This introductory paper is the research content of the paper ["Novel Magnesium Based Materials: Are They Reliable Drone Construction Materials? A Mini Review"] published by [Frontiers in Materials].
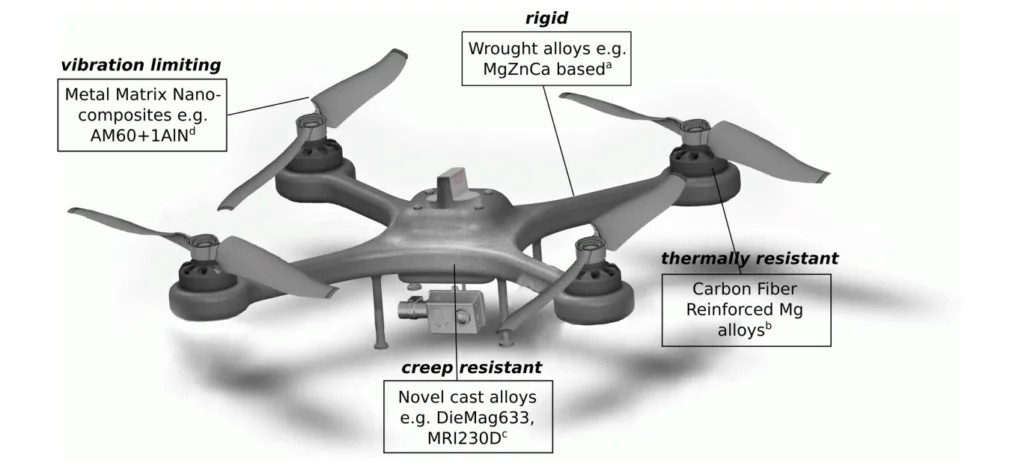
1. Overview:
- Title: Novel Magnesium Based Materials: Are They Reliable Drone Construction Materials? A Mini Review
- Author: Daniel Höche, Wolfgang E. Weber, Eugen Gazenbiller, Sarkis Gavras, Norbert Hort, Hajo Dieringa
- Publication Year: 2021
- Publishing Journal/Academic Society: Frontiers in Materials
- Keywords: ultra-lightweight construction, hybrid design, magnesium alloy, aerial vehicle, urbane mobility
2. Abstracts / Introduction
Novel magnesium-based materials are presented as ideal candidates for future aviation vehicles due to their lightweight nature, which can significantly enhance vehicle range. These materials exhibit excellent castability, are easily machinable, and can be formed into profiles or forgings for next-generation aerial vehicle construction. High-pressure die casting of magnesium alloys is highlighted as superior to aluminum alloys for large quantities of identical components, attributed to lower iron solubility in magnesium, extending tool and casting life, and approximately 30% shorter die filling times due to lower density. Cost-effective novel die casting alloys like DieMag633 or MRI230D, offering superior specific strength at both room and elevated temperatures, are noted alongside wrought alloys such as AZ31 and emerging Mg-Zn-Ca based alloys with improved formability. While magnesium alloys' susceptibility to environmental influences is acknowledged, the paper indicates that suitable coatings and novel corrosion protection concepts under development may mitigate these concerns. The mini-review introduces a paradigm shift towards utilizing new magnesium materials in drone construction, discussing future applications in next-generation aerial vehicles and suggesting possible research topics.
3. Research Background:
Background of the Research Topic:
Lightweight materials, particularly magnesium and its alloys, are of significant interest across various industrial sectors, including automotive, civil engineering, battery technology, and medical implants. Prior research has extensively explored the application of magnesium-based materials in vehicle designs, demonstrating the feasibility of functionalizing magnesium alloys. This context motivates the investigation into novel magnesium-based materials for constructing vehicle components, specifically for quadcopters and next-generation aerial vehicles, contingent upon meeting technical and economic criteria.
Status of Existing Research:
Current drone construction predominantly utilizes composite materials, such as sandwich panels with fiberglass, graphite fiber, or aramid-based skins and polymer foams as core materials, established within the aviation sector. Examples include CFRP-based designs in City-Airbus, Lilium-Jet, and Volocopter. However, the paper points out the potential for new magnesium alloys like DieMag633, MRI230D, Mg-Zn-Ca based alloys, magnesium foams and high strength AM60 + 1AIN nanocomposites, especially for manned aerial vehicles (MAVs) and air-taxis, which could be expensive and environmentally unfriendly if conventionally designed. The DJI Inspire 2 UAV, featuring an AZ91 housing, and DJI Mavic Air, using AZ91-based brackets, exemplify initial magnesium applications in aerial vehicles. Phantom 4 Pro V2.0 utilizes a titanium-magnesium hybrid structure for airframe rigidity.
