This article introduces the paper "Aerospace and High Performance Alloys Database Ferrous • FeUH H-13 August 2008" published by "CINDAS LLC".
1. Overview:
- Title: Aerospace and High Performance Alloys Database Ferrous • FeUH H-13
- Author: J. C. Benedyk
- Publication Year: August 2008
- Publishing Journal/Academic Society: CINDAS LLC
- Keywords: H-13 steel, AISI/UNS (T20813), composition limits, hot work steel, premium grades, superior grades, toughness, thermal fatigue resistance, alloying elements, microstructure, carbide size, carbide distribution, martensitic steel, air hardening, ultrahigh-strength steel, heat treatment, mechanical properties, airframe applications, landing gear applications, ultimate tensile strength, thermal shock resistance, austenitizing, tempering, secondary hardness, fracture toughness, fatigue strength, elevated temperatures, hydrogen embrittlement, corrosion-resistant coating, oxidation, vanadium content, vanadium carbides, wear resistance, homogenization, powder metallurgy, ingot metallurgy, hot work die, mold materials, nonferrous casting, ferrous casting, hot forming operations, molding of plastics, die casting dies, aluminum die casting, magnesium die casting, extrusion tools, containers, hot forging dies, stamping dies, hot shear blades, plastic molds, thermal fatigue, hot erosion, hot hardness, thermal shock resistance, water cooled dies, nitriding, hard coating, commercial designations, specifications, heat treatment, microstructure, annealing, normalizing, stress relieving, hardening, austenitization, quenching, tempering, stabilizing, retained austenite, nitriding, hardness, room temperature hardness, hot hardness, nitrided case hardness, forms and conditions available, melting and casting practice, physical properties, thermal properties, melting range, phase changes, thermal conductivity, thermal expansion, specific heat, thermal diffusivity, density, specific gravity, electrical properties, magnetic properties, emittance, damping capacity, chemical environments, general corrosion, stress corrosion, oxidation resistance, hydrogen resistance, corrosion/erosion by molten metal, liquid metal induced embrittlement resistance, solid metal induced embrittlement resistance, nuclear environment, mechanical properties, specified mechanical properties, NADCA H-13 207-97 H-13 Steel Acceptance Criteria, other H-13 Steel Acceptance Criteria, mechanical properties at room temperature, tension stress-strain diagrams, tensile properties, compression stress-strain diagrams, compression properties, impact, notch properties, fracture toughness, plane strain fracture toughness, mechanical properties at various temperatures, tensile properties, compression stress-strain diagrams, compression properties, impact, bending, torsion and shear, bearing, stress concentration, notch properties, fracture toughness, combined loading, ductile to brittle transition temperature, creep and creep rupture properties, fatigue properties, high-cycle fatigue, low-cycle fatigue, elastic properties, poisson’s ratio, modulus of elasticity, modulus of rigidity, tangent modulus, secant modulus, thermal fatigue properties, CWRU thermal fatigue test, IITRI thermal fatigue test, thermal fatigue tests of H-13 steel suppliers, fabrication, forming, hot working, forging, machining and grinding, joining, surface treating.
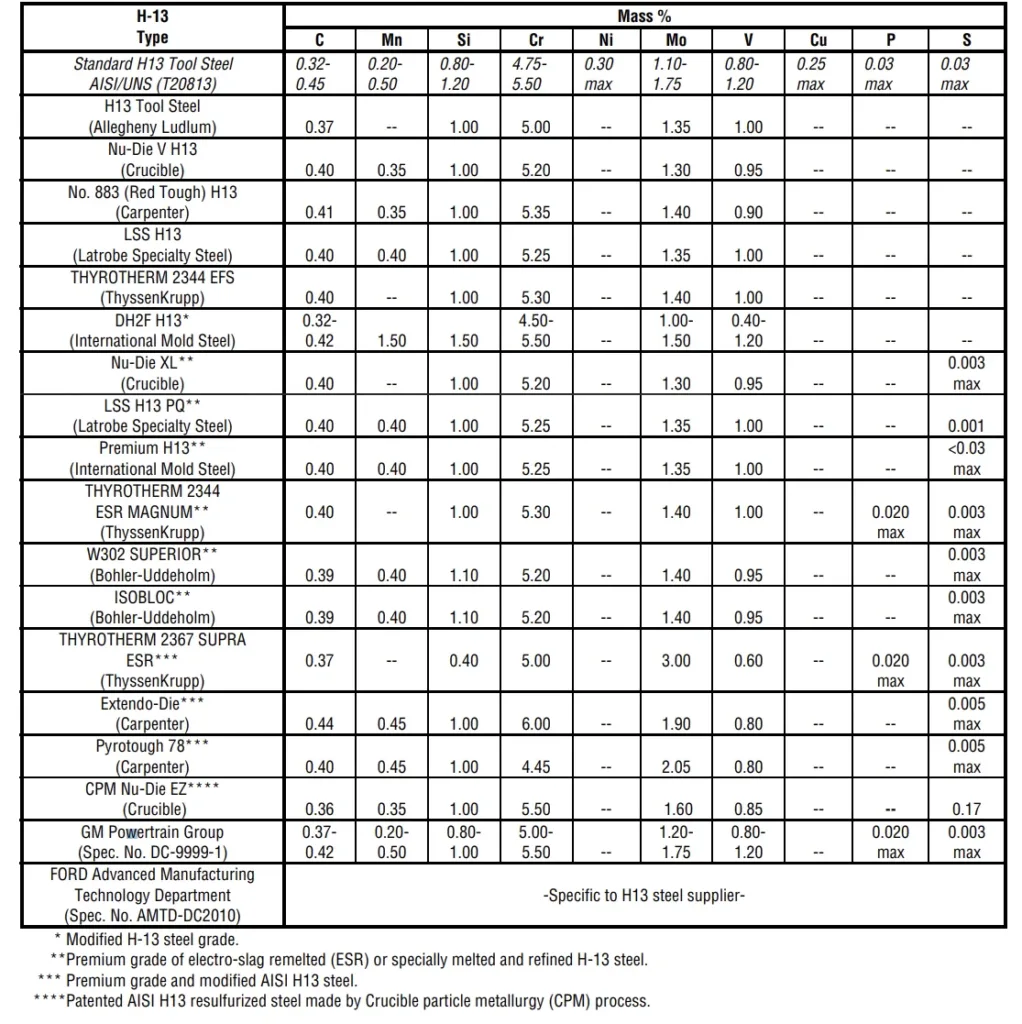
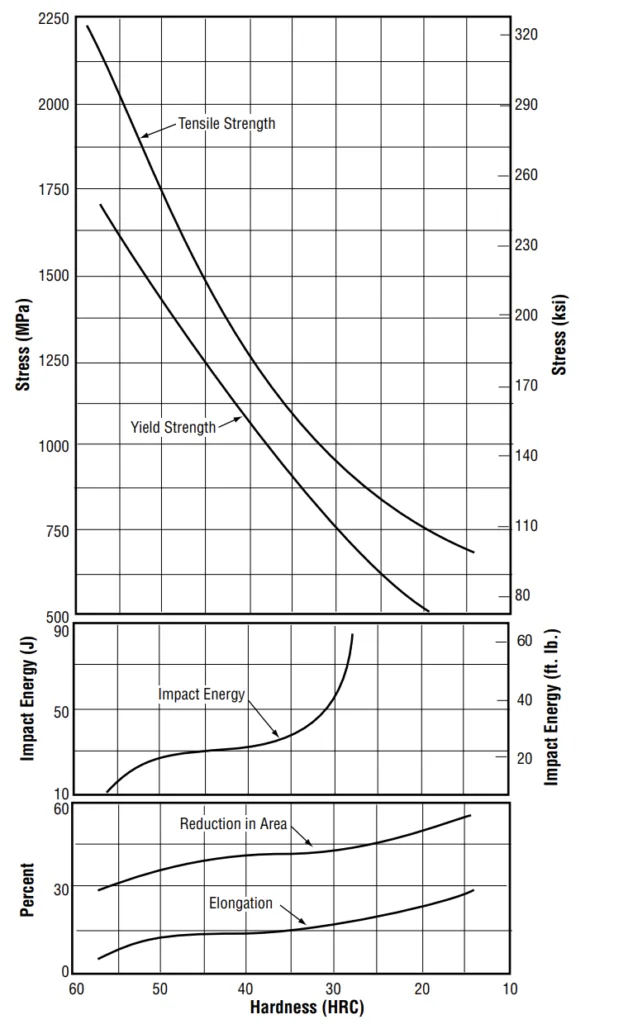

2. Abstracts or Introduction
1.0 General
This medium alloy, martensitic, air hardening, Ultrahigh-strength steel is similar to H-11 and H 11 Mod in composition, heat treatment, and many properties. The steels H-11, H-11 Mod, and H-13 exhibit several properties that are important in airframe and landing gear applications, including the ability to be heat treated to an ultimate tensile strength of 300 ksi while having excellent thermal shock resistance. These grades are typically hardened by austenitizing and cooling in air, flowing inert gas, oil, or hot salt bath. Upon tempering, they show secondary hardness maxima in their tempering curves and, upon being double or triple tempered at 1050-1100F, typically develop the combination of high hardness (44-48 Rc
) and high room temperature ultimate tensile strength (220-250 ksi) combined with good fracture toughness and maximum fatigue strength at room and elevated temperatures.
H-13 steel is not as commonly used as H-11 Mod as a constructional steel in ultrahigh-strength applications, although it can be substituted for H-11 Mod in cases where availability or the slightly better wear resistance and other characteristics of H-13 offer advantages.
