Alloy Casting and its Preparation Method
[P], vol. 6, 2016-12-20 (in Chinese).
[38] S. Tu, F.C. Liu, G.J. Li, et al., Fabrication and characterization of high-strength
water-soluble composite salt core for zinc alloy die castings [J], Int. J. Adv. Manuf.
Technol. 95 (1–4) (2018) 505–512.
[39] S. Tu, Z.T. Fan, F.C. Liu, et al., Preparation and properties of a binary composite
water-soluble salt core for zinc alloy by die casting, Chin. J. Eng. 39 (11) (2017)
1692–1698 (in Chinese).
[40] G.Q. Liu, L.X. Ma, L J, Handbook of Substances Properties Data in Chemical and
Engineering (Inorganic Vol), Chemical Industry Press, Beijing, 2012.
[41] http://www.crct.polymtl.ca/fact/phase_diagram.php?file¼KCl-KNO3.jp
g&dir¼FTsalt.
[42] F.C. Liu, Z.T. Fan, X.W. Liu, et al., Research on humidity resistance of sodium
silicate sand hardened by twice microwave heating process, Mater. Manuf. Process.
29 (2) (2014) 184–187.
[43] F.C. Liu, Z.T. Fan, X.W. Liu, et al., Effect of surface coating strengthening on
humidity resistance of sodium silicate bonded sand cured by microwave heating,
Mater. Manuf. Process. 31 (12) (2016) 1639–1642.
[44] F.C. Liu, Z.T. Fan, X.W. Liu, et al., Aqueous gel casting of water-soluble calciabased ceramic core for investment casting using epoxy resin as a binder, Int. J. Adv.
Manuf. Technol. 86 (5–8) (2016) 1235–1242.