Necessity of the Research:
The pursuit of ultra-lightweight drones is a primary objective in drone development. Conventional materials like CFRP can lead to flexible structures requiring additional measures to limit deformations. Magnesium alloys offer a potential alternative, promising enhanced rigidity and potentially improved acoustic emission profiles. Concerns regarding corrosion in magnesium alloys are addressed by the development of novel corrosion protection concepts, suggesting that these concerns may be less critical than perceived under expected in-service exposure conditions. Furthermore, ecological footprint and social acceptance of materials in drone design are important considerations, where magnesium alloys present a potentially favorable profile compared to CFRP in terms of recyclability and carbon footprint.
4. Research Purpose and Research Questions:
Research Purpose:
This mini-review aims to introduce the paradigm change of utilizing novel magnesium materials as drone construction material and to discuss future fields of applications within next-generation aerial vehicles, both manned and unmanned. It also seeks to address possible research topics in this area.
Key Research:
The key research questions implicitly addressed in this review are:
- Can novel magnesium-based materials offer a reliable alternative to existing materials in drone construction?
- What are the advantages of using magnesium alloys compared to aluminum alloys and composite materials in drone applications, particularly in high-pressure die casting and structural components?
- How can the challenges associated with magnesium alloys, such as corrosion susceptibility, be mitigated for aerial vehicle applications?
- What are the potential future research directions and applications for magnesium alloys in next-generation aerial vehicles?
5. Research Methodology
Research Design:
This paper is designed as a mini-review, synthesizing existing literature and knowledge on magnesium alloys and their potential application in drone construction. It adopts a descriptive approach, outlining the properties of magnesium alloys, comparing them to alternatives, and discussing their suitability for various drone components.
Data Collection Method:
The data collection method involves reviewing and referencing existing research and publications in the fields of materials science, aerospace engineering, and drone technology. The authors draw upon prior studies, technical reports, and industry examples to support their arguments and assessments.
Analysis Method:
The analysis method is qualitative, involving comparative analysis of material properties, manufacturing processes, and application requirements. The authors assess the advantages and disadvantages of magnesium alloys in the context of drone construction, considering factors such as weight, strength, castability, corrosion resistance, and environmental impact. The review also incorporates examples of existing drone designs and historical applications of magnesium in aircraft to illustrate the potential and feasibility of magnesium alloy usage.
Research Subjects and Scope:
The research subject is novel magnesium-based materials and their application in aerial vehicle construction, specifically drones. The scope is focused on evaluating the potential of magnesium alloys as structural materials for various drone components, comparing them with conventional materials like aluminum alloys and composites. The review considers both die-cast and wrought magnesium alloys and discusses their suitability for different parts of unmanned and manned aerial vehicles.
6. Main Research Results:
Key Research Results:
- Magnesium alloys are ideal for future aviation vehicles due to their low density, enhancing vehicle range.
- High-pressure die casting of magnesium alloys is superior to aluminum for large-scale production due to longer tool life and faster die filling times (approximately 30% shorter).
- Novel die casting alloys (DieMag633, MRI230D) and wrought alloys (AZ31, Mg-Zn-Ca based alloys) offer improved specific strength and formability.
- Magnesium alloys can replace various drone components, including fuselage, wings, tails, and rotor blade housings.
- Magnesium Metal Matrix Nano-composites (MMNC's) show excellent properties with small ceramic nanoparticle additions, increasing both mechanical strength and ductility.
- Magnesium alloys offer advantages in vibration damping and rigidity, potentially improving acoustic emission profiles and crash-worthiness.
- Novel corrosion protection concepts mitigate corrosion concerns for magnesium alloys in drone applications.
- Magnesium alloys are more easily recyclable compared to CFRP, with a comparable carbon footprint to aluminum.
Analysis of presented data:
The paper presents material selection charts (Figure 1) based on Ashby methodology, comparing Mg alloys, Al alloys, Ti alloys, and Composites in terms of:
- (A) Stiffness-limited design: Young's modulus vs. Density, showing Mg alloys positioned favorably for light-weight/stiffness-limited applications.