3. Research Background:
Background of the Research Topic:
- Hot-work tool steels like H-13 are crucial in die casting and hot forming due to their capacity to maintain hardness and strength at elevated temperatures.
- H-13 is preferred for aluminum and magnesium die casting dies, extrusion tools, hot forging and stamping dies, hot shear blades, and plastic molds.
- Key properties include thermal fatigue, hot erosion, wear resistance, and hot hardness retention at temperatures up to 1000F or higher.
- Good thermal shock resistance allows dies and tools to be internally water-cooled.
- Surface treatments like nitriding or hard coatings are used to enhance wear resistance.
Status of Existing Research:
- Premium and superior grades of H-13 are available with controlled compositions and refined microstructures for improved toughness and thermal fatigue resistance.
- Powder/particle metallurgy grades offer significantly refined carbide and sulfide distributions for enhanced properties compared to conventional ingot metallurgy H-13 steel.
- Research has explored the effects of austenitizing temperatures (1950F and 2050F) on improving thermal fatigue resistance due to increased softening resistance under thermal stress cycling.
- NADCA has specified compositions and microcleanliness limits for premium and superior grades of H-13 for die casting dies.
Necessity of the Research:
- Selecting the appropriate H-13 steel grade is critical for cost-effectiveness in various applications.
- Understanding the heat treatment and microstructure of H-13 is essential for optimizing its performance in demanding applications like die casting and hot forming.
- Characterizing the mechanical and physical properties of H-13 at room and elevated temperatures is necessary for proper material selection and application design.
- Investigating surface treatments like nitriding and coatings is important for enhancing wear and corrosion resistance and extending the service life of H-13 dies and tools.
4. Research Purpose and Research Questions:
Research Purpose:
This paper aims to provide a comprehensive handbook-level overview of H-13 die steel, covering its properties, heat treatment, fabrication, and performance characteristics, primarily for die casting and hot work tooling applications.
Key Research:
- Chemical composition, commercial designations, and specifications of H-13 steel grades.
- Heat treatment procedures, including annealing, stress relieving, hardening, tempering, and stabilizing, and their effects on microstructure and hardness.
- Physical properties such as thermal conductivity, thermal expansion, specific heat, density, and elastic modulus.
- Mechanical properties at room and elevated temperatures, including tensile strength, yield strength, hardness, impact toughness, fracture toughness, fatigue properties, and creep resistance.
- Fabrication aspects including forming, machining, grinding, welding, and surface treatments.
- Performance in various environments, including general corrosion, stress corrosion, oxidation, molten metal contact, and thermal fatigue.
Research Hypotheses:
- Higher austenitizing temperatures (1950F-2050F) improve thermal fatigue resistance in H-13 steel compared to conventional 1850F austenitizing.
- Premium and superior grades of H-13 steel, with controlled compositions and refined microstructures, exhibit enhanced toughness and thermal fatigue resistance.
- Surface treatments like nitriding and PVD coatings improve wear resistance, corrosion resistance, and thermal fatigue life of H-13 dies and tools.
- Stress accelerated tempering affects the hardness and performance of H-13 steel under service conditions involving elevated temperatures and stress.
5. Research Methodology
Research Design:
This paper is a descriptive review, compiling and summarizing existing literature, specifications, and research findings on H-13 die steel. It is based on data from handbooks, technical papers, material specifications, and research reports.
Data Collection Method:
Data was collected from:
- Metals Handbooks
- HEAT TREATER’S GUIDE
- NADCA standards
- Material Data Sheets from steel manufacturers (Allegheny Ludlum, Assab Steels, Bohler-Uddeholm, Carpenter, Crucible, Latrobe, ThyssenKrupp, International Mold Steel, MetalTek, Osprey Metals, GM Powertrain Group, FORD)
- Research publications and reports (Ph.D. Thesis, SDCE International Die Casting Congress papers, Die Casting Research Foundation reports, IIT Research Institute reports, TPTC Confidential Reports, Journal articles).
