This article introduces the paper 'Applicability of high strength thread forming Aluminum bolts in magnesium power train components' published by '9th European All-Wheel Drive Congress Graz'.
1. Overview:
- Title: Applicability of high strength thread forming Aluminum bolts in magnesium power train components
- Author: Gerhard Gerstmayr, Philipp Oberhuber, Thomas Jakob, Heinz Leitner
- Publication Year: 2009
- Publishing Journal/Academic Society: 9th European All-Wheel Drive Congress Graz
- Keywords: Aluminum thread forming bolts, magnesium, power train components, mechanical properties, creep, relaxation, corrosion behaviour, bolted joint.
![Figure 1. Tightening process in pre-cast core hole of AZ91 with TAPTITE2000® M8x EN AW 6056 T6 (a); with
TAPTITE2000® M8 EN AW 7075 T6 (b) [8]](https://castman.co.kr/wp-content/uploads/image-1165-1024x383.webp)
2. Abstracts or Introduction
Abstract
"Aluminum thread forming bolts in combination with
magnesium clamping parts in power train components
offer a high potential to save costs and weight. This
paper discusses the applicability of high strength thread
forming bolts in magnesium nut materials focused
on mechanical properties of the aluminum bolt and
the Mg-nut material, creep and relaxation as well as
corrosion behaviour of the bolted joint."
Introduction
"The current state of technology for fastening magnesium
power train components is the use of metric steel or
aluminum bolts. Due to physical and chemical properties
of the used materials, difficulties like high clamping load
loss at elevated temperatures and strong corrosive
attack which requires costly corrosion protection
systems must be taken into account. The objective of
this paper is the development and to evaluate a high
strength thread forming aluminum bolt for magnesium
components regarding mechanical properties,
relaxation and corrosion behavior. Benefits of this bolt
connection system are weight reduction in comparison
to steel bolts, lower loss of clamping load, less contact
corrosion and cost reduction by using thread forming
technology (elimination of drilling and thread cutting
operations).
Power train components such as gear boxes are
currently manufactured predominantly from aluminum
alloys. The pressure to reduce CO2 emissions forces
OEMs and suppliers to reduce the weight of vehicles.
One option for doing so is to replace aluminum alloys
with magnesium alloys. However magnesium requires
the fastening technology to be adapted - especially
with regard to corrosion and relaxation."
3. Research Background:
Background of the Research Topic:
Current fastening solutions for magnesium power train components predominantly utilize metric steel or aluminum bolts. However, these conventional methods encounter challenges such as significant clamping load loss at elevated temperatures and susceptibility to corrosive attack. These issues necessitate complex and costly corrosion protection systems. The automotive industry's drive to reduce CO2 emissions and vehicle weight is pushing for the replacement of aluminum alloys with lighter magnesium alloys in power train components like gear boxes. This shift demands an adaptation of fastening technologies, particularly concerning corrosion and relaxation performance in magnesium applications.
Status of Existing Research:
Existing applications of aluminum bolts in automotive predominantly employ machined threads, typically using alloys EN AW 6056 (AlSi1MgCuMn) and EN AW 6013 (AlMg1Si0,8CuMn). Thread forming aluminum bolts, however, require higher strength characteristics due to the resistance of the nut material during thread formation, especially in die casted core holes with high thread coverage. Current standards and publications primarily address machined metric nut threads in conjunction with metric ISO threads, neglecting the specific considerations for thread forming in magnesium.
Necessity of the Research:
This research is necessitated by the need to develop and evaluate high-strength thread forming aluminum bolts specifically tailored for magnesium components. This approach aims to achieve weight reduction compared to steel bolts, minimize clamping load loss, reduce contact corrosion, and realize cost savings through thread forming technology by eliminating drilling and thread cutting operations. A comprehensive evaluation of mechanical properties, relaxation behavior, and corrosion resistance is crucial to validate the applicability of this fastening solution in demanding power train environments.
4. Research Purpose and Research Questions:
Research Purpose:
The primary research purpose is "the development and to evaluate a high strength thread forming aluminum bolt for magnesium components regarding mechanical properties, relaxation and corrosion behavior."