- (B) Strength-limited design: Strength vs. Density, again indicating Mg alloys' competitiveness.
- (C) Safe design: Fracture toughness vs. Elastic limit, highlighting Mg alloys' suitability for safe design considerations.
- (D) Economical/ecological constraints: Product of mechanical parameters (Stiffness, Strength, Fracture toughness) vs. Product of non-physical properties (Price, CO2 footprint, Recycling fraction), suggesting a balanced profile for Mg alloys.
Figure 2 illustrates potential applications of Mg-based alloys/hybrid materials in a quadcopter, categorizing material requirements for different components:
- Vibration limiting: Metal Matrix Nano-composites e.g. AM60+1AIN for vibration-sensitive parts.
- Rigid: Wrought alloys e.g. MgZnCa based for structural rigidity.
- Creep resistant: Novel cast alloys e.g. DieMag633, MRI230D for components requiring creep resistance.
- Thermally resistant: Carbon Fiber Reinforced Mg alloys for thermal stability.
Figure Name List:
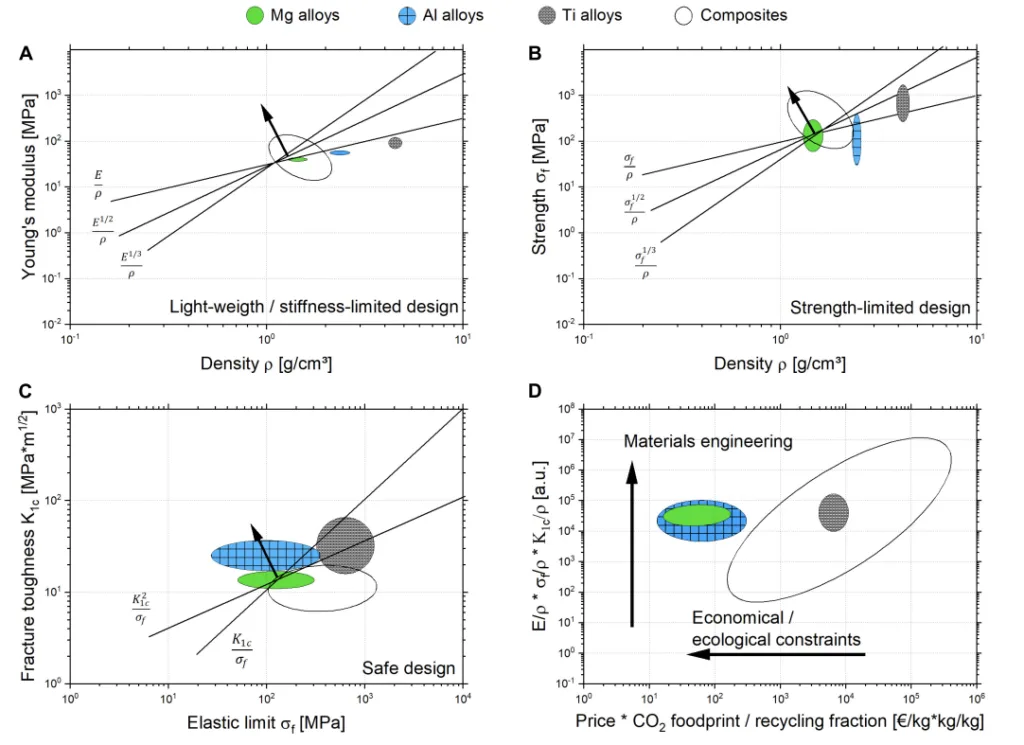
- FIGURE 1 | Materials selection following Ashby for aerospace applications
- FIGURE 2 | Possible Mg-based alloys/hybrid materials for application in aerial vehicle construction like a quadcopter
7. Conclusion:
Summary of Key Findings:
The review concludes that magnesium-based materials are highly promising for drone construction, particularly when high rigidity and noise reduction are critical. Magnesium alloys offer economic advantages in drone construction, potentially enhanced by techniques like UHPC die hydroforming. Compared to CFRP, magnesium alloys are more readily recyclable. The authors assert that magnesium is a viable drone construction material, emphasizing its lightweight, castability, and improved properties in novel alloys.
Academic Significance of the Study:
This mini-review contributes to the academic field by consolidating information on the potential of magnesium alloys in aerospace, specifically drone construction. It highlights the material's advantages and addresses common concerns, providing a concise overview for researchers and engineers in materials science and aerospace engineering. The paper also points out the need for further research and development in magnesium alloy applications for aerial vehicles.