Analysis Method:
The paper synthesizes and organizes information from various sources to provide a comprehensive overview of H-13 steel. It uses tables, figures, and descriptive text to present data on composition, properties, heat treatment, and performance. Analysis is primarily qualitative, focusing on summarizing and explaining the reported data and trends. Quantitative analysis is limited to presenting data directly from cited sources, such as property values and graphical data from figures.
Research Subjects and Scope:
The subject of this paper is H-13 hot-work die steel. The scope includes:
- Chemical composition, designations, and specifications.
- Heat treatment and microstructure.
- Physical, mechanical, and environmental properties.
- Fabrication and joining methods.
- Performance in die casting and hot work tooling applications.
6. Main Research Results:
Key Research Results:
- Composition and Grades: Standard and premium/superior grades of H-13 steel are defined by AISI/UNS (T20813) and modified compositions with controlled impurities (P, S) and alloying elements. Tables 1.4.1, 1.4.2, and 1.4.3 detail these compositions and inclusion limits.
- Heat Treatment: Annealing, stress relieving, hardening (austenitizing and quenching), and tempering procedures are critical for achieving desired properties. Figures 1.5.4.1, 1.5.5.1, 1.5.5.2, 1.5.5.3, 1.5.5.8, 1.5.8.1, 1.5.8.2, 1.5.8.3, 1.5.8.4, 1.5.8.6, and 1.5.8.7, and Tables 1.6.1.1, 1.6.1.2, 1.6.1.3, 1.6.1.4, 1.5.11.2, 1.6.3.1 illustrate heat treatment cycles, phase transformation diagrams, tempering curves, and nitriding case characteristics.
- Microstructure: Annealed microstructure consists of a ferritic matrix with spheroidized carbides (Figure 1.5.2.1). Hardened and tempered microstructure is tempered martensite with fine carbides (Figures 1.5.8.7, 1.5.8.8).
- Hardness: Room temperature hardness varies with heat treatment and grade (Tables 1.6.1.1, 1.6.1.2, 1.6.1.3, 1.6.1.4, 1.6.3.1). Hot hardness and nitrided case hardness are also characterized (Figures 1.6.2.1, 1.6.2.4, Table 1.6.2.2, 1.6.2.3, 1.6.3.1).
- Mechanical Properties: Tensile properties, impact toughness, and fracture toughness are presented at room and elevated temperatures (Tables 3.2.1.1, 3.2.1.2, 3.2.1.4, 3.2.3.1, 3.2.3.2, 3.2.3.3, 3.3.1.4, 3.3.3.1, Figures 3.2.1.3, 3.2.7.1.1, 3.2.7.2.2, 3.2.7.2.3, 3.2.7.2.4, 3.2.7.2.5, 3.2.7.2.6, 3.3.1.1, 3.3.1.2, 3.3.1.3, 3.3.3.2, 3.3.3.3, 3.3.3.4, 3.3.3.5, 3.3.7.2.2, 3.3.7.2.4, 3.3.7.2.5, 3.3.9.1).
- Thermal Fatigue: CWRU and IITRI thermal fatigue tests demonstrate the influence of austenitizing temperature, steel grade, and heat treatment on thermal fatigue resistance (Figures 3.7.1.3, 3.7.1.4, 3.7.2.5, 3.7.3.1, 3.7.3.4, 3.7.3.5, Table 3.7.1.5, 3.7.3.2).
- Corrosion and Wear: Nitriding and PVD coatings enhance corrosion and wear resistance, particularly against molten aluminum (Figures 2.3.1.1, 2.3.3.1, 2.3.3.2, 2.3.5.1, 2.3.5.5, Tables 1.5.11.2, 1.6.3.1).
- Physical Properties: Thermal conductivity and thermal expansion data are provided in Tables 2.1.3.1, 2.1.3.2, 2.1.4.1, 2.1.4.2, 2.1.4.3, 2.1.4.4 and density in Table 2.2.1.1.
Analysis of presented data:
- Heat Treatment Optimization: Higher austenitizing temperatures (1950-2050F) generally improve thermal fatigue and hot hardness, although grain size may increase (Figures 1.5.5.4, 1.5.5.5, 1.5.5.6, 3.7.1.3). Double or triple tempering is crucial for achieving optimal toughness and dimensional stability (Figure 1.5.4.1, 1.5.8.4, Table 1.5.8.10).
- Grade Selection: Premium and superior grades offer enhanced properties due to controlled composition and refining processes, justifying their use in critical applications like die casting dies (Tables 1.4.2, 1.4.3, Figures 3.3.9.1, 3.7.3.1, 3.7.3.4, 3.7.3.5).
- Surface Treatment Benefits: Nitriding and PVD coatings significantly improve surface hardness, wear resistance, and corrosion resistance, extending the life of H-13 dies and tools, especially in contact with molten aluminum (Figures 1.5.11.1, 2.3.5.1, 2.3.5.5, Tables 1.5.11.2, 1.6.3.1).
- Stress and Temperature Effects: Stress accelerated tempering and thermal fatigue are important considerations in hot work applications, influencing hardness and failure mechanisms (Figures 1.5.9.3, 1.5.9.4, 1.5.9.5, 3.7.2.5).