Key Research:
This paper focuses on assessing the "applicability of high strength thread forming bolts in magnesium nut materials" with a specific emphasis on:
- Mechanical properties of the aluminum bolt.
- Mechanical properties of the magnesium nut material.
- Creep and relaxation characteristics of the bolted joint.
- Corrosion behaviour of the bolted joint.
Research Hypotheses:
While not explicitly stated as formal hypotheses, the research operates under the implicit assumption that "Thread forming high-strength aluminum bolts used for magnesium alloys provide considerable potential for reducing cost and weight". The study aims to validate this potential by demonstrating acceptable performance in mechanical properties, relaxation, and corrosion resistance.
5. Research Methodology
Research Design:
The research employs an experimental design involving comparative testing of different material combinations and conditions. The study investigates the performance of thread forming aluminum bolts in various magnesium die-cast alloys under static and dynamic loading, elevated temperatures, and corrosive environments.
Data Collection Method:
Data was collected through a series of controlled experiments, including:
- Tightening process analysis: Measuring torque and clamping load during bolt tightening until failure.
- Static bolting tests: Evaluating tightening properties of bolts in different heat treatment conditions and core hole sizes.
- Relaxation tests: Assessing clamping load loss over time at elevated temperatures (120°C) under both static and pulsating service loads.
- Corrosion tests: Conducting salt spray tests (ISO 9227:2006) for 720 hours to evaluate galvanic corrosion and stress crack corrosion resistance.
Analysis Method:
The collected data was analyzed using:
- Comparative analysis: Comparing the performance of different aluminum bolt alloys (EN AW 6056 T6, EN AW 7075 T6, EN AW 7075 T79) and magnesium alloys (AZ91, AE44, MRI153) across various tests.
- Metallographic investigations: Examining bolt and nut threads to understand failure mechanisms and material behavior during tightening.
- Extrapolation techniques: Using creep models (Norton) to extrapolate relaxation test data to longer durations (4000 hours).
- Statistical analysis: Assessing the influence of heat treatment, core hole size, and loading conditions on bolt performance.
Research Subjects and Scope:
The research focused on:
- Materials: Magnesium die cast alloys AZ91, AE44, and MRI153; Aluminum alloys EN AW 6056 (AlSi1MgCuMn) T6, EN AW 7075 (AlZn5,5MgCu) T6 and T79.
- Fasteners: TAPTITE2000® M8 thread forming aluminum bolts in different heat treatment conditions (T6, T79, FTR, FHT).
- Test Parameters: Temperature (room temperature, 120°C), static and pulsating loads, salt spray corrosion environment, varying core hole tolerances (LCT, UCT).
- Scope: Applicability of high strength thread forming aluminum bolts in magnesium power train components, specifically addressing mechanical performance, relaxation, and corrosion.
6. Main Research Results:
Key Research Results:
- Material Strength and Tightening: EN AW 7075 T6 bolts exhibited higher failure torque compared to EN AW 6056 T6 bolts due to superior material strength. EN AW 7075 T6 also provided a larger available torque range for clamping load build-up.
- Heat Treatment and Tightening: EN AW 7075 T79 demonstrated suitability for over-elastic tightening due to a better balance of strength and ductility, achieving comparable clamping loads to T6 at both lower and upper core hole tolerance limits, with a significantly larger tear-off angle.
- Relaxation Behavior: At 120°C, Mg-alloy AE44 showed significantly better relaxation properties than AZ91, retaining higher clamping loads over time. EN AW 7075 T79 bolts exhibited less clamping load drop compared to T6 bolts. Bolts with final heat treatment (FHT) showed lower relaxation rates than those with final thread rolling (FTR).
- Pulsating Service Load: Superimposed pulsating service loads at 120°C resulted in slightly higher relaxation rates compared to static loading for AE44. However, AZ91 showed significant deterioration in relaxation behavior under pulsating loads.
- Corrosion Resistance: Aluminum bolts (EN AW 6056 and EN AW 7075) demonstrated better galvanic corrosion behavior compared to steel bolts in combination with magnesium, except for steel bolts used with aluminum cup washers which showed similar corrosion performance to aluminum bolts. Stress crack corrosion was observed in EN AW 7075 T6 bolts under specific conditions (stainless steel clamping component) but not in Al-Mg structures representative of the investigated application.