Practical Implications:
The practical implications are significant for the drone manufacturing industry. The review suggests that adopting magnesium alloys can lead to lighter, more efficient drones with improved performance and potentially lower environmental impact due to recyclability. The discussion of specific alloys and manufacturing techniques provides actionable insights for engineers considering magnesium in drone design and manufacturing.
Limitations of the Study and Areas for Future Research:
As a mini-review, this paper is limited in scope and depth compared to a comprehensive study. It primarily outlines the potential of magnesium alloys without in-depth experimental validation or detailed case studies. Areas for future research include:
- Further investigation into novel magnesium alloy development tailored for drone-specific requirements.
- Experimental validation of magnesium alloy performance in drone components under various operational conditions.
- Development and optimization of corrosion protection strategies for magnesium alloys in aerial environments.
- Research into efficient joining technologies for magnesium-based drone structures.
- Life cycle assessments comparing magnesium-based drones with those made from other materials to quantify environmental and economic benefits.
- Exploration of additive manufacturing techniques for magnesium drone parts.
8. References:
- American Aviation (1955). American Aviation. 14, 58-60.
- Arjomandi, M., Agostino, S., Mammone, M., Nelson, M., and Zhou, T. (2006). Classification of Unmanned Aerial Vehicles. Report for Mechanical Engineering class. Adelaide: University of Adelaide.
- Arnold, S. M., Cebon, D., and Ashby, M. (2012). Materials Selection for Aerospace Systems. Tech. Rep. 2012-217411, NASA/TM. Washington, D.C: NASA.
- Ashby, M. F. (2010). Materials Selection in Mechanical Design. Oxford: Butterworth-Heinemann.
- Beck, A. (1939). Magnesium Und Seine Legierungen (in German), 2 Edn. Berlin: Springer.
- Brooke-Holland, L. (2012). Unmanned Aerial Vehicles (drones): an Introduction. London: House of Commons Library.
- Czerwinski, F. (2014). Overcoming barriers. Adv. Mat. Proc. 5, 28-31.
- Dalamagkidis, K. (2015). "Classification of UAVs," in Handbook of Unmanned Aerial Vehicles, eds K. P. Valavanis and G. J. Vachtsevanos (Berlin: Springer), 83-91. doi: 10.1007/978-90-481-9707-1_94
- Deng, M., Höche, D., Lamaka, S. V., Snihirova, D., and Zheludkevich, M. L. (2018). Mg-Ca binary alloys as anodes for primary Mg-air batteries. J. Power Sourc. 396, 109-118. doi: 10.1016/j.jpowsour.2018.05.090
- Dieringa, H. (2011). Properties of magnesium alloys reinforced with nanoparticles and carbon nanotubes: a review. J. Mater. Sci. 46, 289-306. doi: 10.1007/s10853-010-5010-6
- Dieringa, H., and Bohlen, J. (2016). Magnesiumlegierungen im Leichtbau. Nachhaltige Konstruktion 10, 24-25.
- Dieringa, H., and Kainer, K. (2009). Technologische Eigenschaften und Potential von Magnesium-legierungen (in German). Gießerei-Rundschau 56, 114-119.
- Dieringa, H., and Kainer, K. U. (2013). Die Leichtbauwerkstoffe für den Fahrzeugbau (in German). Wiesbaden: Springer Fachmedien Wiesbaden, 199-442.
- Dieringa, H., Bohlen, J., Hort, N., Letzig, D., and Kainer, K. U. (2007). "Advances in manufacturing processes for Magnesium alloys," in Magnesium Technology 2007 (TMS), eds R. S. Beals, A. A. Luo, N. R. Neelameggham, and M. O. Pekguleryuz (TMS The Minerals, Metals and Materials Society), 3-8.
- Dieringa, H., Hort, N., and Kainer, K.-U. (2004). Magnesium based MMCss reinforced with C-fibers. Adv. Tehnol. Mater. Mater. Process. J. 6, 136-141.
- Dieringa, H., Hort, N., Letzig, D., Bohlen, J., Höche, D., Blawert, C., et al. (2018). "Mg Alloys: Challenges and Achievements in Controlling Performance, and Future Application Perspectives," in Magnesium Technology 2018. TMS 2018. The Minerals, Metals & Materials Series, eds D. Orlov, V. Joshi, K. Solanki, and N. Neelameggham (Cham: Springer).