Figure Name List:
- Figure 1.5.2.1 Annealed quality “AS” microstructure chart for annealed H-13 steel showing acceptable (AS1-AS9) and unacceptable (AS10-AS18) microstructures according to NADCA—all microstructures at 500x and etched with 5% Nital (Ref. 4)
- Figure 1.5.2.2 Banding microsegregation chart for annealed H-13 steel blocks showing acceptable and unacceptable microstructures according to NADCA—all microstructures at 50x and etched with Villella’s reagent (Ref. 4)
- Figure 1.5.4.1 Schematic of NADCA—recommended austenitizing, quenching, and tempering heat treatment cycle for H-13 steel (Ref. 4)
- Figure 1.5.5.1 Isothermal phase transformation diagram for H-13 steel (0.40 C, 1.05 Si, 5.00 Cr, 1.35 Mo, 1.10V) austenitized at 1850F (Ref. 3)
- Figure 1.5.5.2 Time-temperature transformation diagram for premium grade H-13 steel (Thyrotherm 2344 ESR Magnum, ThyssenKrupp Specialty Steels, Inc.) austenitized at 1870–1920F (Refs. 17, 18)
- Figure 1.5.5.3 Kinetics of bainite transformation for H-13 and H-11 steels compared at given austenitizing temperatures (Ref. 29)
- Figure 1.5.5.4 ASTM grain size versus austenitizing temperature for H-13 steel and air cooled for 0.5-in. cube samples soaked at temperature for 25–80 minutes (Ref. 28)
- Figure 1.5.5.5 Volume % carbide (95% confidence interval) in the as-quenched condition of air cooled (AC) small sections and larger 6- and 12-in rounds of H-13 steel as a function of austenitizing temperature for given soak times (Ref. 28)
- Figure 1.5.5.6 As-quenched hardness as a function of austenitizing temperature of air cooled (AC) small sections and larger 6- and 12-in rounds of H-13 steel for given soak times (Ref. 28)
- Figure 1.5.5.7 As-Quenched microstructure for H-13 steel showing moderate carbide precipitation at grain boundaries and finely dispersed carbides in matrix (Ref. 30)
- Figure 1.5.5.8 Continuous cooling transformation diagram for H-13 steel austenitized at 1970F showing cooling curves A through E (Ref. 30)
- Figure 1.5.8.1 Hardness variation with tempering temperature for H-13 steel air cooled from 1875F and tempered 2 h at temperature (Ref. 1)
- Figure 1.5.8.2 Hardness as a function of tempering temperature for H-13 steel austenitized at 1850F and 1800F, air cooled, and double tempered (Ref. 3)
- Figure 1.5.8.3 Hardness as a function of tempering temperature for H-13 steel austenitized at 1950F and 1800F, air cooled, and tempered for 2 h (Ref. 3)
- Figure 1.5.8.4 Tempering curve (double tempered 2 h + 2 h) for H-13 steel after air quenching (AC) 0.5-in. square samples from 1875, 1950, and 2050F (Ref. 28)
- Figure 1.5.8.5 Master tempering parameter curve for H-13 steel hardened by austenitizing at 1750–1950F and quenching (Ref. 4)
- Figure 1.5.8.6 Time-temperature tempering diagram for H-13 steel hardened by austenitizing at 1875F (Ref. 32)
- Figure 1.5.8.7 Acceptable microstructures (500x, 5% Nital etch) of H-13 steel properly heat treated by austenitizing, quenching, and tempering as per NADCA acceptance criteria (numbering HS1-HS9 does not denote a quality ranking as all are acceptable) (Ref. 4)
- Figure 1.5.8.8 Typical microstructure from the center of a six-inch-thick H-13 steel die hardened commercially in a vacuum furnace at 1850F and double tempered (2 h at 1050F + 2 h at 1100F) (Ref. 30)
- Figure 1.5.8.9 Dimensional change of H13 steel in a 1 x 2 x 6 in. block versus tempering temperature (Ref. 3)
- Figure 1.5.9.1 Variable section creep specimen used to study stress accelerated tempering of H-13 steel as reported in Figures 1.5.9.2–1.5.9.5 (Ref. 25)
- Figure 1.5.9.2 Tempering curves for H-13 steel constructed from unstressed section of test specimen shown in Figure 1.5.9.1 (Ref. 25)
- Figure 1.5.9.3 Hardness change (microhardness surveys converted to Rockwell C) in H-13 steel measured along variable section creep specimen shown in Figure 1.5.9.1 due to stress accelerated tempering at 1000F (Ref. 25)
- Figure 1.5.9.4 Hardness change (microhardness surveys converted to Rockwell C) in H-13 steel measured along variable section creep specimen shown in Figure 1.5.9.1 due to stress accelerated tempering at 1050F (Ref. 25)
- Figure 1.5.9.5 Hardness change (microhardness surveys converted to Rockwell C) in H-13 steel measured along variable section creep specimen shown in Figure 1.5.9.1 due to stress accelerated tempering at 1100F (Ref. 25)
- Figure 1.5.11.1 Cross-sectional optical micrographs of gas nitrided, ion nitrided, and salt bath nitrided H-13 steel after austenitization at 1890F and triple tempering (70X magnification) (Ref. 34)
- Figure 1.5.11.3 Gas nitrided case (24 h at 975F) produced on H-13 steel that was austenitized at 1890F, triple tempered at 950F, and surface activated in manganese phosphate (300X magnification) (Ref. 35)
- Figure 1.6.1.5 Room temperature hardness or “red hardness” of H-13 steel hardened and tempered as indicated after exposure to elevated temperatures for 4-100 h (Ref. 36)
- Figure 1.6.1.6 Tempering curves of H-13 steel air quenched after austenitizing at 1750, 1850, and 2050F showing hardness (Rc or HRC) as a function of time at a tempering temperature of 1100F (Ref. 22)
- Figure 1.6.1.7 Tempering curves for H-13 steel air quenched after austenitizing at 1750, 1850, and 2050F, tempering to 45 HRC, and showing hardness (Rc or HRC) as a function of time at a tempering temperature of 1000F (Ref. 22)
- Figure 1.6.2.1 Typical hot hardness of H-13 steel for specimens oil quenched from 1850F and double tempered 2 + 2 h at indicated tempering temperature (Ref. 37)
- Figure 1.6.2.4 Effect of temperature on hot Brinell hardness (HB) of hardened (austenitized and quenched, untempered) H-13 steel (Ref. 44)
- Figure 2.3.1.1 Potentiodynamic polarization curves of AISI H-13 steel measured in a 3.5% NaCl solution at pH = 6 on an (…) untreated sample, (----) nitrogen plasma immersion ion implantation (PIII) processed sample (T=300C, t=12 h), and (—) nitrogen PIII processed sample (T=450C, t=9 h) (Ref. 45)
- Figure 2.3.3.1 Comparative oxidation resistance of H-13 and maraging steels at 1000F (Ref. 46)
- Figure 2.3.3.2 Cross sectional view of oxide buildup in thermal fatigue crack in hardened H-13 steel specimen: (a) 50x, nital etch and (b) 500x, nital etch (Ref. 22)
- Figure 2.3.5.1 Variations in corroded/eroded depth of immersion test specimens of hardened and tempered H-13 steel as heat treated and machined and separately nitrided by gas or ion nitriding maintained in a molten Al-Si-Cu (KS ALDC) aluminum alloy at 1300F for 43 h (Ref. 47)
- Figure 2.3.5.2 Schematic diagram of accelerated washout testing arrangement at Case Western Reserve University (CWRU) with molten aluminum alloy injected into die cavity at ~70 in/s (Ref. 48)