Analysis of presented data:
- Figure 1: Illustrates the tightening process, showing that EN AW 7075 T6 bolts achieve higher torque and clamping load before failure compared to EN AW 6056 T6. The forming torque is lower for EN AW 7075 T6.
- Figure 2: Compares the mechanical properties of EN AW 7075 in T6 and T79 conditions, highlighting the trade-off between strength and ductility. T6 has higher strength, while T79 has higher breaking elongation.
- Figure 3: Shows the influence of heat treatment (T6 vs. T79) and core hole tolerance (LCT vs. UCT) on tightening characteristics of EN AW 7075 bolts. T79 exhibits a larger tear-off angle, especially at UCT.
- Figure 4 & 5: Depict the relaxation behavior of AZ91 and AE44 at 120°C. AE44 shows a slower relaxation rate and higher remaining clamping load after extended time. Extrapolation to 4000 hours (Figure 5) further emphasizes the superior long-term performance of AE44.
- Figure 6: Demonstrates the impact of heat treatment condition and production sequence on relaxation in MRI153. T79 bolts and FHT bolts show improved relaxation resistance compared to T6 and FTR bolts.
- Figure 8, 9 & 10: Illustrate the influence of pulsating service load on relaxation. Figures 9 and 10 (logarithmic scale) highlight the initial clamping load drop during heat-up phase under dynamic load, especially for AZ91.