- Dieringa, H., Katsarou, L., Buzolin, R., Szakacs, G., Horstmann, M., Wolff, M., et al. (2017). Ultrasound assisted casting of an AM60 based metal matrix nanocomposite, its properties, and recyclability. Metals 7:388. doi: 10.3390/met7100388
- Dong, P. A. V., Azzaro-Pantel, C., and Cadene, A.-L. (2018). Economic and environmental assessment of recovery and disposal pathways for cfrp waste management. Resour. Conserv. Recycl. 133, 63-75. doi: 10.1016/j.resconrec.2018.01.024
- DOW (1941). Application of Magnesium Alloys on the Junckers ju-88 Bomber. The DOW chemical report. Midland, MI: The DOW Chemical Company, 11373.
- Ehrenberger, S. (2020). Carbon Footprint of Magnesium Production and its Use in Transport Applications, Update of Life Cycle Assessment of Magnesium Components in Vehicle Construction. Available online at: https://elib.dlr.de/140926/1/2020-10-30_IMA_LCA-Study_Report_Update.pdf (accessed March 8, 2021).
- Ehrenberger, S., Dieringa, H., and Fridrich, H. (2013). Life Cycle Assessment of Magnesium Components in Vehicle Construction. Available online at: https://elib.dlr.de/87332/1/2013-12_IMA_LCA-Study_Report_Part-I-and-II_incl-summary.pdf (accessed June 22, 2020).
- Fahlstrom, P., and Gleason, T. (2012). Introduction to UAV systems. Hoboken, NJ: John Wiley & Sons.
- Gavras, S., Zhu, S., Easton, M. A., Gibson, M. A., and Dieringa, H. (2019). Compressive creep behavior of high-pressure die-cast aluminum-containing magnesium alloys developed for elevated temperature applications. Front. Mater. 6:262. doi: 10.3389/fmats.2019.00262
- Goh, G., Agarwala, S., Goh, G., Dikshit, V., Sing, S. L., and Yeong, W. Y. (2017). Additive manufacturing in unmanned aerial vehicles (uavs): challenges and potential. Aerosp. Sci. Technol. 63, 140-151. doi: 10.1016/j.ast.2016.12.019
- Hallion, R. P. (2017). "Germany and the invention of the all-metal cantilever airplane, 1915-1925: a historical review," in Proceedings of the 55th AIAA Aerospace Sciences Meeting, (Reston, VA: AIAA).
- Höche, D., Lamaka, S. V., Vaghefinazari, B., Braun, T., Petrauskas, R. P., Fichtner, M., et al. (2018). Performance boost for primary magnesium cells using iron complexing agents as electrolyte additives. Sci. Rep. 8:7578.
- Jenkins, D. R. (2001). Magnesium Overcast: The Story of the Convair B-36. Thurgoona: Specialty Press.
- Kirkland, N. T. (2012). Magnesium biomaterials: past, present and future. Corros. Eng. Sci. Technol. 47, 322-328. doi: 10.1179/1743278212y.0000000034
- Kleiner, M., Curbach, M., Tekkaya, A. E., Ritter, R., Speck, K., and Trompeter, M. (2008). Development of ultra-high performance concrete dies for sheet metal hydroforming. Prod. Eng. 2, 201-208. doi: 10.1007/s11740-008-0099-z
- Kucharczyk, A., Naplocha, K., Kaczmar, J. W., Dieringa, H., and Kainer, K. U. (2017). Current Status and Recent Developments in Porous Magnesium Fabrication. Adv. Eng. Mater. 20:1700562. doi: 10.1002/adem.201700562
- Lamaka, S. V., Höche, D., Petrauskas, R. P., Blawert, C., and Zheludkevich, M. L. (2016). A new concept for corrosion inhibition of magnesium: suppression of iron re-deposition. Electrochem. Commun. 62, 5-8. doi: 10.1016/j.elecom.2015.10.023
- Lilium (2018). Simplicity was Our Most Complicated Goal. Lilium-Technology. Available online at: https://lilium.com/technology/ (accessed June 22, 2020).