- Figure 2.3.5.3 Test pin design and position within die cavity of CWRU accelerated washout test arrangement shown in Figure 2.3.5.2 (Ref. 48)
- Figure 2.3.5.4 Microstructural cross sections (500x) PVD coated pin specimens tested in CWRU accelerated washout arrangement shown in Figure 2.3.5.2 (Ref. 48)
- Figure 2.3.5.5 Effect of various types of PVD coatings shown in Figure 2.3.5.4 on washout resistance of H-13 steel die casting core pins in CWRU accelerated washout test shown in Figures 2.3.5.2 and 2.3.5.3 (Ref. 48)
- Figure 2.3.6.1 Schematic drawing of TPTC U-bend liquid zinc embrittlement test procedure conducted on H-13 steel plate specimens: original annealed specimen bent into U-shape, heat treated, bent to an incipient plastic flow condition at a displacement of Δd (left), displacement held by fastener, and immersed in a molten zinc bath (right) (Ref. 50)
- Figure 2.3.6.2 Liquid zinc embrittlement TPTC U-bend test data (Y-axis: time to fracture in hours; X-axis: test conditions as shown in Figure 2.3.6.1) conducted on H-13 steel plate specimens (Ref. 50)
- Figure 3.2.7.1.1 Effect of notch radius on the impact strength of Izod type specimens of H-13 steel heat treated to 48 Rockwell C and tested at room temperature (Ref. 61)
- Figure 3.2.7.2.2 Room temperature plane strain fracture toughness (KIc) of small and large size specimens of H-13 steel versus austenitizing temperature (a) and tempered hardness (b) after all specimens were double tempered at 1100F (2 + 2 h) for austenitizing soak times and cooling conditions given (25 min soak and air quench for small specimens and 50 and 60 min soak and simulated laboratory quench for 6- and 12-in. rounds) (Ref. 28)
- Figure 3.2.7.2.3 Variation of room temperature plane strain fracture toughness KIc of heat treated H13 steel, austenitized at 1870F for 30 min, quenched at various rates, and tempered to 44 HRC, as a function of quench rate (Ref. 76)
- Figure 3.2.7.2.4 Charpy V-notch (CVN) impact values of H13 steel quenched at various rates after austenitizing at 1870F for 30 min and tempered to 44 HRC (Ref. 76)
- Figure 3.2.7.2.5 Correlation between (KIc/σys)2 and CVN/σys at room temperature for H13/H11 steels (Ref. 77)
- Figure 3.2.7.2.6 Experimental values of KIc at room temperature compared with values of KIc calculated from CVN and HRC data at room temperature (see linear regression relationship in 3.2.7.2) for H13 and H11 steels (Ref. 77)
- Figure 3.3.1.1 Effect of elevated temperature on tensile strength of H-13 steel heat treated to room temperature Rockwell C (HRC) hardness values given (Ref. 44)
- Figure 3.3.1.2 Effect of elevated temperature (C x 1.8 + 32 = F) on tensile and 0.2 yield (creep limit) strength (N/mm2 x 0.145 = ksi) and reduction in area of H-13 steel heat treated to room temperature strength level given (Ref. 17)
- Figure 3.3.1.3 Flow stress (determined from modified Johnson-Cook model of flow stress and tuned by OXCUT computer program and experimental data from lathe machining experiments) of H-13 steel at temperatures of 800–1200C (1472-2192F) and strain rates of 6 x 103 – 9 x 105 1/s for H-13 steel originally at 46 Rockwell C (HRC) hardness (MPa x 0.145 = ksi) (Ref. 57)
- Figure 3.3.3.2 Longitudinal Charpy V-notch impact resistance versus austenitizing temperature for H-13 steel specimens austenitized for treatment times given, air quenched (small size specimens) or cooled to simulated quenching of 6- and 12-in. rounds, double tempered at 1000F (2 + 2 h), and subsequently tested at room temperature and 800F (Ref. 28)
- Figure 3.3.3.3 Longitudinal Charpy V-notch impact resistance versus austenitizing temperature for H-13 steel specimens austenitized for treatment times given, air quenched (small size specimens) or cooled to simulated quenching of 6- and 12-in. rounds, double tempered at 1100F (2 + 2 h), and subsequently tested at room temperature and 800F (Ref. 28)
- Figure 3.3.3.4 Longitudinal Charpy V-notch impact resistance versus austenitizing temperature for H-13 steel specimens austenitized for treatment times given, air quenched (small size specimens) or cooled to simulated quenching of 6- and 12-in. rounds, double tempered at 1150F (2 + 2 h), and subsequently tested at room temperature and 800F (Ref. 28)
- Figure 3.3.3.5 Longitudinal Charpy V-notch impact resistance versus tempered hardness for H-13 steel specimens austenitized at 1875, 1950, and 2025F for soak times given, air quenched (small size specimens) or cooled to simulated quenching of 6- and 12-in. rounds, tempered, and subsequently tested at 800F (Ref. 28)
- Figure 3.3.7.2.1 Figure] Short rod (chevron-notch) fracture toughness specimen used to obtain data shown in Figure 3.3.7.2.2 with shaded area denoting crack advance increment (Refs. 78, 79)
- Figure 3.3.7.2.2 [Figure] Temperature dependence of KIc (KIv ~ KIc) of H13 steel, VASCO MA ultrahigh strength steel, M 50 high temperature bearing steel, and S 2 tool steel used for drill bit bearings (SOLAR STEEL) (heat treatment and room temperature property data on these steels presented in Table 3.3.7.2.3) (Ref. 78)
- Figure 3.3.9.1 Representation of DBTT curves based on Charpy V-notch (CVN) tests of low quality and high quality H-13 tool steels heat treated as per NADCA 207-97 (3.1.1) (Ref. 60)
- Figure 3.4.1 Creep characteristics of H-13 steel heat treated to 216 ksi room temperature tensile strength (~44–46 HRC): strain duration in h (to 1% creep limit – left or creep rupture – right) as a function of stress (N/mm2 x 0.145 = ksi) at temperatures (C x 1.8 + 32 = F) indicated (Ref. 17)
- Figure 3.5.1.1 Fatigue strength (N/mm2 x 0.145 = ksi) of smooth and notched specimens tested at room temperature in fully reversed tension-compression (R = -1) of hardened H-13 steel in relation to microstructural homogeneity achieved by electric arc air melted, ESR, and special treatment (patented Isodisc process) (Ref. 38)
- Figure 3.5.1.2 [Figure] Tension-tension (R = +0.2) fatigue curves determined at 60 Hz for longitudinal specimens of air melted () and ESR () heats of H-13 steel in the hardened condition (austenitized at 1850F, oil quenched, and double tempered 2 + 2 h at 1090F to 48 HRC hardness) (Ref. 62)
- Figure 3.5.1.3 [Figure] Fully reversed tension-compression (R = -1) fatigue curves determined at 60Hz for longitudinal ( – ESR, – air melted) and transverse ( – ESR, – air melted) H-13 steel in the hardened condition (austenitized at 1850F, oil quenched, and double tempered 2 + 2 h at 1090F to 48 HRC hardness) (Ref. 62)
- Figure 3.7.1.1 [Figure] Schematic drawing of CWRU thermal fatigue test used in studying H-13 thermal fatigue and heat checking resistance showing apparatus used to dip specimen into molten A380 aluminum at 1300F (upper) and water cooled H-13 steel test specimen (lower) (Refs. 22–24, 48)