- Figure 11 & 12: Show corrosion attack on magnesium flange and aluminum bolts (EN AW 6056 and EN AW 7075) after 720 hours of salt spray test. Both aluminum bolts exhibit considerable corrosion.
- Figure 13 & 14 & 15: Show corrosion attack for steel bolts with different protection systems. Steel bolt with aluminum cup washer (Figure 13) shows minimal corrosion, while zinc flake coated and sealed steel bolt (Figure 15) shows significant corrosion on magnesium.
- Figure 16 & 17: Show bolted joints prepared for stress crack corrosion and galvanic corrosion testing.
- Table 1: Lists the bolt systems tested in the salt spray test, detailing bolt type, material, coating, and additional protection.
Figure Name List:

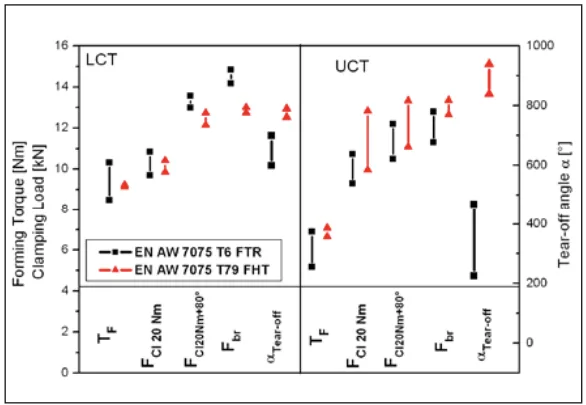
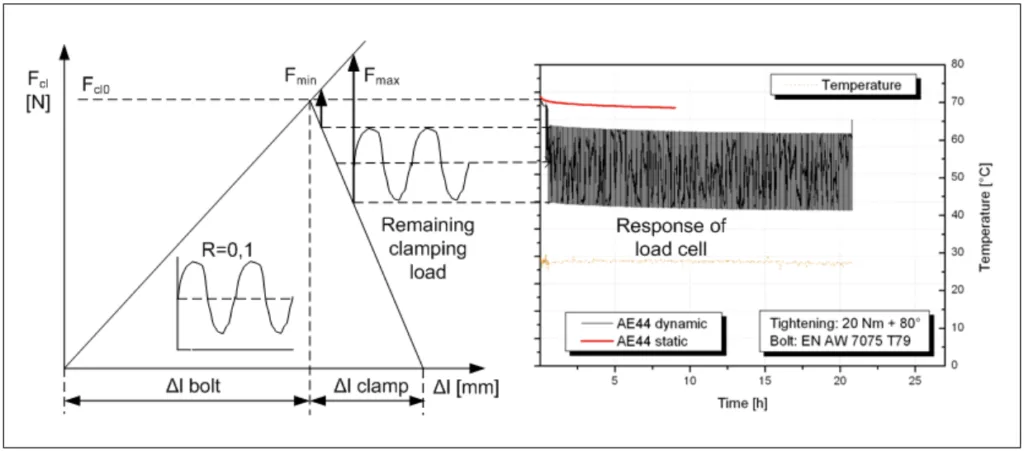
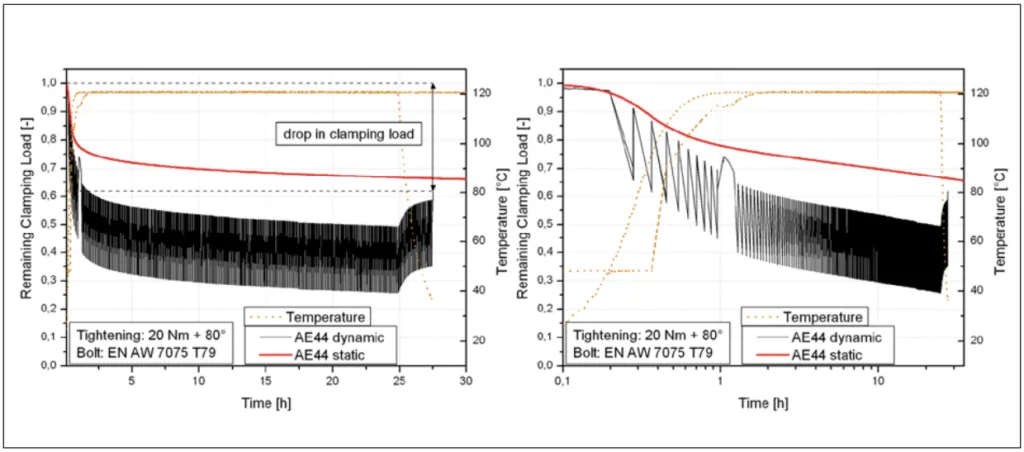
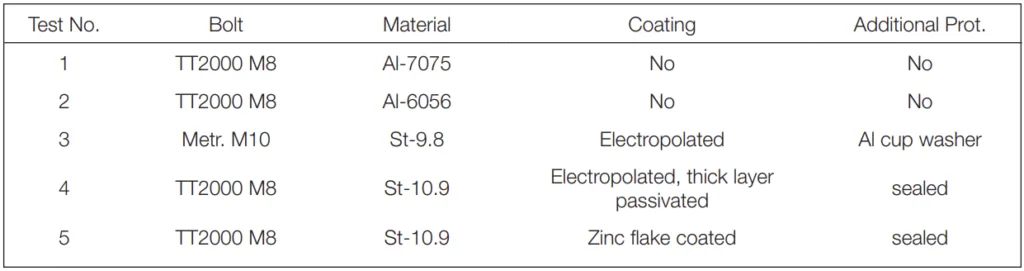
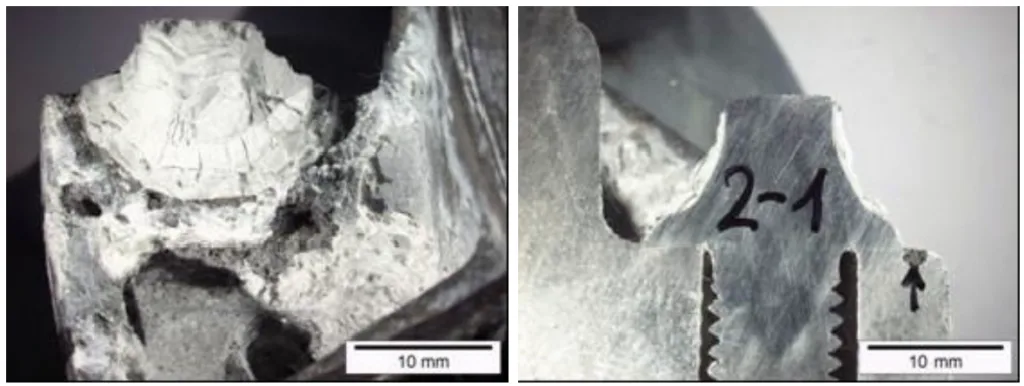
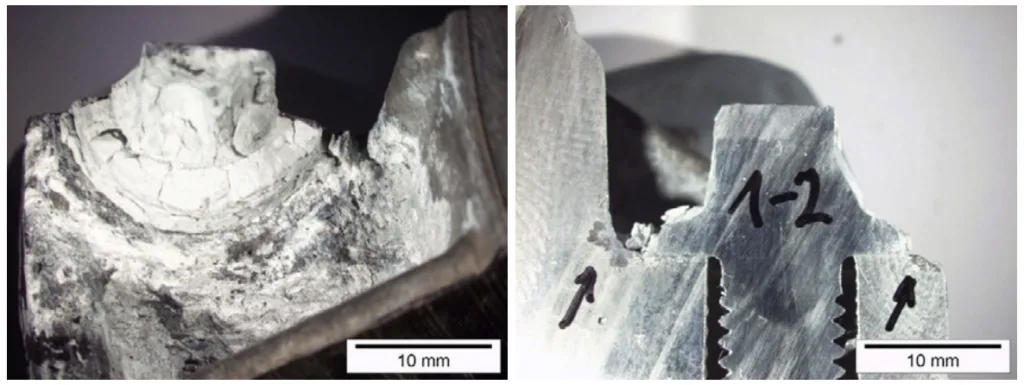
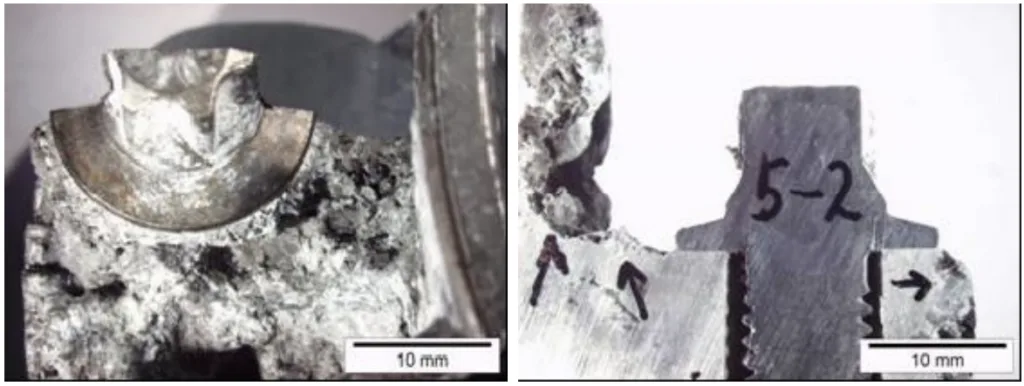
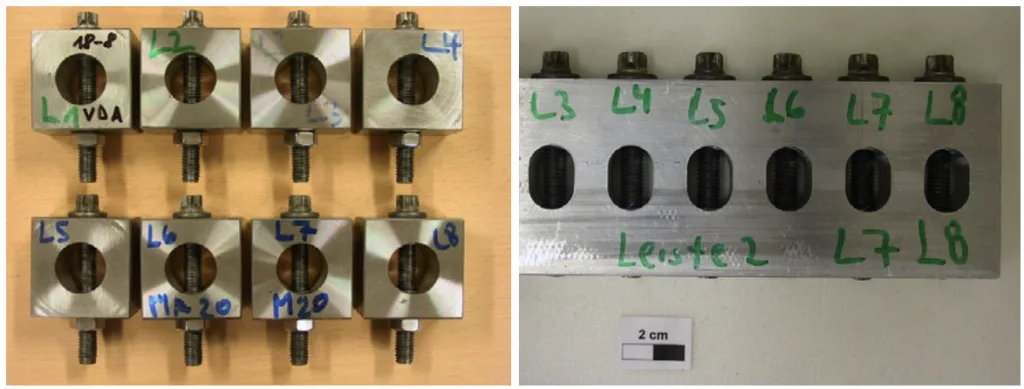
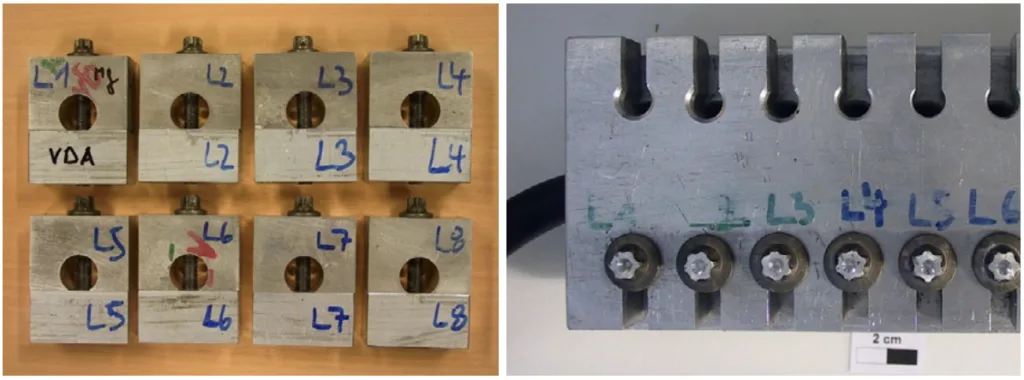
- Figure 1. Tightening process in pre-cast core hole of AZ91 with TAPTITE2000® M8x EN AW 6056 T6 (a); with TAPTITE2000® M8 EN AW 7075 T6 (b) [8]