- Luthringer, B. J., Feyerabend, F., and Willumeit-Romer, R. (2014). "Magnesium-based implants: a mini-review. Magnes. Res. 27, 142-154. doi: 10.1684/mrh.2015.0375
- Malaki, M., Xu, W., Kasar, A. K., Menezes, P. L., Dieringa, H., Varma, R. S., et al. (2019). Advanced metal matrix nanocomposites. Metals 9:330. doi: 10.3390/met9030330
- Marker, T. (2013). Evaluating the Flammability of Various Magnesium Alloys During Laboratory-and Full-Scale Aircraft Fire Test. New Jersey, NY: US Department of Transportation..
- Megson, T. H. G. (2016). Aircraft Structures for Engineering Students. Oxford: Butterworth-Heinemann.
- Mouritz, P. A. (2007). Review of z-pinned composite laminates. Compos. Part A Appl. Sci. Manuf. 38, 2383-2397. doi: 10.1016/j.compositesa.2007.08.016
- Naghdi, F., Kang, J., and Kim, H. (2016). Microstructure and high-temperature mechanical properties of the mg-4zn-0.5ca alloy in the as-cast and aged conditions. Mater. Sci. Eng. A 649, 441-448. doi: 10.1016/j.msea.2015.10.011
- Ostrowsky, I., and Henn, Y. (2007). "Present state and future of magnesium application in aerospace industry," in Proceeding of the International Conference "New Challenges in Aeronautics", (India: ASTEC).
- Pan, H., Ren, Y., Fu, H., Zhao, H., Wang, L., Meng, X., et al. (2016). Recent developments in rare-earth free wrought magnesium alloys having high strength: a review. J. Alloys Compd. 663, 321-331. doi: 10.1016/j.jallcom.2015.12.057
- Reed, S. A. (1925). Aeronautical Propeller. US Patent, No. 1,542,412.
- Rittmeier, L., Losch, T., Sinapius, M., and Lammering, R. (2018). Investigation on the influence of material interfaces and impedance changes on the propagation of guided waves in laminated steel layers. Procedia Manuf. 24, 196-202. doi: 10.1016/j.promfg.2018.06.039
- Rothert, H., and Gensichen, V. (1987). Nichtlineare Stabstatik (in German). Berlin: Springer.
- Scott, R. C., Bartels, R. E., Funk, C. J., Allen, T. J., Sexton, B. W., Dykman, J. R., et al. (2016). Aeroservoelastic test of the subsonic ultra-green aircraft research truss-braced wing model. J. Guid. Control Dyn. 39, 1820-1833. doi: 10.2514/1.g000265
- Sun, J., Guan, Q., Liu, Y., and Leng, J. (2016). Morphing aircraft based on smart materials and structures: a state-of-the-art review. J. Intell. Mater. Syst. Struct. 27, 2289-2312. doi: 10.1177/1045389x16629569
- Timmis, A. J., Hodzic, A., Koh, L., Bonner, M., Soutis, C., Schafer, A. W., et al. (2015). Environmental impact assessment of aviation emission reduction through the implementation of composite materials. Int. J. Life Cycle Assess. 20, 233-243. doi: 10.1007/s11367-014-0824-0
- Tu, T., Chen, X.-H., Chen, J., Zhao, C.-Y., and Pan, F.-S. (2019). A high-ductility Mg-Zn-Ca magnesium alloy. Acta Metall. Sin. 32, 23-30.
- Weibel, R., and Hansman, R. J. (2004). "Safety considerations for operation of different classes of UAVs in the nas," in Proceedings of the AIAA 4th Aviation Technology, Integration and Operations (ATIO) Forum (Reston, VA: AIAA).
- Xianhua, C., Yuxiao, G., and Fusheng, P. (2016). Research progress in magnesium alloys as functional materials. Rare Metal Mater. Eng. 45, 2269-2274. doi: 10.1016/s1875-5372(17)30015-2
- You, S., Huang, Y., Kainer, K. U., and Hort, N. (2017). Recent research and developments on wrought magnesium alloys. J. Magnes. Alloys 5, 239-253. doi: 10.1016/j.jma.2017.09.001
9. Copyright:
- This material is "Höche, Daniel; Weber, Wolfgang E.; Gazenbiller, Eugen; Gavras, Sarkis; Hort, Norbert; Dieringa, Hajo"'s paper: Based on "Novel Magnesium Based Materials: Are They Reliable Drone Construction Materials? A Mini Review".
- Paper Source: https://doi.org/10.3389/fmats.2021.575530
This material was created to introduce the above paper, and unauthorized use for commercial purposes is prohibited.
Copyright © 2025 CASTMAN. All rights reserved.