- Figure 3.7.1.2 [Figure] Thermal cycle used in determining thermal fatigue resistance of H-13 steel in the CWRU test for different austenitizing temperatures (Figure 3.7.1.3) and various types and grades of H-13 steel (Figure 3.7.1.4) (Refs. 22–24)
- Figure 3.7.1.3 [Figure] Thermal fatigue behavior in the CWRU test (Figure 3.7.1.1) of H-13 steel austenitized at 1750, 1850, 1950, and 2050F, air quenched, and all tempered to 45 Rc (HRC) showing average maximum crack length in microns (μ) (upper) and summation of total crack area (lower) as a function of number of cycles (Refs. 22–24)
- Figure 3.7.1.4 [Figure] Thermal fatigue behavior in the CWRU test (Figure 3.7.1.1) of various types and grades of H-13 steel austenitized at 1850F, air quenched, and all tempered at 1100F to 45 Rc (HRC) showing average maximum crack length in microns (μ) (upper) and summation of total crack area (lower) as a function of number of cycles (Refs. 22–24)
- Figure 3.7.2.1 [Figure] Heating and cooling curves for H-13 steel during a short cycle of thermal cycling between 1100 and 400F in the IITRI thermal fatigue test (Refs. 25, 66)
- Figure 3.7.2.3 [Figure] Number of cycles to crack initiation of H-13 steel in IITRI thermal fatigue test according to the cycle shown in Figure 3.7.2.1 as a function of cleanliness of the steel as rated by the number of +4 mm oxide inclusions at 320x magnification in 40 random fields (Ref. 66)
- Figure 3.7.2.4 [Figure] Heating and cooling curves for H-13 steel during a long cycle of thermal cycling between 1100 and 400F in the IITRI thermal fatigue test (Ref. 25)
- Figure 3.7.2.5 [Figure] Tempering of IITRI thermal fatigue fins (HRC hardness noted on fins) during short and long thermal cycling for 250–16,000 cycles (Ref. 25)
- Figure 3.7.3.1 [Figure] Thermal fatigue data from Crucible Steel Co. test (alternate immersion of square specimens in molten A380 aluminum at 1250F and quenching in a water bath at 200F with examination for cracks every 10, 000 cycles) (Ref. 43)
- Figure 3.7.3.3 [Figure] Thermal fatigue testing apparatus of EWK/Thyssen Krupp Specialty Steel: Ar atmosphere to avoid corrosion, induction heating to 1200F, water bath maintained at or near room temperature and at a pH = 10.5 to improve wetting, 2 x 2 x 0.40 in. H-13 steel samples cut from 30 x 8 in. forged slabs in transverse direction and rough machined, samples were hardened and tempered to 44–46 HRC and ground to a fine finish (Ref. 68)
- Figure 3.7.3.4 [Figure] Total crack length measured on samples of a superior grade of AISI H-13 (Thyrotherm 2344 EFS Supra) and a modified grade of H-13 (Thyrotherm 2367 EFS Supra) heat treated to 44–46 HRC and tested in the EWK/Thyssen Krupp Specialty Steel thermal fatigue apparatus shown in Figure 3.7.3.3 (Ref. 68)
- Figure 3.7.3.5 [Figure] Microscopic evaluation at 200x of some thermal fatigue cracks developed in samples (Figure 3.7.3.4) from the EWK/Thyssen Krupp Specialty Steel thermal fatigue test (Figure 3.7.3.3) (Ref. 68)
7. Conclusion:
Summary of Key Findings:
- H-13 steel is a versatile hot-work tool steel widely used for die casting and hot forming due to its excellent temper resistance, hot hardness, and thermal shock resistance.
- Optimal heat treatment, particularly austenitizing and tempering, is crucial for achieving desired mechanical properties and performance. Higher austenitizing temperatures can enhance thermal fatigue resistance.
- Premium and superior grades, along with powder metallurgy routes, offer improved properties compared to conventional H-13 steel.
- Surface treatments like nitriding and PVD coatings are effective in enhancing wear and corrosion resistance, extending tool life.
- Understanding stress accelerated tempering and thermal fatigue behavior is essential for predicting and improving the service life of H-13 components in demanding applications.
Academic Significance of the Study:
- This paper provides a comprehensive compilation of data and research findings on H-13 steel, serving as a valuable resource for experts and researchers in materials science and manufacturing engineering.
- It highlights the complex interplay between composition, heat treatment, microstructure, properties, and performance of H-13 steel, offering insights for further research and development in hot-work tool steel technology.
- The detailed review of thermal fatigue testing methodologies (CWRU, IITRI, and supplier-specific tests) contributes to the understanding and standardization of thermal fatigue assessment for die materials.
Practical Implications:
- The information presented aids in informed material selection and heat treatment design for H-13 steel tooling, optimizing performance and extending service life in die casting, forging, extrusion, and molding applications.
- Understanding the effects of processing parameters, such as austenitizing temperature and quenching rate, allows for tailored heat treatments to meet specific application requirements.
- The review of surface treatments provides guidance for enhancing wear and corrosion resistance, reducing downtime and improving productivity in manufacturing processes.
- The data on mechanical and physical properties at various temperatures is crucial for accurate design and simulation of H-13 tooling and components.
Limitations of the Study and Areas for Future Research:
- This paper is a summary of existing literature and data, not an original experimental study.
- The depth of analysis is limited by the scope of the reviewed documents.
- Further research is needed to:
- Investigate the long-term performance of advanced H-13 grades and surface treatments in industrial die casting and hot forming environments.
- Develop more accurate predictive models for thermal fatigue and stress accelerated tempering in H-13 steel.
- Optimize powder metallurgy processing and alloying strategies for enhanced H-13 steel properties.
- Standardize thermal fatigue testing methods to improve data comparability across different studies and suppliers.
8. References:
- 1. Metals Handbook Ninth Edition. Volume 1. Properties and Selection: Irons and Steels, American Society for Metals (now ASM International), 1978, pp. 437–39.
- 2. Metals Handbook Ninth Edition. Volume 3. Properties and Selection: Stainless Steels, Tool Materials and Special-Purpose Metals, American Society for Metals (now ASM International), 1980, pp. 421–69.
- 3. HEAT TREATER’S GUIDE: Practices and Procedures for Irons and Steels, ASM International, 2nd Ed., 1998, pp. 600-605.
- 4. Premium and Superior Quality H-13 Steel and Heat Treatment Acceptance Criteria for Pressure Die Casting Dies: NADCA #207-2003, North American Die Casting Association (NADCA), River Grove, Illinois, 2003.
- 5. Allegheny Ludlum H-13 Tool Steel, UNS T20813, DATA SHEET.