- Figure 2. Minimum tensile strength Rm, yield strength Rp0.2 and breaking elongation of M8 EN AW 7075 in T6 and T79 heat treatment condition and different final production step
- Figure 3. EN AW 7075 in conditions T6 and T79 tightened in AZ91 core holes with minimal and maximum core hole size
- Figure 4. Drop in clamping load at 120°C of AZ91 and AE44 tightened into pre-cast core holes with upper core hole tolerance using EN AW 7075 in T79 condition
- Figure 5. Extrapolation of relaxation test data of AZ91 and AE44 to 4000 hours
- Figure 6. Influence of heat treatment condition and production sequence of EN AW 7075 on drop in clamping load in MRI153 at 120°C (LCT)
- Figure 7. Relaxation test arrangement
- Figure 8. Influence of pulsating service load on drop in clamping load at RT of Mg-alloy AE44 (UCT)
- Figure 9. Influence of pulsating service load on drop in clamping load at 120°C of AE44 (UCT) (a); logarithmic scale (b)
- Figure 10. Influence of pulsating service load on drop in clamping load at 120°C of AZ91 (UCT) (a); in logarithmic scale (b)
- Figure 11. Side view and longitudinal cut of M8 EN AW 6056 after 720 hours of salt spray test
- Figure 12. Side view and longitudinal cut of M8 EN AW 7075 after 720 hours of salt spray test
- Figure 13. Side view and longitudinal cut of 9.8 steel bolt, electroplated with Al cup washer after 720 hours salt spray test
- Figure 14. Side view and longitudinal cut of 10.9 steel bolt, electroplated, thick layer-passivated and sealed after 720 hours salt spray test
- Figure 15. Side view and longitudinal cut of 10.9 steel bolt, zinc flake coated and sealed after 720 hours salt spray test
- Figure 16. Bolted joints for stress crack corrosion and galvanic corrosion testing
- Figure 17. Bolted joints for stress crack corrosion testing
7. Conclusion:
Summary of Key Findings:
The study concludes that both EN AW 7075 T6 and T79 aluminum alloys are suitable for thread forming in magnesium alloys AZ91, AE44, and MRI153. EN AW 7075 T79 is preferred for over-elastic tightening due to its improved ductility and comparable clamping load performance to T6. Mg-alloy AE44 exhibits superior relaxation resistance at 120°C compared to AZ91, especially under pulsating service loads. The heat treatment and production sequence of EN AW 7075 bolts significantly influence relaxation behavior, with T79 and final heat treatment showing better performance. Aluminum bolts generally demonstrate better corrosion behavior than steel bolts in magnesium joints, except for steel bolts with aluminum cup washers. EN AW 7075 T79 is deemed uncritical regarding stress crack corrosion in typical automotive applications.