- 6. Assab Steels 8407 SUPREME Hot Work Steel, DATA SHEET.
- 7. Bohler-Uddeholm ORVAR H-13 Hot Work Tool Steel, DATA SHEET.
- 8. Bohler-Uddeholm SUPERIOR H-13 Hot Work Tool Steel, DATA SHEET.
- 9. Bohler-Uddeholm ISOBLOC H-13 Hot Work Tool Steel, DATA SHEET.
- Carpenter Pyrotough® 78 Hot Work Die Steel. DATA SHEET.
- Carpenter No. 883® Hot Work Die Steel (Red-Tough) (AISI H-13), DATA SHEET.
- Crucible Nu-Die® XL (Premium Quality AISI H-13) Tool Steel, DATA SHEET.
- International Mold Steel DH2F Pre-Hardened H-13-Type Mold Steel, DATA SHEET.
- International Mold Steel Premium H-13 Hot Work Die and Mold Steel, DATA SHEET.
- Latrobe LSS® H-13 Tool Steel, DATA SHEET.
- Latrobe VDC® H-13 Tool Steel, DATA SHEET.
- ThyssenKrupp Specialty Steels THYROTHERM 2344, DATA SHEET.
- ThyssenKrupp Specialty Steels THYROTHERM 2344 ESR MAGNUM, DATA SHEET.
- ThyssenKrupp Specialty Steels THYROTHERM 2367 SUPRA ESR, DATA SHEET.
- Premium Grade H-13/Hot Work Tool Material Standard Specification: Die Insert and Heat Treating Specification, Spec. No. DC-9999-1, GM Powertrain Group, 6-29-2001.
- Die Insert Material and Heat Treatment Performance Requirements: General Applications, Spec. No. AMTD DC2010, FORD Advanced Manufacturing Technology Development, 17 February 2003.
- Benedyk, J. C., Thermal Fatigue Behavior of H-13 Die Steels, Ph.D. Thesis, Case Western Reserve University, January, 1969.
- Benedyk, J. C., Moracz, D. J., and Wallace, J. F., “Thermal Fatigue Behavior of Die Materials for Aluminum Die Casting, ” Paper No. 111, 6th SDCE (Society of Die Casting Engineers) International Die Casting Congress, November 16–19, 1970.
- Dunn, R. P., “Thermal Fatigue Behavior of H-13 Steel & Other Die Materials for Aluminum Die Casting, ” Report of the Task Group on Materials & Surface Treatments for Dies, Die Casting Research Foundation 1969 Annual Meeting, October 8, 1969.
- Nolen, R. K., Benedyk, J. C., and Howes, M. A. H., Investigation of Strain Softening Occurring during Thermal Fatigue, Internal Research and Development Project Final Report on Project B1051, IIT Research Institute, October 23, 1969.
- Purohit, S. and Tszeng, C., “Carbide Dissolution in H-13 Tool Steel during Austenitization, ” TPTC (Thermal Processing Technology Center, Illinois Institute of Technology) Project Review, 2003.
- Pacyna, J. and Mazur, A., “The Influence of Grain Size upon the Fracture Toughness of the Hot-Work Tool Steel, ” Scandinavian J. of Metallurgy, No. 12, 1983, pp. 22–28.
- Schmidt, M. L., “Effect of Austenitizing Temperature on the Structure and Mechanical Property Behavior of Laboratory Treated Specimens and Large Section Sizes of H-13 Tool Steel, ” Paper No. G-T87-006, 14th SDCE (Society of Die Casting Engineers) International Die Casting Congress, May 11–14, 1987.
- Stuhl, J. H. and Schindler, A. M., “New Materials Study of 5% Chromium Type Steels for Use in Die Casting Dies, ” Paper No. G-T75-053, 8th SDCE (Society of Die Casting Engineers) International Die Casting Congress, May 17–20, 1975.
- Conybear, J. A., “Vacuum Hardening of H-13 Die Steels: Experience with Convective Assisted Heating and Isothermal Holding in Regard to Distortion and Metallurgical Properties, ” reprinted from Industrial Heating, August, 1993.
- Alloy Tool Steel SPEC FACTS A.I.S.I. H-13, DATA SHEET.
- Thelning, K. E., “How Far Can H-13 Die Casting Die Steel Be Improved, ” Paper No. 114, 6th SDCE (Society of Die Casting Engineers) International Die Casting Congress, November 16–19, 1970.
- Huffman, D. D. “Avoiding Retained Austenite in Tool Steels, ” Source Book on Heat Treating: Vol. II – Production and Engineering Practices, American Society for Metals (now ASM International), December, 1974, pp. 276–79.
- Y.-M. Rhyim, et al., “Effect of Surface Treatment on the Life of AISI H-13 Steel Core Pin for Die Casting, ” Key Engineering Materials, Vols. 326–28, 2006, pp. 1181–84.
- Metals Handbook Ninth Edition. Volume 9: Metallography and Microstructures, American Society for Metals (now ASM International), 1985, p. 228.
- Cremisio, R. S., Pridgeon, J. W., and Mills, D. W, Hot Work Materials Processing and Metallurgy for Hot Extrusion Applications, AJAX Forging and Casting Co., Allegheny Ludlum Industries Co., Ferndale, MI, 1977, pp. 24–25.
- Metals Handbook Ninth Edition. Volume 1. Properties and Selection: Irons and Steels, American Society for Metals (now ASM International), 1978, p. 440.
- Schindler, A. M., Kulmberg, A., and Stuhl, J. H., “Thermal Fatigue of H-13 in Die Casting Applications, ” Paper No. G-T77-065, 9th SDCE (Society of Die Casting Engineers) International Die Casting Congress, June 6–9, 1977.
- Metals Handbook Ninth Edition. Volume 9: Metallography and Microstructures, American Society for Metals (now ASM International), 1985, p. 271.
- MetalTek MTek T90813 H-13 Tool Steel, DATA SHEET.
- Osprey Metals H-13 Tool Steel Powder Grades, DATA SHEETS.
- Cremisio, R. S., Pridgeon, J. W., and Mills, D. W, Hot Work Materials Processing and Metallurgy for Hot Extrusion Applications, AJAX Forging and Casting Co., Allegheny Ludlum Industries Co., Ferndale, MI, 1977, pp. 4–13.
- Crucible CPM® Nu-Die® EZ, DATA SHEET, Issue #2.
- Engineering Properties of Steel: Hot Work Tool Steels, ASM International, 1982, pp. 457–62.
- da Silva, L. L. G., Ueda, M., and Nakazato, R. Z., “Enhanced Corrosion Resistance of AISI H13 Steel Treated by Nitrogen Plasma Immersion Ion Implantation, ” Surf. Coat. Techn., 201, 2007, pp. 8291–94.
- Hamaker, J. C. and Yates, D. H., “A Forward Look at the New Die Steels, ” Paper No. 1201, 4th SDCE (Society of Die Casting Engineers) International Die Casting Congress, November 14–17, 1966.
- Youn, K.-T., et al., “An Evaluation of Thermal Fatigue Cracking and Chemical Reaction in Die Casting Mould, ”Key Engineering Materials, Vols. 345-346, 2007, pp. 701–04.
- Test data and review of latest research on H-13 steel kindly provided by Prof. J. Wallace of CWRU.
- Kamdar, M. H., “Liquid-Metal Embrittlement, ” Metals Handbook. Volume 11. Failure Analysis and Prevention, ASM International, 1986, pp. 225–38.
- Kim, T., et al., “Liquid Zinc Embrittlement Study of H 13 Steel in Various Austenitized and Tempered Conditions, ” TPTC Confidential Report for Industrial Client (data kindly provided with permission), 2008.
- Kamdar, M. H., “Embrittlement by Solid-Metal Environments, ” Metals Handbook. Volume 11. Failure Analysis and Prevention, ASM International, 1986, pp. 239–44.
- Takao, et al., “Crack Initiation and Propagation Mechanism of Die for Extruding 7000 Series Alloy, ” Keikinzoku Fakkai Koen Gaiyo, 1993, Vol. 84, pp. 275–76 (in Japanese).
- Benedyk, J., et al., “Literature Survey on H-13 Extrusion Die Failure (I), ” TPTC Confidential Report for Industrial Client, 2003.
- Gordon, P., “Metal-Induced Embrittlement of Metals – An Evaluation of Embrittler Transport Mechanisms, ” Met. Trans. A, V. 9A, Feb., 1978, pp. 267–73.
- Kim, C. D, “Hydrogen-Damage Failures, ” Metals Handbook. Volume 11. Failure Analysis and Prevention, ASM International, 1986, pp. 245–51.
- Rosenfield, A. R. and Marshall, C. W., “Ductile-to Brittle Fracture Transition, ” Metals Handbook. Volume 11. Failure Analysis and Prevention, ASM International, 1986, pp.69, 100.
- Shatla, M., Kerk, C., and Altan, T., “Process Modeling in Machining. Part I: Determination of Flow Stress Data, ” International J. of Machine Tools & Manufacture, Vol. 41, 2001, pp. 1511–34.
- Crucible Nu-Die® V (AISI H-13) Tool Steel, Issue #13, DATA SHEET.
- Plane Strain Fracture Toughness (KIc) Data Handbook for Metals, Army Materials and Mechanics Research Center, Watertown, MA, December, 1973.
- Brada, G., “Effects of Quench Rate and Impact Test Temperature on the Toughness and Microstructure of H13, ” Die Casting Engineer, May, 2002, pp. 22–24.
- Huffman, D. D., “Aluminum Extrusion Tooling: Where Do We Stand?, ” International Extrusion Technology Seminar, 1969, paper no. 23.
- Philip, T.V., “ESR: A Means of Improving Transverse Mechanical Properties in Tool and Die Steels, ” Metals Technology, Dec., 1975, p. 554.
- Manson, S. S., Thermal Stress and Low-Cycle Fatigue, McGraw-Hill, 1966, pp. 125–91.
- Manson, S. S. and Halford, G., “A Method of Estimating High-Temperature Low-Cycle Fatigue Behavior of Materials, ” NASA Lewis Research Center, Cleveland, Ohio, January, 1967.
- Barrow, B. J., “The Thermal Fatigue Resistance of H-13 Die Steel for Aluminum Die Casting Dies, ” NASA Technical Memorandum 83331, NASA Lewis Research Center, Cleveland, Ohio, August, 1982.
- Rostoker, W., et al., The Metallurgy of Thermal Fatigue: Summary Report IV on Thermal Fatigue Resistance of Martensitic Steels, IITRI-B879-20, July 17, 1967.
- Alloy Tool Steel SPEC FACTS Premium Grade H-13, DATA SHEET.
- Ehrhardt, R., et al., “Improving the Heat Checking Characteristics of AISI H13 by Modification of the Chemical Composition, ” Die Casting Engineer, Nov., 2003, pp. 30–37.
- Metals Handbook Ninth Edition. Vol. 16. Machining, ASM International, 1989, pp. 712–26.
- Metals Handbook Ninth Edition. Vol. 16. Machining, ASM International, 1989, pp. 557–64)
- Bosheh, S. S. and Mativenga, P. T., “White Layer Formation in Hard Turning of H13 Tool Steel at high Cutting Speeds Using CBN Tooling, ” International J. of Machine Tools & Manufacture, Vol. 46, 2006, pp. 225–33.
- Metals Handbook Ninth Edition. Vol. 16. Machining, ASM International, 1989, pp. 514–19)
- Extrusion Dies & Tooling Manual: Recommended Handling and Maintenance, Aluminum Extruders Council, pp. 16-17.
- Björk, T., Westergård, R., and Hogmark, S., “Wear of Surface Treated Dies for Aluminium Extrusion – A Case Study, ” Wear, Vol. 249, 2001, pp. 316–23.
- Müller, K. B., “Deposition of Hard Films on Hot Working Steel Dies for Aluminium, ” J. of Materials Processing Technology, Vols. 130-131, 2002, pp. 423–37.
- Okuno, T., “Effect of Microstructure on the Toughness of Hot Work Tool Steels, H13, H10, H19,” Tran. ISIJ, Research Article, Vol. 27, 1987, pp. 51–59.
- Leskovšek, V., “Correlation Between the KIc,the HRC and the Charpy V-Notch Test Results for H11/H13 Hot work Tool Steels at Room Temperature,” Steel Research Int., Vol. 79, No. 4, 2008, pp. 306–13.
- Barker, L. M. and Leslie, W. C.,” Short Rod KIc Tests of Several Steels at Temperatures to 700K,” Fracture 1977, Vol. 2, ICF4, Waterloo, Canada, June 19–24, 1977, MS311, pp. 305–11.
- ASTM E 1304: Standard Test Method for Plane-Strain (Chevron-Notch) Fracture Toughness of Metallic Materials.
- Qamar, S. Z., et al., “Regression-based CVN-K-Ic Models for Hot Work Tool Steels,” Mater. Sci. and Eng., Vol. A 430, 2006, pp. 208–15.
9. Copyright:
- This material is "Author: J. C. Benedyk"'s paper: Based on "Aerospace and High Performance Alloys Database Ferrous • FeUH H-13 August 2008".
- Paper Source: [Not available in the document]
This material was summarized based on the above paper, and unauthorized use for commercial purposes is prohibited.
Copyright © 2025 CASTMAN. All rights reserved.