Academic Significance of the Study:
This research provides a comprehensive handbook-level understanding of the applicability of high strength thread forming aluminum bolts in magnesium components. It systematically investigates the interplay of material selection, heat treatment, loading conditions, and environmental factors on the performance of these bolted joints. The findings contribute valuable data and insights to the field of lightweight material joining, particularly for magnesium applications in demanding environments.
Practical Implications:
The findings offer practical guidelines for engineers in designing bolted joints for magnesium power train components. The study suggests that EN AW 7075 T79 thread forming aluminum bolts, when combined with creep-resistant magnesium alloys like AE44, offer a viable solution for weight and cost reduction. The recommendation to use EN AW 7075 T79 bolts and to consider final heat treatment for improved relaxation performance are directly applicable in industrial settings. The comparison with steel bolts and the identification of aluminum cup washers as an effective corrosion protection method for steel bolts also provide valuable options for designers.
Limitations of the Study and Areas for Future Research:
The study is limited to specific materials (AZ91, AE44, MRI153, EN AW 7075, EN AW 6056), bolt size (M8), and test conditions. Future research could expand the scope to include:
- Investigation of other magnesium and aluminum alloys.
- Evaluation of different bolt sizes and thread geometries.
- Long-term performance assessment under more complex and realistic service conditions, including torsion fatigue and varying temperature profiles.
- Further exploration of advanced corrosion protection methods for aluminum-magnesium joints.
- Detailed analysis of the influence of core hole casting tolerances on joint performance in mass production scenarios.
- Investigation of the reusability of formed magnesium nut threads in service conditions.
8. References:
- 1. S.M. Zhu, M.A. Gibson, J.F. Nie, M. A. Easton, T.B. Abbott, "Microstructural analysis of the creep resistance of die-cast Mg-4AI-2RE alloy", Scripta Materialia 58, 2008, pp. 477-480
- 2. I.P. Moreno, T.K. Nandy, J.W. Jones, J.E. Allison, T.M. Pollock, "Microstructural stability and creep of rare-earth containing magnesium alloy", Scripta Materialia 48, 2003, pp. 1029-1034
- 3. P. Bakke, A. Fischersworring-Bunk, I deLima, H. Lilholt, I. Bertilsson, F. Abdulwahab, P. Labelle, "The European Union Mg-Engine Project - Generation of Material Property Data for Four Die Cast Mg-Alloys", SAE technical paper 2006-01-0070, 2004
- 4. F. vonBuch, S. Schumann, H. Friedrich et al, „New Die Casting Alloy MRI153 for Power-Train Applications“, Magnesium Technology, 2002
- 5. F. Heinrich: „Aluminiumschrauben mit gesteigerten mechanischen Eigenschaften für höher beanspruchte Leichtmetallverbindungen“, 8. Informations- und Diskussionsveranstaltung, Darmstadt, 10.05.2006
- 6. K. Westphal: „Verschraubung von Magnesium-komponenten“, Metall 56. Jahrgang, 1-2/2002, Seite 32ff
- 7. H. Friedrich: „Werkstofftechnische Anforderungen an gewindefurchende Verbindungselemente“, DVM Bericht 671, 2004, S. 23
- 8. C. Hinteregger "Innovative Leichtmetall-verschraubungen im Fahrzeuggetriebebau“, PhD-Thesis, University of Leoben, 2008
- 9. Forschungsvereinigung Antriebstechnik [Drive Technology Research Association] FVA project 470 – maximum strength aluminum bolts
- VDA Prüfblatt 621-415, Prüfung des Korrosionsschutzes von Kraftfahrzeuglackierungen bei zyklisch wechselnder Beanspruchung
- Aluminium Taschenbuch 15. Auflage, Band 1: Grundlagen und Werkstoffe, ISBN 3-87017-241-X, Düsseldorf, 1995
9. Copyright:
- This material is Gerhard Gerstmayr, Philipp Oberhuber, Thomas Jakob, Heinz Leitner's paper: Based on "Applicability of high strength thread forming Aluminum bolts in magnesium power train components".
- Paper Source: DOI URL (Not available in the text, insert if known)
This material was summarized based on the above paper, and unauthorized use for commercial purposes is prohibited.
Copyright © 2025 CASTMAN. All rights reserved.